熔融沉积成型机床设计
36页 15000字数+说明书+任务书+12张CAD图纸【详情如下】
任务书.doc
传动轴.DWG
入嘴.DWG
喷嘴.DWG
垫片.DWG
外文翻译.doc
大齿轮.DWG
小齿轮.DWG
左顶板.DWG
挤压头左板.DWG
接头.DWG
滚珠丝杆.dwg
熔融沉积成型机床设计论文.doc
装配图.DWG
评阅表.doc
转接头.DWG
鉴定意见.doc


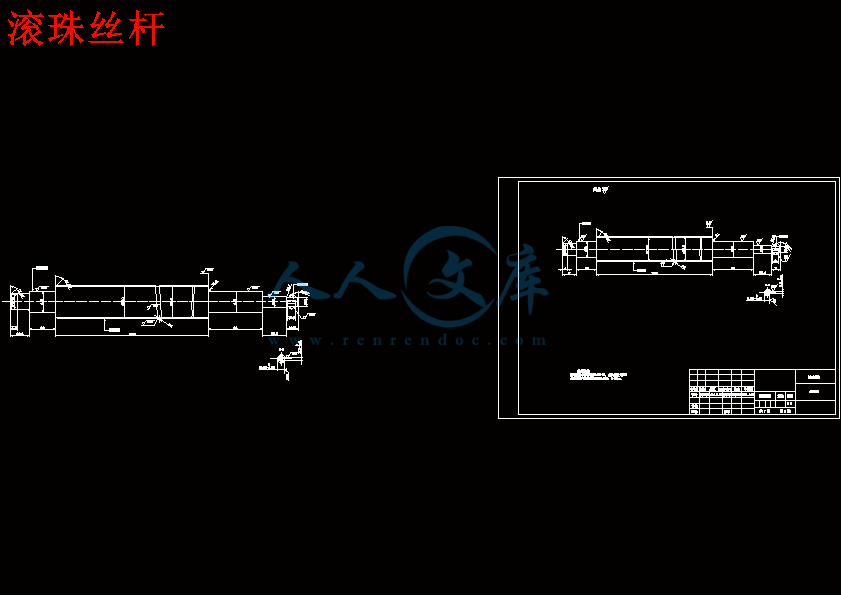

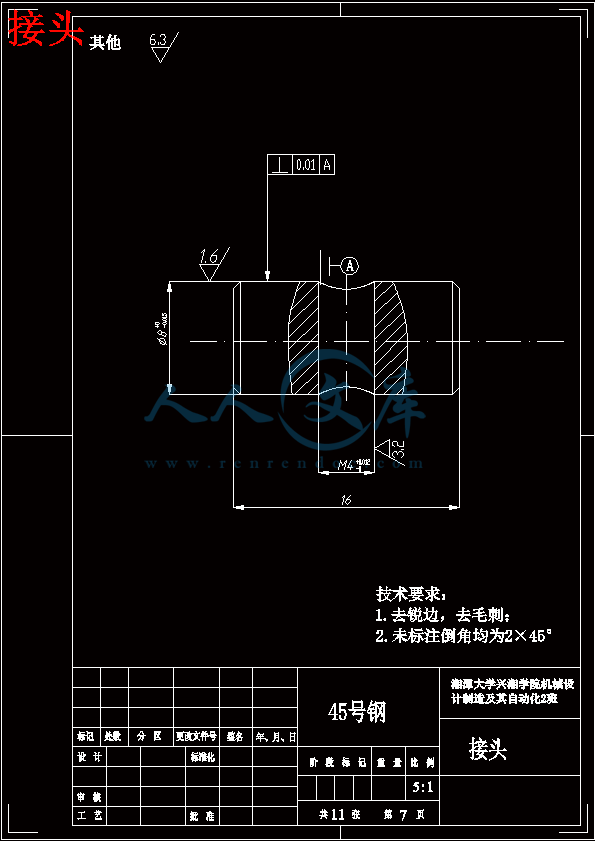
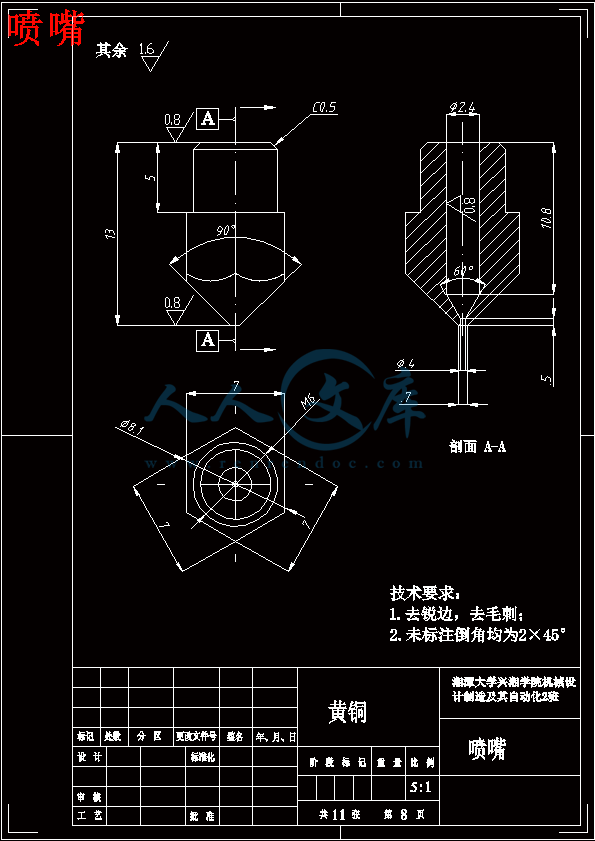

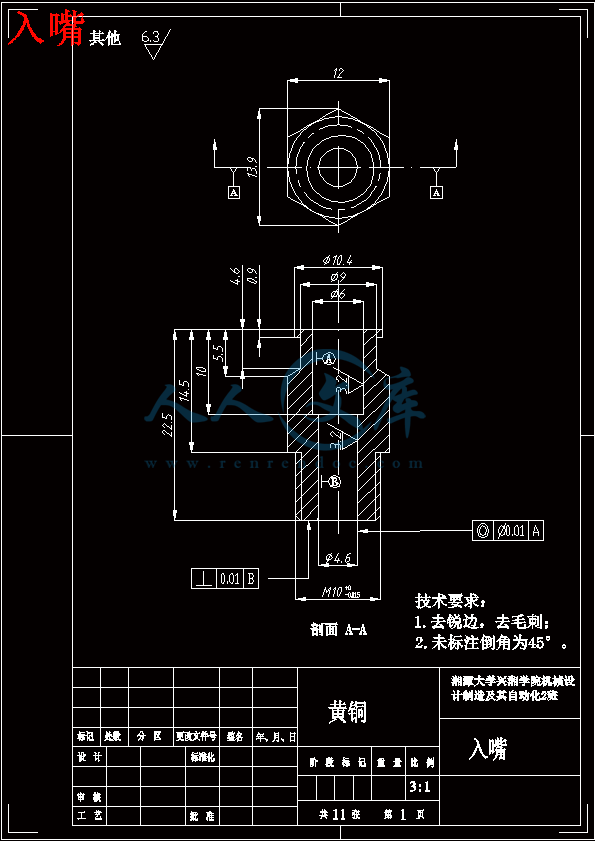

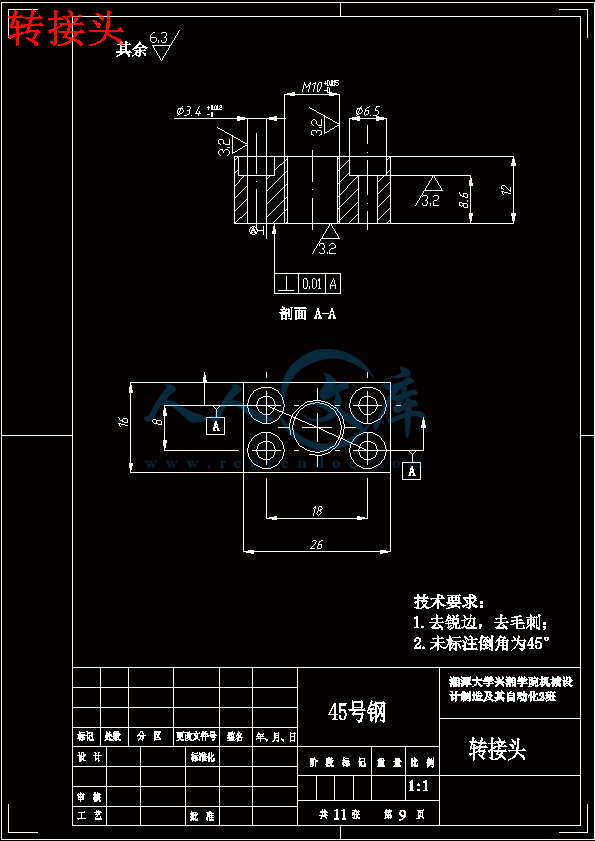
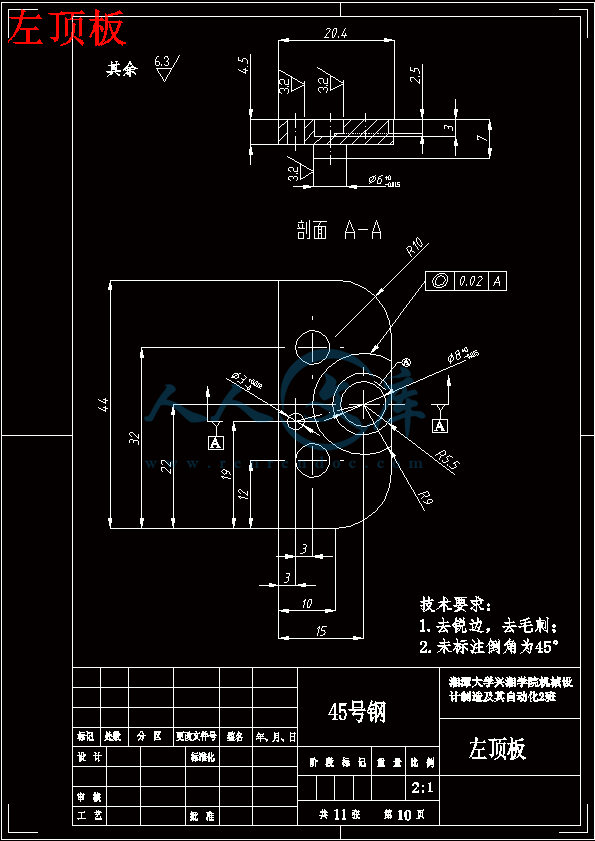
目录
1 绪论3
1.1 引言3
1.2 熔融沉积成型技术概论3
1.2.1 熔融沉积成型技术的特点4
1.2.2 熔融沉积成型技术 - 工艺过程5
1.2.3 熔融沉积成型技术的应用6
1.3 熔融沉积成型技术存在问题及发展方向7
1.3.1 熔融沉积成型技术的现状7
1.3.2 熔融沉积成型技术的发展方向8
2 总体方案及结构设计10
2.1 引言10
2.2 总体设计要求10
2.3 熔融沉积成型机床的结构运动方案11
3 电机方案的选择及选型13
3.1 电机方案的比较13
3.2 步进电机的选型13
4 挤出装置的设计18
