小型电动助力播种机的设计【优秀】【word+XX张CAD图纸全套】【农用机械】【毕业设计】
【带任务书+开题报告+外文翻译+实习报告】【68页@正文31300字】【详情如下】【需要咨询购买全套设计请加QQ1459919609】
任务书.doc
前开沟器(2#).dwg
前飞轮套筒(4#).fdwg.dwg
后开沟器(2#).dwg
后机架(2#).dwg
后飞轮套筒(4#).fdwg.dwg
地轮轴(2#).dwg
外文原文.pdf
外文资料翻译封面及格式要求.doc
实习报告.doc
封面.docx
开沟器固定架(3#).dwg
摘要.doc
播种机开题报告.doc
支撑架3#.dwg
毕业设计成果盒统一粘贴封面.doc
沟深调节器4#).dwg
目录.doc
离合链轮4#.fdwg.dwg
装配图0#.dwg
覆土器(3#).dwg
计算书.doc
译文.doc
资料
车把(2#).dwg
轴承座4#.dwg
轴承盖4#.dwg
毕业设计(论文)任务书
名称小型电动助力播种机设计
发任务书日期: 2012年3月 19 日
1、本毕业设计(论文)课题应达到的目的:
1)培养学生综合应用所学理论知识和技能,分析和解决机械工程实际问题的能力,熟悉生产技术工作的一般程序和方法。
2)培养学生懂得工程技术工作所必须的全局观念、生产观念和经济观念,树立正确的设计思想和严肃认真的工作作风。
3)培养学生调查研究,查阅技术言文献、资料、手册,进行工程计算、图样绘制及编写技术文件的能力。
2、本毕业设计(论文)课题任务的内容和要求(包括原始数据、技术要求、工作要求等):
本毕业设计课题任务的内容:电动助力式小型播种机以人力和电动机(48V直流)动力相结合,主要用于农户田间播种和设施种植播种(以小麦、玉米为主),增加部分装置也可用于施肥、耙磨、除草等田间作业。技术要求:播种深度20~60mm连续可调,播种行距200~500mm连续可调,播种穴距0~500mm可调,种子破碎率和播种均匀度符合国家标准,工作要求:最大生产率为10亩/日。该机结构主要由机架、动力装置、操纵机构、开沟器、镇压轮、播种量调节器和料斗等组成。本设计要求达到结构合理、生产成本低、能耗小,效率高,满足工作性能,而且操作方便的目的。设计成果要求设计图纸和设计计算书各1套,并进行计算机仿真样机和优化设计。
3、对本毕业设计(论文)课题成果的要求(包括图表、实物等硬件要求):
设计说明书不少于2万字;工程绘图量不少于折合成图幅为A0号的图纸3张;用计算机进行设计、计算与绘图一般不少于2/3;并进行计算机仿真样机和优化设计。查阅文献15篇以上,翻译与课题有关的外文资料,译文字数不少于3000字。
4、主要参考文献
[1] 董刚 李建功 潘凤章主编.机械设计(第三版)北京:机械工业出版社1998
[2]成大先主编.械设计图册 北京:化学工业出版社 1997
[3]蔡春源主编.机电液设计手册 北京:机械工业出版社 1997
[4]徐灏主编.新编机械设计师手册 北京:机械工业出版社 1995
[5]朱喜林 张代治主编.机电一体化设计基础 北京:科学出版社 2004
[6]求是科技编著.PLC应用开发技术与工程实践 北京:人民邮电出版社 2005
[7]雷天觉主编.液压工程手册 北京:机械工业出版社 1990
[8]孙桓 陈作模主编.机械原理(第六版)北京:高等教育出版社 2001
[9]王爱玲主编.现代数控机床 北京:国防工业出版社 2003
[10]赵如福主编.金属机械加工人员手册(第三版)上海科学技术出版社 1990
[11]齐麟 张亚雄 黎上威 董学朱 胡松春编著 蜗杆传动设计(上、下册)北京:机械工业出版社 1987
[12]齿轮手册编委会编著 齿轮手册(上、下册) 北京:机械工业出版社 1990
[13]《现代机械传动手册》编委会编著 现代机械传动手册 北京:机械工业出版社 1995
[14]郭爱莲主编.新编机械工程技术手册 经济日报出版社 1991
[15]杨公源主编.机电控制技术及应用 北京:电子工业出版社 2005
[16]袁任光编著.可编程序控制器选用手册 北京:机械工业出版社 2002
[17]饶振纲 王勇卫编著.滚珠丝杠副及自锁装置 北京:国防工业出版社 1990
[18]陆玉 何在洲 佟延伟主编.机械设计课程设计(第三版)北京:机械工业出版社 1999
[19]数字化手册系列(软件版)编写委员会编著.机械设计手册(软件版)R2.0北京:机械工业出版社 1999
5、本毕业设计(论文)课题工作进度计划:
起 迄 日 期工 作 内 容
3.19~3.25
3.26~4.08
4.09~5.20
5.21~6.17
6.18~6.24
完成毕业实习报告,开题报告。
设计任务分析与总体方案的确定。
