丰田COLLORA车盘式制动器设计
34页 15000字数+说明书+任务书+开题报告+6张CAD图纸【详情如下】
丰田COLLORA车盘式制动器设计开题报告.doc
丰田COLLORA车盘式制动器设计说明书.doc
任务书.doc
制动衬块.dwg
制动钳体.dwg
前制动盘.dwg
后制动盘.dwg
指导记录.doc
活塞.dwg
答辩相关材料.doc
装配图.dwg
过程管理封皮.doc

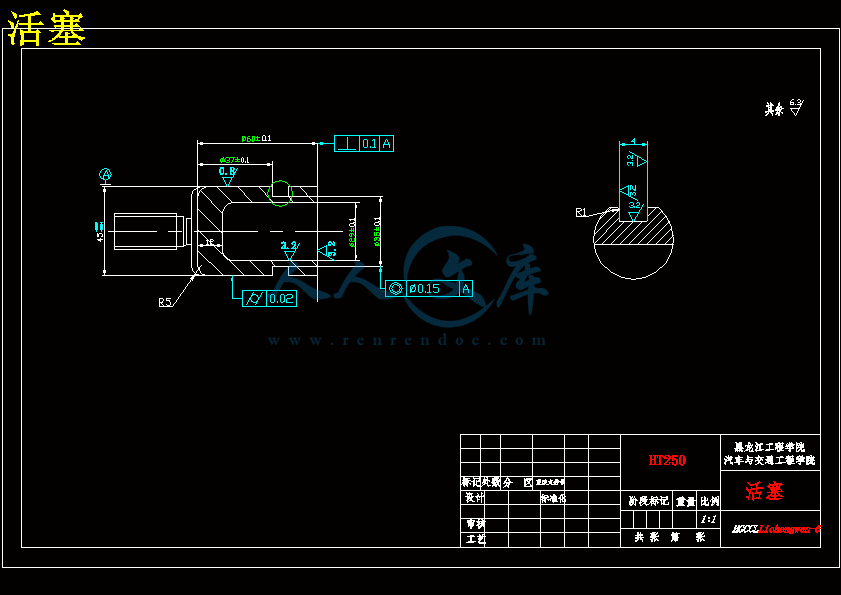

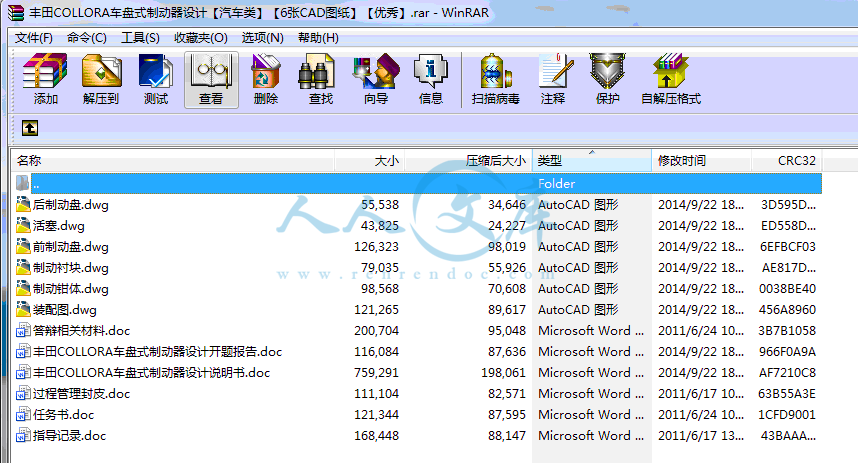
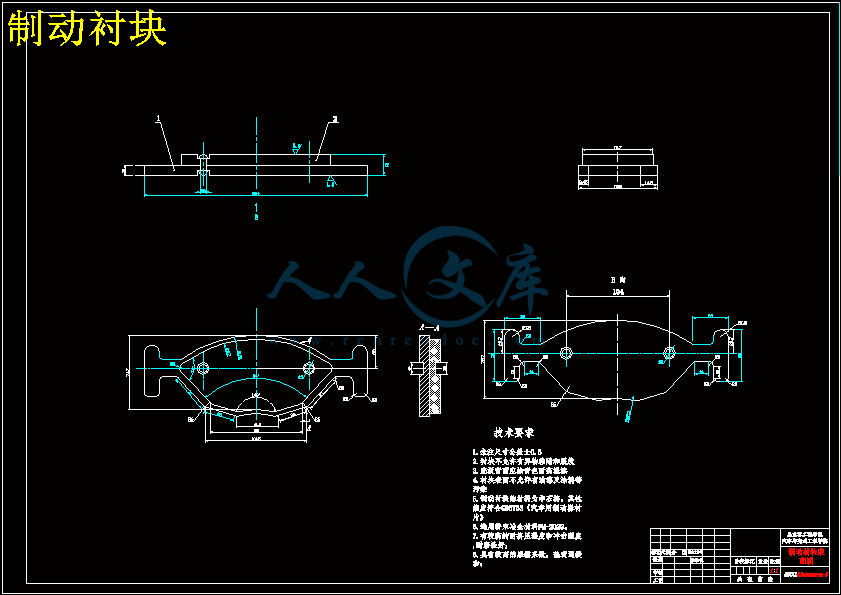
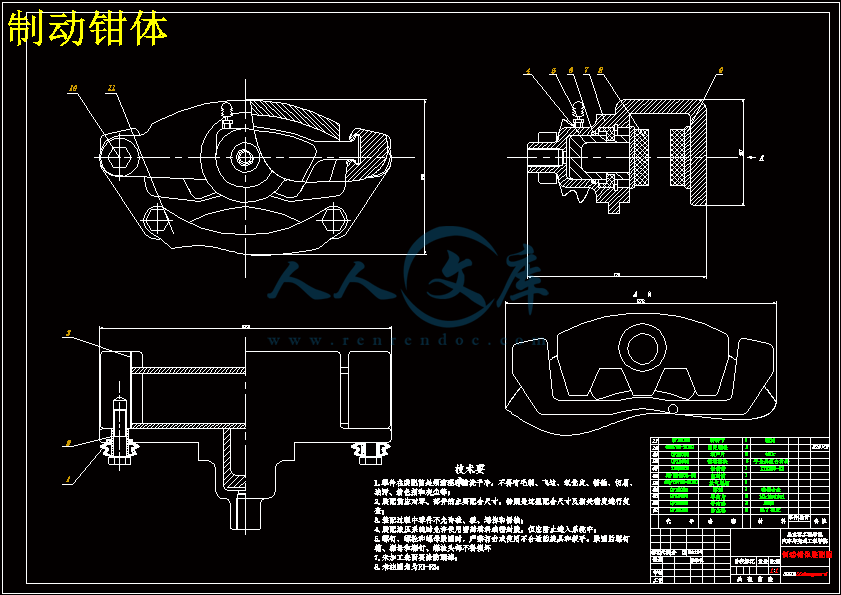
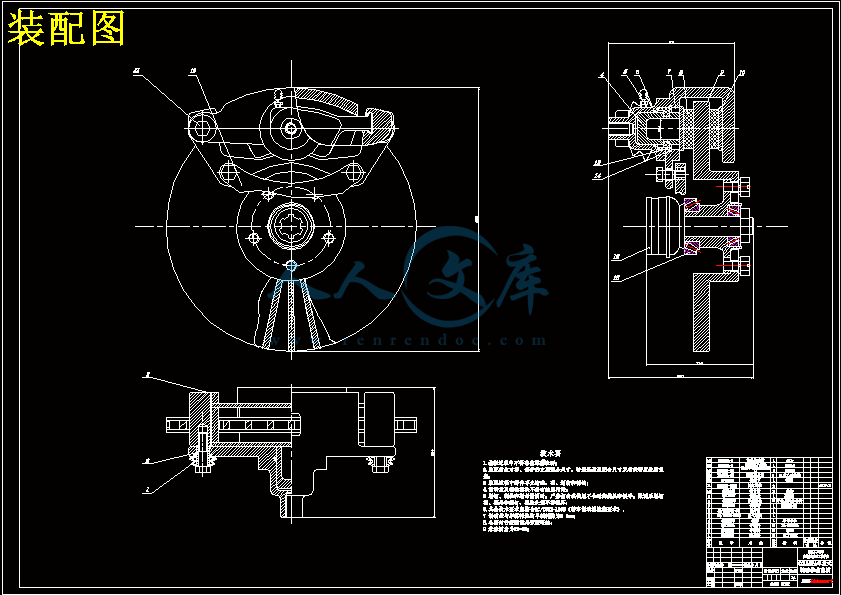
目 录
摘要I
AbstractII
第1章 绪论1
1.1制动器的介绍与特点1
1.2国内汽车盘式制动器应用情况2
第2章 制动器的设计原则4
2.1汽车盘式制动器4
2.2卡罗拉盘式制动器的结构与工作原理4
2.3 制动器设计的一般原则6
2.3.1制动驱动机构的选择7
2.3.2制动管路的选择7
2.4 本章小结8
第3章 制动器结构设计9
3.1 丰田COLLORA的主要技术参数9
3.2 制动系统的主要参数选择及计算8
3.2.1同步附着系数9
3.2.2制动强度和附着系数利用率11
3.2.3制动器最大制动力矩12
3.2.4 制动器因数12
3.3 制动器的结构参数与摩擦系数13
3.3.1制动盘结构参数13
3.3.2摩擦衬块的结构参数14
3.4 制动器主要零件的结构设计16
3.4.1制动底板16
3.4.2制动轮缸16
3.4.3制动盘16
3.4.4制动钳16
3.4.5摩擦材料16
3.4.6摩擦衬块18
3.4.7制动摩擦衬片18
3.4.8制动间隙18
3.5本章小结18
