壳体侧抽芯注塑模设计
54页 22000字数+说明书+21张CAD图纸【详情如下】
侧型芯.dwg
动模仁.dwg
动模座板.dwg
垫块.dwg
壳体侧抽芯注塑模设计论文.doc
壳体零件图.dwg
复位杆.dwg
定位圈.dwg
定模座板.dwg
导柱.dwg
封面.doc
拉料杆.dwg
推杆.dwg
推板.dwg
推板固定板.dwg
推板导柱.dwg
摘要.doc
支承板.dwg
斜导柱固定板.dwg
斜滑杆.dwg
浇口套.dwg
脱浇板.dwg
表格.doc
装配图.dwg
镶块1.dwg

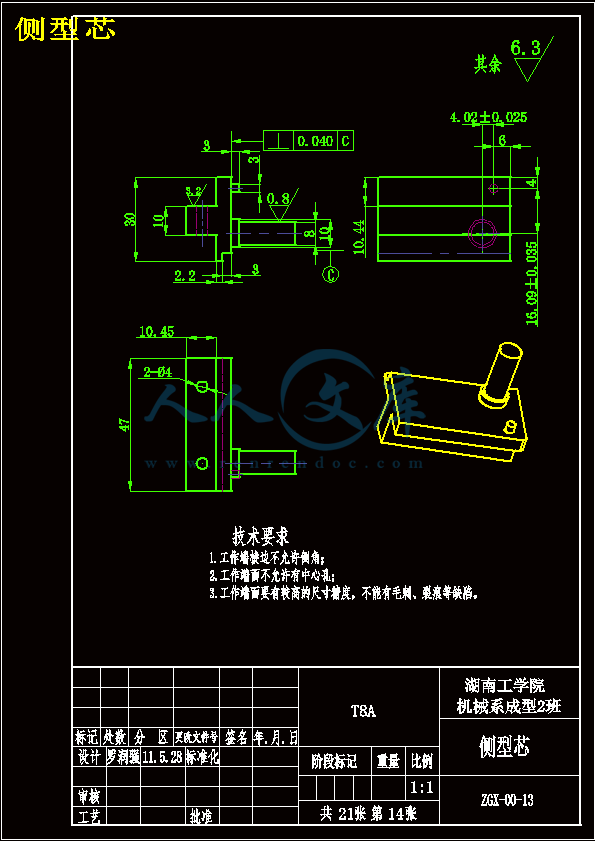
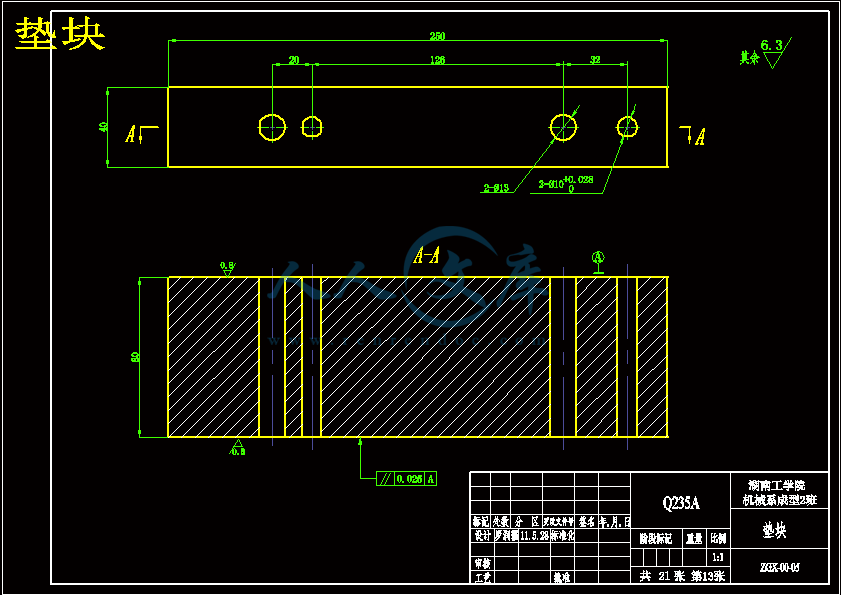
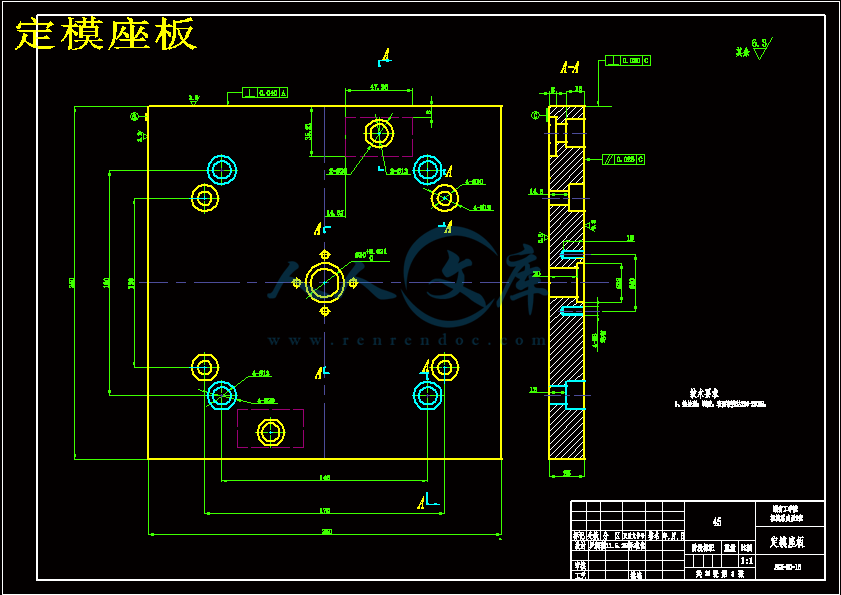


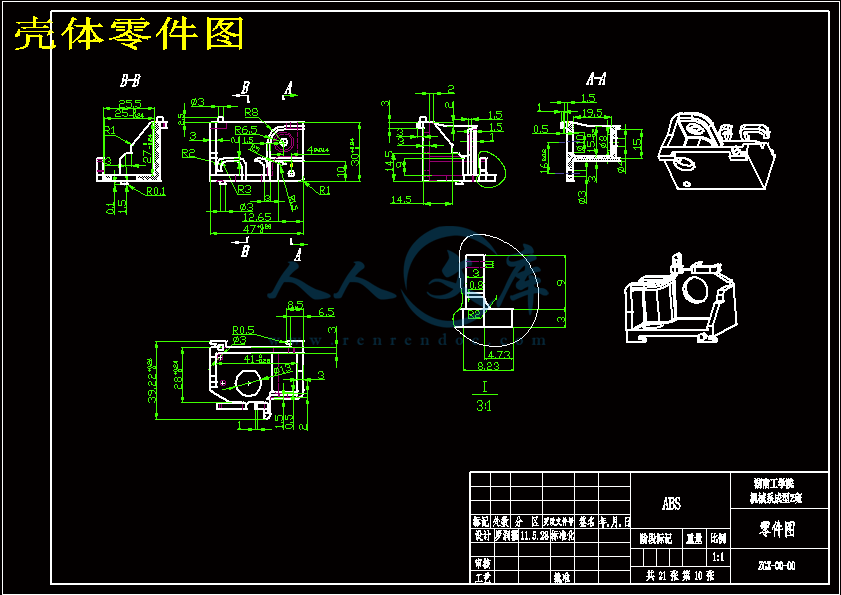
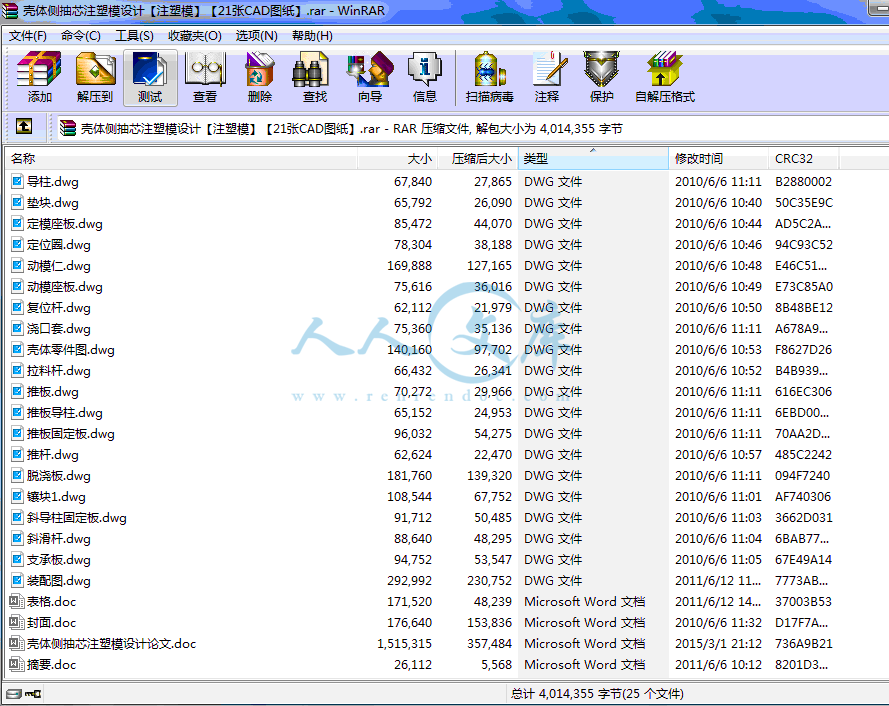
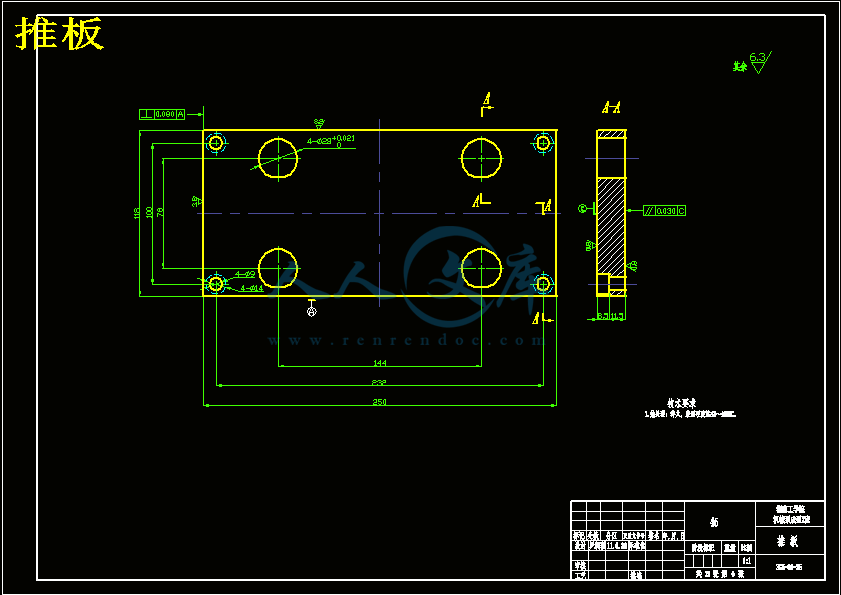
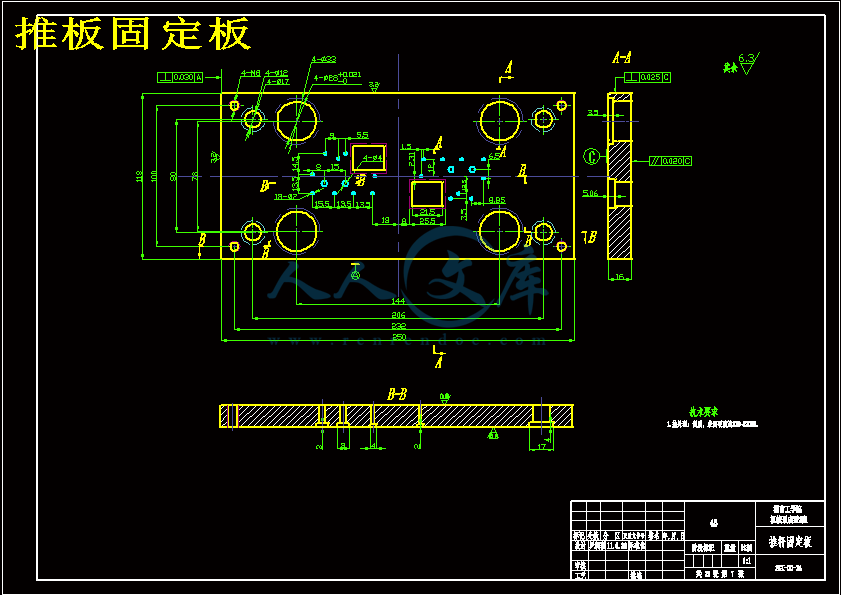