实施设计、计算、绘图、试验。
进行计算机仿真样机和优化设计,并编写设计说明书。
毕业设计(论文)答辩及成绩评定。
摘要
随着近来温室大棚的发展以及环保发展意识的日益增强,小型机的需求就显得更为重要,尤其以电力为动力装置的机械。然而目前广泛应用的播种机是以内燃机及人力为动力装置。本设计电动小型播种机与传统的播种机相比.新颖之处在于播种机完全采用电力为动力装置,从而改善了人们在田间作业时的工作环境,况且更符合环保发展的观点。
本设计主要用于农户田间播种和设施种植播种.增加部分装置也可用于施肥、耙磨、除草等田间作业。详细介绍了播种机的结构组成以及各部件的形式、要求以及功用。详细介绍了电动小型播种机动力装置及各部件要求,包括播种机的动力选择、机械传动的选择及尺寸、排种轮设计、排肥轮的设计、开沟器的设计、轴的设计、链轮的设计、其他的各部件设计以及播种机的工作要求、播种前的准备及播种机的使用等。在设计中考虑播种深度连续可调、播种行距连续可调、播种穴距可调、种子破碎率和播种均匀度符合国家标准。设计中在考虑实用的同时,兼顾经济节约,从而达到结构合理、生产成本低、能耗小、效率高,而且操作方便的目的。
关键词:电动 小型 播种机
Abstract
With the development of the greenhouse and the consiousness of protecting our ervironment ,boosting up ,the apply of the powy machine becomes more important ,especially the machine with electric power .but at the present time the seeding-machine which is adopted abroadly is drived ba gad engine or man power .this kind of minitype seeding-machine knows from the conventional seeding-machine .Its novel aspect is its drive set which are drived by electric power completly ,so they will improve the work condition ,and accord with euthenics .
This design is applied mostly with the farms of the farmers ,they can also used to fertilize、abrade、get rid of grass and so on ,when we incress some equipment .My design introduce the structure of the seeding-machine and the types of many parts 、some request an fuction .My design introduce the drive equipment of the machine and the types of many parts 、request and fuction .My design also introduce the drive equipment of the machine and the request of the parts which consist of the selecting of the power 、the size 、the design of the axial 、chain wheel 、some other parts and so on .We must consider suiting well of the depth 、the row spacing 、the distance of scoop and the rate of seeds breaking up when seeding .In my design ,while thinking over applied ,I give attention to saving econmy ,consequently achieve structure in reason 、the cost of produce lowness 、the cost of power lowness 、the effidiency highness and convenient when operating .
