果蔬大棚电动卷帘机的设计【优秀】【农业用机械类】【12张CAD图纸】【毕业设计】
【word文档包含:外文翻译,53页@正文15400字】【详情如下】【需要咨询购买全套设计请加QQ1459919609】.bat
传动轴.dwg
卷绳管.dwg
正文.doc
法兰.dwg
箱座a1.dwg
箱盖.dwg
绞盘.dwg
蜗杆.dwg
蜗轮A1.dwg
装配图.dwg
轴承支座.dwg
输出轴.dwg
齿轮.dwg
果蔬大棚电动卷帘机的设计
摘 要
果蔬大棚卷帘机是今后大棚种植必需的机械装备和发展方向,它改变了传统人工卷帘操作的方法,比人工操作提高效率十几倍以上,解决了每天卷放草帘的劳动强度,改善了严冬露天操作的环境,重要的是缩短了卷、放草帘所消耗的时间,延长了光照时间.大大提高了劳动效率和经济效益.
现今市场上主要供应的是一种是走动式卷帘机这种卷帘机利用卷帘机的动力上下自由卷放草帘子,不必受大棚坡度大小的限制。但这种卷帘机结构复杂,稳定性差,寿命低,且不适合长度过大的大棚。
本课题所设计的是一种固定式卷帘机,它模拟人工操作,通过缠绕在绳上的绳子的拉紧和放松,实现草帘的卷收和铺放。
其主要机构包括电动机、减速机、卷帘装置等。本课题着重对卷帘机的减速机及卷帘装置进行设计,使其在压低成本的前提下满足普通斜坡式大棚的要求。
关键词:卷帘机,减速机,传动比,抗弯强度
FRUITS AND VEGETABLES BIG AWNING ELECTRICALLY OPERATED VOLUME CURTAIN MACHINE
Abstract:The fruits and vegetables big awning volume curtain machine will be the next big awning planter essential machinery equipment and the development direction, it changed the traditional artificial volume curtain operation method, will enhance above efficiency several times compared to the manual control, solved the daily volume to graze animals the curtain the labor intensity, improved the severe winter open-air operation environment, more importantly reduced the volume, has grazed animals the time which the curtain consumed,Lengthened the illumination time.Enhanced the labor efficiency and the economic efficiency greatly.
Nowadays in the market the main supply is one kind is takes a walk about the type volume curtain machine this kind of volume curtain machine use volume curtain machine power the free volume to graze animals the curtain screen, does not need to receive the big awning slope size the limit. But this kind of volume curtain machine structure is complex, the stability is bad, the life is low, also does not suit the length oversized big awning.
What this topic designs is one kind of stationary volume curtain machine, it simulates the manual control,Through winding on rope string tautness and relaxation,The realization grass curtain volume receives and sets.
Its main organization including electric motor, speed reducer, volume curtain installment and so on. This topic emphatically carries on the design to the volume curtain machine speed reducer and the volume curtain installment, causes it in to reduce the cost under the premise to satisfy the ordinary pitch type big awning the request.
