钻套的数控加工工艺及程序编程设计【优秀】【数控编程类】【带ug三维】【1张CAD图纸全套】【SK025】
【33页@正文11500字】【详情如下】【需要咨询购买全套设计请加QQ1459919609 】
zuantao.prt
图片.bmp
摘要.doc
正文.doc
钻套的数控加工工艺及程序设计.doc
零件图.dwg
目录
前言5
第一章 零件工艺分析7
1.1零件图的审查7
1.1.1图纸的正确性分析及尺寸标注7
1.1.2技术要求分析7
1.1.3材料分析8
1.1.4结构工艺性分析8
1.2工艺装备的选择8
1.2.1机床的选择8
1.2.2夹具的选择9
1.2.3不同机床上的装夹9
1.3刀具的选择10
1.3.1刀具的材料及性能10
1.3.2刀具的确定11
1.4切削用量的选择15
1.4.1背吃刀量ap(即切削深度)的确定15
1.4.2主轴转速的确定16
1.4.3进给速度的确定17
第二章 加工工序的设计18
2.1工序的划分18
2.1.1工序划分的原则18
2.1.2工序的划分方法18
2.1.3划分工序18
2.2工序1的加工过程19
2.2.1确定工件坐标系19
2.2.2工件的装夹19
2.2.3加工刀具的选择19
2.2.4加工路线20
2.2.5加工程序21
2.3工序2的加工过程23
2.3.1确定工件坐标系23
2.3.2工件的装夹23
2.3.3加工刀具的选择24
2.3.4加工路线24
2.3.5加工程序25
第三章 零件实体展现及注意事项25
3.1实体展现25
3.2数控车床操作注意事项26
设计总结28
致谢29
参考文献30
附录31
摘要
