基于ANSYS的框架式汽车大梁校正仪设计
71页 28000字数+说明书+任务书+开题报告+CATIA三维+6张CAD图纸【详情如下】
ANSYS文件.rar
CATIA三维建模.rar
举升臂.dwg
任务书.doc
卡钳.dwg
基于ANSYS的框架式汽车大梁校正仪设计开题报告.doc
基于ANSYS的框架式汽车大梁校正仪设计说明书.doc
底板.dwg
拉塔.dwg
指导记录.doc
支撑轴.dwg
校正仪爆炸图.dwg
校正仪装配图.dwg
框架式校正仪装配图.dwg
相关材料.doc
过程管理封皮.doc
题目审定表.doc
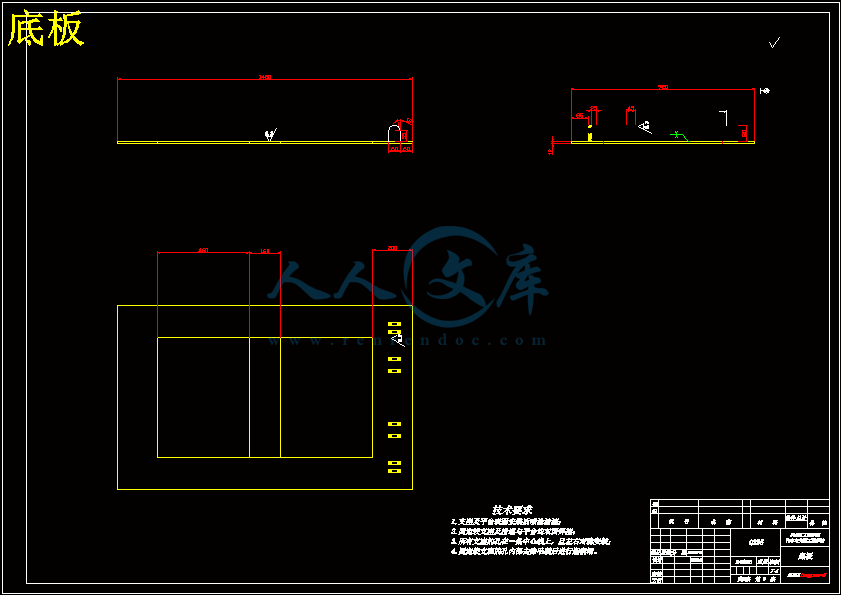

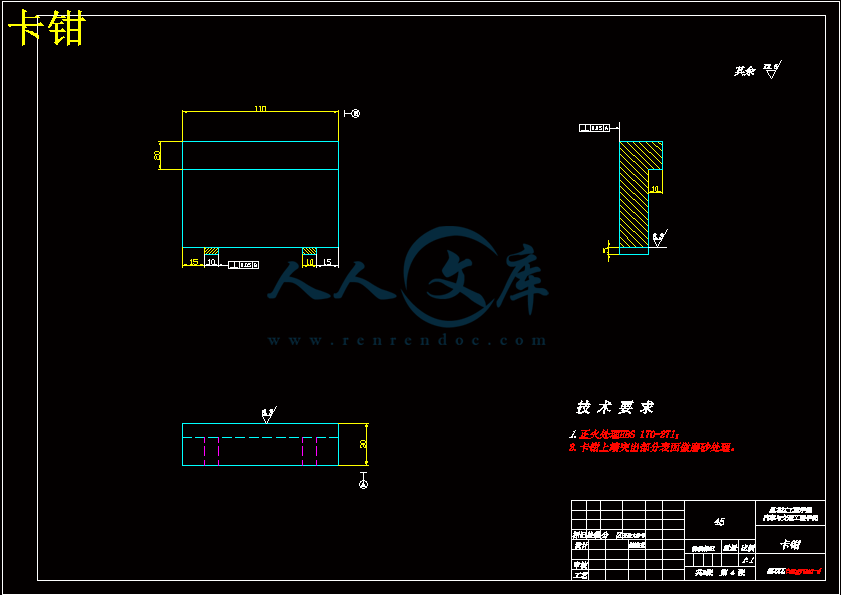

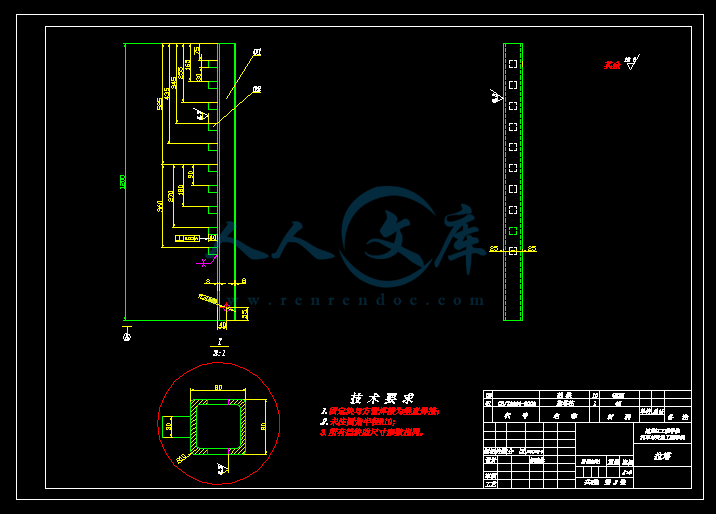
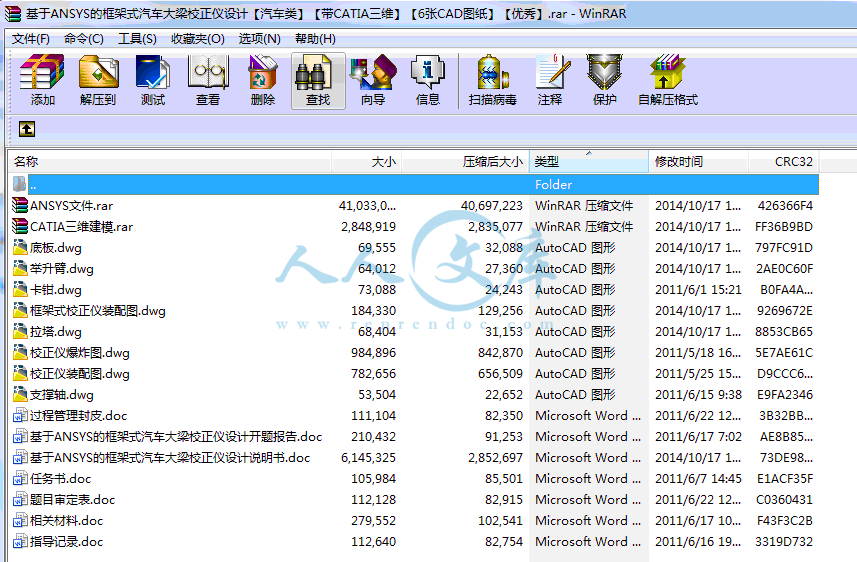

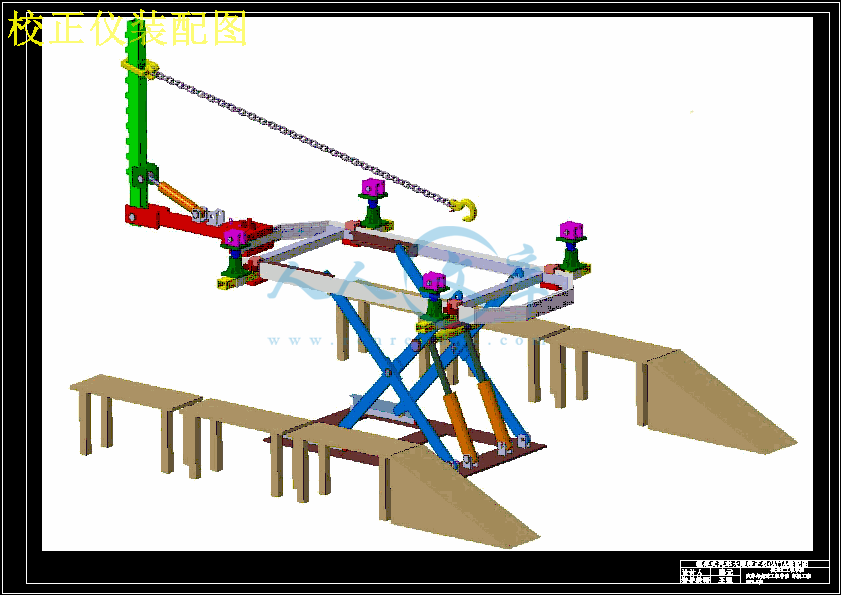
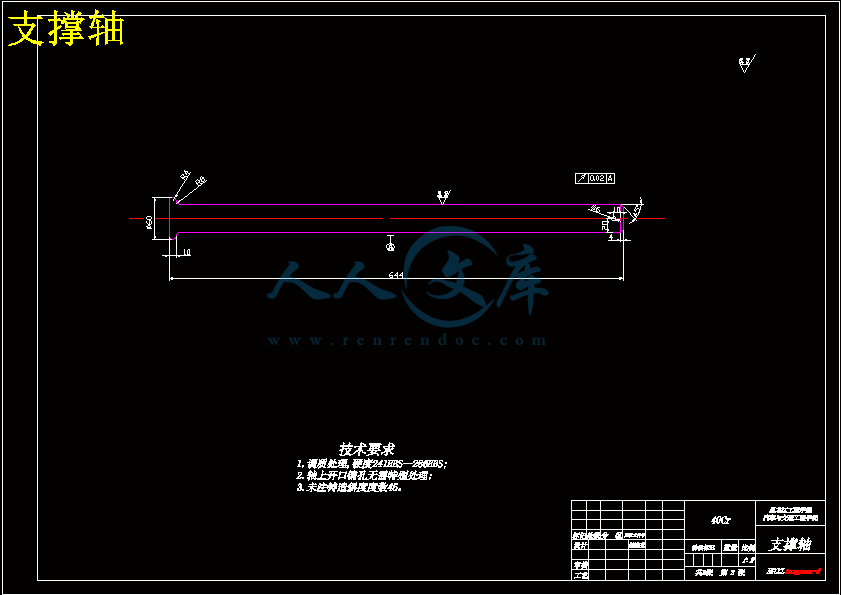
目 录
第1章 绪论1
1.1 选题背景,研究目的及意义1
1.2 国内外研究现状1
1.2.1 大梁校正仪的发展历史1
1.2.2 国内外研究状况及结果2
1.3 研究内容及研究方法2
第2章 校正仪的整体结构设计4
2.1 简述框架式汽车大梁校正仪工作原理4
2.2 举升机构主要结构确定4
2.2.1 举升机构整体结构形式及基本组成4
2.2.2 举升机构各零部件安装位置及润滑5
2.3 举升平台及定位夹具主要结构确定5
2.3.1 举升平台整体结构形式及基本组成5
2.3.2 定位夹具整体结构形式及基本组成6
2.4 拉塔的主要结构确定6
2.4.1 拉塔横梁处整体结构形式及基本组成6
2.4.2 拉塔柱的结构形式及基本组成7
2.5 其它附件7
2.6 确定框架式大梁校正仪各结构尺寸及材料7
2.6.1 建立待修汽车基本参数模型8
2.6.2 校正仪底部结构部分主要尺寸及材料的确定8
2.6.3 校正仪中间结构部分尺寸及材料的确定8
2.6.4 校正仪上部平台结构尺寸及材料的确定9
2.6.5 定位夹具的尺寸及材料的确定11
2.6.6 拉塔组件的尺寸及材料的确定12
2.6.7 方凳及斜坡板凳的尺寸确定13
2.7 设备各部件质量的估算及设计举升质量13
