后桥壳体零件的卧式三面单工位组合钻床设计
70页 22000字数+说明书+任务书+外文翻译+5张CAD图纸【详情如下】
中间钻模板总成.dwg
主轴箱总装图.dwg
任务书.doc
后桥壳体加工工序图.dwg
后桥壳体加工示意图.dwg
后桥壳体零件的卧式三面单工位组合钻床设计说明书.doc
外文翻译--数控技术和装备发展趋势及对策.doc
机床尺寸联系图.dwg
目录.doc


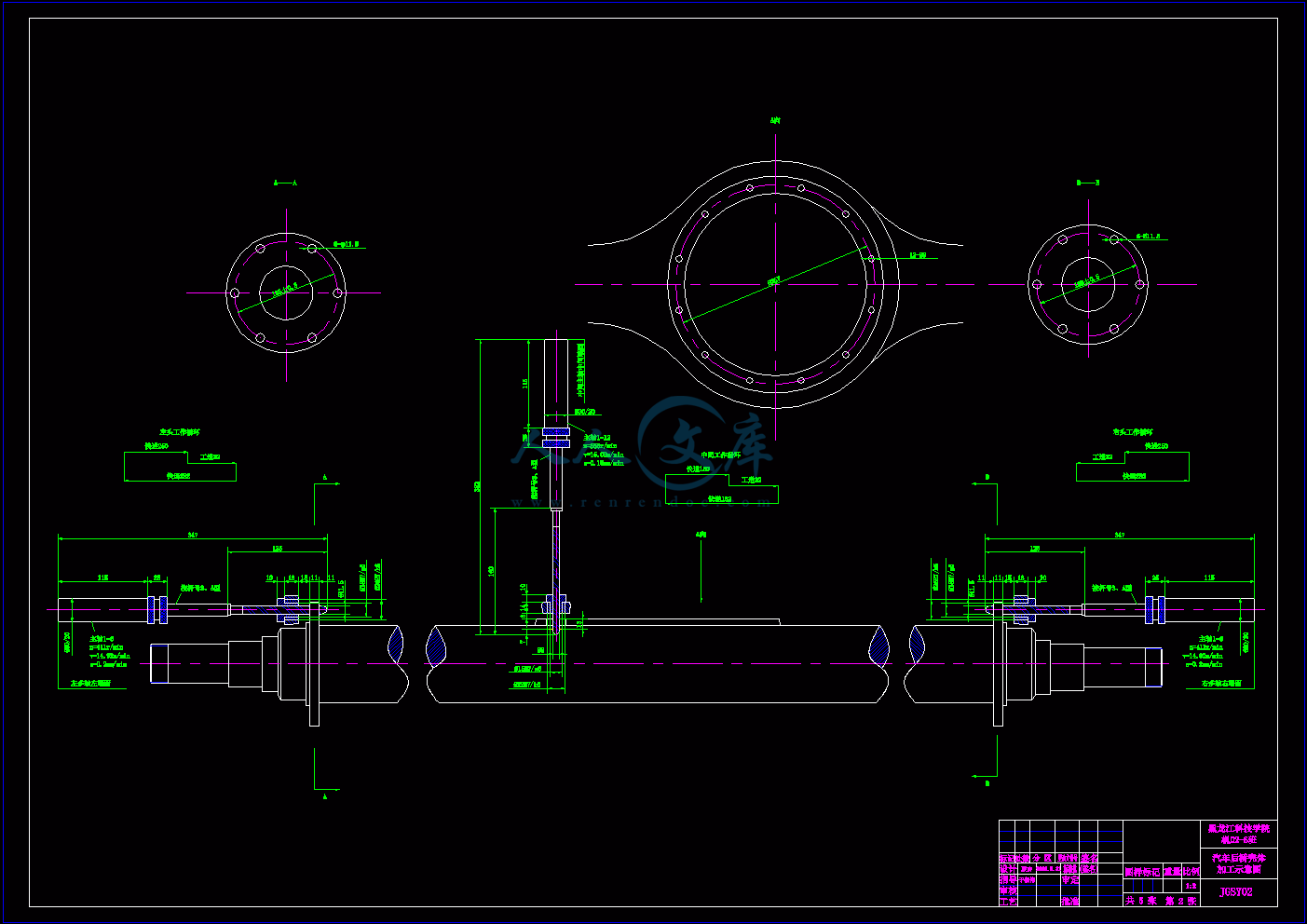
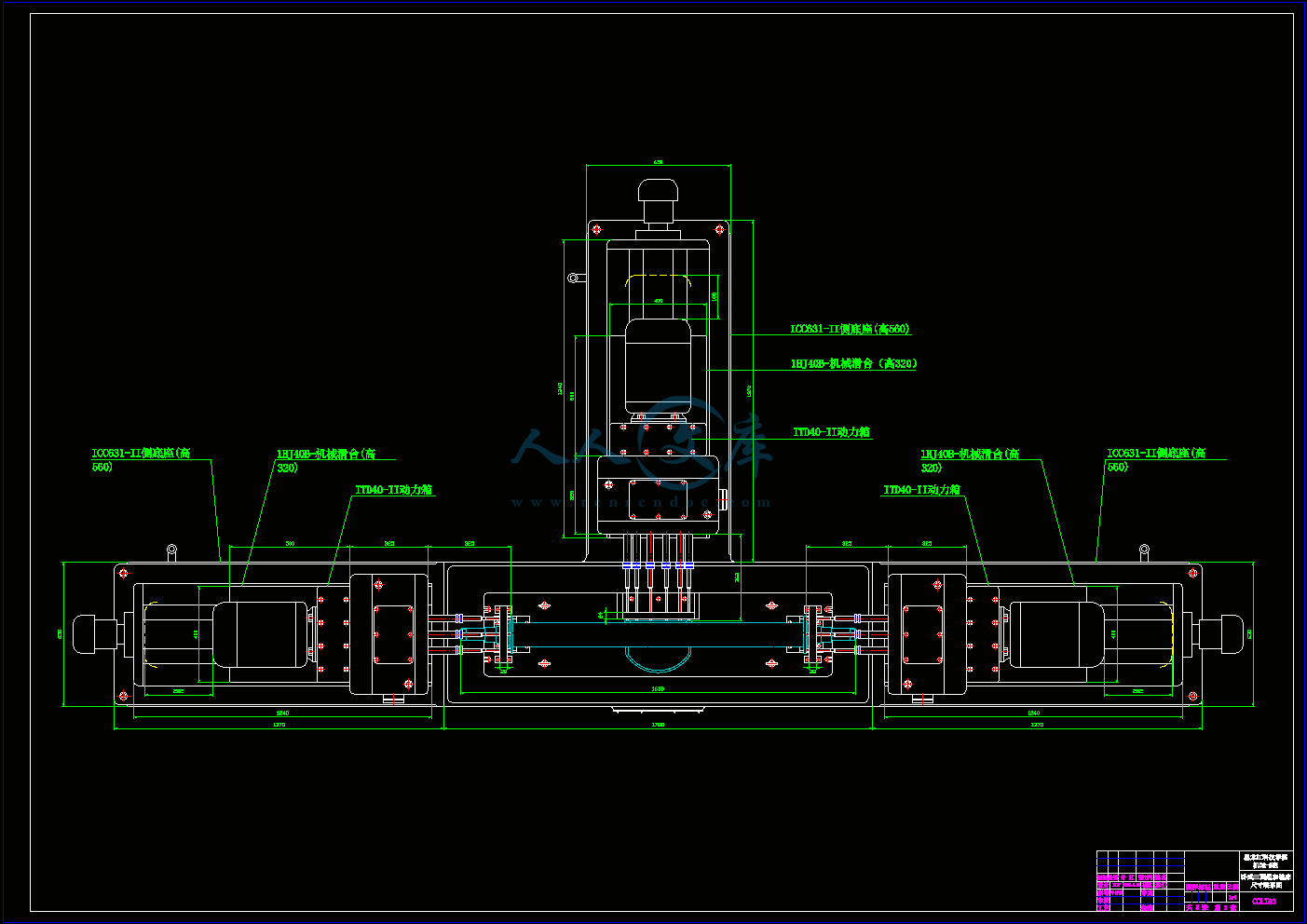


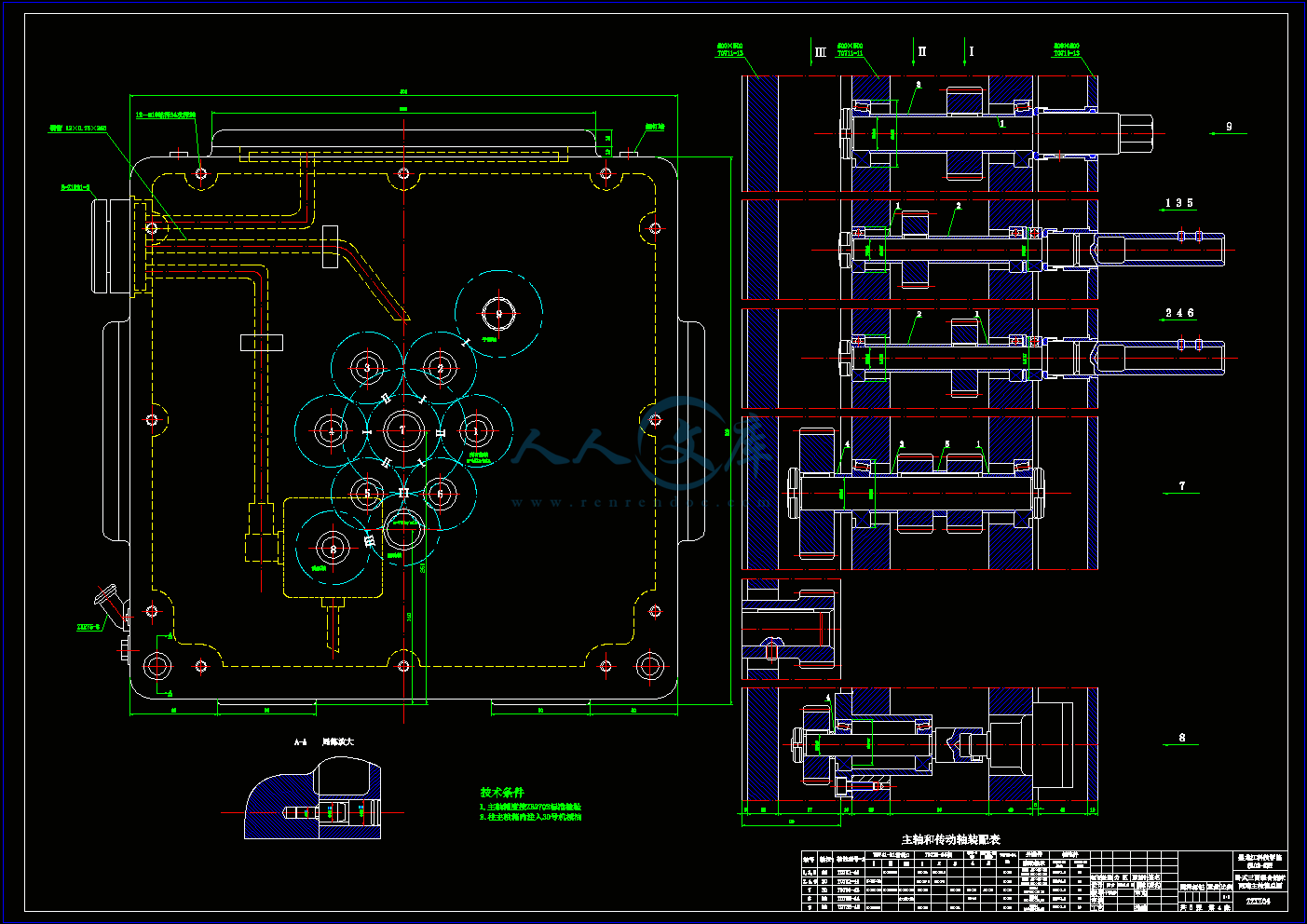
目 录
摘 要I
Abstract II
第1章 绪论 1
1.1 论文背景及研究意义 1
1.2 组合机床发展概况 1
1.2.1 组合机床的由来 1
1.2.2 组合机床技术装备现状与发展趋势 2
1.3 设计研究的主要内容 3
第2章 卧式三面组合钻床总体设计 4
2.1 组合钻床工艺方案的制定 4
2.1.1 工艺过程和加工精度的要求 4
2.1.2 加工零件的特点 4
2.1.3 定位基准及加压部位的选择 4
2.1.4 孔间中心距的影响 4
2.1.5 工件的生产方式 5
2.2 组合钻床配置形式及结构方案的确定 5
2.2.1 加工精度 5
2.2.2 机床生产率 5
2.2.3 被加工件的尺寸、形状、加工部位的特征 5
2.2.4 操作的方便性 5
2.2.5 夹具形式对机床方案的影响 5
2.3 主要参数的计算 5
2.3.1 确定切削用量、计算各主轴转速 5
2.3.2 确定切削三要素 7
2.4 组合机床总体设计 8
2.4.1 被加工零件工序图 8
2.4.2 加工示意图的设计 8
2.4.3 机床联系尺寸图的绘制13
2.4.4 经济性分析17
第3章 主轴箱设计21
3.1 主轴箱设计的原始依据21
3.2 主轴箱传动系统的设计及计算21
3.2.1 传动路线拟定思路23
3.2.2 分配传动比、初定传动轴位置、确定齿轮齿数24
