【温馨提示】 购买原稿文件请充值后自助下载。
[全部文件] 那张截图中的文件为本资料所有内容,下载后即可获得。
预览截图请勿抄袭,原稿文件完整清晰,无水印,可编辑。
有疑问可以咨询QQ:414951605或1304139763
摘 要
在现有的三坐标联动数控机床的工作台上再增加一个具有两个旋转自由度的数控回转工作台,将其安装在原有的工作台上,与原有的工作台成为一个整体,成为一个多自由度的回转工作台,即双回转数控工作台。再通过对数控系统的升级(不属于此题范畴),使该机床成为五坐标联动的数控机床。这样的双回转数控工作台不仅可以沿X、Y、Z方向作平行移动,在A、B两轴能同时运动,且能随时停止,在A轴上能够在一定角度内连续旋转,在B轴上可以做360度的连续旋转。不仅可以加工简单的直线、斜线、圆弧,还可适应更复杂的曲面和球形零件的加工。
关键词:数控,回转工作台,五坐标联动,双回转,机床
ABSTRACT
At current three sit the mark connect the number that move the work on the stage controls the machine bed increases a number for having two revolve free degree controls the turn-over work set, will its gearing is in the original work on the stage, with originally possessed of the work set becomes a the whole, becoming the turn-over work set of a many free degrees, namely the double turns round the number controls the work set. Pass again the grade creep( do not belong to this category) that logarithms control system, make the machine's bed become five sit the mark connect the dynamic number controls the machine bed. Such a turn-over number controls the work set can not only make the parallel ambulation along the X, Y, the direction of Z, continuing to revolve in A, B two stalks can at the same time exercise, and can at any time stop, on the A stalk can in the certain angle, canning the 360 degrees of revolving continuously on the B stalk. Can not only process the simple straight line, oblique line, arc, can but also adapt to the more complicated curved face to processes with the spheroid spare parts.
Key words:The numeric controls, Turning round the work set, Five sit the mark; Connect to move, The double turns round, Machine bed
目 录
第1章 绪 论 1
1.1 本课题的研究范围及应解决的主要问题 1
1.2 本课题的研究目的和现实意义. 1
1.3 国内外现有数控发展状况 2
1.4 当代数控发展的主要趋势 3
1.4.1 基于PC的开放式数控系统已得到广泛认可,具有强大的生命力……………………………………………………………………. 5
1.4.2 全数字化是未来数控系统发展的必然趋势. 6
1.4.3 多通道软件体系结构是适应整合数控机床的不二选择. 6
1.4.4 网络化功能已从单一的数据传输向网络监控、维护与管理方向发展. 6
1.4.5 高速高精度控制是数控技术发展的永恒主题. 8
1.4.6 智能化控制是提高数控加工效率的有效手段. 10
1.4.7 CAD/CAM与CNC的集成已成为扩展数控系统功能的重要途径. 10
1.5 数控机床的升级(五轴联动) 11
第2章 电动机的选择与控制 12
2.1 步进电动机的特点与种类 12
2.1.1 步进电动机的特点 12
2.1.2 步进电动机的种类 12
2.2 步进电动机的选择 14
2.3 步进电动机的控制 14
2.3.1 步进电动机的速度控制 14
2.3.2 步进电动机的点—位控制 20
2.3.3 步进电动机的加减速控制 22
第3章 工作台方案的选定 24
3.1 分度工作台 24
3.2 数控回转工作台 25
3.2.1 开环数控转台 26
3.2.2 闭环数控回转工作台 27
3.3 双螺距蜗杆传动 27
第4章 双回转数控工作台结构设计 30
第5章 蜗轮蜗杆设计计算 34
5.1 蜗杆传动输入参数 34
5.2 接触疲劳强度计算 34
5.3 确定蜗轮蜗杆主要尺寸 36
5.4 蜗杆的传动效率 37
5.5 蜗杆蜗轮的精度等级的选择 37
5.6 蜗杆传动的热平衡计算 38
第6章 齿轮设计计算 39
6.1 齿轮设计输入参数 39
6.2 齿轮传动结构形式和布置形式 39
6.3 材料及热处理 39
6.4 齿轮基本参数 40
6.5 齿面接触疲劳强度的校核 43
6.6 齿根弯曲强度的校核 44
第7章 控制系统的设计 46
7.1 单片机 46
7.2 扩展数据存储器 47
7.3 键盘及显示电路的设计 48
7.4 越界报警电路设计 48
7.5 环形分配器的选用 49
7.6 驱动电路的设计 49
7.7 电源电路设计 50
7.8 程序设计 52
第8章 误差补偿分析 59
8.1 成型运动误差补偿概述 60
8.2 基本运动形式的软件补偿 62
8.2.1 直线运动的数控指令修正 63
8.2.2 圆弧运动的数控指令修正 63
第9章 进给系统精度分析 65
9.1 直线轨迹 68
9.2 圆弧轨迹 69
第10章 结 论 71
参考文献 72
英文原文: 73
中文译文: 78
致 谢 82
第1章 绪 论
1.1 本课题的研究范围及应解决的主要问题
随着科学技术的迅速发展,机械产品的形状和结构不断地改进,这就要求机床设备具有较好的通用性和较大的灵活性,以适用生产对象频繁变化的需要。特别是对于航天航空等部门中的加工批量不大、生产周期要求短、改型频繁、形状复杂、精度要求又很高的这类零件的加工,三坐标联动数控机床在这方面起了举足轻重的作用。但是随着高精尖技术要求的不断提高,三坐标联动机床已经不能满足要求。而五坐标联动机床就能满足这些要求。
采用5轴联动对三维曲面零件的加工,可用刀具最佳几何形状进行切削,不仅光洁度高,而且效率也大幅度提高。一般认为,1台5轴联动机床的效率可以等于2台3轴联动机床,特别是使用立方氮化硼等超硬材料铣刀进行高速铣削淬硬钢零件时,5轴联动加工可比3轴联动加工发挥更高的效益。
在现有的三坐标联动的数控机床的工作台上,增加一个旋转工作台(一台带有两个旋转自由度的数控回转工作台),在通过对数控系统的升级改造(不属于此设计范围)使该机床成为五坐标联动的数控机床.
