X-Y型数控铣床工作台的设计【8张图纸】【优秀】
收藏
资源目录
压缩包内文档预览:
编号:419962
类型:共享资源
大小:1.32MB
格式:RAR
上传时间:2015-03-28
上传人:上***
认证信息
个人认证
高**(实名认证)
江苏
IP属地:江苏
35
积分
- 关 键 词:
-
X-Y型
数控铣床
工作台
设计
图纸
- 资源描述:
-
X-Y型数控铣床工作台的设计
38页 18000字数+说明书+外文翻译+8张CAD图纸【详情如下】
X-Y型数控铣床工作台的设计.txt
X-Y型数控铣床工作台的设计说明书.doc
X-Y工作台装配图.dwg
Y底座.dwg
外文翻译--多目标优化激光切割工艺 中文版.doc
外文翻译--多目标优化激光切割工艺 英文版.pdf
工作台.dwg
滚动导轨副.dwg
滚珠丝杠副.dwg
端盖.dwg
螺母支座.dwg
轴承支座.dwg


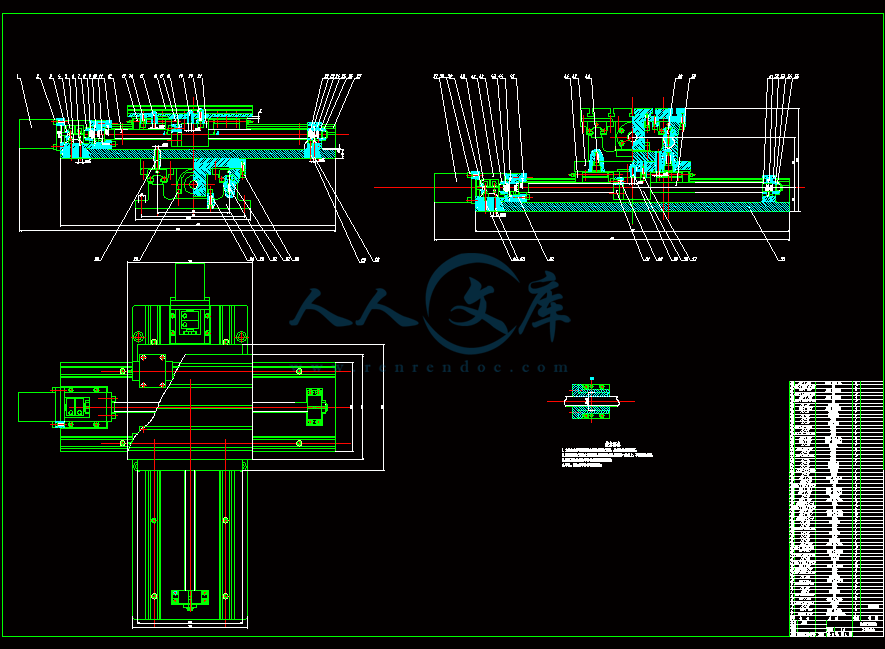

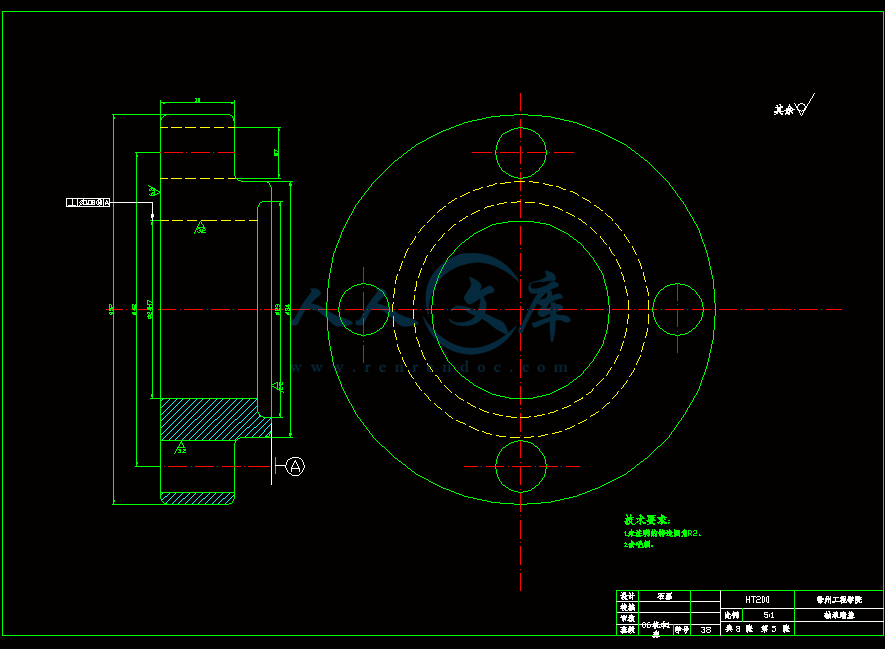


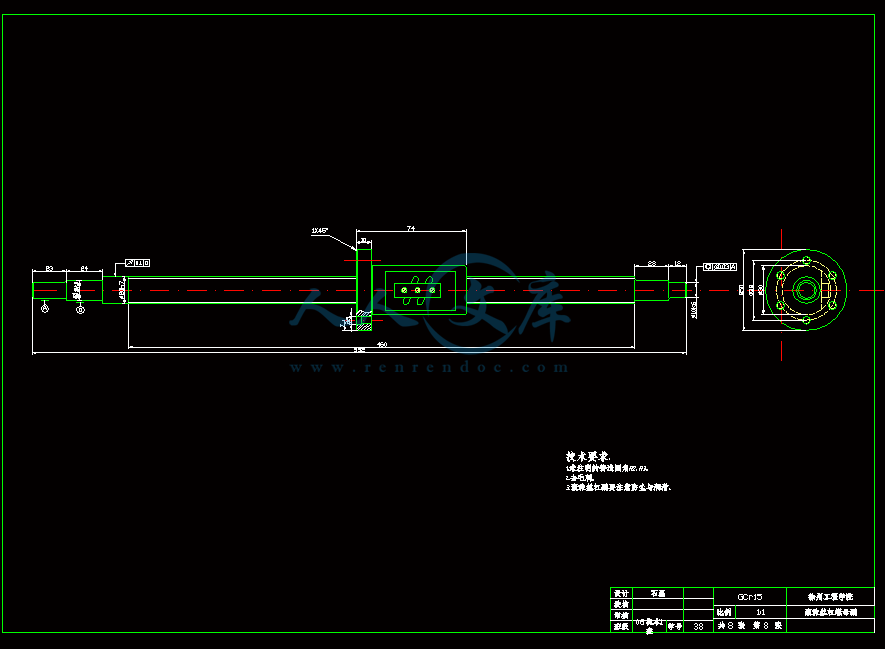


目 录
1绪论1
1.1课题的选择背景1
1.2设计目的及意义1
1.3总体方案的设计2
2交流伺服电动机的选型3
2.1交流伺服电动机的选型3
2.1.1电机的选择依据.4
2.1.2电机的负载力矩和惯量的计算.5
2.2交流伺服电动机概述.6
2.2.1选择伺服电动机.7
3丝杠的选型7
3.1丝杠的介绍7
3.1.1丝杠螺母机构基本传动形式7
3.1.2滚珠丝杠副的组成及特点7
3.1.3滚珠丝杠副的典型结构形式8
3.1.4滚珠丝杠副轴向间隙的调整和预紧9
3.1.5滚珠丝杠副的密封与润滑9
3.2丝杠螺母副的选择10
3.3丝杠的校核11
3.4滚珠丝杠支承的选择12
3.4.1支承方式的选择12
3.4.2轴承的选择13
3.5设计滚珠丝杠应注意的问题15
4联轴器的选型17
4.1联轴器的介绍17
4.2选择联轴器的类型17
4.2.1初选联轴器的类型17
4.2.2初选联轴器18
4.3联轴器的校核19
4.3.1转矩的校核20
4.3.2销的抗剪强度的校核20
5导轨的选型及计算21
5.1 导轨的组成种类及其应满足的要求21
5.2导轨材料的选择及热处理21
5.2.1导轨材料的选择21
5.2.3导轨的热处理22
5.3导轨的选型及长度估算22
5.4导轨副的额定寿命计算23
5.5滚动导轨副的技术要求25
5.6导轨防护罩的设计25
5.6.1导轨防护罩的介绍25
6.6.2导轨防护罩的选择25
5.7导轨的注意事项26
6机座的设计27
6.1机座的作用及基本要求27
6.2机座的设计27
6.2.1机座自身刚度27
6.2.2提高机座连接处的接触刚度28
6.3机座材料的选择28
结论29
致谢30
参考文献31
附录32
1绪论
1.1课题的选择背景
X – Y数控工作台是指能分别沿着X 向和Y向移动的工作台。数控机床的加工系统、立体仓库中堆垛机的平面移动系统、平面绘图仪的绘图系统等,尽管结构和功能各不相同,但基本原理相同。机电一体化系统是将机械系统与微电子系统结合而形成的一个有机整体。在中小形企业中,由于产品更新换代频繁,且大都是一些适应市场的单件,小批零件,若由数控机床来解决这些零件的加工精度和自动化问题,因成本高,而不现实。为此,数控工作台,作为工装与通用机床(立铣,立镗,钻等)陪用,以解决单件,小批。小尺寸复杂零件的孔,槽及凸轮等精度加工问题,具有一定的灵活性,通用性和经济性。X - Y工作台的机电一体化系统可以设计为开环、半闭环和闭环伺服系统三种。开环的伺服系统采用步进电机驱动,系统中不设置传感与检测设备,半闭环的伺服系统中一般采用交流或直流伺服电机驱动,并在电机输出轴端设置传感与检测设备;闭环的伺服系统中也是采用交流或直流伺服电机驱动,但检测与传感设备设置在工作台末端。数控交流伺服X-Y工作台系统是由控制计算机部分、伺服驱动部分、机械传动部分及检测部分组成,采用闭环控制方式。
1.2设计目的及意义
《机电一体化系统设计》课程设计是培养学生设计能力的重要实践性教学环节之一,是综合运用所学过的机械、电子、自动控制、计算机等知识进行的基本设计训练。其目的是:
1)能够正确运用《机电一体化系统设计》课程的基本理论和相关知识,掌握机电一体化系统(产品)的功能构成、特点和设计思想、设计方法,了解设计方案的拟定、比较、分析和计算,培养学生分析问题和解决问题的能力,使学生具有机电一体化系统设计的初步能力;
2)通过机械部分设计,掌握机电一体化系统典型机械零部件和执行元件的计算、选型和结构设计方法和步骤;
3)通过测试及控制系统方案设计,掌握机电一体化系统控制系统的硬件组成、工作原理,和软件编程思想;
4)通过课程设计提高学生应用手册、标准及编写技术说明书的能力,促进学生在科学态度、创新精神、专业技能等方面综合素质的提高。
1.3总体方案的设计
设计一台数控铣床XY工作台,采取PLC控制,控制方式采用交流伺服、运动控制器和PC机(闭环控制)。
X-Y工作台的机械主体部分直线导轨和滚珠丝杠,联轴器,工作台面。电气部分的关联性及传动装置的保护性,X轴及Y轴两端配有高质量的缓冲器,同时可选配在工作台的两端配有限位检测开关,部分工作台的配有原点检测开光,并提供光电编码装置以适于闭环控制,原点开关的位置可以打距离的调节。其具体参数如下:
X方向行程:100mm Y方向行程:160mm
工作台面的参考尺寸:240260mm
工作台和工件最大物重质量60kg
工作台表面滑动摩擦系数为0.5
平均切削力:500N
快进进给速度:1000mm/min
最高运动速度:10000mm/min
脉冲当量0.001mm
定位精度: 0.02mm
工作寿命:每天8小时,工作8年,250天/年
- 内容简介:
-
Optics & Laser Technology 40 (2008) 562570Multi-objective optimisation of laser beam cutting processAvanish Kumar Dubey?, Vinod YadavaDepartment of Mechanical Engineering, Motilal Nehru National Institute of Technology, Teliarganj, Allahabad, UP 211004, IndiaReceived 31 July 2007; received in revised form 1 September 2007; accepted 7 September 2007AbstractThis paper presents a hybrid Taguchi method and response surface method (TMRSM) for the multi-response optimisation of a laserbeam cutting process. The approach first uses the Taguchi quality loss function to find the optimum level of input cutting parameterssuch as assist gas pressure, pulse width, pulse frequency and cutting speed. The optimum input parameter values are further used as thecentral values in the response surface method to develop and optimise the second-order response model. The two quality characteristicsKerf width (KW), and material removal rate (MRR), that are of different nature (KW is of the smaller-the-better type, while MRR is ofthe higher the better type), have been selected for simultaneous optimisation. The results show considerable improvement in both thequality characteristics when the hybrid approach is used, as compared the results of a single approach.r 2007 Elsevier Ltd. All rights reserved.Keywords: Taguchi method; Laser beam cutting; Hybrid approach1. IntroductionThe laser was invented in 1960s and has wide applica-tions in the field of fine cutting of sheet metals due to itsprecision and high intensity 1,2. Laser beam cutting(LBC)canbesuccessfullyusedforthecuttingofconductive and nonconductive difficult-to-cut advancedengineering materials such as reflective metals, plastics,rubbers, ceramics and composites. Apart from cuttingdifficult-to-cut materials, LBC is most