【温馨提示】 购买原稿文件请充值后自助下载。
[全部文件] 那张截图中的文件为本资料所有内容,下载后即可获得。
预览截图请勿抄袭,原稿文件完整清晰,无水印,可编辑。
有疑问可以咨询QQ:414951605或1304139763
摘 要
本文以4110柴油机的相关参数作为参考,对四缸柴油机的连杆进行了结构设计和尺寸计算,并对连杆进行了运动学和动力学的理论分析,最后运用Pro/E进行三维建模运用ANSYS进行了有限元分析。
首先,以运动学和动力学的理论知识为依据,对连杆的运动规律以及在运动中的受力等问题进行详尽的分析,并得到了精确的分析结果,同时对连杆用材料进行了比较与分析。其次分别对连杆大头、连杆杆身以及连杆小头进行结构设计及尺寸计算,并进行了结构强度和刚度的校核。再次,应用CAD软件:Pro/E软件建立了连杆的三维几何模型,在此工作的基础上,又对静力作用下对连杆的两种特殊工况;拉伸、压缩工况下进行了受力计算,再将连杆三维几何模型导入ANSYS中对其进行了定义特性、网格划分、施加约束和载荷,最后进行计算以达到对连杆进行强度校核的目的。
关键词:柴油机;连杆;强度校核;Pro/E;ANSYS
ABSTRACT
Taking 4110 as the reference parameters of the diesel engine, four-cylinder diesel e-
ngine connecting rod on the design and size were calculated, and linkage to the theory of kinematics and dynamics analysis, and finally the use of Pro / E for the use of three-dim-
ensional modeling ANSYS finite element analysis carried out.
First, the theoretical knowledge of kinematics and dynamics based on the movement
of connecting rod and the force in motion a detailed analysis of such issues and get accurate results, while the materials were used on the rod comparison and analysis. Followed by on the connecting rod, connecting rod shaft and the connecting rod small end and size of stru-
ctural design calculations, and were checking the structural strength and stiffness. Again, application CAD software: Pro / E software to establish a link of three-dimensional geome-
tric model, based on the work in this, but also on the static on the link under the two special conditions; tension, compression conditions were the force calculation, and then link into ANSYS three-dimensional geometric model is defined in its properties, meshing, impose constraints and loads, and finally calculated to achieve the purpose of checking the strength rod