1.2 本课题的研究目的和现实意义.
装备工业的技术水平和现代化程度决定着整个国民经济的水平和现代化程度,数控技术及装备是发展新兴高新技术产业和尖端工业(如信息技术及其产业、生物技术及其产业、航空、航天等国防工业产业)的使能技术和最基本的装备。而数控技术又是当今先进制造技术和装备最核心的技术。当今世界各国制造业广泛采用数控技术,以提高制造能力和水平,提高对动态多变市场的适应能力和竞争能力。此外世界上各工业发达国家还将数控技术及数控装备列为国家的战略物资,不仅采取重大措施来发展自己的数控技术及其产业,而且在“高精尖”数控关键技术和装备方面对我国实行封锁和限制政策。总之,大力发展以数控技术为核心的先进制造技术已成为世界各发达国家加速经济发展、提高综合国力和国家地位的重要途径。 而5轴联动加工又是数控技术发展的重中之重,采用5轴联动对三维曲面零件的加工,可用刀具最佳几何形状进行切削,不仅光洁度高,而且效率也大幅度提高。一般认为,1台5轴联动机床的效率可以等于2台3轴联动机床,特别是使

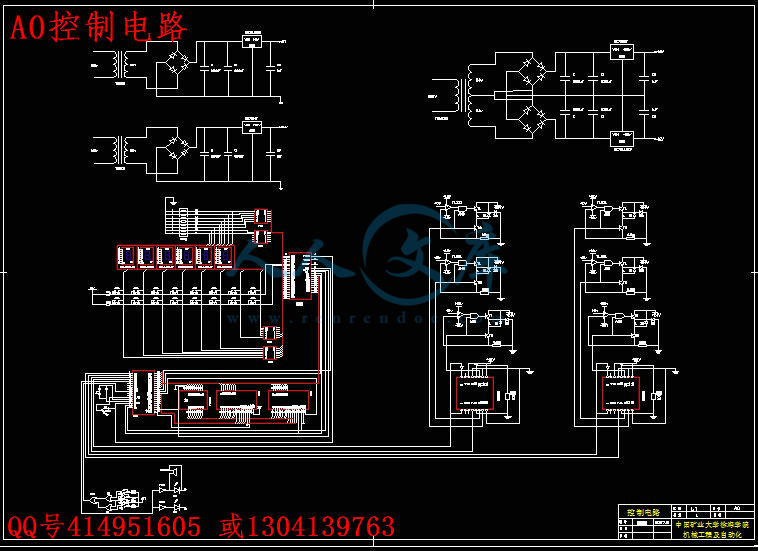



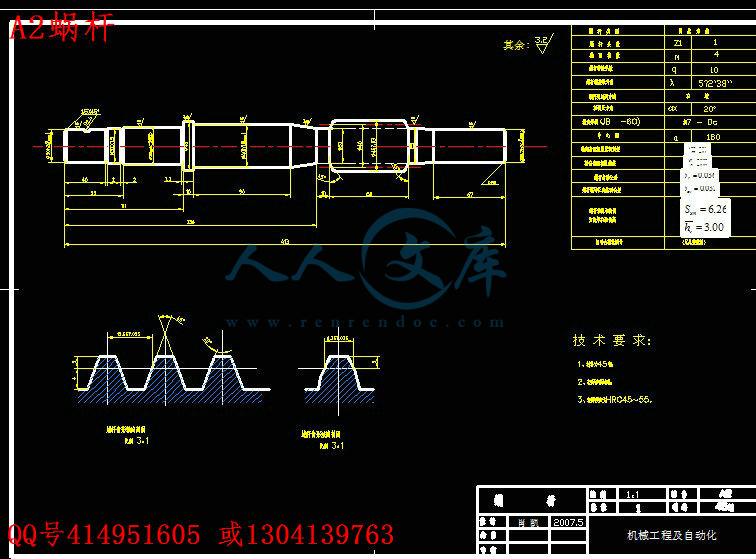
