方刀架零件的工艺及铣槽38mm夹具设计
25页 5800字数+说明书+任务书+工序卡+工艺过程卡+4张CAD图纸【详情如下】
任务书.doc
工序卡.doc
工艺过程卡.doc
方刀架毛坯图.dwg
方刀架零件图.dwg
方刀架零件的工艺及铣槽38mm夹具设计说明书.doc
铣槽38mm夹具装配图.dwg
铣槽38mm夹具零件图.dwg
目 录
一 零件的分析 ………………………………………………………1
二 工艺规程设计 ……………………………………………………2
(一)确定毛坯的制造形式 ………………………………………2
(二)定位基准的择 ………………………………………………2
(三)制定工艺路线 ………………………………………………3
(四)确定加工余量、工序尺寸及毛坯尺寸的确定 ……………5
(五) 确定切削用量及基本工时 …………………………………6
三 专用夹具设计………………………………………………………17
夹具概念 ……………………………………………………17
夹具设计 ……………………………………………………18
夹具图绘制 …………………………………………………19
四 课程设计心得体会…………………………………………………21
五.参考文献 …………………………………………………………22
一、零件分析 (一)零件的作用
题目所给定的零件是车床上的方刀架,其主要作用就是通过装在刀架上的其它零件夹紧刀具,换刀时,在手柄转动下,带动方刀架回转,以达到换刀的目的。
(二)零件的工艺分析
方刀架以下表面为基准加工加工其周围一系列的孔,孔之间有一定的位置要求,现将加工部位分述如下:
1、以下表面和中心通孔为基准的表面 这组表面先加工下表面,此表面精度要求高,其表面粗糙度要求达到0.8,要求平面度0.05,相对于零件图中A面的跳动为0.05。以此表面为基准加工Φ48H7、Φ48.2孔。
2、工件表面的孔 钻攻8-M16孔,钻孔Φ16H7,钻通孔Φ10.2,钻2-Φ10.2×26,攻M12×20,攻M12×30,扩孔Φ19.2,此系列孔加工时通过钻模板来保证位置精度,其中Φ48H7孔必须在Φ16H7和Φ19.2孔中心连线上。Φ16H7孔垂直度要求相对于B面100:0.1,孔内壁表面粗糙度要求达到1.6。
二.工艺规程设计
(一)确定毛坯的制造形式
