油箱盖热锻模电解加工工装设计【全套CAD图纸】【原创毕业设计】
收藏
资源目录
压缩包内文档预览:
编号:365155
类型:共享资源
大小:9.17MB
格式:ZIP
上传时间:2014-11-16
上传人:好资料QQ****51605
认证信息
个人认证
孙**(实名认证)
江苏
IP属地:江苏
45
积分
- 关 键 词:
-
油箱盖
锻模
电解
加工
工装
设计
全套
cad
图纸
原创
毕业设计
- 资源描述:
-
【温馨提示】 购买原稿文件请充值后自助下载。
以下预览截图到的都有源文件,图纸是CAD,文档是WORD,下载后即可获得。
预览截图请勿抄袭,原稿文件完整清晰,无水印,可编辑。
有疑问可以咨询QQ:414951605或1304139763
油箱盖热锻模电解加工工装设计开题报告
一、选题的目的及意义
基于电解过程中的阳极溶解原理并借助于成型的阴极,将工件按一定形状和尺寸加工成型的一种工艺方法,称为电解加工。
采用电解加工实现模具加工具有表面质量好,使用寿命长,脱模好,成本低的优点。通过本课题的设计,达到:(1)培养学生综合运用所学的基础课、技术基础和专业课的知识,分析解决工程技术问题的能力;(2)巩固加深扩大基本理论和技能;(3)受高级工程技术人员能力的训练;调研、查阅文献,制定方案、设计、撰写。(4)创新能力和团队精神。
二、国内外研究现状
在经历大约20年的低潮后,从20世纪90年代后期起,电解加工又重新焕发了生机。其研究机构及人员逐渐壮大,应用领域(尤其在航天、航空、军工领域)有所扩展,研究成果及论著数量激增,工艺技术水平及设备性能均达到了一个新的高度。
1工艺技术研究
目前,电解加工工艺技术研究涉及的方向较多,但主要集中在微秒级脉冲电流加工、微精加工、数控展成加工、阴极设计及磁场对电解加工的影响等五大领域。下面分别加以详述。
1.1微秒级脉冲电流加工
自20世纪70年代初起,前苏联、美国、日本、法国、波兰、瑞士、西德等相继开始了对脉冲电流电解加工的研究。在国内,多家单位相继开展了毫秒级脉冲电流电解加工的研究并成功用于工业生产。随着近代功率电子技术的发展,新型快速功率电子开关元件如MOSFET、IGBT等出现,使得有可能实现微秒级脉冲电流电解加工。20世纪90年代以来,微秒级脉冲电流电解加工基础工艺研究取得突破性进展。研究表明,此项新技术可以提高集中蚀除能力,并可实现0.05mm以下的微小间隙加工,从而可以较大幅度地提高加工精度和表面质量,型腔最高重复精度可达0.05mm[1,2,3],最低表面粗糙度可达Ra0.40µm[1],有望将电解加工提高到精密加工的水平,而且可促进加工过程稳定并简化工艺,有利于电解加工的扩大应用。
国内外众多研究机构利用微秒级脉冲电流开展了模具型腔及叶片型面加工、型腔抛光、电解刻字、电解磨等工艺可行性试验以及气门模具生产加工试验[1,3],研究成果进一步从工艺角度证实了上述结论。
1.2微精加工
从原理上而言,电化学加工技术可分为两类:一类是基于阳极溶解原理的减材技术,如电解加工、电解抛光等;另一类是基于阴极沉积原理的增材技术,如电镀、电铸、刷镀等。这两类技术有一个共同点,即材料的去除或增加过程都是以离子的形式进行的。由于金属离子的尺寸非常微小(10-1nm级),因此,相对于其它“微团”去除材料方式(如微细电火花、微细机械磨削),这种以“离子”方式去除材料的微去除方式使得电化学加工技术在微细制造领域、以至于纳米制造领域存在着极大的研究探索空间。从理论上讲,只要精细地控制电流密度和电化学发生区域,就能实现电化学微细溶解或电化学微细沉积。微细电铸技术是电化学微细沉积的典型实例,它已经在微细制造领域获得重要应用。微细电铸是LIGA技术一个重要的、不可替代的组成部分,已经涉足纳米尺寸的微细制造中,激光防伪商标模版和表面粗糙度样块是电铸的典型应用[5,6]。但电化学溶解(成型)加工的杂散腐蚀及间隙中电场、流场的多变性严重制约了其加工精度,其加工的微细程度目前还不能与电化学沉积的微细电铸相比。目前电化学微精成型加工还处于研究和试验阶段,其应用还局限于一些特殊的场合,如电子工业中微小零件的电化学蚀刻加工(美国IBM公司)、微米级浅槽加工(荷兰飞利浦公司)、微型轴电解抛光(日本东京大学)已取得了很好的加工效果,精度已可达微米级[5]。微细直写加工、微细群缝加工及微孔电液束加工,以及电解与超声、电火花、机械等方式结合形成的复合微精工艺已显示出良好的应用景[9~12]。
数控展成加工
传统的拷贝式电解加工的阴极设计制造困难,加工精度难以保证。尤其对整体叶轮上的扭曲叶片之类通道狭窄的零件表面,由于受工具阴极刚性及加工送进方式的限制,拷贝式电解加工更难以完成其加工任务。20世纪80年代初,以简单形状电极加工复杂型面的柔性电解加工——数控展成电解加工的思想开始形成,它以控制软件的编制代替复杂的成形阴极的设计、制造,以阴极相对工件的展成运动来加工出复杂型面。这种加工方法工具阴极形状简单,设计制造方便,应用范围广,具有很大的加工柔性,适用于小批量、多品种、甚至单件试制的生产中。80年代中期,前苏联乌法航空学院特种加工工艺及设备研究所以过程控制为突破口,设计了一种柔性电解加工单元,应用特殊的电流脉冲波形和高选择性的电解液,加工精度达0.02mm,表面粗糙度达Ra0.2~0.6m。波兰华沙工业大学的Kozak教授于1986年率先提出了电解铣削的思想,以棒状旋转阴极作类似于圆柱状侧铣刀的成形运动来形成加工表面,成功地应用于直升机旋翼座架型面的加工,加工中采用NaNO3电解液,精度可达±0.01~0.02mm,表面粗糙度达Ra0.16~0.63m。波兰Cracow金属切削学院的A.Ruszaj和J.Cekaj教授利用形似球头铣刀的工具阴极,进行了型面光整加工的试验研究,取得了形状误差小于0.01mm的加工效果,从而证明了该工艺在模具的光整加工方面具有很好的应用价值。美国、英国、俄罗斯都高度重视数控电解加工技术的研究并已得到应用,在新型航空发动机及航天火箭发动机的研制中发挥了重要作用。美国GE公司的五轴数控电解加工,美国、俄罗斯仿形电解加工带冠整体叶轮代表了数控电解加工整体叶轮的国际先进水平。
南京航空航天大学从20世纪80年代中期开始进行数控展成电解加工工艺技术的研究,已在电解加工设备研制、加工机理研究、控制软件编制及工艺试验等方面均取得了重要进展[7,8,9]。具体研究内容包括以下几方面:
(1)设备研制:研制了五轴数控电解加工机床及配套的多轴联动数控系统。该机床具有三个直线运动坐标轴及二个旋转运动坐标轴,各轴均采用步进电机驱动。多轴联动数控系统为二级数控系统,上位机为一台通用计算机,用于数据处理及生成数控加工程序,下位机为组合在一起的五台经济型二轴数控单元及其驱动单元,用于驱动机床各轴运动。(2)成形规律研究:研究了棒状外喷式阴极、三角形截面内喷式阴极、矩形截面内喷式阴极三种状况下展成电解加工间隙随一些主要工艺参数变化的规律。(3)阴极设计:针对整体叶轮结构,设计制造了不同结构的开槽阴极、型面精加工阴极,并通过工艺试验对其结构进行不断改进,现已设计出了新颖结构的组合式开槽阴极及矩形截面整体式型面精加工阴极,很好地解决了加工过程中易产生的阴极短路烧伤问题。
(4)加工软件开发:针对整体叶轮的开槽加工及型面精加工,开发了相应的数控展成电解加工软件,具有叶片型面的数据处理、数控加工的展成运动轨迹计算及整体叶轮的三维型面几何造型等功能。
(5)加工工艺试验:包括直纹面、非直纹面整体叶(涡)轮及带冠整体叶轮的展成电解加工、叶片型面电解抛光与五轴联动电解磨削等。试验表明,工艺过程稳定可靠可以获得较高的加工精度和较低的表面粗糙度。
阴极设计
目前的生产实际中,多采用迭代试验修正法来制作阴极,这不仅浪费人力物力,而且要求操作者具备丰富的实践经验和很高的技术水平,同时也大大延误了生产周期,增加了制造成本。特别是对于形状复杂和精度要求较高的零件,阴极设计问题已成为影响电解加工应用的一个重要原因。南京航空航天大学研究设计了阴极设计CAD/CAE/CAM系统的结构框架以及开发策略。该系统基于专家系统,结合专业技术人员和领域专家的经验来优选工艺参数,并且采用基于自由边界的数值算法,保证算法的收敛性[10]。南京航空航天大学还提出了一种基于正问题数值求解模拟“试验修整”进行阴极设计的方法。该方法将生产实际中制造阴极的过程再现于计算机上。采用有限元求解拉普拉斯方程得到加工间隙中的电位分布,通过不断地将获得的等位线与理想工件边界进行比较,将得到的差值映射到阴极端
用来指导阴极的修整,直到工件阳极端的差值小于所允许的值。该
设计方法具有易于处理复杂边界、
收敛性好、精度高的特点[11]。
合肥工业大学也提出了应用阴极设计数据表来进行阴极设计的方法,通过合理设计工艺试验,获取了特征部位的加工间隙偏差值,据此计算出各特征部位对应阴
极处的附加修正量。在此基础上,建立五种阴极设计数据表,为阴极设计提供了丰富的修正数据。在此基础上,可望建立阴极设计数据库[12]。
磁场提高电解加工精度的研究这项技术早期研究较多的是磁场对电解磨削、电解抛光的影响。近年来,国内开展了电解成型加工叠加磁场的研究。西北工业大学的研究发现当加工对象是钛合金或者是在NaCl电解液中加工45钢时,磁场可以显著减少杂散腐蚀,提高加工精度,而在NaNO3电解液中加工45钢则效果甚微[13]。西安工业学院进行了磁场影响电场的仿真试验及在电解加工装置上叠加磁场的加工工艺试验。试验表明,电解加工过程中叠加磁场会改变原有电场分布,进而改变间隙流场的分布,从而有利于解决以往电解加工过程中的杂散腐蚀现象,提高电解加工的质量。只有在叠加磁场方向垂直于电场方向且N极指向电场叠加磁场时,对电场均布有较明显的作用 [14]。此外,采取切割流线的方向叠加磁场,洛仑兹力的作用有利于成股的束流展开;磁场可以减小电解液的粘度,改善其流动性能,有利于及时排走电解产物和热量,改善加工条件,提高加工稳定性[15]。
除了上述五大研究方向之外,带冠整体叶轮加工、周期循环电解加工、数控铣床电解加工、脉冲电解加工间隙测控方法、基于BP神经网络的电解加工精度预测模型、电解加工中管理系统的开发等工艺技术的研究均有所创新或突破。
三、本课题的研究手段和预期结果
1、研究内容
(1)查阅文献资料,详细研究零件图,了解零件的结构。
(2)根据零件的结构选取毛坯的种类和制造方法毛坯余量的选择。
(3)制定工艺规程和可行性分析。
(4)选择粗精基准,计算和选择金属切削机床的技术参数。
(5)根据电解加工工装的结构设计工序过程中的专用夹具。
2、本课题可能遇到的问题及其研究方法
(1)在刚开始的时候工序的划分以及定位基准会比较难选择,所以就在过程中腰认真分析零件图,了解电解加工工装的结构特点及相关的技术要求而加工工序要根据生产类型,零件的结构来认真分析。
(2)在夹具设计的时候也可能遇到问题,比如工件的定位是否正确,定位精度是否满足要求等等,所以要调查现阶段国内外比较先进的电解加工工装结构,从整体上把握设计的方向,了解电解加工工装的加工工艺规程及夹具的设计原理。
(3)通过大量的资料,研究零件的结构,选择合适的加工方法,及选择合理的基准和工序安排。
(4)熟悉夹具的结构选择合理的机床及装夹设备,确定加工余量和工序,进行精细的准确的尺寸计算,和时间的估算。
3、课题预期结果
(1)了解了电解加工工装的作用,完成对零件的结构分析,并制作出合理的夹具及装夹方案
(2)在保证经济和尺寸精度的要求下制定出合理的加工方法及加工工序。
(3)在老师的要求下及自己的计划内完成各项任务。
4、完成课题所需的工作条件
在前期得做好各项准备,要查阅大量的文献了解电解加工工装的结构,并在CAD,PRO/E上画出这个零件,认真去了解他的结构,这当中就需要一些工具书比如机械加工工艺手册,夹具设计图册,刀具设计手册以及有关教材及参考资料,最后如果有需要还可以选择去工厂调研,以上条件具备完成本课题所需的工作条件。
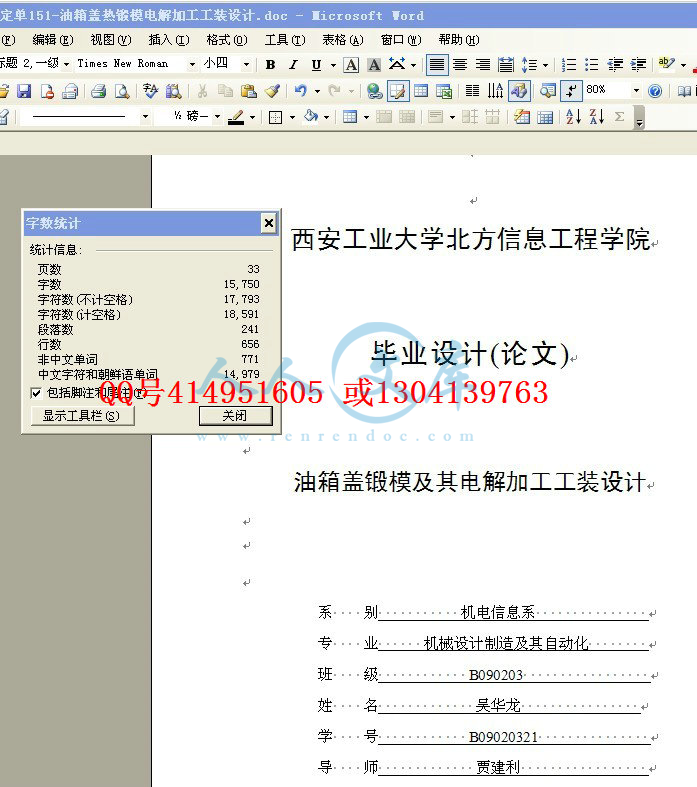

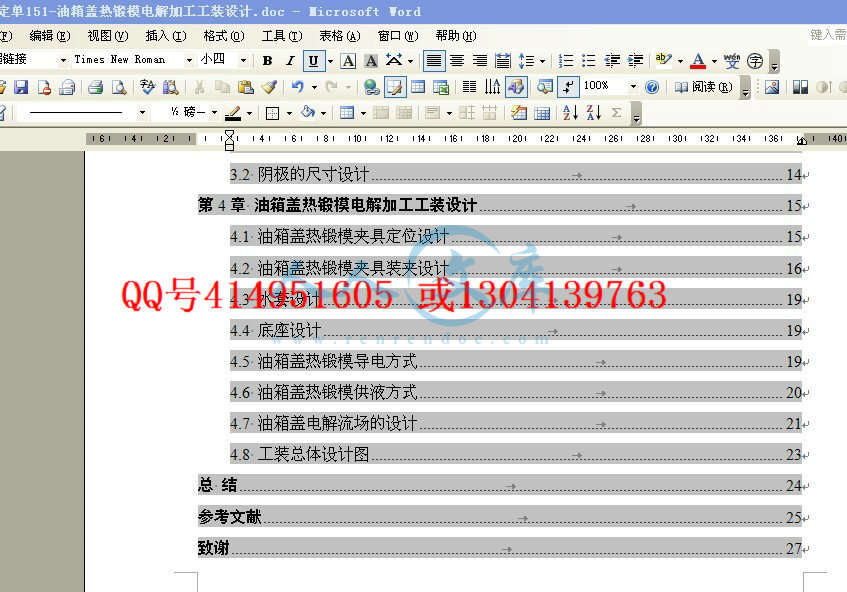





- 内容简介:
-
西安工业大学北方信息工程学院毕业设计(论文)开题报告题目:油箱盖热锻模电解加工工装设计系 别 机电信息系 专 业 机械设计制造及自动化 班 级 B090203 姓 名 吴华龙 学 号 B09020327 导 师 贾建利 2012年 12 月 24 日101、毕业设计(论文)综述(题目背景、研究意义及国内外相关研究情况):1.1题目背景:采用电解加工实现模具加工具有表面质量好,使用寿命长,脱模好,成本低的优点。通过本课题的设计,达到:(1)培养学生综合运用所学的基础课、技术基础和专业课的知识,分析解决工程技术问题的能力;(2)巩固加深扩大基本理论和技能;(3)受高级工程技术人员能力的训练;调研、查阅文献,制定方案、设撰写;(4)创新能力和团队精神。 基于电解过程中的阳极溶解原理并借助于成型的阴极,将工件按一定形状和尺寸加工成型的一种工艺方法,称为电解加工。1.2研究意义电解加工是利用金属在电解液中发生电化学阳极溶解的原理将工件加工成形的种特种加工方法。