widely used inindustries to achieve complex shapes/profiles with closetolerances for cutting of steel sheets 3. The most widelyused industrial lasers for cutting of sheet metals are gaseousCO2and solid state Nd:YAG. There has been growinginterest in recent years in the use of pulsed Nd:YAG lasersfor precision cutting of thin sheet metals because of its highintensity, low mean beam power, good focusing character-istics, and narrow heat affected zone (HAZ).LBC is a thermal energy based non-conventional cuttingmethod in which sheet material is cut mainly due to meltingand vaporisation. The molten material is ejected with thehelp of high-pressure assist gas jet 4. The schematic of theLBCprocesshasbeenshowninFig.1.Sinceitsintroduction, LBC has always been a major research areafor getting the exceptionally good quality of cut. Thequality of cut solely depends on the setting of processparameters such as laser power, type and pressure of assistgas, sheet material thickness and its composition, cuttingspeed, and mode of operation (continuous wave or pulsedmode). A lot of experimental investigation has beenundertaken with the aim of analysing the effect of processparameters on cut geometry, and cut surface quality.In most of the experimental investigations of the LBCprocess, researchers have varied one factor at a time toanalyse the effect of input process parameters on outputqualitycharacteristicsorresponses510.Butthistechnique requires a large number of experimental runsbecause only one factor is varied in each run, keeping allotherfactorsconstant.Also,inthistechnique,theinteraction effects among various input process parametersare not considered. To overcome these problems, someresearchershaveincorporateddesignofexperimentsmethodologies such as the response surface methodology(RSM) and Taguchi methodology (TM) during experi-mental study of LBC process.Tam et al. 11 applied the Taguchi method to study thelaser cutting process for 4.5mm thick mild steel sheet. TheARTICLE IN PRESS/locate/optlastec0030-3992/$-see front matter r 2007 Elsevier Ltd. All rights reserved.doi:10.1016/j.optlastec.2007.09.002?Corresponding author. Tel.: +915322271812; fax: +915322445101.E-mail address: avanishdubey (A. Kumar Dubey).signal-to-noise (S/N) ratio of overall figure-of-merit wasconsidered as quality function. This quality functionintegrates the weighted effects of quality characteristics(Kerf width (KW), surface roughness, micro-hardness,slope of cut edge and HAZ) and cost components (cuttingspeed, oxygen pressure and beam power). Lim et al. 12have applied the same approach for the study of the surfaceroughness obtained during high-speed laser cutting ofstainless steel sheets. Li et al. 13 have also appliedTaguchis robust design methodology to study the width ofcut and HAZ during laser cutting of (quad flat no (QFN)lead) packages using a diode pumped solid state laser(DPSSL) system. The cutting parameters taken are: lasercurrent, laser frequency and cutting speed.Mathew et al. 14 performed parametric studies onpulsed Nd:YAG laser cutting of fibre reinforced plasticcomposite sheet (2mm thick). A central composite design(CCD) with uniform precision was used for experimentaldesign and a second-order response surface model for HAZandKerftaperwasdeveloped.Theinputprocessparameters were cutting speed, pulse energy, pulse dura-tion, pulse repetition rate and gas pressure. Almeida et al.15 applied factorial design approach to determine theeffects of pulse energy, overlapping rate and type of assist-gas on the surface roughness and dross formation (edgeirregularity) during Nd:YAG laser cutting of pure titaniumand titanium alloy (Ti6Al4V).The design of experiments based studies on LBC processso far have been mainly aimed at the optimisation of thesingle quality characteristic at a time. It has been foundthat the optimum parameter settings for one qualitycharacteristic may deteriorate other quality characteristics.As the aim of a manufacturing process is always toimprove the overall quality of a product it is necessary tooptimisethemultiplequalitycharacteristicssimulta-neously. Antony 16 has demonstrated a Taguchi qualityloss function based multi-objective optimisation techniquefor manufacturing processes taking an example of electro-nic assembly problem. He