【温馨提示】 购买原稿文件请充值后自助下载。
[全部文件] 那张截图中的文件为本资料所有内容,下载后即可获得。
预览截图请勿抄袭,原稿文件完整清晰,无水印,可编辑。
有疑问可以咨询QQ:414951605或1304139763
摘 要
机械手是在机械化,自动化生产过程中发展起来的一种新型装置。机械手虽然目前还不如人手那样灵活,但它具有能不断重复工作和劳动,不知疲劳,不怕危险,抓举重物的力量比人手力大的特点,因此,机械手已受到许多部门的重视,并越来越广泛地得到了应用。
在机械加工中,大部分零件都要进行多种工序加工。在一般数控机床的整个加工过程中,真正用于切削的时间只占整个工作时间的30%左右,其余的大部分时间都花在安装、调整刀具、装卸、搬运零件和检查加工精度等辅助工作上。自动换刀装置是数控加工中心在工件的一次装夹中实现多道工序加工不可缺少的装置。为充分发挥机床的作用,数控中心均配有自动换刀装置。
本课题重点在于镗铣加工中心换刀机械手的结构设计。目前工业机械手主要用于机床加工、铸造、热处理等方面,无论数量,品质还是性能方面都不能完全满足工业发展的需要。本课题重点解决的问题:换刀机械手部件的结构设计,对关键零件进行校核以及尺寸的优化选取。
主要设计内容有:
(1)设计镗铣加工中心换刀机械手部件的结构,传动系统以及驱动系统,使其能够满足快速,平稳,准确换刀的功能。
(2)完成重要零件的设计,主要包括齿轮的设计,轴的设计,手指的设计。使用Pro/E对所有换刀机械手零件进行三维建模,并建立总装模型。
(3)用AutoCAD画出换刀机械手重要零部件的二维图纸。
关键词:镗铣加工中心;结构设计;换刀机械手;伸缩回转式单臂双爪机械手。
Abstract
The robot is a new device developed in the mechanization and automation of the production process. Although the robot is not as staffing flexibility, but it has repeated the work and labor, I do not know fatigue, not afraid of danger, the the snatch weight of force than manual force, Therefore, the robot has been subject to many sectors, and increasingly has been applied more widely.