KEY WORDS :electromotion minitype seeding-machine
目录
第1章 前言1
1.1播种机的常识和技术现状1
1.2播种方式及常见播种类型3
1.2.1条播3
1.2.2穴播4
1.2.3撒播4
1.2.4精密播种4
1.2.5联合作业机和免耕播种5
1.3播种工作过程和机械构造5
1.3.1工作过程5
1.3.2机械构造6
1.4播种机械的发展趋势7
第2章 总体设计9
2.1 概述9
2.2 设计任务10
2.3 设计目的10
2.4 动力方案选择10
2.5 设计题目分析及设计思想12
2.6 设计主参数及机构类型确定12
2.6.1工作速度12
2.6.2播量的确定13
2.6.3种、肥箱的容积13
2.6.4机架设计14
2.6.5工作幅度14
2.6.6 排种、排肥机构设计14
2.6.7开沟器设计18
2.6.8覆土器设计22
2.6.9镇压轮设计23
2.6.10 地轮设计23
第3章 传动设计及播种技术措施25
3.1传动原理简图和动力传递路线图25
3.1.1传动原理简图25
3.1.2动力传动路线图25
3.2传动原理25
3.3技术措施26
3.3.1播种均匀性和各行排量一致性措施26
3.3.2降低破种率措施27
3.3.3种肥同播时,肥料的利用率27
第4章 零部件设计28
4.1种箱及肥箱设计28
4.2开沟器设计及校核29
4.3排种器31
4.4地轮参数确定32
4.4.1轮子直径和轮辋宽度的确定32
4.4.2轮子滚动阻力计算32
4.5电机和电瓶选择及链轮设计33
4.5.1电机总功率确定33
4.5.2电动机及电瓶的选择34
4.5.3传动比的确定35
4.5.4链轮选择及设计计算36
4.6地轮轴设计40
4.7键的校核47
4.8销的校核48
4.9轴承的校核48
第5章 电气控制系统设计49
5.1电气系统设计原则49
5.2电气元件的选择49
第6章 播种机使用52
6.1播种量调整52
6.2实际操作说明53
6.2.1播种作业前准备53
6.2.2播种机的试播及作业55
6.2.3播种机的保养与保管56
6.2.4播种质量检查56
第7章 毕业设计小结59
参考文献61
第1章 前言
1.1 播种机的常识和技术现状
以作物种子为播种对象的机械称为种植机械,即播种机械。农业是关系国计民生的基础产业,而播种作业是农业生产过程中六大环节之一,播种机械化是农业机械化过程中最为复杂,也是最为重要的工作。播种机械所面对的播种方式、作物种类、品种变化繁多,这就需要播种机械有较强的适应性并且能满足不同种植要求的工作性能。
播种机一般由机架、牵引或悬挂装置、种子箱、排种器、传动装置、输种管、开沟器、划行器、行走轮和覆土镇压装置等组成。其中影响播种质量的主要是排种装置和开沟器。
1.机械播种的农业技术要求:
1)播量符合要求且准确,排种(排肥)均匀稳定,穴距及每穴粒数均匀。
2)播深符合要求且均匀一致,种子应播在湿土上,用湿土覆盖,无露籽现象,覆土均匀,干早地区播后应同时镇压,以利保墒。
3)播行直,行距一致,地头整齐,不重不漏。
4)尽量采用联合作业。
2.播种机的性能指标:排量稳定性、各行排量一致性、排种均匀性和播种均匀性、穴粒数合格率、粒距合格率、播深稳定性、种子破损率。
3.播种机的分类:
播种机的种类很多,一般可按下列方法进行分类。
1)按播种方式分为撒播机、条播机、穴播机和精密播种机。
2)按适应作物分为谷物播种机、中耕作物播种机及其他作物播种机。
3)按联合作业分为施肥播种机、播种中耕通用机、旋耕播种机、旋耕铺膜播种机。
4)按动力联接方式分为牵引式、悬挂式和半悬挂式。
5)按排种原理分为机械式、气力式和离心式播种机。
公元前1世纪,中国已推广使用耧,这是世界上最早的条播机具,至今仍在北方旱作区广泛应用(如图1—1)。
图1—1三耧车
欧洲第一台播种机于1636年在希腊制成。1830年,俄国人在畜力多铧犁上加装播种装置制成犁播机。英、美等国在1860年以后开始大量生产畜力谷物条播机。20世纪以后相继出现了牵引和悬挂式谷物条播机,以及运用气力排种的播种机。1958年挪威出现第一台离心式播种机,50年代以后逐步发展各种精密播种机(如图1—2)。
图1—2气吸式播种机
中国在20世纪50年代从国外引进谷物条播机、棉花播种机等,60年代先后研制成功悬挂式谷物播种机(如图1-3)、离心式播种机、通用机架播种机和气吸式播种机等多种机型,并研制成功了磨纹式排种器。到70年代,已形成播种中耕通用机和谷物联合播种机两个系列并投入生产。供谷物、中耕作物、牧草、蔬菜用的各种条播机和穴播机都已得到推广使用。与此同时,还研制成功了多种精密播种机。
图1—3 国内常见的谷物播种机
1.2 播种方式及常见播种类型