has found considerable im-provementinmultiplequalitycharacteristics,incomparison to single quality characteristics.Different hybrid approaches have recently been used forthe optimisation of different machining processes. Taguchimethod with fuzzy logic 17 or with grey relational analysis18 has been used to optimise the electrical dischargemachining process (a non-conventional thermal basedmachining process) with multiple machining performance.Chiadamrong 19 has suggested a sequential integrationapproach of TM and RSM to optimise the qualitycharacteristics in manufacturing system. He demonstratedthe hybrid methodology by taking a case study of printedcircuit board manufacturing plant and found a significantreduction in quality loss. The hybrid approach of TM andRSM has yet not been applied in the study of LBC processwith single or multiple performance measures.In the present paper a hybrid Taguchi method andresponse surface method (TMRSM) approach has beenused to develop the response models and to optimise theARTICLE IN PRESSNomenclaturebregression coefficientDcomposite desirabilitydindividual desirabilityknumber of responses or quality characteristicsLijthe quality loss for the ith quality characteristicat the jth trial condition or runLi*maximum quality loss for the ith qualitycharacteristic among all the experimental runsmMean of multiple S/N ratios of all experimentalrunsnnumber of experimental runspnumber of control factors or input processparameterswiweighting factor assigned to ith response orquality characteristicxiith input process parameter or control factorYjtotal normalised quality loss value in jthexperimental runyiresponse or observed quality value in ithexperimental runyijnormalised quality loss value for ith experi-mental run and jth quality characteristicZS/N ratioZopredicted multiple S/N ratio at optimumparameter levelsZejmultiple S/N ratio of jth trial condition orexperimental runGAS JETDRAG LINESMELTING OR SLAGNOZZLEGASFOCUSING OPTICSLASERBEAM CUTTING EDGE ON WORKPIECE Fig. 1. Schematic of laser beam cutting.A. Kumar Dubey, V. Yadava / Optics & Laser Technology 40 (2008) 562570563LBC process for multiple quality characteristics such asKW,andmaterialremovalrate(MRR).ApulsedNd:YAG laser beam is used for cutting of thin sheets ofmagnetic material (grain oriented high silicon-alloy steelsheets used in transformers). The quality characteristics oftwo different nature (KW is of smaller-the-better (SB) typeand MRR is of higher-the-better (HB) type) with unequalweighting factor (KW: 80%, and MRR: 20%) have beenselected. Firstly, TM is applied to determine the optimumprocess parameters for multiple quality characteristics (i.e.for minimum KW and maximum MRR). The output(optimum parameter values) from TM is further used ascentral value in RSM. The second-order response modelfor KW and MRR has been developed by performing theexperiments using the central composite rotatable design(CCRD) matrix 20. The MINITAB software has beenused to calculate the final results of multi-objectiveoptimisation. The results of multi-objective optimisationusing Taguchis quality loss function only have also beencompared with the results from hybrid approach.2. Experimental planning methods2.1. Taguchi methodIn the Taguchi method, the optimum level of input processparameters or control factors are decided on the basis ofstatistical analysis of experimental results that makes theprocessinsensitivetotheeffectofvariationsduetouncontrollableornoisefactorssuchasenvironmentaltemperature, humidity and vibration. In this method, theexperiments are performed as per specially designed experi-mental matrix known as orthogonal array (OA) 2122. Theselection of OA is based on the total degree of freedom (dof) ofthe process. Mathematically, the dof can be computed as 22:dof number of levels ? 1 for each control factor number of levels for A ? 1? number of levels for B ? 