轧辊车床PLC触摸屏控制系统设计
基于plc的轧辊车床触摸屏控制系统设计【优秀PLC系统设计+4张CAD图纸】
【带任务书+36页@正文15200字】【详情如下】【需要咨询购买全套设计请加QQ1459919609 】.bat
IO接口图A0.dwg
主电路图.dwg
任务书.doc
封面.docx
摘要1.doc
梯形图A0.dwg
系统方框图A1.dwg
轧辊车床PLC触摸屏控制系统设计正文.doc
任务书
题目名称轧辊车床PLC触摸屏控制系统设计
一、设计目的、意义
轧辊车床主要应用与冶金制造行业,它主要是对各类长短不同、重量不同的轧辊外表层进行切削加工。由于在轧辊切削过程中对切削速度、刀架档位及进刀速度有特殊要求,所以控制轧辊车床的PLC输入/输出点数也相应增多,同时考虑到余量,可选用欧姆龙中型C200Hα系列PLC。该系列PLC集中了“信息化对应控制器”功能的SYSMACa系列可编程控制器,实现了工业现场的自动控制。同时,触摸屏的加入使操作更加方便,实时的报警信息是维护和改进更加方便。
本课题主要介绍了欧姆龙PLC及触摸屏在轧辊车床上的应用,通过对轧辊车床基本功能及运动方式的介绍,增加了读者对PLC各个通道的地址分配及PLC程序设计的认识;。
二、设计内容、技术要求(研究方法)
设计内容,
1)PLC及连接PLC外围设备选用
2)触摸屏组件选用,人机界面选用
3)PLC输入与输出硬件接线设计,PLC与主轴和刀架硬件的接线设计,PLC地址分配
4)PLC与触摸屏画面的通信设置
技术要求
1)以PLC作为控制核心
2)所设计的控制系统要能满足实际要求
3)组态软件设计的操作界面要友好,易操作
三、设计完成后应提交的成果
1.开题报告一份;
2.设计说明书一份,不少于1.5万字;
3.技术资料
(1)PLC控制系统的IO接线图:A0图纸一张;
(2)PLC控制系统梯形图:A0图纸一张;
(3)轧辊车床系统框图:A1图纸一张。
四、设计进度安排
2012年2月27日-2012年3月4日——接受任务,市场调查;
2012年3月5日-2012年3月18日——查阅文献、收集资料,撰写并提交开题报告;
2012年3月19日-2012年4月1日——确定设计方案。
2012年4月2日-2012年4月15日——IO接线设计 IO地址分配
2012年4月16日-2012年4月29日——刀架及主轴的接线设计,PLC与人机界面的连接设计
2012年4月30日-2012年5月13日——触摸屏画面组态设计
2012年5月14日-2012年6月3日——轧辊车床PLC程序设计
2012年6月4日-2012年6月10日——撰写设计说明书并用计算机绘图;
2012年6月11日-2012年6月15日——完成说明书及图纸的打印,准备答辩。
五、主要参考资料
[1] 关学锋,3-PTT型滑块式并联机床的PLC控制【M】,机械设计与制造文章 ,2009(5):317—320
[2] 熊幸明,千斤顶油缸加工专用机床的PLC控制系统设计【M】,机床电器文章, 2002(2):214—225
[3] 吴晓,活塞环仿形车、铣组合机床PLC控制的研究【J】,南通工学院学报,1999(11):317—323
[4] 杨世成,基于PLC控制的三轴钻专机控制系统设计【M】,机电产品开发与创新,2009(9):112—115
[5] 杨滨,基于PLC控制系统的电解加工机床改造【M】,新技术新工艺文章, 2011(1):23—27
[6] Michel Gilles.Programmabe Logic Controllers:Architecture and Application Wiley【M】.1990.242
[7] G.L.Batten. Programmabe Controllers:hardware.software and Application..New York:MC Graw-Hill【M】,1994,212:234
摘 要
在国内轧辊制造行业使用的重型轧辊车床中,有许多是20世纪60年代和70年代制造的,目前仍作为轧辊加工的主要设备在服役。它们的主拖动普遍采用大功率直流电动机来实现,调速手段除少数延用F一D机组形式外,多数在20世纪80年代完成了第一步改造。利用PLC控制单元驱动伺服电动机合理的无级调速范围,代替原来纯机械的有级变速,进而达到在不降低机械传动性能的情况下,简化机械传动系统,改进机床操作性能。成功应用在重型轧辊车床上。
本文介绍了触摸屏PLC控制系统在C84型轧辊车床上的应用,其中包括轧辊车床的组成、参数说明、控制系统构成及选型、扎辊车床的硬件接线、PLC输入/输出地址分配、触摸屏画面的组态、PLC梯形图程序、指令表程序及PLC与触摸屏的通信。通过对轧辊车床PLC及触摸屏的介绍,我们进一步熟悉了PLC与触摸屏的设计方法及在工程应用中所要注意的问题。
关键词:轧辊车床;PLC;触摸屏;梯形图;组态
ABSTRACT
