MG700-WD型采煤机截割部的设计【优秀毕业设计】【word+2张CAD图纸全套】
【55页@正文10300字】【详情如下】【需要咨询购买全套设计请加QQ1459919609】.bat
截割部总装图.dwg
正文.doc
行星减速器.dwg
摘 要
本次设计的主要目的是对MG700-WD型采煤机截割部的设计计算。MG700-WD型采煤机截割部主要是由四级齿轮传动组成,截割部电机放在摇臂内横向布置,电动机输出的动力经由三级直齿圆柱齿轮和行星轮系的传动,最后驱动滚筒旋转。
本此设计结果对截割部的轴、传动齿轮、轴承和联接用的花键等部件进行了设计计算、强度校核和选用,主要部件的设计计算和强度校核进行了叙述和介绍。本次设计认真完成了对MG700-WD型采煤机截割部设计。
关键词:截割部;行星轮系;传动齿轮
Abstract
The main purpose of this design is the MG700-WD Shearer Calculation of cutting unit。MG700-WD shearer cutting unit is mainly composed of four-gear transmission,Department of Motor cutting in on the arm horizontal layout,Motor output power by three spur gear and planetary gear drive,Finally driven rotating drum。
The results of this design of cutting unit shaft, transmission gears, bearings and spline connection with such parts of the design calculations, checking and selection intensity,The main components of the design and strength check calculation was described and introduced。This design carefully completed MG700-WD shearer cutting unit design。
Keyword: cutting department; planetary gear; transmission geart
目 录
摘 要.I
AbstractII
第1章 绪论1
1.1 研究目的和意义1
1.2 国内外发展情况1
第2章 方案比较论证4
2.1 方案对比4
2.2 研究设计方案6
第3章 截割部的设计及计算7
3.1 摇臂尺寸的确定及电动机的规格7
3.2 总传动比及传动比的分配8
3.2.1 总传动比的确定8
3.2.2 传动比的分配8
3.3 截割部传动计算10
3.3.1 各级传动转速、功率、转矩10
3.3.2 截割部齿轮设计计算12
3.3.3 截割部行星机构的设计计算27
3.3.4 轴的设计及校核36
3.3.5 轴承的寿命校核45
3.3.6 花键的强度校核46
结 论48
致 谢49
参考文献50
CONTENTS
AbstractI
Chapter 1 Introduction1
1.1 The purpose and significance1
1.2 Domestic and international developments.1
Chapter 2 Program comparisons4
2.1 Program comparison4
2.2 Research and design programs.6
Chapter 3 Cutting on the design and calculation7
3.1 Rocker arm and the motor to determine the size
Specifications7
3.2 Domestic and international developments8
3.2.1 Determination of the total transmission
Ratio..8
3.2.2 The allocation of transmission ratio.8
3.3 Calculation of cutting unit drive10
3.3.1 Levels of transmission speed, power,
Torque10
3.3.2 Cutting Unit Gear Design12
3.3.3 Cutting the Department of Design and
calculation of planetary bodies27
3.3.4 Axis Design and Verification36
3.3.5 Check bearing life45
3.3.6 Spline strength check.46
Conclusions48
Acknowledgements49
References.50
第1章 绪论
1.1 采煤机截割部研究目的和意义
随着采煤机械化的发展,采煤机是现在最主要的采煤机械,本次设计是对中厚煤层采煤机截割部进行设计,其目的在于更加详细的掌握了采煤机截割部传动系统,从而来更好的优化采煤机截割部的传动系统,提高工作效率并且能够对于发现的问题得到很好的解决,锻炼了自己发现问题、分析问题、解决问题的能力,为以后的实际工作打下了良好的基础。煤机截割部作为采煤机的主体,其结构和各部件的选择直接影响到采煤机的工作效率和采煤量,所以说对采煤机截割部的设计是非常重要的。
