QTZ125塔式起重机总体及臂架、变幅机构的设计【优秀毕业设计】【word+12张CAD图纸全套】
【带任务书+开题报告+实习报告+外文翻译】【100页@正文39000字】【详情如下】【需要咨询购买全套设计请加QQ1459919609】
QTZ125参数.doc
QTZ125塔式起重机设计任务书.doc
专业英文翻译
卷筒.dwg
变幅小车A1.dwg
实习报告.doc
小图合计6张.dwg
开题报告.doc
总图合计3张.dwg
机构简图.dwg
正文.doc
计算书.doc
计算书封面.doc
毕业设计(论文)任务书
QTZ125塔式起重机总体、臂架、变幅机构设计
1、毕业设计(论文)目的:
本次毕业设计是对机械专业学生在毕业前的一次全面训练,目的在于巩固自己所学知识并把所学知识运用到实际设计当中,真正明白知识如何应用。训练学生综合运用所学知识分析和解决问题的能力。将所学知识应用与实际培养独立工作能力。毕业设计要求每个学生在工作过程中,要独立思考,刻苦钻研,有所创新、解决相关技术问题。通过毕业设计,使学生掌握塔式起重机的总体设计、塔身的设计、整体稳定性计算等内容,为今后步入社会、走上工作岗位打下良好的基础。
2、毕业设计(论文)任务内容和要求(包括原始数据、技术要求、工作要求等):
(1)设计任务:
①总体参数的选择(QTZ125级别)
②结构形式
(2)总体设计
①主要技术参数性能
②设计原则
③平衡重的计算
④塔机的风力计算
⑤整机倾翻稳定性的计算
(3)变幅机构的设计和计算
① 建立变幅机构的数学模型
② 钢丝绳的选择和校核
③ 卷筒的设计和绕绳系统的计算
④ 验算实际变幅速度
⑤ 电动机的选择
⑥ 蜗轮蜗杆减速器的设计
(4) 臂架的设计和计算
① 分析单双吊点的优缺点
② 吊点位置的选择
③ 臂架结构参数选择
④ 臂架主参数选择与计算
(5)变幅的设计和计算
(6) 要求
① 主要任务:学生应在指导教师指导下独立完成一项给定的设计任务,编写符合要求的设计说明书,并正确绘制机械与电气工程图纸,独立撰写一份2500~~3500字毕业设计小论文,并绘制有关图表。
② 知识要求:学生在毕业设计工作中,应综合运用多学科的理论、知识与技能,分析与解决工程问题。通过学习、钻研与实践,深化理论认识、扩展知识领域、延伸专业技能。
③ 能力培养要求:学生应学会依据技术课题任务,完成资料的调研、收集、加工与整理,正确使用工具书;培养学生掌握有关工程设计的程序、方法与技术规范,提高工程设计计算、图纸绘制、编写技术文件的能力;培养学生掌握实验、测试等科学研究的基本方法;锻炼学生分析与解决工程实际问题的能力。
④ 综合素质要求:通过毕业设计,学生应掌握正确的设计思想;培养学生严肃认真的科学态度和严谨求实的工作作风;在工程设计中,应能树立正确的生产观、经济观与全局观。
⑤ 设计成果要求:
1)凡给定的设计内容,包括说明书、计算书、图纸等必须完整,不得有未完的部分,不应出现缺页、少图纸现象。
2)对设计的全部内容,包括设计计算、机械构造、工作原理、整机布置等,均有清晰的了解。对设计过程、计算步骤有明确的概念,能用图纸完整的表达机械结构与工艺要求,有比较熟练的认识图纸能力。对运输、安装、使用等亦有一般了解。
3)说明书、计算书内容要精练,表述要清楚,取材合理,取值合适,设计计算步骤正确,数学计算准确,各项说明要有依据,插图、表格及字迹均应工整、清楚、不得随意涂改。制图要符合机械机械制图标准,且清洁整齐。小论文要符合论文书写规范。
4)对国内外塔式起重机情况有一般的了解,对各种塔式起重机有一定的分析、比较能力。
其他各项应符合本资料有关部分提出的要求。
3、毕业设计(论文)成果要求(包括图表、实物等硬件要求):
① 计算说明书一份
内容包括:设计任务要求的选型、设计计算内容、毕业实习报告等。作到内容完整,论证充分(包括经济性论证),字迹清楚,插图和表格正规(分别进行统一编号)、批准,字数要求不少于2万字;撰写中英文摘要;提倡学生应用计算机进行设计、计算与绘图。
② 图纸一套
1)总图一张(0号)
2)变幅机构图一张(0号)
3)臂架图一张(0号)
4)零件图至少三张(2,3,4号)
