蜂蜜离心机设计【10张CAD图纸+WORD毕业论文】【农业机械资料】
收藏
资源目录
压缩包内文档预览:(预览前20页/共22页)
编号:402067
类型:共享资源
大小:10.93MB
格式:RAR
上传时间:2015-01-28
上传人:好资料QQ****51605
认证信息
个人认证
孙**(实名认证)
江苏
IP属地:江苏
45
积分
- 关 键 词:
-
蜂蜜
离心机
设计
全套
cad
图纸
word
毕业论文
农业机械
资料
- 资源描述:
-
【温馨提示】 购买原稿文件请充值后自助下载。
[全部文件] 那张截图中的文件为本资料所有内容,下载后即可获得。
预览截图请勿抄袭,原稿文件完整清晰,无水印,可编辑。
有疑问可以咨询QQ:414951605或1304139763
目录
绪论 2
1. 选题目的 2
2. 国内离心分离研究发展 2
3. 主要差距 3
4. 国外离心分离技术的发展 3
5. 发展趋势 4
第一章 离心机的概述 6
1.1 离心机 6
1.2 离心机原理 7
1.3 离心机的分类 7
1.3.1、按分离因素Fr值分 7
1.3.2、按操作方式分 8
1.3.3、按卸渣方式分 8
1.3.4、按工艺用途 9
1.3.5、按安装的方式分 9
1.3.6、按国家标准与市场使用份额分 9
第二章 蜂蜜离心机设计步骤 10
2.1 主要参数 10
2.2 蜂蜜离心机总体方案: 10
2.2.1 设已知条件 10
2.2.2 确定各轴转速 11
2.2.3 功率计算 11
2.2.4 计算各轴的输入转矩 11
2.3 输出部分设计 13
第三章 离心机各部件设计 14
3.1 驱动部分机构设计: 14
3.2 机架部分结构设计: 14
3.3 轴支撑座结构设计: 15
3.4 旋转支架的设计: 15
3.5 脚座部分结构设计: 16
3 .6 传动部分结构设计: 16
第四章 全文总结 19
参考文献 20
致谢 21
绪论
1. 选题目的
养蜂即蜜蜂养殖是人工饲养蜂蜜而取其产品包括蜂蜜、蜂王浆、蜂胶、花粉、蜂蜡等产品的事业,包括在广义的畜产内,所以广义地说蜜蜂也是家畜。蜂蜜养殖的历史有数千年之久,蜂蜜的利用是从渔猎时代开始的。然而蜂蜜是昆虫蜂蜜从开花植物的花中采得的花蜜在蜂巢中酿制的蜜。蜂蜜从植物的花中采取含水量约为80%的花蜜或分泌物,存入自己第二个胃中,在体内转化酶的作用下经过30分钟的发酵,回到蜂巢中吐出,蜂巢内温度经常保持在35℃左右,经过一段时间,水份蒸发,成为水分含量少于20%的蜂蜜,存贮到巢洞中,用蜂蜡密封。这个时候人类便拨开蜂蜡,收获蜜蜂的劳动果实蜂蜜,可是怎样收取小小蜂蜜留下的点点产物呢,人工取用的话,很麻烦,提取的不彻底,而且弄脏手啊,衣服什么的,效率也极低,于是我们便需要发明一种取蜜机器——蜂蜜离心机,这样可以更有效率的并彻底地将蜂蜜利用离心力甩出来。
2. 国内离心分离研究发展
我国离心机行业尚属正在发展中,总体水平不高。随着社会进步,人们对环保.能源以及装备对品质的影响有了新的认识。同时国外技术交流和合作以及成套项目的引进、消化与吸收,促进了我国离心分离技术的迅速发展。
1)已基本形成了一种科研、设计和制造的体。
2)成立了分离领域的学术组织。
3)在基础理论与应用方面进行了研究。
4)目前已能生产三足、上悬、活塞、螺旋、离心力卸料、震动、进动卸料、刮刀及虹刮刀、翻袋及旁滤等离心机;分离机则有蝶式、室式及管式。上述产品不仅遍及全国且远销国外,且技术特性有所提高。
5)为满足特殊工艺要求(防污染、密闭、防爆灯),一些新的离心机亦先后问世。内旋转子过滤离心机的研制,立式密闭螺旋机及复试机等已投产。
6)自控技术与CAD技术的应用。
7)各种相关标准的制定。
8)同国外著名离心机厂商的技术合作。
3. 主要差距
尽管我国的离心分离设备有了很大的进展,但从整体而言,与世界先进国家相比,差距甚大,主要表现在:
1)规模、品种少,系列化程度差。特别缺少集几种结构形式,集几种推动力于一体的复合式离心机。
2)技术参数低。国外离心分离机械产品的参数普遍高于我国,并继续向高参数、大容量方向发展,以卧螺离心机为例,最近研制的机型为国内最大的,其转鼓直径亦仅720mm,长径比最大为L/d-4,分离因数亦较低,而国外转鼓最大直径已达2.1m,长径比L/d-6,处理能力大雨200m3/h,可用于二相或三相分离,还发展了双向挤压型、沉降、过滤复合机型。目前,较先进的机型都采用计算机控制,会随着物料特性和参数的变化自动调节其相应的工况。
3)产品进展缓慢。而国外,由于采用模块化的组合结构,特别是采用了大规模定制设计的心手段,故能满足用户的个性化需求,并加快了产品的更新换代速度,甚至还储备所谓“冷冻产品”,以随时适应市场竞争的需求
4)其他方面。在产品的可靠性、稳定性、自控技术、加工工艺、新材料的使用、配套产品的品质,以及理论研究等方面,均存在不少的差距。
4. 国外离心分离技术的发展
受新技术推动及相关产业发展的影响,国外离心分离技术的进展主要体现在以下几个方面:
1)加强理论研究,选择最佳设计方案
2)瑞典Alfa-laval公司,在碟片流道研究中发现,碟片间隙横断面上的速度分布取决于一个无量纲数“λ”,而工业离心机的“λ”通常在5~28之间。随着“λ”值的增加,碟片的转速增加,薄层减少,可提高雷诺数并缓和涡流。通过对碟片间隔件和分布孔的巧妙设计,进料量可增加20%。此外,还对相分离技术进行了研究。
近年来,研究人员为选择最佳方案,采用流场分离法、有限元模拟法、大梯度密度梯级法、反模态分析法等,对离心机的工作性能和关键零件进行研究,为设计优良性能的离心机提供了理论依据。并对待内洗涤的卧螺离心机中堰池深度以及卧螺离心机技术参数之间的关系等进行了最佳化研究。
2)技术参数的提高和新机型的问世
为提高产品的纯度,及满足能源和环保的要求,高参数已成为国外的发展特点。由于生物工程需要分离极细的颗粒,如细菌、霉及胰岛素等,故最新蝶式机已可处理0.1um微粒,且分离因数可达5000.如德国Westfalia公司的CSA160机型和瑞典Alfa-laval公司的BTAX510机型均属此例,随着工艺要求的提高,新机型不断问世。美国Dorr-Oliver公司的BH-46型蝶式机,转鼓内径已达1.2m,转鼓重量为4.5t,用2个功率为220kW的电机驱动,最大生产能力为450m3/h,当量沉降面积已达250,000m2,为蝶式机之最。
瑞典Alfa-laval公司用于生物技术的BTUX510型蝶式机,具有自动调节的涡流喷嘴。利用喷嘴进料黏度和浓度的关系,可提供供恒定的固相浓度,与进料速度和固体含量的变化无关。
而具有1000分离因数的卧螺离心机,可从某种长度上弥补管式分离机的不足。
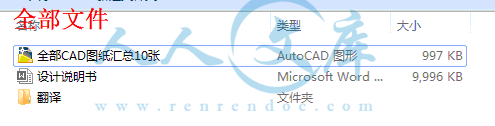
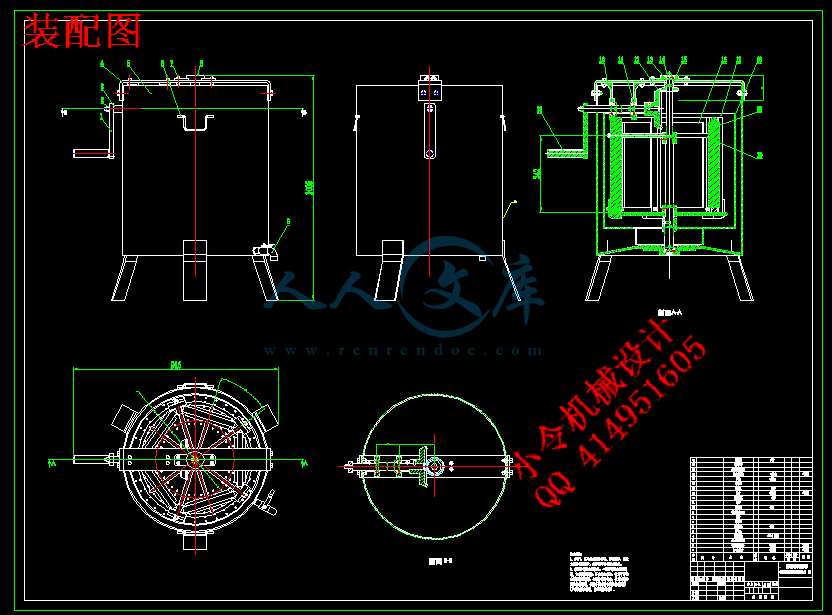

BTNX3560-A机型的特点是先进的旋转动态设计:主轴承改为弹性安装,可延长寿命,降低机器噪音和震动。德国Krauss-Maffei公司最新研制
- 内容简介:
-