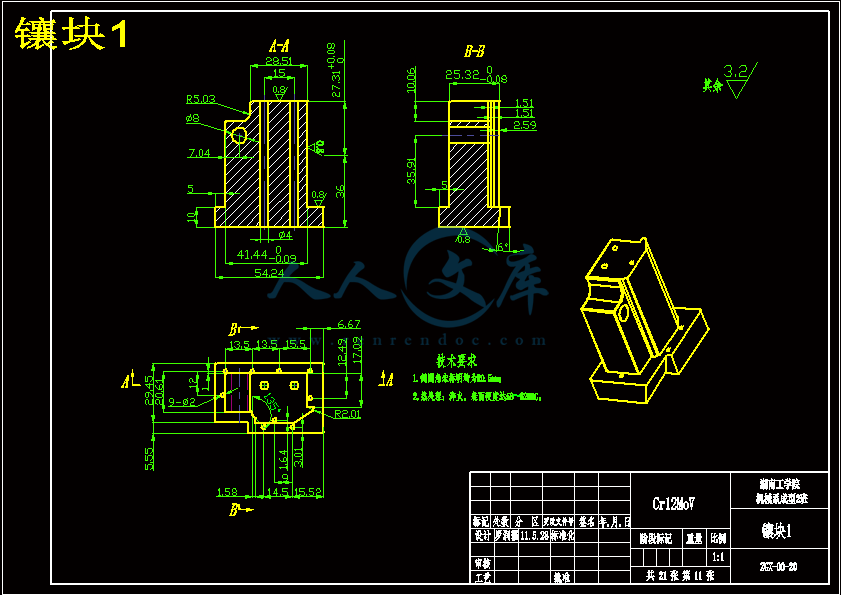
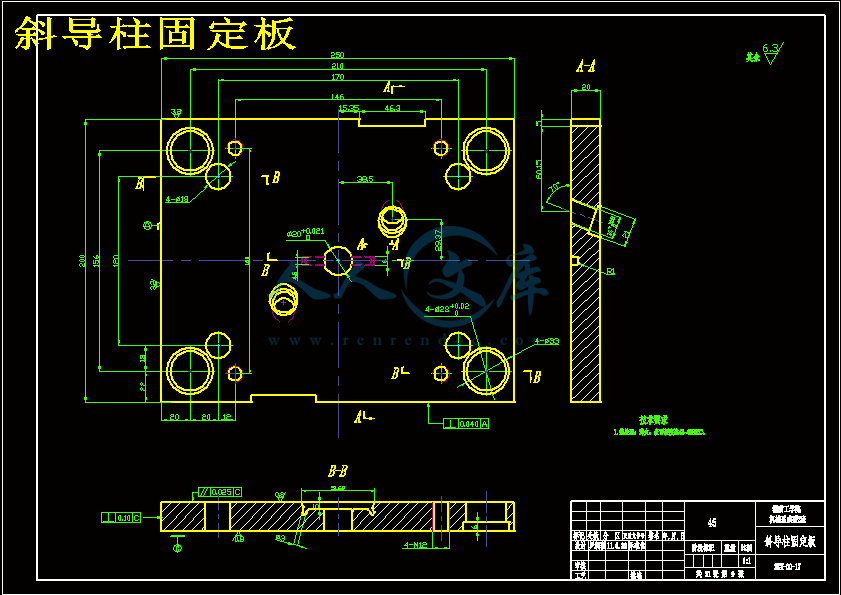
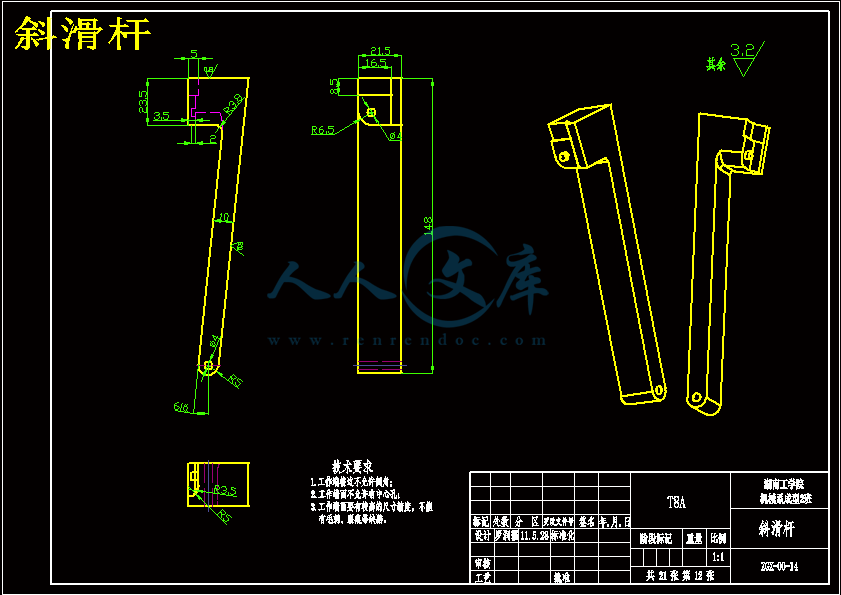

目 录
1 前言1
2 绪论2
2.1概述2
2.2我国塑料模现状2
2.3 我国塑料模的发展趋势3
3 塑件成型工艺分析5
3.1 塑件图5
3.2 塑件工艺分析5
3.2.1 精度等级5
3.2.2 脱模斜度5
3.2.3 塑件圆角6
3.3 ABS塑料性能特性与工艺参数6
3.3.1 ABS化学与物理特性6
3.3.2 ABS塑料的成型条件7
4 拟定模具结构形式8
4.1 型腔数目的确定8
4.2 分型面的选择9
5注塑机型号的确定11
5.1 注塑容量的计算11
5.2锁模力的计算11
5.3 注塑机的选用12
5.4 有关参数的校核13
5.4.1由注塑机料筒速率校核模具的型腔数13
5.4.2 注射压力的校核13
5.4.3 锁模力的校核13
5.4.4 开模行程的校核14
6 浇注系统的设计14
6.1 主流道的设计15
6.2 分流道的设计17
6.3 冷料穴的设计19