Key word Volume curtain machine,Speed reducer,Velocity ratio,Bending strength.
目 录
1 绪论1
1.1 本课题研究意义1
1.2 本课题的研究现状1
1.3 设计任务与要求3
1.4 拟解决的关键问题3
1.5 拟采用的研究手段4
2 传动装置的总体设计4
2.1 确定传动方案4
2.2 电动机的选择4
2.3 计算总传动比和分配各级传动比5
2.4 计算传动装置的运动和动力参数5
3 传动机构及零件的设计计算6
3.1 带传动的设计计算6
3.2 减速器的设计计算7
3.2.1 蜗轮蜗杆的设计计算7
3.2.2 蜗杆的设计10
3.2.3 齿轮的设计计算17
3.2.4 传动轴的设计22
3.2.5 输出轴的设计29
3.2.6 箱体的设计36
3.3 卷动机构的设计38
3.3.1 卷绳管的设计计算38
3.3.2 绞盘的设计计算41
3.3.3 滑动轴承的设计43
3.3.4 法兰连接的设计43
4 结论46
参考文献47
致谢49
外文文献原文
译文
1 绪论
1.1 本课题研究意义
随着城乡人民生活水平的提高,冬季栽培鲜菜、鲜果的温室大棚蓬勃发展,其规模越来越大。但是,在温室大棚作业中,卷铺草帘是最费时费工的主要作业环节之一,尤其在严寒冬季的凌晨和傍晚,在寒风刺骨的恶劣条件下,农民站在大棚顶上从事着艰苦笨重的草帘卷铺劳动,情况可想而知。对于一个长80米大棚来说,每天都要在早上拉启、傍晚放下,各要用大约40分钟左右。严格的来说,冬天里的阳光和温度是“果蔬大棚”中作物正常生长所依赖的珍贵资源。农民要争分夺秒,辛苦是可想而知的[1]。但这仍然解决不了问题, 由于“果蔬大棚”保温帘开启和关闭时间相对集中,引起的劳力不足和耗用时间过长,已经严重制约了“果蔬大棚”的产量效益和发展空间。
电动卷帘机的出现则彻底解决了人工卷铺帘子带来的一系列不便。使用电动卷帘机,可随时启动,延长了光照时间,增加了光合作用,更重要的是节省劳动时间,减轻了劳动强度。日光温室在深冬生产过程中,每一千平方米温室人工控帘约需1.5小时,而卷帘机只需5分钟左右,太阳落山前,人工放帘需用约1小时左右,由此看来,每天若用卷帘机起放帘子,比人工节约近2小时的时间。同时延长了室内宝贵的光照时间,增加了光合作用时间 。另外,使用电动卷帘机对草帘、棉帘保护性好,延长了草帘、棉帘的使用寿命,既降低生产成本,同时因其整体起放,其抗风能力也大大增强。总体上可使农民能比较轻松地用更多的精力提高对蔬菜进行管理,提高品质、扩大规模[2]。
因此,开发经济、实用的电动卷帘机是一项很好的研究课题。
1.2 本课题的研究现状
目前国内生产的卷帘机主要有两种工作方式[3]:一种是固定式,卷帘机固定在大棚后墙的砖垛上,它模拟人工操作,通过缠绕在轴上的绳子的拉紧和放松。利用机械动力把草帘子卷上去,利用大棚的坡度和草帘子的重量往下滚放草帘子。该种型号的卷帘机造价较高,大棚要有一定的坡度,如果棚面坡度太平,草帘子滚不下来,当风大时容易乱绳并影响工作,且安装复杂。另一种是走动式,这种卷帘机由悬臂杆、支撑杆、电机、减速机构和卷帘轴等组成。其工作方式是采用机械手的原理,利用卷帘机的动力上下自由卷放草帘子,不必受大棚坡度大小的限制。但存在以下不足,悬臂杆和支撑杆稳定性差,对草帘整体弯度要求较高,不易满足长度较大的大棚,且其卷帘轴被焊接成整体构件,拆装不方便。
对于较常见的80米长的果蔬大棚,通过文献检索,有一些满足要求的卷帘机械,现将代表性的结构特点分析如下。
图1[4]是一种卷帘机的使用状态示意图,该卷帘机采用固定式结构,主要由工作电机及固定机构,减速机,卷绳管,卷帘绳,螺栓,轴承等组成。其工作原理为电机通过减速箱减速,使输出轴与卷绳管连接,带动卷绳管转动,卷绳管与卷帘绳一端固定,电机工作,卷绳管带动卷帘绳卷起,卷帘绳带动草帘卷起,完成卷的过程。电动反转,卷帘在自身重力作用下沿绳放下,完成放的过程。其中卷帘机的电机和减速机分别固定在一电机支杆上,电机支杆的下端固定在温室的墙上。大棚卷帘机包括多个卷绳管支承机构,卷绳管直接与减速箱的输出轴相连。卷绳管通过支架固定。支架通过螺栓固定在大棚的顶墙上。卷帘绳一端套在卷绳轴上,另一端绕过卷轴大棚顶端。其中电机通过减速机予以减速,带动整体。优点:结构简单,以电机驱动,卷帘卷起速度快,省工省力,适合大面积作业。
参 考 文 献
[1] 张福墁.农业现代化与我国设施园艺工程[J].农业工程学报,2002,18(增刊):123
[2] 《宝钢减速器图册》编委会编.宝钢减速器图册.北京:机械工业出版社,1995﹒76.
[3] 潘文维,罗庆熙,李 军.我国温室产业现状及发展建议[J].北京园艺,2002,(3):425
[4] 周长吉. 日光温室的结构优化[J].农业工程学报,1996,12(增刊):27229
[5] 崔保苗,王占文,赵聪,慧张静.JL250型日光温室卷帘机的设计研究.山西农业大学学报,2003,23(3):261-264
[6] 李永春.温室大棚卷帘机.中国专利:00210621.3,2000-10-7
[7] 朴义浩.蔬菜大棚卷帘机.中国专利:97205153.8,1998-4-22.