播种方式应根据作物品种和当地农业技术要求而定,并随农业生产的发展而发展。基本播种方式有:条播、穴播(点播)、撤播、精密播种、及联合作业播种机五种。
与播种方式对应,播种机主要有谷物条播机、玉米穴播机、棉花穴播机、牧草撒播机等。这几种机型的辅助部件基本相同,只是其核心工作部件——排种器有较大差异。
1.2.1条播:
按要求的行距、播深和播量将种子播成条行,称为条播。条播一般不计较种子粒距,只注意一定长度区段内的粒数。条播的作物便于进行中耕除草、追肥、喷药等田间管理工作,故应用广泛。条播根据作物生长习性不同,有窄行条播、宽带条播、宽窄行条播等不同形式。其条播机主要用于谷物、蔬菜、牧草等小粒种子的播种作业。
1.2.2穴播(点播):
按规定的行距、穴距、播深将种子定点播入土中,称为点播。在地上定点掘穴,将几粒种子成簇的播入种穴,称为穴播。这种播种方法可保证苗株在田间分布合理、间距均匀。较条播节省种子。成簇播种可以提高出苗能力。每穴可播 1粒或多粒种子,分别称单粒精播和多粒穴播。其穴播机主要用于玉米、棉花、甜菜、向日葵、豆类等需要中耕的作物,通常又称中耕作物播种机。
1.2.3撒播:
将种子按要求的播量撒布于地表,称为撒播。撒播时种子分布不太均匀,且不能完全被土覆盖,因出苗率低。常用的撒播机为离心式撒播机,附装在农用运输车的后部,由种子箱及其下方的一个高速旋转的撒布轮构成。撒布轮由运输车的地轮通过链条传动。种子由种子箱落到撒布轮上,在离心力作用下沿切线方向撒出,播幅可达8~12米,但作业粗放,种子不易播匀,且露于地表,易遭鸟兽啄食。撒播机也可用以施撒粉状或粒状肥料、石灰及其他物料。附装撒播装置也可安装在农用飞机上使用。
1.2.4精密播种:
以精确的播种量、株行距和深度,将种子播入土中,称为精密播种。具有节省种子、免除出苗后的间苗作业、使每株作物的营养面积均匀等优点。多为单粒穴播和精确控制每穴粒数的多粒穴播。一般在穴播机各类排种器的基础上改进而成。如改进窝眼轮排种器上孔型的形状和尺寸,使其只接受一粒种子并防止空穴;将排种器与开沟器直接连接或置于开沟器内以降低投种高度,控制种子下落速度,避免种子弹跳;在水平圆盘排种器上加装垂直圆盘式投种器,以改变投种方向和降低投种高度,避免种子位移;在双圆盘式开沟器上附装同位限深轮,以确保播种深度稳定。多粒精密穴播机是在排种器与开沟器之间加设成穴机构,使排种器排出的单粒种子在成穴机构内汇集成精确数量的种子群,然后播入种沟。此外,还研制了一些新的结构,如使用事先将单粒种子按一定间距固定的纸带播种,或使种子从一条垂直回转运动的环形橡胶或塑料制种带孔排入种沟等。
1.2.5联合作业和免耕播种:
如在谷物条播机上加设肥箱、排肥器和输肥管,即可在播种的同时施肥,称为联合作业和免耕播种。与土壤耕作、喷撒杀虫剂和除莠剂、铺塑料薄膜(地膜覆盖机械)等项作业联合组成的联合作业机,有的能一次完成土壤播前耕作、施种肥、土壤消毒、开排水沟、播种、施杀虫剂和除莠剂等项作业。免耕播种机是在前茬作物收获后的茬地上直接开出种沟播种,也称直接播种机或硬茬播种机,可防止土壤流失,节约能源,降低作业成本,多用于谷物、牧草和青饲玉米等作物的播种作业。
参考文献
【1】成大先主编.机械设计手册单行本 机械传动[M].北京:化学工业出版社.
【2】张光裕主编.工程机械底盘机构与设计[M](上册).北京:机械工业出版社,1986.
【3】沈鸿主编.机械工程手册[M] .北京:机械工业出版社,1982.
【4】成大先主编. 机械设计图册[M].北京: 化学工业出版社,1997.
【5】刘兴加编.播种机械[M].北京:农业出版社,1980.
【6】张德文等.精密播种机械[M].北京:农业出版社,1982.
【7】中国农业机械化科学研究院.农业机械设计手册[M].北京: 机械工业出版社,1988.
【8】辽宁省农牧业农业机械化局主编.播种机械[M].北京:农业出版社,1982.
【9】孙有亮主编.机械制造技术基础[M]. 北京:北京大学出版社,2009.
【10】东北农学院.农业机械学[M](理论与设计,上册). 北京:农业出版社,1961.
【11】朱喜林,张代治主编.机电一体化设计基础[M].北京: 科学出版社,2004.
【12】陆玉,冯立艳著.机械设计课程设计[M].北京:机械工业出版社,2006.
【13】李宝筏主编.农业机械[M].北京:中国农业出版社,2003.
【14】李海明主编.现代农业机械装备[M]. 北京:中国农业科学技术出版社,2006.
【15】刘景泉主编.农机使用手册[M].北京:人民交通出版社,2005.
【16】《现代机械传动手册》编委会. 现代机械传动手册[M].北京:机械工业出版社,1987.
【17】袁任光编著.可编程序控制器选用手册.北京:机械工业出版社,2002.
