二柱大采高掩护式液压支架设计
84页 32000字数+说明书+任务书+外文翻译+6张CAD图纸【详情如下】
二柱大采高掩护式液压支架设计说明书.doc
任务书和摘要.doc
后连杆.DWG
外文翻译--自移式液压支架.doc
底座.dwg
总装图.dwg
摘要及目录.doc
液压系统原理图.DWG
立柱.dwg
顶梁.DWG

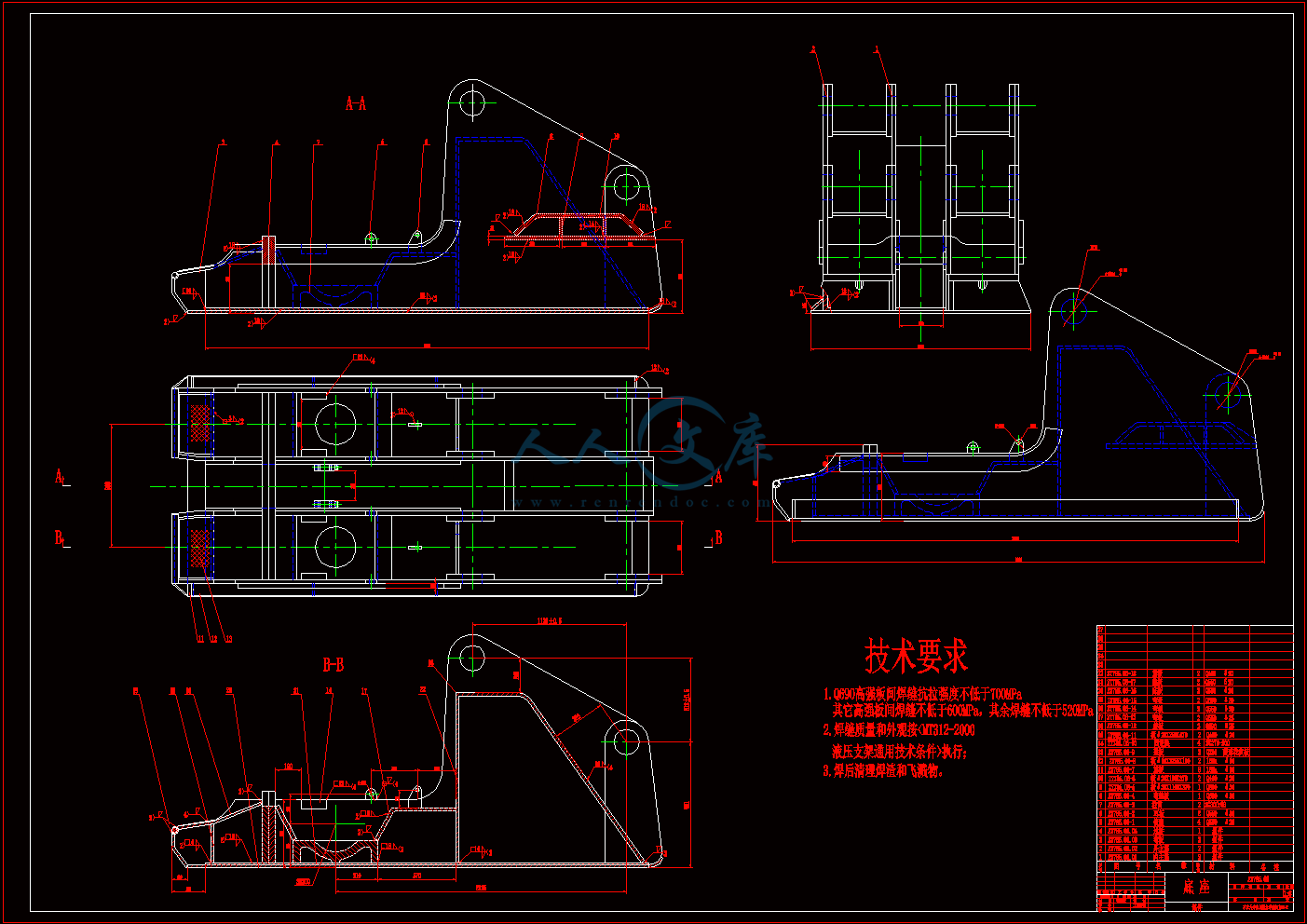



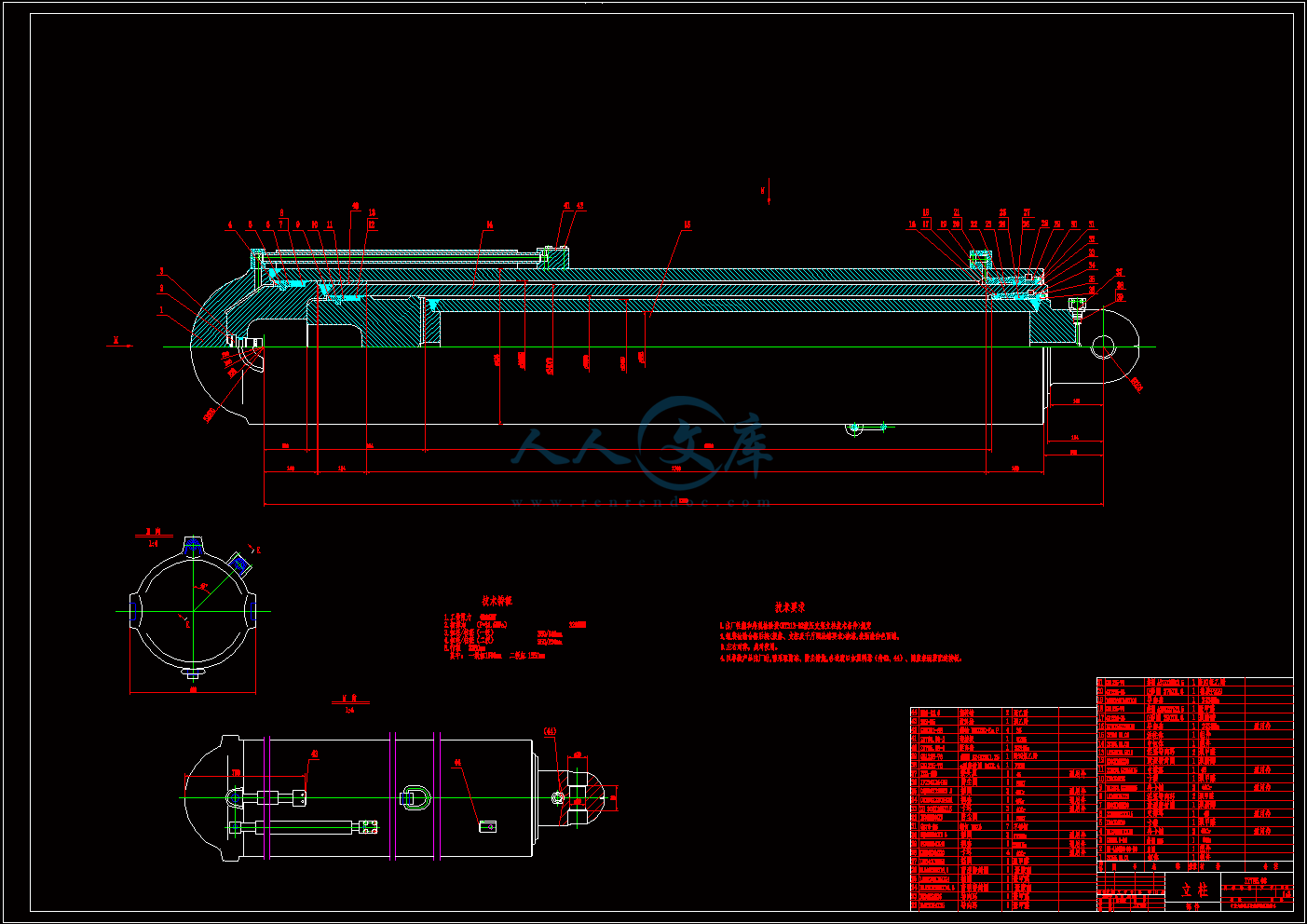
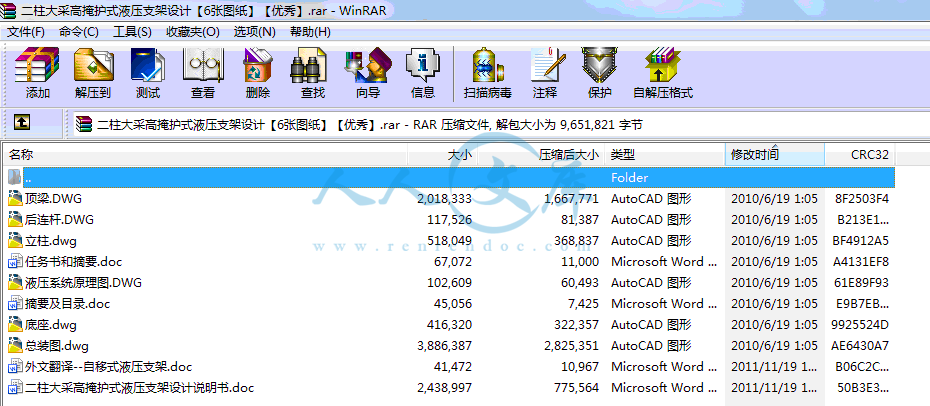

目 录
1序论1
1.1液压支架的用途1
1.2液压支架的工作原理1
1.3液压支架的设计目的、要求和基本参数 2
1.3.1设计目的2
1.3.2 对液压支架的基本要求3
1.3.3 设计支架必需的基本参数3
1.4液压支架的分类3
1. 5 液压支架的主要结构件及其用途4
1.5.1顶梁4
1.5.2底座4
1.5.3掩护梁4
1.5.4活动侧护板5
1.5.5连杆5
1. 6液压支架的液压系统5
1.6.1液压支架传动系统的基本要求 5
1.6.2液压支架的液压传动特点 5
1.7液压支架的选型 6
1.8液压支架的设计动向 7
2液压支架的结构设计7
2.1 液压支架的主要尺寸的确定 7
2.1.1支架高度和伸缩比7
2.1.2支架间距8
2.1.3底座长度8
2.1.4顶梁长度的确定8
2.1.5立柱布置 10
2.1.6通风断面的计算 10
2.2各部件结构选择11
2.2.1顶梁 11
2.2.2底座 13
2.2.3立柱 14
2.2.4推移千斤顶 15
2.2.5平衡千斤顶 16
2.2.5侧推千斤顶 16
2.3液压支架基本技术参数的确定16
2.3.1支护面积 16
2.3.2支护强度与工作阻力17
2.3.3确定立柱的技术参数 17
2.3.4立柱的初撑力与泵站的额定工作压力 18
2.3.5安全阀压力和立柱工作阻力的确定 18
2.3.6推移千斤顶 18
2.3.7平衡千斤顶 19
3液压支架的受力分析21