1for each interaction 1?,1where, A and B are the interacting control factors.In the Taguchi method, the S/N ratio (Z) is used torepresent the quality characteristics for the observed dataor responses. Here, the signal represents the desirablevalue and the noise represents the undesirable value andS/N ratio expresses the scatter around the desired value.The larger the S/N ratio, smaller will be the scatter.Depending on the experimental objectives, there are severalquality characteristics. In the present case, a smaller valueof KW and a higher value of MRR are desirable. In theTaguchi method these characteristics are termed SB typeand HB type respectively. Mathematically, the S/N ratios(Z) for SB and HB type quality characteristics can becomputed as 2122:Z ?10log10MSD,(2)where, MSD=mean square deviation from the desiredvalue and commonly known as quality loss function.For SB?type;MSD 1=nXni1y2i#,(3)For HB?type;MSD 1=nXni11=y2i#,(4)where, yiis the observed response or quality value at the ithtrial or experimental run and n is the number of trials atsame parameter level.In multi-objective optimisation, a single overall S/Nratio for all quality characteristics is computed in place ofseparate S/N ratios for each of the quality characteristic.This overall S/N ratio is known with the name of multipleS/N ratio (MSNR). The MSNR for jth trial Zej iscomputed as given below 16.Zej ?10log10Yj,(5)YjXki1wiyij,(6)yijLijLi?,(7)where Yjis the total normalised quality loss in jth trial, wirepresentstheweightingfactorfortheithqualitycharacteristic, k is the total number of quality character-istics and yijis the normalised quality loss associated withthe ith quality characteristic at the jth trial condition, and itvaries from a minimum of zero to a maximum of 1. Lijisthe quality loss or MSD for the ith quality characteristic atthe jth trial, and Li*is the maximum quality loss for the ithquality characteristic among all the experimental runs.2.2. Response surface methodRSM is a collection of statistical and mathematicalmethods that are useful for the modelling and optimisationof the engineering science problems. In this technique, themain objective is to optimise the responses that areinfluenced by various input process parameters. RSM alsoquantifies the relationship between the controllable inputparameters and the obtained responses. In modelling andoptimisation of manufacturing processes using RSM, thesufficient data is collected through designed experimentation.In general, a second-order regression model is developedbecause first-order models often give lack-of-fit 23.According to RSM, all the input process parameters areassumed to be measurable, the corresponding responsescan be expressed as follows:y fx1; x2;:; xp,(8)where, x1, x2,y, xpare input process parameters and y isthe response which is required to be optimised. Here, it isassumed that the independent variables (input processARTICLE IN PRESSA. Kumar Dubey, V. Yadava / Optics & Laser Technology 40 (2008) 562570564parameters) are continuous and controllable by experi-ments with negligible errors. It is also required to find asuitable approximation for the true functional relationshipbetween independent variables and responses. Usually, asecond-order regression model as given below is utilised inRSM.y b0Xpi1bixiXpi1biix2iXiXjbijxixj,(9)where, all bs are regression coefficients determined by leastsquare method 23. In order to estimate the regressioncoefficients in this model each variable ximust be taken atleast three different levels. This requires 3pnumber ofexperiments in factorial design but it is a tedious job withlarge number of factors. For fitting second-order model anew design known as CCD is generally used 20. Itrequires experimentation with 2pnumber of experiments offactorial design and 2p+1 combination of additionalfactors. These combinations are taken as given below:0;0.;0; ?a;0;.;0; a;0.;0;0;?a;.;0; 0;a.;0.0;0;.;?a; 0;0.;a:Here, the value of code a is equal to (2p)1/4, and it isintroduced to provide the orthogonal property to array.The coded level 0 represents the central value of inputprocess parameters.It is important for a second-order model to provideoptimum prediction about the process behaviour within thespecified range of all input process parameters. So themodel should have a reasonably consistent and stableprediction of responses at points of interest xi. This can beachieved by CCRD. According to CCRD methodology,standard error is kept same for all points that are at thesame distance from the centre of the region. This can bestated mathematically as follows 20:x21 x22 ? x2p constant:(10)CCRD requires minimum five levels of all factors for