[8] 杜根锁.大棚卷帘机.中国专利:00258689.4,2001-8-22
[9] 黄彗春,沈永鹤.温室草帘自爬式卷帘机构的运动和受力分析.机械制造, 2004, 42(481): 35~37
[10] 濮良贵,纪名刚.机械设计.北京:高等教育出版社,2001﹒235
[11] 葛中民,机械设计基础.北京:高等教育出版社,1999.132
[12] 孟兆范,张秀彬.电动双制式草帘卷放机的安装.农机使用与维修,2002, (3): 3
[13] 梁光启、林子为,工程材料学 , 上海科学技术出版社,1987
[14] 吴宗泽、罗圣国主编,机械设计课程设计手册,高等教育出版社,1992
[15] 机械工程手册编辑委员会编机械,机械工程程手册,第1~6卷机械工业出版社,1982
[16] 周明衡,常德功主编.机械传动基础部件 标准联轴器手册.沈阳:辽宁科技出版社,1995
[17] 王步瀛 机械零件强度计算的理论和方法.北京:高等教育出版社,1986
[18] 邱宣怀主编.机械设计.北京:高等教育出版社,1997
[19] 章日晋等编.机械零件的结构设计.北京:机械工业出版社,1987
[20] 齿轮手册委员会.齿轮手册.北京:高等教育出版社,1990
