【温馨提示】 购买原稿文件请充值后自助下载。
以下预览截图到的都有源文件,图纸是CAD,文档是WORD,下载后即可获得。
预览截图请勿抄袭,原稿文件完整清晰,无水印,可编辑。
有疑问可以咨询QQ:414951605或1304139763
摘 要
金属压铸是将熔融状态或半熔融状态的合金浇压铸机的压室,在高压力的作用下,以极高的速度充填在压铸模的型腔内,并在高压下使熔融合金冷却而成形的高效益、高效率的精密铸造方法。
根据零件的结构和尺寸设计了完整的模具。设计内容主要包括:浇注系统设计、成型零件设计、抽芯机构设计、推出机构设计以及模体结构设计。根据铸件的形状特点、零件尺寸及精度,选定了合适的压铸机,通过准确的计算并查阅设计手册,确定了成型零件以及模体的尺寸及精度,在材料的选取及热处理要求上也作出了详细说明,并在结合理论知识的基础上,借助于计算机辅助软件绘制了各部分零件及装配体的立体图和工程图,以保障模具的加工制造。
关键词:压铸;压铸模具;镁合金;抽芯
Abstract
Metal casting is molten state or half molten state alloy die-casting machine water pressure chamber, in under the action of high pressure, high speed filling in the pressure of the mold cavity inside, and under high pressure make molten alloy cooling and forming of high benefit, high efficiency of precision casting method.
According to the parts of the structure and size design of a complete mould. Design content mainly includes: gating system design, molding parts design, core-pulling mechanism design, launch mechanism design and die structure design. According to the shape of the casting characteristics, parts size and precision, select the appropriate die casting machine, through accurate calculation and consult the manual design, determines the forming parts and die body size and precision, in material selection and heat treatment requirements also make a detailed description, and in combination with theory based on the knowledge, with the aid of computer aided software rendering each parts and assembly body graphic model and engineering drawing, in order to ensure the mould processing and manufacturing.
Keywords: Die casting; Die casting mould; Magnesium alloy; core-pulling
目 录
摘 要、关键词 I
Abstract、Key words II
目 录 III
一. 引言 1
二、铸件成型工艺的可行性分析……………………………………………….………4
2.1 铸件分析………………………………………………………………..………4
2.2铸件的原材料分析…………………………………………………………………4
2.3成型工艺分析………………………………………………………………………5
三、 压铸机的选择及分型面的设计……………………………………………………6
3.1 估算零件体积和投影面积……………………………………………………6
