X6132铣床的数控化改造设计【优秀机械毕业设计@word+6CAD全套图纸】
07- 评语.doc
X6132铣床的数控改造任务书.doc
封皮.doc
总汇6张CAD图纸.dwg
正文.doc
毕业设计(论文)任务书
毕业设计(论文)题目:
X6132铣床数控改造
毕业设计工作内容:
1、实际调研,收集相关资料,完成开题报告;1—3周。
2、结合生产实际,对X6132铣床数控改造;
3、设计X6132铣床数控改造原理图; 4—7周。
4、设计X6132铣床车床数控改造纵向、横向进给结构8—11周。
5设计相关零件图; 12—13周
6、撰写毕业设计论文;准备答辩。 14---16周。
注:要求全部用计算机绘图和打印文稿(交打印件和电子稿)
资料:
1、金属切削机床与数控机床;
2、非标设计手册;
3、金属切削用量手册;
4、相关的技术资料。
指导教师意见:
X6132铣床数控改造
摘 要
本文提供了一种X6132铣床的数控化改造方案,改造的主要模块有:机械部分和数字控制电路部分。机械部分主要是对丝杠、驱动元件的改造。改造后的系统是以步进电机为驱动执行元件的开
环控制系统,控制系统使系统能够控制进给轴的转速,并实现其正反转控制工作台,实现其纵、横向进给运动,以8031型单片机为控制处理芯片,通过键盘输入加工程序控制X6132铣床数控化
改造后是升降台式的。使得改造后的机床能加工除了铣削键槽、平面及孔等简单的零件外,还能加工形状复杂(如加工圆弧面、斜面及凸轮等)的零件。改造后的数控机床具有高精、高效及
加工产品范围广等特点。随着制造技术的发展,现代数控机床借助现代设计技术、工序集约化和新的功能部件使机床的加工范围、动态性能、加工精度和可靠性有了极大的提高。
关键词 数控改造 ; X6132 ;开环控制
X6132 Transformation NC
Abstract
In this paper ,in base of our country’s eco-mimic condition and the expensive CNC, in order to extend machining scope, high accuracy , small batch, and has a good
condition in excitedly complicities market .So, the memorization rebuilding of X6132is so necessary and feasible. This paper provides a way of how to implement the
synchronized mo-tion of the two axes in the X and Y plane with CNC system and an open-loop control which use stepping motors as actuators on a X6132 mill,and the
microcomputer is 8031.the memorization rebuilding of X6132 milling machine not only is used for machining keyway, plane and hole etc,but also, it can ma- unfitting
complicated ship and the accuracy is high.The technology of CNC has become the key and basic technology in the manufacturing in-dustry.With the development of
manufacturing technology, modern CNC machine tools with modern design techniques, process intensification and new features to make machine tools, machining range,
dynamic performance, machining accuracy and reliability has improved greatly.
