【温馨提示】 购买原稿文件请充值后自助下载。
[全部文件] 那张截图中的文件为本资料所有内容,下载后即可获得。
预览截图请勿抄袭,原稿文件完整清晰,无水印,可编辑。
有疑问可以咨询QQ:414951605或1304139763
摘 要
本说明书描述了MG200/475-W型液压牵引采煤机整机方案设计以及截割部的设计和计算过程。
MG200/475-W型液压牵引采煤机可用于煤层厚度为1.3-2.5m、煤质中硬的缓倾斜煤层。与传统的纵向布置的单电机采煤机相比,该采煤机将截割电机直接安装在截割部壳体内,齿轮减速装置全部集中在截割部壳体及行星减速器内,取消了螺旋伞齿轮、固定减速箱、摇臂回转套等结构,使其结构更简单、紧凑,可靠性更高。
截割部是采煤机直接落煤、装煤的部分,其消耗的功率约占整个采煤机功率的80%-90%,主要由截割部壳体、截割电机、齿轮减速装置、滚筒等组成。该采煤机的截割部采用四级传动;前三级为直齿传动,第四级为行星传动。二级传动的圆柱齿轮为可换齿轮,使输出转速可根据不同的煤质硬度在两档速度内选取。截割部采用了三个惰轮轴,使采煤机能够满足截割高度对截割部长度的要求。设计将截割部行星减速器和滚筒直接联结,取消了安装在滚筒上的截齿,使结构简单、可靠。
关键词:采煤机,截割部,结构,设计
Abstract
This brochure describes the type of hydraulic MG200/475-W shearer traction unit program design and cutting the Department of Design and calculation process.
MG200/475-W traction Shearer hydraulic seam thickness can be used for a .3-2.5 m, Hard coal to the gently inclined seam. With the traditional vertical layout of the single-motor compared to Shearer, Shearer will be the ranging-arm installed directly in the cutting of the shell, gear device exclusively on cutting Shell and planetary reducer, the abolition of the spiral bevel gears, gear box fixed, Rocker rotating sets of structures, their structure is simpler, more compact and higher reliability.
