截面管材滚切机设计
36页 14000字数+说明书+任务书+开题报告+4张CAD图纸【详情如下】
任务书.doc
内封评语.doc
切管机.dwg
夹爪(A3).dwg
截面管材滚切机设计开题报告.doc
截面管材滚切机设计论文.doc
新型圆截面管材滚切机装配图.dwg
滚切小齿轮(A1).dwg


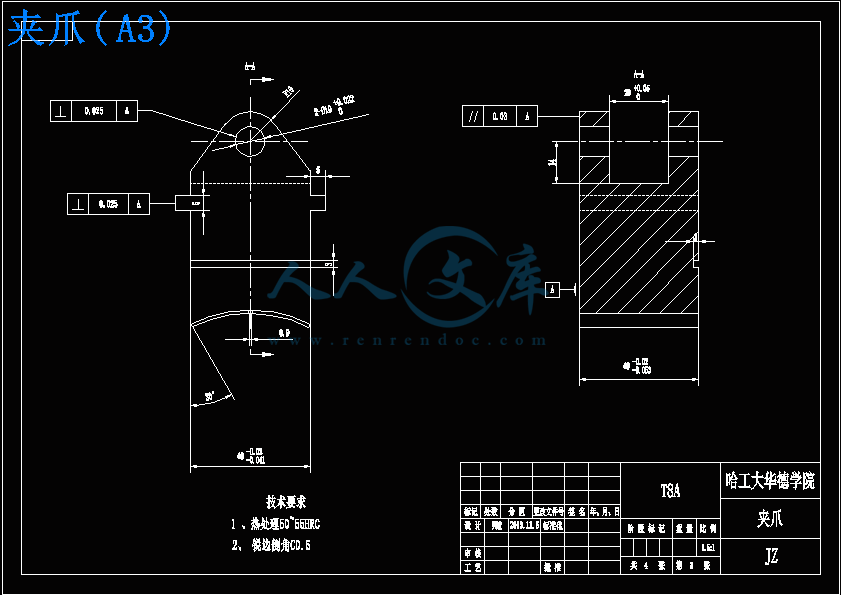
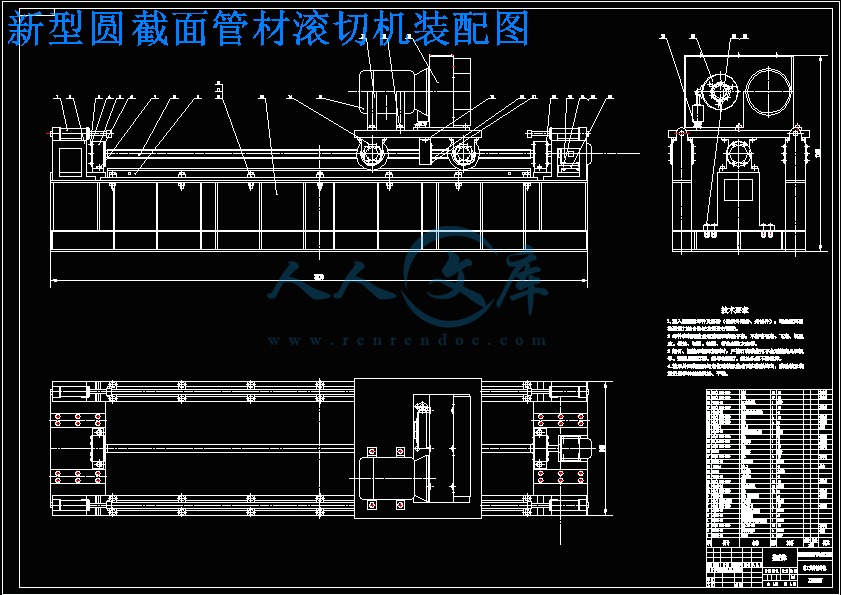
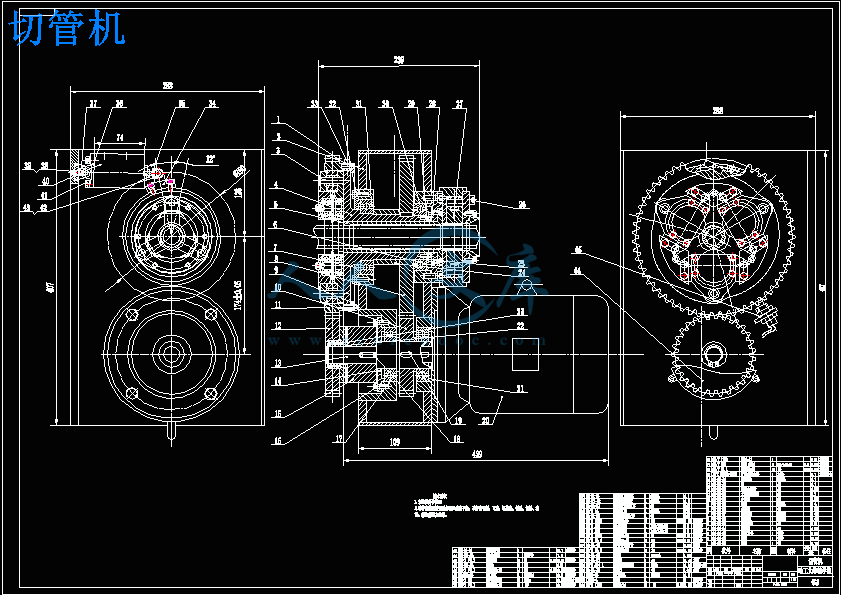

摘 要
随着切割机的发展,采用滚切机在线切断管材是近几年在国外发展起来的新技术。这种滚切机是利用三把带有楔角的圆盘形滚切刀片,采用滚动压入的方法将管材切断。由于采用了滚压无屑剪切,刀具的滚切行程略大于管材壁厚即可切断管材,因而效率高(尤其是对于大直径管材)。可以实现小噪音、无切屑、小(无)毛刺切管,并可保证管材切口绝对垂直于管材轴线。从而可简化生产工艺、减少设备的投资、降低生产成本,并可改善生产环境,解决了长期困扰钢管企业的噪音问题。
我设计是端面凸轮式钢管在线滚切机,滚切式切断的工作原理是利用三把带楔角的碟形滚切刀片均匀的安装在刀头架上,刀头架由驱动齿轮带动旋转,齿轮由齿条驱动,端面凸轮推动齿条从而使刀头架进给的同时实现径向进给,刀片与被切管材接触后,除绕管材公转外,还绕自身中心轴旋转,在管材表面实现纯滚动,在径向进给系统的作用下逐渐将管材切断。这种切断方式可实现切口断面轮廓不失真。滚切式即近年来发展的旋转楔入法。
关键词 管材 滚切机 端面凸轮
Abstract
Along with the development of cutting machine, cutting machine adopts the roll online in recent years in foreign countries cut off the tubes are developed new technology. This kind of cutting machine is rolling by 3 to a wedge disc shape roll, the rolling pressure blade cut into the methods will pipes cut off. Since it is a rolling a chip less shear, the cutting tool roll-cut trip is slightly higher than the pipe wall thickness can be cut off, and high efficiency pipes, especially for large diameter tubes). Can realize the little noise, no scraps, small (no) burr cut tube, and can ensure the pipe in vertical pipe axis incision absolute. Thus, can simplify production technology, reducing equipment investment, reduce the production cost, and can improve the production environment, solved the problem of noise steel enterprises.
My design is section CAM tubular steel rolling cutting machine, get online cut off the work of principle is to use the wedge with three of the disc roll-cut blade even installed in frame on, cutter head frame is driven gear, gear rotating driven by rack drive, promoting rack and CAM section head into the frame to realize radial feeding, the blade was cut pipe after contact with, in addition to the revolution around the pipe outside, still around their own center axis rotation in pipes, achieving pure rolling, surface in radial feeding system under the function of the pipes cut off gradually. This cut way can realize incision section contour not distortion. Roll-cut type is rotating wedge method in recent years.
