资源目录
压缩包内文档预览:(预览前20页/共59页)
编号:422422
类型:共享资源
大小:922.63KB
格式:RAR
上传时间:2015-04-03
上传人:上***
认证信息
个人认证
高**(实名认证)
江苏
IP属地:江苏
39
积分
- 关 键 词:
-
箱体
钻孔
组合机床
设计
图纸
钻孔组合机床
箱体钻孔
- 资源描述:
-
箱体钻孔组合机床设计
57页 29000字数+说明书+文献综述+4张CAD图纸【详情如下】
主轴箱展开图.dwg
总图.dwg
机床尺寸联系图.dwg
箱体图.dwg
箱体钻孔组合机床设计文献综述.doc
箱体钻孔组合机床设计说明书.doc
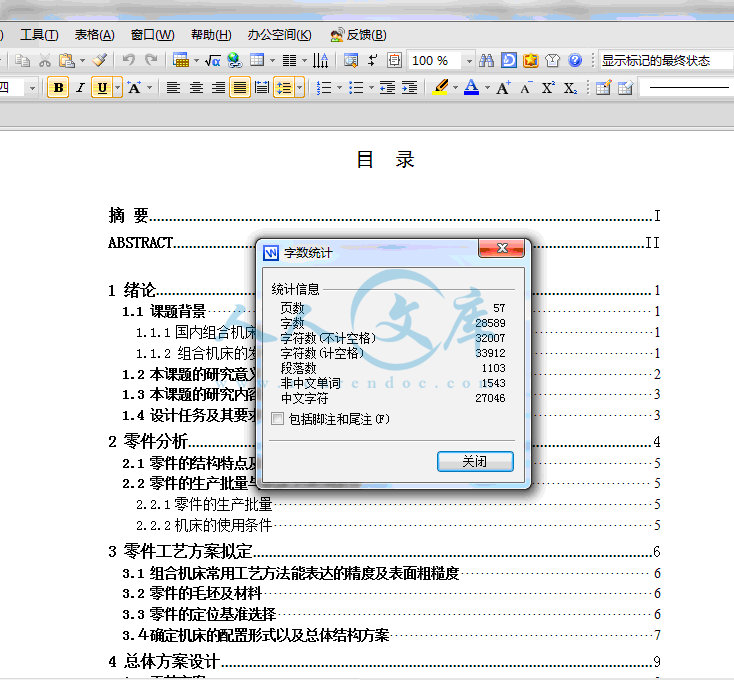
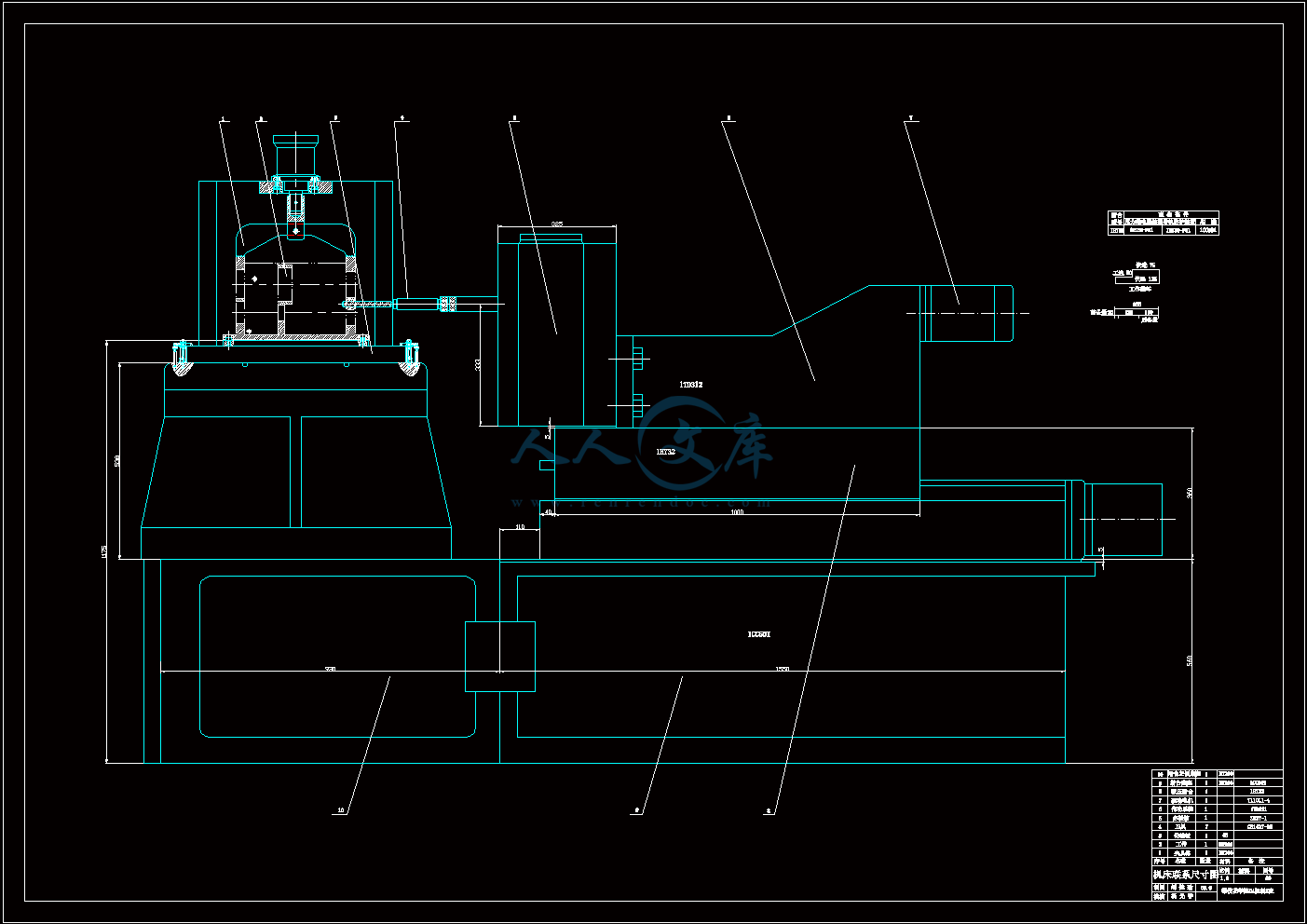



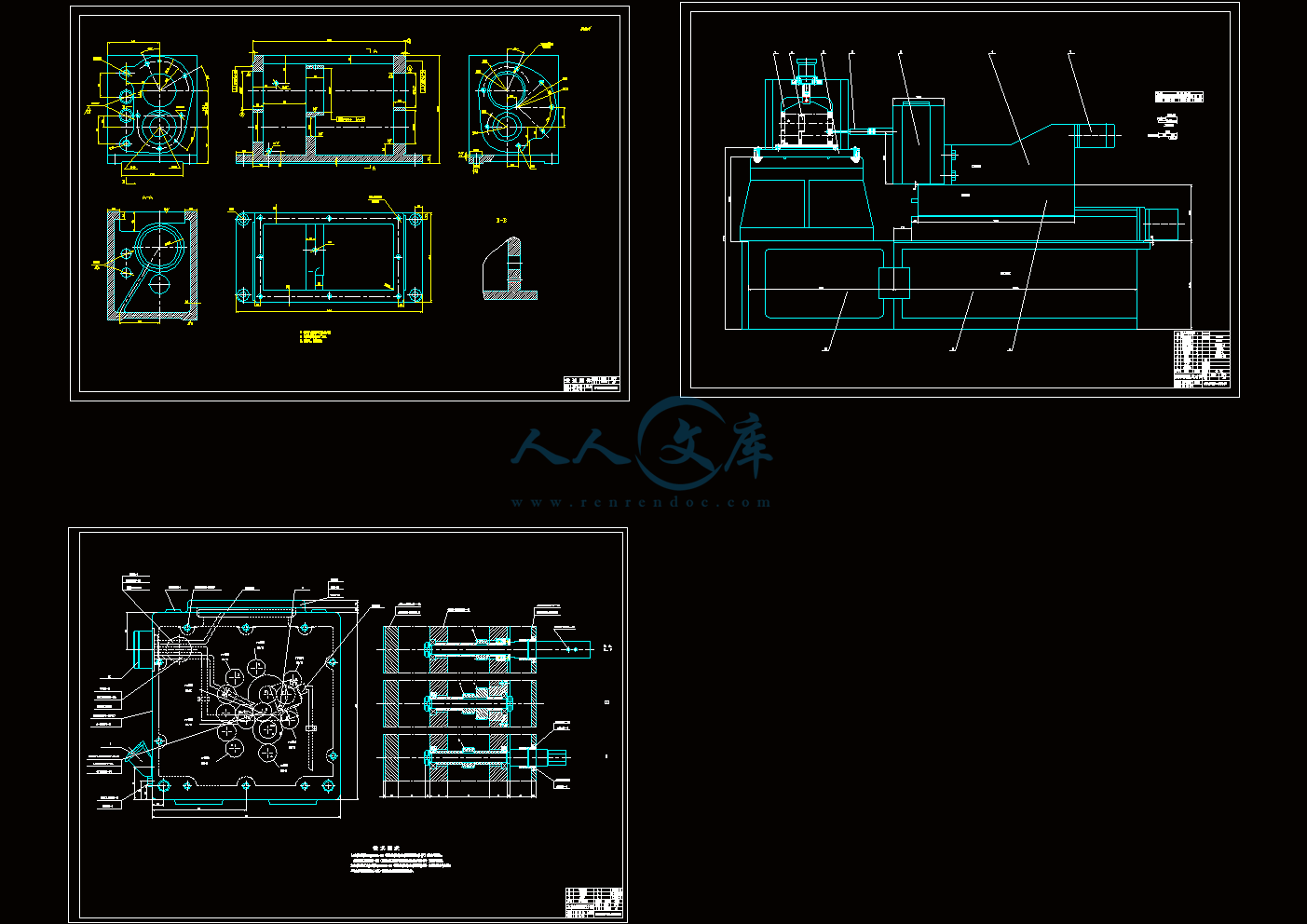
目 录
摘 要I
ABSTRACTII
1 绪论1
1.1 课题背景1
1.1.1国内组合机床的发展现状1
1.1.2 组合机床的发展趋势1
1.2 本课题的研究意义2
1.3 本课题的研究内容3
1.4 设计任务及其要求3
2 零件分析4
2.1 零件的结构特点及其技术要求5
2.2 零件的生产批量与机床的使用条件5
2.2.1零件的生产批量5
2.2.2机床的使用条件5
3 零件工艺方案拟定6
3.1 组合机床常用工艺方法能表达的精度及表面粗糙度6
3.2 零件的毛坯及材料6
3.3 零件的定位基准选择6
3.4确定机床的配置形式以及总体结构方案7
4 总体方案设计9
4.1 工艺方案9
4.2 总体方案9
5 组合机床设计——三图一卡设计11
5.1 被加工零件图11
5.2 零件加工示意图12
5.2.1示意图上应标注的内容12
5.2.2绘制加工示意图及绘制之前的有关计算12
5.3 机床联系尺寸图19
5.3.1选用动力部件20
5.3.2确定装料高度22
5.3.3初步确定夹具轮廓尺寸22
5.3.4底座轮廓尺寸22
5.3.5初步确定多轴箱轮廓尺寸23
5.3.6机床联系尺寸图的画法和步骤24
5.4 机床生产率计算卡25
5.4.1理想生产率Q25
5.4.2实际生产率Q126
5.4.3机床负荷率27
5.4.4生产率计算卡27
6 多轴箱设计30
6.1 多轴箱的通用零件30
6.2 多轴箱设计33
6.2.1绘制多轴箱设计原始依据图33
6.2.2确定主轴结构型式及齿轮模数34
6.2.3多轴箱的传动系统设计34
6.2.4多轴箱的传动系统设计41
7 夹具设计44
7.1 机床夹具概论44
7.2 问题的提出45
7.3 夹具设计45
7.4 夹具设计及操作的简要说明47
结论48
参考文献49
致 谢50
摘 要
机械制造业是一个国家经济发展的重要支柱。而制造业的生产能力主要取决于制造装备——机床的先进程度。组合机床兼有低成本和高效率的优点,在大批、大量生产中得到广泛应用,并可用以组成自动生产线。
本文对箱体螺纹孔的加工工艺进行了详细的分析,对其孔的加工提出了“一次装夹,单工位加工,达到产品图样的精度要求”的思路,并根据这一思想设计了七轴头单工位钻孔组合机床。
该组合机床由立柱、立柱底座、中间底座、液压滑台、动力箱、多轴箱等组成。本文对各部分的设计进行了详细的计算和论证。
关键词 组合机床,变速箱体,钻孔
ABSTRACT
The machinery Manufacture is an important pillar of economic development in a country. While the capability of production in trade of manufacture mostly depends on the advanced producing equipment-machine tool. modular machine tools have advantages of high efficiency and low cost. It is widely used in large batch production and can be consisted automatic production line.