加工时,工件接直流电源的正极,工具接负极,两极之间保持较小的间隙。电解液从极间间隙中流过,使两极之间形成导电通路,并在电源电压下产生电流,从而形成电化学阳极溶解。随着工具相对工件不断进给,工件金属不断被电解,电解产物不断被电解液走,最终两极间各处的间隙趋于一致,工件表面形成与工具工作面基本相似的形状。电解加工对于难加工材料、形状复杂或薄壁零件的加工具有显著优势。目前,电解加工已获得广泛应用,如炮管膛线,叶片,整体叶轮,模具,异型孔及异型零件,倒角和去毛刺等加工。并且在许多零件的加工中,电解加工工艺已占有重要甚至不可替代的地位。1.3国内外相关研究情况电解加工以其加工速度快、表面质量好、凡金属都能加工而且不怕材料硬、韧、无宏观机械切削力、工具阴极无损耗、可用同一个成形阴极作单方向送进而成批加工复杂型腔、型面、型孔等优点,在20 世纪60 年代初,首先在炮管膛线和航空发动机涡轮叶片的加工中得到应用,其后又逐渐扩大应用于锻模型腔、深孔、小孔、长键槽、等截面叶片整体叶轮的加工以及去毛刺等领域,取得了显著的技术、经济效果。但是,在70 年代以后,随着国际市场经济竞争形式的变化,产品更新换代快,生产批量减小,使得电解加工的适用范围也发生变化。总体看应用范围有所减小,但应用要求却越来越高。在经历大约20年的低潮后,从20世纪90年代后期起,电解加工又重新焕发了生机。其研究机构及人员逐渐壮大,应用领域(尤其在航天、航空、军工领域)有所扩展,研究成果及论著数量激增,工艺技术水平及设备性能均达到了一个新的高度。1工艺技术研究目前,电解加工工艺技术研究涉及的方向较多,但主要集中在微秒级脉冲电流加工、微精加工、数控展成加工、阴极设计及磁场对电解加工的影响等五大领域。下面分别加以详述。1.3.1微秒级脉冲电流加工自20世纪70年代初起,前苏联、美国、日本、法国、波兰、瑞士、西德等相继开始了对脉冲电流电解加工的研究。在国内,多家单位相继开展了毫秒级脉冲电流电解加工的研究并成功用于工业生产。随着近代功率电子技术的发展,新型快速功率电子开关元件如MOSFET、IGBT等出现,使得有可能实现微秒级脉冲电流电解加工。20世纪90年代以来,微秒级脉冲电流电解加工基础工艺研究取得突破性进展。研究表明,此项新技术可以提高集中蚀除能力,并可实现0.05mm以下的微小间隙加工,从而可以较大幅度地提高加工精度和表面质量,型腔最高重复精度可达0.05mm,最低表面粗糙度可达Ra0.40,有望将电解加工提高到精密加工的水平,而且可促进加工过程稳定并简化工艺,有利于电解加工的扩大应用。国内外众多研究机构利用微秒级脉冲电流开展了模具型腔及叶片型面加工、型腔抛光、电解刻字、电解磨等工艺可行性试验以及气门模具生产加工试验1,3,研究成果进一步从工艺角度证实了上述结论。1.3.2微精加工从原理上而言,电化学加工技术可分为两类:一类是基于阳极溶解原理的减材技术,如电解加工、电解抛光等;另一类是基于阴极沉积原理的增材技术,如电镀、电铸、刷镀等。这两类技术有一个共同点,即材料的去除或增加过程都是以离子的形式进行的。由于金属离子的尺寸非常微小(10-1nm级),因此,相对于其它“微团”去除材料方式(如微细电火花、微细机械磨削),这种以“离子”方式去除材料的微去除方式使得电化学加工技术在微细制造领域、以至于纳米制造领域存在着极大的研究探索空间。从理论上讲,只要精细地控制电流密度和电化学发生区域,就能实现电化学微细溶解或电化学微细沉积。微细电铸技术是电化学微细沉积的典型实例,它已经在微细制造领域获得重要应用。微细电铸是LIGA技术一个重要的、不可替代的组成部分,已经涉足纳米尺寸的微细制造中,激光防伪商标模版和表面粗糙度样块是电铸的典型应用。但电化学溶解(成型)加工的杂散腐蚀及间隙中电场、流场的多变性严重制约了其加工精度,其加工的微细程度目前还不能与电化学沉积的微细电铸相比。目前电化学微精成型加工还处于研究和试验阶段,其应用还局限于一些特殊的场合,如电子工业中微小零件的电化学蚀刻加工(美国IBM公司)、微米级浅槽加工(荷兰飞利浦公司)、微型轴电解抛光(日本东京大学)已取得了很好的加工效果,精度已可达微米级。微细直写加工、微细群缝加工及微孔电液束加工,以及电解与超声、电火花、机械等方式结合形成的复合微精工艺已显示出良好的应用前景。数控展成加工传统的拷贝式电解加工的阴极设计制造困难,加工精度难以保证。尤其对整体叶轮上的扭曲叶片之类通道狭窄的零件表面,由于受工具阴极刚性及加工送进方式的限制,拷贝式电解加工更难以完成其加工任务。20世纪80年代初,以简单形状电极加工复杂型面的柔性电解加工数控展成电解加工的思想开始形成,它以控制软件的编制代替复杂的成形阴极的设计、制造,以阴极相对工件的展成运动来加工出复杂型面。这种加工方法工具阴极形状简单,设计制造方便,应用范围广,具有很大的加工柔性,适用于小批量、多品种、甚至单件试制的生产中。80年代中期,前苏联乌法航空学院特种加工工艺及设备研究所以过程控制为突破口,设计了一种柔性电解加工单元,应用特殊的电流脉冲波形和高选择性的电解液,加工精度达0.02mm,表面粗糙度达Ra0.20.6m。波兰华沙工业大学的Kozak教授于1986年率先提出了电解铣削的思想,以棒状旋转阴极作类似于圆柱状侧铣刀的成形运动来形成加工表面,成功地应用于直升机旋翼座架型面的加工,加工中采用NaNO3电解液,精度可达0.010.02mm,表面粗糙度达Ra0.160.63m。波兰Cracow金属切削学院的A.Ruszaj和J.Cekaj教授利用形似球头铣刀的工具阴极,进行了型面光整加工的试验研究,取得了形状误差小于0.01mm的加工效果,从而证明了该工艺在模具的光整加工方面具有很好的应用价值。美国、英国、俄罗斯都高度重视数控电解加工技术的研究并已得到应用,在新型航空发动机及航天火箭发动机的研制中发挥了重要作用。美国GE公司的五轴数控电解加工,美国、俄罗斯仿形电解加工带冠整体叶轮代表了数控电解加工整体叶轮的国际先进水平。2.本课题研究的主要内容和拟采用的研究方案、研究方法或措施2.1 研究的主要内容根据研究对象油箱盖热锻模,设计一套加工该热锻模的电解加工工装,包括:(1)连杆热锻模电解加工阴极;(2)装夹热锻模加工阴极和工件的夹具装置;(3)运用Pro/E、UG等软件画出油箱盖热锻模电解加工工装三维装配图。电解加工装置除了应保证工件装夹和定位外,还应考虑导电、供液、流场分布,非加工面的保护,工件和工具(即正负极、阴阳极)之间的绝缘等问题。课题研究的主要内容是通过对所给零件的分析,设计加工零件的阴极,以及装夹高温合金零件电解加工的阴极和工件的夹具装置。