【温馨提示】 购买原稿文件请充值后自助下载。
[全部文件] 那张截图中的文件为本资料所有内容,下载后即可获得。
预览截图请勿抄袭,原稿文件完整清晰,无水印,可编辑。
有疑问可以咨询QQ:414951605或1304139763
保险座塑料注塑模具设计
摘要
模具是工业生产中使用极为广泛的主要工艺装备,它是当代工业生产的重要手段和工艺发展方向,许多现代工业的发展和技术水平的提高,在很大程度上取决于模具工业的发展水平。本论文主要介绍了保险座的塑料注塑模具的设计。
设计中首先通过分析塑件的形状及工艺特性,选择了合适的模具设计方案;其次是对注塑机的选择,包括注射机的初选和注射机有关参数的校核,并确定了注射机;再次完成模具的结构设计,包括分型面的选择和确定、型腔数目的确定及型腔的排列、浇注系统的设计、成型零件结构设计、抽芯机构设计、推出机构的选择、冷却系统的设计、标准模架的选择。最后对成型零件尺寸进行计算,确定工艺参数。
采用此模具能够保证塑件尺寸外形以及表面要求,而且成本低、结构简单、开模容易、效率高,具有较强的实用性。
关键词:塑料注塑模具;注塑机;结构设计
The design of plastic injection mould for the Safety box
Abstract
Mold is widely used in industrial production the main technological equipment, It is an important means of modern industrial production and process development direction ,Many modern industrial development and the improvement of the technical levels ,Largely depends on the development of die and mould industry level. This paper mainly introduced the plastic injection mold insurance seat of design.
First through analysis in the design of plastic parts, process characteristics and shape ,choose the proper mould design ,Second is the choice of injection, mcluding injection machine of primaries and injection machine related parameter respectively ,To determine the injection machine;Complete the die structure design again ,Enclose the choice and determination parting ,Cavity number of determining and cavity arrangement ,The design of gating system ,Molding parts structure design ,Core-pulling mechanism design, selection of launch institutions, cooling system design, standard formwork choice ,Finally calculated for molding parts size, determine the process parameters.
Using this mold can guarantee plastics dimension appearance and surface requirements , And low cost, simple structure and easy to open mold, high efficiency, with strong practicability.
KeyWords: Plastic injection mold; injection machine; Structure design
主要符号表
K 安全系数 E 材料弹性模量
Smax 塑料的最大收缩率 P1 脱模阻力
Smin 塑料的最小收缩率 C 型芯成型部分断面的平均