③ 3000字左右的毕业设计小论文一篇
4、主要参考文献:
要求按国标GB 7714—87《文后参考文献著录规则》书写。
[1] 哈尔滨建筑工程学院主编.工程起重机.北京:中国建筑工业出版社
[2] 董刚、李建功主编.机械设计.机械工业出版社
[3] 机械设计手册.化学工业出版社(5册)
[4] GB/T9462—1999 塔式起重机技术条件
[5] GB/T13752—1992 塔式起重机设计规范
[6] GB5144—1994 塔式起重机安全规程
[7] 濮良贵、纪名刚主编.机械设计(第八版).高等教育出版社
5、毕业设计(论文)课题工作进度计划:
起 迄 日 期工 作 内 容
2013.2.25-2013.3.10
2013.3.11-2013.3.24
2013.3.25-2013.4.7
2013.4.8-2013.4.14
2013.4.15-2013.4.28
2013.4.29-2013.5.12
2013.5.13-2013.6.2.
2013.6.3-2013.6.9
2013.6.10-2013.6.13
2013.6.14-2013.6.29外文翻译
熟悉整理资料
毕业实习
撰写开题报告及任务书
方案选择及总体设计
绘制总图
变幅机构设计及其图纸绘制
臂架设计及其图纸绘制
完成毕业设计小论文
准备论文及答辩
摘要
QTZ125型塔式起重机布置合理,外形美观,使用方便,维修简单,工作平稳,就位快捷方便、高效。该塔机为上回转,水平臂架,小车变幅,液压自升式多用途塔机,起重力矩为1250KN2m,最大起重量为10T,独立架设最大起升高度可达200m,最大变幅为63m。
? 变幅机构是为了满足物料装卸工作位置要求,充分利用自身的起吊能力(幅度减少能提高起重量),实现改变幅度的工作机构,并用来扩大塔式起重机的工作范围,提高生产率。
QTZ125塔式起重机是通过移动牵引起重小车实现变幅的。工作时吊臂安装在水平位置,小车由变幅牵引机构驱动,沿着吊臂轨道(弦杆)移动。小车变幅的优点是:变幅时物料做水平移动,安装就位方便;速度快、功率省;幅度有效利用率大。其缺点为:吊臂承受较大的弯距,结构笨重,用钢量大。绳索牵引式变幅机构的小车依靠钢丝绳牵引沿吊臂轨道运行,其驱动力不受附着力的限制,故能在略呈倾斜的轨道上行走,又由于驱动装置在小车外部,从而使小车自重大为减少,所以适用于大幅度起重量较大的起重机。在塔式起重机中大都采用绳索牵引式变幅机构,这样既可以减轻吊臂载荷,又可以使工作可靠,而且因为驱动装置放在吊臂根部,平衡重也可以减少。
关键词:QTZ125塔机、变幅机构、绳牵引小车式
ABSTRACT
QTZ125 tower crane has reasonable layout, beautiful appearance, it is convenient to use, it is simple to repair, it works stable convenient and efficient. The rotary mode is turning on,ir has horizontal jib, trolley, hydraulic jack-up multi-purpose cranes, its lifting moment is 1250KN 2 m and the maximum lifting weight is 10T the maximum lifting height and amplitude is 200m and 63m.
Luffing mechanism make full use of its lifting capacity of (reduction can improve the weight) to meet the requirement of the material handling work location to change the working mechanism of amplitude and to expand the scope of tower crane work, improve productivity.