3.1概述 22
3.1.1液压支架工作状态 22
3.1.2计算载荷的确定 22
3.2液压支架的受力分析23
3.3顶梁载荷分布28
3.4支护强度计算29
3.5底座接触比压计算30
3.6支护效率34
3.7支架受力的影响因素34
4液压支架的强度条件36
4.1强度条件36
4.2液压支架的强度校核37
4.2.1顶梁强度校核 37
4.2.2底座强度校核 43
4.2.3 顶梁上平衡千斤顶耳板的强度校核 47
4.2.4 掩护梁的强度校核 48
4.2.5 平衡千斤的强度校核 53
4.2.6 立柱强度校核 54
4.2.7 前连杆强度校核及对应销轴 61
4.2.8 后连杆强度校核及对应销轴 63
5 液压支架的液压系统 64
5.1立柱和千斤顶65
5.2支架液压阀66
5.2.1液控单向阀66
5.2.2安全阀66
5.2.3操纵阀67
5.3液压支架液压原理图67
5.4液压支架的控制方式67
5.4.1手动控制67
5.4.2自动控制68
5.5液压系统安装、调试、保养68
5.5.1安装68
5.5.2调试74
5.5.3保养75
结论77
参考文献78
翻译部分
英文原文79
中文译文83
致谢87
摘 要
本课题的研究内容是掩护式液压支架的总体设计。
液压支架作为回采工作面的一种支护设备,液压支架在工作过程中能否取得良好的支护效果,取决于支架的架型,结构和相关参数。首先,通过几何做图法进行四连杆机构优化设计来确定支架的四连杆机构各杆系的长度;然后,通过三维软件3DMAX来进行实体建模,并进行了动画仿真和简单的有限元分析;其次,以力学模型为依据,分析了液压支架的顶梁、掩护梁上载荷的作用机理,得到了较为合理的支架载荷的计算公式;再次,结合本次设计的支架,从平面和空间两方面对支架主要结构件进行受力分析;最后对支架主要结构件、连接销轴、连接耳板进行强度效核。
在完成本设计的过程中,利用理论分析的同时,也采用了许多实际经验,做到理论与实践相结合。
关键词:掩护式支架;四连杆;优化设计;力学特征;强度
ABSTRACT