第4章 制动系统驱动机构的设计19
4.1 制动轮缸设计19
4.1.1 制动轮缸直径与工作容积19
4.1.2 制动轮缸活塞宽度与筒壁宽度20
4.2 制动主缸设计21
4.2.1 制动主缸直径与工作容积21
4.2.2 制动主缸活塞宽度与筒壁宽度22
4.3制动主缸行程的计算22
4.4制动踏板力与踏板行程23
4.5真空助力器24
4.6制动力分配调节装置25
4.7 本章小结26
结论27
参考文献28
致谢29
附录30
摘 要
国内汽车市场迅速发展,随着汽车保有量的增加,带来的安全问题也越来越引起人们的注意,而制动系统则是汽车主动安全的重要系统之一。因此,如何开发出高性能的制动系统,为安全行驶提供保障是我们要解决的主要问题。另外,随着汽车市场竞争的加剧,如何缩短产品开发周期、提高设计效率,降低成本等,提高产品的市场竞争力,已经成为企业成功的关键。
主要根据已有的丰田COLLORA车辆的数据对制动系统进行设计。首先介绍了汽车制动系统的结构、分类,并通过对盘式制动器的结构及优缺点进行分析。确定方案采用液压双回路盘式制动器。进行前后制动器、制动主缸的设计计算,主要部件的参数选择及制动管路布置形式,确立了COLLORA车制动器比较完整的设计。
关键词:制动器;盘式制动器;COLLORA;活塞;同步系数
ABSTRACT
The rapid development of the domestic vehicle market, However, with increasing of vehicle, security issues are arising from increasingly attracting attention, the braking system is one of important system of active safety. Therefore, how to design a high-performance braking system, to provide protection for safe driving is the main problem we must solve. In addition, with increasing competition of vehicle market, how to shorten the product development cycle, to improve design efficiency and to lower costs, to improve the market competitiveness of products, and has become a key to success of enterprises.
This paper mainly introduces the design of braking system ,which based on the data of brake system used in callola. Fist of all, braking system’s development, structure and category are shown, and according to the structures, virtues and weakness of drum brake and disc brake, analysis is done. At last, the plan adopting hydroid two-backway brake with front disc and rear drum. Besides, this paper also introduces the designing process of front brake and rear brake, braking cylinder, parameter’s choice of main components braking and channel settings.
