四工位的卧式组合机床设计及其控制系统设计
32页 16000字数+说明书+12张CAD图纸【详情如下】
7工艺简图.dwg
A0多轴箱.dwg
A0机床联系尺寸总图.dwg
A0钻床卡具.dwg
A1多轴箱检查图.dwg
A2PLC梯形图.dwg
A2加工示意图.dwg
A2液压系统图04.dwg
A2电气图.dwg
A3生产率计算卡.dwg
半轴零件图.dwg
四工位的卧式组合机床设计及其控制系统设计说明书.doc
摘要.doc
被加工零件工序图.dwg
说明书.doc





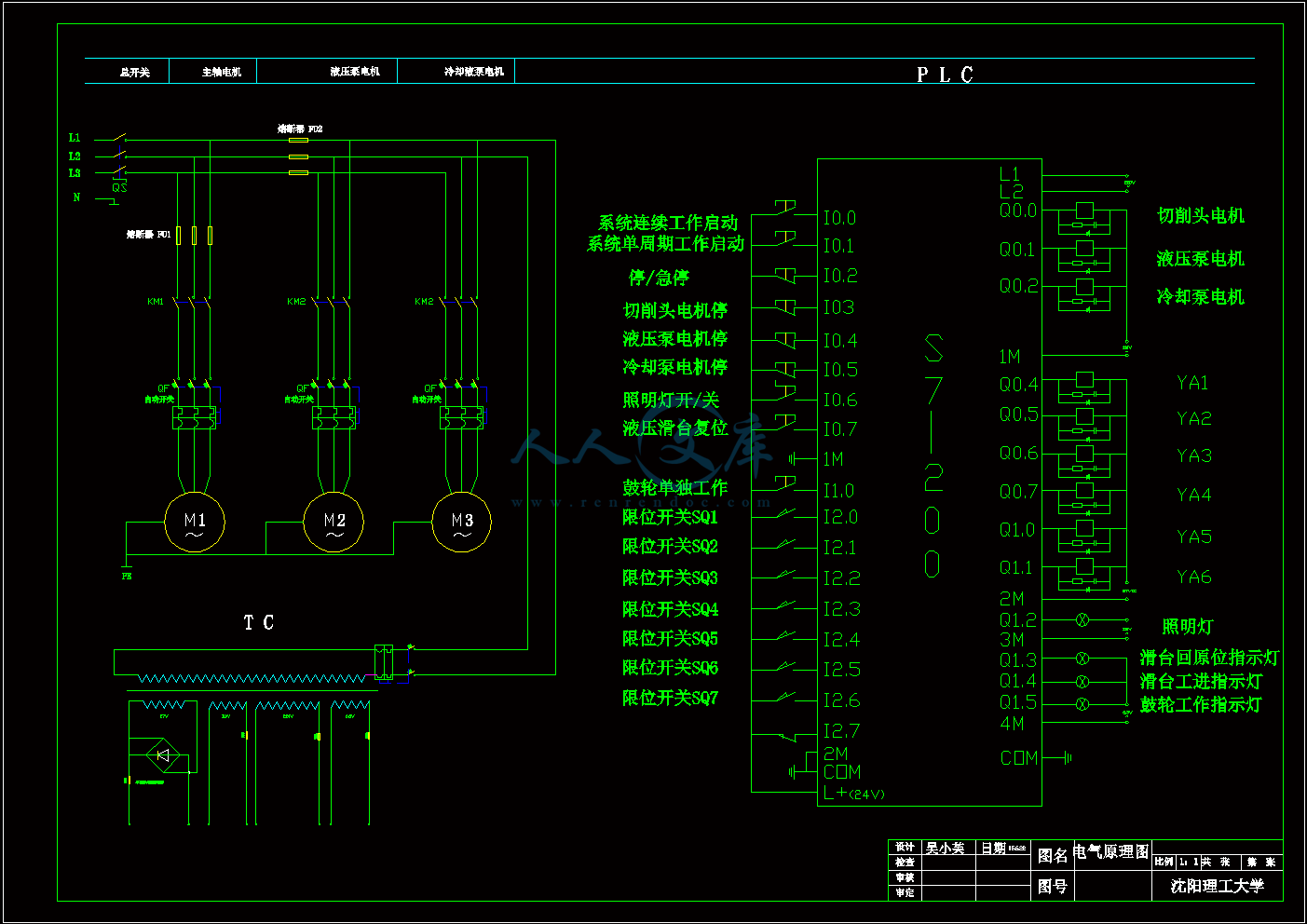

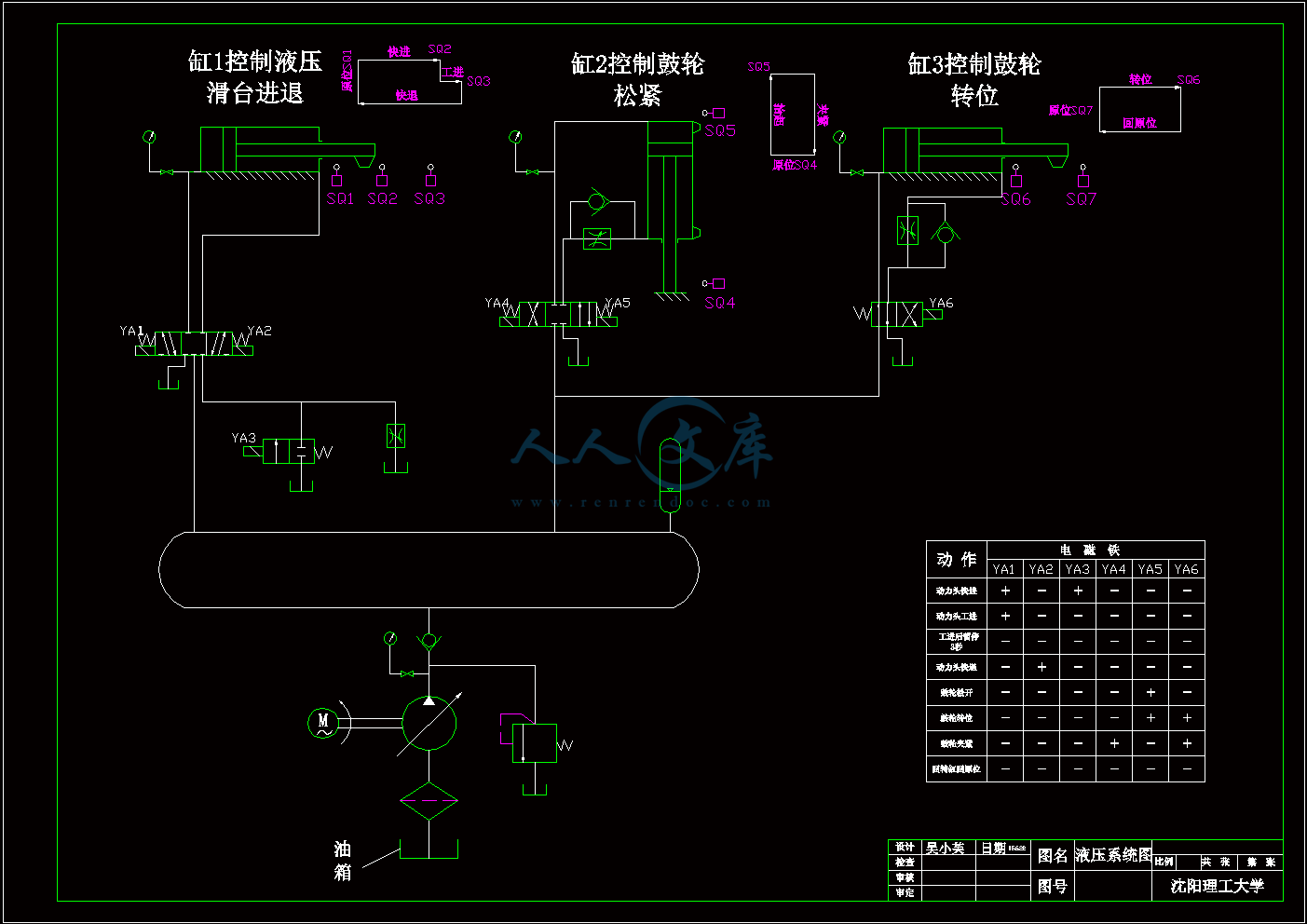
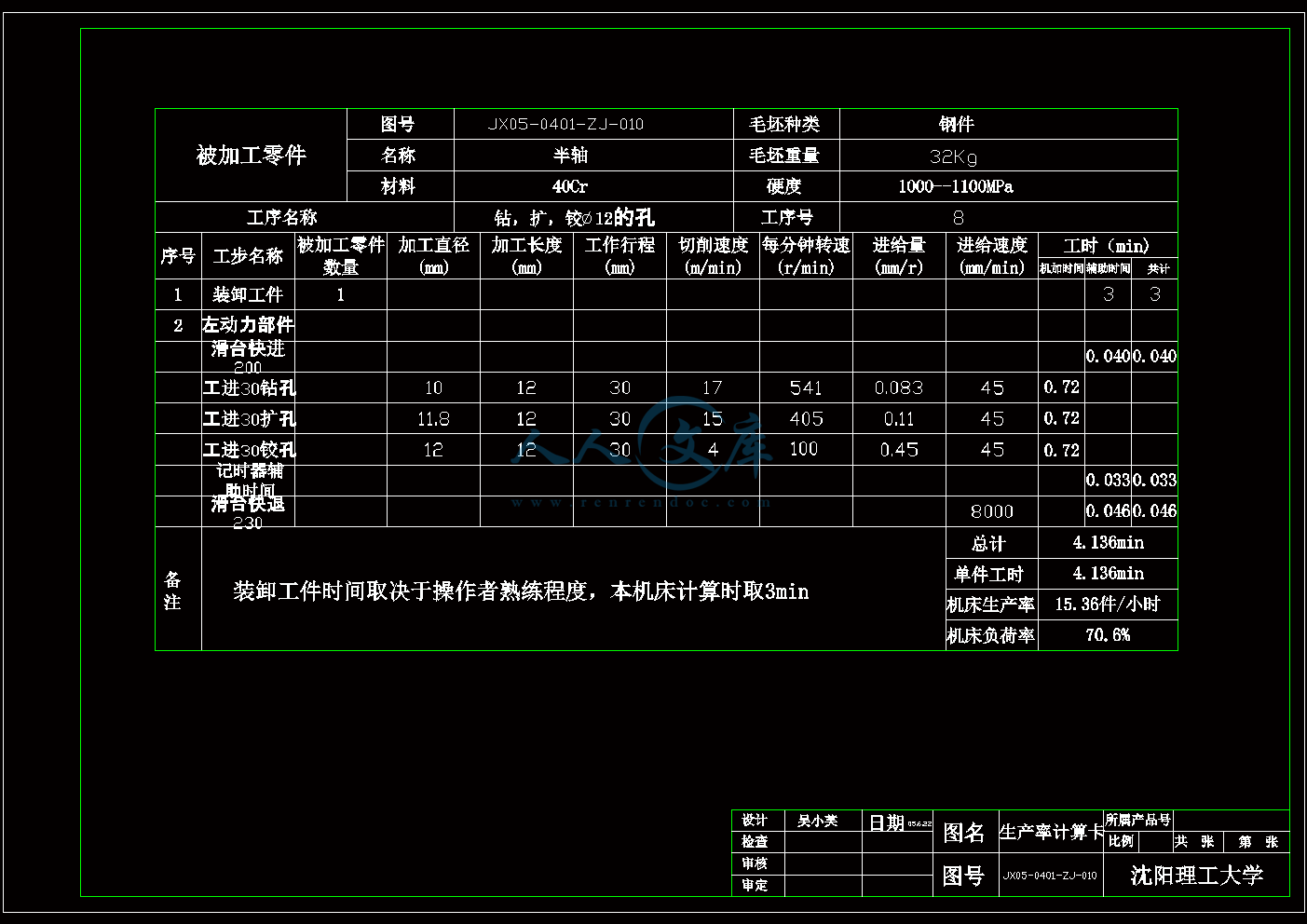
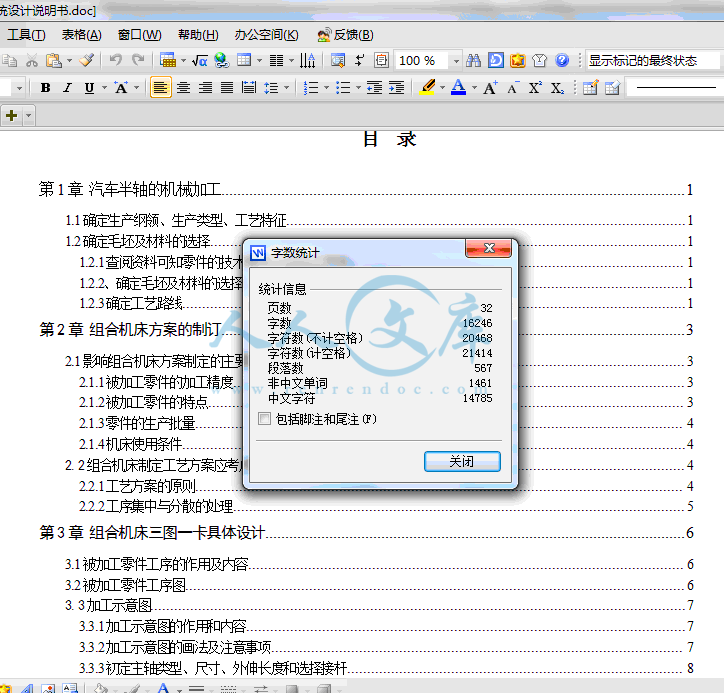


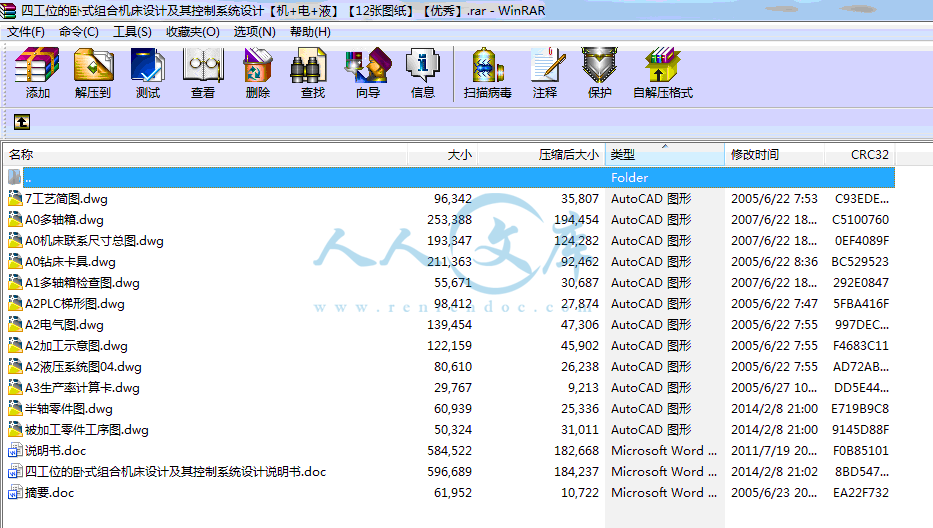
目 录
第1章 汽车半轴的机械加工1
1.1确定生产纲领、生产类型、工艺特征1
1.2确定毛坯及材料的选择1
1.2.1查阅资料可知零件的技术要求及结构工艺性:1
1.2.2、确定毛坯及材料的选择1
