数控车床进给系统传动系统设计
38页 22000字数+说明书+任务书+外文翻译+8张CAD图纸【详情如下】
A3轴承盖(A3).dwg
XY工作台设计图纸.dwg
主轴(A1).dwg
外文翻译--一个激光束加工(LBM方法)数据库的切割瓷砖 中文版.doc
外文翻译--一个激光束加工(LBM方法)数据库的切割瓷砖 英文版.pdf
拨块(A3).dwg
数控车床进给系统传动系统设计说明书.doc
滚珠丝杠副(A2).dwg
燕尾槽导轨(A1).dwg
论文.doc
轴承支座(A2).dwg
防尘盖(A3).dwg
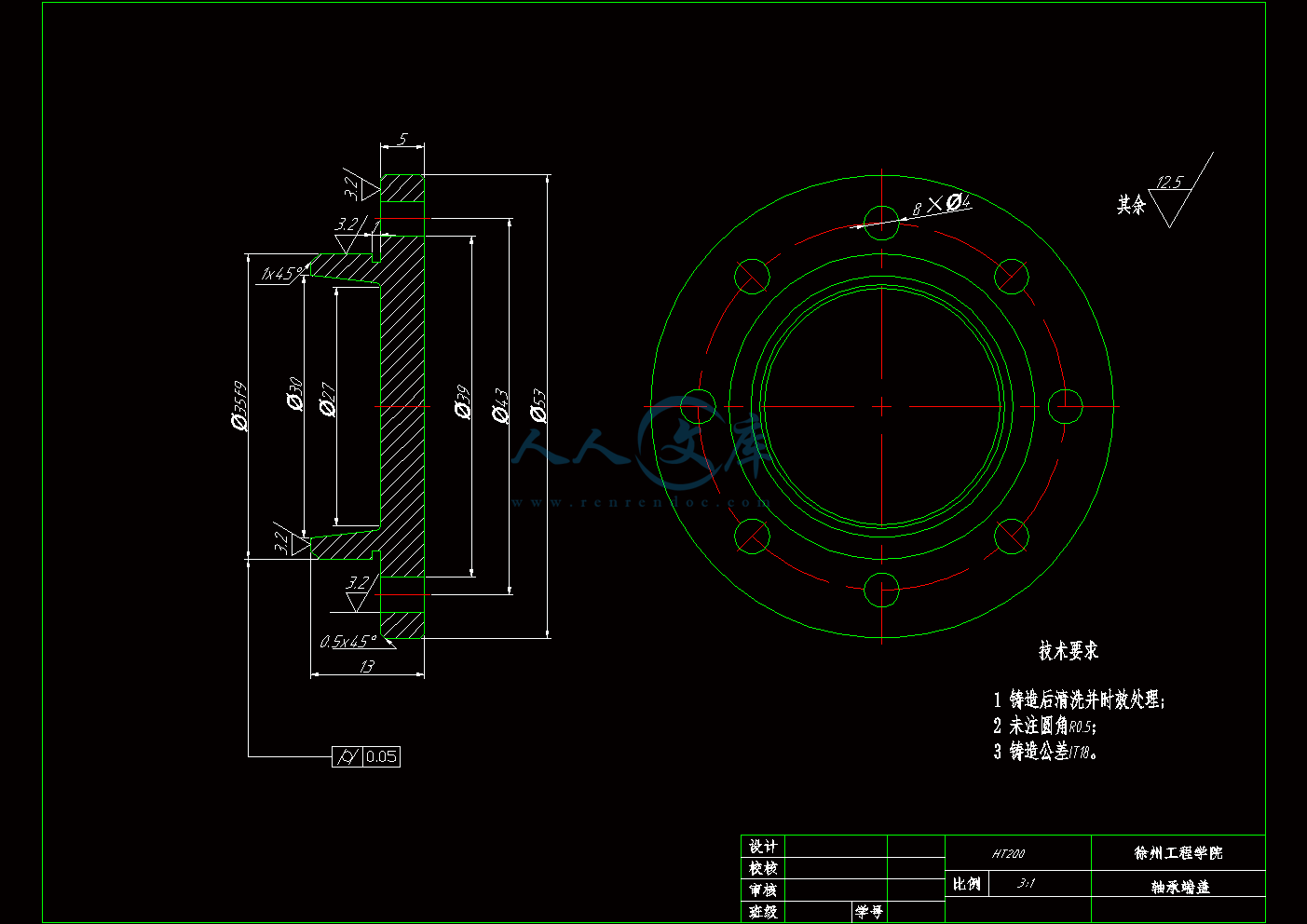