thecalculation of regression coefficients. In this situation, thetotal number of combinations or runs required becomes2p+2p+more than one runs at centre. In present case offour control factors an standard CCRD matrix with 7central point runs has been selected 20.The developed response model is used for findingoptimum level of input process parameters. This isobtained by location of stationary points that will lead toa point of maximum or minimum response 23.3. Experimental procedure and operating parametersThe experimental studies were performed on a 200Wpulsed Nd:YAG laser beam machining system with CNCwork table. The oxygen is used as an assist gas. Thevariable input process parameters (or control factors)taken are assist gas pressure, pulse width, pulse frequency,and cutting speed. Focal length of lens used is 50.0mm.Nozzle diameter (1.0mm), nozzle tip distance (1.0mm),and sheet material thickness (0.5mm) were kept constantthroughout the experimentation. The two quality char-acteristics analysed are KW and MRR. The grain orientedhigh silicon-alloy steel sheet (a magnetic material sheetused in transformer cores) was used in the experiments assheet material. Two cuts each of 15mm length wereobtained in each experimental run. The KW was measuredusing the Tool Makers Microscope (Model RTM-900,RADICAL Instruments, India) at 10? magnification. TheKW (mm) taken is the mathematical average of two cutscorresponding to same experimental run. KW of each cuthas been measured at three different places at the top of thesheet. Average of these three measurements represents theKW of each cut. The MRR (mg/min) is calculated by usingthe following formula:MRR Loss of mass during each cut ? cutting speedlength of cut.(11)The MRR calculated is also taken as average of twocuts. The loss of mass was obtained by weighing thespecimen before and after the cutting using ElectronicBalance (Model A?120, Shimandzu Corporation, Japan).Thecontrolfactorstakenarethegaspressure(1.53.5kg/cm2),pulsewidthorpulseduration(1.01.4ms), pulse frequency (2028Hz), and cutting speed(2575mm/min). The numerical values of factors atdifferent levels are shown in Table 1. An exhaustive pilotexperimentation is done to decide the parameter rangefor quality cut. Here, the quality cut basically representsthe complete through and dross free cutting without anyburning effect as per visual inspection through nakedeye. For example, the minimum pulse width, maximumcutting speed and gas pressure were found to be 0.6ms,125mm/min and 4.5kg/cm2, respectively for completethrough cutting but, below the pulse width of 1.0ms, andbeyond the cutting speed of 75mm/min and gas pressure of3.5kg/cm2, the cutting was not free from burning effectand/or dross adhesion to the bottom surface of the sheet.The quality characteristics measured are KW and MRR.The initial setting of input parameters is: gas pressure?1.5kg/cm2, pulse width ?1.0ms, pulse frequency ?20Hz,and cutting speed ?25mm/min.In present case of four parameters at three differentlevels assuming no interaction between factors, the dof hasARTICLE IN PRESSTable 1Control factors and their levels used in OA design matrixSymbolFactorsUnitLevel 1Level 2Level 3AGas pressurekg/cmBPulse widthms1.01.21.4CPulse frequencyHz202428DCutting speedmm/min255075A. Kumar Dubey, V. Yadava / Optics & Laser Technology 40 (2008) 562570565been calculated using Eq. (1):dof 3 ? 14 1 9.Hence, a standard L9OA is selected for experimentaldesign matrix (Table 2).The control factors, their numerical and coded valuesused in CCRD matrix are shown in Table 3. The CCRDmatrix contains total 31 runs with 2pfactorial runs, 2paxial runs, and 7 centre point runs. Number of controlfactors (p) in present case are 4.Therefore, total number of runs 24+2*4+7 31The central value of process parameters correspondingto code 0 is the optimum parameter level obtained frommulti-objective optimisation using TM. The value of a inCCRD is calculated asa 2p1=4 2.Therefore, the coded values for different levels in CCRDare ?2, ?1, 0, 1, and 2. The spread of parameter variationbetween two adjacent levels have been tightened with aview to capture close variations of control factors fromcentral value of the range. The numerical values assigned togas pressure, pulse width, pulse frequency and cuttingspeed at different coded levels are so chosen that the rangeof parameters do not exceed the extreme limits ofindividual process parameters decided for complete throughcutting as observed during pilot experimentations.4. Response surface modellingThe second-order response surface model for KW andMRR has been developed from the experimental responsevalues obtained using CCRD experimental matrix (Table 4).The model developed using MINITAB software isKWmm 0:1511 0:0746x1 0:3736 x2? 