QTZ125 tower crane changes amplitude through a mobile traction lifting trolley. When the crane works the jib is installed in a horizontal position, the car alongs the crane rail (chord) move which drived by amplitude traction mechanism.The advantages are: when the trolley works the material move horizontally, it is convenient to install; it has fast speed, it saves power and the effective utilization rate is great. Its shortcomings are: the jib beers a big bending moment, heavy structure and a large quantity of steel. Rope traction luffing car moves along the boom in orbit rely on wire rope traction, its driving force is not affected by adhesion, it can be walking in slightly inclined orbit and because the driver in the car outside, so that the weight of the car is reduced greatly so it is suitable for large amplitude heavy crane. Most of the tower use crane rope traction luffing mechanism which not only can reduce the crane load but also can make reliable work and because the drive device on the jib root the balance weight can also reduced.
Keywords: QTZ125 tower crane, luffing mechanism, rope trolley type
目录
第一章 前言1
1.1塔式起重机概述1
1.2塔式起重机的发展趋势3
第二章 总体设计4
2.1 概述4
2.2 总体设计方案的确定5
2.2.1金属结构5
2.2.2工作机构25
2.3 总体设计原则29
2.3.1 整机工作级别32
2.3.2 机构工作级别32
2.3.3 主要技术性能参数32
2.4平衡臂与平衡重的计算33
2.5起重特性曲线35
2.6塔机风力计算37
2.6.1工作工况Ⅰ38
2.6.2工作工况Ⅱ42
2.6.3工作工况Ⅲ44
2.6.4非工作工况Ⅳ46
2.7整机的抗倾翻稳定性48
2.7.1工作工况Ⅰ49
2.7.2工作工况Ⅱ50
2.7.3非工作工况Ⅲ·51
2.7.4工作工况Ⅳ51
第三章 塔身的设计计算52
3.1塔身的总体模型52
3.2 塔身的受力分析及验算53
3.2.1.塔身的受力分析53
3.2.2 塔身内力计算及组合56
3.2.3 塔身整体稳定性和强度验算59
第四章 变幅机构的设计和计算71
4.1变幅机构的形式71
4.2 确定卷筒尺寸71
4.2.1 卷筒名义直径71
4.2.2 多层绕卷筒相关参数计算72
4.3选择电动机、减速器、制动器、联轴器72
4.3.1选择电动机72
4.3.2 选择减速器73
4.3.3 变幅机构制动器的选择74
4.3.4变幅机构联轴器的选择75
4.4. 验算变幅速度77
4.5验算起、制动时间验算77
4.6电动机发热校验79
4.7 校验卷筒强度80
第五章 变幅小车的设计81
5.1 变幅小车的形式81
5.2 变幅小车的设计82
5.2.1 绳索牵引式小车构造及其驱动方式82
5.2.2运行小车牵引力计算83
5.2.3 牵引绳最大张力86
5.2.4 选择牵引绳87
5.2.5 牵引卷筒计算87
第六章 毕业设计小结90
致谢91
参考书目93
第一章 前言
1.1 塔式起重机概述
随着建筑行业的兴起,城镇人口的增多,高层建筑已经成为了一个趋势,来满足人们的住房需求。然而,在建筑行业中,能同时完成垂直升降和水平移动的起重机械很多,但综合其机动灵活性,起升高度,实用性等因素应用最广泛的是塔式起重机。