1.2.3确定工艺路线1
第2章 组合机床方案的制订3
2.1影响组合机床方案制定的主要因素3
2.1.1被加工零件的加工精度3
2.1.2被加工零件的特点3
2.1.3零件的生产批量4
2.1.4机床使用条件4
2.2组合机床制定工艺方案应考虑的问题4
2.2.1工艺方案的原则4
2.2.2工序集中与分散的处理5
第3章 组合机床三图一卡具体设计6
3.1被加工零件工序的作用及内容6
3.2被加工零件工序图6
3.3加工示意图7
3.3.1加工示意图的作用和内容7
3.3.2加工示意图的画法及注意事项7
3.3.3初定主轴类型、尺寸、外伸长度和选择接杆8
3.3.4确定各工序的切削用量9
3.4机床联系尺寸总图12
3.4.1、联系尺寸总图的作用与内容12
3.4.2绘制机床联系尺寸总图之前应确定的主要内容12
3.5机床生产率计算卡13
第4章 组合机床主轴箱的设计14
4.1绘制多轴箱设计的原始依据14
4.2主轴、齿轮的确定14
4.3多轴箱传动设计15
4.3.1本次设计对多轴箱传动系统的一般要求15
4.3.2参照所画主轴箱图,其传动树15
4.3.3润滑泵轴和手柄轴的安置16
4.4主轴的坐标位置16
第5章 随行卡具的设计17
5.1机床夹具设计17