Key words: Braking;Brake Disc; Collora; Piston;Synchronous Coefficient
1.1制动器的介绍与特点
现在,盘式制动器在汽车上已经越来越多地被采用,特别是在轿车上已被广泛采用。盘式制动器在液力助力下制动力大且稳定,在各种路面都有良好的制动表现,其制动效能远高于鼓式制动器,而且空气直接通过盘式制动盘,故盘式制动器的散热性很好。但是盘式制动器结构相对于鼓式制动器来说比较复杂,对制动钳、管路系统要求也较高,而且造价高于鼓式制动器。
汽车制动系可分为行车、驻车、应急、辅助内部分装置。任何制动装置都具有供能装置、控制装置、传动装置和制动器四个部分组成。较为完善的制动系还具有制动力调节装置,以及报警装置、压力保持装置。
盘式制动器多用于汽车的前轮,有不少车辆四个车轮都用盘式制动器。制动盘装在轮级上、与车轮及轮胎一起转动。当驾驶员进行制动时,主缸的液体压力传递到盘式制动器。该压力推动摩擦衬片靠到制动盘上,阻止制动盘转动。
现在,盘式制动器在汽车上已经越来越多地被采用,特别是在轿车上已被广泛采用,在很多中高级轿车上,前后轮都已经采用盘式制动器。盘式制动器在液力助力下制动力大且稳定,在各种路面都有良好的制动表现,其制动效能远高于鼓式制动器,而且空气直接通过盘式制动盘,故盘式制动器的散热性很好。但是盘式制动器结构相对于鼓式制动器来说比较复杂,对制动钳、管路系统要求也较高,而且造价高于鼓式制动器。 第2章 制动器的设计原则
汽车制动系统总体方案设计,主要涉及制动器的结构型式选择,制动驱动机构的结构型式选择,制动管路布置结构型式的选择等三个方面。本章将就这三个方面的问题进行分析论证
2.1汽车盘式制动器
按摩擦副中固定元件结构,盘式制动器可分为钳盘式和全盘式。
固定钳盘式在汽车上用的最早(50年代就开始使用),优点是:除活塞和制动块外无滑动件,这易保证钳的刚度,易实现从鼓式到盘式的改进,也能适用分路系统的要求。
近年来,由于汽车性能要求的提高,固定钳盘式的缺点,暴露较明显,因而导致浮动钳(特别是滑动钳)的迅速发展。首先,固定钳至少要有两个油缸分置于制动盘两侧,所以须有横跨的内部油道或外部油道来连通,这就使制动器的径向和轴向尺寸加大,布置也较难;而浮动钳的外侧无油缸,可将制动器进一步移进轮毂;其次,在严酷的使用条件下,固定钳容易使制动液温度过高而汽化,浮动钳由于没有跨越制动盘的油道或油管,减少了受热机会。所以制动温度可以比固定钳低30-50度,又采用浮动钳可将活塞和油缸等精密件减去一半,造价大为降低。
综合以上各项,参照所给参数以现代汽车上实际采用的型式,确定本设计的前轮制动器为浮动钳盘式制动器。
2.2卡罗拉车盘式制动器的结构与工作原理
浮钳盘式制动钳的工作原理:如图2.2所示,制动钳壳体2用螺栓5与支架1相连接,螺栓5兼作导向销。支架1固定在前悬架焊接总成(亦称车轮轴承壳体)的法兰板上,壳体2可沿导向销与支架作轴向相对移动。支架固定在车轴上,摩擦块11和12布置在制动盘13的两侧。制动分泵8设在制动钳内。制动时,制动钳内油缸活塞8在液压力作用下推动内摩擦块12,压靠到制动盘内侧表面后,作用于分泵底部的液压力使制动钳壳体在导向销上移动,推动外摩擦块11压向制动盘的外侧表面。内、外摩擦块在液压作用下,将制动盘的两侧面紧紧夹住。由于制动盘是紧固在前轮毂上的,因此实现了前轮的制动。
前制动器的制动间隙是自动调节的。它是利用分泵活塞密封圈4的弹性变形来实现的。制动时,橡胶密封圈变形,制动一结束,密封圈恢复原状,活塞在弹性作用下回到原位。在制动盘和内、外摩擦块磨损后引起制动间隙变大,超过活塞8的设定行程时,活塞在制动液压力作用下克服密封圈的摩擦阻力继续向前移,直到完全制动为止。活塞和密封圈之间的相对位移补偿了过量的间隙,制动间隙一般单边
为0.05-0.15mm。内、外摩擦块的材料采用以石棉为主、混合树脂并与树脂结合的材料与钢板通过螺栓连接在一起制成的。
2.3制动器设计的一般原则
1 制动器效能,指在良好路面上,汽车以一定初速度制动到停车的制动距离或制动时汽车的减速度。在评比不同结构形式的制动器效能时,常用一种称为制动效能因数的无因次指标。制动效能因数的定义为:在制动鼓和制动盘的作用半径上所得到的摩擦利于输入力之比。
2 制动器效能恒定性,即汽车高速行使或下长坡连续制动时汽车制动效能保持的程度。如前所述,影响摩擦因数的因素包括摩擦副材料、摩擦副表面温度和水湿程度。因为制动过程是及时把汽车行驶的动能通过制动器吸收转化为热能,所以制动器温度升高后能否保持在冷状态时的制动效能,已成为设计汽车制动器时要考虑的一个重要问题。由于领蹄的效能因数大于从蹄,稳定性却比从蹄差,因此各种鼓式制动器的效能因数取决于两蹄的效能因数,故就整个鼓式制动器而言,也在不同程度上存在着效能本身与其稳定性的矛盾。而盘式制动器的制动效能最为稳定。
