菌类培养袋分离机构设计
45页 13000字数+说明书+实习报告+开题报告+外文翻译+3张CAD图纸【详情如下】
内封.doc
实习报告.doc
摘要.doc
机械外文翻译--现场测量的作用.doc
目录.doc
菌类培养袋分离机构装配图.dwg
菌类培养袋分离机构装配图.exb
菌类培养袋分离机构设计开题报告.doc
菌类培养袋分离机构设计说明书.doc
轴零件图.dwg
轴零件图.exb
齿轮零件图.dwg
齿轮零件图.exb


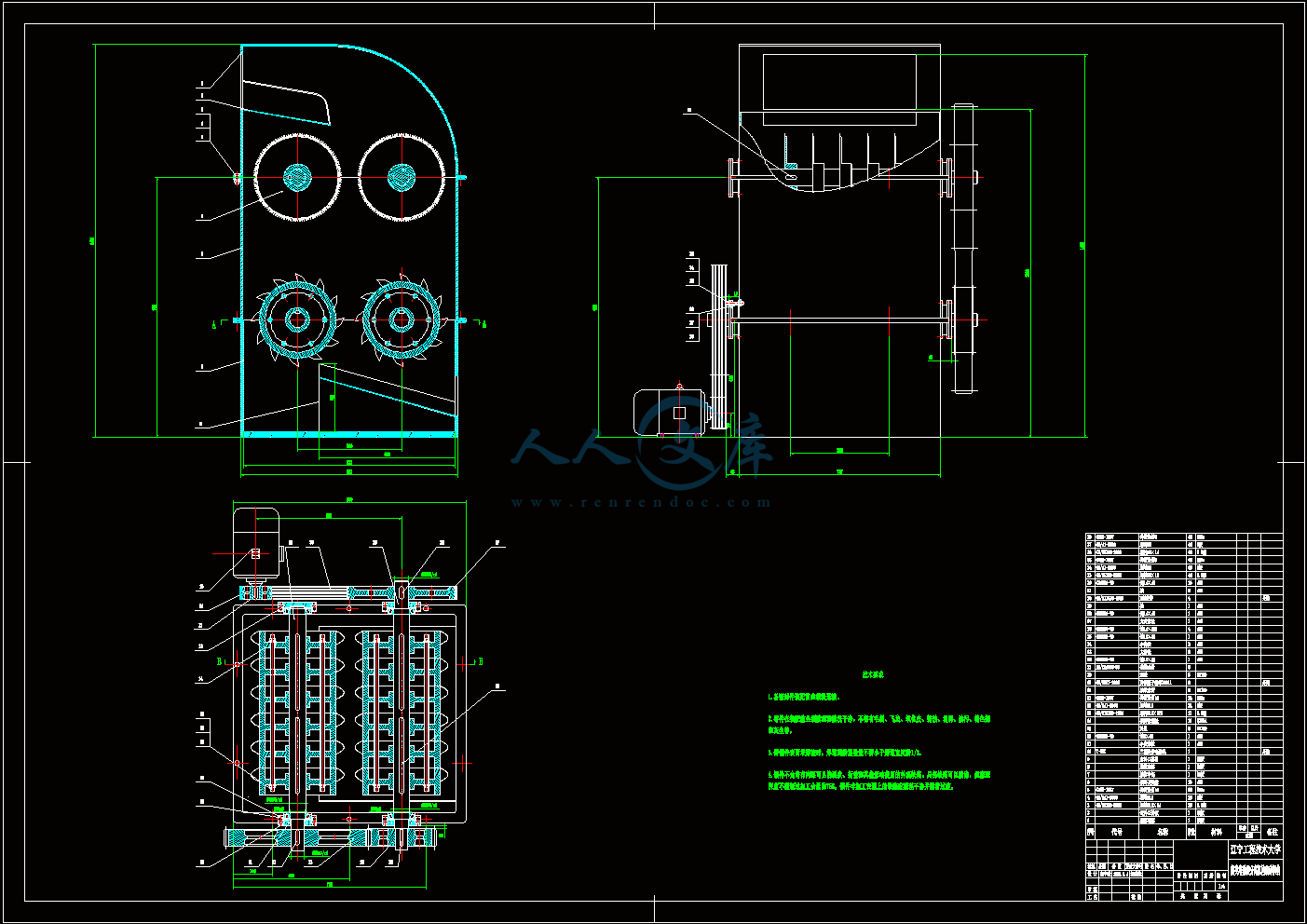
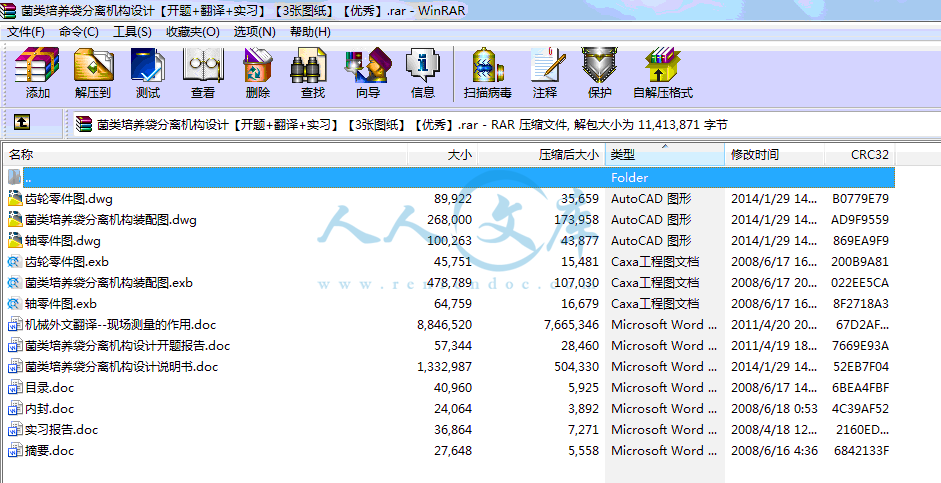
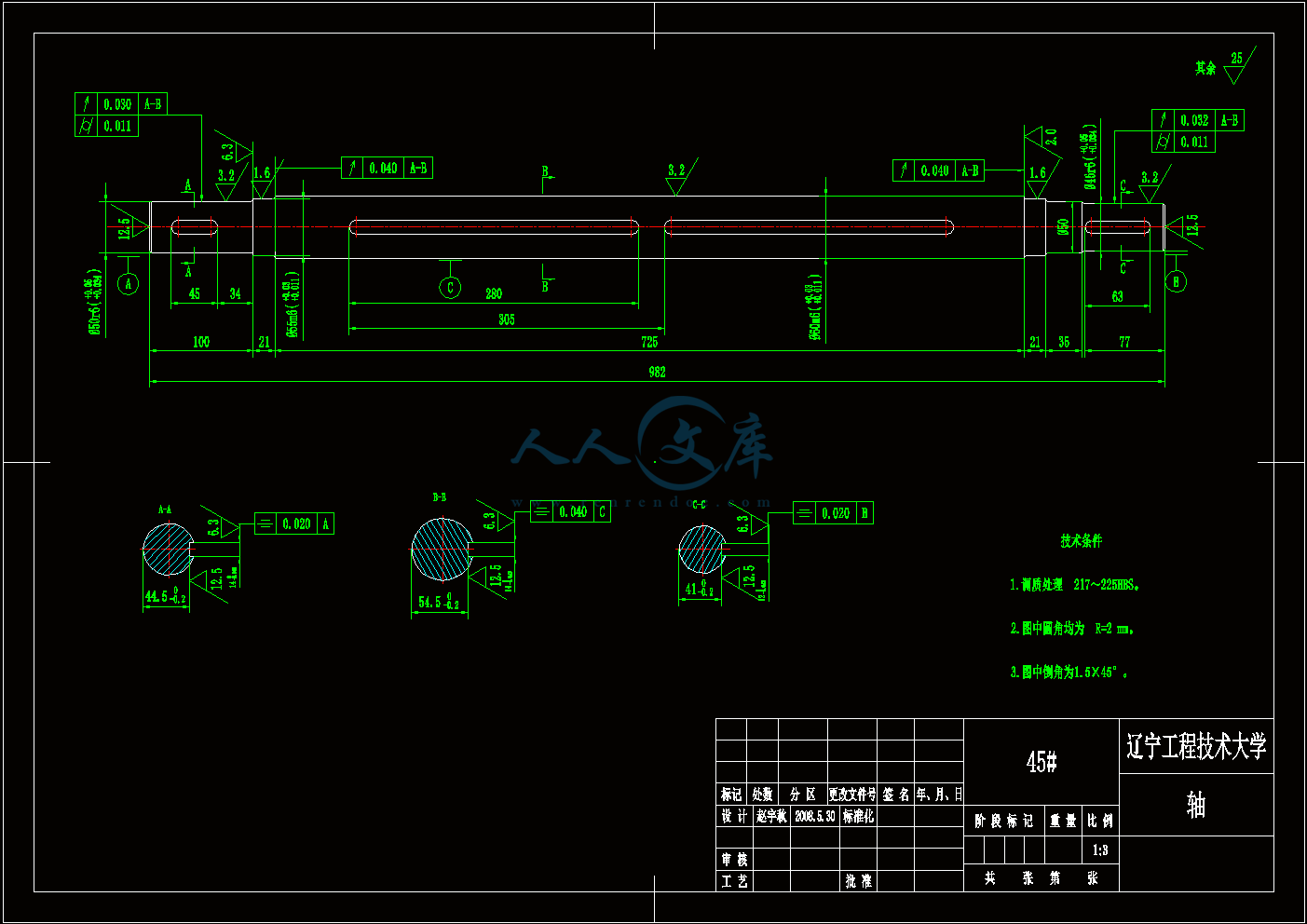
目录
前言1
1培养袋破碎机构的简介3
1.1关于蘑菇培养袋与培养基分离措施的分析3
1.2培养袋破碎机构的工作原理3
2破碎机构的结构尺寸5
2.1箱体尺寸的确定5
2.2工作机构部分尺寸的确定6
2.2.1破碎齿辊轮结构的分析6
2.2.2破碎齿辊轮尺寸的确定8
2.2.3破碎刀具轮的尺寸确定9
3选取电机11
3.1选择电动机系列11
3.2选择电动机功率11
4各轴段轴径的确定13
5轴承型号的选择15
6 V带传动的设计计算16
6.1确定设计功率16
6.2选择带型16
6.3确定小带轮基准直径16
6.4确定大带轮基准直径17
6.5验算带的速度17