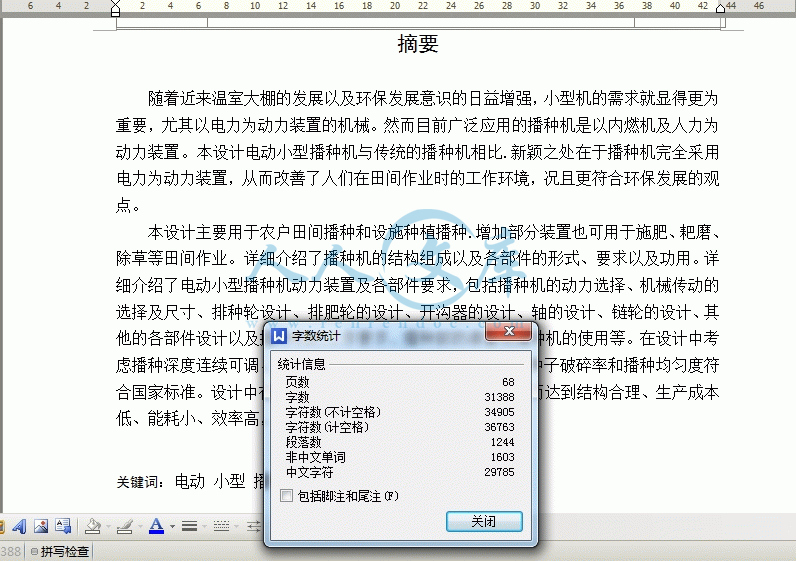
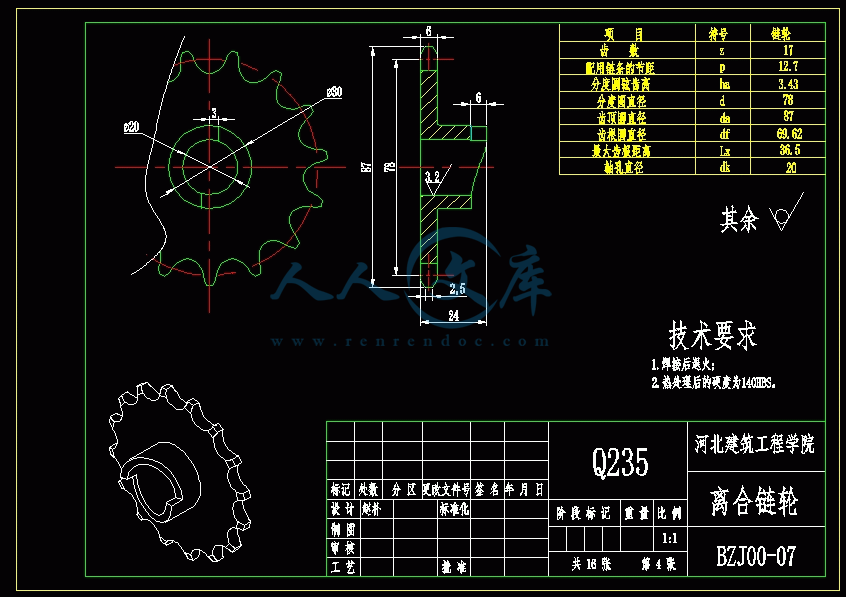
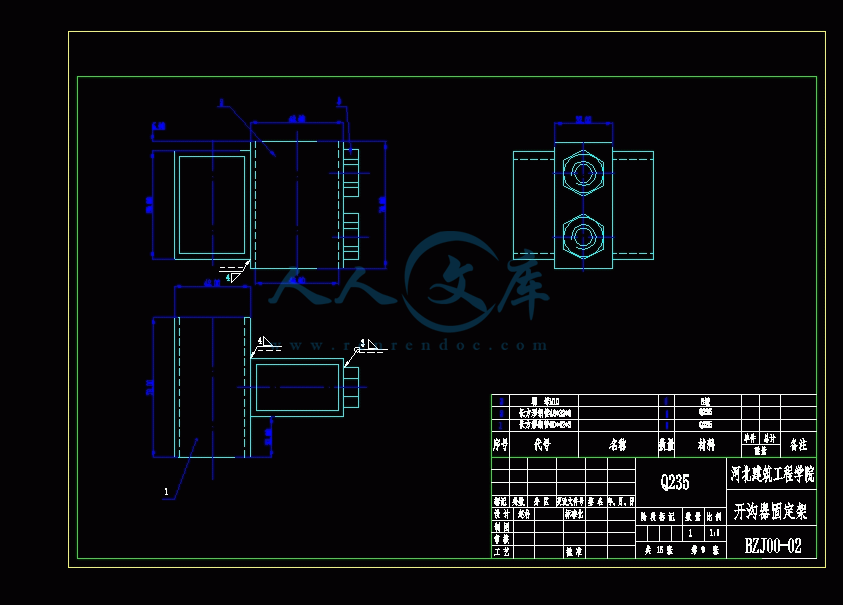