This paper analyzes gear box casing of threading holes of a disc. The idea is once clamping the work. The accuracy can be satisfied the demand of drawing. According above idea, the 7-spindle modular machine tool has been drilled.
This paper presents the design and calculating of each part of this machine tool.
Key words Modular machine tool, gear box casing,drilling
- 内容简介:
-
攀枝花学院Panzhihua University本科毕业设计(论文)文献综述院 (系): 机 电 工 程 学 院 专 业: 机械设计制造及其自动化 班 级: 2004机制2班 学生姓名: 刘 艳 瑜 学 号: 200410627116 2008 年 3 月 25 日本科生毕业设计(论文)文献综述评价表毕业设计(论文)题目箱体钻孔组合机床的设计综述名称箱体钻孔组合机床设计文献综述评阅教师姓名杨 光 春职称高级工程师评 价 项 目优良合格不合格综述结构01文献综述结构完整、符合格式规范综述内容02能准确如实地阐述参考文献作者的论点和实验结果03文字通顺、精练、可读性和实用性强04反映题目所在知识领域内的新动态、新趋势、新水平、新原理、新技术等参考文献05中、英文参考文献的类型和数量符合规定要求,格式符合规范06围绕所选毕业设计(论文)题目搜集文献成绩综合评语: 评阅教师(签字): 年 月 日文献综述:箱体钻孔组合机床设计文献综述1 本课题的研究意义,国内外研究现状,水平和发展趋势组合机床是以通用部件为基础,配以按工件特定外形和加工工艺设计的专用部件和夹具,组成的半自动或自动专用机床。 组合机床一般采用多轴、多刀、多工序、多面或多工位同时加工的方式,生产效率比通用机床高几倍至几十倍。由于通用部件已经标准化和系列化,可根据需要灵活配置,能缩短设计和制造周期。因此,组合机床兼有低成本和高效率的优点,在大批、大量生产中得到广泛应用,并可用以组成自动生产线。 组合机床一般用于加工箱体类或非凡外形的零件。加工时,工件一般不旋转,由刀具的旋转运动和刀具与工件的相对进给运动,来实现钻孔、扩孔、锪孔、铰孔、镗孔、铣削平面、切削内外螺纹以及加工外圆和端面等。有的组合机床采用车削头夹持工件使之旋转,由刀具作进给运动,也可实现某些回转体类零件(如飞轮、汽车后桥半轴等)的外圆和端面加工。 二十世纪70年代以来,随着可转位刀具、密齿铣刀、镗孔尺寸自动检测和刀具自动补偿技术的发展,组合机床的加工精度也有所提高。铣削平面的平面度可达0.05毫米1000毫米,表面粗糙度可低达2.50.63微米;镗孔精度可达IT76级,孔距精度可达O.03O.02微米。 专用机床是随着汽车工业的兴起而发展起来的。在专用机床中某些部件因重复使用,逐步发展成为通用部件,因而产生了组合机床。 最早的组合机床是1911年在美国制成的,用于加工汽车零件。初期,各机床制造厂都有各自的通用部件标准。为了提高不同制造厂的通用部件的互换性,便于用户使用和维修,1953年美国福特汽车公司和通用汽车公司与美国机床制造厂协商,确定了组合机床通用部件标准化的原则,即严格规定各部件间的联系尺寸,但对部件结构未作规定。 通用部件按功能可分为动力部件、支承部件、输送部件、控制部件和辅助部件五类。动力部件是为组合机床提供主运动和进给运动的部件。主要有动力箱、切削头和动力滑台。 支承部件是用以安装动力滑台、带有进给机构的切削头或夹具等的部件,有侧底座、中间底座、支架、可调支架、立柱和立柱底座等。 输送部件是用以输送工件或主轴箱至加工工位的部件,主要有分度回转工作台、环形分度回转工作台、分度鼓轮和往复移动工作台等。 控制部件是用以控制机床的自动工作循环的部件,有液压站、电气柜和操纵台等。辅助部件有润滑装置、冷却装置和排屑装置等。 为了使组合机床能在中小批量生产中得到应用,往往需要应用成组技术,把结构和工艺相似的零件集中在一台组合机床上加工,以提高机床的利用率。这类机床常见的有两种,可换主轴箱式组合机床和转塔式组合机床。 在科学技术飞速发展的今天,先进组合机床的生产技术亦日新月异,主要有以下发展趋势:1组合机床品种的发展重点在组合机床这类专用机床中,回转式多工位组合机床和自动线占有很重要的地位。因为这两类机床可以把工件的许多加工工序分配到多个加工工位上,并同时能从多个方向对工件的几个面进行加工,此外,还可以通过转位夹具(在回转工作台机床上)或通过转位、翻转装置(在自动线上)实现工件的五面加工或全部加工,因而具有很高的自动化程度和生产效率,被汽车、摩托车和压缩机等工业部门所采用。 根据有关统计资料,德国在19901992年期间,回转式多工位组合机床和自动线的产量约各占组合机床总数的50%左右。应指出,回转式多工位组合机床实际上是一种特殊型式的小型自动线,适合于加工轮廓尺寸250mm的中小件。与自动线相比,在加工同一种工件的情况下,回转式多工位组合机床所占作业面积要比自动线约小2/3。2自动线节拍时间进一步缩短目前,以大批量生产为特征的轿车和轻型载货车,其发动机的年产量通常为60万台左右,实现这样大的批量生产,回转式多工位组合机床和自动线在三班运行的情况下,其节拍时间一般为2030秒,当零件生产批量更大时,机床的节拍时间还要更短些(表1)。在70年代,自动线要实现这样短的节拍,往往要采用并列的双工位或设置双线的办法,即对决定自动线节拍的、工序时间最长的加工工序要通过并联两个相同的加工工位,如果限制性工序较多时,则通过采用两条相同的自动线来平衡自动线系统的加工节拍。显然,这样就要增加设备投资和作业面积。缩短基本时间的主要途径是采用新的刀具材料和新颖刀具,以通过提高切削速度和进给速度来缩短基本时间。缩短辅助时间主要是缩短包括工件输送、加工模块快速引进以及加工模块由快进转换为工进后至刀具切入工件所花的时间。为缩短这部分空行程时间,普遍采用提高工件(工件直接输送)或随行夹具的输送速度和加工模块的快速移动速度。3组合机床柔性化进展迅速十多年来,作为组合机床重要用户的汽车工业,为迎合人们个性化需求,汽车变型品种日益增多,以多品种展开竞争已成为汽车市场竞争的特点之一,这使组合机床制造业面临着变型多品种生产的挑战。为适应多品种生产,传统以加工单一品种的刚性组合机床和自动线必须提高其柔性。在70年代,数控系统的可靠性有了很大的提高,故到70年代末和80年代初,像Alfing、Hller-Hille和Ex-cell-o等公司相继开发出数控加工模块和柔性自动线(FTL),从此数控组合机床和柔性自动线逐年增多。在1988年至1992年间,日本组合机床和自动线(包括部分其它形式的专用机床)产量的数控化率已达32%39%,产值数控比率达35%51%;德国组合机床和自动线产量的数控化率为18%62%,产值数控化率达45%66%(表2)。这些数字表明,近十年来,组合机床的数控化发展是十分迅速的。应指出,进入90年代以来,汽车市场竞争更趋激烈,产品市场寿命进一步缩短,新车型的开发周期日益缩短(目前一般为35个月),汽车品种不断增多,因而汽车工业对柔性自动化技术装备的需求量日益增多。如日本丰田汽车公司,在本世纪末的目标是公司下属工厂的柔性化加工系统的普及率达到100%。很显然,组合机床及其自动线在保持其高生产效率的条件下,进一步提高其柔性就愈来愈具有重要意义。4加工精度日益提高特别自80年代中期以来,汽车制造业为增强其汽车的竞争力,不断地加严其发动机关键件的制造公差,并通过计算机辅助测量和分析方法,以及通过设备能力检验来提高其产品的质量。目前,在验收组合机床和自动线时,已普遍要求设备的工序能力系数要大于1.33,有的甚至要求工序能力系数要大于1.67,以便确保稳定的加工精度。应指出,采用Cp1.33来验收设备,这实际上是加严了工件的制造公差,即工件的实际加工公差仅为工件给定公差的1/31/2,这无疑是对组合机床和自动线提出了更高的要求。组合机床制造厂为了满足用户对工件加工精度的高要求,除了进一步提高主轴部件、镗杆、夹具(包括镗模)的精度,采用新的专用刀具,优化切削工艺过程,采用刀具尺寸测量控制系统和控制机床及工件的热变形等一系列措施外,目前,空心工具锥柄(HSK)和过程统计质量控制(SPC)的应用已成为自动线提高和监控加工精度的新的重要技术手段。空心工具锥柄是一种采用径向(锥面)和轴向(端面)双向定位的新颖工具,其优点是具有较高的抗弯刚度、扭转刚度和很高的重复精度。在机床上采用空心锥柄的镗刀,就可使用预调的刀具加工出IT7/IT6精密孔。SPC是基于工序能力的用于监控工件加工质量的一种方法。目前,在自动线上这种质量保证系统愈来愈多地被用来对整个生产过程中的加工质量进行连续监控。5综合自动化程度日益提高近十年来,为进一步提高工件的加工精度和减少工件在生产过程中的中间储存、搬运以及缩短生产流程时间,将工件加工流程中的一些非切削加工工序(如工序间的清洗、测量、装配和试漏等)集成到自动线或自动线组成的生产系统中,以实现工件加工、表面处理、测量和装配等工序的综合自动化。6自动线可靠性和利用率不断改善和提高自动线的经济性只有在其进行连续生产的情况下才有可能实现。为提高自动线加工过程的可靠性、利用率和工件的加工质量,目前在自动线上愈来愈多的采用过程监控,对其各组成设备的功能、加工过程和工件加工质量进行监控,以便快速识别故障、快速进行故障诊断和早期预报加工偏差,使操作人员和维修人员能及时地进行干预,以缩短设备调试周期、减少设备停机时间和避免加工质量偏差。显然,提高自动线的利用率和工件加工质量是生产控制和监控的主要目的。从目前自动线生产控制和监控的内容看,生产控制和监控系统基本上是由质量监控系统、自动线运行控制与监控系统和刀具监控系统这几个部分组成的。近年来,质量监控已日益成为现代自动线生产监控的重要一环。这主要是由于汽车工业不断提高发动机质量的缘故。各汽车制造厂普遍要求将零件的设计公差带压缩1/31/2作为工序公差,对机床能力系数提出了很高的要求。为此,自动线制造厂为确保设备具有稳定的加工质量,已日益重视应用SPC对自动线的生产过程进行连续监控,对加工质量偏差的趋向进行早期预报,以便把工件的加工公差始终控制在预定的范围内。现代自动线的过程控制和监控不仅包含对变得愈来愈复杂的自动线的过程控制和对所有终点开关、电动机保护开关、节拍时间、冷却和润滑液的供给以及液压、气动功能等进行监控和诊断,而且还包括对刀具耐用度、设备维修间隔和工件计数等进行管理,并通过一些直观的过程图形显示、操作指引、故障报警和诊断指示,使操作人员更便于监控整个自动线的生产过程。7、其它技术的应用动向在工业发达国家的组合机床行业中,下列技术得到了较为广泛的应用。组合机床设计普及CAD技术:在国外许多公司中,组合机床设计已普遍采用CAD工作站,在设计室几乎很难见到传统的绘图板。CAD除应用于绘图工作外,并在构件的刚度分析(有限元方法)、组合机床及自动线设计方案比较和选择,以及方案报价等方面均已得到广泛应用,从而显著地提高了设计质量和缩短了设计周期。加之国外许多公司在组合机床和自动线组成模块方面的系列化和通用化程度很高(一般达90%以上),使组合机床和自动线的交货期进一步缩短。推行并行工程:近十年来,为缩短汽车开发周期、降低制造费用和提高产品质量,世界上许多汽车厂都在积极推行日本丰田汽车公司首创的精益生产方式(LeanProduction)。旨在从整体优化的观点合理配置和利用企业拥有的生产要素,以达到高速、高效、高质量和低成本地开发制造汽车,促使企业获得更高的综合效益。