(1)在刚开始的时候工序的划分以及定位基准会比较难选择,所以就在过程中腰认真分析零件图,了解电解加工工装的结构特点及相关的技术要求而加工工序要根据生产类型,零件的结构来认真分析。(2)在夹具设计的时候也可能遇到问题,比如工件的定位是否正确,定位精度是否满足要求等等,所以要调查现阶段国内外比较先进的电解加工工装结构,从整体上把握设计的方向,了解电解加工工装的加工工艺规程及夹具的设计原理。(3)通过大量的资料,研究零件的结构,选择合适的加工方法,及选择合理的基准和工序安排。(4)熟悉夹具的结构选择合理的机床及装夹设备,确定加工余量和工序,进行精细的准确的尺寸计算,和时间的估算。2.2拟采用的研究方案2.2.1 方案一:从导电方面考虑设计方案,有两种选择,一是将电缆线引入,用线鼻子直接接到工件阳极跟工件阴极,二是在工作箱外将电源线接到滑枕体及不锈钢工作台,电流通过阴极安装板及工作台传导到阴极和阳极。前者线路损失小,且因工作台、夹具均不带电,可以采用耐蚀的非金属材料,如采用金属材料对不带电的零件则加以阴极保护,防止电化学杂散腐蚀。但此方案的缺点是工作箱内导线较多,走线较复杂,布局欠佳,每次装卸工件时还要拆卸线鼻子,并要防止正负极线鼻子相碰或正极线鼻子与工作箱相碰而引起送电时短路。所以选第二种方案。2.2.2方案二:从流场方面考虑设计方案,根据电解液的流动方向、加工送进方向及加工间隙之间的几何关系,可分为三种流动形式,即侧流式、正流式和反流式。可根据加工对象的几何形状确定流动形式。对于型面曲率变化不大的三维型面如一般叶片型面、叶片锻模型腔等,可采用侧流式,对于圆孔、型孔可采用正流式或反流式,对于某些复杂的型腔或型面,可在阴极上设计适当的通液槽(孔)采用正流式或反流式,或者两种流动形式都存在的复合流动形式进行加工。针对我的零件采用复合式。在流场设计方面还应该考虑电解液流速和进口压力。确定电解液流速的原则:(1)选则适当高的流速,能从加工间隙中带走电解产物,且使电解液流动处于紊流状态,这样有利于均匀流场并消除浓差极限,(2)选择适当高的流速以控制温升。电解液压力的确定,是指加工间隙进口处的压力和电解液输出泵的出口,考虑到管道中的压力损失,一般电解液泵出口压力需比电解液进口压力高0.05-0.1pa。2.2.3方案三:从阴极设计方面提出设计方案,对其阴极型管的直线度有严格要求。端面倒角10,在侧面间隙,约0.150.22mm,减去阴极单面涂层厚度约0.05mm,还有足够的间隙空间允许电解液顺畅通过;端面制成加工凸缘根据加工孔径的大小和精度要求,确定凸缘外径和加工刃带的宽度。3.本课题研究的重点及难点,前期已开展工作电解加工是利用金属在电解液中产生电化学阳极溶解的原理对工件进行成形加工的特种加工,又称电化学加工。电解加工的重点是针对不同的加工零件设计出加工该零件的阴极以及装夹该零件电解加工的阴极和工件的夹具装置。电解加工的难点是电解加工是一种复制加工, 工具阴极的轮廓形状须根据图纸给定的工件形状和加工间隙的分布规律来设计,加工间隙分布的不均匀导致阴极设计非常困难。工作定位 阴极设计 流程设计 导电 Cad二维图 图3.1 proe三维图 图3.2图3.1油箱盖热锻模cad二维图图3.2油箱盖热锻模proe三维图4.完成本课题的工作方案及进度计划(按周次填写)12周:熟悉课题,完成关于电解加工的2000字文献综述,翻译外文资料; 3周:确定油箱盖热锻模设计及其电解加工工装方案,绘制其结构草图,准备开题答辩; 46周:进行油箱盖热锻模设计及其电解加工阴极设计计算; 79周:进行油箱盖热锻模电解加工工装设计,包括导电、供液方式和流场设计,准备中期答辩; 1015周:完善整个电解加工工装设计、完成装配图(包括三维装配图)及零件图的绘制等工作; 1618周:对所有图纸进行校核,编写设计说明书,所有资料提请指导教师检查,准备毕业答辩;参考文献1. 沈健,张海岩;锻模电解加工工具电极的反拷和修正方法J;电加工与模具;2001年04期2. 张春,李毅;模具型腔的数控铣削法电解加工J;电加工与模具;2004年04期3. 沈健;热锻模电解加工工具电极的反拷和修正J;模具工业;2005年11期4. 朱树敏;陈淑芬;张海岩;低浓度复合电解液的性能及应用J;电加工;1985年06期5. 朱树敏;沈光祖;锻模的脉冲电流电解加工J;电加工;1990年01期6. 沈健,朱树敏,陈远龙;锻模电解加工新技术J;电加工;1998年01期7. 朱永伟,万胜美,朱树敏;振动进给、脉冲电流电解加工设备及工艺的研究J;电加工;1996年05期8. 赵雪松,朱树敏;镍钛合金球拍的电化学加工J;电加工;1999期04期9. 姚宏伟,卢星河;装饰不锈钢管材的快速电化学蚀刻J;化学世界;2002年01期10. 刘德成;夹心式复合加工表面形貌特征J;新技术新工艺;2007年03期11. 张海岩;齿轮的电化学去毛刺工艺研究J;新技术新工艺;1996年04期12. 吴蒙华,李晓伟,刘晋春,郭永丰;不锈钢凹形字图的快速电解蚀刻J;新技术新工艺;1997年01期13. 赵雪松,苏学满,杨明;模具钢电解机械复合抛光工艺研究J;中国机械工程;2003年12期14. 柯旭贵;基于VBA的参数化图形的建立与实现J;安徽机电学院学报;2001年02期15. 朱荻;国外电解加工的研究进展J;电加工与模具;2000年01期16. 徐家文,王建业,田继安;21世纪初电解加工的发展和应用J;电加工与模具;2001年06期17. 王建业,冯倩,罗干英,刘丛宽,林苏文,罗天友;高频、窄脉冲电流电解加工模具试验研究J;电加工;1999年04期18. 周茂军,苏铁明,欧宗瑛;以SolidWorks为支撑软件的模具标准件库的开发J;大连轻工业学院学报;2001年04期 19. D Zhu, K P. Ra jurkar. M ode ling and Verification o f IntereletrodeGapin E lectrochem icalM ach ining w ith Passiva ting Electroly te J. IMECM, ASME, MED, 1999, 10: 589-59620.R R com pany, UK. F in ishes b lades in one opera tion J .M ach ine ry and Produc tion Eng ineering, 1985 ( 7) : 44-4821.D B Ender. Implementation of Deadband Reset Scheduling for the E lmi ination of Stick-slip Cycling in Contro l Valves J.Journa lA, 1997, 38 ( 1): 11- 5 指导教师意见(对课题的深度、广度及工作量的意见) 指导教师: 年 月 日 6 所在系审查意见: 系主管领导: 年 月 日注:1. 