要求制动器的热稳定性好,除选择其效能因数对摩擦系数敏感性较低的制动器类型外,还要求摩擦材料有较好的抗热衰退性和恢复性,并且应使制动鼓(制动盘)有足够的热容量和散热能力。
3 制动器间隙调整,是汽车保养作业较为频繁的项目之一。故选择调整装置的结构形式和安装位置必须保证调整操作方便。最好采用间隙自动装置。
4 制动器的尺寸和质量。随着现代汽车车速的日益提高,处于汽车行驶稳定性的考虑,轮胎尺寸往往选择较小。这样,为了保证所要求的制动力矩而确定的制动鼓(制动盘)直径就可能过大而难以在轮毂内安装。因而应选择尺寸小而效能高的制动器形式。对于高速轿车,为提高制动时的稳定性,在前悬架(独立悬架)设计中,一般采用较小的主销偏移距。为此,前制动器位置有时不得不外移到更靠近轮毂,导致其布置困难。车轮制动器为非簧载质量,故应尽可能减轻其质量,以改善行驶平顺性。 第3章 制动器结构设计
3.1 丰田COLLORA的主要技术参数
车轮制动器是行车制动系的重要部件。按GB7258-2004的规定,行车制动
必须作用在车辆的所有的车轮上。
在制动器设计中需预先给定的整车参数如表3.1所示
表3.1 丰田卡罗拉整车参数
已知参数 车型2.0LGLX
轴距L(mm) 2600
整车整备质量(Kg) 1335
满载质量(Kg) 1805
最小离地间隙(mm) 160
最大扭矩(N·m) 173
3.2 制动系统的主要参数选择及计算
本次设计是以COLLORA拉汽车的制动系统为研究对象,结论为:
1、对汽车制动器的结构和形式进行分析;
2、对汽车的制动力分配系数进行确定;
3、对制动强度和附着系数利用率、制动器最大制动力矩进行了计算分析;
4、根据现有资料对制动器的结构进行了设计并进行了相关的校核;
5、完成了前、后制动器装配图、制动轮缸装配图、制动管路布置图、相关零件图的绘制;
6、对液压管路的布置进行了设计;
7、对制动轮缸和制动主缸的主要结构进行了设计和校核。
由于是第一次接触制动系统设计经验欠缺水平有限,设计过程中难免有缺陷和不足。特别是对于现在汽车制动系统中应用越来越广泛的ABS系统没有深入的了解,需要在以后的工作和学习中这些弥补不足和缺陷。
参考文献
[1]方泳龙.汽车制动理论与设计[M].北京:国防工业出版社,2005.
[2]刘惟信.汽车制动系统的结构分析与设计计算[M].北京:清华大学出版社,2004.
[3]王望予.汽车设计[M].北京:机械工业出版社,2006.
[4]余志生.汽车理论[M].北京:机械工业出版社,2006.
[5]陈家瑞.汽车构造(下)[M],机械工业出版社:2005.
[6]凤勇.汽车机械基础[M].北京:人民交通出版社,2005.
[7]刘品,李哲.机械精度设计与检测基础[M].哈尔滨:哈尔滨工业出版社,2005:
[8]刘惟信.汽车设计[M].北京:清华大学出版社,2001.
[9]齐晓杰,安永东,齐英杰.汽车液压、液力与气压传动技术[M].北京:化学工业出版社,2005.
[10]程国华.汽车制动系统发展漫谈[J]:汽车运用,2003,5(6).
[11]刘彬.汽车制动系统使用中的误区[J]:汽车运用,2003,9(1).
[12]应之丁,吴萌岭,王文强,张为民.制动缸密封件的设计分析[J]:机车车辆工艺,1999,6(5).
[13]朱旬,金海东.轿车制动主缸结构浅析[J]:汽车研究与开发,1999,4(8).
[14]陈步童.微型汽车制动系统常见故障诊断与检修[J]:无锡职业技术学院学报,
2003,8(3).
[15]胡兴军,白杉.汽车制动系统电子化技术[J],商用汽车,2004,8(5).
[16]全国文献工作标准化技术委员会.GB/T 12676-1999 中国标准书号[S].北京:中国标准出版社,1999.
[17]全国文献工作标准化技术委员会第七分委员会.GB 5763-1998 中国标准书号[S].北京:中国标准出版社,1998.
[18]Journal of Materials Engineering and Performance[J],Microstructure and detachment mechanism of friction layers on the surface of brake shoes 2003.
[19]Influence of the state of the mating friction elements of the drum brake on the outer thermal field[J]:Engineering transaction, 2002.