1 Optimized Kinematics of Mechanical Presses with Noncircular Gears E. Dodge ( l ) , M. Hinderance Received on January 8, 1997 Abstract:The quality of parts manufactured using metal forming operations depends to a large degree on the kinematics of the press ram. Non-circular Geary to obtain those stroke-time behaviorisms we aim at as an optimum for the various metal forming ope with a rotational-angle-dependent speed ratio in the press drive mechanism offer a new WA rations in terms of manufacturing. The paper explains the principle using a prototype press which was built by the Institute for Metal Forming and Metal Forming Machine Tools at Hanover University. It will present the kinematics as well as the forces and torques that occur in the prototype. Furthermore, the paper demonstrates using one example of deep drawing and one of forging that the press drive mechanism with non-circular gears may be used advantageously for virtually all metal forming operations. Keywords: Press, Gear, Kinematics 1 introductive Increasing demands on quality in all areas of manufacturing engineering, in sheet metal forming as well as in forging, go hand in hand with the necessity to make production economical. Increasing market orientation requires that both technological and economic requirements be met. The improvement of quality, productivity and output by means of innovative solutions is one of the keys to maintaining and extending ones market position.In the production of parts by metal forming, we need to distinguish between the period required for the actual forming process and the times needed to handle the part. With some forming processes we have to add time for necessary additional work such as cooling or lubrication of the dies. This yields two methods of optimization, according to the two aspects of quality and output. In order to satisfy both aspects, the task is to design the kinematics taking into account the requirements of the process during forming; also to be considered is the time required for changing the part as well as for auxiliary operations in line with the priority of a short cycle time. 2 Pressing Machine Requirements One manufacturing cycle, which corresponds to one stroke of the press goes through three stages: loading,forming and removing the part. Instead of the loading and removal stages we often find feeding the sheet, especially in sheer cutting. For this, the press ram must have a minimum 2 height for a certain time. During the forming period the ram should have a particular velocity curve,which will be gone into below. The transitions between the periods should take place as quickly as possible to ensure short cycle time. The requirement of a short cycle time is for business reasons, to ensure low parts costs via high output. For this reason stroke numbers of about 24/min for the deep drawing of large automotive body sheets and 1200/min for automatic punching machines are standard practice.Increasing the number of strokes in order to reduce cycle times without design changes to the pressing machine results in increasing strain rates, however. This has a clear effect on the forming process, which makes it necessary to consider the parameters which determine the process and are effected by it. In deep drawing operations, the velocity of impact when striking the sheet should be as low as possible to avoid the impact. On the one hand, velocity during forming must be sufficient for lubrication. On the other hand, we have to consider the rise in the yield stress corresponding to an increase in the strain rate which creates greater forces and which may cause fractures at the transition from the punch radius to the side wall of the part. In forging, short pressure dwell time is desirable. As the pressure dwell