【温馨提示】 购买原稿文件请充值后自助下载。
以下预览截图到的都有源文件,图纸是CAD,文档是WORD,下载后即可获得。
预览截图请勿抄袭,原稿文件完整清晰,无水印,可编辑。
有疑问可以咨询QQ:414951605或1304139763
目录
摘 要 2
关键词: 3
ABSTRACT 3
Keyword: 4
第1章绪论 4
1.1引言 4
1.2确定毛坯的制造形式 5
1.3零件的工艺分析 5
1.4国内形势 7
第2章 总体设计 8
2.1 机床联系尺寸图的绘制 8
2.2切削用量及时间定额 12
2.3.机床联系尺寸图 13
2.3.1联系尺寸图的作用及内容 13
2.3.2选择动力箱 14
2.3.3夹具轮廓尺寸确定 15
2.3.4机床装料高度 15
2.3.5中间底座轮廓尺寸 15
2.3.6确定多轴箱轮廓尺寸 17
2.3.7机床联系尺寸图绘制注意事项 18
2.4.机床生产率计算卡 19
第3章 主要技术参数 21
第4章 传动方案和传动系统图的拟定 22
第5章 主要设计零件的计算和验算 26
5.1主轴箱的箱体 26
5.2.传动系统的I轴及轴上零件设计 28
5.2.1普通V带传动的计算 28
5.2.2多片式摩擦离合器的计算 30
5.2.3齿轮的验算 32
5.2.4传动轴的验算 34
5.2.5轴承疲劳强度校核 36
结论 38
参 考 文 献 39
致谢 40
摘 要
众所周知,在现代机械制造业中,企业对专用机床有着广泛的需求。一般钻床劳动强度大,专用性能低,生产率不高且不能保证精度;而专用钻床操纵方便、省力、容易掌握,不易发生操作错误和故障,不仅能减少工人的疲劳,保证工人和钻床的安全,还能提高钻床的生产率。因此,专用机床的使用,对企业的竞争力有着十分重要的作用。本文针对一般钻床上述种种缺点及加工对象的具体情况设计一台曲轴油孔专用钻床,力求达到满足性能要求,经济效益和人机关系等技术经济指标。
这次我设计的任务是,用来钻削曲轴轴颈上的油孔,该油孔的直径约10mm、孔深约100mm。我的具体任务就是钻2个Φ10的通孔。曲轴油孔的零件图, 精度要求比较高。为了保证加工要求,经过对零件的分析,拟订出工艺。根据加工要求,本道工序采用专用钻床进行加工。在夹具设计中,对零件图进行分析,采用工件采用三面定位,以底面为主要定位面,后面为导向面,左侧面为止推面。采用此方法限制了六个自由度,为完全定位。主轴箱的设计中,以提高主轴的刚度,采用刚性主轴,由于我所设计的是卧式钻床,主要承受的是径向力,所以在三爪自定心卡盘上装夹。三爪自定心卡盘的三个卡爪是同步运动的,能自动定心,一般不需要找正。该卡盘装夹工件方便、省时,但夹紧力小,适用于装夹外形规则的中、小型工件。而机床总体设计中,各部件的设计,要以有利于操作者操作为设计方向,从而达到进一步提高劳动生产效率,降低生产成本的最终目的。
关键词:
专用钻床、曲轴油孔、机床夹具
ABSTRACT
As everyone knows, in the modern mechanical manufacturing, enterprise has extensive demand for special machine tool. Ordinary drilling machine, high labor intensity, the special properties of low, productivity is not high and the accuracy can not be ensured; and the special drill press convenient operation, labor-saving, easy to master, not easy to operation mistake and failure, not only can reduce the fatigue of workers, to ensure the safety of workers and drilling machine, drilling machine can improve the productivity. Therefore, the use of special machine tools, has a very important effect on the competitiveness of enterprises. In this paper, according to the specific cases of the general machine faults and processing object to design a special crankshaft oil hole drill, and strive to meet the performance requirements, technical and economic indicators of economic and human relations.
This time I design task is the special machine, used for drilling oil hole of crankshaft journal, the oil hole diameter of about 10mm, the hole depth is about 100mm. The specific task is to drill holes 2Φ 10. The crankshaft oil hole parts diagram, with relatively high precision. In order to guarantee the processing requirements, parts of the analysis, a process. According to the requirements of the processing, the exclusive use of a process of drilling machine processing. In fixture design, carries on the analysis to the parts drawing, the workpiece surface by three positioning, to the bottom as the main location, behind the guide surface, left side thrust surface. Using this method limits the six degrees of freedom, for the complete localization. Spindle box design, in order to improve the stiffness of the spindle, the spindle rigidity, because what I design is horizontal drilling machine, mainly bear the radial force, so in the three claw chuck clamping. Three claw, three claw chuck is synchronous movement, automatic centering, generally do not need to find it. The chuck clamping the workpiece is convenient, time-saving, but the clamping force is small, suitable for clamping the regular shape of workpiece, small. The overall design of machine tools, the design of each component, to help operator to design direction, so as to further improve labor productivity, reduce the production cost of the ultimate goal.
Keyword:
Special drill press, the crankshaft oil hole, machine tool fixture
第1章绪论
1.1引言
毕业设计是我们在学完了大学全部基础课、专业课之后进行的一次系统的、全方位的综合性训练,也是搭建从学校到工作岗位非常重要的“桥梁”。在这次毕业设计中,我应用到了我在大学所学的知识探索并解决设计中遇到的问题,是我从一名普通大学生跨入到设计者行列之中不可缺少的一步,在这次设计中我初步了解了正确的设计方法,也使我具具有了初步的提出问题、分析问题、解决问题的能力,可以说这次毕业设计为我以后成为一名优秀的设计者打下了坚实的基础。
这次我的设计,首先了解曲轴油孔的工艺分析, 掌握机床总体设计,根据轴类工件的特点,采用卧式机床。机床夹具设计,是这次设计的重点,夹具设计的思路是:①明确设计任务,收集设计资料;②拟订夹具的结构方案、绘制结构草图;③绘制夹具总装图。





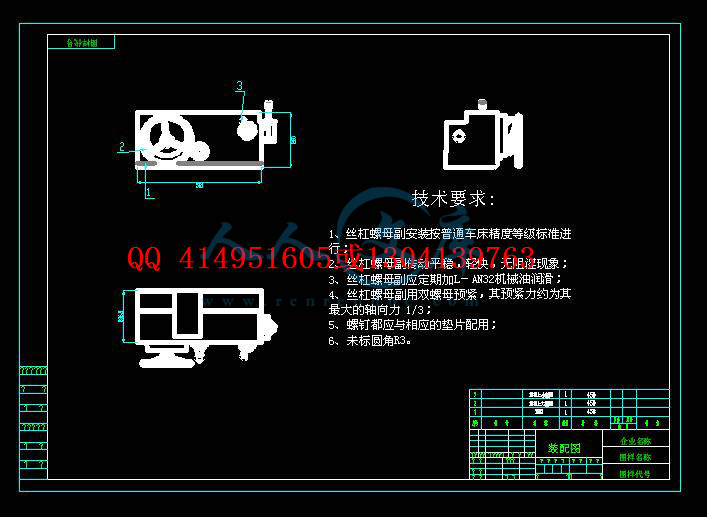