Key words: Diesel engine;Connecting rod;Strength check;Pro/E;ANSYS
目 录
摘要 Ⅰ
Abstract Ⅱ
第1章 绪 论 1
1.1 选题的目的和意义 1
1.2 国内外的研究现状 2
1.3设计研究的主要内容 4
第2章 连杆的结构设计与分析 5
2.1 连杆的运动和受力分析 5
2.2 连杆的结构分析 5
2.3 连杆的工作条件和设计要点 6
2.4 连杆的材料性能及特点 6
2.5 连杆基本参数的确定 7
2.6 连杆小头的结构设计 8
2.6.1 小头结构型式 8
2.6.2连杆衬套 8
2.6.3小头结构尺寸 9
2.7连杆杆身的结构设计 9
2.7.1杆身结构型式 9
2.7.2杆身结构尺寸 9
2.8 连杆大头的结构设计 10
2.8.1 大头结构型式 10
2.8.2大头结构尺寸 10
2.9 连杆螺栓的设计 10
2.10 本章小结 11
第3章 连杆的强度、刚度计算 12
3.1连杆小头的强度校核 12
3.2连杆小头的刚度计算 14
3.3连杆杆身的强度校核 14
3.4连杆大头的强度校核 17
3.5连杆螺栓的工作负荷与预紧力 18
3.6连杆螺栓的屈服强度校核和疲劳计算 19
3.7本章小结 19
第4章 连杆三维模型的建立及有限元分析 20
4.1 建立连杆大小头及杆身 20
4.1.1建立新文件 20
4.1.2建立连杆体主体 20
4.1.3建立连杆大头和小头 21
4.1.4建立小头油孔 21
4.1.5建立连杆凹槽 22
4.1.6 建立连杆大头部位凸台 22
4.1.7建立螺栓孔 23
4.2建立连杆端盖 23
4.3建立连杆螺栓 24
5.4建立轴瓦及衬套 24
4.5连杆工况选择与载荷计算 25
4.5.1 计算工况的选择 25
4.5.2 连杆载荷的计算 25
4.6连杆几何模型的建立 27
4.7约束条件 29
4.8 连杆应力分析 29
4.8.1连杆拉伸工况下的应力分析 29
4.8.2连杆压缩工况下的应力分析 34
4.9连杆安全系数计算 39
4.10 本章小结 40
结 论 41
参考文献 42
致 谢 43
附 录 44
第1章 绪 论
1.1 选题的目的和意义
内燃机自十九世纪后期出现以来,经过一百多年的不断研究和改进,已经发展到比较完善的程度,它以热效率高、功率和转速范围宽广、比重量较小的优点,在动力机械中占有极其重要的地位,广泛应用于国民经济和军事装备的各个领域[1]。
连杆是内燃机中的重要的传动零件之一,其作用是连接活塞与曲轴,将作用在活塞上的力传给曲轴,使活塞的往复运动转变为曲轴的旋转运动,对外输出做功。连杆小端工作时作往复运动,大端作旋转运动,杆身作复杂的平面运动,因此连杆的受力情况十分复杂。连杆是内燃机中承受负荷最严重的零件之一,工作时同时承受着活塞传来的气体压力、往复惯性力和它本身摆动时所产生的惯性力的作用,这些力的大小和方向周期性变化。在长期使用中,连杆会因活塞的剧烈推力和曲轴的高速运转等因素,出现弯曲和扭曲现象。连杆一旦出现弯曲和扭曲,除了会使活塞拉缸外,还会致使活塞、气缸、曲轴等机件出现不正常磨损,并很容易引起疲劳破坏而断裂,导致发动机故障,直接关系到使用人的安全,造成极严重的后果。
以往,连杆的的制造以铸造法和锻造法为主;20世纪80年代以来,由于采用粉末锻造法大批量生产的粉锻连杆具有力学性能优、尺寸精度高、质量较轻及质量偏差很小等特点,因而相继在发达国家快速发展,逐渐取代铸造和锻造连杆。而高密度烧结法制造连杆也快速发展,并具有良好的力学性能。
现今随着计算机技术的迅速发展,特别是各种分析软件的日益成熟,在发动机研制开发过程中,对其零部件进行计算机数值模拟已成为辅助设计的重要手段。目前,有限元法已日趋成熟实用,所应用的领域也越来越广并发挥着越来越重要的

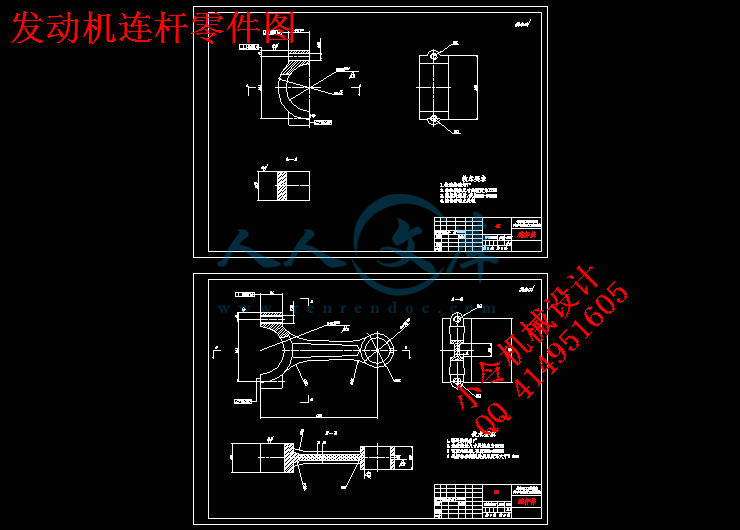


作用。有限元方法是近似求