6.6初定中心距18
6.7计算基准长度18
6.8计算实际中心距18
6.9计算小带轮包角19
6.10确定V带根数19
6.11确定单根V带的预紧力21
6.12计算作用在轴上的压力21
6.13带轮材料和结构的确定22
6.14带轮结构尺寸的确定22
7齿轮尺寸的确定:24
7.1选择齿轮材料24
7.2按齿面接触疲劳强度设计计算24
7.3齿根弯曲疲劳强度校核计算28
7.4齿轮其他尺寸的计算29
8各轴段长度的确定31
9键的选择及强度校核32
9.1键的选择32
9.1.1键联接的定义及分类32
9.1.2键联接的选择32
9.2键的强度校核33
9.2.1键尺寸的确定33
9.2.2键强度的校核34
10结论38
致谢39
参考文献40
附录A41
附录B52
摘要
目前,随着我国人民的文化生活和物质生活的提高,人们对精神生活的要求也越来越高。其中对饮食的享受就占很大的比列。众所周知,蘑菇的味道十分鲜美,并且深受大家的喜爱。据了解蘑菇已经是世界上人工栽培最广泛,消费量最大的食用菌。但是在蘑菇的培养过程中,却产生了很多急需解决的问题。就拿如何处理用完的培养袋和培养基这个问题来说,我们就会发现其中有很大的研究价值。
本文对如何去分离培养袋和培养基并进行回收进行了综合阐述,对分离培养袋和培养基的方法进行了分析和研究;经过仔细的论证,确定了培养袋分离机构的具体方案。结合常用农用机械中的破碎机构以及矿山双齿辊破碎机的机构,对分离机构的破碎部分进行设计,形成了具有自己特色的破碎工作机构。