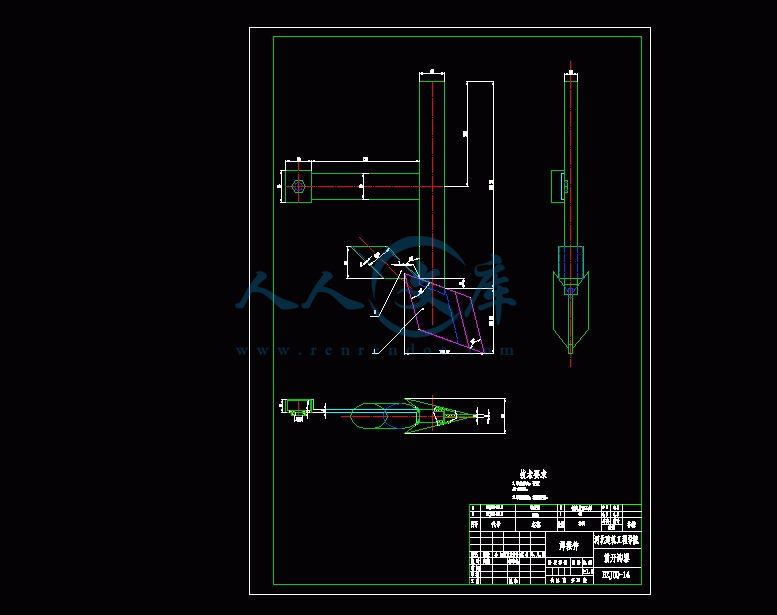
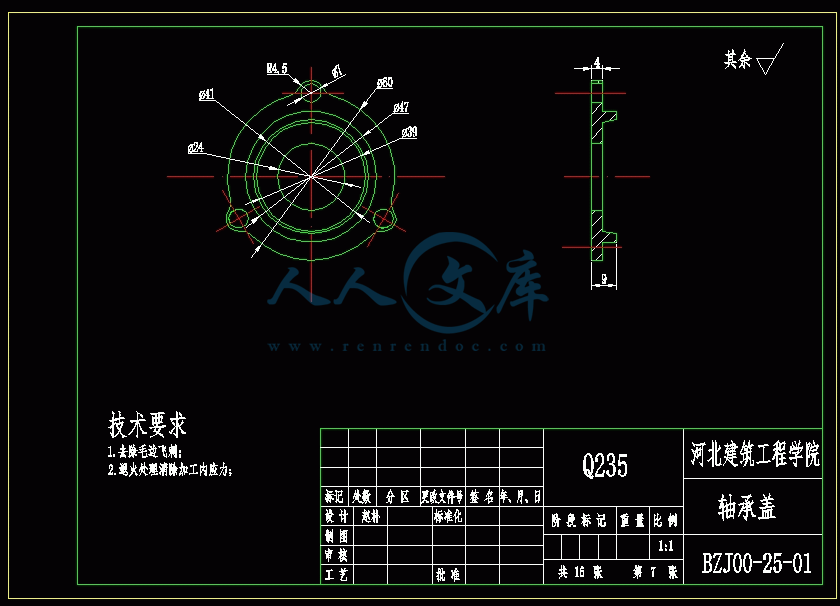
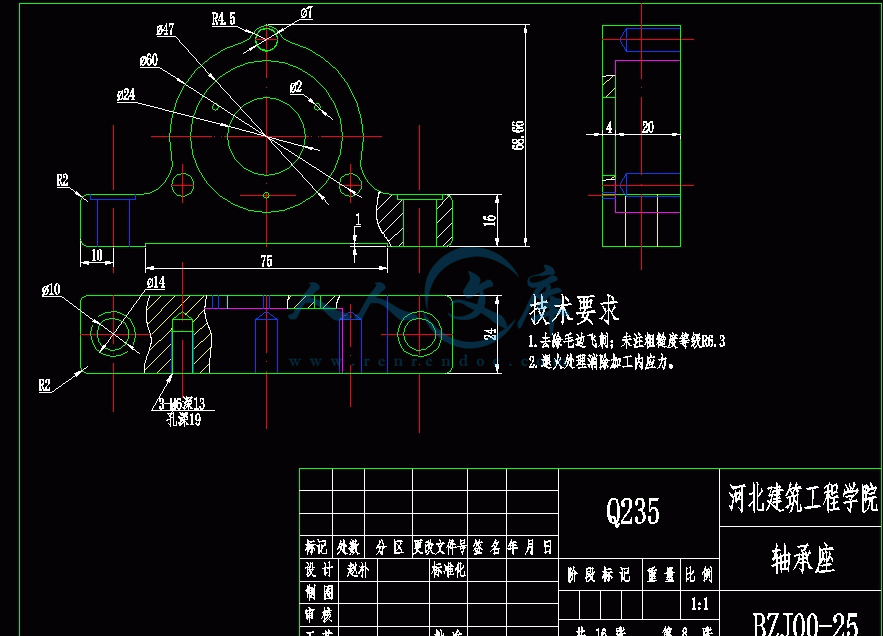