正文:宋体小四号字,行距22磅。2. 开题报告由各系集中归档保存。毕业设计(论文)任务书系(部): 专业: 班级 姓名 学号 1.毕业设计(论文)题目: 油箱盖热锻模电解加工工装设计 2.题目背景和意义: 采用电解加工实现模具加工具有表面质量好,使用寿命长,脱模好,成本低的优点。通过本课题的设计,达到:(1)培养学生综合运用所学的基础课、技术基础和专业课的知识,分析解决工程技术问题的能力;(2)巩固加深扩大基本理论和技能;(3)受高级工程技术人员能力的训练;调研、查阅文献,制定方案、设计、撰写。(4)创新能力和团队精神。 3.设计(论文)的主要内容(理工科含技术指标):根据研究对象油箱盖热锻模,设计一套加工该热锻模的电解加工工装,包括:(1)连杆热锻模电解加工阴极;(2)装夹热锻模加工阴极和工件的夹具装置;(3)运用Pro/E、UG等软件画出油箱盖热锻模电解加工工装三维装配图。电解加工装置除了应保证工件装夹和定位外,还应考虑导电、供液、流场分布,非加工面的保护,工件和工具(即正负极、阴阳极)之间的绝缘等问题。 4.设计的基本要求及进度安排(含起始时间、设计地点): 设计要求:通过设计,提高学生设计和创新能力。设计说明书包括文献综述、设计方案和决策及思路,设计中对导电、供液以及有关结构和装夹的计算和说明。 进度安排:12周:熟悉课题,完成关于电解加工的2000字文献综述,翻译外文资料; 3周:确定油箱盖热锻模设计及其电解加工工装方案,绘制其结构草图,准备开题答辩; 46周:进行油箱盖热锻模设计及其电解加工阴极设计计算; 79周:进行油箱盖热锻模电解加工工装设计,包括导电、供液方式和流场设计,准备中期答辩; 1015周:完善整个电解加工工装设计、完成装配图(包括三维装配图)及零件图的绘制等工作; 1618周:对所有图纸进行校核,编写设计说明书,所有资料提请指导教师检查,准备毕业答辩; 5.毕业设计(论文)的工作量要求: 实验(时数)*或实习(天数): 2周 图纸(幅面和张数)*: A0#图纸不少于3张 其他要求:论文字数1.5万字以上;外文翻译不少于1000英文单词;参考文献中文15篇, 英文3篇。 指导教师签名: 年 月 日 学生签名: 年 月 日 系主任审批: 年 月 日说明:1本表一式二份,一份由学生装订入附件册,一份教师自留。2 带*项可根据学科特点选填。油箱盖热锻模电解加工工装设计开题报告一、 选题的目的及意义基于电解过程中的阳极溶解原理并借助于成型的阴极,将工件按一定形状和尺寸加工成型的一种工艺方法,称为电解加工。采用电解加工实现模具加工具有表面质量好,使用寿命长,脱模好,成本低的优点。通过本课题的设计,达到:(1)培养学生综合运用所学的基础课、技术基础和专业课的知识,分析解决工程技术问题的能力;(2)巩固加深扩大基本理论和技能;(3)受高级工程技术人员能力的训练;调研、查阅文献,制定方案、设计、撰写。(4)创新能力和团队精神。 二、国内外研究现状在经历大约20年的低潮后,从20世纪90年代后期起,电解加工又重新焕发了生机。其研究机构及人员逐渐壮大,应用领域(尤其在航天、航空、军工领域)有所扩展,研究成果及论著数量激增,工艺技术水平及设备性能均达到了一个新的高度。1工艺技术研究目前,电解加工工艺技术研究涉及的方向较多,但主要集中在微秒级脉冲电流加工、微精加工、数控展成加工、阴极设计及磁场对电解加工的影响等五大领域。下面分别加以详述。1.1微秒级脉冲电流加工自20世纪70年代初起,前苏联、美国、日本、法国、波兰、瑞士、西德等相继开始了对脉冲电流电解加工的研究。在国内,多家单位相继开展了毫秒级脉冲电流电解加工的研究并成功用于工业生产。随着近代功率电子技术的发展,新型快速功率电子开关元件如MOSFET、IGBT等出现,使得有可能实现微秒级脉冲电流电解加工。20世纪90年代以来,微秒级脉冲电流电解加工基础工艺研究取得突破性进展。研究表明,此项新技术可以提高集中蚀除能力,并可实现0.05mm以下的微小间隙加工,从而可以较大幅度地提高加工精度和表面质量,型腔最高重复精度可达0.05mm1,2,3,最低表面粗糙度可达Ra0.401,有望将电解加工提高到精密加工的水平,而且可促进加工过程稳定并简化工艺,有利于电解加工的扩大应用。国内外众多研究机构利用微秒级脉冲电流开展了模具型腔及叶片型面加工、型腔抛光、电解刻字、电解磨等工艺可行性试验以及气门模具生产加工试验1,3,研究成果进一步从工艺角度证实了上述结论。1.2微精加工从原理上而言,电化学加工技术可分为两类:一类是基于阳极溶解原理的减材技术,如电解加工、电解抛光等;另一类是基于阴极沉积原理的增材技术,如电镀、电铸、刷镀等。这两类技术有一个共同点,即材料的去除或增加过程都是以离子的形式进行的。由于金属离子的尺寸非常微小(10-1nm级),因此,相对于其它“微团”去除材料方式(如微细电火花、微细机械磨削),这种以“离子”方式去除材料的微去除方式使得电化学加工技术在微细制造领域、以至于纳米制造领域存在着极大的研究探索空间。从理论上讲,只要精细地控制电流密度和电化学发生区域,就能实现电化学微细溶解或电化学微细沉积。微细电铸技术是电化学微细沉积的典型实例,它已经在微细制造领域获得重要应用。微细电铸是LIGA技术一个重要的、不可替代的组成部分,已经涉足纳米尺寸的微细制造中,激光防伪商标模版和表面粗糙度样块是电铸的典型应用5,6。但电化学溶解(成型)加工的杂散腐蚀及间隙中电场、流场的多变性严重制约了其加工精度,其加工的微细程度目前还不能与电化学沉积的微细电铸相比。目前电化学微精成型加工还处于研究和试验阶段,其应用还局限于一些特殊的场合,如电子工业中微小零件的电化学蚀刻加工(美国IBM公司)、微米级浅槽加工(荷兰飞利浦公司)、微型轴电解抛光(日本东京大学)已取得了很好的加工效果,精度已可达微米级5。微细直写加工、微细群缝加工及微孔电液束加工,以及电解与超声、电火花、机械等方式结合形成的复合微精工艺已显示出良好的应用景912。数控展成加工传统的拷贝式电解加工的阴极设计制造困难,加工精度难以保证。尤其对整体叶轮上的扭曲叶片之类通道狭窄的零件表面,由于受工具阴极刚性及加工送进方式的限制,拷贝式电解加工更难以完成其加工任务。