he paper mainly foused on the problem which is design out a type of shield support.
The hydraulic support described is a part of the mining industry equipment in the mine, used for protection of working environment in the gallery. It works well or bad at work basing on its support mode, frame and some parameters. In the first step, the optimal values of some parameters of the leading four-bar mechanism are determined by using geometric sketch. Secondly, the model is founded with the three-dimensional software,3DMAX, and also do the Simulink, SimMechanics and simple analysis. Then on the base of mechanic model of support-surrounding, the mechanism and loads on the support is decided. The next work, with the condition of the design, the main mechanics of hydraulic support is analyzed and calculated by plane and spatial model. Finally, the under frame, top beam cave shield, wrists and hydraulic column are analyzed by calculation. And draw out all the process drawings.
During the course of doing the paper, author not only analyses something theoretical, but also adopted a lot of actual experiences. Combining theory and practice. Therefore, the paper possesses theory and practical value, so it measures up the requiring of the nation to the undergraduate.
Key words: shield hydraulic support; four-bar links; optimal design; mechanics characteristics; strength
液压支架的液压传动,与其他机械的容积式液压传动有很大的区别,其特点如下:
工作液的压力高(管路内的压力达20~40MPa,立柱内的压力达30~70MPa),流量大(30~150l/min);
在液压系统中,采用粘度低和容量大的液体为工作介质;
液压缸、操纵阀,其他调节和控制装置等总的数量大(高压泵1~6台,液压缸300~1500个,安全阀150~300个,还有同样数量的液控单向阀);
很长的液压管路(200~300m刚性管,500~3000m高压软管);
泵——液压缸传动系统的换算弹性模数较低;
根据支架的数目改变液流的参数;
所有支架在结构上都有着相同的液压缸、液压装置以及他们之间都有相同的连接方式(相同的液压系统);
每节支架都重复着相同的工序,这些工序的总和构成液压支架的基本工序; 2 液压支架的结构设计
2.1 液压支架的主要尺寸的确定
2.1.1 支架高度和伸缩比
由设计要求已知:
支架的最大高度
Hm=5.5m
支架最小高度
Hn=2.55m
支架伸缩比
m===2.16
2.1.2 支架间距
支架间距就是指相邻支架中心线间的距离,按下式计算
= +n
式中 —支架间距(支架中心距)