该破碎机构可以很方便的将培养袋和培养基分离,并能节省大量的人力和物力,而且也能为很多蘑菇种植场创造出额外的利润。极大的增大了蘑菇培养袋和培养基的回收和利用的效率,对防止造成“白色污染”,节约资源起到了很大的作用。
关键词:培养袋;破碎;齿辊;物料
蘑菇培养袋为食品级塑料袋,比一般塑料较硬,而培养基为锯末等混合物,凝结成块并与培养袋粘在一起。要想将培养袋与培养基分开,就必须采取某种措施使培养基与培养袋不再黏粘在一起,并使凝聚成块的培养基变成很小的颗粒状;若要实现这种想法,可有很多种方式,绞、切、磨、挤,等等。
若是通过绞碎的方式分离培养袋和培养基,虽然破碎效果较为明显,但是生产效率比较低,而且容易使塑料和培养基的颗粒相当,不易分开,所以用绞碎的方式不合理;若是用切割的方式去分离,虽然保持了培养袋较大的颗粒状,但是由于培养基与培养袋之间的黏着,很难将两者彻底分开,所以用切割的方式也不合理;若是采用磨碎的方式,则机器结构会很复杂,而且要求也比较高,造价也会很高,所以不宜采用磨碎的方式;挤压分离的方式,虽然结构相对简单,但是工作效率低,而且不能保证每个培养袋都能被分开,所以也不宜用这种方式。综合来看,若是将切割和挤压这两种方式结合起来,破碎效果则非常显著。