Heavy-duty roll lathe roll in the domestic manufacturing industry, many of which are manufactured in the 1960s and 1970s, is still as roll processing equipment in service. The main drag of commonly used high-power DC motor speed control means in addition to a few continue to use the F-D unit in the form, most completed in the 1980s the first step in the transformation. Stepless speed range of the PLC control unit to drive the servo motor instead of the original pure mechanical variable speed, and then reached in the case without reducing the performance of mechanical transmission, simplifying the mechanical drive system, improved the performance of the machine operator. Successfully applied in heavy-duty roll lathe.
This article introduces a touch screen PLC control system in the bed of the C84-type roller vehicle, including the composition of the rolling roll lathe the parameter descriptions, control systems constitute and selection bar roll lathe of hardware terminal, the PLC input / output address allocated, touch-screen picture of theconfiguration, PLC ladder program instruction list program and the PLC and touch screen communication. The introduction of the roll lathe PLC and touch screen, we become more familiar with PLC and touch screen design and pay attention to problems in engineering applications.
Key words: Roll lathe; PLC; touch screen; ladder ;Configuration
目 录
摘 要………………………………………………………………………………………Ⅰ
Abstract……………………………………………………………………………………Ⅱ
第1章 绪论………………………………………………………………………………1
1.1 选题背景及研究的目的和意义……………………………………………………1
1.1.1选题背景……………………………………………………………………1
1.1.2研究的目的与意义…………………………………………………………2
1.2 基本内容和拟解决的问题…………………………………………………………3
1.2.1基本内容……………………………………………………………………3
1.2.2拟解决的问题………………………………………………………………3
第2章 轧辊车床的主要结构与控制要求…………………………………………4
2.1轧辊车床的主要结构………………………………………………………………4
2.2轧辊车床的控制要求………………………………………………………………4
2.3继电器电气线路的分析……………………………………………………………6
2.3.1主电路分析…………………………………………………………………6
2.3.2控制电路分析………………………………………………………………6
2.3.3整机线路联锁与保护………………………………………………………7
2.4 本章小结……………………………………………………………………………7
第3章 元器件的选择…………………………………………………………………8
3.1 伺服电动机的选择 ……………………………………………………………… 8
