绞车实验台设计(液压系统)
83页 45000字数+说明书+10张CAD图纸【详情如下】
任务书.doc
实验台装配图.dwg
导向套A3.dwg
摘要.doc
毕业设计封面.doc
油箱A3.dwg
油箱支架A3.dwg
泵站装配图A0.dwg
活塞A3.dwg
活塞杆A3.dwg
液压缸装配图A0.dwg
目录.doc
端盖A3.dwg
绞车实验台设计(液压系统)说明书.doc
缸筒A2.dwg

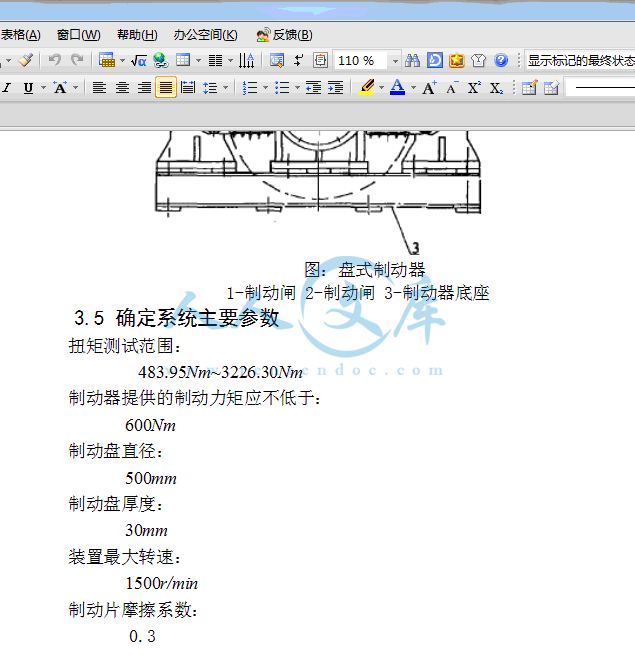
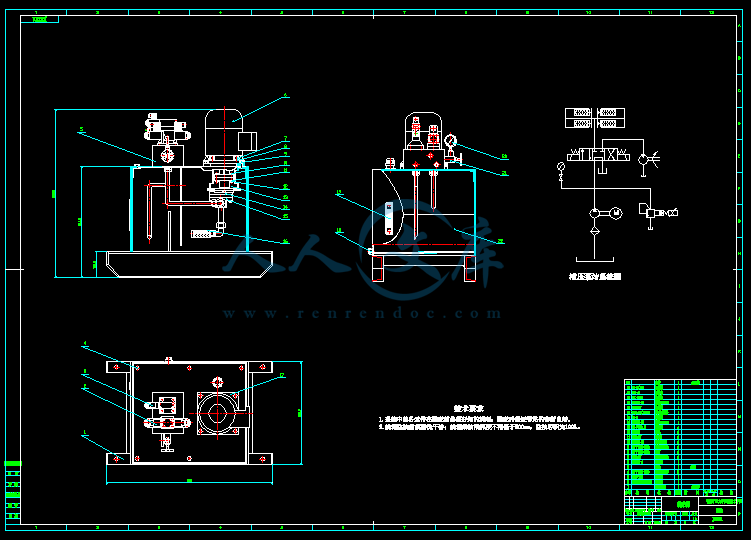
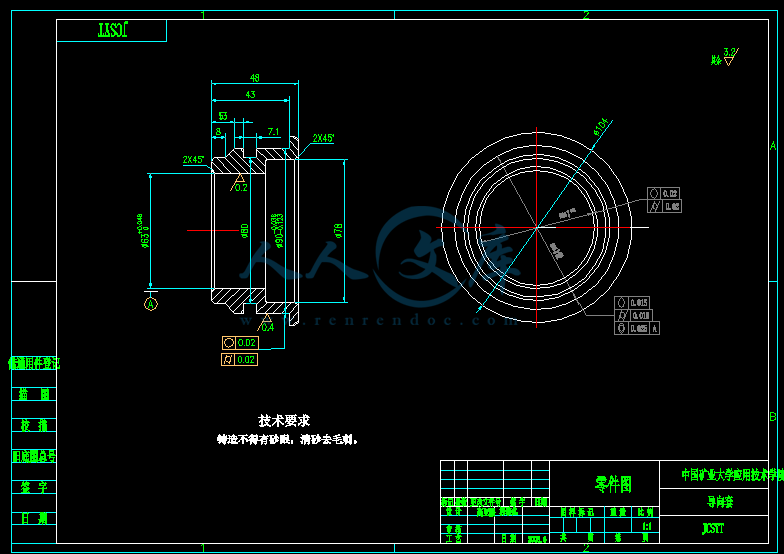
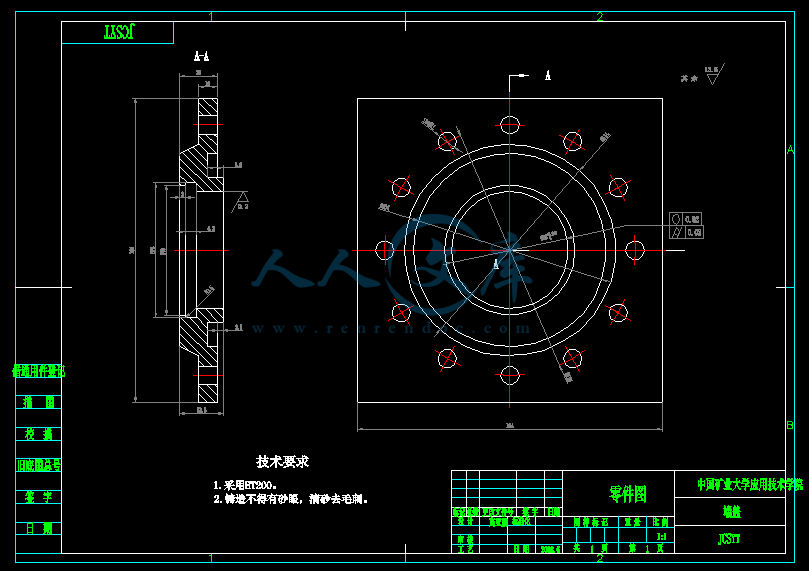

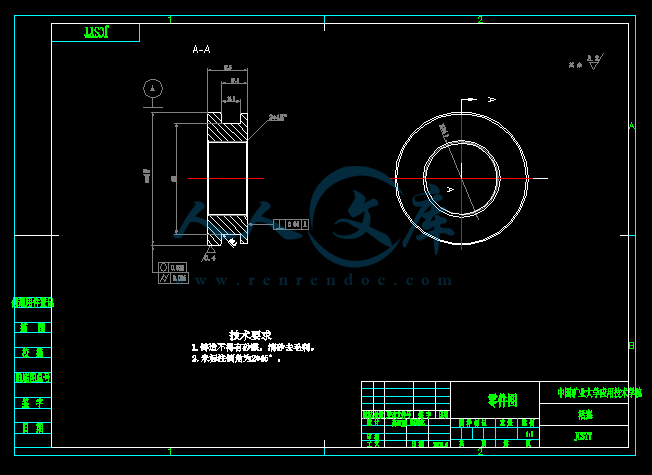


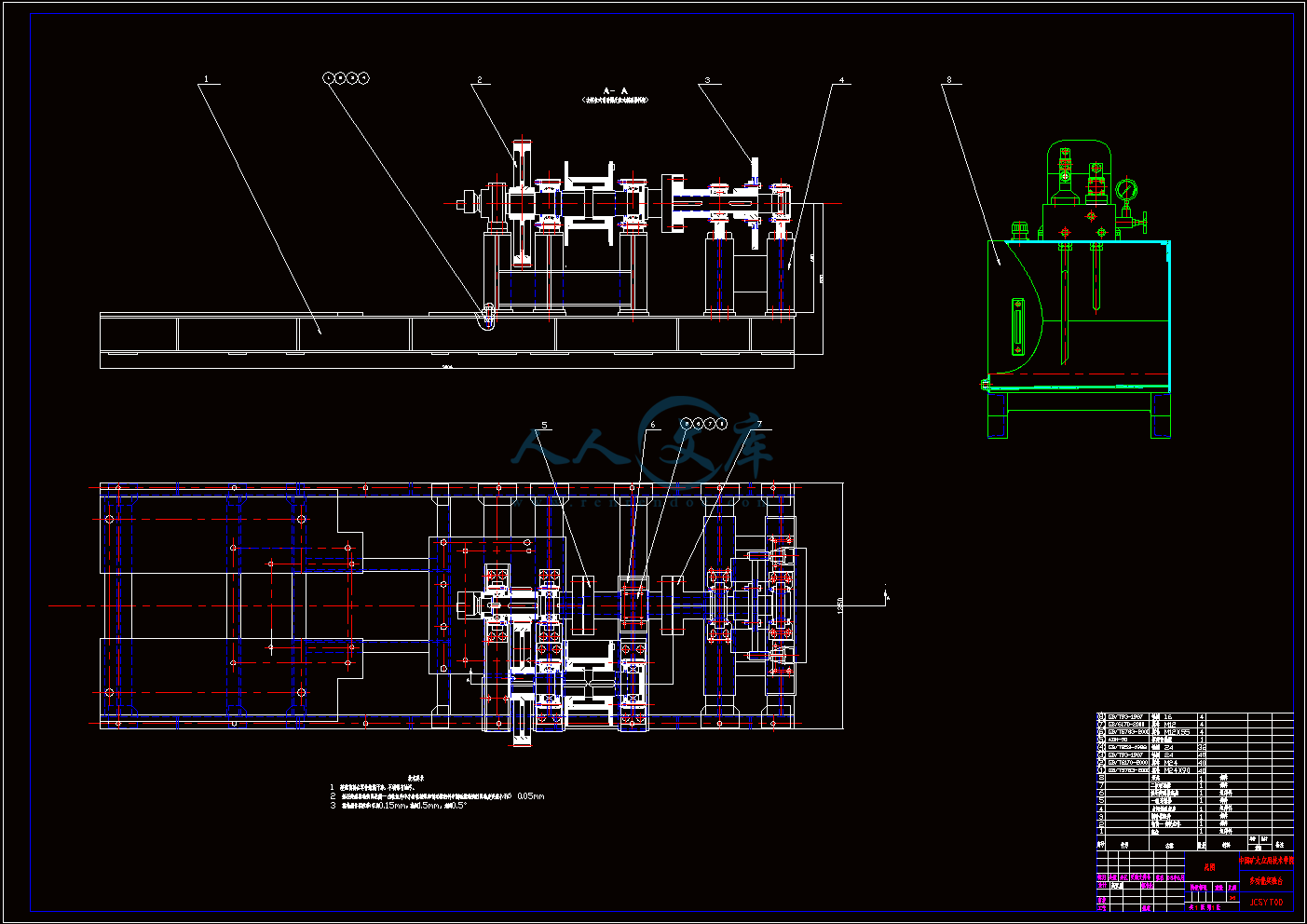
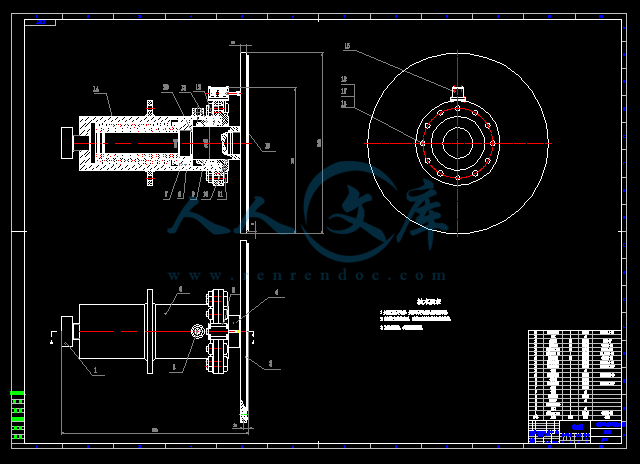
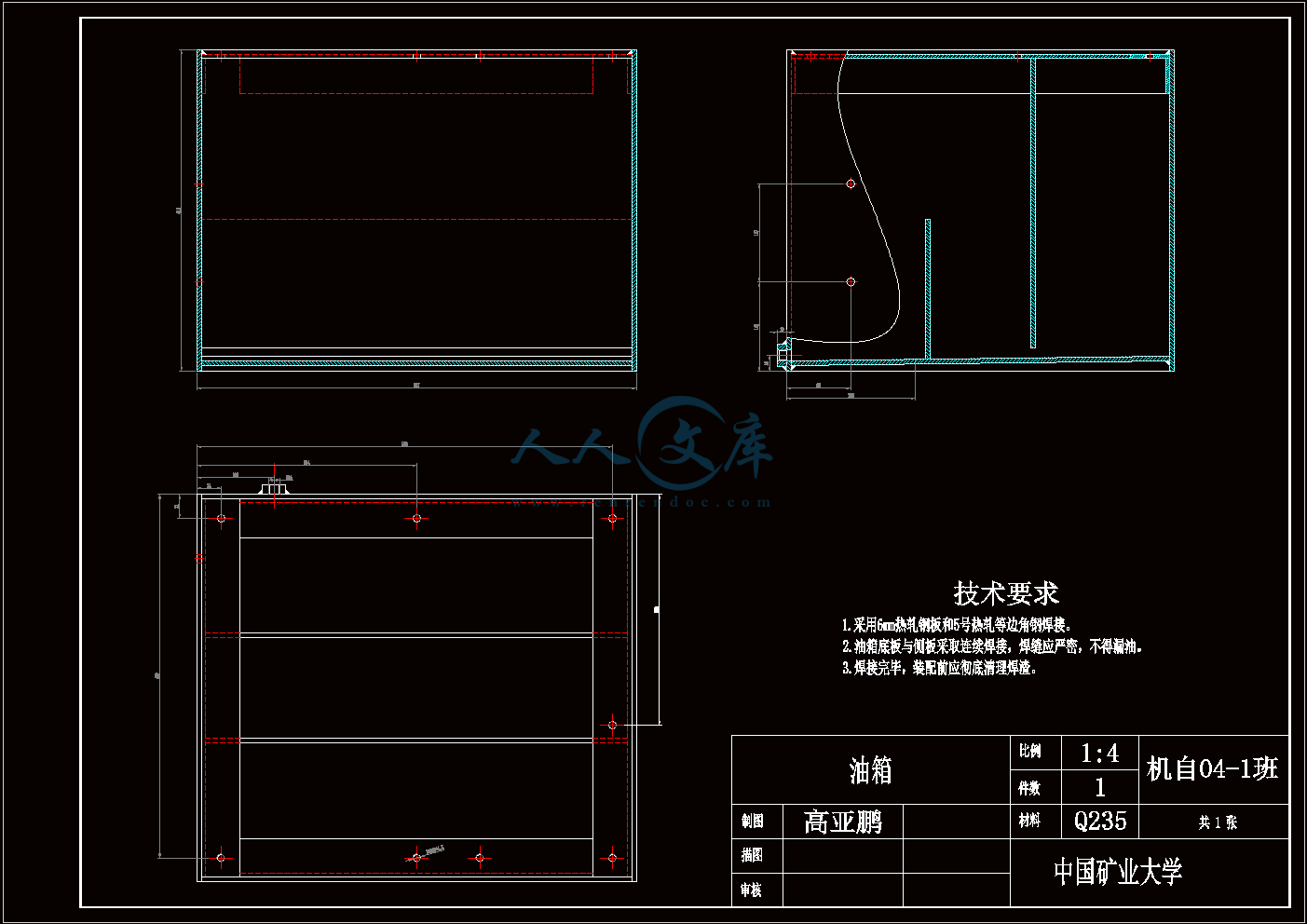

目录
1 绪论1
1.1矿井提升在矿山生产中的地位1
1.2矿井提升设备的现状与发展趋势1
1.3 液压系统1
2液压系统的设计3
2.1液压系统的使用要求及速度负载分析3
2.1.1使用要求3
2.1.2速度负载分析3
2.2液压系统方案设计4
2.2.1确定回路方式4
2.3液压系统各元件概述7
2.3.1液压执行元件的选择7
2.3.2液压控制元件的选定7
2.3.3泵的选型7
2.3.4系统中管路的选定9
2.3.5电机的选用9
3 制动系统整体方案确定10
3.1 制动器的类型选择原则10
3.2 制动器规格的计算原则11
3.3 制动器校核验算原则11
3.4 制动器方案确定11
3.5 确定系统主要参数12