零件材料为45钢,方刀架用于夹持刀具,工作时受到的力与振动较大,因此应该选用锻件,以使金属纤维尽量不被切断,提高零件力学性能和强度,保证零件工作安全可靠。由于零件年产量为中批生产,而且零件属于轻型机械,故可采用模锻成型。这从提高生产率,保证加工精度上考虑,也是应该的。
零件形状并不复杂,因此毛坯形状可与零件形状尽量接近,各孔不锻出。
(二)定位基准的选择
基准选择是工艺规程设计中的重要工作之一。基准选择的正确与合理,可以使加工质量得到保证,生产率得到提高,否则加工工艺过程中的问题百出,更有甚者,还会造成大批零件报废,使生产无法正常进行。
1 、粗基准的选择
粗基准的选择应满足以下的要求:
保证加工其他面时有足够的加工余量。
保证精加工时定位面有一定的精度。
为满足上述要求,应选下表面作为粗基准。
2、 精基准的选择
为了保证阶精度,采用底面为精基准,符合基准重合原则和基准统一原则。
(三)制定加工工艺路线
制定工艺路线的出发点,应当是使零件的加工精度和表面质量等技术要求能得到合理的保证。在生产纲领已确定为中批生产的条件下,可以考虑采用效率较高的通用机床配以专用夹具,并尽量使用工序集中来提高生产率。除此之外,还要考虑经济效果,以便使生产成本尽量下降。
工艺路线方案一:
工序1:备料
工序2:锻造毛坯
工序3:热处理(正火)
工序4:车端面
粗镗孔至Φ47.7 精镗孔至Φ48H7
精镗孔Φ48.2
倒角3×45°
工序5:掉头车另一端面,精镗孔Φ60
车倒角1.5×45°
工序6:铣四侧面
工序7:铣通槽
工序8:钻通孔Φ15,扩孔至Φ15.85,铰孔至Φ16H7
钻8-Φ14底孔,攻螺纹8-M16
钻通孔Φ10.2,钻2-Φ10.2×26
攻螺纹2-M12×20,攻螺纹M12×30
扩底孔Φ19.2
工序9:钻扩槽内斜孔至Φ9.8,铰斜孔至Φ10H7
工序10:铣槽R9
工序11:铣槽R4
工序12:铣端面四周的倒棱
工序13:精铣通槽基面
工序14:磨下表面
工序15:磨四周面
工序16:终检:上表面的跳动允差0.05
槽的基面平面度允差0.1
底面的平面度允差0.05
跳动允差0.05
工序17:倒锐角去毛刺
工序18:清洗
工序19:发兰
工艺路线方案二:
工序1:备料
工序2:锻造毛坯
工序3:粗铣底面
工序4:精铣上面(从底面为基准压紧)
工序5:粗铣四侧面
工序6:铣通槽
工序7:半精磨上面(留量)
工序8:半精磨另五面