3.2 直流电机的选择 …………………………………………………………………10
3.3 本章小结 …………………………………………………………………………10
第4章 控制系统的硬件设计………………………………………………………11
4.1 确定I/O点数 ……………………………………………………………………11
4.2 PLC 的选型 ………………………………………………………………………12
4.3 PLC I/O 分配表 …………………………………………………………………16
4.4 PLC 控制系统外部接线图设计 …………………………………………………17
4.5 轧辊车床PLC与人机界面的连接 ………………………………………………17
4.6 本章小结 …………………………………………………………………………18
第5章 控制系统的软件设计………………………………………………………19
5.1 控制系统程序设计 ………………………………………………………………19
5.2 本章小结 …………………………………………………………………………27
结论………………………………………………………………………………………28
参考文献…………………………………………………………………………………29
致谢………………………………………………………………………………………31
第1章 绪 论
1.1 选题背景及研究的目的与意义
1.1.1 选题背景
在国内轧辊制造行业使用的重型轧辊车床中,有许多是20世纪60年代和70年代制造的,目前仍作为轧辊加工的主要设备在服役。它们的主拖动普遍采用大功率直流电动机来实现,调速手段除少数延用F一D机组形式外,多数在20世纪80年代完成了第一步改造。利用PLC控制单元驱动伺服电动机合理的无级调速范围,代替原来纯机械的有级变速,进而达到在不降低机械传动性能的情况下,简化机械传动系统,改进机床操作性能。成功应用在重型轧辊车床上。
现代化生产的水平、产品的质量和经济效益等各项指标,在很大程度上取决于生产设备的先进性和电气自动化程度。机电一体化技术是随着科学技术的不断发展,生产工艺不断提出新的要求而迅速发展的。在控制方法上主要是从手动到自动;在控制功能上,是从简单到复杂;在操作上,是由笨重到轻巧。随着新的控制理论和新型电器及电子器件的出现,又为电气控制技术的发展开拓了新的途径。
传统的机床电气控制是继电器接触式控制系统,由继电器、接触器、按钮、行程开关等组成,实现对机床的启动、停车、有极调速等控制。继电器接触式控制系统的优点是结构简单、维护方便、抗干扰强、价格低,因此广泛应用于各类机床和机械设备。目前,在我国继电器接触式控制仍然是机床和其他机械设备最基本的电气控制形式之一。
参考文献
[1] 关学锋,3-PTT型滑块式并联机床的PLC控制[M],机械设计与制造,2009(5):317-320
[2] 熊幸明,千斤顶油缸加工专用机床的PLC控制系统设计[M],机床电器, 2002(2):214-225
[3] 吴晓,活塞环仿形车、铣组合机床PLC控制的研究[J],南通工学院学报,1999(11):317-323
[4] 杨世成,基于PLC控制的三轴钻专机控制系统设计[M],机电产品开发与创新,2009(9):112-115
[5] 杨滨,基于PLC控制系统的电解加工机床改造[M],新技术新工艺文章, 2011(1):23-27
[6] 宋志峰,多工位于组合机床中PLC控制系统的应用[M],装备制造技术,2011(2):234-245
[7] 赵良,PLC控制技术在自动机床扩切机中的应用[M],工业控制计算,1996(10):210-215
[8] 陈远龙,电解加工机床PLC控制系统调试技术[C],第13届全国特种加工学术会议论文集,2009:323-345
[9]王凯,触摸屏和PLC控制系统在在轧辊磨床上的应用[M],现代机械,2010(2):314-334
[10]许其清,基于触摸屏与PLC控制的铜铝复合散热器自动焊接专机的电气系统设计[M],仪器技术与传感器 ,2007(10):112
[11]苟晓卫,PLC与触摸屏快速入门与实践[M],机床电器,2010(8):342-347
[12]范永胜.电气控制与PLC应用[M].北京:中国电力出版社,2008.
[13]皮壮行.可编程序控制器的系统设计与应用实例[M].北京:机械工业出版社,2009.
[14]常斗南.可编程控制器原理、应用、实验[M].北京:机械工业出版社,2009.
[15]王也平.可编程序控制器原理及应用[M].成都:西南交通大学出版社,2009.
[16]李宗宝.PLC控制原理分析及其在工业中的应用[J].中国高新技术业,2009,(4):66-67.
[17]李嘉强.PLC在电机控制中的典型应用[J].机电信息,2009,(24):65-66.
[18]丁炜,魏孔平.可编程控制器在工业控制中的应用[M].化学工业出版社,2008.

