筒形件的落料、拉伸复合模及单工序冲孔模具设计【优秀冲压复合模设计+18张CAD图纸】
筒形件的落料、拉伸、冲孔复合模具设计
筒形件的冲压复合模具设计
电器开关网芯零件的落料、拉伸复合模及单工序冲孔模具设计
电器开关网芯的冲压工艺规程及模具设计
电器开关网芯的冲压工艺及模具设计
单工序冲孔模具设计
落料、拉伸复合模及单工序冲孔模具的设计
筒形件的落料、拉伸复合模及单工序冲孔模具设计【优秀冲压复合模设计+18张CAD图纸】
【带2套模具+任务书+开题报告+外文翻译+32页@正文11800字】【详情如下】【需要咨询购买全套设计请加QQ1459919609 】.bat
Recent developments in sheet hydroforming technology.pdf
Stamping formability of pure titanium sheets.pdf
上模座.dwg
下模座.dwg
中文摘要.doc
任务书.doc
冲头.dwg
冲孔模具上模座 .dwg
冲孔模具下模座 .dwg
冲孔模具卸料板 .dwg
冲孔模具装配图.dwg
凸模.dwg
凸模固定板.dwg
凹模.dwg
卸料板.dwg
压料板.dwg
垫板.dwg
复合模具打印图纸总汇17张.dwg
开题报告.doc
拉深凹模.dwg
推件器.dwg
目录.doc
第1套落料拉深复合模具
第2套冲孔模具
翻译.doc
英文摘要.doc
落料凹模.dwg
落料拉深复合模具总装图.dwg
论文.doc
零件图.dwg
南 昌 航 空 大 学 科 技 学 院
毕业设计(论文)任务书
I、毕业设计(论文)题目:
筒形件零件冲压工艺及模具设计
II、毕业设计(论文)使用的原始资料(数据)及设计技术要求:
一.原始资料:
(1)筒形件零件图 1张,零件大批量生产
(2)冷冲模标准 1套
二.技术要求:
(1)设计出的冲压模具能保证有正确的板料定位和冲压顺序动作、送料和取件方便;模具结构
紧凑;装配关系准确。
(2)设计出的模具零件图尺寸齐全、加工要求和材料选择合理。
III、毕业设计(论文)工作内容及完成时间:
3月19日~3月25日: 课题调研,查阅有关资料(至少含两篇外文资料);
3月26日~4月10日: 撰写开题报告,翻译一篇外文资料;
4月11日~4月19日: 熟悉AutoCAD/UG软件,进行零件三维造型;
4月20日~4月28日: 针对所给的冲压件进行工艺分析,提出工艺设计方案;
4月29日~5月25日: 绘制所需冲压模具装配图;
5月26日~6月9日: 绘制冲压模具全套模具零件图;
6月10日~6月16日: 撰写毕业设计论文,并装订。
Ⅳ、主要参考资料:
[1]王孝培主编. 冲压手册(修订本)[M].北京:机械工业出版社. 1990年
[2]姜奎华主编. 冲压工艺与模具设计[M]. 北京:机械工业出版社. 1997年
[3]薛啓翔等编著. 冲压模具设计制造难点与窍门[M].北京:机械工业出版社. 2003年
[4]Sang-Wook Lee. A Study on the bi-directional springback of sheet metal stamping[J]. Journal of
Materials Processing Technology. 167(2005):33-40
[5]S.H.Zhang,Z.R.Wang,Y.Xu,Z.T.Wang,L.X.Zhou. Recent developments in sheet hydroforming
technology[J]. Journal of Materials Processing Technology. 151(2004):237-241
筒形件零件冲压工艺及模具设计
摘要:冲裁是利用冲模使部分材料或工序件与另一部分材料、工(序)件或废料分离的一种冲压工序。冲裁是切断、落料、冲孔、冲缺、冲槽、剖切、凿切、切边、切舌、切开、整修等分离工序的总称。冲孔是将废料沿封闭轮廓从材料或工序件上分离的一种冲压工序,在材料或工序件上获得需要的孔。
本设计进行了落料、拉伸复合模和单工序冲孔模具的设计。文中简要概述了冲压模具目前的发展状况和趋势。对产品进行了详细工艺分析和工艺方案的确定。按照冲压模具设计的一般步骤,计算并设计了本套模具上的主要零部件,如:凸模、凹模、凸模固定板、垫板、凹模固定板、卸料板、导尺、挡料销、导正销等。模架采用标准模架,选用了合适的冲压设备。设计中对工作零件和压力机规格均进行了必要的校核计算。模具的冲孔和落料凸模分别用不同的固定板固定,便于调整间隙;冲孔凹模和落料凹模则采用整体固定板固定。落料凸模内装有导正销,保证了工件上孔和外形的相对位置准确,提高了加工精度。如此设计出的结构可确保模具工作运行可靠和冲压产品大批量生产的要求。
关键词:复合模;冲压模具;标准模架;冲压设备;校核;冲孔;落料
Electrical switches network-parts stamping process and die design
Abstract: Die Blanking is to use some of the material or process conditions and other materials, processes or pieces of waste separation of a stamping process. Blanking is Cut-off、Falls the material、Punch holes、Flushes lacks、Flushes the trough、Splits cuts、Splits cuts、The chisel cuts、Cutting edge、Cuts the tongue、Incision、Renovation and other separation processes known. Punch will be closed along the contour waste materials or processes from the isolated pieces of a stamping process, the materials or processes obtained on the needs holes.