4.1 结构尺寸的确定18
4.2 挤出机构的设计要求18
4.3 挤出装置的组成19
4.4 挤出机构齿轮组设计20
4.4.1 按齿面接触强度来设计20
4.4.2 按齿根弯曲强度设计23
4.5 轴设计26
4.5.1 作用在齿轮上的力26
4.5.2 初步确定大齿轮轴的最小直径26
4.5.3 轴的结构设计27
4.6 挤出机构流道口设计28
4.7 加热腔的设计30
4.7.1 加热腔入口溢料问题的分析30
4.7.2 流涎问题的分析31
4.7.3 解决方案31
参 考 文 献33
摘 要
熔融沉积成型技术(FDM)是目前国内外应用最为广泛的快速成型技术之一。它可以快速、精确地将设计思想从CAD模型物化为具有一定功能的原型或零件,从而实现对产品的快速测评及修改,有效的缩短了产品的开发周期。在熔融沉积快速成型中,成型精度对最终产品的质量起着决定性的作用,但是目前成型机的成型精度往往不高,如何提高成型精度是当今快速成型研究的一个重要方向。
本课题围绕熔融成型机,重点研究了该设备的机械系统,提出一套完整的机械设计方案。具体工作如下:
(1)结合传统的FDM熔融沉积成型设备,从整机的外形尺寸、最大成形空间、成形精度、主要运动结构和方式等方面,进行了细致和分析。在吸收了不同机型之间的优点和缺点之后,大致拟定了熔融成型机机械系统总体设计方案中的机械传动结构、三轴运动方式以及加热挤出头结构,确定了机械结构设计中的几个关键技术问题。
(2)以机械设计原理为依据,结合对FDM整个机械系统的几大构件制定的设计方案,按照整机设计需求参数,分别对运动系统、导向系统、机械结构和包装造型进行了具体的参数化选择,着重设计了加热挤出头结构,解决与优化了流涎问题,然后按照机身结构设计原则设计并完成了全部零部件的三维实体建模、装配以及工程图。
关键字:快速成型;FDM;加热挤出头
ABSTRACT
The fused deposition?rapid prototyping?technology?(FDM)?is?one?of?the?at home and abroad?the most widely used?rapid prototyping technology. It can?quickly and accurately?Design ideas from the CAD model materialized as proto types or parts of certain functions in order to achieve the rapid evaluation and modification of the product, effectively shortening the product development cycle. In fused deposition modeling, forming precision on the final product quality plays a decisive role, but the current forming machine precision is not high, how to improve the precision of the rapid prototyping is an important direction of research.