Keywords pipe roll cutting machine section CAM
目 录
摘要I
AbstractII
第1章 绪论1
1.1课题背景1
1.2国内外研究现状3
1.2.1非剪切类的切断方法3
1.2.2剪切类切断方法4
第2章 方案确定5
2.1旧型滚切机在实际应用中存在的问题5
2.2设计原理6
第3章 滚切机本体设计10
3.1 参数选择及基本数据确定10
3.3 滚切力的计算12
3.3.1 滚切力的理论分析12
3.3.1.4 径向加工力的计算13
3.3.2 切向加工力的计算14
3.3.3 转盘轴及轴上部件14
3.4 刀夹座的设计15
3.5 齿轮参数选择及齿轮轴强度校核16
3.7 进给架、进给环设计20
3.8.1系杆架转动力矩21
3.9本章小结22
第4章 部件设计23
4.1 夹紧装置设计23
4.1.1夹紧装置液压缸的设计24
4.1.2夹紧凸轮的设计26
4.2 小车行走装置设计27
4.2.1 小车动力传动方式的选择27
4.2.2 小车主体的受力分析27
4.2.4 行走小车电动机的选取29
4.3 本章小结30
结论31
致谢32
参考文献33
第1章 绪 论
1.1 课题背景
管材在连续生产过程中,在线切断设备是整个生产线中的关键设备之一。我国目前有1700多条直缝焊管生产线,普遍采用飞据在线锯切管材。采用飞据在线锯切管材存在如下问题:一是切后管断面留有毛刺,为去除毛刺后续工序必须加平头设备;二是锯切过程噪音污染严重;三是锯切增加了金属消耗;四是当锯切大直径管材时,生产效率特别低。
管材在生产和使用过程中,为切除头尾不合格部分或将长管分切成定长等,切断工序是不可少的。由于管材断面形状呈空心状,在切断过程中,其切口的断面形状很易失真。因而管材切断技术的要求更高。除了通常要求的切口断面宏观平直、毛刺小,生产率高、噪音小、金属损耗少以外,还要求断面轮廓形状不失真或少失真。因而国内外一直在探讨各种因素对切口质量的影响规律,以寻求新的切断方法。 第2章 方案确定
2.1 旧型滚切机在实际应用中存在的问题
目前,飞锯机是钢管切断的主要设备主要功能是将在线生产的管材定尺切断。它不仅控制管材的定尺切断精度,同时制约着生产线的生产速度。飞锯的通常形式为电机带动锯片高速旋转将管子切断。由于其切削机理为高温熔融状态下的摩擦过程,这种形式结构简单,造价低,但噪音大,切口毛刺大,对于小型机组很方便使用;但对于直径在273mm以上的大规格圆管的切断就很难满足工艺要求。对于大规格焊管生产线上的飞锯机,国内传统的形式有三种:
(1)单锯片式
用一张锯片一次切断整根钢管。锯片直径很大,如锯切Φ508mm ×14mm圆管或400mm ×400mm×14的方矩形管,锯片直径需在1600mm以上,锯切功率需达250kw工作时噪音很大,且管子端口不好,毛刺大,又不好清除。
(2)滚切式
其结构是通过一组刀片的径向旋转、挤压钢管切断。虽然比大直径的锯片有一定的优越性,但仅使用于圆管,不能用于方矩形管和开口型材,并有收缩口现象,且在钢管级高、璧厚大时切断就非常困难了。
(3)双剧平推式
这是国外20世纪50年代淘汰产品,它不仅结构庞大,功率消耗大,致命缺陷是切断面不平、错位,切削过程中易变形,导致管子切口有阶梯,若是圆管还可在平头工序修正,若是方形管就很难处理了。