The design of the loading material, tensile modulus and single composite processes Piercing Die Design. This paper briefly outlined the Stamping Die current development status and trends. Identify the product of a detailed analysis and the process. Stamping die design in accordance with the general steps to calculate and design the sets on the main mold parts, such as: Terrace die、Cavity die、Punch-holder、Dunn age、Die holder、Stripper、 Jig、Pin stop、Pilot and so on. Die-standard model planes, to choose a suitable stamping equipment. Design work on the parts and specifications will press for the necessary checking calculation. Punch and Die blanking punch were different plate fixed to facilitate adjustment gap; Punch and Die blanking die is used overall fixed plate. Blanking punch contents is a derivative sales, and guarantee the work piece and the shape of the holes in the relative position accurately, improve processing accuracy. So the structure is designed to ensure reliable operation of die stamping products and the requirements of large-scale production.
Keywords: Combination die;Stamping die tool;Standard die set;Stamping Equipment;Check;Punch;Blanking.
Signed guidance of the teachers:
目 录
中文摘要 Ⅰ
英文摘要 Ⅱ
1 绪论1
1.1 概述1
1.2 冲压技术的进步1
1.3 模具的发展与现状2
1.4 模具CAD/CAE/CAM技术6
1.5 课题的主要特点及意义8
2 冲压工艺方案的制定8