2 本课题的基本内容,预计可能遇到的困难,提出解决问题的方法和措施本课题基本内容是箱体钻孔组合机床的设计,要研究的主要内容有:1)设计开始的过程中,我们应该认真分析零件图,了解箱体的结构特点和相关的技术要求,对其钻孔的每一个细节,都应仔细的分析,如孔系之间的位置精度、同轴度、平行度,孔的粗糙度等,特别是要注意各孔系自身精度(同轴度、圆度、粗糙度)和它们的相互位置精度(轴线之间的平行度、垂直度以及轴线与平面之间的平行度、垂直度等要求),箱体的个孔的尺寸是整个设计加工的关键,必须弄懂其每个尺寸的意义。我们采用AutoCAD软件绘制零件图,一方面增加对零件的了解认识,另一方面增加我们对AutoCAD软件的熟悉。2)箱体钻孔组合机床的设计过程是整个设计的重点内容,在设计过程中,我们必须严格的计算加工时的切削用量、主轴进给量、以及主轴转速,我们还得认真的选择床身、支撑架等的型号,这个阶段内容较多,设计的范围也比较广,为了设计的参数合理,我们必须广泛查阅相关的书籍,达到设计的合理性和实用性。3)为了工件加工时定位准确和加紧的快速,提高效率和降低工人的劳动强度,提高零件钻孔加工精度和安装找正方便,我们要采用专用的钻孔夹具。在夹具设计过程中,我们统一采用以底面为主要定位面来进行加工。因为我们未学习过夹具的设计和计算。所以工作量大大的增加了,只有通过在实习过程中对夹具的感性认识和夹具设计参考书以及夹具图册来进行设计和计算。所以,夹具的设计也是整个设计过程的一个难点。夹具的设计必须要保证夹具的定位准确和机构合理,考虑夹具的定位误差和安装误差。我们将通过对工件与夹具的认真分析,结合一些夹具的具体设计事例,查阅相关的夹具设计资料,联系在工厂看到的一些零件加工的夹具来解决这些问题。3 本课题拟采用的研究手段(途径)和可行性分析钻孔组合机床一般用于加工箱体类或非凡外形的零件。加工时,工件一般不旋转,由刀具的旋转运动和刀具与工件的相对进给运动,来实现钻孔、扩孔、锪孔、铰孔、镗孔、切削内外螺纹等。其主轴的转速和进给量直接影响加工的零件的精度及加工质量。本次毕业设计过程中,为了保证形体钻孔的合理性、实用性以及加工精度等要求,我们在图书馆努力收集有关钻孔组合机床的各类资料在箱体钻孔组合机床的设计中作为参考,提高其加工的合理性,同时结合我们在成都内燃机厂和内江峨柴厂对钻孔组合机床的一些认识来提高我们设计的组合机床的实用性。在箱体钻孔组合机床的设计中,我们必须保证其主轴箱中各个主轴的进给量相同,而且必须保证各个主轴的转速的同步性,以及加工时的各切削用量的准确性。经过以上对箱体钻孔组合机床的分析,结合平时老师的讲解及书本知识,本次课题设计将圆满完成。参考文献1 赵如福.金属机械加工工艺人员手册.上海科学技术出版社.19902 张耀宸.机械加工设计手册.航空工业出版社.19873 王先逵.机械制造工艺学.机械工业出版社.20064 李庆余.机械制造设计装备设计.机械工业出版社.20065 肖继德.机床夹具设计.机械工业出版社.20056 机床夹具图册(上、下册).贵州人民出版社.19837 雷天觉.液压工程手册.机械工业出版社.19908 路甬祥.液压气动技术手册.机械工业出版社.20029 谢家瀛.组合机床设计简明手册.机械工业出版社.199210沈阳工业大学.组合机床设计.上海科学技术出版社.198511 Machine Tools N.chernor 1984.12 Machine Tools Netalworking John L.Feirer 197313 Handbook of Machine Tools Manfred weck 1984攀枝花学院本科毕业设计箱体钻孔组合机床设计学生姓名: 学生学号: 院(系): 机电工程学院 年级专业: 2004级机制自动化 指导教师: 助理指导教师: 二八年六月53攀枝花学院毕业设计 摘要摘 要机械制造业是一个国家经济发展的重要支柱。而制造业的生产能力主要取决于制造装备机床的先进程度。组合机床兼有低成本和高效率的优点,在大批、大量生产中得到广泛应用,并可用以组成自动生产线。本文对箱体螺纹孔的加工工艺进行了详细的分析,对其孔的加工提出了“一次装夹,单工位加工,达到产品图样的精度要求”的思路,并根据这一思想设计了七轴头单工位钻孔组合机床。该组合机床由立柱、立柱底座、中间底座、液压滑台、动力箱、多轴箱等组成。本文对各部分的设计进行了详细的计算和论证。关键词 组合机床,变速箱体,钻孔ABSTRACTThe machinery Manufacture is an important pillar of economic development in a country. While the capability of production in trade of manufacture mostly depends on the advanced producing equipmentmachine tool. modular machine tools have advantages of high efficiency and low cost. It is widely used in large batch production and can be consisted automatic production line.This paper analyzes gear box casing of threading holes of a disc. The idea is once clamping the work. The accuracy can be satisfied the demand of drawing. According above idea, the 7-spindle modular machine tool has been drilled. This paper presents the design and calculating of each part of this machine tool.Key words Modular machine tool, gear box casing,drilling攀枝花学院毕业设计 目录目 录摘 要IABSTRACTII1 绪论11.1 课题背景11.1.1国内组合机床的发展现状11.1.2 组合机床的发展趋势11.2 本课题的研究意义21.3 本课题的研究内容31.4 设计任务及其要求32 零件分析42.1 零件的结构特点及其技术要求52.2 零件的生产批量与机床的使用条件52.2.1零件的生产批量52.2.2机床的使用条件53 零件工艺方案拟定63.1 组合机床常用工艺方法能表达的精度及表面粗糙度63.2 零件的毛坯及材料63.3 零件的定位基准选择63.确定机床的配置形式以及总体结构方案74 总体方案设计94.1 工艺方案94.2 总体方案95 组合机床设计三图一卡设计115.1 被加工零件图115.2 零件加工示意图125.2.1示意图上应标注的内容125.2.2绘制加工示意图及绘制之前的有关计算125.3 机床联系尺寸图195.3.1选用动力部件205.3.2确定装料高度225.3.3初步确定夹具轮廓尺寸225.3.4底座轮廓尺寸225.3.5初步确定多轴箱轮廓尺寸235.3.6机床联系尺寸图的画法和步骤245.4 机床生产率计算卡255.4.1理想生产率Q255.4.2实际生产率Q1265.4.3机床负荷率275.4.4生产率计算卡276 多轴箱设计306.1 多轴箱的通用零件306.2 多轴箱设计336.2.1绘制多轴箱设计原始依据图336.2.2确定主轴结构型式及齿轮模数346.2.3多轴箱的传动系统设计346.2.4多轴箱的传动系统设计417 夹具设计447.1 机床夹具概论447.2 问题的提出457.3 夹具设计457.4 夹具设计及操作的简要说明47结论48参考文献49致 谢50攀枝花学院毕业设计 1 绪论1 绪 论1.1 课题背景1.1.1国内组合机床的发展现状近年来,随着数控技术,电子技术,计算机技术的发展,组合机床的服务对象已经由过去的农用机械,载货汽车向以轿车工业为重点的转移,组合机床行业开展了针对轿车零件关键工艺研究开发的科研攻关,采取引进技术,合作生产和自行开发相结合;组合机床也由过去的刚性组合机床向具有一定柔性,可实现多品种加工方向的变化,先后开发了转塔组合机床,主轴移动式组合机床,自动更换主轴箱式组合机床,同时又应用数控技术发展了三坐标加工单元等数控组合机床,把纯刚性的设备变为具有一定柔性,可变可调的装备;组合机床的加工精度以过去多完成粗加工,半精加工向精加工方向转化。组合机床行业开发了针对汽车发动机五大件加工的关键工艺设备,使行业在精加工机床的品种上有了较大扩充,为提供成套设备创造了条件;组合机床制造技术由过去的以机加工为主的单机及自动化向综合成套方向转换,加强了相应配套技术与产品的研究开发,行业的已经初步具备了向用户提供自毛坯上线,经机械加工和非机械加工至成品下线的成套技术装备,包括整个车间的切屑和冷却处理系统;组合机床的控制技术由传统的程序控制技术向数控,计算机管理与监控方向发展。组合机床行业企业生产的组合机床的控制技术,已完成了由接触-继电器控制向可编程控制的转变,从而大大的提高了组合机床的可靠性,故障率大为降低;组合机床的开发已经又过去的人工设计转向计算机辅助设计。组合机床行业大力推行CAD,为提高设计速度,保证设计质量,缩短供货周期创造了有利的条件。国内该行业虽然取得了很大的进步与发展,但是,在制造技术高速发展上的今天,由于基础比较薄弱,从整体看,与国外先进水平与国内的用户的要求还存在一定的差距,主要表现在产品的可靠性太差,难以适应大批量生产的需要,可调可变性,柔性较差,缺少必要的适应多种加工的新产品,系统化,通用化,模块化程度底,致使制造周期过长,满足不了用户的要求,科学管理,成本控制水平不高,在市场上缺乏竞争力等不足之处。1.1.2组合机床的发展趋势1高速化:由于机构各组件分工的专业化,在专业主轴厂的开发下,主轴高速化日益普及。过去只用于汽车工业高速化的机种(每分钟1.5万转以上的机种),现在已成为必备的机械产品要件。2 精密化:由于各组件加工的精密化,微米的误差已不是问题。以电脑辅助生产(CAM)系统的发展带动数控控制器的功能越来越多。3 高效能:对机床高速及精密化要求的提高导致了对加工工件制造速度的要求提高。同时,由于产品竞争激烈,产品生命周期缩短,模具的快速加工已成为缩短产品开发时间所必须具备的条件。对制造速度的要求致使加工模具的机床向着高效能专业化机种发展。4系统化:机床已逐渐发展成为系统化产品。现在可以用一台电脑控制一条生产线的作业,不但可缩短产品的开发时间,还可以提高产品的加工精度和产品质量。5复合化:产品外观曲线的复杂化致使模具加工技术必须不断升级,机床五轴加工、六轴加工已日益普及,机床加工的复合化已是不可避免的发展趋势。1.2 本课题的研究意义机床工业是现代工业特别是现代制造业的基础,在国民经济中占有重要的战略地位。对我国而言,机床工业不仅仅具有重要的经济意义,而且还具有重要的国防战略意义。研究机床工业的特点,有助于我们了解机床工业的特殊规律,从而找到适合我国国情的机床工业发展之路。机床工业的发展带动了制造业和工业的发展。对一个国家而言,本土的机床工业与本土的制造业及工业紧密相连,高水平的本土机床工业有助于提升本土制造业及工业的水平。机床工业与一个国家的工业竞争力、制造业发展水平紧密相关,本国的机床工业水平越高,工业和制造业竞争力越强。我国工业竞争力和制造业发展水平不高,一定程度上是与我国机床工业发展水平不高相联系的。加快我国机床工业的发展,提高我国机床工业技术和管理水平,将有利于我国工业和制造业发展。所以对机床的研究设计意义是极其重大的。组合机床的机构简单,生产率和自动化程度高的特点,又具有一定的重新调整能力,组合机床是根据加工工件的需要,以大量系列化,标准化的通用部件为基础,配以少量的专用部件,对一种或数种工件按预先确定的工序进行加工的高效专用机床,它既具有专用机床的结构简单,又能适应工件变化的需要。