这种方式是将培养袋用某种刀具破碎开来,然后通过挤压的方式使培养袋与培养基不再粘结,培养基不再凝聚成块,最后用振动的方式即可让破碎后的培养袋与培养基分开。根据实地考察,收完蘑菇后的培养袋一般比较柔软潮湿,可先放在空旷处进行晾晒,便于进行破碎工作。对于,蘑菇培养袋这种比较柔软的东西,不宜整体挤压破碎,但是若采用刀具先将培养袋切割成段状,然后再进行挤压就十分容易使培养基与培养袋之间不再黏着,也可使培养基不在凝聚成块并被磨成较小的颗粒,而破碎后的培养袋与培养基的混合物料通过振动的方式便可轻松分开。所以设计的分离机构可以分成两部分:破碎部分和筛分部分。而我重点设计的部分就是破碎部分。
1.2 培养袋破碎机构的工作原理
对于培养袋的破碎机构主要是参考煤矿破碎机工作机构的工作原理去设计,它的主要优点是:结构简单,机体紧凑轻便,价格低廉,工作可靠,调整破碎比比较方便。缺点是:生产能力较低,要求将物料均匀连续地喂到破碎轮全长上,否则破碎轮磨损不均,且所要破碎的物料也不易均匀,需要经常修理。
破碎机构的工作部分如图1.2-1所示,该部分主要由两对轮组成:上面的一对轮装有锯齿形刀具,目的是为了将培养袋切割成条段状;下面一对轮是表面比较粗糙的辊轮,用于进行二次破碎,通过挤压力使培养基与培养袋之间没有黏着力,并使本来凝聚成块的培养基变成很小的颗粒物。另外一方面该工作机构的上下两对轮的左右两部分的转速也是不同步的,正因如此,左右两轮之间形成了一个“搓”力,“切”的力与“搓”的力、“挤”
的力与“搓”的力两者的相互叠加使破碎效果更加显著,也让后期的筛分工作变得十分简单。