6.4 浇口的设计20
6.4.1浇口类型的选择20
6.4.2 浇口尺寸的确定22
6.4.3 浇口剪切速率的校核23
6.5 排气系统的设计23
7 成型零件设计23
7.1 成型零件的结构设计24
7.2 成型零件钢材的选用25
7.3 成型零件工件尺寸的计算26
7.4 型腔壁厚和底板厚度的计算29
7.4.1 侧壁厚度计算29
7.4.2 底板厚度计算30
8 模架的确定32
9 导向机构的确定32
10 脱模机构的设计34
10.1 脱模力的计算34
10.2 脱模机构的结构设计35
11 侧向抽芯的设计37
11.1 抽芯距与抽芯力的计算37
11.2 斜导柱圆形截面直径的计算40
11.3 斜导柱圆长度的计算40
11.4 斜滑杆的设计41
12 模温调节系统的设计42
12.1 冷却系统的设计42
13 数控程序的编制47
14 设计小结49
参考文献50
致 谢51
摘 要
本论文介绍了壳体的注射模设计过程。主要研究带有侧凹或侧孔结构的塑料制件如何分型和脱模的,本塑件侧面带有三个小孔,直接开模无法实现分型,这就涉及到斜导柱和斜滑杆的设计以及他们的工作原理,利用注塑机开合模的作用力进行侧抽芯,一方面减少了一些零件的使用,降低成本;另一方面省去一些零件的安装工序,节约时间,缩短生产周期,提高经济效益。本文还介绍了型腔数量和布局的确定、注射机选择、浇注系统设计、模板及其标准件的选用、脱模及抽芯机构的设计、成型部件的设计等。
关键词:注塑摸;斜滑杆;侧抽芯;壳体
ABSTRACT
This paper has introduced the design process of injection mould of the shell. The main research the plastic workpiece with side concave or side hole is how to divide structure and draw of patterns. Because the side of model has three eyelets, it is unable to realize by directly operating the mold, by designing the slanting leader pin and the lifter. We use the action of the injection molding machine to carry on core-pulling. The advantage of this design are reducing the use of some components, lowing the cost, omitting some component to install the working procedure, saving time, reducing the production cycle and enhancing the economic efficiency. This article also introduces die space quantity and the layout determination, the injection machine choice, the casting system design, the template and the standard part selection, the drawing of patterns and core-pulling organization design, the formation parts design etc.