3.2.3 修正各主轴转速、切削速度、主轴每转进给量27
3.3 主轴箱通用轴类零件选择28
3.3.1 确定传动轴的直径及选材28
3.3.2 主轴及通用传动轴结构型式的选择方案29
3.3.3 通用齿轮及其他通用件29
3.4 轴和齿轮的校核29
3.4.1 主轴的力学计算模型29
3.4.2 齿轮模数的验算36
3.5 主轴箱坐标的计算38
3.5.1 主轴箱坐标系原点的确定38
3.6 变位齿轮设计45
第4章 夹具设计47
4.1 定位支承系统设计47
4.1.1 定位支承系统的设计原则47
4.1.2 定位支承元件及其布置47
4.2 导向装置设计48
4.2.1 导向装置的作用48
4.2.2 导向装置的类型选择48
4.2.3 固定式导套的设计48
4.3 夹紧机构设计49
4.3.1 夹紧方案的确定49
4.3.2 夹紧力的计算49
第5章 专题52
5.1 确定毛坯的制造形式52
5.1.1 车桥焊接工艺52
5.1.2 汽车后桥焊接设备52
5.1.3 基准的选择52
5.2 工艺路线的拟定52
5.3 机械加工余量,工序尺寸及毛坯尺寸的确定53
结束语 62
致 谢 63
参考文献 64
摘 要
本次设计从企业实际需求出发,在全面分析被加工零件的结构特点、尺寸精度、被加工孔相互之间位置精度、表面粗糙度和技术要求的基础上,指出采用现有设备不仅工人劳动强度大,生产率低,而且零件加工精度难以保证。根据实际需要,研制出了卧式三面单工位组合钻床。
本文首先通过分析比较,确定了卧式三面单工位组合钻床的配置型式及结构的最佳方案,遵循机械设计中标准化、通用化、系列化原则,给出机床的总体设计,按照设计组合机床“三图一卡”的原则绘制出代表机床总体设计的被加工零件工序图、加工示意图、机床联系尺寸图和生产率计算卡。由于在本台组合钻床上需同时加工三个部位共24个孔,不仅孔多、间距小,采用常规方法排箱无法实现三个加工部位孔的工序集中的加工方案。本钻床的主轴箱传动系统通过采用变位齿轮和滚珠轴承等结构方面的创新设计,将常规方法下不能完成的排箱成为可能
关键词: 组合钻床、主轴箱、夹具设计、传动设计
Abstract