2.7.1 估算拉塔组件的质量14
2.7.2 估算平台上设备的质量14
2.7.3 估算平台中部的质量14
2.7.4 估算底板处的质量15
2.7.5 实际设计举升质量15
2.8 本章小结15
第3章 校正仪的力学分析及校核16
3.1 双铰接剪刀式举升机构的力学模型16
3.1.1 举升机构力学模型建立与分析16
3.1.2 举升机构主要关系参数的确定17
3.2 液压机构力的分析与计算17
3.2.1 确定载荷与液压缸推力的关系17
3.2.2 计算液压缸的推力18
3.3 举升机构的力学分析与计算19
3.3.1 举升机最低状态时,各臂受力情况19
3.3.2 举升机举升到最高位置时,各臂受力情况20
3.4 定位夹具及拉塔的力学分析与计算22
3.4.1 定位夹具的受力分析22
3.4.2 拉塔的受力分析22
3.5 主要零部件的强度校核23
3.5.1 举升臂AOB的强度校核23
3.5.2 举升臂COD的强度校核25
3.5.3 液压缸上端支承轴的强度校核27
3.5.4 连接举升臂销轴的强度校核27
3.5.5 平台内横梁的强度校核28
3.5.6 定位夹具的强度校核29
3.5.7 定位夹具支撑横梁的强度校核30
3.5.8 拉塔的强度校核31
3.5.9 拉塔处液压缸支撑销轴的强度校核32
3.6 本章小结33
第4章 校正仪液压系统的选择与计算34
4.1 液压系统的选择34
4.1.1液压系统的介绍34
4.1.2液压系统的选型34
4.2 液压系统的计算35
4.2.1 举升处液压缸行程的计算35
4.2.2 举升处液压系统工作压力的计算36
4.2.3 关于拉塔处液压系统的相关选择36
4.3 本章小结36
第5章 校正仪三维建模与整机装配37
5.1 CATIA软件简介37
5.2 利用CATIA进行三维建模38
5.2.1 底坐板的建立38
5.2.2 举升臂AOB的建立39
5.2.3 液压缸支承轴的建立39
5.2.4 上平台的建立40
5.2.5 夹具的建立40
5.2.6 拉塔柱的建立42
5.3 整机装配42
5.3.1 CATIA装配功能概述43
5.3.2 装配的CATIA零件图43
5.3.3 CATIA整机装配图及爆炸图48
5.4 本章小结50
第6章 校正仪主要零部件有限元分析51
6.1 ANSYS有限元分析软件介绍51
6.2 ANSYS与CATIA接口的建立51
6.3利用ANSYS对主要零部件进行分析52