5.1.1机床夹具概论17
5.1.3确定工件的夹紧方式和设计夹紧装置以及卡紧力计算18
第6章 液压系统的设计18
6.1液压系统图的设计及说明18
6.2液压系统计算20
6.2.1 液压缸设计计算步骤20
6.2.2液压缸性能参数的计算21
第7章 组合机床的电气系统21
7.1 PLC梯形图的设计步骤21
7.1.1PLC梯形图的设计一般分为以下几个步骤:21
7.1.2电气接线图和PLC程序的说明22
结 论25
谢 辞26
参考文献27
第1章 汽车半轴的机械加工
1.1确定生产纲领、生产类型、工艺特征
首先分析、研究被加工零件,通过认真阅读被加工零件图样,研究被加工零件的用途、尺寸、形状、材料、硬度、重量、加工部位的结构和加工精度及表面粗糙度要求等内容。通过产品装配图样和有关工艺资料的分析,充分认识被加工零件在产品中的地位和作用,从而来确定汽车半轴的机械加工工艺,使它保证各种加工要求和经济精度。
1、由N=20000件/年,知道零件的生产纲领;
2、生产类型的确定——大批量生产;
3、该工件的工艺特性
针对工件的结构形状及正常的经济精度和位置精度的分析,可知零件的加工要求。同时工件是大批量生产,可以采用高度自动化专用机床进行生产,可以广泛采用高效专用夹具、专用量具及自动检测装置。因此,在实际加工中我采用组合机床进行加工。这样容易保证加工精度,提高生产率,使产品成本相对降低,提高产品的经济效益。