1.2 国内外发展情况
世界上第1 台采煤机是原苏联于1952 年生产并开始使用的,我国于1952 年购进并使用,与此同时,鸡西煤矿机械厂即开始进行仿制工作,于1954年制造出我国第1 台深截式采煤机,即顿巴斯- 1型采煤康拜因,随后批量生产。在顿巴斯- 1 型采煤康拜因的基础上,经过研究、改进和完善,设计制造了多种型式的采煤康拜因,这一时期的采煤机称为中国第1 代采煤机[1]。
20 世纪60 年代初,在顿巴斯- 1 型采煤康拜因的基础上,我国开始自行研制生产采煤机,1964 年生产出MLQ - 64 型,1968 年生产出MLQ1 - 80 型浅截式单滚筒采煤机,成为我国第2 代采煤机。我国第2 代采煤机的特点是截割部滚筒采用摇臂调高,牵引机构也为钢丝绳牵引,通过应用证明,采用钢丝绳牵引,绳筒磨损严重,使用寿命短,同时牵引力较小,容易拉断而导致伤人和机器下滑事故。该类型采煤机采用了液压传动,具有无级调速和过载保护等特点[2]。
我国于20 世纪60 年代末70 年代初开始研制第3 代采煤机即双滚筒采煤机。1975 年生产的MLS3 - 170 型采煤机,实现了滚筒采煤机由单滚筒向双滚筒的飞跃。MLS3 - 170 型采煤机的2 个可调高滚筒放在采煤机的两端,利用摇臂调高。牵引机构采用圆环链牵引,提高了牵引力,但不适应大倾角采煤[3]。
1983 年研制生产的大功率无链牵引双滚筒采煤机,采用了三头螺旋滚筒, 滚筒转速有所降低; 牵引机构采用齿轮- 销轨式, 传动平稳, 消除了链牵引的缺点,机器的使用寿命延长,增设了副牵引部和可靠的液压制动装置,可用于大倾角(40~50°) 煤层而不需要设防滑安全绞车,提高了工作效率,加大了生产能力。MG132P320 - W新型液压牵引采煤机是由泰山建能公司、煤炭科学研究总院、新汶矿业集团联合研制完成的。该采煤机采用滚筒式采煤机发展趋势的多电机横向布置,液压牵引系统打破常规,采煤机牵引部泵箱把长期使用的“湿腔”布置分离液压元件改为“干腔”布置,实现了采煤机液压系统的创新。该机在同类采煤机设计中达到了国内先进水平[4]。
国内于1976 年研制出第1 台电牵引采煤机。1991 年,由煤炭科学研究总院上海分院与波兰科玛克公司合作,研制成功我国第1 台采用交流变频调速的MG344 - PWD 型薄煤层强力爬底板电牵引采煤机,性能良好,电牵引采煤机成为我国第4 代采煤机。2005 年煤炭科学研究总院上海分院又开发出总装机功率达1 815 kW的大功率采煤机。随后,更大功率的电牵引采煤机MG900/ 2215 - GWD 也问世,该型采煤机的控制达到了国际先进水平,是目前国内功率最大的采煤机。如果采用长摇臂,最大采高可达到创记录的6 m ,该型采煤机完全能够满足国内煤矿高产高效工作面的生产需要[5]。
20世纪40年代初,英国和苏联相继研制出来了链式采煤机。这种采煤机是用截链落煤,在截链上安装有被称为截齿的专用截煤工具,其工作效率低。同时德国研制出了用刨削方式落煤的刨煤机。50年代初,英国和德国相继研制出了滚筒采煤机,在这种采煤机上安装有截煤滚筒,这是一种圆筒形部件,其上装有截齿,用截煤滚筒实现装煤和落煤。这种采煤机与可弯曲输送机配套,奠定了煤炭开采机械化的基础。这种采煤机的主要缺点有二,其一是截煤滚筒的安装高度不能在使用中调整,对煤层厚度及其变化适应性差;其二是把圆筒形截煤滚筒改进成螺旋叶片式截煤滚筒,即螺旋滚筒,极大地提高了装煤效果。这两项关键的改进是滚筒式采煤机成为现代化采煤机械的基础[6]。
可提高螺旋滚筒采煤机或刨煤机与液压支架和可弯曲输送机配套,构成综合机械化采煤设备,使煤炭生产进入高产、高效、安全和可靠的现代化发展阶段。从此,综合机械化采煤机采煤设备成为各国地下开采煤矿的发展方向。自70年代以来,综合机械化采煤设备朝着大功率、遥控、遥测方向发展,其性能日益完善,生产率和可靠性进一步提高。近年来,由于长壁综采的发展,采煤机开采的产量有所回落,但 1999 年产煤量为 2.21 亿吨,仍占井工煤炭总产量的 53%。在美国,采煤机掘进平均班进尺 60 米,日产煤 2000 吨,有些高产工作面日进尺可达 100 米,月产量达 10 万吨.英国井工开采一直以长壁为主,巷道掘进主要靠悬臂式掘进机,但自从 80 年代后期使用连续采煤机开采取得良好的效益以来,用采煤机掘进已经成为英国煤巷掘进的主要方法之一,约占总掘进量的65%。南非和澳大利亚两国根据各自的煤层地质条件,在传统的房柱式开采基础上成功地开发出了旺格维利和西格玛两种短壁采煤方法],扩大了采煤机的应用范围,提高了资源回收率[7]。其中,南非全国约有 230 多台采煤机用于房柱式开采,其产量约占井工总产量的90%[.德国使用采煤机在海底煤层开采已有 40 多年的历史,效果显著,其中有 5 个工作面一直保持 200 万吨的年产量。另外,印度和加拿大等国家使用采煤机进行短壁开采,也取得了很好的经济效益[7]
参考文献
1 李森. 煤层高效开采技术. 大众科学,2007
2 员创治.陈永峰.潘晓恒. 滚筒采煤机在我国的发展前景. 煤矿开采,1996
3 戴绍诚,李芬,田小明. 滚筒采煤机在神府矿区的应用前景. 煤矿设计,1996
4 冯冠学.滚筒采煤机开采工艺在上湾矿井中的使用煤炭工程. 煤炭工程,2002
5 浦国树,张世洪,陈建文. 滚筒式采煤机的技术现状和发展趋势. 煤矿机
电,2003
6 R·希尔,陈雁译. 适用于所有开采的机器—连续采煤机. 中国煤炭,1999
7 方莜萍.内孔滚压加工方法的研究.农业机械学报,1997,第28卷第3期.