6.3.1定位夹具卡钳的有限元分析52
6.3.2液压缸支撑轴的有限元分析56
6.3.3举升臂的有限元分析59
6.3.4拉塔柱的有限元分析62
6.4 本章小结65
结论66
参考文献67
致谢68
绪 论
选择背景、研究目的及意义
随着汽车市场的不断发展与壮大,与之相协调的汽车维修行业也迅速发展起来。目前在汽车事故中对大梁及钣金的修复十分常见。而随着对售后服务的要求的不断提升,也为了更好的发展企业,各维修厂家已经开始了激烈的服务竞争。汽车大梁校正仪是在因交通事故碰撞所致车身损坏,以及大梁变形等的技术数据恢复中重要的维修设备。在以往的事故后维修时,很多企业选择了更换零部件,但是这样往往会增加客户的损失及保险公司的负担。汽车大梁校正仪的出现避免了高额的更换费用,这样既减少了顾客的损失,也可促进制造设备企业市场的发展。利用大梁校正仪专业设备方可保证对汽车大梁的维修的质量水平。然而对于在维修中为了保证汽车安全的定位,方便的使用,高维修水平等众多关键要素,必须设计质量及安全可靠的设备。因此,为了满足维修企业对占地空间的要求及保证维修质量。对框架式汽车大梁校正仪进行深入研发将对我国在这一领域发展有实质性的意义。本课题基于计算机仿真平台,应用CAD/CAE领域比较领先的设计软件AutoCAD进行二维草图绘制,使用了当前先进的三维设计软件CATIA进行三维建模及整机装配,在产品投入生产之前运用ANSYS软件进行质量分析,可及时发现并更改设计中的缺陷,完善设计方案,减少产品开发周期,提高研发的质量和效率,为此设备的生产实际提供一些有价值的理论支持。
1.2 国内外研究现状
1.2.1 大梁校正仪的发展历史
汽车大梁校正仪的发展已经有了将近30年的历史。它的出现主要是基于剪式汽车举升机的框架的改装。由于举升机历史较长,技术较成熟,所以在80年代期间,美国及欧洲就率先通过对剪式举升机的改造而研发出框架式大梁校正仪。九十年代欧洲通过出口到中国市场逐渐把它的产品推向亚洲地区。90年代中期,在我国山东地区逐渐出现了很多此类设备制造企业,目前在国内市场发展史已经是标新立异。经过几十年的发展,剪式举升机及一些定位夹具已经更新了很多代,框架式汽车大梁校正仪至今也经历了许多变化与改进。目前欧美已经将其产品出口至全世界,我国山东地区少数企业也已经打破传统局面,将设备出口至芬兰等北欧国家。而框架式大梁校正仪使用方便,占地空间较小,也受到很多实力雄厚的特约维修站的欢迎。 