1.2确定毛坯及材料的选择
1.2.1查阅资料可知零件的技术要求及结构工艺性:
1)汽车半轴外圆表面和端面加工,由于半轴头部3个孔的精度要求要对其进行钻扩铰的加工。
2)对热处理后的零件进行校正、探伤,保证零件的工艺性能良好。
1.2.2、确定毛坯及材料的选择
1)查阅零件图和技术要求及结构工艺性可知此工件采用40Cr材料,根据零件加制造毛坯,精度等级为2级。分析零件的材料的特征,查《机械制造设计手册》来确定。
2)确定零件毛坯尺寸查工艺手册
毛坯尺寸:零件需车削加工部位比加工后单边厚2.5mm工工艺性及零件的轮廓、尺寸精度、形状、位置、加工表面技术要求,最终确定了采用模锻件来
毛坯无明显的裂纹缺陷,未注圆角为R2~R3
1.2.3确定工艺路线
1)根据零件结构工艺性和经济精度,按照粗、精加工分开原则,工序集中原则,来确定机械加工工序的安排顺序,按照以下原则来初步拟订两条加工工艺路线:(1)先加工基准面,(2)划分加工阶段,(3)先面后孔,(4)次要表面可在阶段进行加工一、分析、研究、加工要求和现场工艺