组合机床有70%80%的通用零,部件,而这些零部件是经过精心设计和长期生产实践考验的,所以工作稳定,可靠;设计时,对于通用的零部件主要是选用,不必重新设计,所以设计周期短;又因为这些通用零部件可以预先制造出来并可成批生产,因此它的制造周期短,并可降低成本;当被加工对象改变时,它的通用部件可以重新利用,组合成新的组合机床,因此有利于产品更新。毕业设计是高等教育体系中非常重要的环节,它可以检验自己对专业知识理解与掌握的程度,也可以提高自己综合运用所学知识的能力,也能在分析问题和解决问题的过程中学到更多新的知识。就我个人而言,我希望能通过这次毕业设计对自己未来将从事的工作进行一次适应性训练,从中锻炼自己分析问题、解决问题的能力,为今后参加祖国的“四化”建设打下一个良好的基础。所以,无论从国家还是就我个人而言,研究组合机床设计是很有必要的。由于能力所限,设计尚有许多不足之处,恳请各位老师给予指导。1.3 本课题的研究内容根据组合机床设计的一般步骤,本课题主要包括组合机床通用部件的选择,主轴箱设计,夹具设计等内容。1.4 设计任务及其要求设计题目所给的是箱体钻孔组合机床设计。其设计任务及其要求有1 在保证满足各项技术要求的前提下,力求结构简单、先进和合理,动作准确可靠,便装拆维修,操作安全可靠;2 设计内容包括:组合机床设计、夹具设计;3 零件尽可能的采用标准件;4 在结构方案和有关尺寸确定后,绘制出装配图和零件图;5 绘制零件图包括结构图形、尺寸、公差、形位公差和表面粗糙度值;尺寸表注要注意基准和完整;必须注明必要的技术要求;6 掌握必要的机械零件的设计和加工工艺的有关知识;7 熟悉机械制图、配合与公差、机械原理、金属材料等方面的有关知识。攀枝花学院毕业设计 2 零件分析2 零件分析变速器在汽车等领域被广泛运用,是重要的箱体零件之一。变速箱体是变速器的主要零件之一,在工作过程中直接起支撑的作用,所以对其刚度和硬度等力学性能都有较高要求。图2.1 箱体零件图2.1 零件的结构特点及其技术要求被加工零件为变速箱体 (见图2.1),其材料为铸钢HT200,常温下的力学性能200MPa,属于脆性材料,塑性和韧性差,不能锻造和冲压,焊接性很差,流动性好,可切削性好,用于承受中等负荷重要件。加工部位及其要求:在端面上加工5个M10螺孔的底孔,2个M16螺纹的底孔。表面粗糙度Ra为32。2.2 零件的生产批量与机床的使用条件2.2.1零件的生产批量生产纲领(考虑废品及备品率)年产量3万件,单班制生产。零件的生产批量是决定采用单工位,多工位或自动线,还是按中小批量设计组合机床的重要因素,被加工零件的生产批量越大,工序安排一般趋于分散,而且其粗、精加工应分别在不同的机床上完成,以保证加工精度,但对于中小批量生产的情况,则力求减少机床台数,此时应将工序尽量集中在一台或少数几台机床上进行,以提高机床的利用率,本课题要求年产量为3万件,结合实际情况,考虑零件的大小,形状,应属于中小批量的生产规模,所以宜采用组合机床。2.2.2机床的使用条件机床总体设计,在考虑达到技术性能指标的同时,必须注意机床操作者的生理和心理特征,成分发挥人和机床的各自特点,达到人机最佳综合功效。机床各部件相对位置的安排,应保证:(1)操作者和工件有适当的相对位置,有足够的活动看见,以便于工件的装卸、刀具的安装调试、加工情况的观察和工件检验。(2)操作者与操作手柄等控制元件的适当位置,有足够的操作空间,达到操作准确、省力、方便。(3)操作件应按照GB4141选用,操作件之间有合理的距离。(4)功能不同的按钮应有不同的颜色,且这些颜色应和人的视觉习惯一致、符合人的心理生理特征。防止误操作。机床工件的安装高度,应充分考虑人的身体高度,按照机床的形式,合理确定。操作者站立不动,手臂最大可及的工作范围是1600mm,正常活动范围是1200mm。常用的手柄应集中设置在操作者正常活动范围内,不常用的手柄可就近设置。视距是指人在操作过程中正常的观察距离,一般为50760mm,最佳为560mm。人的眼睛沿水平方向运动与垂直方向运动灵活,目测水平尺寸比垂直尺寸精确,且不易疲劳,因而视觉接受的信号源应尽量水平排列。攀枝花学院毕业设计 3 零件工艺方案拟定3 零件工艺方案拟定3.1 组合机床常用工艺方法能表达的精度及表面粗糙度麻花钻由于受结构和切削条件等的限制,加工后孔的质量比较低(孔公差1T11级以下;表面粗糙度506.3),因而一般常只用于孔的粗加工。由于被加工零件的工艺要求,加工部位尺寸,形状,结构特点,材料,生产率要求不同,设计组合机床必须采用不同的工艺方案和工艺过程。从分析被加工零件可知,属于箱体端面孔加工的问题,查金属切削刀具等设计资料书可知:该工件所采用的加工工艺方法为钻孔加工即可。 3.2 零件的毛坯及材料由于该零件的形状较复杂,为铸件,而且属于大批量生产,选择制造精度与生产率都比较高的毛坯制造方法,则选择机器加工中的消失模铸造,以便后序工序加工时减少工时定额,提高加工精度等级等。3.3 零件的定位基准选择组合机床是针对一种零件或零件的一道工序而设计的,正确选用加工定位基准,是确保加工精度的重要条件,同时也有利于实现最大限度的集中工序,从而收到减少机床台数的效果,对于箱体零件的定位基准的选择,因为箱体零件的加工工序多,这类零件一般都有较高精度的孔加工的需要,有常常要在几次安装下进行,因此“一面两孔”是最常用的方法,它的特点:1 可以简单的消除工作的六个自由度,使工作获得稳定可靠的定位。2 有同时加工零件的五个表面的可能,既能高度集中工序,又有利于提高各面上孔的精度。3 “一面两孔”可作为零件从粗加工到精加工的全部工序的定位基准,使零件在整个加工过程中基准统一,从而减少由基准转移带来的累计误差,有利于保证零件的加工精度,同时使机床上工序的许多部件实现通用化,有利于缩短设计,制造周期,降低成本。4 易于实现自动化定位,夹紧,并有利于防止切削落于定位基面上。“一面两孔”定位在箱体上的加工定位中占有重要的地位,本课题的工件却具备“一面两孔”的定位条件,又因为该工件的重要性,要求具有良好的使用性能,因而不用增设工艺销孔来获得合理准确的定位基准。综上所述,该矿车轮零件在机床上的定位方案只能选择“一面两孔定位”。3.4 确定机床的配置形式以及总体结构方案零件加工工艺方案将决定组合机床的加工质量、生产率、总体布局和夹具结构等。考虑到被加工的零件是钻5个M10螺孔,2个M16螺孔,并针对零件的形状、大小、材料、硬度、刚性、加工部位的结构特点、加工精度、表面粗糙度以及定位、夹紧方法、工艺过程、所采用的刀具及切削用量、现场的环境和条件、生产率要求等。划分工序可以有两种趋向:工序集中和工序分散。工序的集中分散各有其长处,一般说来,在大批量生产中以提高生产率为主,需广泛采用多刀、单轴与多轴自动或半自动机床,多轴龙门铣床、组合机床等,故采取工序集中可以获得突出的效果。此次设计的箱体端面钻孔组合机床很大程度上使各工序尽量集中,发挥组合机床的优点,同时使各种误差减小到最低限度。遵循以下几点基本原则:(1)选择合适、可靠的工艺方法;(2)加工合理安排;(3)工序集中原则;(4)定位基准及夹紧点选择原则;(5)制定工艺方案1)装卸、夹紧;2)钻孔;3)攻丝。一台组合机床主要由滑台、钻削头、夹具、多轴箱、动力箱、立柱、立柱底座、中间底座、侧底座以及控制部件和辅助部件等组成。其中夹具和多轴箱是按加工对象设计的专用部件,其余均为通用部件,且专用部件中的绝大多数零件(约70%90%)也是通用零件。加工时,刀具由电动机通过动力箱、多轴箱驱动做旋转主体运动并通过各自的滑台带动做直线进给运动。根据所选用的通用部件的规格大小以及结构和配置形式等方面的差异,将组合机床分为大型组合机床和小型组合机床两大类。习惯上滑台台面宽度大于250mm的为大型组合机床,滑台台面宽度小于250mm的为小型组合机床。根据组合机床的配置形式,可将其分为具有固定夹具的单工位组合机床、具有移动夹具的多工位组合机床和转塔式组合机床三类。按照组成部件的配置形式及动力部件的进给方向,单工位组合机床又分为卧式、立式、倾斜式和复合式四种类型。a 卧式组合机床卧式组合机床的刀具主轴水平布置,动力部件沿水平方向进给,按加工要求的不同,可配置成单面、双面或多面的形式。本题目选用单面即可。b 立式组合机床立式组合机床的道具主轴垂直布置,动力部件沿垂直方向进给。一般只有单面配置一种形式。c 倾斜式组合机床倾斜式组合机床的动力部件倾斜布置,沿倾斜方向进给。可配置成单面双面或多面的形式,以加工工件上的倾斜表面。d 复合式组合机床复合式组合机床是卧式、立式、倾斜式两种或三种形式的组合。上面已分析过本题目选择固定式夹具单工位组合机床。攀枝花学院毕业设计 4 总体方案设计4 总体方案设计4.1 工艺方案 根据工件图(见图2.1),工件材料ZT200,室温下的力学性能200MPa,属于脆性材料,塑性和韧性差,不能锻造和冲压,焊接性很差,铸造性良好,可切削性好。如前零件分析所知该零件主要是在工件单面进行多孔加工,属大批量的中、小零件加工,且工件被加工螺孔之间沿圆周偏差不大于,等级要求不高,而且设计所要求加工的箱体端面的螺孔位置特殊,加工起来相对简单,因此采用固定式夹具单工位卧式单面钻孔组合机床即可,加工工艺方案切削参数如下:加工M10螺孔,查阅机械加工工艺手册表2.3-71 攻丝及装配前的钻孔直径得:刀具直径 d=8.5mm 切削速度 =15m/min 进给量 =0.1mm/r加工M16螺孔,查阅机械加工工艺手册表2.3-71 攻丝及装配前的钻孔直径得:刀具直径 d=13.9mm 切削速度 =15m/min 进给量 =0.1mm/r4.2 总体方案在机床总体布局若采用单孔单钻的方式分别对工件上各个孔进行加工,不仅不能保证各孔之间的相对位置精度,同时单孔钻削加工工时也要增加。由生产批量为大批量生产若分开加工,工步增多不能保证生产批量。若在同一台机床上钻削加工,不存在换刀工序,螺纹底孔同时加工完成。同时由被加工零件特点加工孔的中心线与定位基面垂直,分析需要单面加工的箱体零件,本题目选用用卧式机床和立式机床都可,本次设计中选取卧式机床。为了达到缩短工时,减小机床占地面积和达到大批量生产,我们采用卧式单面组合钻床,螺孔同时加工。1 机床工作循环如下:上料工件夹紧滑台工进滑台锁紧主轴启动进给滑台快进进给滑台工进进给滑台停止、主轴继续转动进给滑台快退滑台松开滑台快退工件松开下料2 机床配置型式:(1)单工位组合机床 该机床具有固定式夹具,通常可安装一个工件特别适用于大、中型箱体零件加工。利用多轴箱同时从几个方向对工件加工。但其机动时间不能与辅助时间重合,因而生产率比多工位机床低。(2)多工位组合机床 主要适用于中小零件加工,通常被加工工件安装在多工位工作台上,并由工作台带动作间歇运动,使工件由一个工位辅送到下一个工位。同时采用多工位组合机床时,由于能在不同工位上对工件进行顺序加工或平行顺序加工,从而提高了工序集中程度,并能设置单独卸装工位,使辅助时间与机动时间重合,提高生产率。由上面机床的两种配置型式和零件加工技术要求,为使设计简单经济,不考虑零件的其他加工程序,所以选择单工位组合机床,因该工件轮廓尺寸与重量都较小,且属于大批量生产,加工螺孔相对简单,工件加工利用多轴箱工作。采用刚性主轴还能提高其加工精度,所以选用单工位卧式单面钻组合机床加工该零件即节省工时,又增加经济效率。组合机床总体方案设计在于对其专用部件设计和编制“三图一卡”,即绘制被加工零件工序图、加工示意图、机床联系尺寸图,编制生产率计算卡。在绘制被加工零件工序图时,要标明其加工部位尺寸、精度以及加工时定位基准,夹紧位置等应尽量体现其加工零件的特点。绘制加工示意图前要根据加工材料和进给量,计算加工是所受力、力矩和切削功率,刀具耐用度以选择其刀具与接杆和导向装置等一些通用零部件。主轴箱设计是组合机床中的一个重要专用部件。首先应根据加工孔系的分布范围确定其轮廓尺寸,选定其多轴箱型号,然后计算出箱体中各个轴(主要为主动轴和从动轴)的坐标与轴上齿轮之间的传动关系等等。夹具设计是组合机床的另一个重要的专用部件。