20世纪80年代初,以简单形状电极加工复杂型面的柔性电解加工数控展成电解加工的思想开始形成,它以控制软件的编制代替复杂的成形阴极的设计、制造,以阴极相对工件的展成运动来加工出复杂型面。这种加工方法工具阴极形状简单,设计制造方便,应用范围广,具有很大的加工柔性,适用于小批量、多品种、甚至单件试制的生产中。80年代中期,前苏联乌法航空学院特种加工工艺及设备研究所以过程控制为突破口,设计了一种柔性电解加工单元,应用特殊的电流脉冲波形和高选择性的电解液,加工精度达0.02mm,表面粗糙度达Ra0.20.6m。波兰华沙工业大学的Kozak教授于1986年率先提出了电解铣削的思想,以棒状旋转阴极作类似于圆柱状侧铣刀的成形运动来形成加工表面,成功地应用于直升机旋翼座架型面的加工,加工中采用NaNO3电解液,精度可达0.010.02mm,表面粗糙度达Ra0.160.63m。波兰Cracow金属切削学院的A.Ruszaj和J.Cekaj教授利用形似球头铣刀的工具阴极,进行了型面光整加工的试验研究,取得了形状误差小于0.01mm的加工效果,从而证明了该工艺在模具的光整加工方面具有很好的应用价值。美国、英国、俄罗斯都高度重视数控电解加工技术的研究并已得到应用,在新型航空发动机及航天火箭发动机的研制中发挥了重要作用。美国GE公司的五轴数控电解加工,美国、俄罗斯仿形电解加工带冠整体叶轮代表了数控电解加工整体叶轮的国际先进水平。南京航空航天大学从20世纪80年代中期开始进行数控展成电解加工工艺技术的研究,已在电解加工设备研制、加工机理研究、控制软件编制及工艺试验等方面均取得了重要进展7,8,9。具体研究内容包括以下几方面:(1)设备研制:研制了五轴数控电解加工机床及配套的多轴联动数控系统。该机床具有三个直线运动坐标轴及二个旋转运动坐标轴,各轴均采用步进电机驱动。多轴联动数控系统为二级数控系统,上位机为一台通用计算机,用于数据处理及生成数控加工程序,下位机为组合在一起的五台经济型二轴数控单元及其驱动单元,用于驱动机床各轴运动。(2)成形规律研究:研究了棒状外喷式阴极、三角形截面内喷式阴极、矩形截面内喷式阴极三种状况下展成电解加工间隙随一些主要工艺参数变化的规律。(3)阴极设计:针对整体叶轮结构,设计制造了不同结构的开槽阴极、型面精加工阴极,并通过工艺试验对其结构进行不断改进,现已设计出了新颖结构的组合式开槽阴极及矩形截面整体式型面精加工阴极,很好地解决了加工过程中易产生的阴极短路烧伤问题。(4)加工软件开发:针对整体叶轮的开槽加工及型面精加工,开发了相应的数控展成电解加工软件,具有叶片型面的数据处理、数控加工的展成运动轨迹计算及整体叶轮的三维型面几何造型等功能。(5)加工工艺试验:包括直纹面、非直纹面整体叶(涡)轮及带冠整体叶轮的展成电解加工、叶片型面电解抛光与五轴联动电解磨削等。试验表明,工艺过程稳定可靠可以获得较高的加工精度和较低的表面粗糙度。阴极设计目前的生产实际中,多采用迭代试验修正法来制作阴极,这不仅浪费人力物力,而且要求操作者具备丰富的实践经验和很高的技术水平,同时也大大延误了生产周期,增加了制造成本。特别是对于形状复杂和精度要求较高的零件,阴极设计问题已成为影响电解加工应用的一个重要原因。南京航空航天大学研究设计了阴极设计CAD/CAE/CAM系统的结构框架以及开发策略。该系统基于专家系统,结合专业技术人员和领域专家的经验来优选工艺参数,并且采用基于自由边界的数值算法,保证算法的收敛性10。南京航空航天大学还提出了一种基于正问题数值求解模拟“试验修整”进行阴极设计的方法。该方法将生产实际中制造阴极的过程再现于计算机上。采用有限元求解拉普拉斯方程得到加工间隙中的电位分布,通过不断地将获得的等位线与理想工件边界进行比较,将得到的差值映射到阴极端用来指导阴极的修整,直到工件阳极端的差值小于所允许的值。该设计方法具有易于处理复杂边界、收敛性好、精度高的特点11。合肥工业大学也提出了应用阴极设计数据表来进行阴极设计的方法,通过合理设计工艺试验,获取了特征部位的加工间隙偏差值,据此计算出各特征部位对应阴极处的附加修正量。在此基础上,建立五种阴极设计数据表,为阴极设计提供了丰富的修正数据。在此基础上,可望建立阴极设计数据库12。磁场提高电解加工精度的研究这项技术早期研究较多的是磁场对电解磨削、电解抛光的影响。近年来,国内开展了电解成型加工叠加磁场的研究。西北工业大学的研究发现当加工对象是钛合金或者是在NaCl电解液中加工45钢时,磁场可以显著减少杂散腐蚀,提高加工精度,而在NaNO3电解液中加工45钢则效果甚微13。西安工业学院进行了磁场影响电场的仿真试验及在电解加工装置上叠加磁场的加工工艺试验。试验表明,电解加工过程中叠加磁场会改变原有电场分布,进而改变间隙流场的分布,从而有利于解决以往电解加工过程中的杂散腐蚀现象,提高电解加工的质量。只有在叠加磁场方向垂直于电场方向且N极指向电场叠加磁场时,对电场均布有较明显的作用 14。此外,采取切割流线的方向叠加磁场,洛仑兹力的作用有利于成股的束流展开;磁场可以减小电解液的粘度,改善其流动性能,有利于及时排走电解产物和热量,改善加工条件,提高加工稳定性15。除了上述五大研究方向之外,带冠整体叶轮加工、周期循环电解加工、数控铣床电解加工、脉冲电解加工间隙测控方法、基于BP神经网络的电解加工精度预测模型、电解加工中管理系统的开发等工艺技术的研究均有所创新或突破。三、本课题的研究手段和预期结果1、研究内容(1)查阅文献资料,详细研究零件图,了解零件的结构。(2)根据零件的结构选取毛坯的种类和制造方法毛坯余量的选择。(3)制定工艺规程和可行性分析。(4)选择粗精基准,计算和选择金属切削机床的技术参数。(5)根据电解加工工装的结构设计工序过程中的专用夹具。2、本课题可能遇到的问题及其研究方法(1)在刚开始的时候工序的划分以及定位基准会比较难选择,所以就在过程中腰认真分析零件图,了解电解加工工装的结构特点及相关的技术要求而加工工序要根据生产类型,零件的结构来认真分析。(2)在夹具设计的时候也可能遇到问题,比如工件的定位是否正确,定位精度是否满足要求等等,所以要调查现阶段国内外比较先进的电解加工工装结构,从整体上把握设计的方向,了解电解加工工装的加工工艺规程及夹具的设计原理。(3)通过大量的资料,研究零件的结构,选择合适的加工方法,及选择合理的基准和工序安排。(4)熟悉夹具的结构选择合理的机床及装夹设备,确定加工余量和工序,进行精细的准确的尺寸计算,和时间的估算。3、课题预期结果(1)了解了电解加工工装的作用,完成对零件的结构分析,并制作出合理的夹具及装夹方案(2)在保证经济和尺寸精度的要求下制定出合理的加工方法及加工工序。