P0 单位面积的包紧力 h 型芯被塑料包紧部分的长度
Δs 塑件公差 P0 单位面积的包紧力
D腔 型腔內形尺寸 Φ 安全系数
Qcp 塑料平均收缩率 S 顶顶出行程
ds 塑件外径基本尺寸 1 富裕量
Ds 塑件內形基本尺寸 2 顶出行程富裕量
h腔 凸模/型芯高度尺寸 α 倾斜角
Hs 塑件內形深度基本尺寸 Q 抽拔阻力
P1 动模受的总压力 P 斜导柱所受的弯曲力
F 塑件的投影面积 ε 塑件收缩率
P 型腔压力 f 摩擦系数
K 修正系数 μ 塑料泊桑比
B 动模垫板的宽度 L 支撑块的跨距
目录
1 绪论 1
1.1 前言 1
1.2模具发展现状及发展方向 1
1.2.1塑料模具工业的发展现状 1
1.2.2我国塑料模具发展走势 3
1.3本课题的设计内容 5
2 模具方案的论证和选择 6
2.1分型面的选择 6
2.2分型面选择原则 6
2.2.1分型面的分类 6
2.2.2分型面的选择原则 7
2.2.3分型面的确定 7
3 注射机的选择 8
3.1零件的材料及其注射工艺性 8
3.1.1 ABS的工艺条件 8
3.2型腔数目的确定及分布 8
3.3注塑机的选择 9
3.4注射机参数校核 9
3.4.1最大注射量校核 9
3.4.2最大注射压力的校核 9
3.4.3锁模力的校核 9
3.4.4开模行程校核 10
4 浇注系统的设计 11
4.1浇注系统的作用 11
4.2浇注系统的组成 11
4.2.1主流道部分设计 11
4.2.2冷料穴设计 12
4.2.3分流道设计 12
4.2.4浇口设计 13
5 成型零件工作尺寸的计算 14
5.1 影响塑件尺寸精度的因素 14
5.2模具成型零件的工作尺寸计算 14
5.2.1成形收缩率 15
5.2.2模具成形零件的制造误差 15
5.2.3零件的磨损 15
5.2.4模具的配合间隙的误差 15
5.3型腔和型芯尺寸计算 15
5.3.1型腔径向尺寸计算 15
5.3.2型腔的深度尺寸 16
5.3.3型芯的径向尺寸 16
5.3.4型芯的高度尺寸 16
5.3.5中心距尺寸计算 16
5.4动模板的强度校核 16
6 导向机构设计 19
6.1 导向机构的作用和设计原则 19
6.1.1导向机构的作用 19
6.1.2导向机构的设计原则: 19
6.2导柱、导套的设计 19
6.2.1导柱的设计 20
6.2.2导套的设计 20
7 脱模机构的设计 21
7.1 基本考虑和要求 21
7.2 推出机构的确定 21
7.3 推件板脱模机构设计的特点和基本原则 21
7.4 顶杆横截面直径校核 22
7.4.1脱模力的计算 22
7.4.2推杆直径的校核 22
8 侧向分型与抽芯机构的设计 24
8.1 基本考虑和要求 24
8.1.1侧向分型与抽芯机构应具备的基本功能 24
8.2 抽芯机构的概述 24
8.3斜导柱抽芯机构设计原则与确定 24
8.4 斜导柱抽芯机构的有关参数计算 25
8.4.1抽芯距S 25
8.4.2斜导柱倾斜角的确定 25
8.4.3斜导柱直径的确定 26
8.4.4斜导柱长度的计算 27
8.5 滑块的设计 27
8.6 导滑槽的设计 28
8.7 滑块定位装置 28
8.7.1滑块的作用和结构形式 28
9 模具的材料 29
9.1 塑料模具用钢的必要条件 29
9.2 选择钢材的条件 29
9.3 本模具材料的选择 29
9.4 模具的淬火硬度 30
9.5 模具的表面粗糙度 30
9.6 热处理的选择 30
10 模具的可行性析 31
10.1其它结构零部件设计 31
10.2 本模具的特点 31
10.3 市场前景与经济效益分析 31
11 总结 32
参考文献 33
致谢 34
毕业设计(论文)知识产权声明 35
毕业设计(论文)独创性声明 36
1绪论
1.1 前言
模具生产技术水平的高低,已成为衡量一个国家产品制造水平高低的重要标志,因为模具在很大程度上决定着产品的质量、效益和新产品的开发能力。现代模具工业有“不衰亡工业”之称。模具是工业生产的基础工艺装备,也是发展和实现少无切削技术不可缺少的工具。如汽车、拖拉机、电器、电机、仪器仪表、电子等行业有60%—80%的零件需用模具加工,轻工业制品的生产中应用模具更多。螺钉、螺母、垫圈等标

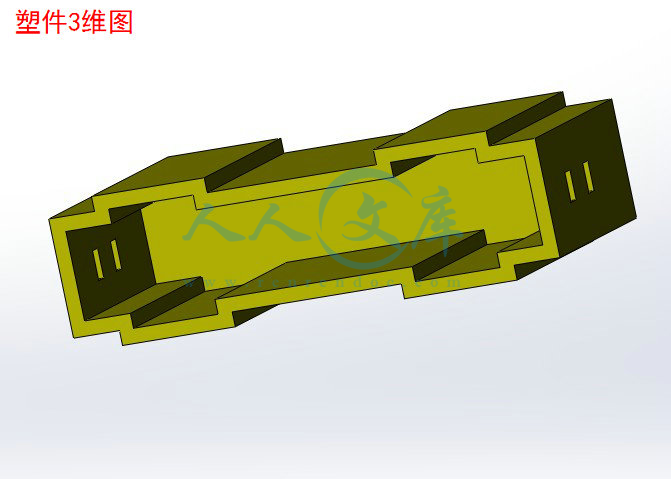



![零件图合图[18张].jpg](/ueditor/net/upload/2015-03-02/1b9833e9-e052-45fd-97f1-4182d03d5772.jpg)