8 祁威.滚筒采煤机施工煤平巷经济效益浅析.煤矿开采, 1999
9 成大先. 机械设计手册. 化学工业出版社,2004
10 孙桓,陈作模,葛文杰 .机械原理.高等教育出版社,2005
11 饶振纲. 行星齿轮传动设计. 化学工业出版社, 2003
12 王洪欣. 机械设计工程学.北京:中国矿业大学出版社,2006
13 王文斌. 机械设计手册.北京:机械工业出版社,2004
14 叶克明. 齿轮手册.北京:机械工业出版社,1990
15 徐灏. 新编机械设计师手册. 北京:机械工业出版社,1994
16 张树森. 机械制造工程学.东北大学出版社.1994:52-63
17 于慕松.采煤机.中国矿业大学出版社.2001:3-8
18 濮良贵.机械零件.北京人民教育出版社,1992:98-101
19 程居山. 矿山机械. 中国矿业大学出版社2005(8):59-63
20 李昌熙,沈立山,高荣. 采煤机. 北京:机械工业出版社,1988
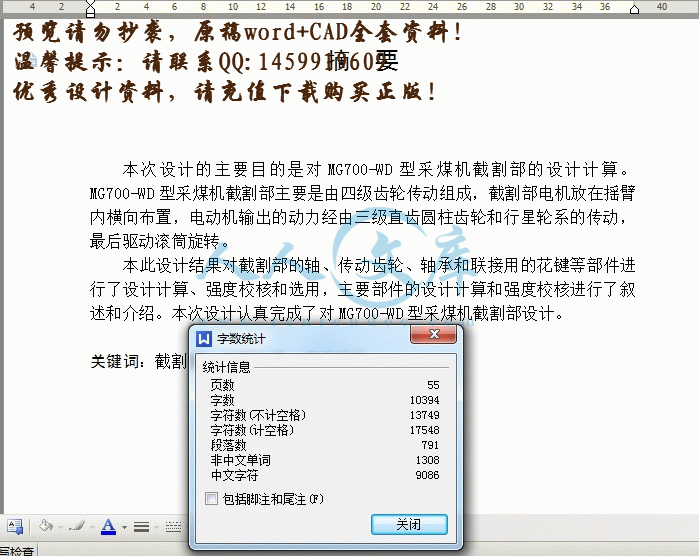

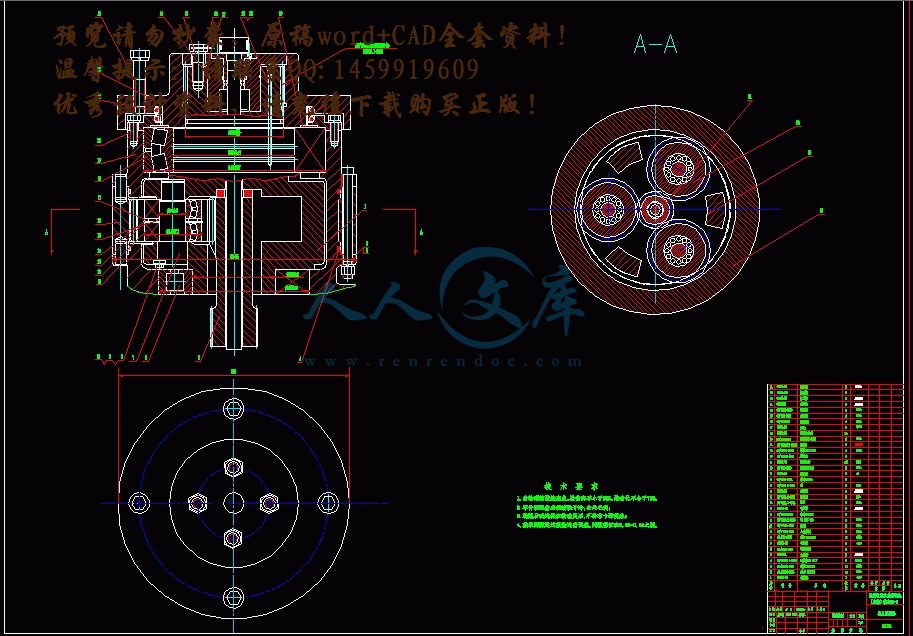