Key Words numerization rebuilding ;X6132 ;open-loop control
目录
摘要I
AbstractII
第1章 绪论1
1.1 课题研究的背景必要性1
1.2 数控机床的产生及发展简史1
1.3 数控机床组成2
1.4 机床数控化改造的必要性和迫切性3
1.5 机床数控化改造的意义3
1.5.1 从微观上看3
1.5.2 从宏观上看4
1.6 本章小结5
第2章 数控系统设计的总体方案6
2.1 数控铣床改造设计总体要求和内容6
2.2 数控系统总体设计方案的拟定及框图6
2.2.1 系统总体方案的确定6
2.2.2 系统总体方案框图7
2.3 机床进给伺服系统机械部分设计计算包括的内容8
2.4 本章小结8
第3章 铣床机械机构设计9
3.1 数控机床的数据9
3.2 工艺数据9
3.3 数控改造的纵向方向(X轴)的设计10
3.3.1 切削力的计算10
3.3.2 丝杠工作时轴向压力F轴的计算11
3.3.3 滚珠丝杠副工作负荷的计算及电动机的选择11
3.3.4 滚珠丝杠副轴向刚度Kz的计算16
3.3.5 滚珠丝杠副临界转速的验算18
3.4 关于滚珠丝杠副性能的分析18
3.5 横向(Y轴)的设计19
3.6 轴承的选择20
3.6.1 轴承的寿命计算20
3.6.2 轴承布局21
3.6.3 轴承装置的设计21
3.6.4 轴承的配置21
3.6.5 轴承的配合22
3.6.6 轴承的润滑23
3.7 本章小结24
结论25
致谢26
参考文献27
附录28
第1章绪论
1.1课题研究的背景必要性
随着科学技术的发展,机械产品日趋精密、复杂、而且产品的生产周期短、改型频繁。这不仅对机床设备提出精度与效率的要求提出了通用性与灵活的要求。特别是航空、造船、武器、模具
生产等精密加工的零件具有精度高、形状复杂、经常变动的特点。因此机械产品部件的生产设备机床也相应的提出了高性能、高精度化的要求。
利用计算机控制数控机床进行加工使得零件的加工变得十分的方便、快速,很大程度上节约了人力和物力的使用,使得工业自动化程度更高。但是许多企业由于资金等方面的约束不能及时引
进先进数控机床,这样制约了生产率的提高,不利于自动化程度的提高。因此各种机床的数控改造开发成为众多专业技术人员研究的[1]。
并且目前在机械行业中,随着市场经济的发展,产品更新周期越来越短,中小批量的生产所占有的比例越来越大,对机械产品的精度和质量要求也在不断地提高与推进。所以普通机床越来越
难以满足加工的要求,同时由于技术水平的提高,数控机床的价格在不断下降,因此,数控机床在机械行业中的使用将越来越普遍,而对原有普通机床数控化改造也应是越来越广泛,依照设
计任务本设计对X6132立式铣床进行了数控化改造[2]。
1.2数控机床的产生及发展简史
随着科学技术的发展,机械产品的结构越来越合理,其性能、精度和效率日趋提高,因此对加工机械产品零部件的生产设备-----机床也相应地提出了高性能、高精度与高自动化的要求。
在机械产品中,单位与小批量产品占到70%---80%,这类产品一般都采用通用机床加工,当产品改变时,机床与工艺装备均需作相应的变换和调整,而且通用机床的自动化程度不高,基本上需
要人工操作,难以提高生产效率和保证生产质量。特别是一些有曲线、曲面轮廓组成的复杂零件,只能借助靠模和仿形机床,或者借助划线和样板手工操作的方法来加工,加工精度和生产效
率受到很大的限制。
数字控制机床就是为了解决单位、小批量,特别是复杂型面零件加工的自动化,并保证质量要求而产生的。
数控机床的发展简史
在美国诞生了第一台数控机床后,可划分为两个阶段:
第一阶段:数控阶段(1952~1970年)。早期采用数字逻辑电路组合成一台机床,专用计算机作为数控系统,被称为硬件连接数控,简称为数控。
第二阶段:计算机数控(CNC)阶段(1970年~现在)。到1970年,通用小型计算机作为数控系统的核心部件,从此进入了计算机数控阶段。
1.3数控机床组成
数控铣床是在一般铣床的基础上发展起来的,两者的加工工艺相同,结构也有些相似,但数控铣床是靠程序控制的自动加工机床,所以其结构也与普通铣床有较大区别。
数控铣床一般由数控系统、主传动系统、进给伺服系统、冷却润滑系统等几大部分组成:
1.主轴箱 包括主轴箱体和主轴传动系统,用于装夹刀具并带动刀具旋转,主轴转速范围和输出扭矩对加工有直接影响。
