双辊连铸机主传动系统的设计【优秀3+2张CAD图纸】
【带外文翻译+43页@正文16900字】【详情如下】【需要咨询购买全套设计请加QQ1459919609 】.bat
中等厚度薄板连铸技术研究外文文献翻译@中英文翻译@外文翻译.doc
分齿箱总装图.dwg
分齿箱总装图.pdf
副本图纸
双辊连铸机主传动系统的设计.doc
总装图.dwg
总装图.pdf
说明书副本.pdf
目录
第 1 章 绪论1
第 2 章 双辊连铸机传动系统与分齿箱7
第 3 章 双辊连铸机主传动部分设计11
第 4 章 连续铸钢的经济效益分析38
结束语40
致谢41
参考文献42
第 1 章 绪论
1.1 国内外连铸技术的发展概况
连续铸钢由于与常规生产相比具有生产工序简化,金属收得率提高,能源消耗降低, 劳动条件得到改善和连铸坯质量好等优越性,因此,是当前钢铁行业中发展最快的技术 之一,现在,全世界的连铸比(见表 1.1)和连铸坯产量在不断增加,围绕连铸的新技 术,新工艺,新设备,在不断的开发成功并被加以广泛推广应用,连续铸钢已经成为钢 铁行业生产中必不可少的工艺环节,是否发展连铸技术以及技术水平的高低,生产进行 的如何已经成为衡量各个钢铁生产企业生产,技术,管理水平的标志之一。
从一九九五年美国亨特工程公司研制开发成功的第一台连铸轧机以来,世界上不少 国家也先后研制成功了一些不同形式的连铸轧机。比较典型的有法国 3C,联邦德国的 克虏柏。国内从六十年代初开始研制连续铸轧设备,到目前为止已经制造出了第四代。 1.2 双辊连铸机主传动系统比较
从设备的发展状况看,亨特和国产Ⅳ型采用了多辊矫直机,张力在卷曲机和矫直机 之间产生,对主机无影响,只单纯起卷曲,卷紧带材的作用。3C 和克虏柏取消了矫直 机,使主机直接与卷曲设备构成张力。3C 还取消了牵引机,通过实践得出,在主机与 卷曲机之间产生一定的张力,可使铸轧同类产品时减少一定的轧制力和粘辊程度,对卷 齐带材,减少带材擦伤也有好处,并且,3C 和克虏柏与亨特相比,可减少 2~3 米的系 列长度。
从机架结构上看,亨特、3C 和克虏柏均采用闭式机架,并且都有简易换辊装置, 这里克虏柏铸轧机又采用了一套液压倾翻机构,可使机架在换辊时与地面垂直。而国产 Ⅳ型采用开式机架,用天车吊出轧辊。这样虽然减少了换辊空间,取消了换辊装置,却 大大延长了换辊时间,降低了设备利用率,增大了劳动强度。3C 法成功地采用了立式 铸轧工艺,使轧辊的更换更加容易,简化了换辊装置。
在驱动方面,克虏柏采用了两套轧机驱动系统,它包括直接安装在两个轧辊轴颈上 的液压马达和行星齿轮箱。两个驱动系统即可联动又可单动。每个油马达即可输出最大 力矩又可使其相互间按比例输出力矩。与传统驱动方式相比,它结构紧凑,总轴向尺寸
大约减少了 30~40%,取消了带齿型接手和花键的复杂而昂贵的机—电系统。由于轧辊 与驱动装置一同调整,从而有效的减少了换辊时间。其缺点是上下辊分别驱动,增加了 两辊的同步控制。
参考文献
[1]齿轮手册编委会.齿轮手册.北京:机械工业出版社.2000.8.
[2]徐灏.机械设计手册.北京:机械工业出版社,1991.9.
[3]倪思康.双辊薄带连铸研究.全国连铸技术研讨会论文集.上海:1994.11. [4]熊毅刚.板坯连铸.冶金工业出版社.1994.
[5].连续铸钢手册.冶金工业出版社.1990.
[6]国外连铸连轧方法评述.中南矿冶学院科技情报室.1978年8 月.
[7]徐有荣等.液态铸轧低碳钢板的研究.钢铁出版社.1986.
[8]周明衡.减速器选用手册.北京:化学工业出版社.2002.4.
[9]赵家礼.电动机维修手册.北京:机械工业出版社.2003.
[10]卜炎.机械传动装置设计手册.北京:机械工业出版社.1998.12.
[11]王海文.轧钢机械设计.北京:机械工业出版社.1983.6.
[12]王建中.公差与制图技术手册.沈阳.辽宁科学技术出版社.1939.1


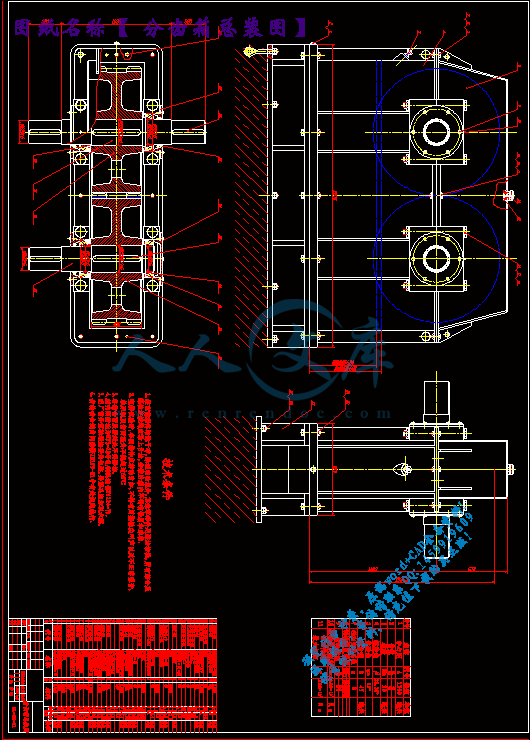
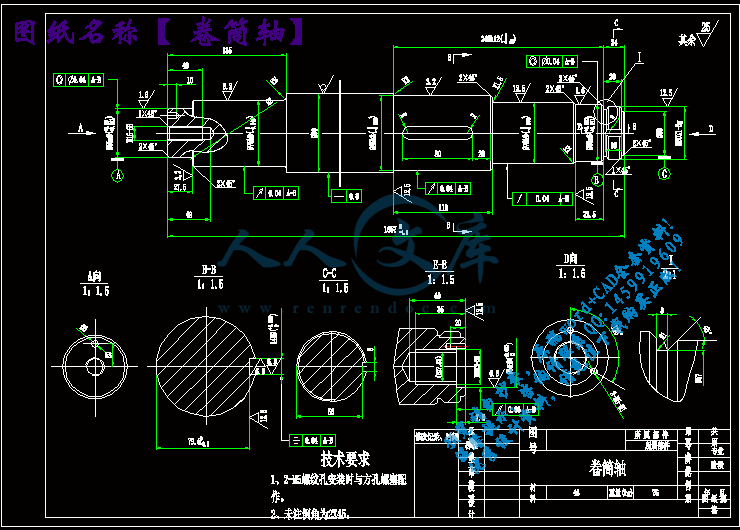