因为夹具将会影响零件加工精度,在设计前要绘制草图以确定可行的结构及其主要轮廓尺寸。攀枝花学院毕业设计 5 组合机床设计三图一卡设计5 组合机床设计三图一卡设计根据前几章分析和指定的机床工艺方案及机床的配置型式结构方案下面用图纸的表达形式三图一卡设计,来表示组合机床的总体设计。其内容包括:绘制被加工零件图、加工示意图、机床联系尺寸图,编制生产率计算卡。被加工零件(见图2.1)。其材料为铸钢ZT200,常温下的力学性能200MPa,加工部位及要求为:面上有7孔,即、;其他技术要求见图纸。5.1 被加工零件图被加工零件图是根据选定的工艺方案,表明零件的形状、尺寸、硬度、以及在所设计的组合机床上完成的工艺内容和所采用的定位基准、夹压点的图纸。是组合机床设计的主要依据,也是制造、验收和调整机床的重要技术条件。1 在被加工零件图上标注的内容有(1)加工零件的形状、主要轮廓尺寸和本机床要加工部位的尺寸、精度 、表面粗燥度、形位精度等技术要求,以及对上道工序的技术要求等。(2)本工序所选定的定位基准,夹紧部位及夹紧方向。(3)被加工零件的名称、编号、材料、硬度及被加工部位的加工余量等。2 绘制被加工零件工序图的一些规定(1)除加工部位用粗实线画外,其余部位用细实线绘制。定位基准、夹紧部位、夹紧方向等需用符号表示;本道工序保证的尺寸、角度等,均在尺寸下画横线标出(2)注明零件对机床加工提出的某些特殊要求,如对精镗孔机床应注明是否允许留有退刀痕迹。(3)各加工部位的位置尺寸,应由定位基准标起。当定位基准与设计基准不重合时应进行换算。(4)对各加工部位的位置尺寸当为不对称公称公差尺寸时,换算为对称公差尺寸即使名义尺寸位于公差带的中央。被加工零件图见图2.1。5.2 零件加工示意图加工示意图是被加工零件工艺方案在图样上的反映,表示被加工零件在机床上的加工过程,刀具的布置位置以及工件、夹具、刀具的相对位置关系。机床的工作行程及工作循环等,是刀具、夹具、多轴箱、液压和其他系统设计选择动力部件的主要依据,是整台组合机床布局形式的原始要求,也是调整机床和刀具所必需的重要技术文件。5.2.1示意图上应标注的内容1 机床的加工方法,切削用量,工作循环和工作过程。2 工件、夹具、刀具及多轴箱之间的相对位置尺寸及联系尺寸。如工件端至多轴箱端面的距离等。3 主轴的结构类型、尺寸及外伸长度、刀具类型,数量和结构尺寸,刀具与导向装置的配合,刀具、接杆、主轴之间的连接方式。刀具按照终了位置绘制。5.2.2绘制加工示意图及绘制之前的有关计算1 刀具的选择选择刀具,应考虑工艺要求与加工尺寸精度、工件材质、表面粗糙度及生产率的要求。只要条件允许应尽量选用标准刀具。为了提高工序集中程度或满足精度要求,可以采用复合刀具。孔加工刀具的长度应保证加工终了时刀具螺旋槽尾端与导向套之间有3050mm距离,以便于排出切削和刀具磨损后又一定的向前调整量。所以,根据零件要加工的螺孔,参照以上要求,依据机械加工工艺师手册(杨叔子主编)孔加工刀具表20-2、表20-3和表20-4,加工M10螺孔选择高速钢直柄麻花钻(GB143585)直径d=8.5 mm,l=117mm,加工M16螺孔也选择选择高速钢直柄麻花钻(GB143585)直径d=13.9mm,l=160mm。2 导向套的选择组合机床加工孔时,除了采用刚性主轴加工方案外,零件上孔的位置精度主要靠刀具的导向装置来保证。因此正确选择导向装置的类型,合理确定其尺寸、精度,是设计组合机床的重要内容,也是绘制加工示意图时必须解决的问题。导向装置有两大类,即固定式导向和旋转式导向。在加工孔径不大于40mm或摩擦表面线速度小于20m/min时,一般采用固定式导向,刀具或刀杆的导向部分,在导向套内即转动又作轴向移动。固定导向装置一般由中间套、可换导套和压套螺钉组成。中间套的作用是在可换导套磨损后,可较为方便的更换,不会破坏钻模体上的孔的精度。加工孔径较大或线速度大于20m/min时,一般采用旋转式导向装置。旋转式导向装置将旋转副和直线移动(导向)副分别设置,按旋转副和直线副的相对位置分为内滚式和外滚式两种;滚动轴承安装在刀杆上的旋转导向为内滚式导向,中间导向套只作直线移动,导向长度为(23)d1(d1刀杆直径),导向至工件端面的距离为2050mm,视导向结构而定;滚动轴承内圈安装在中间导向套上,中间导向套不随主轴一起的旋转导向为外滚式导向装置,导向长度为 (2.53.5)d1。旋转式导向装置的极限转速由轴承的极限转速和刀具允许的切削速度决定,导向精度由轴承精度和刀杆、导向套的精度决定。旋转式导向一般通过滑块连轴器(JB/ZQ4384-1986)与主轴“浮动”联接。由于该零件加工孔较小,不需要扩或铰,且其加工时的速度小于20m/mim,所以可选用固定式导向装置,其导向套布置见图5.1得:图5.1 导向套布置图根据前述以及加工要求,选择的刀具为:8.5mm的刀具5把,13.9mm的刀具2把,且为硬质合金钻头。3 导向装置的选择 由于选择刚性主轴,其位置尺寸精度取决于主轴的位置和尺寸精度,对于所加工出的孔的精度将起着重要的角色,而与选择的刀具和有无导向装置没有太大的关系,另外由于该机床所加工的孔的直径和长度均不大,所以选用固定式导向装置,则其布局与参数的选择见图5.2。工艺方法导向布局简图导向长度导向至工件端面的距离刀具与主轴的连接形式钻孔(23)(钻铸铁)刚性 图5.2 钻孔布局简图其导向装置的配合形式如图5.3:图5.3导向装置之间的配合导向装置的配合:导向装置的配合依据参考资料书组合机床设计中的精度进行选择和设计。其精度以及配合的相互关系见表5.1。表5.1 导向配合公差表导向类别工艺方法dDD1刀具导向部分的外径固定式钻孔G7(F8)H7/g6H7/js6用钻头本身导向4 初定切削用量切削用量是指切削速度、进给量、背吃刀量等三个切削要素。它们表示切削过程中切削运动的大小及刀具切入工件的程度,切削速度是切削刃的选定点相对于工件的主运动的瞬时速度,通常用Vc表示,单位为米/分或米/秒。进给量是工件或刀具的每一转或每一往返行程的时间内,刀具与工件之间沿进给运动方向的相对位移,通常用f来表示,单位为毫米/转或毫米/行程。背吃刀量是指通过切削刃基点并垂直于工件平面方向上测量的吃刀深ap,也就是工件待加工表面与已加工表面之间的垂直距离,习惯上也将背吃刀量称为切削深度,通常用ap表示,单位为毫米 。切削深度ap 选择原则是根据工件的加工余量来决定的,选择是应考虑:a 在留下精加工及半精加工余量后,粗加工应尽可能将剩下的余量一次切除以减少走刀次数;b如果工件余量过大,或机床动力不足而不能将粗切削余量一次切除,也应将第一次走刀的切削深度尽可能取大些;c 当冲击负载较大,或工艺系统刚性较差时,应适当减少切削深度;d 一般精切时,可取ap=0.050.8毫米,半精加工时可取ap=1.03.0毫米 。进给量f的选择是主要是根据切削力及加工表面粗糙度:粗加工时,加工表面粗糙度要求不高,进给量主要受刀杆、刀片、工件及机床的强度和刚度所能承受的切削力的限制;半精切削及精切时,进给量主要受表面粗糙度要求的限制,刀具的副偏角愈小,刀尖圆弧半径愈大,切削速度愈高,工件材料的强度愈大,则进给量可愈大 。切削速度vc的选择原则主要考虑切削加工的经济性,必须保证刀具经济寿命,同时切削负载不应超过机床的额定功率,通常的原则是:a 刀具材料的耐热性好,切削速度可高些;b工件材料的强度、硬度高,或塑性太大或太小,切削速度均应取低些,c 加工带外皮的工件时,应付适当降低速度;d要求得到较小的表面粗糙度时,切削速度应避开积屑瘤的生成速度范围,对硬质合金刀具,可取较高的切削速度,对高速钢刀具,常采用低速切削;e 断续切削时,应取较低的切削速度;f 工艺系统刚性差时,切削速度应适当减小;h在切削速度最后确定之前,须验算机床电动机的功率是否足够 。组合机床往往采用多轴、多刀、多面同时加工,且组合机床上的刀具要有足够的使用寿命,以减少频繁换刀。因此,组合机床切削用量一般比通用机床的单刀加工要低30%以上。 同一多轴箱上的刀具由于采用同一滑台实现进给,多以各刀具的每分钟进给量应该相等。因此,应按工件时间最长、负荷最重、刃磨较困难的所谓“限制性刀具”来确定;对于其他刀具,可以在这基础上进行调整其每转进给量,以满足每转进给量相同的要求。另外,在多轴箱传动系统设计完毕、传动齿轮齿数确定后,还要反过来调整初定的切削用量。选择切削用量时,应尽量使相邻主轴转速接近,以使多轴箱的传动链简单些。使用液压滑台时,所选的每分钟进给量一般应比滑台的最小进给量大50%,以保证进给稳定。在组合机床上用多轴箱同时钻5个8.5mm孔、两个14mm孔,查阅机械设计手册然后再攻螺纹,螺距P=1.5和P=2,主轴转速分别为。钻孔8.5 =0.1mm/r =15mm/min钻孔13.9 =0.1mm/r =15mm/min5 确定切削转矩、轴向力和切削功率确定切削转矩、轴向力和切削功率是为了分别确定主轴及其它传动件尺寸、选择滑台及夹具设计、选择主电动机(一般是选择动力箱的驱动电机)提供依据。切削转矩、轴向力和切削功率可利用下列公式计算采用高速钻头钻铸铁孔时: = 式(5.1)= 式(5.2) 式(5.3)式中 轴向切削力(N) 钻头直径(mm) 每转进给量(mm/r)切削转矩() 切削功率(KW) 切削速度(m/min) 材料硬度由上式(5.1)、(5.2)、(5.3)得钻削1、2、3、4、5(即5个M10的螺孔)孔时:=890.93N取 =1000N=2351.52N.mm 取 =2400N.mm=0.1412kw取 =0.2kw钻削6、7(即2个M16的螺孔)孔时:=1456.94N取 =1500N=5986.62N.mm取 =6100N.mm=0.2195kw取 =0.3kw根据上列公式,计算出本工序钻孔的轴向力、切削转矩、切削功率列于表5.2。表5.2 本工序钻孔的F、T、P值孔位孔数钻头直径轴向力F(N)转矩T(N.mm)功率P(kw)1、2、3、4、55钻8.56、72钻13.96 初步确定主轴直径根据切削扭转矩的确定来初步确定主轴的直径,根据公式: 式(5.3)式中 轴直径(mm) 切削扭矩(n/mm)则由式(5.3)得:钻1、2、3、4、5孔时:=24.45mm取=25mm钻6、7孔时:=33.36mm取=35mm本例中,钻1、2、3、4、5孔时=25mm,主轴外伸长度为:=115mm,内径为:=25(H7)mm,内孔长度为:=85mm。钻6、7孔时=35mm,主轴外伸长度为:=115mm,内径为:=35(H7)mm,内孔长度为:=106mm。7 选取刀具接杆由以上可知,多轴箱各主轴的外伸长度为一定值,而刀具的长度也是一定值。因此,为保证多轴箱上的各刀具能同时达到加工终了位置,就需要在主轴与刀具之间设置可调环节。这个可调环节在组合机床上是通过可调整的刀具接杆来解决的。接杆上的尺寸与主轴外伸长度的内孔配合,因此,根据接杆直径和刀具的锥体莫氏锥度,从表中选取。分别为B25/1/50、B35/1/60。8 确定加工示意图的联系尺寸加工示意图联系尺寸图的标注如图5.4所示。图5.4 加工示意图其中最重要的联系尺寸是工件端面到多轴箱端面之间的距离。它等于刀具悬伸长度、螺母厚度、主轴外伸长度与接杆伸出长度(可调)之和,再减去加工孔深(如加工通孔,还应减去刀具的切出值)。为了使所设计的机床结构紧凑,应尽量使工件端面至多轴箱端面间距离最小。因此,选取接杆时,在主轴外伸长度及刀具类型相同的条件下,应首先选取加工部位在外壁的盲孔孔径最大、长度小的主轴刀具接杆;应保证在加工终了位置时钻头等刀具的螺旋槽尾部至导向套端面的距离,以利于排屑和刀具刃磨后向前调整。工件端面到多轴箱端面之间的距离还与机床的总布局有关,如夹具尺寸等。9 确定动力部件的工作循环及工作行程(1)工作进给长度的确定工作进给长度应按加工长度最大的孔来确定。工作进给长度等于刀具的切入值(根据工件端面的误差情况,一般取)加工孔深及切出值之和。所以,轴:L=8+26+13=47mm 轴:L=8+26+16=50mm(2)快速退回长度等于快速引进与工作进给长度之和。