本工件为汽车半轴,生产纲领为N=20000件/年,是大批生产,通过深入现场调查分析零件的加工工艺方法,定位和夹紧方式,所采用的先行的工艺资料,在结合机械加工工艺原则,在保证工件所需求的经济精度和表面粗糙度,同时考虑产品成本及经济性,我们设计是采用把孔加工放到组合机床上加工,这样采用一套专用的固定式夹具、专用刀具、专用量具、自动检测装置,在此四个工位(钻、扩、铰和装卸)来排列设备,进行流水加工,可以保证孔的经济精度6级和表面粗糙度Ra=3.2微米,节约了加工时间,提高了生产效率和经济性。按照粗精加工分开的原则和工序集中的原则来拟订组合机床的工艺方案
方案1
工序1 模锻毛坯
工序2 退火处理
工序3 粗车端面到34.5mm,半精车到34mm,钻中心孔,粗车大端外圆到Φ182mm,半精车到Φ180mm
工序4 钻小端中心孔,粗车端面保证零件总长1007±2mm
工序5 粗车大端端面到32.5mm,半精车至32mm,粗车小端外圆到56mm半精车到Φ54.6mm,精车到Φ54 0/-0.12mm
工序6 粗车大端端面到12.5mm,半精车到12 +0.5/0mm
工序7 铣花键齿,原始齿型压力角为48,侧齿粗糙度Ra<=3.2,分度圆的弧齿厚度5.89-6.06。
工序8 钻大端的孔到Φ10mm到Φ11.8mm到Φ12mm,粗糙度Ra3.2