4 碟形弹簧设计13
4.1 参数计算13
4.2 碟形弹簧设计:13
4.2.1 碟形弹簧的特点及应用13
4.2.2 碟形弹簧的材料及成型后的处理13
4.3碟形弹簧的计算14
4.4 碟形弹簧校核16
5 液压缸主要技术性能参数的计算17
5.1常用液压缸17
5.1.1活塞式液压缸17
5.1.2柱塞式液压缸17
5.2其它形式液压缸18
5.2.1伸缩液压缸18
5.2.2齿条活塞液压缸18
5.2.3增压缸(增压器)18
5.2.4增速缸18
5.3液压缸主要参数的设计计算19
5.3.1液压缸的特征尺寸19
5.3.2 液压缸工作压力的确定20
5.3.3 活塞杆21
5.3.4 缸筒22
5.4 液压缸的校验26
5.4.1缸筒壁厚验算26
5.4.2 活塞杆强度验算29
5.4.3液压缸的稳定性验算29
5.5缸体组件及连接形式30
5.5.1缸体组件30
5.5.2缸体组件的连接形式30
5.6活塞组件及连接形式31
5.6.1活塞组件31
5.6.2活塞组件的连接形式31
5.7密封装置33
5.7.1 O形密封圈33
5.7.2Y形密封圈34
5.8缓冲装置35
5.8.1圆柱形环隙式缓冲装置35
5.8.2圆锥形环隙式缓冲装置36
5.8.3可变节流槽式缓冲装置36
5.8.4可调节流孔式缓冲装置36
5.9排气装置36
6 液压泵的设计计算与选型37
6.1液压泵的分类37
6.2液压泵选择38
6.3 齿轮泵分类与工作原理:38
6.4 外啮合齿轮泵结构组成39
6.5 液压泵的参数计算39
7 泵站电机的计算与选型42
7.1泵的驱动功率42
7.2泵站电机的选型及安装42
7.2.1泵站电机的选型42
7.2.2电动机的安装形式43
7.2.3联轴器43
7.2.4泵组底座43
7.2.5管路附件43
8 液压马达44
8.1液压马达概述:44
8.2液压马达的分类:44
8.2.1高速液压马达:44
8.2.2低速液压马达:45