This topic around the molten molding machine, mainly studies the mechanical system of the device, puts forward a complete set of mechanical design.Specific work is as follows:(1) combined with the traditional FDM fused deposition molding equipment, from the appearance of the whole machine size, maximum forming space, forming precision, main structure and movement mode, are detailed and analyzed.In absorbing the advantages and disadvantages between different models, roughly sketched the melting machine mechanical system overall design scheme of mechanical transmission structure, three axis movement mode and heating extrusion head structure, identified several key technical problems in mechanical structure design.(2)And in accordance with FDM based on principle of mechanical design, the whole of several major components of design scheme of mechanical system, on the demand of the whole machine design parameters, respectively, on the sports system, guiding system, mechanical structure and packaging for the specific parameterized choice, mainly design the structure of heat extrusion head, solving and optimizing the salivate, then design and completed in accordance with the principle of the fuselage structure design all components of the three-dimensional entity modeling, assembly, and engineering drawing.
Key Words: Rapid Prototyping;Fused Deposition;Heating extrusion head
1 绪论
1.1 引言
进入21世纪后,因为一方面,消费者日益个性化、多样化的需求,工业产品要求创造更多需求。另一方面,制造商不仅要设计的产品满足需求的迅速,而且还要缩短设计周期和生产周期抢占市场,市场环境发生了翻天覆地的变化。制造业竞争加剧。
全球市场一体化的形成和提高产量的主要因素通常是有关竞争的成功或失败。为了保持和加强产品在市场上的竞争力,不仅需要设计师可以设计新产品迅速满足市场的需求,并能在短时间内,生产的产品或样品在投放市场之前进行必要的测试。在这种情况下,如果使用传统的制造方法,不仅需要各种各样的机械加工机床、工具、模具、及高水平的技术工人,生产成本高,生产周期长,不能适应快速发展的时代,因此,研究低成本、高效率的生产技术是解决这一问题的关键。
在1980年代末,随着制造业信息化,快速成型技术(Prototypical)应运而生。由于这种技术事新的制造理念,生产速度产品快速灵活的模型的关注。这种技术采用CAD设计、辅助制造、数控、精密的伺服驱动和新型材料等先进技术,成功地实现了产品制造自动化,更大程度提高生产效率和灵活的制造。在响应速度化市场作为第一个目标,市场可以缩短开发周期,降低开发成本,提高企业的生产效率。由于符合现代先进制造技术的发展核心,成型技术发展非常迅速,在发达国家已经成为行业的一个新分支和先进制造技术的支柱产业,制造技术是近年来最热门的研究课题。
1.2 熔融沉积成型技术概论
快速原型设计、快速成型、RP)技术是在1980年代末开发[1]的一种先进制造技术。级联的想法积累分层制造、材料粘合层层叠加形成实体,和3 d产品原型。三维分层制造实体的思想,最早出现在19世纪制造技术发展足够的。早在1892年,地质学家Anther[2]提出了使用新方法的3 d地图分层切片模型。然而,随着社会的发展和科技的进步,快速原型系统及其组成材料的相关研究有了长足的进步,取得了RP技术的快速发展。