本文阐述了钻套的加工工艺,分析该零件的图纸内容、技术要求,确定机床的选择、刀具的选择、切削用量的选择、以及加工顺序的选择等等,通过这些分析后,再编制其数控加工程序,最终完成该零件的实体造型,填写数控加工工艺卡片。
此次设计是我对在校三年以及实习中所学知识的一个验证,由于本人技术有限,题中有不足之处还望老师加以指点。
关键词:材料分析 毛坯的选择 刀具的选择 程序设计
前言
钻套即是引导钻孔的轴套,它的主要作用就是防止钻头引偏,造成加工孔的精度不能达到。所以一般在精度要求不高的时候就不用钻套了,对于要求高或批量生产大的,因钻头对中费时较多所以也必须要钻套。如果是专用夹具的话那一定就要用钻套了。如果夹具对钻孔无关,换句话说对孔的要求不高,批量也不大的话可以不用钻套。
根据钻套的结构和使用特点,主要有四种类型。
①固定钻套
固定钻套的分为两种形式(无肩,带肩),该类钻套外圆以H7/n6或H7/r6配合,直接压入钻模板上的钻套底孔内。在使用过程中若不需要更换钻套(据经验统计,钻套一般可使用1000~12000次),则用固定钻套较为经济,钻孔的位置精度也较高。
②可换钻套
当生产批量较大,需要更换磨损的钻套时,则用可换钻套较为方便,如图1-1所示。可换钻套装在衬套中,衬套是以H7/n6或H7/r6的配合直接压入钻模板的底孔内,钻套外圆与衬套内孔之间常采用F7/m6或F7/k6配合。当钻套磨损后,可卸下螺钉,更换新的钻套。螺钉还能防止加工时钻套转动或退刀时钻套随刀具拔出。
图1-1 可换钻套 图1-2快换钻套
③快换钻套