[21] 减速器实用技术手册编委会编.减速器实用技术手册.北京:机械工业出版社,1992
[22] 齿轮国家标准汇编.北京:中国标准出版社,1992
[23] 洛阳轴承研究所编.滚动轴承产品样品.1989
[24] 黄贵根,黄俞.镶嵌自润滑轴承的应用.润滑与密封,1996
[25] 卜炎编.螺纹联接设计与计算.北京:高等教育出版社,1987
[26] Andrzej.M.Trzynadlowski 著.李鹤轩,李扬译.异步电动机.北京.机械工业出版社,2002
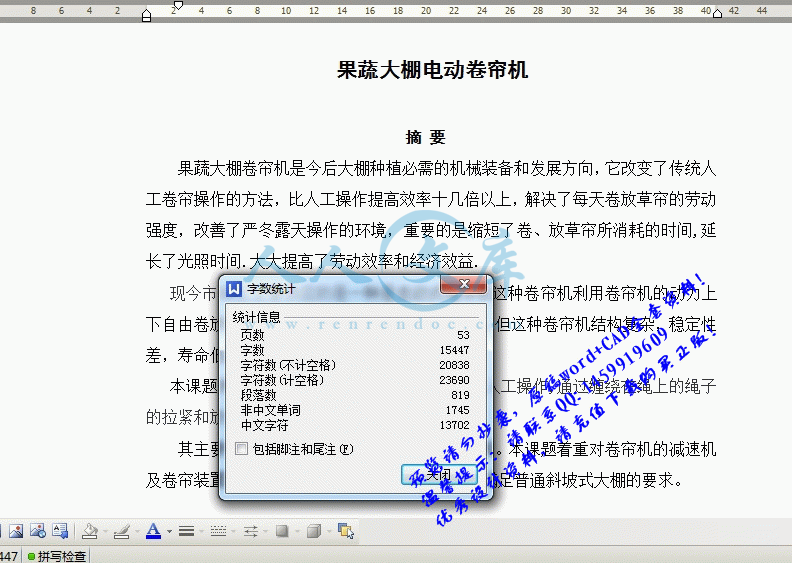