2.1 工艺分析9
2.2 排样图设计11
3 模具总体结构设计11
3.1定位装置13
3.2 出料装置15
4 模具零件的设计与计算16
5 冲压设备的选用18
6 压力中心的计算20
7 冲压件的工艺分析20
8 冲孔工序的计算21
8.1 确定模具压力中心21
9计算凸、凹模刃口尺寸21
10模具总体设计及主要零部件设计22
11模具生产中的故障分析及其解决办法25
12总结26
致谢27
参考文献28
附录
附录A 毕业论文开题报告
附录B1 翻译原文
附录B2 翻译译文
1 绪论
1.1 概述
冲压成形作为现代工业中一种十分重要的加工方法,用以生产各种板料零件,具有很多独特的优势,其成形件具有自重轻、刚度大、强度高、互换性好、成本低、生产过程便于实现机械自动化及生产效率高等优点,是一种其它加工方法所不能相比和不可替代的先进制造技术,在制造业中具有很强的竞争力,被广泛应用于汽车、能源、机械、信息、航空航天、国防工业和日常生活的生产之中。
在吸收了力学、数学、金属材料学、机械科学以及控制、计算机技术等方面的知识后,已经形成了冲压学科的成形基本理论。以冲压产品为龙头,以模具为中心,结合现代先进技术的应用,在产品的巨大市场需求刺激和推动下,冲压成形技术在国民经济发展、实现现代化和提高人民生活水平方面发挥着越来越重要的作用。
参考文献
[1] 李硕本等编著.冲压工艺理论与新技术[M].北京:机械工业出版社,2002.11
[2] 中国模具工业协会.模具行业“十一五”规划[J].模具工业,2005(7):3-8