In view of the actual conditions of enterprises and on the basis of
overall analysingworkPiece structure features,accuracy of size,surface roughness,accuracy of distance between drilled holes and other technical requirements,this article Points out that the existing equipments used to manufacture work Pieces may result in lower Productivity,greater intensity of labor and worse working accuracy. Therefore,it 15 necessary to develop a new type of 24hole single working Position combination drilling machine.
Through analysis and comparison,the article has determined the best
Project ofthestructure and the disposition of the 24 holes combination drilling machine. According to the Principle of standardization,generalization and serialization in machine design,the article offers the master design of the drilling machine,the Process drawing of
work Piece,the working diagram,the connection dimensional drawing of
The drilling machine and the calculating card of Productivity. In some key Parts of the drilling machine,there are certain new designs on the structure of the spindle box and the fixture .With 24hole drilled simultaneously on the drilling machine,in addition to small Spacing between holes and dispersive arrangement of hole Position,the 24 holes drilling Program cannot be completed in conventional way. In the transmission system of 24 hole drilling machine are used some new structural designs such as Pin bearings and Position一changeable gears,50 that the arrangement of hole Position,which cannot be finished in conventional way,can be accolllPlished.The combination drilling machine 15 applied a fast spiral Pinch machinery whose features are not only shortens the time consumed in loading and unloading work Piece but also enhances Productivity.
Key words:Combination drilling machine Spindle box