0:0191 x3 0:0021 x4 0:0013 x21? 0:1274 x22 0:0008x23? 0:0126 x1x2? 0:0029 x1x3 0:0010 x2x3,12MRR mg=min ? 97:6352 ? 23:5623 x1 47:6419 x2 9:0159 x3 1:4135 x4 2:7470 x21? 23:4560 x22? 0:1721 x23? 0:0027 x24 11:2499 x1x2 0:0417 x1x3? 0:1050 x1x4? 1:4063 x2x3 0:2750 x2x4 0:0175 x3x4.13where x1is gas pressure (kg/cm2), x2is pulse width (ms), x3ispulse frequency (Hz), and x4is the cutting speed (mm/min).ARTICLE IN PRESSTable 2Experimental observations using L9OAExperiment no.Factor levelsTop KW (mm)MRR (mg/min)ABCD111110.390044.9375212220.410088.7500313330.4200139.4826421230.3800126.1717522310.415096.5000623120.400046.5625731320.393392.0000832130.3933118.8601933210.400050.1875Table 3Factors and their coded levels in CCRDSymbolFactorsUnitCoded levels?2?1012AGas pressurekg/cm22.53.03.54.04.5BPulse widthMs1.21.4CPulse frequencyHz2022242628DCutting speedmm/min255075100125Table 4Experimental observations using CCRDExperimentno.Factor levelsTop KW(mm)MRR(mg/min)ABCD100000.3683110.25002?1?1?1?10.353375.166731?1?1?10.346776.16674?11?1?10.390086.1667511?1?10.386786.6667600000.3700117.00007?1?11?10.370080.500081?11?10.366779.66679?111?10.390089.166710111?10.416789.50001100000.3767122.000012?1?1?110.3367146.3333131?1?110.3800130.666714?11?110.3867153.33331511?110.3900157.66671600000.3700119.750017?1?111148.66670.3533181?1110.3433145.666719?11110.3967164.00002011110.3733158.33332100000.3767120.500022?20000.3833126.25002320000.3767127.7500240?2000.3233109.50002502000.3933123.25002600000.3833126.25002700?200.3800118.50002800200.4033116.250029000?20.410048.08333000020.3700178.75003100000.3767125.5000A. Kumar Dubey, V. Yadava / Optics & Laser Technology 40 (2008) 562570566To test whether the data are well fitted in model or not,the calculated S value of the regression analysis for KWand MRR are obtained as 0.01167 and 5.101, respectively,which are smaller and R2value for both the responses are83.0% and 98.5%, respectively. The value of R2(adj) forKW and MRR are 68.1% and 97.2%, respectively. Theseare moderately high (except R2(adj) for KW which ismoderate) therefore model fits the data. Hence, the data foreach response are well fitted in the developed models.Analysis of variance (ANOVA) and subsequently F-ratiotest and p-value test have been carried out to test theadequacy of the developed mathematical models for KW aswell as MRR. Table 5 shows the results of ANOVA. p-Valueof the source of regression model and linear effects are lowerthan 0.01 for both the responses. Developed regression modeland linear effect of parameters for both the responses aresignificant. Calculated F-value of the lack-of-fit for KW andMRR are 7.05 and 1.08 respectively, which are lower than thecritical value of the F-distribution 7.87 as found from standardtable at 99% confidence level. Therefore, the developedsecond-order regression model for KW and MRR areadequate at 99% confidence level.5. Results and discussion5.1. Multi-objective optimisation results using TaguchiapproachThe experimental values of responses KW and MRRusing OA design matrix are shown in Table 2. The qualityloss values for different quality characteristics in eachexperimental run are calculated using Eqs. (3) and (4).These quality loss values are shown in Table 6. Thenormalised quality loss for both the quality characteristicsin each experimental run has been calculated using Eq. (7)that is shown in Table 7. The total normalised quality loss(TNQL) and MSNR for multiple quality characteristicsKW and MRR has been calculated using Eqs. (5) and (6).These results are shown in Table 8. In calculating totalnormalised quality loss, two unequal weights i.e. w1 0.2for MRR, and w2 0.8 for KW has been assumed becausethe removal of material in LBC of thin sheets of steels isnot a difficult task but the most important thing is to getnarrow