(3)在老师的要求下及自己的计划内完成各项任务。4、完成课题所需的工作条件在前期得做好各项准备,要查阅大量的文献了解电解加工工装的结构,并在CAD,PRO/E上画出这个零件,认真去了解他的结构,这当中就需要一些工具书比如机械加工工艺手册,夹具设计图册,刀具设计手册以及有关教材及参考资料,最后如果有需要还可以选择去工厂调研,以上条件具备完成本课题所需的工作条件。四、研究进度第1第2周 完成收集资料,开题报告,文献综述及外文翻译等第3-第5周 根据零件结构和尺寸要求,完成工艺规程设计第6第9周 工艺装备设计第10第12周 编写设计说明书 第13周 毕业设计答辩 五、主要参考文献资料1 于勇. 我国机械制造技术的现状及发展方向J. 山西焦煤科技 ,2010,(S1) :75-762 应雷. 浅谈我国机械制造业的困境和发展战略对策J. 科技资讯, 2010,(27) :1123 侯志楠. 浅析机械制造技术的发展历程、现状及趋势J. 2010/204 濮良贵,纪名刚. 机械设计M .高等教育出版社,20065 黎震,朱江峰. 先进制造技术M . 北京理工大学出版,20096 郑修本. 机械制造工艺学M . 北京:机械工业出版社,20077 徐鸿本. 机床夹具设计手册M.辽宁:辽宁科学技术出版社,20048 闻邦椿. 机械设计手册(第5版)第1卷 机械工业出版社, 20109 张捷. 机械制造技术基础M . 西南交通大学出版社 ,200610卢秉桓. 机械制造基础M .北京:机械工业出版社,200811 王先逵. 机械制造工艺学M .北京:机械工业出版社,200412 Handbook of Machine Tools Manfred weckJ ,2005 13Boyes W E. Jigs and Fixture .America,SMEJ,2006西安工业大学北方信息工程学院毕业设计(论文)开题报告题目:油箱盖热锻模电解加工工装设计系 别 机电信息系 专 业 机械设计制造及自动化 班 级 B090203 姓 名 吴华龙 学 号 B09020327 导 师 贾建利 2012年 12 月 24 日101、毕业设计(论文)综述(题目背景、研究意义及国内外相关研究情况):1.1题目背景:采用电解加工实现模具加工具有表面质量好,使用寿命长,脱模好,成本低的优点。通过本课题的设计,达到:(1)培养学生综合运用所学的基础课、技术基础和专业课的知识,分析解决工程技术问题的能力;(2)巩固加深扩大基本理论和技能;(3)受高级工程技术人员能力的训练;调研、查阅文献,制定方案、设撰写;(4)创新能力和团队精神。 基于电解过程中的阳极溶解原理并借助于成型的阴极,将工件按一定形状和尺寸加工成型的一种工艺方法,称为电解加工。1.2研究意义电解加工是利用金属在电解液中发生电化学阳极溶解的原理将工件加工成形的种特种加工方法。加工时,工件接直流电源的正极,工具接负极,两极之间保持较小的间隙。电解液从极间间隙中流过,使两极之间形成导电通路,并在电源电压下产生电流,从而形成电化学阳极溶解。随着工具相对工件不断进给,工件金属不断被电解,电解产物不断被电解液走,最终两极间各处的间隙趋于一致,工件表面形成与工具工作面基本相似的形状。电解加工对于难加工材料、形状复杂或薄壁零件的加工具有显著优势。目前,电解加工已获得广泛应用,如炮管膛线,叶片,整体叶轮,模具,异型孔及异型零件,倒角和去毛刺等加工。并且在许多零件的加工中,电解加工工艺已占有重要甚至不可替代的地位。1.3国内外相关研究情况电解加工以其加工速度快、表面质量好、凡金属都能加工而且不怕材料硬、韧、无宏观机械切削力、工具阴极无损耗、可用同一个成形阴极作单方向送进而成批加工复杂型腔、型面、型孔等优点,在20 世纪60 年代初,首先在炮管膛线和航空发动机涡轮叶片的加工中得到应用,其后又逐渐扩大应用于锻模型腔、深孔、小孔、长键槽、等截面叶片整体叶轮的加工以及去毛刺等领域,取得了显著的技术、经济效果。但是,在70 年代以后,随着国际市场经济竞争形式的变化,产品更新换代快,生产批量减小,使得电解加工的适用范围也发生变化。总体看应用范围有所减小,但应用要求却越来越高。在经历大约20年的低潮后,从20世纪90年代后期起,电解加工又重新焕发了生机。其研究机构及人员逐渐壮大,应用领域(尤其在航天、航空、军工领域)有所扩展,研究成果及论著数量激增,工艺技术水平及设备性能均达到了一个新的高度。1工艺技术研究目前,电解加工工艺技术研究涉及的方向较多,但主要集中在微秒级脉冲电流加工、微精加工、数控展成加工、阴极设计及磁场对电解加工的影响等五大领域。下面分别加以详述。1.3.1微秒级脉冲电流加工自20世纪70年代初起,前苏联、美国、日本、法国、波兰、瑞士、西德等相继开始了对脉冲电流电解加工的研究。在国内,多家单位相继开展了毫秒级脉冲电流电解加工的研究并成功用于工业生产。随着近代功率电子技术的发展,新型快速功率电子开关元件如MOSFET、IGBT等出现,使得有可能实现微秒级脉冲电流电解加工。20世纪90年代以来,微秒级脉冲电流电解加工基础工艺研究取得突破性进展。研究表明,此项新技术可以提高集中蚀除能力,并可实现0.05mm以下的微小间隙加工,从而可以较大幅度地提高加工精度和表面质量,型腔最高重复精度可达0.05mm,最低表面粗糙度可达Ra0.40,有望将电解加工提高到精密加工的水平,而且可促进加工过程稳定并简化工艺,有利于电解加工的扩大应用。国内外众多研究机构利用微秒级脉冲电流开展了模具型腔及叶片型面加工、型腔抛光、电解刻字、电解磨等工艺可行性试验以及气门模具生产加工试验1,3,研究成果进一步从工艺角度证实了上述结论。1.3.2微精加工从原理上而言,电化学加工技术可分为两类:一类是基于阳极溶解原理的减材技术,如电解加工、电解抛光等;另一类是基于阴极沉积原理的增材技术,如电镀、电铸、刷镀等。这两类技术有一个共同点,即材料的去除或增加过程都是以离子的形式进行的。由于金属离子的尺寸非常微小(10-1nm级),因此,相对于其它“微团”去除材料方式(如微细电火花、微细机械磨削),这种以“离子”方式去除材料的微去除方式使得电化学加工技术在微细制造领域、以至于纳米制造领域存在着极大的研究探索空间。从理论上讲,只要精细地控制电流密度和电化学发生区域,就能实现电化学微细溶解或电化学微细沉积。微细电铸技术是电化学微细沉积的典型实例,它已经在微细制造领域获得重要应用。微细电铸是LIGA技术一个重要的、不可替代的组成部分,已经涉足纳米尺寸的微细制造中,激光防伪商标模版和表面粗糙度样块是电铸的典型应用。