Ranging-arm of the shearer is directly charged coal, the coal loaded, its about the power consumption of the entire power shearer 80% -90%, mainly by cutting Shell, cutting electrical, Gear and drum components. The shearer cutting unit used four drive; Before three straight tooth drive, the fourth level of planetary transmission. 2 Drive Gear to be for the gears, enabling the output speed can be based on different coal hardness in two tranches within the selected speed. Cutting the Department has adopted a three lazy axle, to meet the shearer cutting height on the ranging-arm degree requirements. Designed to be cutting planetary reducer and drum direct link, canceled installed in the drum Pick, simple and reliable.
Keywords: shearer, ranging-arm,structure,design
第1章 绪论
1.1引言
我国是产煤大国,煤炭也是我国最主要的能源,是保证我国国民经济飞速增长的重要物质基础。煤炭工业的机械化是指采掘、支护、运输、提升的机械化。其中采掘包括采煤和掘进巷道。随着采煤机械化的发展,采煤机是现在最主要的采煤机械。20世纪70年代主要靠进口采煤机来满足我国生产的需要,到今天几乎是我国采煤机占领我国的整个采煤机市场,依靠科技进步,推进技术创新,开发高效矿井综合配套技术是我国煤炭科技的发展的主攻方向,我国的采煤机现在已经进入了自主研发,标准化,系列化阶段。
1.2采煤机械概述
1.2.1采煤机械化的发展
机械化采煤开始于上世纪40年代,是随着采煤机械(采煤机和刨煤机)的出现而开始的。40年代初期,英国、苏联相继生产了采煤机,联邦德国生产了刨煤机,使工作面落煤,装煤实现了机械化。但是当时的采煤机都是链式工作机构,能耗大、效率低,加上工作面输送机不能自移,所以生产率受到一定的限制。
50年代初期,英国、联邦德国相继生产力滚筒采煤机、可弯曲刮板输送机和单体液压支柱,大大推进了采煤机械化的发展。由于当时采煤机上的滚筒式死滚筒,不能实现跳高,因而限制了采煤机械的适用范围,我们称这种固定滚筒的采煤机为第一代采煤机。这样,50年代各国的采煤机械化的主流还只是处于普通机械化水平。虽然载1954年英国已经研制出了液压自移式支架,但是由于采煤机和可弯曲刮板输送机尚不完善,综采技术仅仅处于开始试验阶段。
60年代是世界综采技术的发展时期。第二代采煤机——单摇臂滚筒采煤机的出现,解决了采高调整的问题,扩大了采煤机的适用范围;特别式1964年第三代采煤机——双摇臂采煤机的出现,进一步解决了工作面自开缺口问题;再加上液压支架和可弯曲刮板输送机的不断完善,滑行刨的研制成功等,
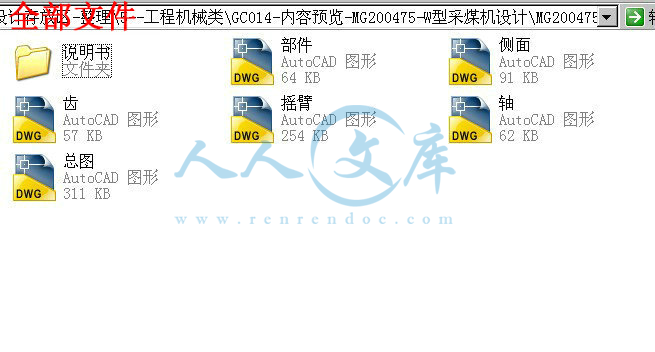




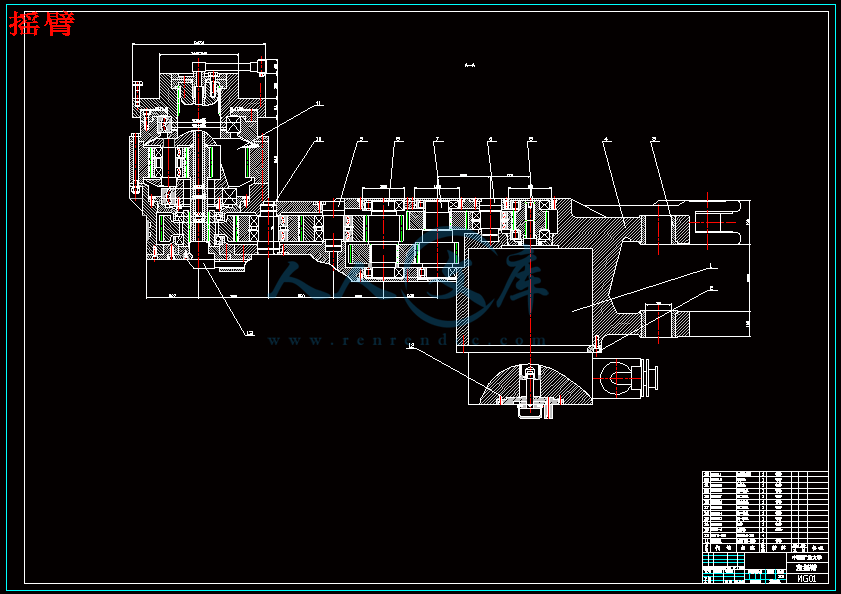
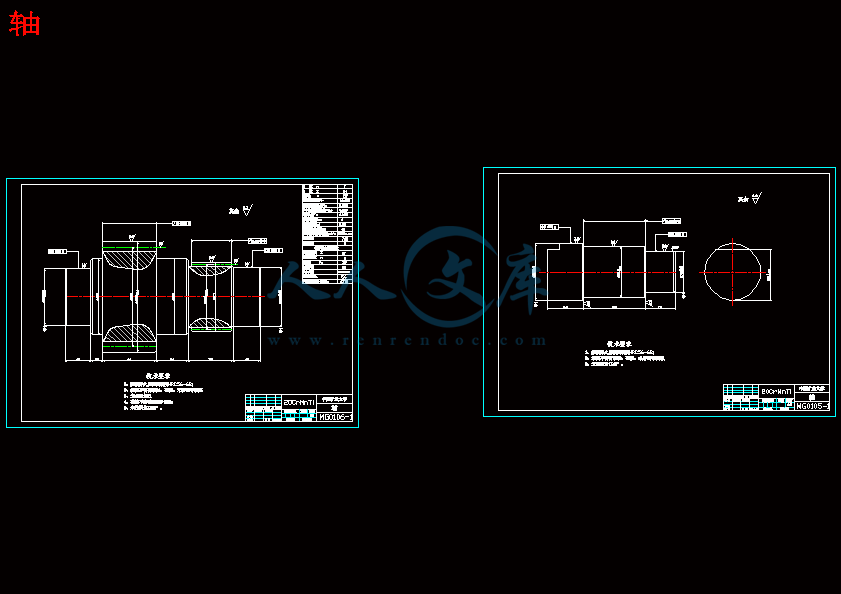