time drops the die surface temperature goes down and as a result the thermal wear This is counteracted by the enhanced mechanical wear due to the greater forming force, but the increase due to the strain rate is compensated by lower yield stress because of the lower cooling of the part. The optimal short pressure dwell can nowadays be determined quantitatively using the finite element method 3. In addition to cost avoidance due to reduction in wear, short pressure dwell time is also an important technological requirement for the precision forging of near net shape parts, which has a promising future. The requirements of high part quality and high output will only be met by a machine technology which takes into account the demands of the metal forming process in equal measure to the goal of decreasing work production costs. Previous press designs have not simultaneously met these technological and economical requirements to a sufficient extent, or they are very costly to design and manufacture, such as presses with link drives 6. This makes it necessary to look for innovative solutions for the design of the press. Its design should be largely standardized and modularized in order to reduce costs 6. 3 Fig 1. Prototype press 3 Press Drive with Noncircular Gears 3.1 Principle The use of non-circular gears in the drive of mechanical crank presses offers a new way of meeting the technological and economic demands on the kinematics of the press ram. A pair of non-circular gears with a constant center distance is thus powered by the electric motor, or by the fly wheel, and drives the crank mechanism itself.The uniform drive speed is transmitted cyclically and non-uniformly to the eccentric shaft by the pair of noncircular gears. If the non-circular gear wheels are suitably designed, the non-uniform drive of the driven gear leads to the desired stroke-time behaviour of the ram. Investigations at the Institute for Metal Forming and Metal Forming Machine Tools (IFUM) of Hanover University have shown that in this simple manner all the relevant uninterrupted motions of the ram can be achieved for various forming processes 2. Apart from, the advantages of the new drive, which result from the kinematics and the shortened cycle time, the drive concept is distinguished by the following favorable Propertius. Because it is a mechanical press, high reliability and low maintenance may be expected. In companion to linkage presses the number of parts and bearings is clearly reduced. Above all, a basic press type can be varied without further design changes by installing different pairs of gears, designed according to the demands of the customer. Unlike link drives, bearing locations and installations do not change within one load class as a result of different kinematics. Thus the above mentioned requirement of popularization and standardization is taken into account Reductions in time and costs are possible for the design and press manufacture. 