8.3液压马达特性参数:45
8.3.1工作压力与额定压力:45
8.3.2流量与容积效率:45
9 液压阀的设计与选型46
9.1 阀块的设计46
9.1.1 设计阀块时应注意事项:46
9.1.2 液压阀块的结构46
9.1.3 液压阀块设计46
9.2 溢流阀49
9.3 换向阀50
10 液压辅助元件选择与设计52
10.1 过滤器的选择52
10.1.1 选择过滤器的基本要求和应考虑的项目53
10.1.2 过滤器的主要性能包括:54
10.1.3过滤器的主要类型54
10.2 油管和管接头的选择55
10.2.1 油管的选择55
10.2.2 管接头的选择56
10.3 油箱的设计和计算56
10.3.1 概述56
10.3.2油箱的构造和设计要点57
10.3.3 油箱结构辅助元件设计:57
10.3.4 油箱的设计:60
10.4 液压泵组的连接和安装方式62
11 液压系统的安装、使用和维护64
11.1 液压系统的安装64
11.2 调试70
11.3 液压系统的合理使用71
11.4 保养73
结 论75
参考文献:76
英文原文77
中文译文81
致 谢85
摘 要
矿井提升设备是沿井筒提升矿石、废石、升降人员和设备、下放材料的大型机械设备。它是矿山井下生产系统和地面工业广场相连接的枢纽、是矿山运输的咽喉。因此,矿井提升设备在矿井生产全过程中占有及其重要的地位。
随着科学技术的发展及生产的机械化和集中化,目前,世界上经济比较发达的一些国家,提升机的运输速度已达,一次提升量达到,电动机容量已经超过,其安全可靠性尤为突出。在矿井生产过程中,如果提升设备出现了故障,必然会造成停产。轻者,影响矿石产量,重者,则会危及人身安全。
此外,矿山提升设备是一大型的综合机械-电气设备,其成本和耗电量比较高,所以,在新矿井的设计和老矿井的改建设计中,确定合理的提升系统时,必须经过多方面的技术经济比较,结合矿井的具体条件,保证提升设备在选型和运转两个方面都是合理的,即要求矿井提升设备具有经济性。