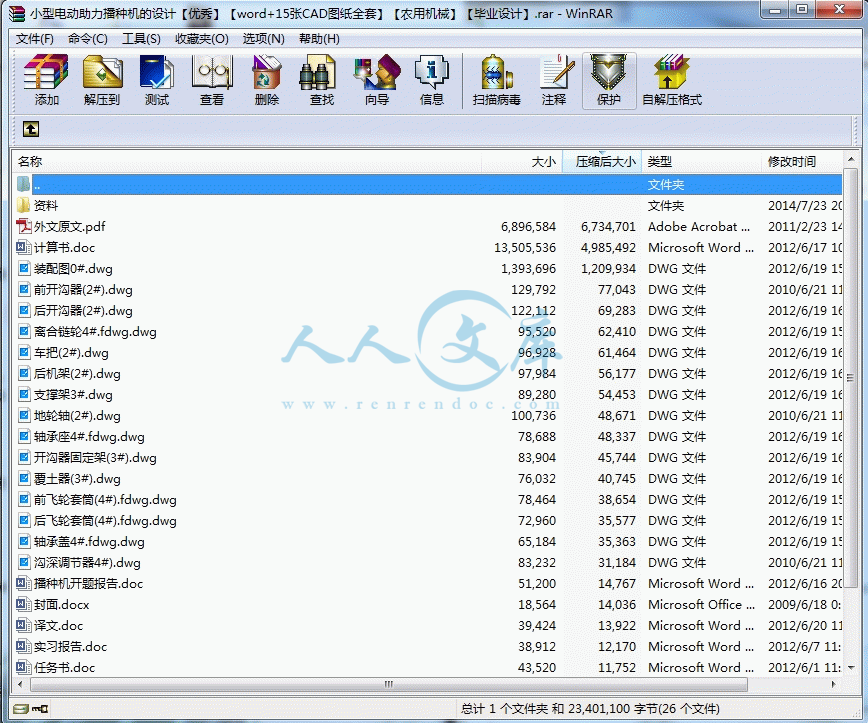
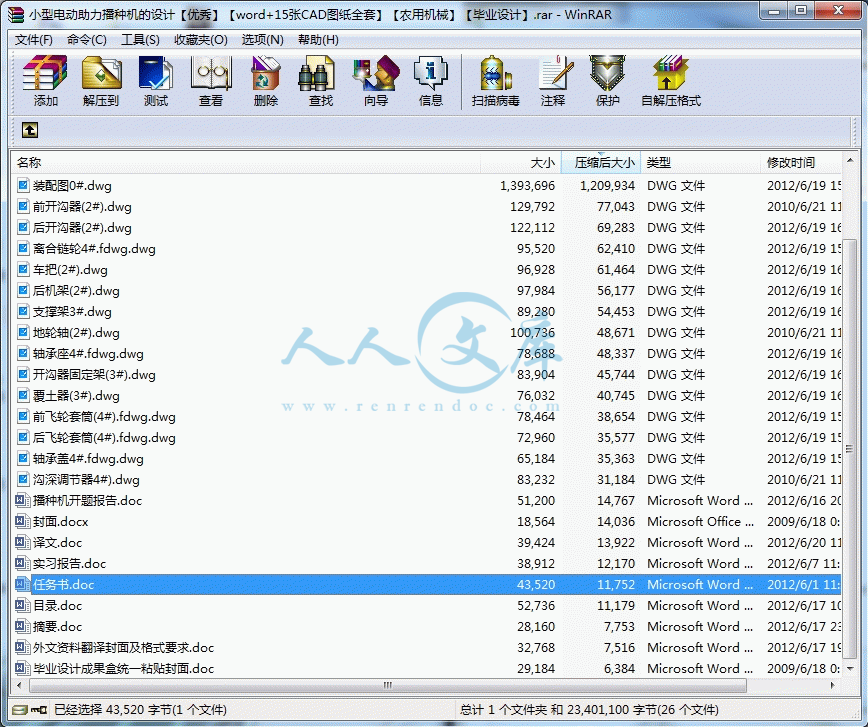