[3] 李大鑫,张秀锦.模具技术现状与发展趋势综述[J].模具制造,2005 (2):1-4
[4] 李德群,肖祥芷.模具CAD/CAE/CAM的发展概况及趋势[J].模具工业,2005(7):9-12
[5] 姜奎华主编.冲压工艺与模具设计[M].北京:机械工业出版社,1998.5
[6] 薛啓翔等编著.冲压模具设计制造难点与窍门[M].北京:机械工业出版社,2003.7
[7] 模具实用技术丛书编委会编.冲模设计应用实例[M].北京:机械工业出版社,1999.6
[8] 郑家贤遍著.冲压工艺与模具设计实用技术[M].北京:机械工业出版社,2005.1
[9] 《冲模设计手册》编写组编著.冲模设计手册[M].北京:机械工业出版社,1999.6
[10] 王孝培主编.冲压手册(修订本)[M].北京:机械工业出版社,1990
[11] Yazheng Liu, Jinghong Sun, et al. Experiment investigation of deep-drawing sheet texture evolution. Journal of Materials processing Technology,140(2003):509-513
[12] 周岁华.汽车冲压材料的合理选择[J].汽车工艺与材料,2005(12):25-28
[13] Yingbin Bao. A comparative study on various ductile crack formation criteria. Journal of engineering materials and technology,2004(7): 314-324
[14] 冯开平,左宗义主编. 画法几何与机械制图[M].广州:华南理工大学出版,2001.9
[15] 李天佑主编.冲模图册[M].北京:机械工业出版社, 1994
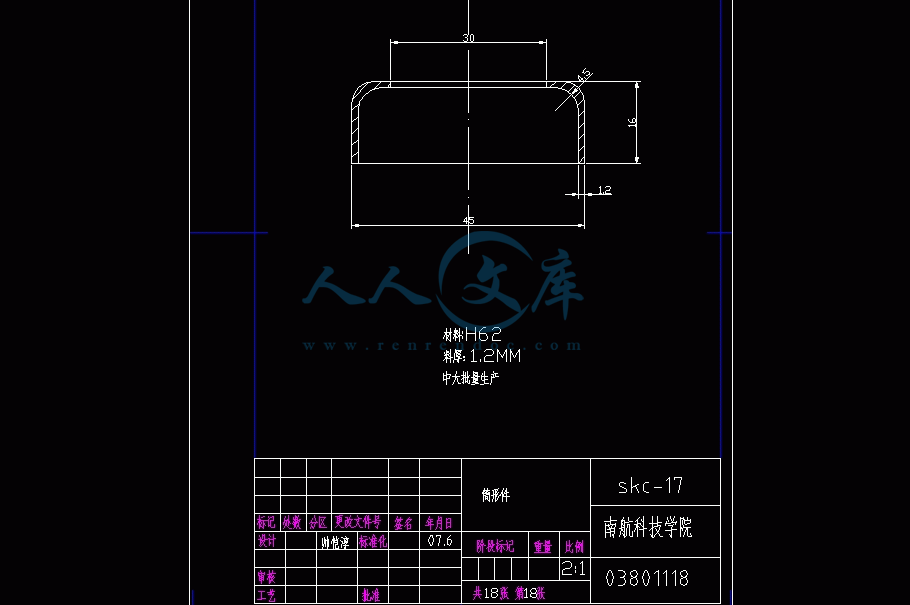
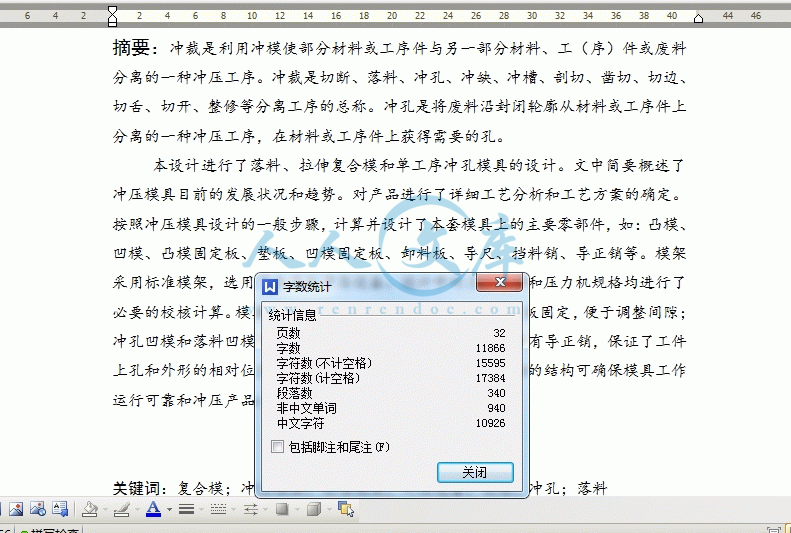


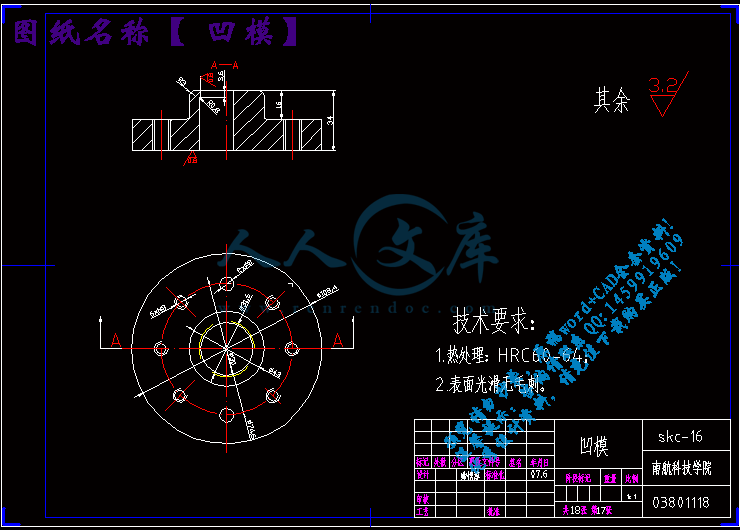
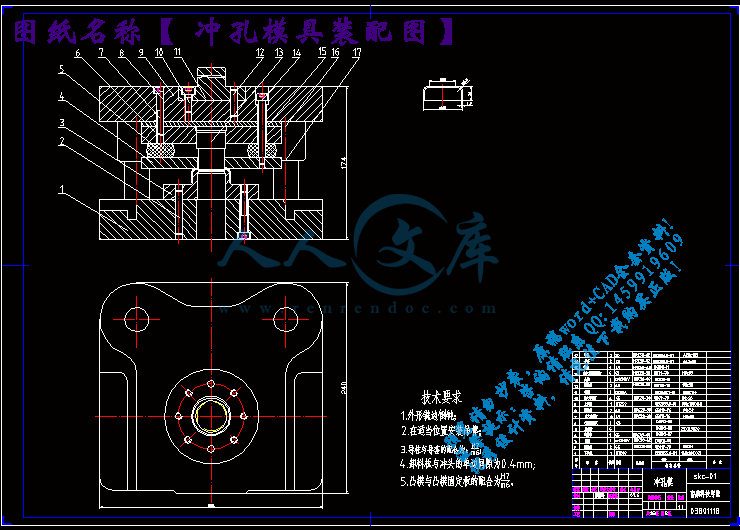



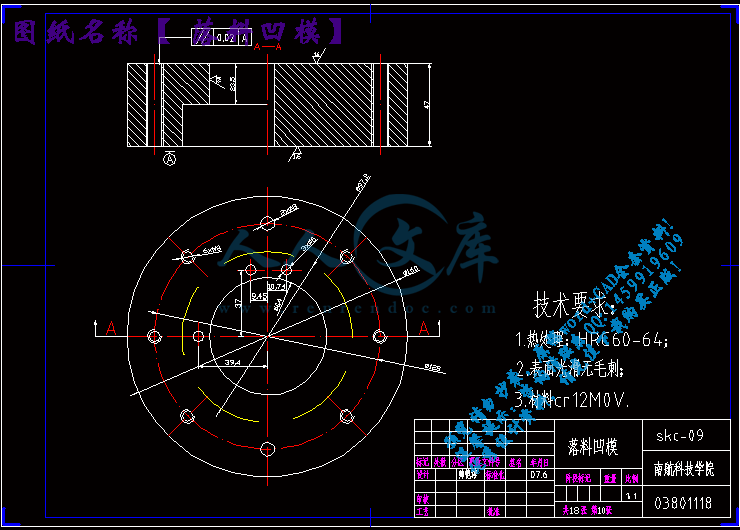
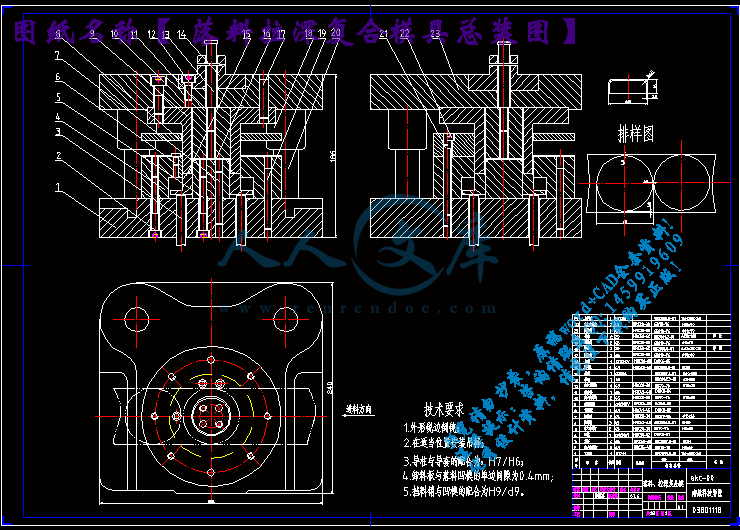
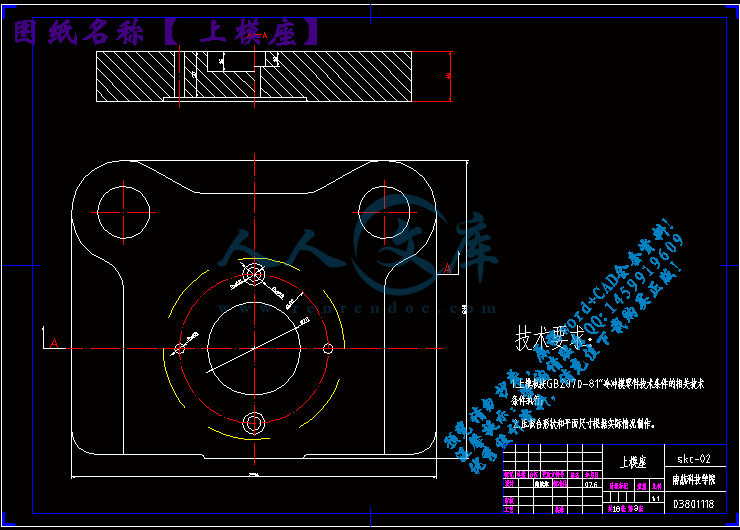
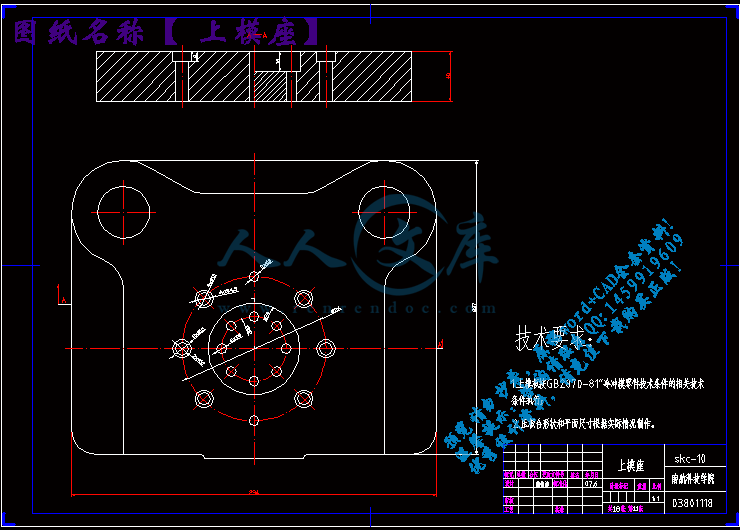

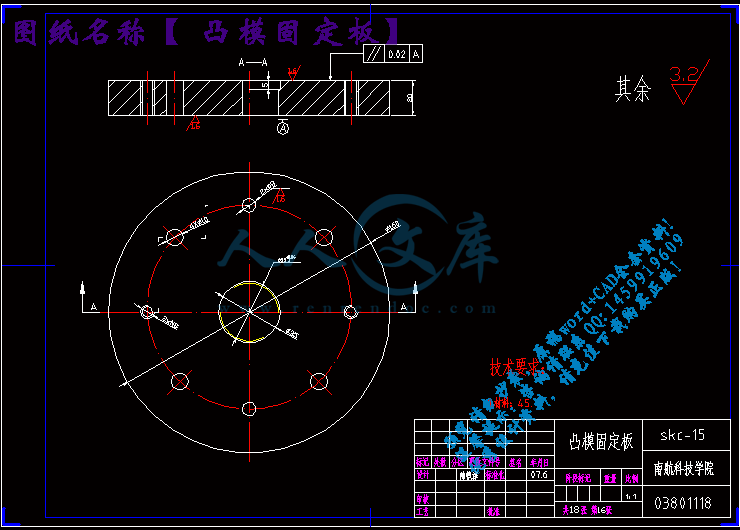


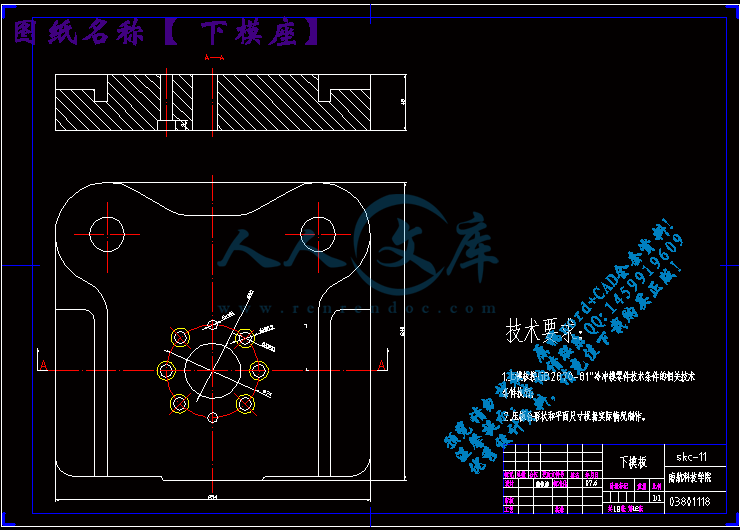
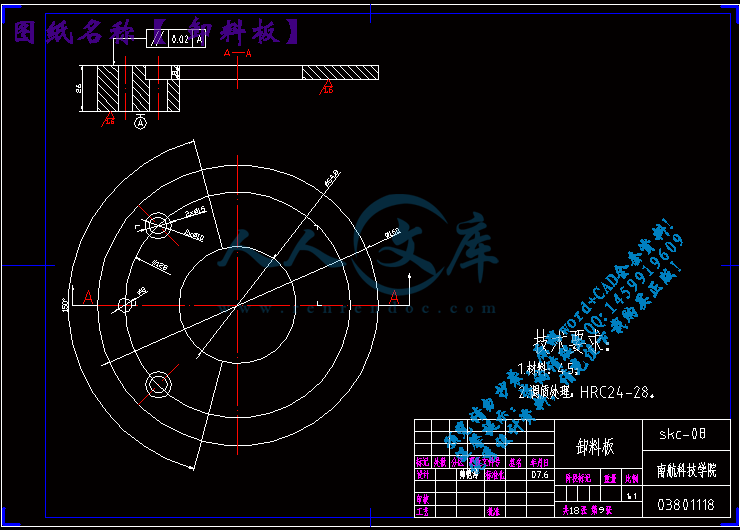
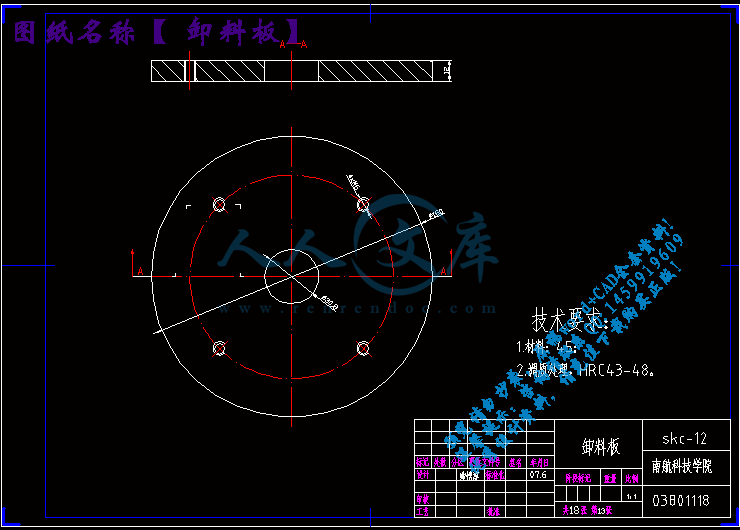