2.进给伺服系统 由进给电机和进给执行机构组成,按照程序设定的进给速度实现刀具和工件之间的相对运动,包括直线进给运动和旋转运动。
3.控制系统 数控铣床运动控制的中心,执行数控加工程序控制机床进行加工。
4.辅助装置 如液压、气动、冷却和润滑系统和排屑、防护等装置。
5.机床基础件 通常是指底座、立柱、横梁等,它是整个机床的基础和框架[3]。数控铣床加工过程示意图 1-1如下:
1.4机床数控化改造的必要性和迫切性
数控机床是一种典型的机电一体化产品,它集精密、柔性和集成与一身,它可以较好的解决形状复杂、精密、小批多变的零件加工问题,能够稳定加工质量和提高生产效率,是一种高度自动
化机床。其造价较低,改造周期短,可靠性高,改造技术也日趋成熟,加之我国特有的经济实用产品“经济型数控装置”的技术指标不断的提高,产品的更新和完善的进度不断的加快,产量
不断的提高,故有广阔的前景,工业发达国家的军、民机械工业已开始大规模应用数控机床。其本质是,采用信息技术对传统产业进行改造。而我国在信息技术改造传统产业方面比发达国家
落后约20年。随着我国现代化制造的不断推进,每年都有大量机电产品进口,这说明了机床数控化改造的必要性和迫切性[4]。
1.5机床数控化改造的意义
旧机床数控化系统改造具有多方面的意义:首先,对原有机床进行升级改造,使机床“起死回生”,增加了机床的使用寿命,拓展了机床的适用范围,提高了机床的加工性能。再有,由于是对
原有机床进行的改造,使企业节省了成本,减少了机床废弃的浪费;使本企业的原有操作人员更容易加快熟悉其全部的操作流程。
由此可见,对原有机床进行数控化改造,对资金和技术要求相对较低。对像我国这样的发展中国家的企业具有深远的意义。
1.5.1从微观上看
数控机床相对传统机床有如下突出的优越性,且这些优越性均来自数控系统所包含的计算机的威力。
1.可以加工出传统机床加工不出来的曲线、曲面等复杂的零件 由于计算机可以瞬时准确地计算出每个坐标轴应该运动的运动量,这就可以复合成复杂的曲线与曲面。
2.可实现加工的自动化,且是柔性自动化,从而效率可比传统机床提高3-7倍,由于计算机有记忆和存储能力,可以将输入的程序记住和存储下来,然后按程序规定的顺序自动去执行,而实
现自动化。传统机床可以靠凸轮或挡块等实现自动化,称之为刚性自动化,但凸轮制造、调整很费时,只有进行大批量生产时才经济合理。而数控机床只要更换一个程序就可实现另一个工件
加工的自动化,从而使单件和小批量生产得以自动化,称之为“柔性自动化”,以适应多品种小批量的生产方式。
3.加工出零件的精度高,尺寸的一致性好,分散度小,使装配容易,不再需要“修配”加工过程自动化,不受人的情绪高低和疲劳的影响。计算机还可以自动进行刀具寿命管理,不会因刀具
磨损而影响工件精度和其一致性。数控系统中增加了机床误差、加工误差修正补偿的功能。使加工精度得到进一步提高。
4.可实现多工序的集中,减少零件在机床间的频繁搬运自动化带来的效果(可以自动更换刀具)。如加工中心,在工件装夹好后,可实现钻、铣、镗、攻丝、扩孔等多工序的加工。现已出现
其它工序集中的机床,如车削中心、车铣中心、磨削中心等。
5.拥有自动报警、自动监控、自动补偿等多种自律功能,因而可实现长时间无人看管在配备多种传感器的条件下,计算机威力的体现可以实现白班有人看管和作好充分准备工作,使得二班、
三班在无人看管条件下进行自动加工。工人只工作8小时,而机床可工作24小时。因而带来的劳动生产率的提高和生产周期的缩短等效益是非常明显的。
此外,机床数控化还是推行FMC(柔性制造单元)、FMS(柔性制造系统)、CIMS(计算机集成制造系统)等企业信息化改造的基础[5]。
1.5.2从宏观上看
工业发达国家的军、民机械工业在上世纪70年代末、80年代初即以开始大规模应用数控机床。其本质是,采用信息技术对传统产业的技术改造。除采用数控机床外,还包括推行CAD、CAE、CAM
、MIS(管理信息系统)、CIMS(计算机集成制造系统)等等,以及在其产品中增加信息技术,包括人工智能等含量。由于采用信息技术对其军、民机械工业进行深入改造,最终使得他们的产
品在国际军、民品市场上的竞争力大为增强。而我们在信息技术改造传统产业方面比发达国家约落后20年,因此每年都有大量机电产品进口。这也就从宏观上说明了机床数控化改造的必要性
和紧迫性。
近年来,全国约改造了两万多台普通机床为经济型数控机床(主要是车床和铣床)。随国产高档数控系统的成功研发,我国又成功地用国产数控系统将普通机床改造为普及型和高级型数控机