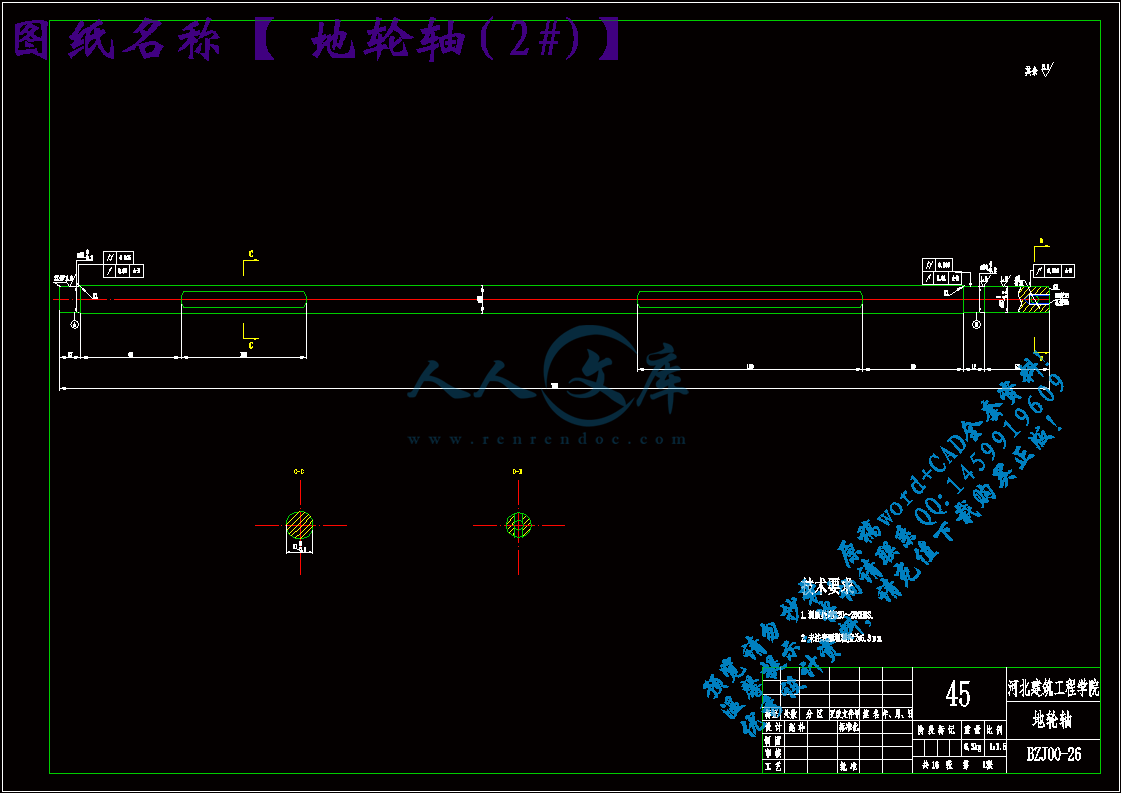




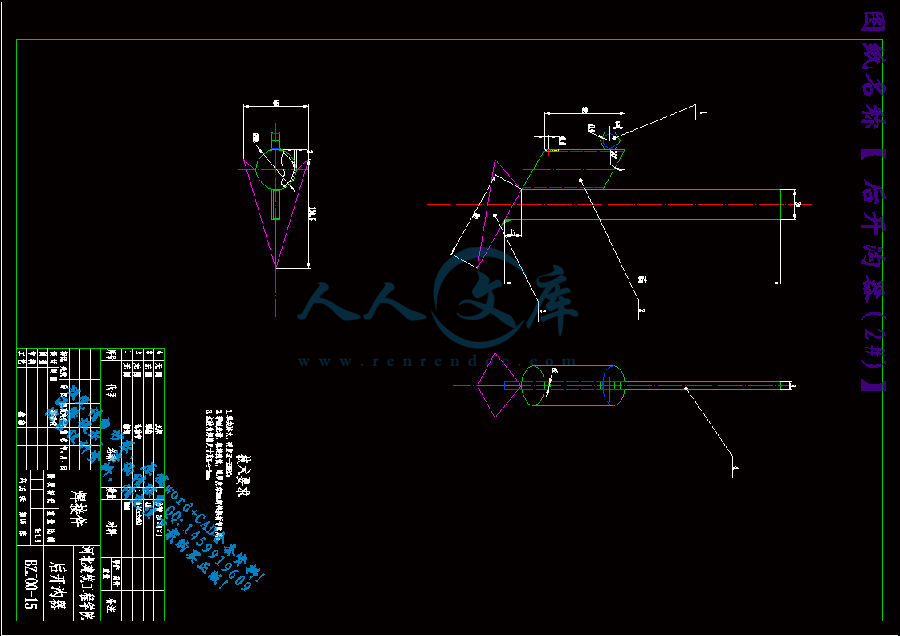
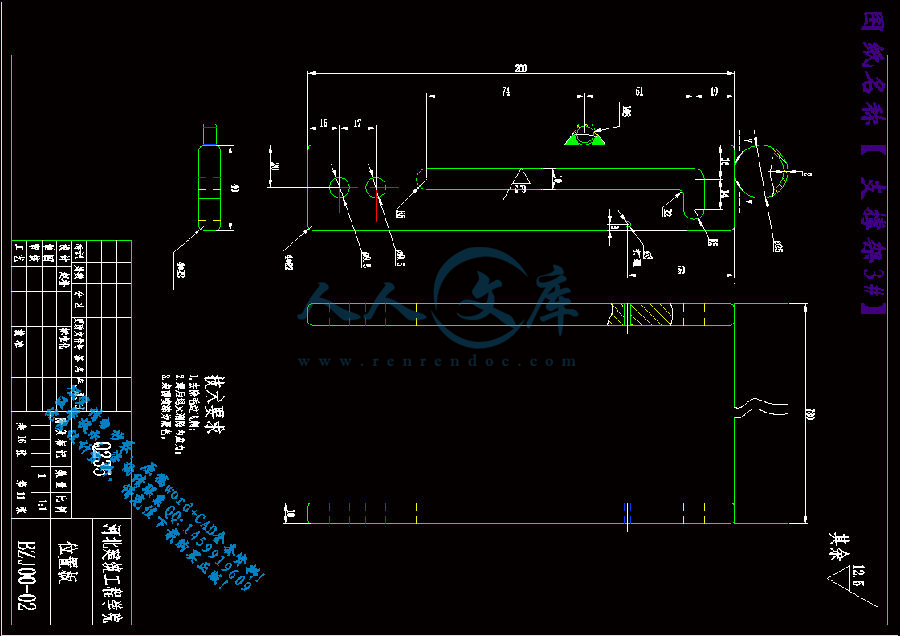