液压系统主要由动力元件、执行元件、控制元件、辅助元件及传动介质五大部分组成。具有以下特点:通过能量的相互转换在运行过程中具有平稳无间隙传动功能,以实现大范围的无级变速,简化传动;可自动循环工作、自动过载保护;在同等功率输出情况下,液压传动装置具有体积小、质量轻、运动惯性小、动态性能好等特点;由于油作为传动介质,液压元件具有自我润滑作用,寿命延长,且液压元件都是标准化、系列化产品,便于互换和推广应用。
关键词:矿井提升设备;液压系统
ABSTRACT
Mine is along the shaft upgrade equipment upgrade ore, waste rock, the movements of personnel and equipment, the decentralization of large-scale machinery and equipment. It is mine and mine production systems connected to the ground at the industrial hub of the transport is mine throat. Therefore, upgrading equipment in the mine shaft in the whole process of production and occupy an important position.
With the development of science and technology and production mechanization and decentralization, at present, the world economy is relatively developed in some countries, upgrading the transport plane has speed, the first upgrade of reach, the motor has exceeded capacity, particularly in its security and reliability. Mine production in the process of upgrading equipment if a fault, will inevitably cause shutdown. Light, the impact of ore production, weight, will endanger their personal safety.
In addition, the mine is a major upgrade of equipment and Machinery - electrical equipment, the cost and power consumption is relatively high, therefore, the design of the new and old mine shaft into the design, determine a reasonable upgrade system, must go through various technical Economy, with the specific conditions of the mine to ensure that upgrading equipment in the selection and operation of the two aspects are reasonable, which called for mine equipment upgrade of an economic nature.
The main driving force from the hydraulic system components, the implementation of components and control devices, components and auxiliary transmission medium five major components. Has the following characteristics: the conversion of energy in the process of running a smooth seamless transmission functions, in order to achieve a wide range of CVT, simplifying transmission; automatically cycle work, automatic overload protection; power output in the same circumstances, the hydraulic Transmission device with small size, light weight, small movement of inertia, good dynamic performance characteristics as a transmission medium because of oil, hydraulic components are self-lubricating, life extension, and hydraulic components are standardized, and serialization of products, facilitate inter - For the promotion and application.
Key words: mine upgrade equipment; hydraulic system