cut kerf. The MRR has been taken as a qualitycharacteristic with the view to include the two qualities ofdifferent nature (here, MRR is HB type and KW is SBtype). Therefore, higher weighting factor has been assignedto KW.The effect of different control factors on MSNR isshown in Table 9. The optimum levels of different controlfactors for minimum KW and maximum MRR obtainedare gas pressure at level 3 (3.5kg/cm2), pulse width at level1 (1.0ms), pulse frequency at level 2 (24Hz), and cuttingspeed at level 3 (75mm/min). The graphical representationARTICLE IN PRESSTable 5Results of ANOVA for developed modelsSourceKW modelMRR modelF-valuep-valueF-valuep-valueRegression5.5800.00176.4500.000Linear15.5900.000265.4100.000Square2.6100.0751.2600.327Interaction0.8800.5290.610.718Lack?of?fit7.050.0131.080.484Table 6Quality loss values for KW and MRRExperiment no.ABCDQuality loss values (dB)KWMRR111110.15214.952?10?4212220.16811.270?10?4313330.17640.514?10?4421230.14440.628?10?4522310.17221.074?10?4623120.16004.612?10?4731320.15471.181?10?4832130.15477.078?10?4933210.16003.970?10?4Table 7Normalised quality loss values for KW and MRRExperimentno.ABCDNormalised qualityloss valuesKWMRR111110.86221.0000212220.95290.2565313331.00000.1038421230.81860.1269522310.97620.2169623120.90700.9313731320.87700.2385832130.87700.1429933210.90700.8017Table 8Total normalised quality loss (TNQL) and Multiple S/N ratios (MSNR)Experimentno.ABCDTNQLMSNR(dB)111110.88980.5073212220.81360.8958313330.82080.8578421230.68031.5598522310.82430.8389623120.91190.4007731320.74931.2534832130.73021.3657933210.88590.5260Mean of multiple S/N ratios of allexperimental runs (m)0.9117A. Kumar Dubey, V. Yadava / Optics & Laser Technology 40 (2008) 562570567of factor effect at different levels on multiple qualitycharacteristics (KW and MRR) is shown in Fig. 2. A betterfeel for the relative effect of the different factors can beobtained by the decomposition of the variance, which iscommonly called ANOVA. It is a computational techniqueto estimate quantitatively the relative significance (F-ratio),and also the percentage contribution of each factor onquality characteristics. The ANOVA given in Table 10,shows the percentage contribution of different controlfactors on multiple quality characteristics (KW and MRR)in increasing order as: pulse frequency (3.2545%), oxygenpressure (8.0840%), pulse width (28.0865%), and cuttingspeed (57.3208%).Conducting a verification experiment is a crucial finalstep of a robust design. Its purpose is to verify that theoptimum conditions suggested by the matrix experiment doindeed give the projected improvement. The confirmationexperiment is performed by conducting a test with optimalsettings of the factors and levels previously calculated. Thepredicted value of MSNR and that from confirmation testare shown in Table 11. The improvement in MSNR at theoptimum level is found to be 1.3090dB. The value of KW(mm) and MRR (mg/min) at this optimum level are0.3733mm and 124.1095mg/min against the initial processparameter setting of 0.3900mm and 44.9375mg/min.5.2. Multi-objective optimisation results using hybridapproachThe optimum parameter level for each control factor asevaluated from the multi-objective optimisation usingTaguchi method is used as a centre value in RSM. Furtherexperiments are conducted to obtain the KW and MRR ineach experimental run using experimental layout as perCCRD (Table 4). The mathematical model developed forKWandMRRareshowninEqs.(12)and(13),respectively. From the developed models, it is clear thatthe pulse width, cutting speed, square effect of pulse width,and interaction effect of pulse frequency and cutting speedare the significant factors for KW because the absolutevalue of corresponding coefficients for these terms are quiteARTICLE IN PRESSTable 9Multiple S/N response (average factor effect at different levels)SymbolMean of multiple S/N ratios (dB)FactorsLevel 1Level 2Level 3AGas pressure0.75360.93311.0484?BPulse width1.1068?1.03350.5948CPulse frequency0.75790.9939?0.9834DCutting speed0.47800.99601.2548?Optimum level.0234 Gas pressure Pulse width Pulse frequency Cutting speedMultiple S/N ratio (dB) 1.51.00.50.01Factor LevelFig. 