4 3.2 Prototype At the Institute for Metal Forming and Metal Forming Machine Tools (IFUM) a C-frame press has been remodeled and a pair of non-circular gears was installed. The previous back gears were replaced by a planetary gear set for this purpose. The work carried out shows that remodeling of existing presses for the new drive is possible. The state of the press at the end of the modelli is shown in figure 1. The press is designed for a nominal ram force of 1,000 N and 200 N of the die cushion. The center distance of the non-circular gears is 600 mm. The pair of non-circular gears has an average transmission ratio of 1.Each gear wheel has 59 gear teeth, straight-toothed,module 10 mm (fiacre 2). The face width is 150 mm. The gears have involute gear teeth. We assume a non-circular base curve for the design of the flank geometry. As a result the tooth geometry of a non-circular gear varies along the circumference. In spite of this, it can be derived from the well-known trapezium rack, however 4, 51. An algorithm for the computation, which takes the addendum and addendum into account exactly, has been developed. Fig. 2 View of the gears from the rear The press is designed for deep drawing of flat parts in single stroke operation mode. The maximum ram stroke is 180 mm, the number of strokes 32/min. At a stroke of 140 mm the ram velocity almost remains constant 71 mammals from 60 mm before lower dead center until lower dead center, see figure 3. Thus the velocity corresponds to the working velocity of hydraulic 5 presses. The velocity of incidence of a crank mechanism with the same number of strokes would be 220 mammals, in comparison. In order to keep the same average velocity with a crank press, the number of strokes would have to be halved. The short cycle time of the jodelled machine results from the fast upward motion. Because the press is run in single stroke operation mode, no particular requirements were made concerning handling time during design. The drive mechanism of the prototype with non-circular gears has in addition a favorable effect on the ram forces and the driving torques (failure 4). For a crank press the nominal force is normally available at 30 rotation of the crank shaft before the lower dead center. This corresponds to a section under nominal force of only 7 5% relative to the stroke. To reach the nominal force of 1,000 N, the drive has to supply a torque of 45 kam at the crank shaft. The prototype only requires 30 kam on account of the additional transmission of the non-circular gears. They are transmitted to a cyclic. non-uniform crank shaft torque, resulting in a nominal force range from 60 to the lower dead center. This corresponds to 27.5% of the stroke. We always find similar conditions if the pair of non-circular gears is stepped down in the operating range of the press. This will almost always be the case with sheet metal forming and stamping. It is thus possible to design some machine parts in a weaker form and to save costs this way. 4 Further Design Examples Using the examples of two stroke-time behaviorisms the design is illustrated in the following. A range of parts is assumed which are to be manufactured by the press. For this purpose the ram velocity requirements and the forming section of the assumed stroke need to be quantified.Furthermore, the time needed for the handling of the part needs to be determined, and also the minimum height which the ram has to assume during the handling. From this, we design the sequence of movements, and we describe it mathematically. At the IFUM, a software program developed by the institute is used. From this mathematical description of the stroke-time behaviour we can calculate the speed ratio of the non-circular gears needed.From this we obtain the outcurves of the gears l, 2, 