塔式起重机(tower crane)简称塔机,亦称塔吊,起源于西欧,是现代工业与民用高层建筑的主要施工机械之一。在高层建筑中其幅度利用率高达80﹪,与其它类型的起重机相比,塔式起重机的优势明显,它有多种类别、形式、性能、大小等,它的突出特点是工作效率高、适用范围广、回转半径大、操作方便可靠等。故塔式起重机在建筑安装工程中得到广泛应用。但是塔机的技术有待于提高。塔机的研究正向着组合式发展。所谓的组合式,就是以塔身结构为核心,按结构和功能特点,将塔身分解成若干部分,并依据系列化和通用化要求,遵循模数制原理再将各部分划分成若干模块。根据参数要求,选用适当模块分别组成具有不同技术性能特征的塔机,以满足施工的具体需求。推行组合式的塔机有助于加快塔机产品开发进度,节省产品开发费用,并能更好的为客户服务。
据相关文献记载,有关塔机的第一项专利早在1900年获得批准,近代塔式起重机出现于1912-1914年。第一台比较完整的近代塔式起重机出现于1923年。1930年德国已经开始将塔式起重机批量生产并投入使用,并用于建筑施工。1941年,有关塔机的德国工业标准DIN8770公布。该标准规定以吊载(t)和幅度(m)的乘积(tm)一起以重力矩表示塔机的起重能力。
我国对塔机的研究生产已有近50年的历史,经历了一个从绘制仿制到自行设计的发展过程。在不断的摸索中,我国逐步掌握了塔机生产的生产技术。20世纪80年代改革开放以后,我国引进了许多先进技术,这极大的促进了我国塔机设计制造技术的进步,一些主要机种已达到或接近国外同类产品质量水平。我国的塔式起重机从科研到加工生产方面取得了可喜的进步,但是在和国外先进塔式起重机的使用寿命,成本等方面还存在着一定的差距。我相信在今后的发展中差距会进一步缩小。
随着高层建筑结构件的预制装配化、工厂化等新工艺、新技术应用的不断扩大。拿来与创新,我们要学习国外先进技术,并能够创造出自己的品牌。在新产品开发上我们要学习国外塔机的一些特点:
⑴ 更多的厂家注重开发经济型城市塔机并扩展成系列。
⑵国外塔机新产品中,有一些新颖的轻、中型折叠式快速安装塔机颇引人注目。
⑶根据一些国家城建当局的有关规定,为防止塔机臂架在狭窄的空间运行发生矛盾,避免吊臂相互碰撞以及碰到邻近的建筑物,在城市高层建筑密集地区施工必须采用动臂式自升塔式起重机。
⑷在经过较长时间研制之后,履带式水平臂架塔机作为一种新产品正式问世。
⑸变频调速系统在国外塔机新产品上得到推广应用。
⑹高新技术开始在塔机上应用。
⑺无论上回转或下回转式塔机,都十分重视驾驶室的平面设计和空间处理。
本次设计的课题为QTZ125自升势塔式起重机的设计,根据其分类特点采用上回转式。