目前,用于切割圆形截面管材,或者圆管材生产线上截断管材时采用的滚切机,在不允许管材旋转时,其滚刀必须绕管材中心公转,同时滚刀沿管面滚动且向中心运动,达到切断管子的目的。
对于上述切割圆形截面管材的技术中,如中国某发明专利,其申请号200610012656.0中公开的《圆管材截面滚切机》,其中阐述的滚切机性能可靠,工作稳定,达到了很好的效果[6]。但是在实际应用中,由于设计的圆盘轴上的滚切装置与旋转环上的传动齿轮之间具有较大的轴向距离,并且旋转环和圆盘轴的旋转配合面在圆盘轴的轴径上,而非圆盘外圈上,导致旋转滚切机构在机架外的悬臂较长,受力状态也不好,这样,若有加工产生的质量偏心,会在滚切工作时产生径向振动,因而降低了圆盘刀的使用寿命;另外,因离合器为常离状态,在启动时,旋转环仅靠圆盘轴与其的摩擦力矩驱动,由于摩擦力矩很小,使旋转环启动滞后,造成滚切装置上的滚轮撞击内凸轮面而产生启动冲击;此外,在滚切结束时,该滚切机中的离合器的分离时刻不易控制;在退刀后,滚切装置相对内凸轮的停止位置不够准确,造成圆盘刀让开距离不足,而妨碍管子再次送入容易打刀,以及存在加紧装置的夹紧中心和滚切中心对中困难、设备的重量较大等实际问题。2.2 设计原理
经过对现有滚切机的结构分析,我总结出目前滚切机出现的主要问题。分别是:
1)滚切机构悬臂长问题;
2)起动时产生冲击的问题;
3)离合器的分离时刻不易控制;
4)退刀时滚切装置相对于内凸轮的停止位置不够准确;
5)夹紧装置的夹紧中心和滚切中心对中困难的问题。
在此基础上进行改进,完成了本次毕业设计。
参考中国某专利新型圆管材滚切机[5]原理图如图2-1所示。 为实现其目的,本设计提供的新型圆形截面管材滚切机,包括传动轴上分别设置的传动件与所对应在圆盘轴上和位于其上的旋转环上连接的传动件;所属圆盘轴的圆盘端面径向滑槽内安装有滚切装置;其中,它具有一个内圈是内凸轮,外圈是一个滚切大齿轮的旋转环安装于圆盘轴的圆盘外圈位置上;在所述旋转环、圆盘轴和机架上安装起动和退刀控制装置;和在所述机架管材入料端设置一个夹紧装置。因此,通过旋转环直接沿圆盘轴的圆盘外圈转动,进一步降低了轴向尺寸,并且使旋转配合面、大齿轮上的啮合点、内凸轮对滚切装置的施力点三者相距很近,受力状态得到明显改善,避免了振动发生;此外,还通过设置了起动及退刀控制装置,保证起动时,控制旋转环被驱动同步运转,避免了起动冲击,离合器切合时刻准确,有利于滚切装置滚切装置退刀后,停在处于相对内凸轮的最大退刀位置点上;另外,增设了夹紧装置,提高了夹紧管材的稳定性和对中可靠性。
连杆与铰接的所述活动刀架间的夹角是100°—180°随着夹角的变化来实现进刀。转盘上设置一个以上的连杆与相对应带有滚刀的刀架连接。本管材截面滚切机采用了转盘上通过铰接的连杆与刀架组成一连杆进退刀机构,并在旋转筒相配合的转盘上安装一摩擦减速装置,通过该装置的作用实现了转盘产生相对于旋转筒的方向转动,用以控制连杆进退刀机构进行切割或者非切割运动,因而该连杆与带有滚刀的刀架机构,和所设置的摩擦减速装置是实现本管材滚切机的关键。解决了现行的滚切机采用的凸轮机构控制滚刀,以及多齿轮组件传动所带来的整体机构复杂的问题。