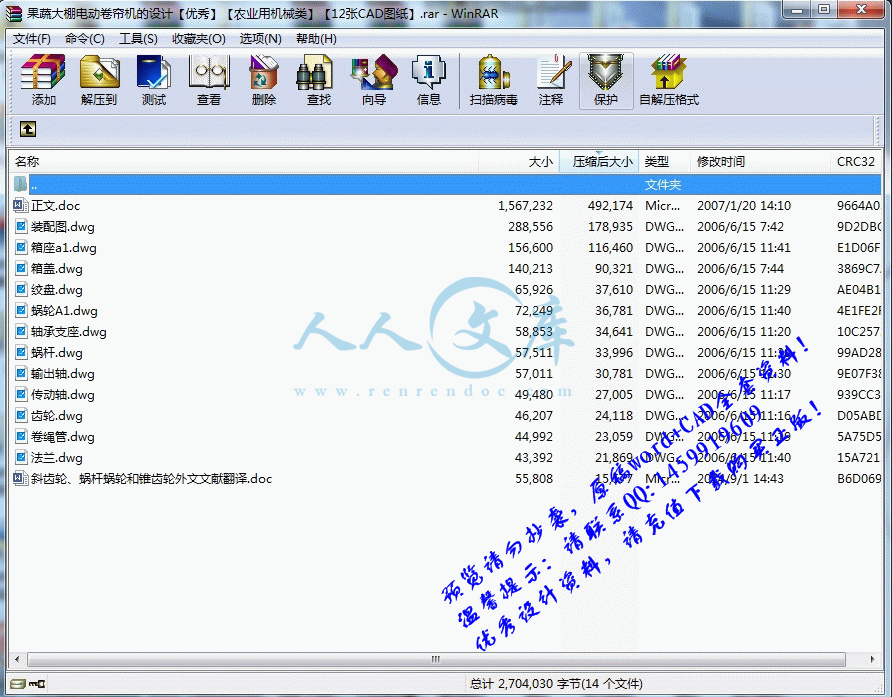
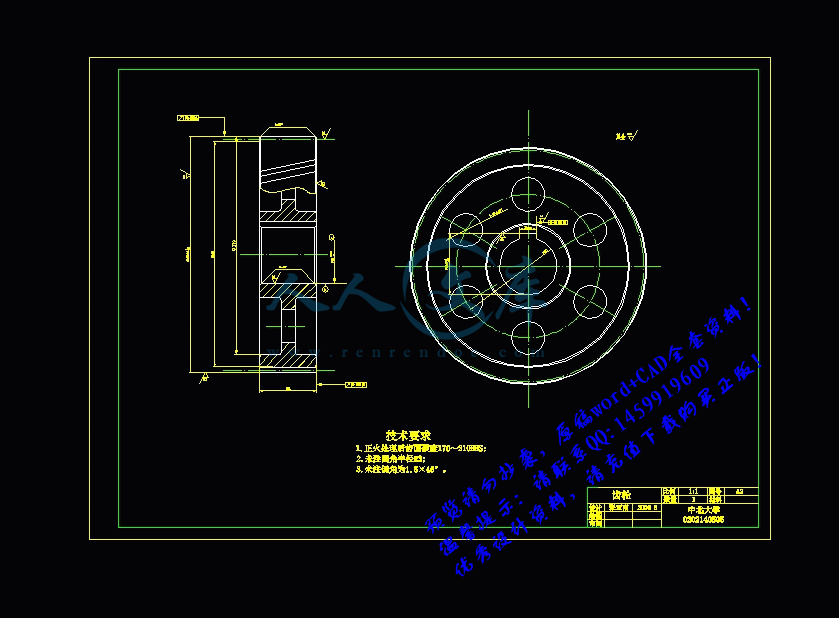

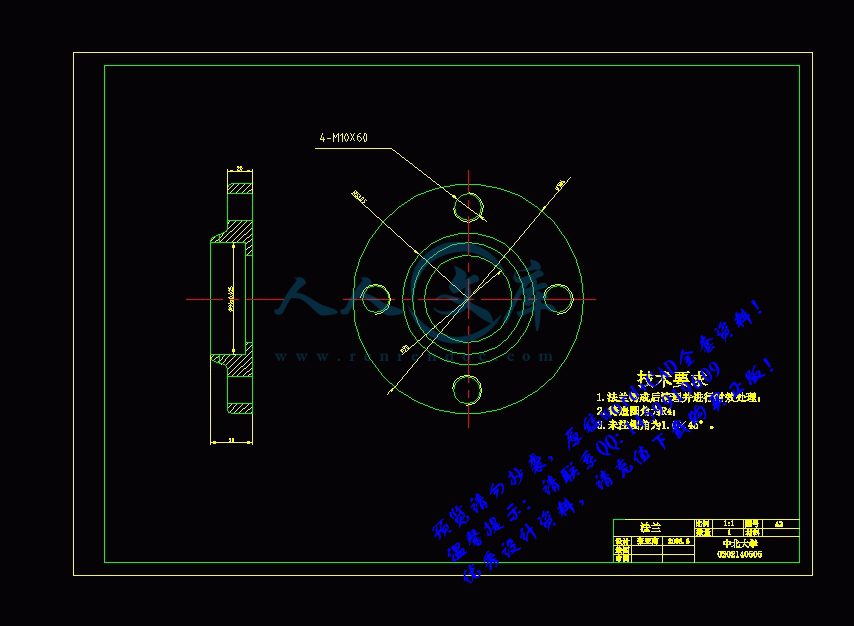

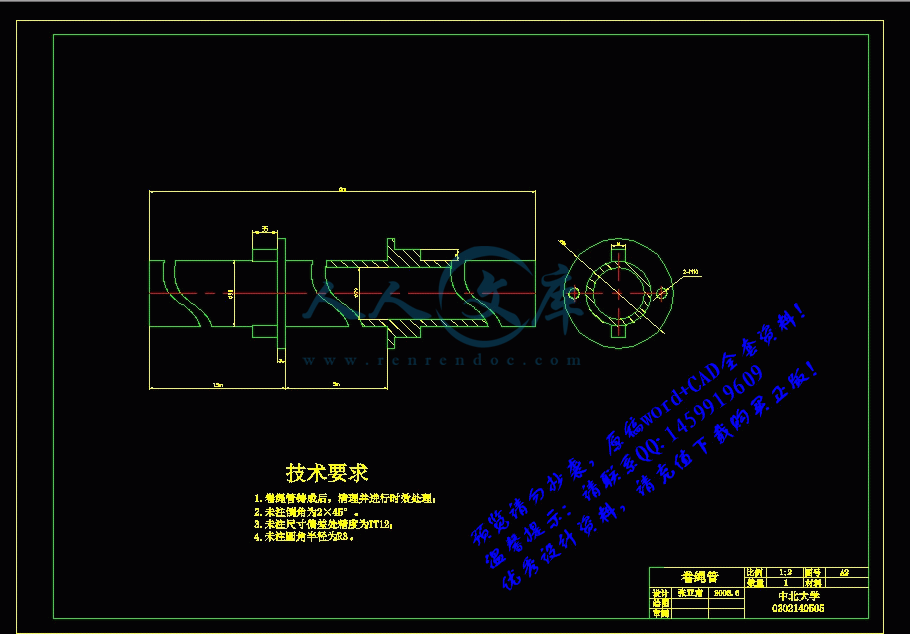



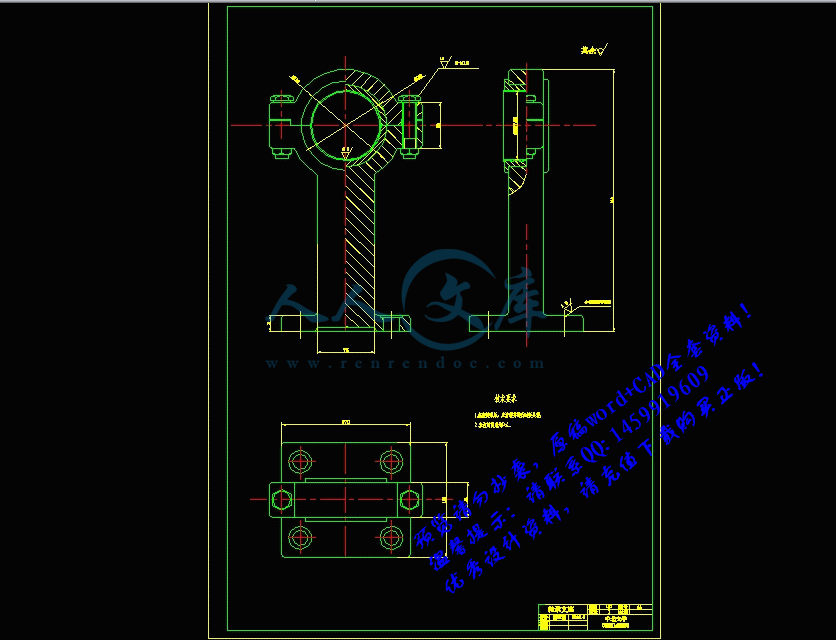
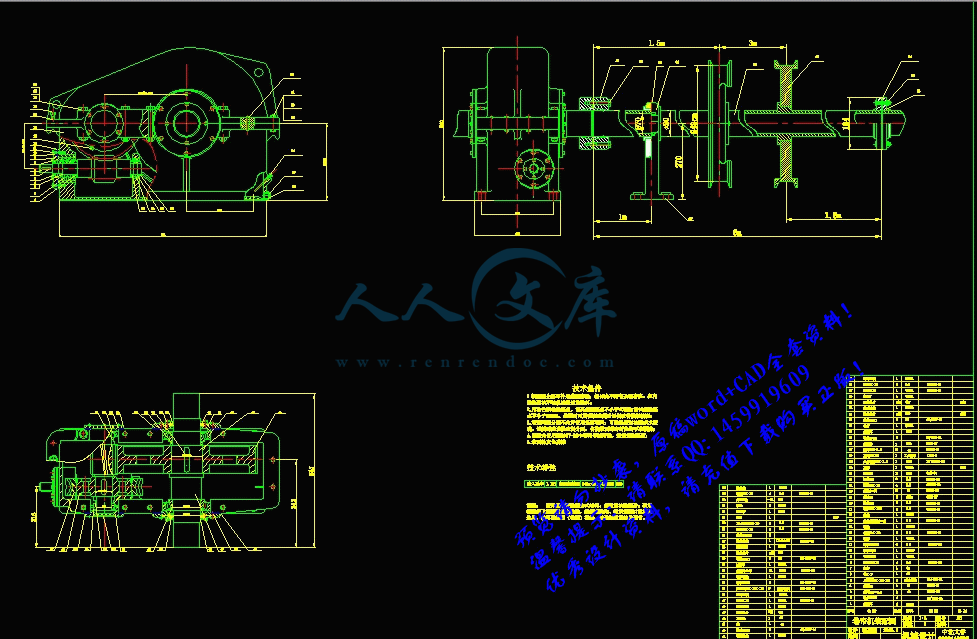

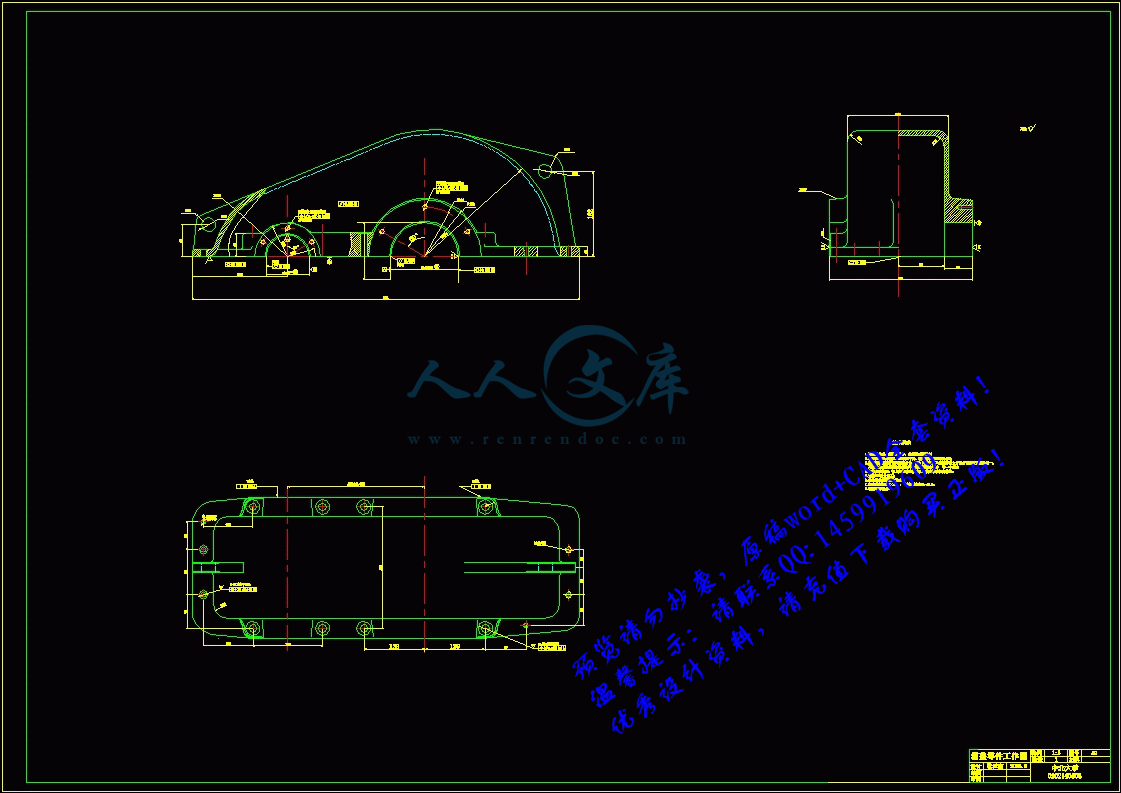