QTZ125型自升式塔式起重机,其吊臂长63米,最大起重量10吨,额定起重力矩125吨米。是一种结构合理、性能比较优异的产品,比较目前国内外同规格同类型的塔机具有更多的优点,能满足高层建筑施工的需要,可用于建筑材料和构件的调运和安装,并能在市内狭窄地区和丘陵地带建筑施工。整机结构大,可满足中大型施工队的要求。
本机以基本高度(独立式)47.3米。用户需高层附着施工,只需提出另行订货要求,即可增加某些部件实现本机的最大设计高度200米,也就是附着高层施工可建高楼65层以上。
1.2塔式起重机的发展趋势
根据国内外一些技术资料的介绍,塔式起重机的发展趋势具体归纳为以下几个方面。
1、吊臂长度加长
在20世纪60年代初,吊臂长度超过40m的较少,70年代吊臂长度已能做到70m。快速拆装下回转塔式起重机的吊臂长度可达到35m。自升式塔式起重机吊臂是可以接长的,标准臂长一般为30~40m,可以接长到50~60m。重型塔式起重机吊臂则更长。随着塔式起重机设计水平的提高,可以解决由臂长加大带来的一些技术问题,而低合金高强度钢材及铝合金的广泛采用也为加长吊臂提供了非常有利的条件。
2、工作速度提高,且能调速
由于调速技术的进步,混轮组倍率的可变、双速、三速电动机及直流电动机调速的应用,使塔式起重机工作速度逐渐提高。20世纪50年代生产的塔式起重机工作速度较低,起升速度一般只有20~30m/min,回转速度为0.6~1r/min,变幅速度为30~40m/min,大车行走速度为10~40m/min,而近几年来塔式起重机工作速度已有提高。起升机构普遍做到具有3~4种工作速度,重物起升速度超过100m/min者已经很多,构件安装就位速度可在0~10m/min范围内进行选择,回转速度一般可在0~1r/min之间进行调节,小车牵引和塔式起重机行走大多也有2~3种工作速度,小车牵引速度最快可达60m/min。
3、改善操纵条件
随着塔式起重机向大型、大高度方向发展,操作人员的能见度越来越差。因此需要在吊臂端部或小车上安装电视摄像机,在操作室利用电视进行操作。有的还采用了双频道的无线电遥控系统,不仅可由地面的操作人员控制吊装,还可以根据事先编排的程序自动进行吊装。
4、更多地采用组装式结构
为了便于产品更新换代,简化设计制造、使用与管理,提高塔式起重机使用的经济效益,国外塔式起重机专业厂已做到产品系列化、部件模数化。以不同模数塔身、臂架标准节组合成变断面塔身和臂架,这不仅能提高塔身、臂架的力学性能,减轻塔式起重机自重,而且可明显减少使用单位塔架、臂架的储备量,为降低成本、简化管理创造了条件。