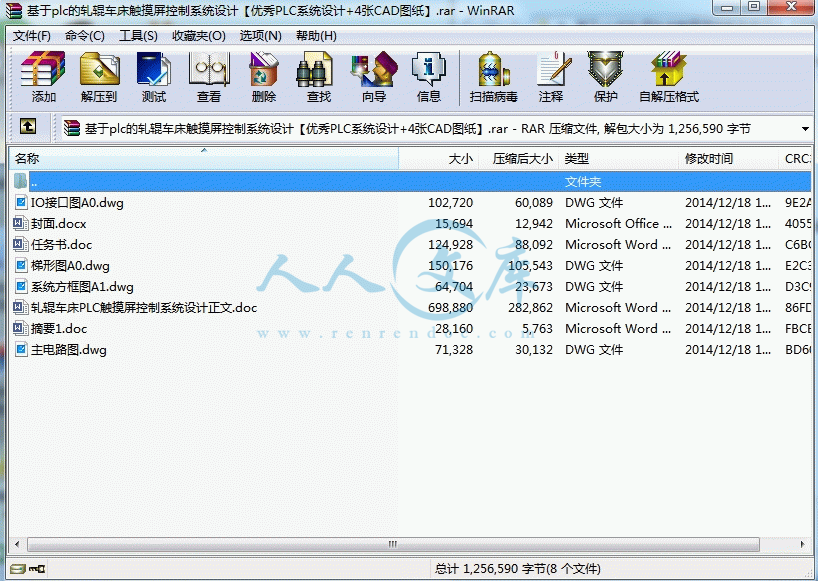

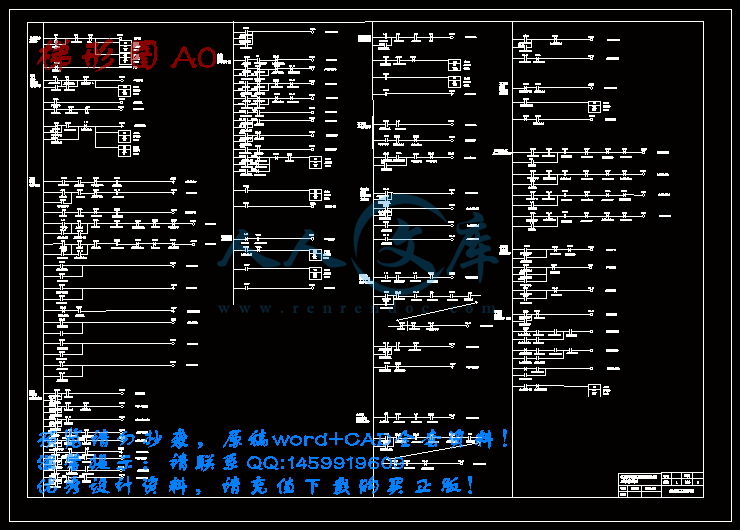
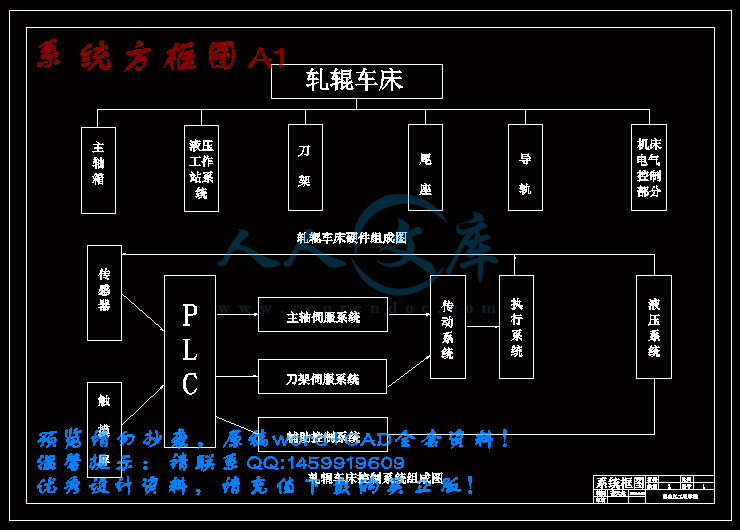