3.2压铸机的选择………………………………………………………………………6
3.3压铸模分型面的设计………………………………………………………………7
四、浇注系统的设计 ……………………………………………………………………8
4.1 浇注系统的分类及选择 ……………………………………………………8
4.2 内浇口的设计 ……………………………………………………………………9
4.3 直浇道的设计 …………………………………………………………………10
4.4 排溢系统 …………………………………………………………………………12
五、铸件成型尺寸的计算 ………………………………………………………………14
5.1 型腔尺寸计算 …………………………………………………………………14
5.2 型芯尺寸计算 …………………………………………………………………14
5.3 中心距位置尺寸计算 …………………………………………………………15
六、导向与脱模机构的设计……………………………………………………………16
6.1导向机构的作用和设计原则…………………………………………………16
6.2导柱、导套的设计…………………………………………………………………16
6.3脱模推出机构的确定………………………………………………………………18
七、侧向分型与抽芯机构的设计…………………………………………………………20
7.1 斜导柱抽芯机构设计原则………………………………………………………20
7.2 抽芯机构的确定…………………………………………………………………20
7.3 斜导柱抽芯机构的有关参数计算………………………………………………20
7.4 滑块的设计………………………………………………………………………23
7.5 导滑槽的设计……………………………………………………………………23
7.6 锁紧块……………………………………………………………………………24
八、冷却系统设计………………………………………………………………………25
8.1冷却系统的设计原则 ……………………………………………………………25
8.2 温度调节对铸件质量的影响……………………………………………………25
8.3 对温度调节系统的要求…………………………………………………………25
8.4 冷却装置的设计要点……………………………………………………………26
8.5冷却系统设计计算………………………………………………………………26
九、其它结构零部件的设计 …………………………………………………………28
十、小结…………………………………………………………………………………29
注释和参考文献…………………………………………………………………………30
谢辞………………………………………………………………………………………31
一、引言
压力铸造是近代金属加工工艺中,发展较快的一种先进的铸造方法。液态金属在高速高压作用下射入紧锁的模具型腔内,并保压、结晶直至凝固,形成半成品或成品[2]。压力铸造作为一种终形和近终形的成形方法,具有生产效率高、经济指标优良、压铸件尺寸精度高和互换性好等特点。在制造业获得了广泛的应用和迅速的发展,压铸件已成为许多产品的重要组成部分。随着轿车、摩托车、内燃机、电子通信、仪器仪表、家用电器和五金等行业的飞速发展,压铸件的功能和应用领域不断扩大,从而促进了压铸技术不断发展,压铸合金品质不断提高。
在压力铸造中,一般作用于原料上的压力在20~200 MPa,充型时浇口处初始速度为15~70 m/s,充型时间仅为0.01~0.20 s。正是由于这种特殊充型方式及凝固方式,导致压力铸造具有自身独特的特点:
1)可以得到薄壁、形状复杂但轮廓清晰的铸件;
2)铸件精度高、尺寸稳定、加工余量少、表面光洁;
3)铸件组织致密、具有较好的力学性能;
4)生产效率高。压力铸造的生产周期短,一次操作的循环时间约5 s~3 min,这种方法适于大批量生产;
5)压力铸造采用镶铸法可以省去装配工序并简化制造工艺;
6)材料利用率高;

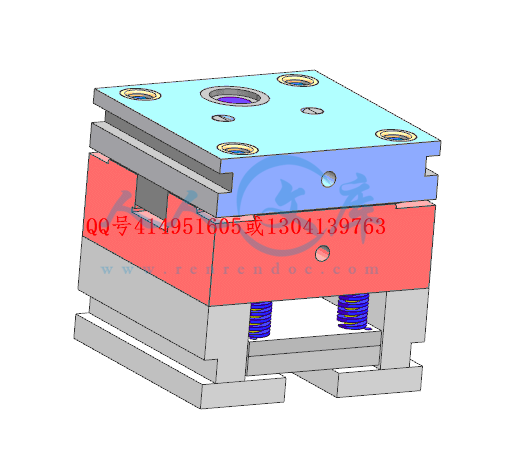
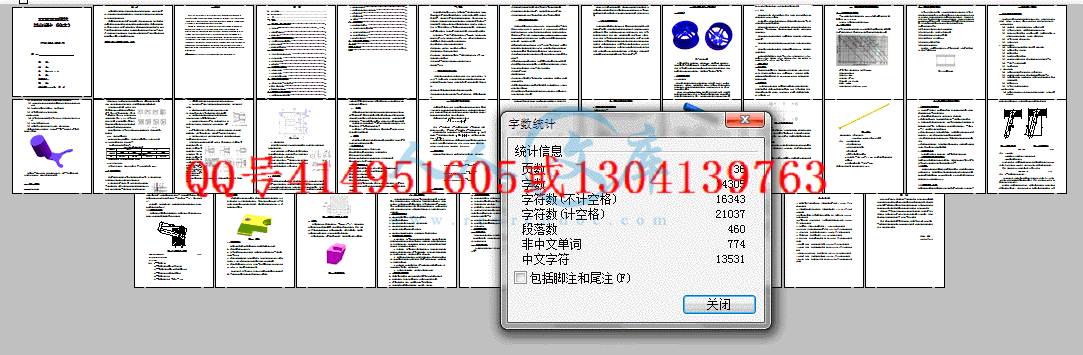
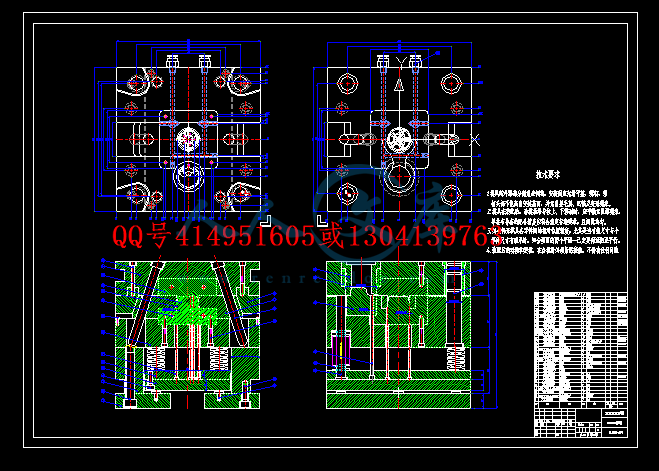
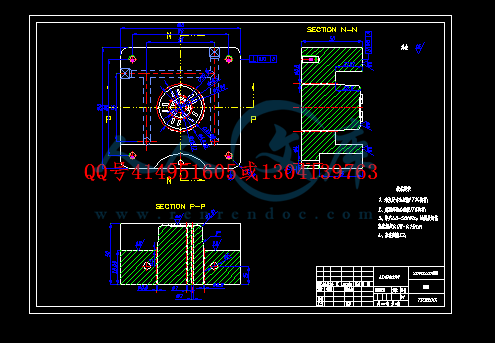