工序9:镗孔扩孔Φ48H7 镗孔Φ48.2 倒角3*45°
工序10:扩孔Φ60 倒角1.5×45°
工序11:铣槽R9
工序12:铣油沟R4
工序13:钻攻2-M12×20 M12×30
钻攻8-M16
工序14:钻铰Φ10斜孔
工序15:钻通孔Φ15,扩孔至Φ15.85,铰孔至Φ16H7
扩孔Φ19.2
工序16:去毛刺
工序17:磨六面
工序18:清洗
工序19:检验
工序20:发兰
方案一基准易于选择,加工性比较好。综合对可得,工艺一优于工艺二。最终选择工艺路线一为本次设计的加工工序。
(四)机械加工余量、工序尺寸及毛坯尺寸的确定
根据《机械制造工艺手册》, 分别确定机械加工余量,以及尺寸及其公差,如加工工序图表所示:结合毛坯图和零件图可知各轴径的总余量分布如下
孔φ48H7
此孔精度IT6, =1.6,参照手册确定工序尺寸及余量为:
粗镗:φ47.7mm
精镗:φ 2Z=0.3mm
2.孔φ16H7 =1.6
钻孔:φ15mm
扩孔:φ15.85mm 2Z=0.15mm
铰孔:φ16H7 2Z=0.15mm
3.孔φ19.2 =3.2
钻孔:φ10.2mm
扩孔:φ19.2mm 2Z=9mm
4.铣通槽 =3.2
粗铣通槽 2Z=3mm
精铣通槽 2Z=2mm
5.磨表面 =0.8 2Z=1mm
6.填写工艺卡片和机械加工工序卡片
(五) 确定切削用量及基本工时
车端面 粗镗孔至Φ47.7 精镗孔至Φ48H7 精镗孔Φ48.2 倒角3*45°
本工序采用计算法
1.加工条件
工件材料:45钢正火,σb=0.35Gpa,模锻
加工要求:车方刀架底面,粗镗Φ48H7孔至47.7,精镗孔至48H7, Ra1.6,精镗孔Φ48.2,倒角3X45
机床CA6140车床
刀具:端面车刀:刀片材料YT15,刀杆尺寸16X25mm2, Kr=90°,r0=15°,a0=12°,re=0.05mm
硬质合金浮动镗刀
2.计算切削用量
1).车端面
吃刀深度ap=5mm
机械制造工艺学课程设计是我们学完了大学的全部基础课、技术基础课以及大部分专业课之后进行的。这是我们在进行毕业设计之前对所学各课程的一次深入的、综合性的总复习,也是一次理论联系实际的训练。因此,它在我们四年的大学生活中占有重要的地位。
就我个人而言,我希望能通过这次课程设计对自己未来将从事的工作进行一次适应性训练,从中锻炼自己分析问题、解决问题的能力,为今后参加祖国“四化”建设打下一个良好的基础。