工序9 清洗
工序10 去毛刺
工序11 防锈处理
工序12 检验入库
方案2
工序1 模锻毛坯
工序2 退火处理
工序3 粗车端面到34.5mm,半精车到34mm,钻中心孔,粗车大端外圆到Φ182,半精车到Φ180
工序4 钻小端中心孔,粗车端面保证零件总长1007±2mm
工序5 粗车大端端面到32.5mm,半精车至32mm,粗车小端外圆到56mm半精车到Φ54.6mm,精车到Φ54 0/-0.12mm
工序6 粗车大端端面到12.5mm,半精车到12 +0.5/0mm
工序7 钻大端的孔到Φ10mm到Φ11.8mm到Φ12mm,粗糙度Ra3.2
工序8 铣花键齿,原始齿型压力角为48,侧齿粗糙度Ra<=3.2,分度圆的弧齿厚度5.89-6.06。
工序9 清洗
工序10 去毛刺
工序11 防锈处理
工序12 检验入库
2)工艺路线的分析比较
工艺路线的方案1,按工序分析,各面的车到普通机床上加工,孔加工放在组合机床上加工,易保证孔的精度要求,以及加工工艺性能较高。先加工基准面的原则及先面后孔的原则,选择工艺方案1比较合适。
4、确定机械加工余量,总的工序尺寸
车大端端面 单边余量2.5mm 厚度为35.5mm 小端的单边余量2 mm直径为58mm
零件总长1010mm