快速引进是指动力部件把主轴箱连同刀具从原始位置送进到工作进给开始位置,其长度按加工具体情况确定。通常在采用固定式夹具的钻、扩、饺孔组合机床上,快速退回行程长度须保证所以刀具均退至夹具导套内而不影响工件装卸。而对于采用移动式或回转式夹具的组合机床,快退行程长度须保证把刀具、托架、钻模板及定位销退离到夹具运动可能碰到的范围之外。快速退回长度=快速引进长度+工作进给长度。则3、4、5、6、7孔的快速退回长度=75+47=122mm则1、2孔的快速退回长度=75+50=125mm综上,取快速退回长度为125mm(3)动力部件总行程长度 动力部件的总行程除应保证要求的工作循环工作行程(快速引进+工作进给=快速退回)外,还要考虑装卸和调整刀具方便,即考虑前、后备量。前备量是指因刀具磨损或补偿制造、安装误差、动力不见尚可向前调节的距离。后备量是指考虑刀具从接杆中或接杆连同刀具一期从主轴孔中取出所需要的轴向极力。理想情况是保证刀具退离夹具导套外端面的距离大于接杆插入主轴孔内(或刀具插入接杆孔内)的长度。因此,动力部件的总行程为快退行程长度与前后备量之和。依此作为选择标准动力滑台或设计专用动力部件的依据。所以本设计中的动力部件总行程长度为:动力部件总行程长度=快速退回长度+前后备量=125+110+20 =255mm 10 加工示意图画法(1)加工示意图的位置,按加工终了时的状况绘制,且其方向与机床的布局相吻合。(2)工件的非加工部位用细实线绘制,其余部分一律按机械制图标准绘制。(3)同一多轴箱上,结构尺寸完全相同的主轴,不管数量多少,只绘制一根,但应在主轴上标注与工件孔号相对应的轴号。(4)主轴间的分布可不按真实的中心距绘制,但加工孔距很近或需要设置径向尺寸较大的导向装置时,则应按比例绘制,以使检查相邻主轴、刀具、导向装置是否发生干涉。(5)对于标准通用结构,允许只绘制外形,标上型号,但对一些专用结构如导向、专用接杆等则应绘出剖视图,并标注尺寸、精度及配合。 5.3 机床联系尺寸图机床联系尺寸图是用来表示机床的配置形式、机床各部件之间的相对位置关系和运动关系的总体布局图。是进行多轴箱、夹具等专用部件设计的重要依据。如图5.6所示,机床联系尺寸图的内容包括机床的布局形式,通用部件的型号、规格,动力部件的运动尺寸和所有电动机的主要参数,工件与各部件间的主要联系尺寸,专用部件的轮廓尺寸等等。绘制机床联系尺寸图之前,应进行下列工作及其有关计算。5.3.1选用动力部件1 滑台的选用 通常,根据滑台的驱动方式、所需进给力、进给速度、最大行程长度和加工精度等因素来选用合适的滑台。初选1HJ型液压滑台,并选择动力滑台及附属部件。根据动力滑台中,液压滑台与机械滑台的优缺点的比较:快进转工进时,转换位置精度较低且考虑到过载保护方面的原因,选择液压滑台,根据计算求出总的切削力P=8000,及液压滑台的主要技术性能比较,选择1HY32系列液压滑台。具体液压滑台的主要技术参数见表5.3:表5.3 液压滑台的主要技术参数型号台面宽度长度行程最大进给力工进速度快进移动速度型型1HY32320mm630mm400mm630mm12500N20650mm/min10m/min根据1HJ32系列液压滑台,选择该系列滑台的附属部件、支承部件以及配套设施部件,经过查资料组合机床设计简明手册可知,如表5.4:表5.4 滑台的附属部件、支承部件以及配套设施部件部件型号立柱滑台侧底座立柱侧底座1HY321HY32M1HY3GABAB4006301CL321CL32M1CC3211CC3221CC321M 1CC322M1CD321M1CD322M1CD321M1CD322M由于该组合机床不需要二次进给,且为了对在加工产生振动,以及吸收振动,选用A型铸铁导轨,即选择的液压滑台是:型。另外由于该机床所选择的加工方式是卧式单面钻,则该液压滑台的配置型式为卧式。(1)驱动方式的确定采用液压驱动还是机械驱动的滑台,可以参照通用部件对液压滑台和机械滑台的性能特点比较,并结合前面分析的具体的加工要求、使用条件等来选用。本例选用1HY32系列液压滑台。(2)确定轴向进给力滑台所需的进给力按下式计算: 由于滑台工作时,除了克服各主轴的轴向力外,还要克服滑台移动时所产生的摩擦阻力,因而,所选滑台的最大进给力应取大些。取(3)确定进给速度液压滑台是靠液压系统中变量叶片泵供油,进口节流调速来实现液压滑台的工作进给速度在一定范围内的无级调节。液压在确定刀具的切削用量是所规定的工作进给速度应大于滑台最小进给速度,1HY系列液压滑台采用滚珠丝杠传动,工作进给速度为mm/min范围内快速移动速度为定值。则由前的轴向力选取滑台的型号为1HY32型。(4)确定滑台进程 由于滑台的行程除保证足够的工作行程外还应留有前备量和后备量。前备量的作用是使动力部件有一定的向前移动的余地,以弥补机床的制造误差及刀具磨损后能向前调整,前备量一般取值范围为1020mm 本设计取前备量为20mm,后备量的作用是使动力部件有一定的向后移动的余地以方便装卸刀具,后备量一般不小于4050mm本设计取为50mm 所以总行程为:工作行程+前备量+后备量=255+20+50=325mm(5) 多轴加工的总切削功率以及主驱动装置的确定确定单根主轴切削功率后,求出多轴加工的总切削功率 式(5.4)但是考虑到在加工过程中有功率损失,选效率为0.82,则总的需要的功率为:未考虑功率损失前:=1.6考虑到功率损失后: 式(5.5)则该主运动驱动装置的式(5.5)得:功率为1.93选择主电机功率为2.2的1NGc25型电动机,且该系列主传动装置具有通用化程度高、选配灵活,便于生产经营管理等优点。其主要技术参数见表5.5:表5.5 主电机的技术参数主电机传动型号转速范围(r/min)主电机功率()配套主轴部件型号低速组高速组1NGc251608002.21TA25、1TA25M、1TZ22 动力箱的选用动力箱主要依据多轴箱所需的电动机功率来选用。多轴箱所需要的电动机功率为 式(5.6)前面已查阅机械加工工艺手册和机械设计手册得知动力箱的切削功率为=0.437kW;P空壳根据周的直径及转速由机械设计手册主轴的空转功率表中查得0.074 kW;一般选取所传动功率1%。多轴箱传动系统设计之前,无法确定时,有下式估算: 式(5.7)式中多轴箱传动效率,加工黑色金属时=080.9,有色金属时=0.70.8;主轴数多,传动复杂时取小值,反之取大值。动力箱的电动机功率应大于计算功率,并结合各主轴要求的转速大小,合理地选定动力箱的电动机功率和型式。据此,选用电动机型号为Y110L14(机械设计实用手册表10-4-1)的1TD321型动力箱,电动机额定功率为2.2KW,驱动轴转速为520r/min。 当动力部件的功率或进给力不能满足要求却相差不打时,可据具体情况适当降低切削用量,或将刀具错开顺序加工,以降低功率和进给力。5.3.2确定装料高度装料高度是指及穿个上工件的定位基准面到地面的垂直距离。我国过去设计组合机床一般取装料高度 H=850mm。为提高通用部件及支撑部件的刚度并考虑自动线 设计时中间底座内袄安装夹具输送、冷却排屑装置,新颁布的组合机床标准推荐装料高度H=1060mm,与国际标准(ISO)一致。在现阶段,设计组合机床时,装料高度视具体情况在H=8501060mm之间选取。选装料高度H应考虑的主要因素是,应与车间里运送工件的滚道高度相适应,工件最低孔位置,主轴箱最低主轴高度和所选通用部件、中间底座、夹具等高度尺寸的限制(该机床所选用滑台与滑座总高=280mm,侧底座高度560mm,夹具底座高度240mm,多轴箱底座高度=560mm),综合上述因素,本例选取装料高度为800mm。5.3.3初步确定夹具轮廓尺寸根据工件尺寸和形状,考虑工件的定位件、夹紧机构、刀杆导向装置的要求空间;并应满足排屑和安装的需要,钻模厚度不小于最小导向长度,因此在钻7个孔时钻模厚度均为35mm。夹具底座的轮廓尺寸由与之配合的滑台底座轮廓尺寸,工件的轮廓尺寸形状,具体结构为:长396mm,宽190mm,高230mm,厚度26mm,被加工的7个螺孔分布在宽190mm,高230mm的端面上。5.3.4底座轮廓尺寸底座的轮廓尺寸要满足夹具在其上面联接安装的需要。左侧底座长度尺寸根据所选动力部件(滑台、滑座)及配套部件(侧底座)的位置关系确定。同时考虑多轴箱处于终了位置时,多轴箱与夹具体之间应有实当距离,以便于机床调整、维修;另外中间底座周边应有不小于70100mm的排屑或冷却液回流槽。左侧底座长度方向尺寸L,要根据所选动力部件和夹具安装要求来确定。其中:L1加工终了位置时,多轴箱端面至工件端面间的距离(mm)本题目L1 =320mmL2多轴箱厚度(mm),本题目多轴箱用90 mm后盖, L2=325mmL3工件长度(mm),本题目工件长度为396mml1滑台与多轴箱的重和长度(mm),本题目为180mml2加工终了位置时,滑台前端面至滑座端面间的距离和前备量之和(mm)本题目为40mml3滑座前端面和侧底座端面距离(mm),本题目为110 mm所以本题目左底座的长度确定为700mm左侧底座长度确定后,多轴箱端面至工件端面间的距离就最后确定了,因此,刀具接杆的长度也就最后确定。底座高度按标准选取560mm。在确定中间底座高度时,应考虑切削的存储和清理以及电气接线盒的安排。如用切削液时,还应考虑容纳35min冷却泵流量切削液。对于加工铸铁件的机床,为了使切削液有足够的沉淀时间,其容量还应加大到1015min的流量。5.3.5初步确定多轴箱轮廓尺寸 标准中规定:卧式配置的多轴箱总厚度为325mm,立式配置的为340mm;宽度和高度按标准尺寸系列表选取。计算时,多轴箱的宽度B和高度H可按下式计算。B=b+2b 式(5.8)H=+ 式 (5.9)式中: b工件在宽度方向相距最远的两孔距离(mm);70+ =123.69 最边缘主轴中心距箱外壁的距离26.31(mm); 工件在高度方向相距最远的两孔距离178(mm); 最低主轴高度31(mm)。b和h为已知尺寸。为保证主轴箱由排布齿轮的足够空间,取=100mm。主轴箱最低主轴高度须考虑到与工件最低孔位置、机床装料高度、滑台滑座总高、侧底座高度、滑座与侧底座之间调整垫高度等尺寸之间的关系来确定。对于该组合机床,要保证润滑不致从主轴衬套处泄漏箱外,则:85140毫米。 图5.5 主轴分布图对于本组合机床的设计为:=100mm若取100毫米,由式(5.8)、式 (5.9)可求出主轴箱轮廓尺寸为: B=b+2=123.69+270=263.69mm H=h+=178+90+70=338mm根据上述计算值,按主轴箱轮廓尺寸系列标准,最后确定主轴箱轮廓 尺寸为: BH=400400mm5.3.6机床联系尺寸图的画法和步骤1 画主视图 主视图的图形布置应与实际机床工作位置一致,并应选择适当的比例 。2 在联系尺寸图上标注尺寸具体的要求是:(1)完整、恰当地标注机床各主要组成部件的轮廓尺寸及相关联系尺寸,应使机床在长、宽、高三个方向的尺寸链封闭。(2)应表示清楚运动部件的原位、终点状态及运动过程情况(可用工作循环图表示),以确定机床最大轮廓尺寸。(3)应注明工件、夹具、动力部件、中间底座对称中心线间的位置关系。(4)应注明电动机的型号、转速及所选标准通用部件的型号规格和其主要轮廓尺寸,作为部件和零件设计的原始依据。在机床各组成部件的设计完成之后,以联系尺寸图为基础进行细化,填加必要的电气、液压控制装置、润滑、冷却、排屑装置等,并加注技术要求等文字说明,便成为机床总图(见图5.6)。图5.6 机床联系尺寸图5.4 机床生产率计算卡根据选定的机床工作循环所要求的工作行程长度、切削用量、动力部件的快速及工进速度等,计算机床的生产率并编制生产率计算卡,用以反映所设计机床的工作循环过程、动作时间、切削用量、生产率、负荷率等。通过生产率计算卡,可以分析所拟定的方案是否满足用户对生产率及负荷率的要求。5.4.1理想生产率Q指完成年生产纲领(包括备品及废品率在内)所要求的机床生产率。