这种新兴的制造技术不受成型几何实体外形限制,直接将三维的立体模型加工变为平面加工,形状特别复杂的物体和简单的物体可以用同样的方法进行制造。具体来说就是通过计算机三维造型系统获得产品的三维实体模型数据,然后经过面化处理,把它变成许多个三角形面化模型得到STL文件,接着以此面化模型为基础,切出沿某一方向的一系列连续截面作为二维切片薄层,再通过数控加工得到那些薄层切片,并将层与层之间粘接起来,如此层层叠加便形成了产品的三维原型。快速成形技术具有传统制造技术无法比拟的优势,于是受到工程界的高度重视, 并在国内外得到迅速的发展。在这个商业市场竞争越来越激烈,商品更新换代越来越快的时代,快速成形技术对制造业的发展起着巨大的影响,产品应用方面的成果也十分显著,这种技术的商品化成为其必然的趋势。
快速成形技术的发展其实也是经历了一个漫长曲折的过程。从二十世纪七十年代末到八十年代初期,几个不同国家的研究学者均独立提出了分层制造的快速成形概念。当时Charles. Hull[3]在美国UVP公司的支持下,完成了第一台能自动建造零件的完整系统(SLA-1),并在1986年申请获得该系统的专利,这个研究成果可以看做是快速成形技术发展史上的一个重要里程碑。同年,Charles W. Hull和UVP公司合作建立了3D System公司,许多关于快速成形的概念和技术在3D System公司中逐步发展成熟。同时许多其它相关学者和公司对快速成形原理及相应的成形系统也相继开发成功,直到九十年代后期共出现了十多种不同的快速成形技术。其中作为主流的是SLA、LOM、SLS、FDM和3DP这五种典型快速成形技术。快速成形技术涉及知识面极广,包括机械工程、激光、自动控制、计算机、材料学等多个前沿学科。随着现代设计和现代制造技术的迅速发展,该技术迅速在工业制造、建筑、艺术、医学、航空航天等领域得到广泛良好的应用。
1.2.1 熔融沉积成型技术的特点
快速成型技术能得到飞速的发展与它自身的特点有很大关系
(1)快速性
采用快速成型技术,从设计思想转变为具有一定结构功能的产品原型原型,一般只需几个小时至几十个小时,从而可以对产品设计进行快速评估、测试及功能试验,以缩短产品开发的研制周期,减少开发费用,提高企业参与市场竞争的能力。
(2)集成性
快速成型机通过计算机直接执行CAD模型的数控指令,避免了数控中的复杂编程,真正实现了设计制造一体化,大大提高了加工效率。与反求工程(Bioengineering)、Tao技术、网络技术、虚拟现实等相结合,成为产品快速开发的有力工具。
(3)高度柔性
若要生产不同形状的零件模型,只需改变CAD模型,重新调整和设置参数即可,成型过程中不需要专门的夹具和工具,成型零件与CAD模型具有直接关联,零件可随时修改,随时制造。
(4)无限制性
快速成型不受零件的形状和复杂程度的限制,可成型任意形状的造型,这就摆脱了传统夹具、工具加工的限制,使高难度、高复杂度的模型的加工变得相对较容易。
(5)材料的广泛性
快速成型技术可以制造树脂类、塑料原型,还可以制造出纸类、石蜡类、复合材料以及金属材料和陶瓷的原型。
(6)低造价性
其制造周期一般为传统的数控切削方法的l/5一1/10,而成本仅为1/3一1/5,它在保证一定精度和零件制作精度的基础上,具有最优的性能价格比,这也是快速成型的到飞速发展的一个重要原因。
1.2.2熔融沉积成型技术 - 工艺过程
产品三维模型的构建
由于RP系统是由三维CAD模型直接驱动,因此首先要构建所加工工件的三维CAD模型。该三维CAD模型可以利用计算机辅助设计软件(如Pro/E,I-DEAS,Fieldworks,UG等)直接构建,也可以将已有产品的二维图样进行转换而形成三维模型,或对产品实体进行激光扫描、CT断层扫描,得到点云数据,然后利用反求工程的方法来构造三维模型。
三维模型的近似处理
由于产品往往有一些不规则的自由曲面,加工前要对模型进行近似处理,以方便后续的数据处理工作。由于STL格式文件格式简单、实用,目前已经成为快速成型领域的准标准接口文件。它是用一系列的小三角形平面来逼近原来的模型,每个小三角形用3个顶点坐标和一个法向量来描述,三角形的大小可以根据精度要求进行选择。STL文件有二进制码和ASCll码两种输出形式,二进制码输出形式所占的空间比ASCII码输出形式的文件所占用的空间小得多,但ASCII码输出形式可以阅读和检查。典型的CAD软件都带有转换和输出stl格式文件的功能。
三维模型的切片处理。
根据被加工模型的特征选择合适的加工方向,在成型高度方向上用一定间隔的平行面切割近似后的模型,以便提取截面的轮廓信息。间隔一般取0.05mm~0.5mm,常用0.1mm。间隔越小,成型精度越高,但成型时间也越长,效率就越低,反之则精度低,但效率高。
成型加工。
根据切片处理的截面轮廓,在计算机控制下,相应的成型头(激光头或喷头)按各截面轮廓信息做扫描运动,在工作台上一层一层地堆积材料,然后将各层相粘结,最终得到原型产品。
成型零件的后处理。
从成型系统里取出成型件,进行打磨、抛光、涂挂,或放在高温炉中进行后烧结,
参 考 文 献
J.A. Lewis, G.M. Grat son, Materials Today 7 (2004) 32.