但电化学溶解(成型)加工的杂散腐蚀及间隙中电场、流场的多变性严重制约了其加工精度,其加工的微细程度目前还不能与电化学沉积的微细电铸相比。目前电化学微精成型加工还处于研究和试验阶段,其应用还局限于一些特殊的场合,如电子工业中微小零件的电化学蚀刻加工(美国IBM公司)、微米级浅槽加工(荷兰飞利浦公司)、微型轴电解抛光(日本东京大学)已取得了很好的加工效果,精度已可达微米级。微细直写加工、微细群缝加工及微孔电液束加工,以及电解与超声、电火花、机械等方式结合形成的复合微精工艺已显示出良好的应用前景。数控展成加工传统的拷贝式电解加工的阴极设计制造困难,加工精度难以保证。尤其对整体叶轮上的扭曲叶片之类通道狭窄的零件表面,由于受工具阴极刚性及加工送进方式的限制,拷贝式电解加工更难以完成其加工任务。20世纪80年代初,以简单形状电极加工复杂型面的柔性电解加工数控展成电解加工的思想开始形成,它以控制软件的编制代替复杂的成形阴极的设计、制造,以阴极相对工件的展成运动来加工出复杂型面。这种加工方法工具阴极形状简单,设计制造方便,应用范围广,具有很大的加工柔性,适用于小批量、多品种、甚至单件试制的生产中。80年代中期,前苏联乌法航空学院特种加工工艺及设备研究所以过程控制为突破口,设计了一种柔性电解加工单元,应用特殊的电流脉冲波形和高选择性的电解液,加工精度达0.02mm,表面粗糙度达Ra0.20.6m。波兰华沙工业大学的Kozak教授于1986年率先提出了电解铣削的思想,以棒状旋转阴极作类似于圆柱状侧铣刀的成形运动来形成加工表面,成功地应用于直升机旋翼座架型面的加工,加工中采用NaNO3电解液,精度可达0.010.02mm,表面粗糙度达Ra0.160.63m。波兰Cracow金属切削学院的A.Ruszaj和J.Cekaj教授利用形似球头铣刀的工具阴极,进行了型面光整加工的试验研究,取得了形状误差小于0.01mm的加工效果,从而证明了该工艺在模具的光整加工方面具有很好的应用价值。美国、英国、俄罗斯都高度重视数控电解加工技术的研究并已得到应用,在新型航空发动机及航天火箭发动机的研制中发挥了重要作用。美国GE公司的五轴数控电解加工,美国、俄罗斯仿形电解加工带冠整体叶轮代表了数控电解加工整体叶轮的国际先进水平。2.本课题研究的主要内容和拟采用的研究方案、研究方法或措施2.1 研究的主要内容根据研究对象油箱盖热锻模,设计一套加工该热锻模的电解加工工装,包括:(1)连杆热锻模电解加工阴极;(2)装夹热锻模加工阴极和工件的夹具装置;(3)运用Pro/E、UG等软件画出油箱盖热锻模电解加工工装三维装配图。电解加工装置除了应保证工件装夹和定位外,还应考虑导电、供液、流场分布,非加工面的保护,工件和工具(即正负极、阴阳极)之间的绝缘等问题。课题研究的主要内容是通过对所给零件的分析,设计加工零件的阴极,以及装夹高温合金零件电解加工的阴极和工件的夹具装置。(1)在刚开始的时候工序的划分以及定位基准会比较难选择,所以就在过程中腰认真分析零件图,了解电解加工工装的结构特点及相关的技术要求而加工工序要根据生产类型,零件的结构来认真分析。(2)在夹具设计的时候也可能遇到问题,比如工件的定位是否正确,定位精度是否满足要求等等,所以要调查现阶段国内外比较先进的电解加工工装结构,从整体上把握设计的方向,了解电解加工工装的加工工艺规程及夹具的设计原理。(3)通过大量的资料,研究零件的结构,选择合适的加工方法,及选择合理的基准和工序安排。(4)熟悉夹具的结构选择合理的机床及装夹设备,确定加工余量和工序,进行精细的准确的尺寸计算,和时间的估算。2.2拟采用的研究方案2.2.1 方案一:从导电方面考虑设计方案,有两种选择,一是将电缆线引入,用线鼻子直接接到工件阳极跟工件阴极,二是在工作箱外将电源线接到滑枕体及不锈钢工作台,电流通过阴极安装板及工作台传导到阴极和阳极。前者线路损失小,且因工作台、夹具均不带电,可以采用耐蚀的非金属材料,如采用金属材料对不带电的零件则加以阴极保护,防止电化学杂散腐蚀。但此方案的缺点是工作箱内导线较多,走线较复杂,布局欠佳,每次装卸工件时还要拆卸线鼻子,并要防止正负极线鼻子相碰或正极线鼻子与工作箱相碰而引起送电时短路。所以选第二种方案。2.2.2方案二:从流场方面考虑设计方案,根据电解液的流动方向、加工送进方向及加工间隙之间的几何关系,可分为三种流动形式,即侧流式、正流式和反流式。可根据加工对象的几何形状确定流动形式。对于型面曲率变化不大的三维型面如一般叶片型面、叶片锻模型腔等,可采用侧流式,对于圆孔、型孔可采用正流式或反流式,对于某些复杂的型腔或型面,可在阴极上设计适当的通液槽(孔)采用正流式或反流式,或者两种流动形式都存在的复合流动形式进行加工。针对我的零件采用复合式。在流场设计方面还应该考虑电解液流速和进口压力。确定电解液流速的原则:(1)选则适当高的流速,能从加工间隙中带走电解产物,且使电解液流动处于紊流状态,这样有利于均匀流场并消除浓差极限,(2)选择适当高的流速以控制温升。电解液压力的确定,是指加工间隙进口处的压力和电解液输出泵的出口,考虑到管道中的压力损失,一般电解液泵出口压力需比电解液进口压力高0.05-0.1pa。2.2.3方案三:从阴极设计方面提出设计方案,对其阴极型管的直线度有严格要求。端面倒角10,在侧面间隙,约0.150.22mm,减去阴极单面涂层厚度约0.05mm,还有足够的间隙空间允许电解液顺畅通过;端面制成加工凸缘根据加工孔径的大小和精度要求,确定凸缘外径和加工刃带的宽度。3.本课题研究的重点及难点,前期已开展工作电
- 温馨提示:
1: 本站所有资源如无特殊说明,都需要本地电脑安装OFFICE2007和PDF阅读器。图纸软件为CAD,CAXA,PROE,UG,SolidWorks等.压缩文件请下载最新的WinRAR软件解压。
2: 本站的文档不包含任何第三方提供的附件图纸等,如果需要附件,请联系上传者。文件的所有权益归上传用户所有。
3.本站RAR压缩包中若带图纸,网页内容里面会有图纸预览,若没有图纸预览就没有图纸。
4. 未经权益所有人同意不得将文件中的内容挪作商业或盈利用途。
5. 人人文库网仅提供信息存储空间,仅对用户上传内容的表现方式做保护处理,对用户上传分享的文档内容本身不做任何修改或编辑,并不能对任何下载内容负责。
6. 下载文件中如有侵权或不适当内容,请与我们联系,我们立即纠正。
7. 本站不保证下载资源的准确性、安全性和完整性, 同时也不承担用户因使用这些下载资源对自己和他人造成任何形式的伤害或损失。

人人文库网所有资源均是用户自行上传分享,仅供网友学习交流,未经上传用户书面授权,请勿作他用。