它与全年工时数有关,一般情况下,单班制生产取2350h,两班制生产取4600h,则本机床的生产率由式(5.10): 式(5.10)5.4.2实际生产率Q1指所设计机床每小时实际可以生产的零件数量。 = (件/小时) 式(5.11)式中:生产一个零件所需要的时间(min),它可根据下式计算: =+=(+)+()min 式(5.12)机加工时间(min),包括动力部件工作进给和死挡铁停留时间。即:=+ 、分别为刀具第、第工作进给行程长度(mm);、分别为刀具第、第工作进给量(mm/min); 死挡铁上的停留时间,一般为在动力部件进给停止状态下,刀具旋转510转所需时间(min); 辅助时间(min),包括快进时间、快退时间、工作台移 动或转位时间,装卸工件时间;即:=、分别为动力部件快进、快退行程长度(mm);动力部件快速行程速度。采用机械动力部件取56m/min;液压动力部件取310m/min;直线移动或回转工作台进行一次工位转换的时间,一般可取0.1min;工件装、卸(包括定位、夹压及清除铁屑等)时间,它取决于工件重量大小、装卸是否方便及工人的熟练程度。根据各类组合机床的统计,一般取0.51.5min。则由式(5.16)得:=+=(+)+() =(+)+() =2.049min经过计算比较,本机床的设计生产率满足理想生产率要求。5.4.3机床负荷率机床负荷率按下式计算:=根据表5.6进行比较所得:表5.6 机床负荷率参数表机床复杂程度主轴数负荷率单面或双面15=0.90116400.900.8641800.800.75三面或四面15=0.8616400.860.8041800.800.75本机床的负荷率根据为:=0.8163根据组合机床的使用经验,适宜的机床负荷率为=0.750.90,本组合机床的负荷率按照上表确定,为:=0.8163。5.4.4生产率计算卡它是按一定格式编制,反映该零件在机床上加工过程、工作时间、机床生产率、机床负荷率的简明表格。表(5.7)为该零件加工单面钻组合机床生产率计算卡。表5.7 生产率计算卡被加工零件图号毛坯种类铸件名称箱体端面毛坯重量40Kg材料HT200硬度175-255HBS工序名称钻螺纹底孔工序号序号工序名称工作行程/mm切速/(m/min)进给量mm/r进给量mm/min工时/min工进时间辅助时间1安装工件2工件定位、夹紧3滑台快进7550004滑台攻进钻M10和M16螺纹底孔深2645150.1500.905死挡铁停留0.016滑台快进12050000.0247工件松开0.058卸下工件0.5备注1.右动力箱驱动的主轴,转速为500r/min2.一个安装加工一个零件3.本机床装卸工件时间取1min累计0.901.149单件总工时2.049机床生产率12.766(件/h)理论生产率15.5683 (件/h)负荷率82%攀枝花学院毕业设计 6 多轴箱设计6 多轴箱设计多轴箱是组合机床的重要专用部件。根据加工示意图所确定的工件加工孔数和配置、切削用量和主轴类型而设计,由通用零件组成。能将动力箱的动力,传递给主轴,使之按要求的转速和转向旋转,提供切削动力。多轴箱与动力箱一起安装于进给滑台上,可完成钻、扩、铰、镗孔等加工工序。6.1 多轴箱的通用零件1 通用箱体类零件通用箱体类零件包括多轴箱箱体、前盖、后盖、上盖和侧盖(见图6.1)。箱体材料为HT200,前、后盖材料为HT150,上盖为HT150。多轴箱体规格见表6.1多轴箱后盖与动力箱的结合面上联接螺孔、定位销孔的大小、位置应与动力箱联系尺寸相适应。图6.1 箱体结构图多轴箱箱体的标准厚度为180mm,用于卧式组合机床的多轴箱前盖厚度为55mm,用于立式的则兼作油池用,故加厚到70mm;基型后盖厚度为90mm ,变型后盖厚度为50mm、100mm和125mm三种,可根据多轴箱内传动系统安排和动力箱与多轴箱的连接情况合理选用。如只在动力箱的输出轴(驱动轴)与多轴箱输入轴上有排或排的一对齿轮啮合,且啮合的齿轮外廓(相啮合的两齿轮的中心矩与两齿轮齿顶圆半径之和)不超出后盖于动力箱连接法兰的范围时,可选用50mm或100mm的后盖,但后盖窗口要按出轮外廓加以扩大并进行补充加工;如果相啮合的齿轮外廓超出后盖与动力箱连接法兰的范围或多余一对啮合齿轮时,若为排齿轮需采用厚度为90mm的后盖,若为排齿轮,需采用厚度为125mm的后盖。根据本题目要求钻7个箱体端面分布的5个M10、2个M16的螺孔,所以选用厚度为125mm的后盖。表6.1多轴箱规格动力箱型号B1H1BH1TD25A320250320,400,500,630250,320,4001TD32A400320400,500,630,800320,400,5001TD40A500400500,630,800,1000400,500,6301TD50A630500630,800,1000,1250500,630,8001TD63A800630800,1000,1250630,800,10001TD80A10008001000,1250800,1000,12502 通用轴类零件(1)通用主轴 通用主轴分为钻削类和攻螺纹类两种。钻削类主轴采用两端轴向定位方式,按支承形式可分为圆锥滚子主轴,滚针轴承主轴,滚珠轴承主轴三种。圆锥滚子轴承主轴,前后支承均为圆锥滚子轴承,可承受交大的径向力和轴向力,轴承数量少,结构简单、装配调整方便,广泛用于扩、镗、铰孔和攻螺纹工序。滚珠轴承主轴,前支承为向心球轴承和推力球轴承,后支承为向心球轴承或圆锥滚子轴承,前支承的推力球轴承设置在深沟球轴承的前边,承受的轴向力大,适用于钻孔工序。滚针轴承主轴,前后支承均为无内圈滚针轴承和推力球轴承,径向尺寸小。使用与主轴间距较小的多轴箱。根据刀具的连接方式,多轴箱主轴又分为浮动主轴和刚性主轴。浮动主轴在多轴箱前盖外的悬伸长度为75mm(立式主轴为60mm),因而又称为短主轴;采用滑块联轴器与刀杆浮动连接,长导向或双导向装置导向,以保证加工精度;用于镗、扩、铰孔等工序。刚性主轴在多轴箱前盖的悬伸长度大于75mm(立式主轴大于60mm),因而又称为长主轴,主轴内孔与刀具或接杆尾部的配合代号为H7/h6,配合长度与主轴内孔直径之比大于1.6,连接刚度高,刀具前端的下垂量小,配合单导向,适用于钻孔、扩孔、倒角及锪平面等工序。主轴材料一般为40Cr钢,热处理C42;用滚针轴承的主轴材料为20Cr钢,热处理,C59。主轴最小轴心距见表6.2所示。表6.2 通用主轴最小间距表主轴直径滚锥轴承主轴主轴直径滚珠轴承主轴202530354050152025304045204815362550.5532039.5433055.558632544.548533560.56368733049.55358634064.5677277814054.5586368735069.572778286914558.56267727781(2)通用传动轴 常用的通用传动轴按用途和支承形式可分为圆锥滚子轴承传动轴、滚针轴承和推力球轴承传动轴、润滑泵轴、手柄轴四种。通用传动轴材料一般为45钢,热处理T215;滚针轴承的传动轴材料20Cr钢,热处理,C59。(3)通用齿轮 通用的齿轮有三种,即传动齿轮、动力箱齿轮和电机齿轮。材料均为45钢,热处理为齿部高频淬火G54。本机床齿轮的选用按照表6.3选用:表6.3 机床齿轮选用表齿轮种类宽度(mm)齿 数模数(mm)孔径(mm)数量传动齿轮24321650连续16702、2.5、32、2.5、3、415、20、30、35、4025、30、35、40、50395507动力箱齿轮84(A型)44(B型)21263、425、30、40、5040电机齿轮792126318、22、28、32、3620(4)润滑泵 规格较大的通用多轴箱常采用R12-1A叶片泵进行润滑。中等规格的多轴箱用一个润滑泵;规格较大且主轴数量多的多轴箱用两个润滑泵。润滑泵泵出的油经分油器至各点。润滑泵安装在前端盖内,润滑泵轴在箱体内的悬伸长度为24mm,传动方式有两种,一是由润滑泵传动轴传动,另一种是通过传动轴上的齿轮直接与润滑泵轴上的齿轮啮合传动,传动齿轮齿宽为12mm。R12-1A叶片润滑泵的每转排油量为6ml,推荐转速为,转速过低,将会导致吸油困难。(5)其他通用零件 除上述零件外,多轴箱上还有隔套、键套、防油套、油杯、定位销以及锁紧螺母、防松垫圈等,都已经标准化或通用化。6.2 多轴箱设计主轴箱是组合机床的重要部件之一,多轴箱的设计也是组合机床设计的重要内容。多轴箱设计的步骤大致为:根据“三图一卡”,绘制多轴箱设计原始依据图;确定主轴结构形式及齿轮模数;拟定多轴箱传动系统;计算主轴及传动轴坐标;绘制坐标检查图;绘制多轴箱总图及零件图。6.2.1绘制多轴箱设计原始依据图多轴箱设计原始依据图是根据“三图一卡”绘制的,其主要内容如下:(1)根据机床联系尺寸图,绘制多轴箱外形图,并标注轮廓尺寸和驱动轴、定位销孔的坐标值。(2)根据联系尺寸图和加工示意图,画出工件与多轴箱的对应位置尺寸,标注所有主轴的坐标值及工件轮廓尺寸。在原始依据图中应注意:多轴箱与工件的摆放位置,一般情况下,工件在多轴箱前面。(3)标注各主轴的转速及旋转方向。绝大部分主轴为逆时针旋转(面对主轴看),故逆时针转向不标,只标注顺时针转向主轴。(4)列表说明各主轴的工序内容、切削用量及主轴的外伸尺寸。(5)表明动力部件的型号及其性能参数。TD32IA型动力箱电机功率,转速1430r/min,驱动轴转速520r/min,驱动轴到滑台表面距离为94.5mm,其他尺寸可查动力箱装配图。 图6.2 组合机床卧式多轴箱原始依据图图6.2为组合机床卧式多轴箱原始依据图;其余原始数据见表6.3:表6.4 主轴外伸尺寸及切削用量轴号主轴外伸尺寸工序内容切削用量(mm/min)(mm/r)(mm/min)1、2、3、4、540/28115钻500150.1506、750/36115钻500150.1506.2.2确定主轴结构型式及齿轮模数一般情况下,根据工件加工工艺、刀具和主轴的连接结构和刀具的进给抗力及切削转矩来确定主轴的结构形式。钻削加工主轴,需承受较大的单向轴向力,故最好选用向心球轴承和推力球轴承组合的支承结构,且推理球轴承配置在主轴前端;如主轴前进和后退两个方向都要进行切削时,可选用前后支承都是圆锥滚子轴承的主轴结构,以便承受两个方向的轴向力;如果主轴孔间距较小,可选用滚针轴承和推力球轴承组合的支承结构,但这种结构的主轴精度和装配工艺性均较差,除非必要时最好不用。 传动轴直径可参考主轴直径大小初步确定,待传动系统拟定后再进行验证。既:初步确定传动轴直径为25mm和35mm。齿轮模数一般用类比法确定,也可以用下式估算 式(6.1)式中 所估算的齿轮模数(mm); 齿轮所传递的功率(kw); 一对啮合齿轮中的小齿轮齿数; 小齿轮的转速(r/min)。多轴箱中的齿轮模数常用2、2.5、3、3.5、4几种。为了便于生产,同一多轴箱中上午齿轮模数不要多于两种。6.2.3多轴箱的传动系统设计组合机床多轴箱的传动系统,就是用一定数量的传动元件,把动力箱的输出轴与各主轴连接起来,组成一定的传动链,并满足各轴的转速和转向要求。多轴箱的特点是:针对某零件的特定工序恒速加工,传动链短;多主轴同时加工,传动链分支多。因此,多轴箱的传动设计,以获得需要的主轴转速和转向为原则,不存在通用机床前缓后急的最小传动比限制,甚至可用升速传动副驱动主轴。1 对多轴箱传动系统的一般要求(1)从面对主轴的位置看去,所有主轴(除非特殊要求外)应逆时针方向旋转。(2)保证主轴转速和转向的前提下,应力求用最少的传动轴和齿轮(数量和规格)。因此,应尽可能用一根传动轴同时带动多根主轴,并将齿轮布置在同一排位置上。当齿轮啮合中心距不符合标准时,可用变位齿轮或略微改变传动比的方法解决。(3)尽量避免主轴兼作传动轴用,以免增加主轴负荷,影响加工质量。遇到主轴分布较密,布置齿轮的空间受到限制,或主轴负荷较小,加工精度要求不高时,也可用一根强度较高的主轴带动根主轴的传动方案。