床,还用国产系统对进口的技术老化数控机床进行改造,使其起死回生。例如:华中数控公司把东方电机厂的10台重型机床(包括2.5m,3.4m,6.3m立车)和中型机床(包括卧车、立铣)及其
它企业总共约50台的关键设备,改造为普及型和高级型数控机床。若购置一台新的数苦恼感机床,进口的要上千万,国产的也要几百万元人民币。而数控化改造一台只需几十万元就够了。所
以比起经济型数控改造来说,经济效益极为显著。内蒙一机集团近年来也加大了普通机床的数控化改造,由西南自动化研究所对部分机床(卧车、铣床等)进行数控化改造,使用效果明显;
又用西门子系统对特大型进口关键设备进行数控改造,使其焕发了青春。
1.6本章小结
本章主要介绍了数控机床的结构特点以及数控机床在未来的发展,机床的数控改造具有效率高,柔性化,减少工人强度等优点,在信息时代的今天,数控机床的改造已经日益普遍,成为发展
的趋势。
第2章 数控系统设计的总体方案
2.1数控铣床改造设计总体要求和内容
X6132立式铣床的原传动系统为其主轴转动由电机经齿轮变速驱动。其主轴的升降用手柄经锥齿轮副,丝杠手动操作。工作台的x轴和y轴分别通过离合器和离合器,由进给电动机通过齿轮变速
驱动丝杠副和实现自动进给。工作台的升降有电动机通过离合器将运动传给丝杠副来实现 。
对X6132立式铣床进行机械部分改造,数控机床的刚度系数应该比同类普通机床高50%;应尽量提高机床的抗振性,通常机床的振动包括强迫振动和受迫振动。要提高机床在低速进给时的平稳
性和运动精度。为实现复杂零件的自动铣削加工,提出三种方案:
第一种方案:工作台升降,工作台x与y轴的进给运动
第二种方案:主轴的升降和工作台的x,y轴的进给运动
第三种方案:工作台的x,y轴进给运动改变为微机控制,实现三轴或二轴的开环同步控制或非同步控制。
上述方案中的第一种由于工作台较重,升降所需的步进电机转矩大,功率损失也大,改造成本较高,第二种方案较易实现,我们这里的设计要求改造x,y轴,z轴作为预留,所以我们这里选择
第三种方案。
为保留原机床的半自动功能,应对原系统作尽可能少的改动,以免微机控制系统出了问题,机床还可手动加工。为此可进行以下改动,如图
2-1所示:
1 保留原机床主轴传动系统。
2 保留机床工作台x,y 轴进给系统,脱开离合器6,7,去掉手轮,将滑动丝杠副换成滚珠丝杠副,并改装减速齿轮箱,减速齿轮,步进电动机(6,7)。
参考文献
1 张俊生.金属切削机床与数控机床.北京机械工业出版社,1994:25~43
2 谢家瀛.机床设计图册.上海出版社,1979.6:44~73
3 明兴祖.数控加工技术.北京化工出版社,2002:47~60
4 赵万昌.电机工程手册.机械工业出版社,1982:129~172
5 李福生.数控机床技术手册.北京出版社,1996:12~56
6 徐宏海,谢富春.数控铣床.北京化工出版社,2003:3~32
7 吴圣庄.金属切削机床技术.北京机械工业出版社,1985:43~56
8 林其骏.机床数控制系统.中国科学技术出版社,1991.9:12~46
9 孙承松.机床设计手册.机械工业出版社.1997:75~94
10 王爱玲.机床.北京出版社.1983第9期:43~100
11 顾维邦.金属切削机床概念.北京机械工业出版社,1996:158~189
12 赵月望.机械制造技术实践.北京机械工业出版社,1993:43~90
13 赵长德.微机原理与接口技术.中国科学技术出版社,1990.9:34~98
14 Gu, L. Z., Wang, d., Xing, L.,etc.Computer simulation and optimization of metal cutting process for mild carbon steels, Journal of Materials Processing Technology
129 (2002) 60~65
15 Didjanin, L. and Kovac, P., Fracture mechanisms in chip formation processes, Materials Science and Technology 13 (1997) 439~444
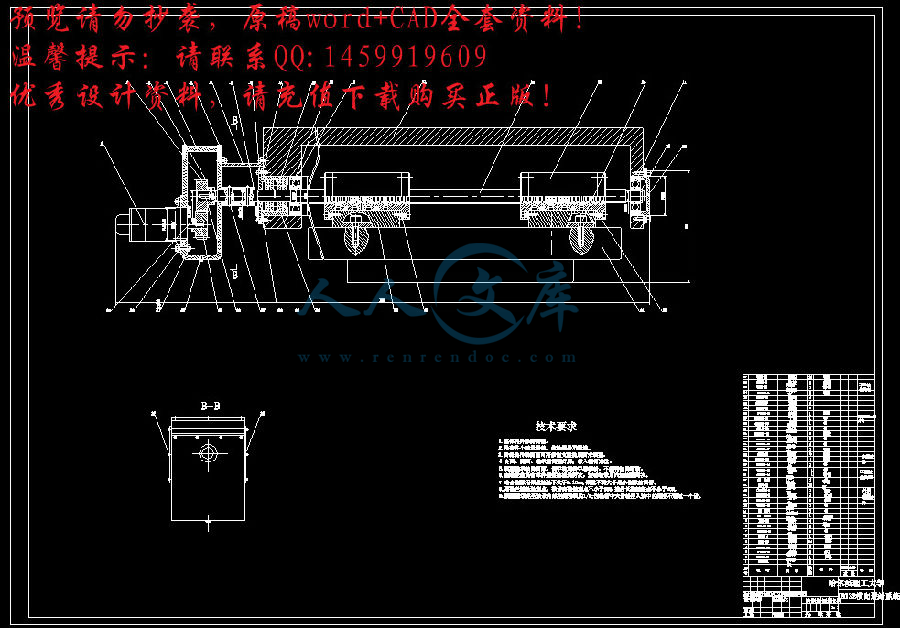