本设计涉及在旋转环、圆盘轴和机架上组合安装起动及退刀控制装置,包括旋转环一径向端开有一个导通的槽孔和相邻的沉槽,则在旋转环上的槽孔内设置的棘轴上安装有棘爪,和在所述沉槽内设置一个弹簧片构成棘轮机构;所述棘爪与对应圆盘轴的圆盘外圈上呈设置用于交替配合或脱开的三个角形棘槽;所述棘爪的另一端与所对应在机架上设置的接近开关接近或远离。这样有利于起动同步平稳,退刀时刻准确,易于控制。
根据设计的特点,所提及滚切装置除上述采用滚刀作为切刀之外,可以在滚切装置上直接固定车刀,同样可以完成管材切割。
在本设计中,由机架的入料端安装一个管材夹紧装置。所述的管材夹紧装置包括固定在机架上的滑道盘,滑道盘一侧面上呈现120°设有三个径向滑道分别安装滑块;所述滑道盘和滑块之间安装返回弹簧,滑道盘和其上同心安装的盖板共同为滑块的滑动导向;该滑块的一段作为夹紧口,另一端通过销轴安装滚轮;该滚轮对应所述滑道盘和盖板的外圈上具有的夹紧凸轮;则夹紧凸轮内圈是由三段相同的收缩曲线首尾相连成的圆周内凸轮,外圈上固定安装有转壁,通过液压缸或气缸矫连接在机架上。因此,该滚轮相对于滑道盘和盖板外圈上具有的夹紧凸轮转动。当要夹紧时,液压缸伸长,推动转臂连带夹紧凸轮一起转动,其夹紧凸轮内凸轮面压迫夹紧滚轮迫使三个滑块,沿滑道盘上的径向滑道同时向管子压紧,自动对中夹紧管子。当要松开管子时,液压缸缩回,拉动转臂使夹紧凸轮回转,返回弹簧推动滑块回退。在本设计中,夹紧凸轮的转动也直接采用电液推杆推动,这样可以在制管生产线上往复运动的滚切机上仅供电即可保证滚切进行。
第3章 滚切机本体设计
3.1 参数选择及基本数据确定
钢管切断规格为外径 Φ76-Φ89mm,壁厚为4mm,钢管生产速度为30m/min,钢管定尺长度为12m。
由以上钢管剪切参数可知
1.在钢管剪切的每一个行程的时间t为
t=钢管定尺长度/钢管生产速度=12m/30m/min=24s
即在钢管剪切的每个行程时间为24s。
即小车运行一个切断来回时间为24s。
2.刀片行程的确定
钢管切割的最大壁厚为4mm,刀片在切割前和切断后应有一个多余的进刀距离,据参考有关图纸和结合实际,定为4mm。
参考文献
1 刘庆国.圆形截面管材滚切机,2006.7
2 刘庆国,于恩林.圆形截面管材滚切机,2004.06
3 于恩林,刘庆国.管材滚压剪切过程的数值模拟及实验研,2004
4 刘庆国.新型圆形截面管材滚切机,2008.12
5 刘庆国. 《新型圆管材滚切机》.专利号ZL 200810080216
6 刘庆国.《圆管材截面滚切机》.专利号ZL 200610012656.0
7 刘庆国.《圆管材滚切机》.专利号ZL 200620023694.1
8 刘庆国.《一种圆管材滚切机》.专利号ZL 200620024271.1
9 刘宝珩.轧钢机械设备,2004.3
10 成大先.机械设计手册1-3卷.第五版.北京:化学工业出版社,2007
11 成大先.机械设计手册(第二卷)[S].北京:化学工业出版社,2002.1
12 成大先.机械设计手册(第四版)[S].北京:化学工业出版社,2002
13 成大先.机械设计图册1-2卷.北京:化学工业出版社,2000
14 安子军.机械原理.国防工业出版社,2009
15 王三民,诸文俊.机械原理与设计[M].北京:机械工业出版社,2001.3
16 李洪.实用机床设计手册[S].辽宁:辽宁科学技术出版社,2001.6