2. Effect of control factors on multiple S/N ratio.Table 10Results of ANOVA for KW and MRRSymbolFactorsDegrees offreedomSum of squaresMean squaresFContribution (%)AGas pressure20.1324#0.06621.10798.0840BPulse width20.46000.23003.849428.0865CPulse frequency20.1066#0.0533?3.2545DCutting speed20.93880.46947.856157.3208ErrorPooled error40.23900.0598Total81.6378100#Pooled factor.Table 11Results of confirmation experiment using Taguchi methodOptimal laser cutting parametersInitialparametersettingPredictionExperimentLevelA1B1C1D1A3B1C2D3A3B1C2D3KW (mm)0.39000.3733MRR (mg/min)44.9375124.1094Multiple S/Nratio (dB)0.50731.66881.8163Improvement of S/N ratio 1.3090dB.A. Kumar Dubey, V. Yadava / Optics & Laser Technology 40 (2008) 562570568high in comparison to other terms. Likewise, the MRR issignificantly affected by cutting speed, pulse width, pulsefrequency, and square effect of cutting speed.The simultaneous optimisation of weighted response forKW (weighting factor=0.8) and MRR (weighting fac-tor=0.2) is obtained by using MINITAB software. Themulti-objective optimisation results are shown in Fig. 3.The results show the graphical representation of individualfactor effects at different level on KW and MRR, andoptimum parameter level has been suggested for minimumKW and maximum MRR. The composite desirability Dand individual desirability d (which depend on weightingfactor and nature of quality characteristics) are also shownin result. The predicted optimal values of KW and MRR inmulti-objectiveoptimisationare0.3172mmand165.9521mg/min,respectively,atassistgaspressur-e 3.5051kg/cm2, pulse width 0.60ms, pulse frequen-cy 28Hz,andcuttingspeed 125mm/min.Theconfirmation test at predicted optimum parameter settinggives KW 0.3267mm and MRR 169.1667mg/min.The optimum quality values of KW and MRR obtainedfrom Taguchi approach and that of hybrid approach havebeen compared in Table 12. The results show that both thequalities have been improved considerably when hybridapproach is applied.6. ConclusionsA hybrid TMRSM approach has been used for multi-objective optimisation of LBC of thin sheet of high silicon-alloy steel. The hybrid approach gives better quality resultsas compared to only Taguchi approach. Based on themodelling and optimisation results, the following conclu-sions can be drawn.(1) The optimum value of KW and MRR obtained frommulti-objective optimisation using Taguchi methodonly are 0.3733mm and 124.1095mg/min, respectivelywhile using the hybrid approach these values are0.3267mm and 169.1667mg/min, respectively. Hencea considerable improvement for both quality charac-teristics has been found with hybrid approach ofTMRSM.(2) The developed response surface model for KW andMRR has been found adequate. It has also been foundthat the linear parameters are significant for both themodels.(3) Pulse width, cutting speed, square effect of pulse width,and interaction effect of pulse frequency and cuttingspeed have been obtained as significant factors for KW.The MRR has been found to be significantly affectedby cutting speed, pulse width, pulse frequency, andsquare effect of cutting speed.AcknowledgementFinancial assistance for this work was granted by theDepartment of Science and Technology (DST), Govern-ment of India, through project no. SR/S3/MERC-0076/2006 entitled Experimental and Numerical Study ofARTICLE IN PRESSHiLo0.84864DOptimalCurd = 0.79803MinimumKerf widd = 0.90247MaximumMRRy = 0.3172y = 165.952125.0125.020.028.00.601.402.504.50Pulse wiPulse frCutting Oxygen p3.50510.6028.0125.0Fig. 3. MINITAB results of multi-objective optimisation using hybrid approach. D, composite desirability; d, individual desirability; Hi, highestparameter values; Lo, lowest parameter values; Cur, current or optimum values; oxygen p, gas (oxygen) pressure; Pulse wi, pulse width; Pulse fr, pulsefrequency; cutting, cutting speed; Kerf wid, Kerf width.Table 12Comparison of results of Taguchi approach and hybrid
- 温馨提示:
1: 本站所有资源如无特殊说明,都需要本地电脑安装OFFICE2007和PDF阅读器。图纸软件为CAD,CAXA,PROE,UG,SolidWorks等.压缩文件请下载最新的WinRAR软件解压。
2: 本站的文档不包含任何第三方提供的附件图纸等,如果需要附件,请联系上传者。文件的所有权益归上传用户所有。
3.本站RAR压缩包中若带图纸,网页内容里面会有图纸预览,若没有图纸预览就没有图纸。
4. 未经权益所有人同意不得将文件中的内容挪作商业或盈利用途。
5. 人人文库网仅提供信息存储空间,仅对用户上传内容的表现方式做保护处理,对用户上传分享的文档内容本身不做任何修改或编辑,并不能对任何下载内容负责。
6. 下载文件中如有侵权或不适当内容,请与我们联系,我们立即纠正。
7. 本站不保证下载资源的准确性、安全性和完整性, 同时也不承担用户因使用这些下载资源对自己和他人造成任何形式的伤害或损失。

人人文库网所有资源均是用户自行上传分享,仅供网友学习交流,未经上传用户书面授权,请勿作他用。