7. In a first example the ram velocity in deep drawing is supposed to be constant during the sheet metal forming at least over 100 mm before the lower dead center and it is supposed to be about 400mm/s. Let the number of strokes be fixed at 30/min. Above 450mm section of stroke, let the time for the handling of the part be the same as for a comparable crank press with 25 strokes per minute. figure 5 shows the stroke-time behaviour , which is attained by the sketched pair of gears. The gear wheels are represented by their outcurves. The conventional cosine curve at 25/min is given for comparison. In addition to the reduction of cycle time by 20%, the ram 6 velocity of impact onto the sheet is also considerably reduced.110 mm before the lower dead center, the velocity of impact is 700 mammals when using the crank mechanism and only 410 mm/s when operated with non-circular gears. A second example shows a drive mechanism as is used for forging. In figure 6, stroke-time behaviour of a conventional forging crank press is compared with the kinematics of the press with non-circular gears illustrated in the picture.The cycle time of the crank press is 0.7 s, the number of strokes is 85/min and the nominal force is 20 MN.Its pressure dwell time is 86 ms with a forming section of 50 mm. The pressure dwell of the press depicted with non-circular gears decreases by 67% to 28 ms. It thus reaches the magnitude familiar from hammers. By increasing the number of strokes by a factor of 1.5, the cycle time decreases by 33% to 46 ms. In spite of this,the handling time remains the same compared to conventional crank press on account of the kinematics of the non-circular gears. In order to achieve these kinematics in this case, a conventional circular gear may be used as driving gear, arranged eccentrically. This reduces the costs for gear manufacture.These examples show that different kinematics can be achieved by using non-circular gears in press drives At the same time the potential of this drive with respect to the realization of the desired kinematics becomes clear as does the reduction of cycle times in production. By varying the examples it is also possible to increase the velocity after impact in deep drawing operations if :his sequence of motions is advantageous for the range of pans to be produced on the press, for reasons of lubrication, for example. 5 Conclusions The requirements of high productivity, reduced costs and the guarantee of high product quality to which all manufacturing companies are exposed, applies particularly to companies in the field of metal working. This situation leads us to reconsider the press drive mechanism in use up to now. The new drive for crank presses with non-circular gears described here allows us to optimize the kinematics of simple mechanical presses. This means that the cycle time is shortened to achieve high productivity and the kinematics follows the requirements of
- 温馨提示:
1: 本站所有资源如无特殊说明,都需要本地电脑安装OFFICE2007和PDF阅读器。图纸软件为CAD,CAXA,PROE,UG,SolidWorks等.压缩文件请下载最新的WinRAR软件解压。
2: 本站的文档不包含任何第三方提供的附件图纸等,如果需要附件,请联系上传者。文件的所有权益归上传用户所有。
3.本站RAR压缩包中若带图纸,网页内容里面会有图纸预览,若没有图纸预览就没有图纸。
4. 未经权益所有人同意不得将文件中的内容挪作商业或盈利用途。
5. 人人文库网仅提供信息存储空间,仅对用户上传内容的表现方式做保护处理,对用户上传分享的文档内容本身不做任何修改或编辑,并不能对任何下载内容负责。
6. 下载文件中如有侵权或不适当内容,请与我们联系,我们立即纠正。
7. 本站不保证下载资源的准确性、安全性和完整性, 同时也不承担用户因使用这些下载资源对自己和他人造成任何形式的伤害或损失。

人人文库网所有资源均是用户自行上传分享,仅供网友学习交流,未经上传用户书面授权,请勿作他用。