第二章 总体设计
2.1概述
塔式起重机是工业与民用建筑施工中,完成预制构件及其他建筑材料与工具等吊装工作的主要设备。在高层建筑施工中其幅度利用率比其他类型起重机高。塔式起重机的起升高度、工作幅度和起重力矩都很大,这就要对其受力、稳定性等进行考虑与计算。塔机的主要性能参数包括:起重量、起升高度、幅度、各机构工作速度、重量指标和起重力矩等。这些参数表明了起重机的工作性能和技术经济指标,它是设计塔式起重机的技术依据,也是生产中选择塔式起重机技术性能的依据。
总体设计是机械设计整个过程中最关键的环节之一。它是使设计产品满足技术参数及形式的总构想,决定了机械设计的成败。在总体设计前,应先进行深入细致的调查研究,收集国内外同类机型的相关资料,了解国内外塔机的使用情况,并进行分析比较,然后制定总的设计方案。设计原则应当在保证所设计的机型达到国家有关标准的同时,力求结构合理,技术先进,积极性好,工艺简单,工作可靠。
参考书目
【1】《建筑机械钢结构》曹会荣 中国建材工业出版社
【2】《工程起重机》哈儿滨建筑大学 中国建材工业出版社
【3】《液压传动设计手册》 煤炭工业部煤炭科学研究所 上海科学技术出版社
【4】《机械设计手册》(1﹑2﹑3﹑4﹑5﹑6)机械工业出版社
【5】《起重运输机金属结构》西南交通大学 王金诺 于兰峰 中国铁道出版社
【6】《液压站设计与使用》张利平 海洋出版社
【7】《液压与气压传动》 王积伟 章宏甲 黄谊 机械工业出版社
【8】《起重机设计手册》 张质文 虞和谦 王金诺 包起帆 中国铁道出版社
【9】《塔式起重机设计规范》国际技术监督局
【10】《塔式起重机设计》范俊祥 中国建材工业出版社
【11】《工程机械液压及液力传动》(上、下册)中国建材工业出版
【12】《起重机与吊装》 华玉洁 化学工业出版社
【13】《起重运输机金属结构》 王金诺 于兰峰 西南交通大
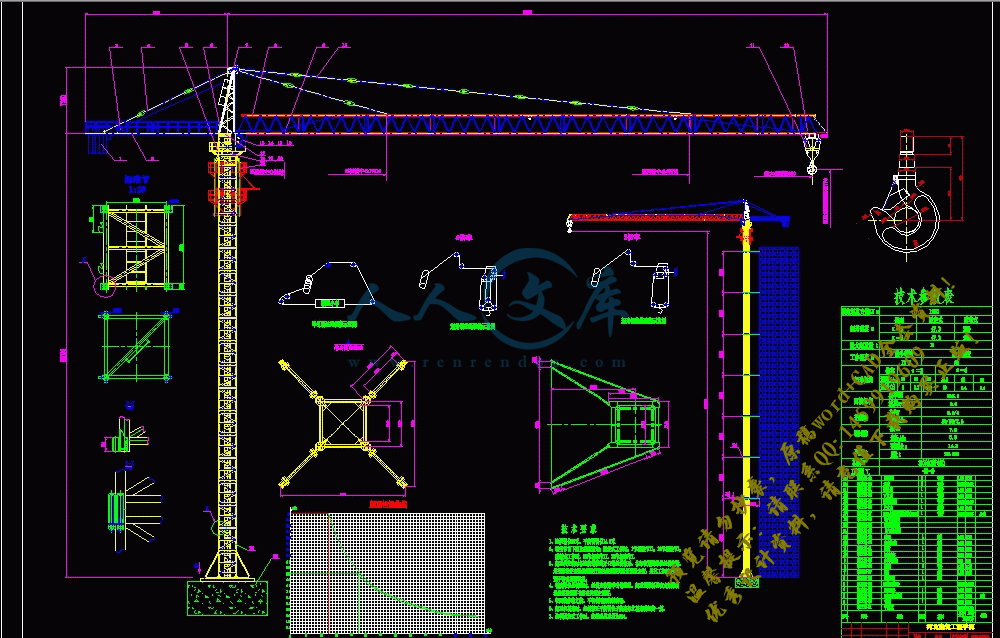

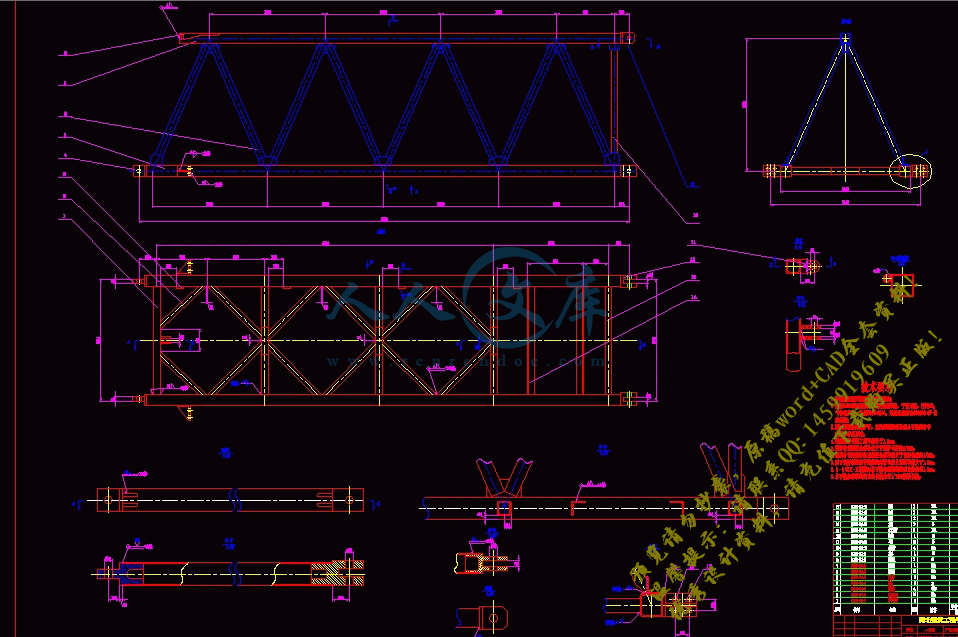
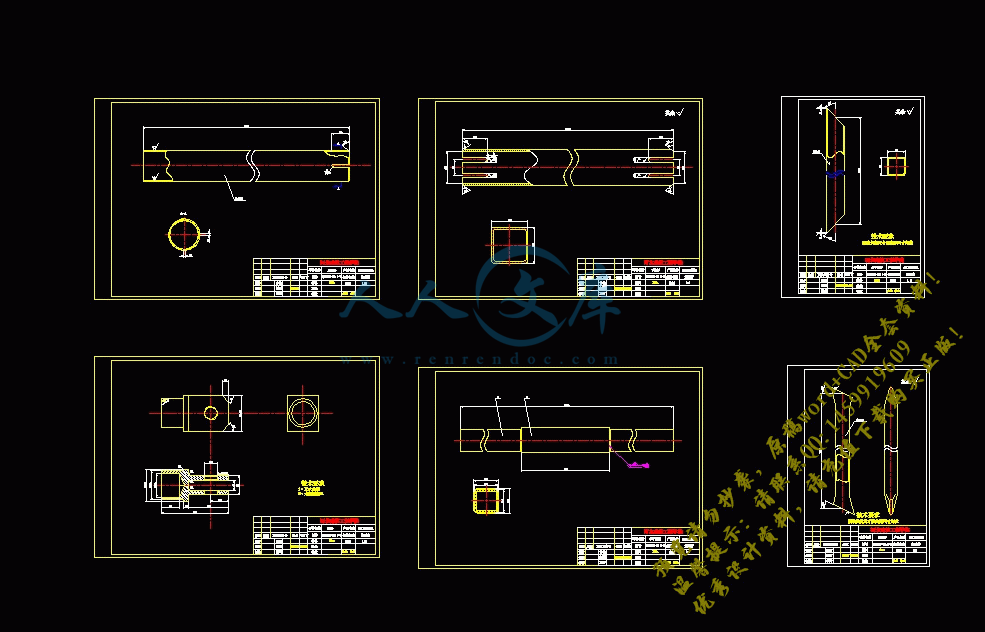



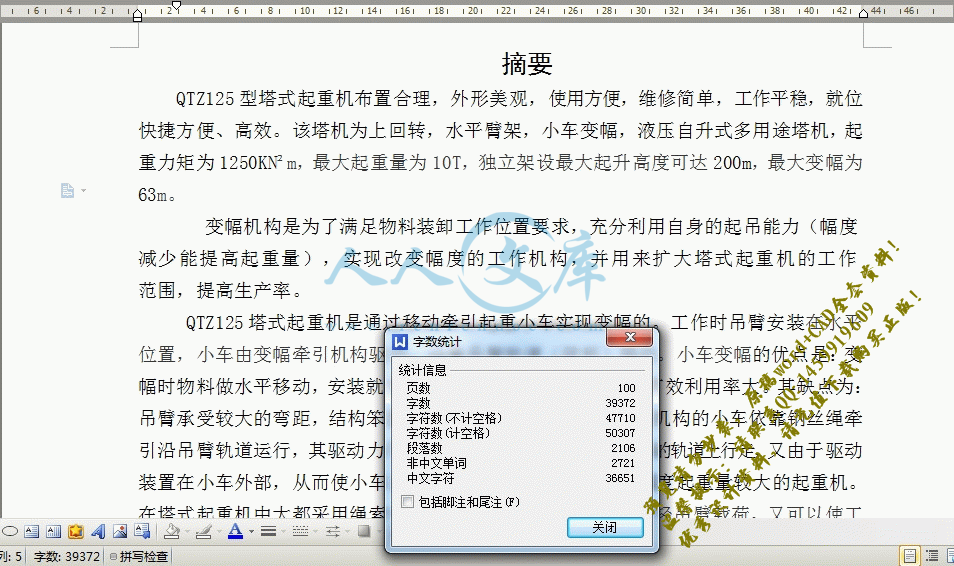
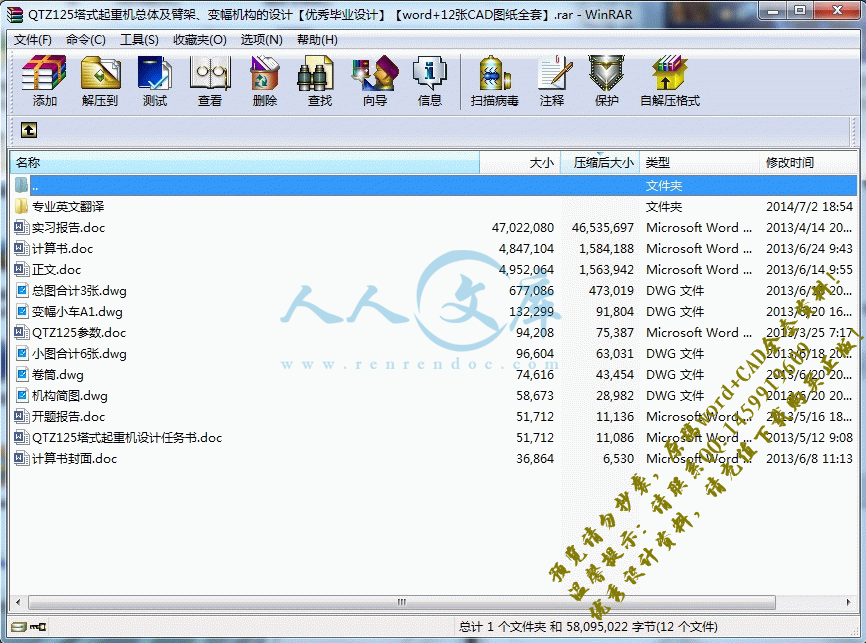