(4)多轴箱内齿轮传动副的最大传动比,最小传动比;最佳传动比为,以使多轴箱结构紧凑;后盖内的齿轮传动比,;除传动链的最后可采用升速传动外,应尽可能避免升速传动,以避免空转功率损失。(5)用于粗加工主轴上的齿轮,应尽可能设置在前端第排,以减少主轴的扭转变形;精加工主轴上的齿轮,应设置在第排,以减小主轴端的弯曲变形。(6)同一主轴箱内,如有粗、精加工主轴,最好从动力箱驱动轴后,就分两条路线传动,以免影响精加工主轴的加工精度。(7)刚性镗孔主轴上的齿轮,其分度圆直径要尽可能大于被加工孔的孔径,以减少振动,提高运动平稳性。(8)驱动轴直接带动的传动轴数不要超过2根,以免给装配带来困难。多轴箱传动设计中,当齿轮排数不够用时,可在保证齿轮强度的前提下增加排数,如在第排齿轮的位置上设两排薄齿轮或在前盖内设置0排齿轮。2 拟定多轴箱传动系统的基本方法拟定多轴箱传动系统的基本方法是:先把所有主轴中心尽可能分布在几个同心圆上,然后在各个同心圆的圆心上分别设置中心传动轴;再把各组同心圆上的中心传动轴再取同心圆,并用最少的传动轴带动这些中心传动轴;把最后的合拢传动轴与动力箱的驱动轴连接起来。(1)把所有主轴分成几组同心圆 被加工零件上加工孔的位置分布是多种多样的,大致可以归纳为“同心圆分布”、“直线分布”和“任意分布”三种类型。根据设计题目要求,要加工的是五个M10、两个M16的螺孔,而且这些螺孔是在箱体端面上随机分布的,所以选择用多组同心圆分布主轴。如图6.3: 图6.3 主轴位置按同心圆分布(2)用传动树形图来描述多轴箱传动系统 传动树形图(如图6.4所示)是一种用简单线条来描述多轴箱传动系统的图形。传动树形图中的“树梢”表示各主轴,如轴;“树根”表示驱动轴,如驱动轴;各分叉点为传动轴,如传动轴。“树枝”以定向边代表各轴之间的传动副,并以箭头表示传动顺序。根据定向边的箭头,就可以清楚地看出系统的传动路线。 图6.4 传动树形图3 变速箱体钻孔组合机床多轴箱传动系统的拟定(1)拟定传动路线 把主轴作为一组同心圆,在其圆心上布置中心传动轴;把主轴作为一组同心圆,在其圆心上布置中心传动轴;把主轴作为一组同心圆,在其圆心上布置中心传动轴。然后将中心传动轴、作为一组同心圆,在其圆心上用传动轴驱动。最后,将传动轴与驱动轴连接起来,形成多轴箱的传动系统。如图6.5所示。 图6.5 箱体钻孔组合机床的多轴箱传动系统图(2)确定驱动轴、主轴位置驱动轴的高度由动力箱联系尺寸图中查出,根据箱体钻孔组合机床多轴箱原始依据图,算出驱动轴、主轴坐标值,见表6.5。 表6.5 多轴箱主轴、驱动轴坐标值 (单位:mm)坐标驱动轴主轴1主轴2主轴3主轴4主轴5主轴6主轴7X11.39-70-70-4604625526.2Y187.0626011017010017053.08280.19(3)确定传动轴位置及齿数已知各主轴转速及驱动轴到主轴之间的传动比: 主轴 驱动轴 各主轴总传动比:=由于所有主轴的转速相同,则各主轴齿轮齿数与驱动轴齿轮齿数之比,即:多轴箱的齿轮模数按驱动轴齿轮估算 则由式(6.1)得:(3032)=321.43由于目前大型组合机床通用的主轴箱中常用的齿轮模数有2、2.5、3、3.5、4等几种,为了便于组织生产,本机床多轴箱输入齿轮模数和其余齿轮模数取相同,即。根据齿轮的传动比和模数初定驱动轴齿轮的齿数和各主轴齿数(各主轴齿数相同)分别为和=19,由图并得各传动轴上齿轮的齿数也为19。1)确定传动轴的位置及其与主轴1、2间的齿轮副齿数 传动轴的位置为主轴1、2同心圆的圆心,且在轴1、2连线的垂直平分线上,这里设轴的位置为=-50mm,=185mm。则中心传动轴的转速为,即。传动轴与主轴1、2的轴心距为:2)确定传动轴的位置及其与主轴3、4、5间的齿轮副齿数 传动轴的位置为主轴3、4、5同心圆的圆心,由于主轴3和5关于主轴4对称,所以计算得轴的位置为,。则中心传动轴的转速为,即。传动轴与主轴3、4、5的轴心距为:3)确定传动轴的位置及其与主轴6、7间的齿轮副齿数 传动轴的位置为主轴6、7同心圆的圆心,且在轴1、2连线的垂直平分线上,这里设轴的位置为,。则中心传动轴的转速为,即。传动轴与主轴6、7的轴心距为:4)确定液压泵轴的位置液压泵轴直接由传动轴上的19齿的齿轮驱动,R12-1A液压泵推荐转速为,因而,传动比为:则:液压泵轴齿轮齿数为 取液压泵的理论转速为液压泵轴与传动轴的轴心距为液压泵轴的齿轮与主轴6的齿轮在同一横截面上,应避免齿顶干涉,为计算方便,设液压泵轴的横坐标值为,则。箱体钻孔组合机床多轴箱的传动系统齿轮的配合如图6.6示。 图6.6 组合机床的多轴箱传动系统齿轮配合图5)确定手柄轴 由于各传动轴的转速相同,所以传动轴兼做调整的手柄轴,用于对刀或机床调整。各传动轴的坐标值见表6.6。表6.6 传动轴的坐标值传动轴编号轴轴轴(50,185)(0,150.11)(0,224)各传动副的中心距及其齿轮齿数见表6.7 表6.7 传动副的中心距(mm)及齿轮数 (单位mm)轴距代号 中心距38.6690.1450.1261.4739主动齿轮Z1919191919从动齿轮Z20202020206)验算各主轴的转速 使各主轴转速的相对损失在以内。(4)绘制传动系统图 传动系统图是表示传动关系的示意图,即用已确定的传动件将驱动轴和各主轴连接起来,绘制在多轴箱轮廓内的传动示意图,如图6.7所示。组合机床主轴数量多,为使传动系统图传动路线清晰可辨,必须标出传动齿轮在多轴箱内的轴向位置。一般情况下,多轴箱箱体内强可排放两排32mm宽或三排24mm宽的齿轮,第排距箱体前壁4.5mm;第排或32mm宽齿轮第排距箱体后壁9.5mm,第、或第、排24mm齿轮皆相距2mm。动力箱齿轮和驱动轴齿轮为第排。 图6.7 箱体钻孔组合机床多轴箱传动系统图6.2.4多轴箱的传动系统设计通用多轴箱的总图由主视图、展开图、装配表和技术要求等四部分组成。主视图和展开图见图6.8,图6.9。 IIIVIIIV图6.8 箱体钻孔组合机床多轴箱主视图1 主视图主要表明多轴箱的主轴、传动轴位置及齿轮传动系统。因此,绘制主视图就是在设计的传动轴系统图上,画出润滑系统,标出主轴、液压泵轴的转向,最低主轴高度及径向轴轴承的外径,以检查相邻孔的最小壁厚。主轴箱多数为标准件,如定位销及销孔结构尺寸,联接螺栓直径及数量,放油塞,注油杯等,在主视图中可示意画出或省略。2 展开图主要表示主轴、传动轴上各零件的装配关系。图中各个零件应按比例画出。对结构相同的同类型主轴和传动轴,可只画一根,但在轴端部须注明各结构相同的同类型主轴和传动轴号;对轴径相同,轴向结构基本相同,只是齿轮齿数及轴向位置不同的两根或两组轴,可合画在一起,即轴心线两边各表示一根或一组轴。展开图上还应标出箱体厚度和内腔有联系的尺寸。图6.9 箱体钻孔组合机床多轴箱展开图3 主轴和传动轴装配表 主轴箱内的零件数量很多,规格不一。把每根轴上的规格、尺寸和数量用装配表表示,不仅使图形清楚醒目,节省了设计的时间,而且有利于组织生产,装配方便,表的格式和内容见表6.8。主轴箱的技术条件在主轴箱总图上应注明主轴箱部装要求,包括:(1)主轴箱制造的技术条件(2)主轴精度等级(3)加入主轴箱的润滑油种类、数量。此外,还要注明必要的设计、装配、检验、调整和使用说明。攀枝花学院毕业设计 7 夹具设计7 夹具设计机床夹具设计在组合机床设计中占有重要的地位。它的好坏将直接影响工件加工表面的位置精度。本夹具主要是用来钻箱体端面分布的7个螺孔,整个需要加工的螺孔的位置尺寸用机床和夹具就能直接保证。因此,在本道工序加工时,主要应考虑如何保证垂直度要求的前题下,提高劳动生产率,降低劳动强度。为了很好利用工厂实际设备和提高生产率,设计专用夹具进行加工。由机械制造工艺系统的组成机床,工件,刀具和夹具可以看出夹具在机械加工中占有很重要的地位,尤其在成批生产时更是大量的采用机床夹具,它们是机床与工件之间的联接装置,使工件相对于机床或刀具获得正确位置,机床夹具的好坏将直接影响工件加工表面的位置精度,所以机床夹具设计是装备设计过程中的一项重要的工作,是加工过程中最活跃的因素之一。夹具设计是组合机床设计的重要步骤之一,夹具设计的基本原则是要保证产品质量、工作效率、人身及设备安全,以及整个生产的经济效果。夹具的设计应满足工件的生产批量,工件加工的精度等,还应该使夹具的结构简单,夹具定位夹紧过程,无过定位或欠定位等。71 机床夹具概论1 机床夹具的分类夹具的分类方法比较多,一般可分为通用夹具和专用夹具。近年来为适应现代机械制造业产品改型快、新品种多、小批量生产的特点,除使用专用夹具外,还发展了通用可调夹具、成组夹具和组合夹具等类型。(1)通用夹具 通用夹具是指已经标准化的,在一定范围内可用于加工不同工件的夹具。如三爪或四爪卡盘、机器虎钳、回转工作台、万能分度头、磁力工作台等。这些夹具已作为机床附件,可以充分发挥机床的技术性能并扩大它的使用范围。所以不论何种生产类型,都广泛使用。(2)专用夹具 专用夹具是指专为某一工件的某道工序的加工而设计制造的夹具。专用夹具一般在一定批量的生产中应用。(3)通用可调夹具和成组夹具 这两种夹具其结构很相似。它们的共同点是:在加工完一种工件后,经过调整或更换个别元件,即可加工形状相似、尺寸相近或加工工艺相似的多种工件。(4)组合夹具 组合夹具是指按某一工件的某道工序的加工要求,由一套事先准备好的通用的标准元件和部件组合而成的夹具。这种夹具用完之后可以拆卸存放,或重新组装新夹具时供再次使用。另外,按所适用的机床把夹具区分为车床夹具、铣床夹具、钻床夹具、镗床夹具和其它机床夹具等类型。2 机床夹具的组成(1)定位元件和定位装置 用于确定工件正确位置的元件或装置,如V形块、定位销,凡是夹具都有定位元件,它是实现夹具基本功能的元件。(2)夹紧元件和夹紧装置 用于固定工件以获得的正确位置的元件或装置。工件在夹具定位之后引进加工之前必须将工件夹紧,使其在加工时在切削力的作用下不离开已获得的定位,有时同一个元件既能定位,也具有夹紧的双重功效。(3)导向元件 确定刀具的位置并引导刀具的元件,它也可以供钻镗类夹具在机床上安装时做基准找正用。(4)夹具体 夹具体也称为夹具本体,用于将各种元件,装置连于一体,并通过它将整个夹具安装在机床上,一般采用铸铁制造,它是保证夹具的刚度和改善夹具动力学特性的重要部分。如果夹具体的刚性不好,加工时将要引起较大的变形和震动,产生较大的加工误差。72 问题的提出本夹具主要用来钻5个和2个分布在箱体端面孔上的孔,在本到工序加工时,主要考虑如何提高劳动生产率、降低劳动强度以及加工精度。73 夹具设计 1 定位基准的选择 在对箱体的结构分析及所要求加工的5个M10以及2个M16的螺纹孔所处的特殊位置,要达到了要求的精度并不困难,可以采用支承板以底面为主定位面,保证端面与底面之间的垂直度要求。定位是采用的“一面两销”(其中一个销为削边销,且其削边与两销中心连线垂直)限制X,Y方向的移动和旋转,限制6个自由度这样实现工件的完全定位。夹紧力由一个气动装
- 温馨提示:
1: 本站所有资源如无特殊说明,都需要本地电脑安装OFFICE2007和PDF阅读器。图纸软件为CAD,CAXA,PROE,UG,SolidWorks等.压缩文件请下载最新的WinRAR软件解压。
2: 本站的文档不包含任何第三方提供的附件图纸等,如果需要附件,请联系上传者。文件的所有权益归上传用户所有。
3.本站RAR压缩包中若带图纸,网页内容里面会有图纸预览,若没有图纸预览就没有图纸。
4. 未经权益所有人同意不得将文件中的内容挪作商业或盈利用途。
5. 人人文库网仅提供信息存储空间,仅对用户上传内容的表现方式做保护处理,对用户上传分享的文档内容本身不做任何修改或编辑,并不能对任何下载内容负责。
6. 下载文件中如有侵权或不适当内容,请与我们联系,我们立即纠正。
7. 本站不保证下载资源的准确性、安全性和完整性, 同时也不承担用户因使用这些下载资源对自己和他人造成任何形式的伤害或损失。

人人文库网所有资源均是用户自行上传分享,仅供网友学习交流,未经上传用户书面授权,请勿作他用。