In machining, most of the parts should be carried out a wide range of machining processes. Whole process in general CNC machine tools for cutting real time accounted for only about 30% of the entire working time, most of the rest of the time is spent on installation, adjustment tool, loading and unloading, handling parts and check processing accuracy auxiliary work on Automatic tool changer CNC machining center in one clamping of the workpiece to achieve multi-channel processing indispensable device. In order to give full play to the role of the machine tool, CNC centers are equipped with automatic tool changer.
The focus of this project is boring and milling machining center blade structural design of the robot. Industrial robot is mainly used for machining, casting, heat treatment, regardless of the quantity, quality or performance are not fully meet the needs of industrial development. Focused on solving the problem of the subject: A tool of the structural design of the robot components, select the check key parts and size optimization.
The main design elements:
(1) Design milling centers gripper parts of the structure, the transmission system and drive system to enable it to meet the fast, smooth and accurate tool.
(2) the completion of the important parts of the design, including the choice of gear design, the design of the shaft bearing. Pro / E 3D modeling, and all parts of gripper
assembly model.
(3) AutoCAD to draw the gripper important parts of the two-dimensional drawings.
Keywords: boring and milling machining center; structural design; gripper; retractable rotary arm claw robot.
目 录
摘 要
Abstract
第1章 绪论 1
1.1选题的背景和意义 1
1.2国内外研究现状和发展趋势 1
1.2.1机械手简介 1
1.2.2 机械手的分类 3
1.2.3工业机械手研究趋势 6
1.3 换刀机械手研究意义 7
1.4 设计的内容和思路 7
第2章 镗铣加工中心换刀机械手总体设计 8
2.1 换刀机械手的工作原理分析 8
2.2 机械手的平稳性 10
2.3 机械手的运动特性 11
2.4 换刀机械手方案的确定 12
第3章 换刀机械手的总体方案设计 12
3.1手爪部分设计 12
3.2 机械手手臂的设计 13
3.3 机械手传动方式的选择 14
3.3.1机械手转过180度的传动机构选择 14
3.3.2 主轴以及机械手上下伸缩的传动机构设计 16
3.4 换刀机械手驱动机构的选择 18
第4章 换刀机械手的结构设计及尺寸确定 19
4.1 手指结构设计及计算 19
4.1.1 手指夹紧力的计算 19
4.1.2 手指部分的相关校核 21
4.2手臂的弯曲变形 23
4.3 轴与机械手配合部分的直径的选取 25
4.4 机械手转过180度的驱动机构设计 26
4.5 设计参数 29
第5章 总结与展望 30
参考文献 31
致 谢 33
第1章 绪论
1.1选题的背景和意义
机械制造业是一个国家最基础的行业,为整个国民经济提供技术装备,其发展水平是国家工业化程度的主要指标之一。在机械工业中,应用机械手的意义可以概括如下:

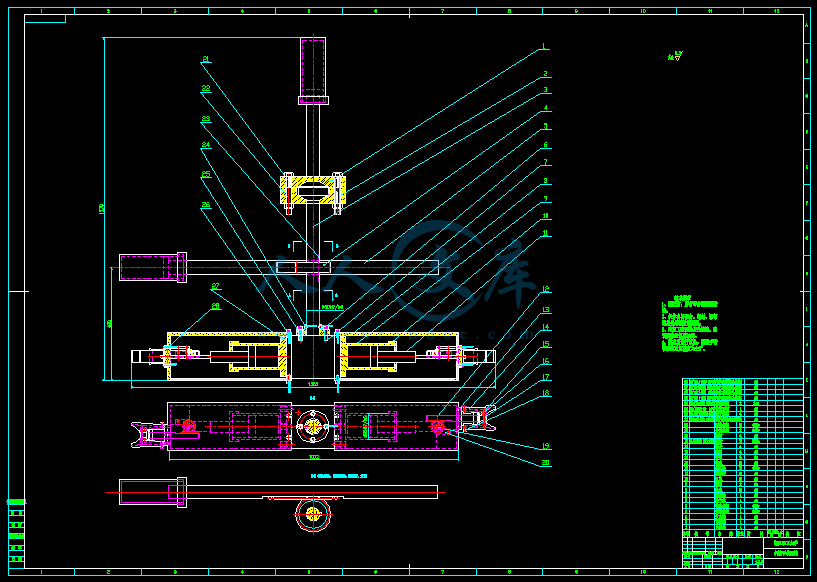

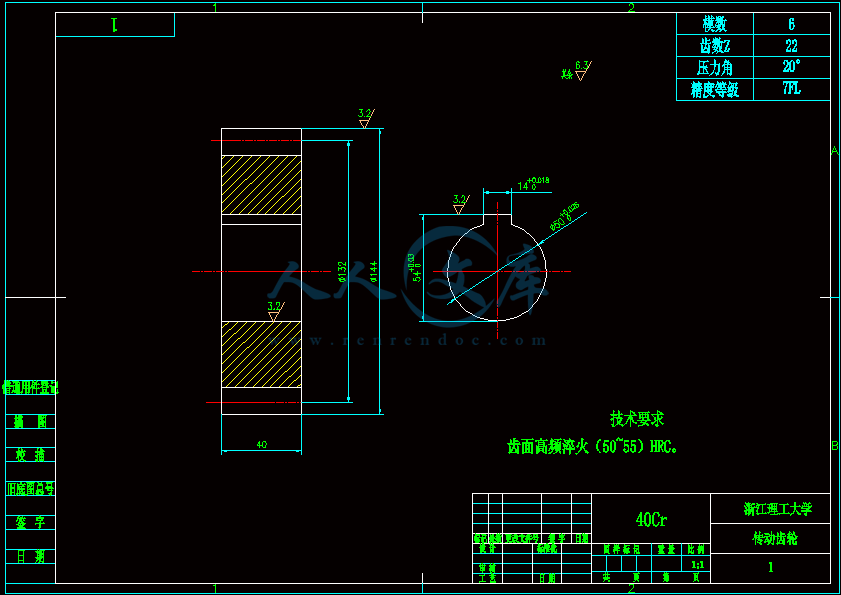
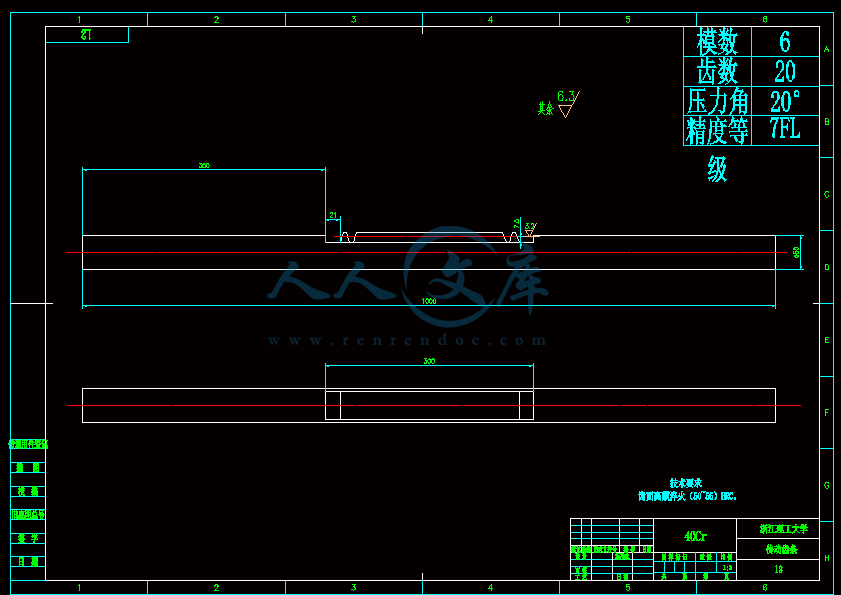

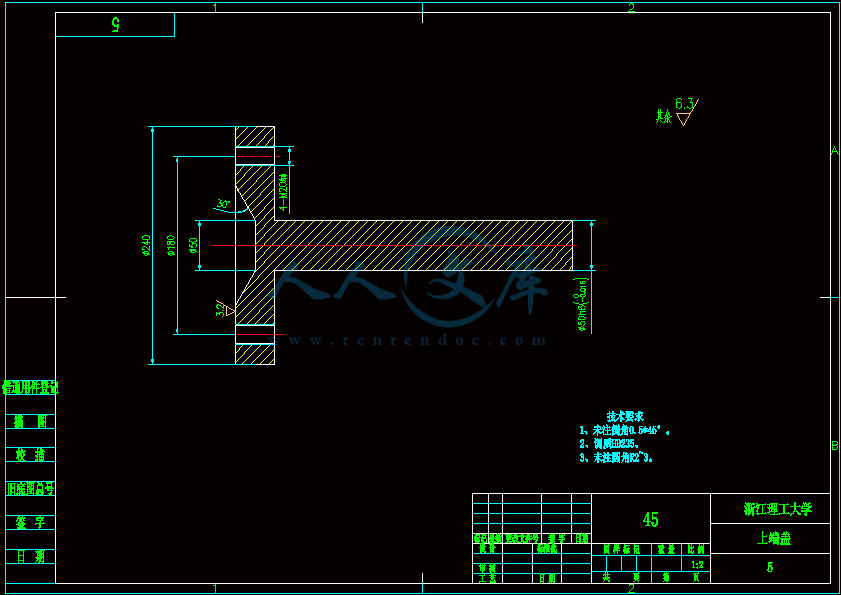
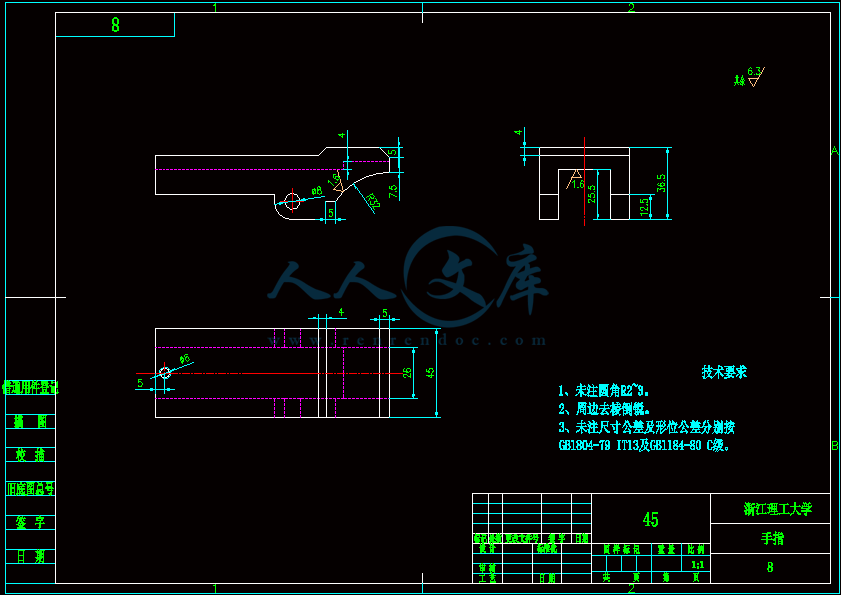
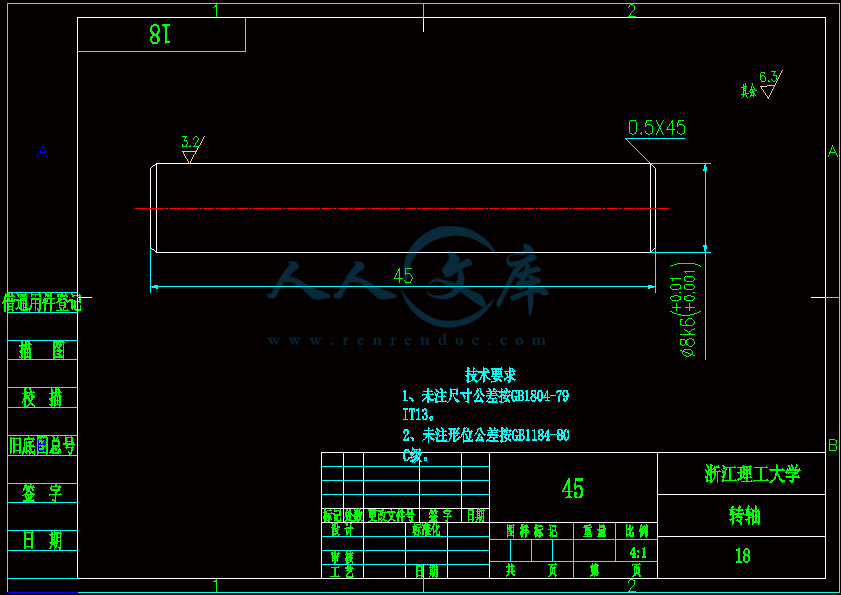