由于能力所限,设计尚有许多不足之处,恳请各位老师给予指教。3.确定定位方案,设计定位元件
方刀架中心孔φ48mm孔是通孔,定位时可利用此孔,加上底面,在工件侧面配以定位板即可达刀对工件的完全定位。即可保证工件不能旋转,不会上下窜动。
4.确定夹紧方式和设计夹紧机构
因为工件属于大批量生产,宜采用专用夹紧装置,通过穿过零件中心的拉杆,由卡环卡住工件,采用液压传动,拉紧工件
5.确定夹具体
将定位、导向、夹紧机构连接在一体,并能正确的安装在机床上。由于液压缸中活塞杆为动力件,考虑刀工件的加工方向,将其置于夹具体下方,夹具体外围由肋板支起,中心为空。
(三)夹具图绘制
(1)夹具总图应遵循机械制图国家标准绘制,图形大小的比例尽量去1:1,为求使绘制的夹具总图具有良好的直观性,如工件过大时选用1:2等缩小比例,过小时取2:1的比例。
(2)在总图中应以最少数量视图清楚地表示出夹具的工作原理和结构,表示各种元件或装置之间的位置关系等。
(3)绘制总图的顺序:先用点划线绘出工件的轮廓外形及定位基准,并用网状线显示出加工余量;把工件轮廓视为透明体,然后按着工件的形状及位置依次画出定位、导向、夹紧及其它元件或装置的具体结构;最后绘制夹具体,形成一个完整的夹具。
(4)在夹具总图上标注出零件编号,按规定要求填写标题栏和明细表。
(5)确定并标注有关尺寸和夹具技术要求。
五 参考文献
1.兰建设主编.机械制造工艺与夹具.北京:机械工业出版社.2004.7
2.董燕主编.公差配合与测量技术. 北京:中国人民大学出版社.2001.3
3.唐建生主编.金属切削原理与刀具.武汉理工大学出版社.2005
4.张普礼主编.机械加工设备. 北京:机械工业出版社.2005.08
5.刘家平主编.机械制图. 西安:西安电子科技大学出版社.2006.02
6.《金属机械加工工艺人员手册》修订组.金属机械加工工艺人员手册.
7.《切削用量手册》
8.《简明机械加工手册》
9. 《机械制造工艺与机床夹具课程设计指导》第2版吴拓编
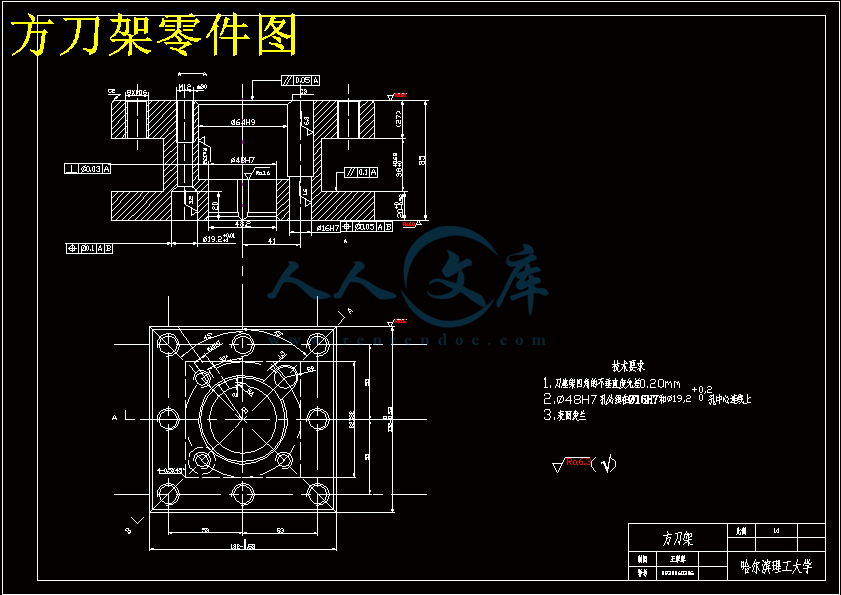
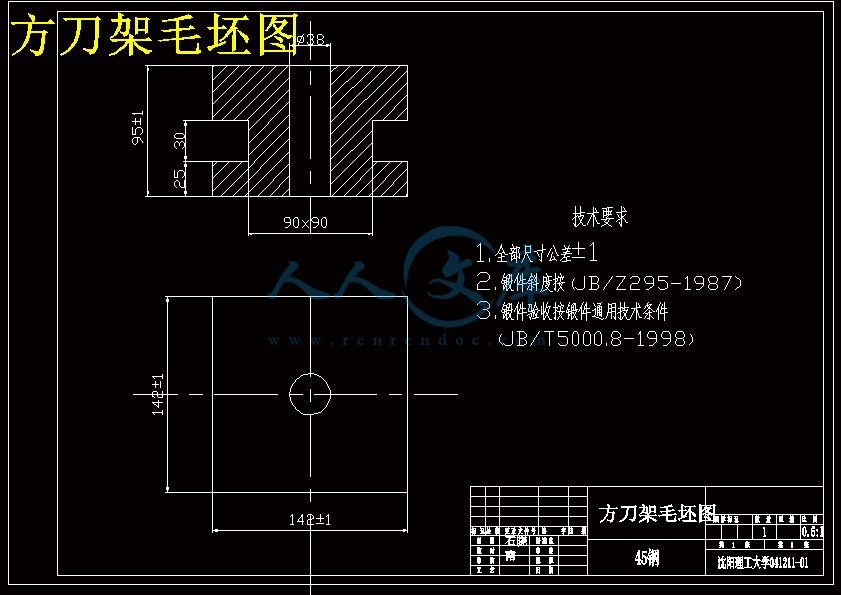



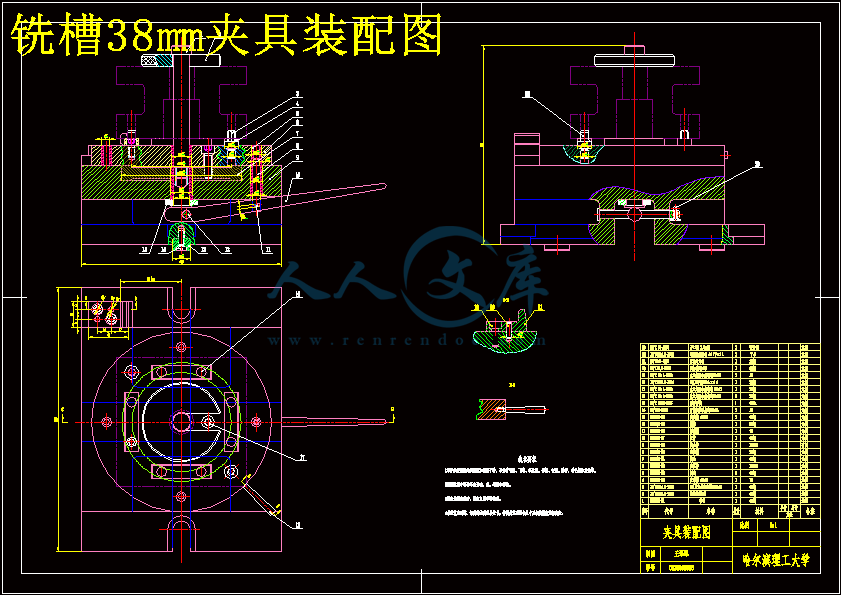