关于框架式汽车大梁校正仪的设计,本产品参照了目前市场上销售较好的此类产品,同时根据常见车型的相关参数设计相关尺寸等参数。框架式汽车大梁校正仪操作方便,占地空间较小,容易维修,受到众多中小维修企业的欢迎,适合我国目前汽车市场的现状和发展趋势,在我国及欧洲市场将有着广阔的发展前景,为一些小型事故碰撞解决修复问题。由于在我国利用计算机CAD/CAE技术对举升机等维修设备的研究起步较晚,一般在90年代初才刚刚开始有产品面试。因此,针对市场目前的状况对大梁校正仪的研究很有实际意义。
框架式汽车大梁校正仪的设计主要完成了以下工作:
(1)通过计算举升机构、定位夹具、拉塔结构及上下平台的尺寸,然后画出二维结构装配图及零件图;
(2)对内外侧举升臂、拉塔处销轴、液压缸支撑轴、拉塔柱、夹具卡钳等进行受力分析计算,通过详细的计算及更改相关尺寸及材料,最终产品的主要零部件强度校核均符合要求;
(3)利用CATIA对其所有零部件进行三维建模,并进行渲染;
(4)利用ANSYS有限元软件对举升臂,定位夹具,拉塔柱,液压缸支撑轴进行有限元分析,经过详细分析以后,我们得到了相关的位移量变形,应力大小等相关数据,最终结果表明本次设计的主要零部件均符合强度要求;
(5)经过分析有限元分析合格后,我们利用CATIA软件对其整个零部件进行虚拟装配,通过使用相关约束、实例化及智能移动等来完成最终装配体,最后在对其进行爆炸分解;
(6)把CATIA中建好的装配图及分解后的爆炸图截图旋转至适当的视角,然后来粘贴到Auto-CAD中。
本次对框架式汽车大梁校正仪的设计参照了了市场上目前较先进的相关产品,并且通过对一些结构的创新使其具有较好的质量水平及技术含量,同时也缩减了产品的成本。并且利用目前较为先进的CAD/CAE软件分析其产品质量,保证产品能够安全可靠的投入到市场当中去。本次设计的内容也对在以后关于大梁校正仪的设计方面提供了相
关的参考。
参考文献
[1 ] 戴冠军.最新客车与轿车车身维修手册[M],北京:中国物资出版社,1996.8.
[2 ] 蒋学祤,蒋崴.汽车维修机工具典型结构[M],北京:人民交通出版社,1994.3.
[3 ] 杜黎蓉,林博正.CATIA V5 三维零件设计[M],北京:人民邮电出版社,2005.9.
[4 ] 王登峰.CATIA V5机械产品精通教程[M],北京:人民交通出版社,2007.4.
[5 ] 程本付.使用通用定位夹具对非承载式车身大梁进行校正[J].汽车维修与保养, 2008.6.?