当被加工孔需依次进行钻、扩、铰时,由于刀具直径逐渐增大,应使用外径相同而内径不同的钻套来引导刀具,这时使用快换钻套可减少更换钻套的时间,如图1-2所示。快换钻套的有关配合与可换钻套的相同。更换钻套时,将钻套的削边处转至螺钉处,即可取出钻套。钻套的削边方向应考虑刀具的旋向,以免钻套随刀具自行拔出。
以上三类钻套已标准化,其结构参数、材料和热处理方法等,可查阅有关手册。
④特殊钻套
由于工件形状或被加工孔位置的特殊性,有时需要设计特殊结构的钻套,如图1-3所示。
在斜面上钻孔时,应采用图1-3a所示的钻套,钻套应尽量接近加工表面,并使之与加工表面的形状相吻合。如果钻套较长,可将钻套孔上部的直径加大(一般取0.1mm),以减少导向长度。
在凹坑内钻孔时,常用图1-3b所示的加长钻套(H为钻套导向长度)。图1-3c、d为钻两个距离很近的孔时所设计的非标准钻套。
参考文献
1 龚洪浪 王贤涛 《数控加工工艺学》 科学出版社 2005.8
2 舒志兵 陈光明 曾孟雄 《数控加工技术》 电子工业出版社 2007.1
3 董霖 《数控技术及加工编程实训教程》 西南交通大学出版社 2007.2.1
4 张丽华 马立克 《数控加工工艺与编程》 大连理工大学出版社
5 张思弟 贺曙新 《数控编程加工技术》 化学工业出版社 2005.6.1
6 黄翔 李迎光 《:数控编程理论.技术与应用》 清华大学出版社 2006.1.1
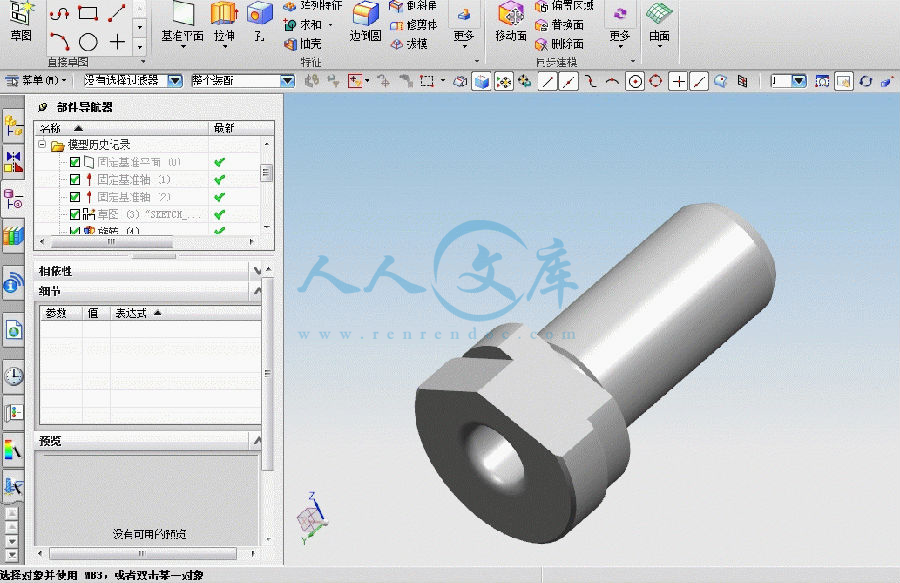
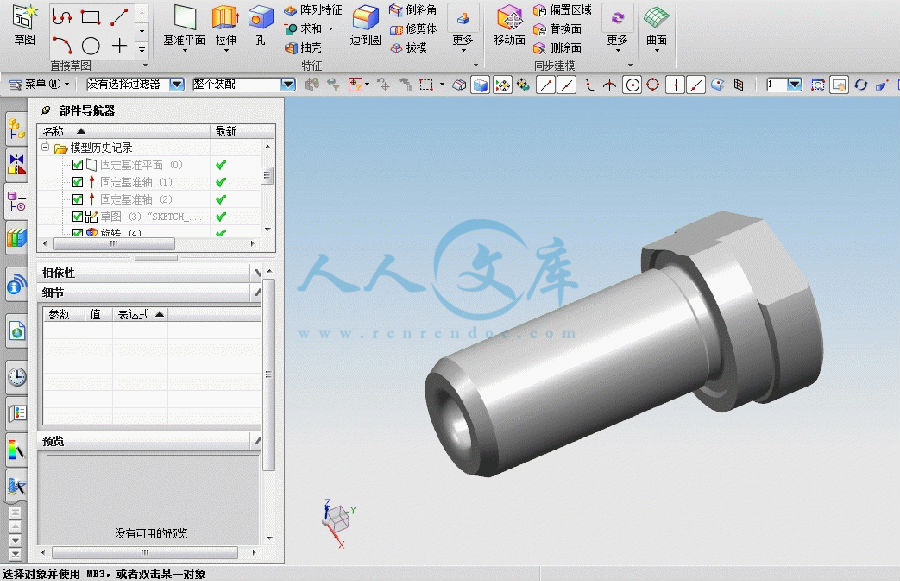
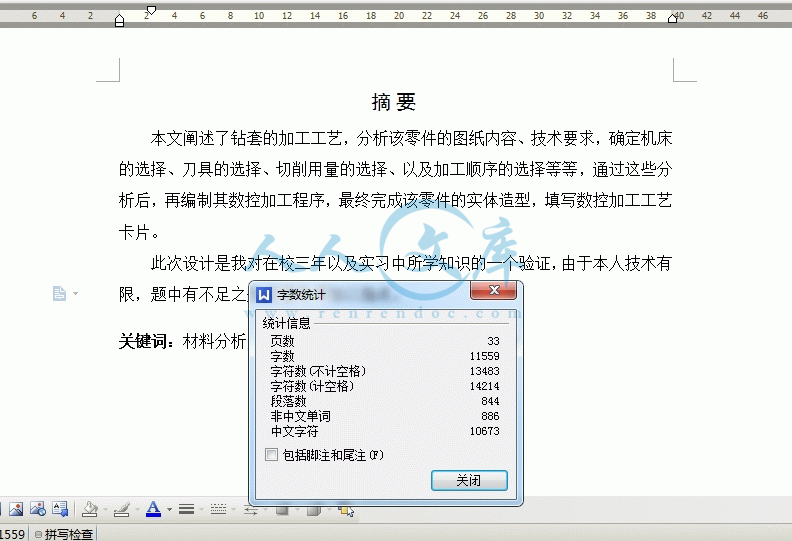

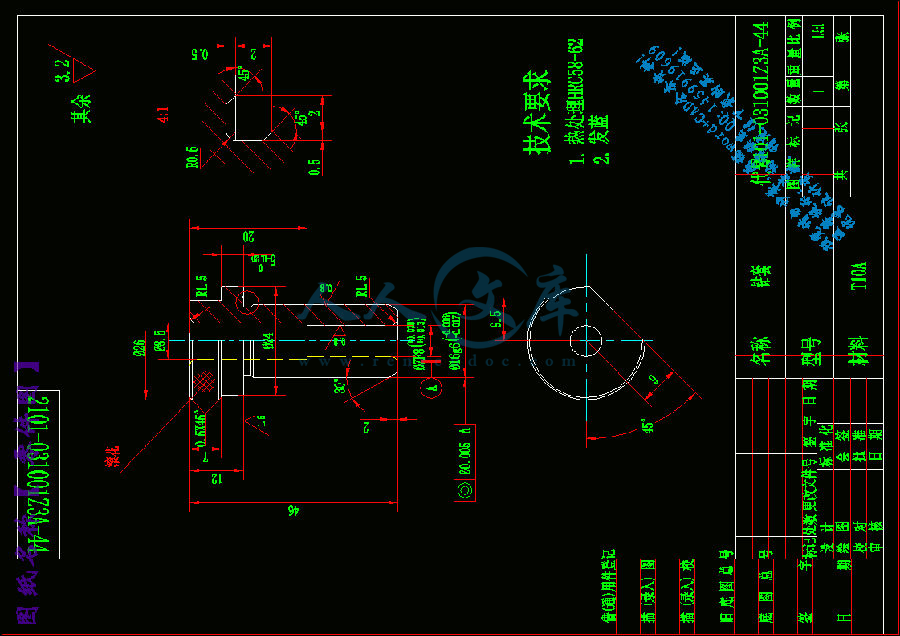