王雪莹. 3D打印技术与产业的发展及前景分析[J] . 中国高新技术企,2012-09-10张剑峰,张建华,赵剑峰,沈以赴,花国然,黄因慧. 激光快速成形制造技术的应用研究进展[J] . 航空制造技术,2002-07-15
张爱英,王连才,刘厚利,魏宏亮,冯增国. 基于快速成型技术的组织工程支架制备进展[J] . 化工进展,2004-03-30
Kathy Lu *, William T. Reynolds 1, 3DP process for fine mesh structure printing, Powder Technology 187 (2008) 11–18
孙勇,王秀峰. 快速原型制造技术在陶瓷制件上的研究进展[N] . 陕西科技大学学报,2004-10-25
陈步庆,林柳兰,陆齐,胡庆夕. 三维打印技术及系统研究[J] . 机电一体化,2005-07-20
王葵,谭威. 快速成型技术及发展[N] . 科技创新导报,2008-03-21
刘厚才,莫健华,刘海涛. 三维打印快速成形技术及其应用[J] . 机械科学 与技术,2008-09-15
汪洋,叶春生,黄树槐. 熔融沉积成型材料的研究与应用进展[J] . 塑料工业,2005-11-30
张会. ZPrinter310系统X-Y执行机构中的Y轴设计[J] . 机械管理开发,2008-06-15
张昌明. 三维打印机ZPrinter310系统Z向升降台的结构设计[J] . 机械管理开发,2008-08-15
刘海涛. 光固化三维打印成形材料的研究与应用[D] . 华中科技大学,2009-05-11
林静. 数字光处理投影系统[D] . 大连理工大学,2008-05-26
蒋玮,徐志祥,赵福令. 直接金属激光烧结成形的机理及实验研究[J] . 中国机械工程,2003-08-15
任乃飞,张福周,王辉,邢志杰. 金属粉末选择性激光烧结技术研究进展[J] . 机械设计与制造,2010-02-08
杨俊杰,邓海兵. 熔融挤压快速成形支撑参数的研究[J] . 机械设计与制造 2006-11-08
罗晋. 熔融沉积成型控制系统的研究[D] . 华中科技大学,2006-04-01
纪良波. 熔融沉积成型有限元模拟与工艺优化研究[D] . 南昌大学,2011-06-01
陈明. 熔丝沉积快速成形的控制及软件系统的研究[D] . 华中科技大学, 2004-04-01
朱利松,叶春生,黄树槐. FDM快速成形系统的控制系统研究[J] . 机床与液压2005,(1):28-29
门东升. 熔融挤压快速成形机喷头的研究[D] .北京化工大学,2003
吴良伟. CAD模型驱动高聚物熔融挤压快速成形技术研究[D] . 清华大学,1998
吴任东. 高速熔融挤压成形工艺及设备研究[D] . 清华大学,2000
黄小毛. 熔丝沉积成形若干关键技术研究[D] . 华中科技大学,2009-06-01
濮良贵,纪名刚. 机械设计[M] . 高等教育出版社,2006-05