Key words:injection mould; lifter; core-pulling; shell
随着经济的发展,各行各业对各类模具的需求不断增加,所需品种也越来越细化. 据预测,国内模具发展的趋势:
(1)模具日趋大型化;模具的精度将越来越高;多功能复合模具将进一步发展;
(2)热流道模具在塑料模具中的比重将逐渐提高;
(3)随着塑料成形工艺的不断改进与发展,气辅模具及适应高压注射成型等工艺的模具将随之发展;
(4)标准件的应用将日渐广泛;
(5)快速经济模具的发展前景十分广阔;
(6)以塑代钢、以塑代木的进程进一步加快,塑料模具的比例将不断增大;
(7)模具技术含量将不断提高,中、高档模具比例将不断增大。
3.2 塑件工艺分析
该塑件为一塑料壳体,结构复杂,塑件壁厚不均,要求材料须有很好的流动性。合理确定塑件壁厚尺寸,如果壁厚值太小,会影响塑件的强度和刚度,并且导致塑料填充困难。壁厚太大,增加冷却时间,降低生产率,产生气泡、缩孔等不良现象。要求壁厚尽可能均匀一致,否则由于冷却和固化速度不一样易产生内应力,引起塑件的变形及开裂。生产批量大,材料为丙烯烃-丁二烯-苯乙烯共聚物(ABS),成型工艺性很好,可以注塑成型。
3.2.1 精度等级
影响塑件精度的因素很多,塑料的收缩、注塑成型条件(时间、压力、温度)等,塑件形状、模具结构(浇口、分型面的选择),飞边、斜度、模具的磨损等都直接影响制品的精度。按SJ1372—1978标准,塑料件尺寸精度分为8级,本塑件所用材料为丙烯烃-丁二烯-苯乙烯共聚物(ABS),由此查塑料模具设计手册可知,本塑件宜选用4级精度。
3.2.2 脱模斜度
由于塑件冷却后产生收缩,会紧紧地包住模具型芯、型腔中凸出的部分,使
参考文献
[1] 许发樾主编.实用模具设计与制造手册[M].北京:机械工业出版社,2001.2
[2] 四川大学等编.塑料成型模具[M].北京:中国轻工业出版社,1982.6
[3] 李建军,李德群.模具设计基础及模具CAD[M].北京:机械工业出版社,2005.7
[4] 叶久新,王群.塑料制品成型模具及模具设计[M].长沙:湖南科学技术出版社.2005.8
[5] 黄毅宏,李明辉.模具制造工艺[M]. 北京:机械工业出版社,2003.7
[6] 付宏生,刘京华.注塑制品与注塑模具设计[M]. 北京:化学工业出版社,2003.6
[7] 卜建新主编.塑料模具设计[M]. 北京:中国轻工业出版社,2005.2
[8] 杜智敏等著.Pro/ENGINEER野火版塑料注射模具设计实例[M]. 北京:机械工业出版社,2005.2
[9] 周凤云.工程材料及应用(第二版)[M].武汉:华中科技大学出版社,2002.11
[10] 沈其文.材料成型工艺基础(第三版)[M].武汉:华中科技大学出版社,2003.9
[11] 大连理工大学工程画教研室编[M].机械制图(第四版).北京:高等教育出版社,1993.5
[12] 王永平编.注塑模具设计经验点评[M]. 北京:高等教育出版社,2004.7
[13] 伍先明等编著.塑料模具设计指导[M].北京:国防工业出版社,2006.5
[14] 周建安. 彩电前壳注射模设计[J].模具制造.2005,12
[15] 阳湘安. 注射模冷却系统的设计及分析[J].模具制造.2004,8.
[16] 李孝宽.对国内模具发展建议性探讨[J] .数控机床市场.2005,8
[17] 任紫亭,郭晓婷.热处理工艺对楔块模具使用寿命的影响[J].机械管理开发.2005,1
[18] 许发樾等. 试论制造业与模具市场[J].模具制造.2004,12
[19] 许荔珉等.注塑成型质量缺陷分析[J].模具技术.2005,2
[20] 付宏生,刘京华.注塑制品与注塑模具设计[J].化学工业出版社.2003.5
[21] 伍先明,张蓉.塑料模具设计指导[J].国防工业出版社.2010.8