[6 ] 王庆五,左昉,胡仁喜.ANSYS 10.0机械设计高级应用实例[M],北京:机械工业出版社,2006.1.
[7 ] 天天汽车工作室.轿车车身维修技能实训[M],北京:机械工业出版社,2003.9.
[8 ] 王宏武,魏发孔钢.丝绳承载受力特性分析及计算[J],甘肃科技,2007.9:77-79.
[9 ] 郑鹏鑫J.FJ-25剪式气压举升机的设计[J],机床与液压,2007.3:118-120.
[10] 杨黎明,黄凯,李恩至,陈仕贤.机械零件设计手册[M],北京:国防工业出版社,1993.8.
[11] 张鹏.俯仰升降式立体车库液压系统设计[J],液压与气动,2007.7:10-11.
[12] 周宁.ABSYS机械工程应用实例[M],北京:中国水利水电出版社,2006.3.
[13] 尤春风.CATIA V5高级应用[M],北京:清华大学出版社,2006.1.
[14] 范钦珊.工程力学——普通高等院校[M],北京:清华大学出版社,2005.8.
[15] 孙训方.材料力学(I)第5版[M],北京:高等教育出版社,2009.7.
[16] 杨可桢,程光蕴,李仲生.机械设计基础[M],北京:高等教育出版社,2008.6.
[17] 马兰.机械制图[M],北京:机械工业出版社,2006.5.
[18] 周松鹤,徐烈姮.工程力学[M],北京:机械工业出版社,2007.5.
[19] James.E.Duffy.Collision Repair Fundamentals[M],Singapore:Original edition published by Cengage Learning,2008.9.
[20] Tang Nade.America Multirack 2000 Beam Calibrator[J],Beijing:China Academic Journal Electronic Publishing House,1999.11.
[21] Orbak AY, Turkay OS , Eskinat E,etal.Model reduction in the physical domain[J].Systems Control Eng Proc Inst Mech Eng:Part I,2003.6.
[22] Alhanati FJS.PCP Axial Load:Theory and Lab Result[J],Paper SPE 90153,2004.2