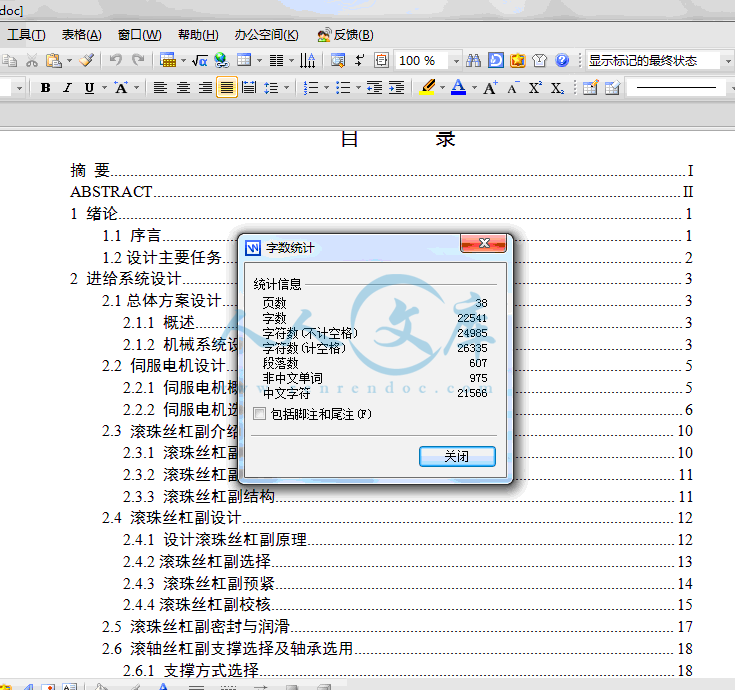
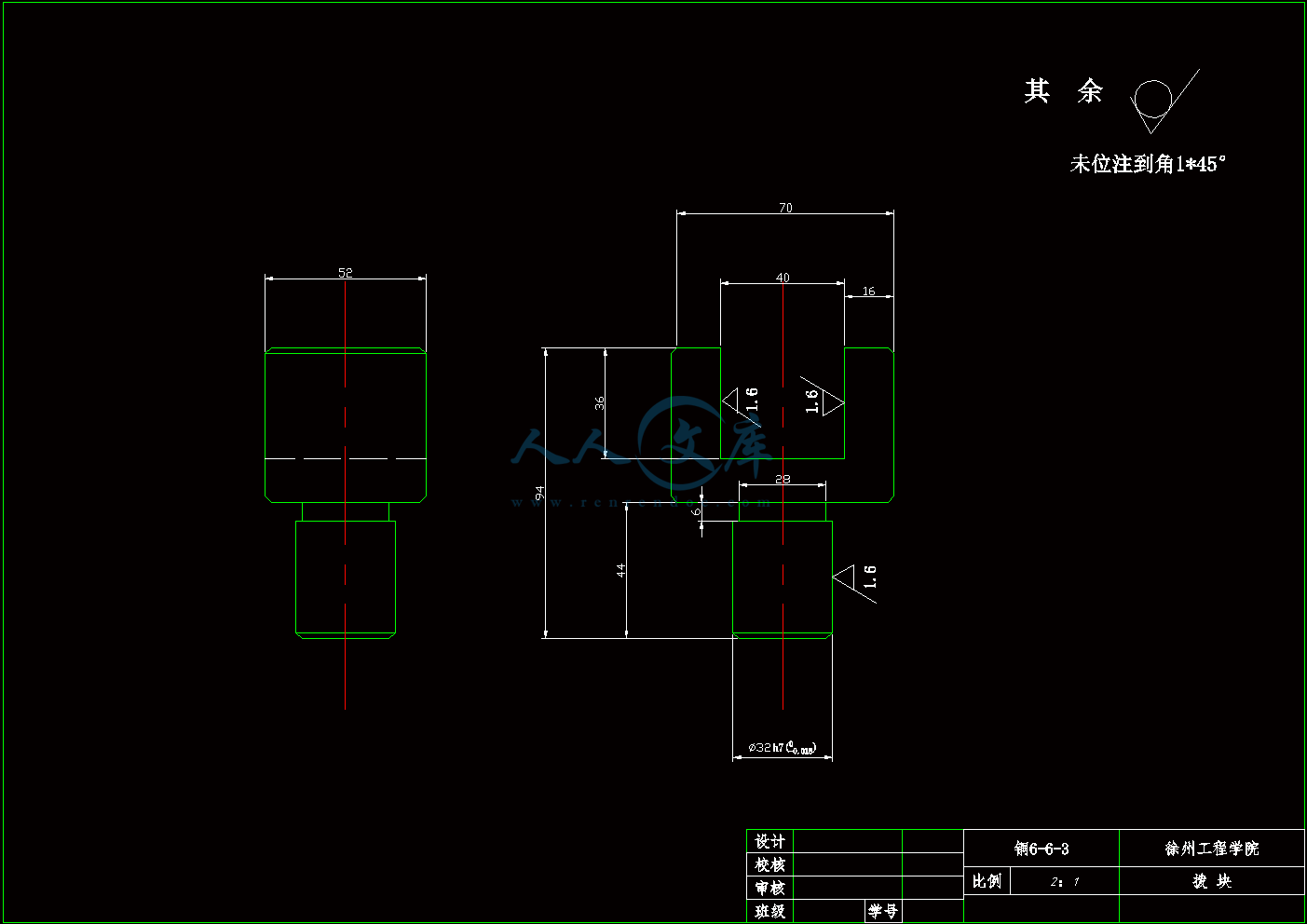
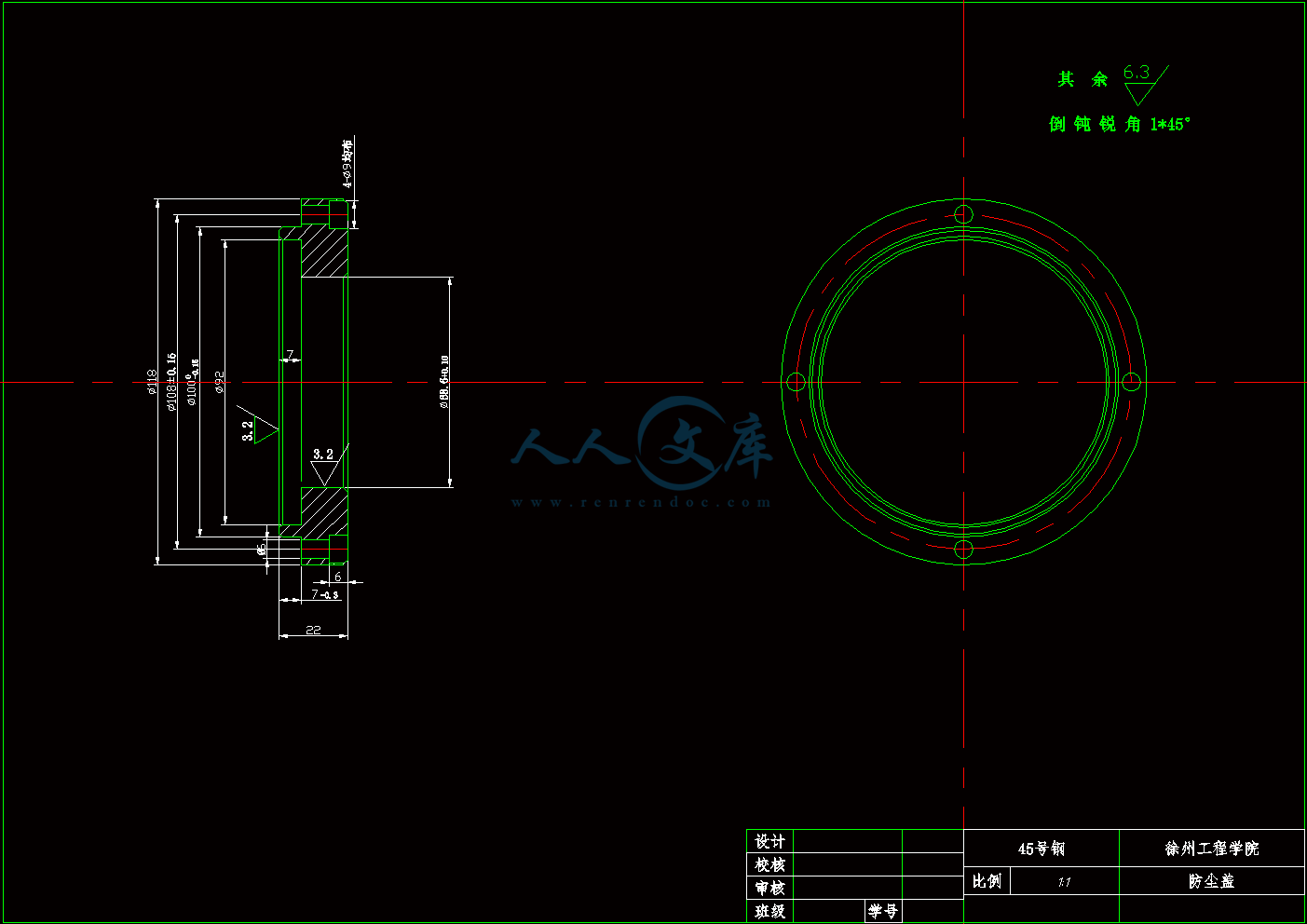
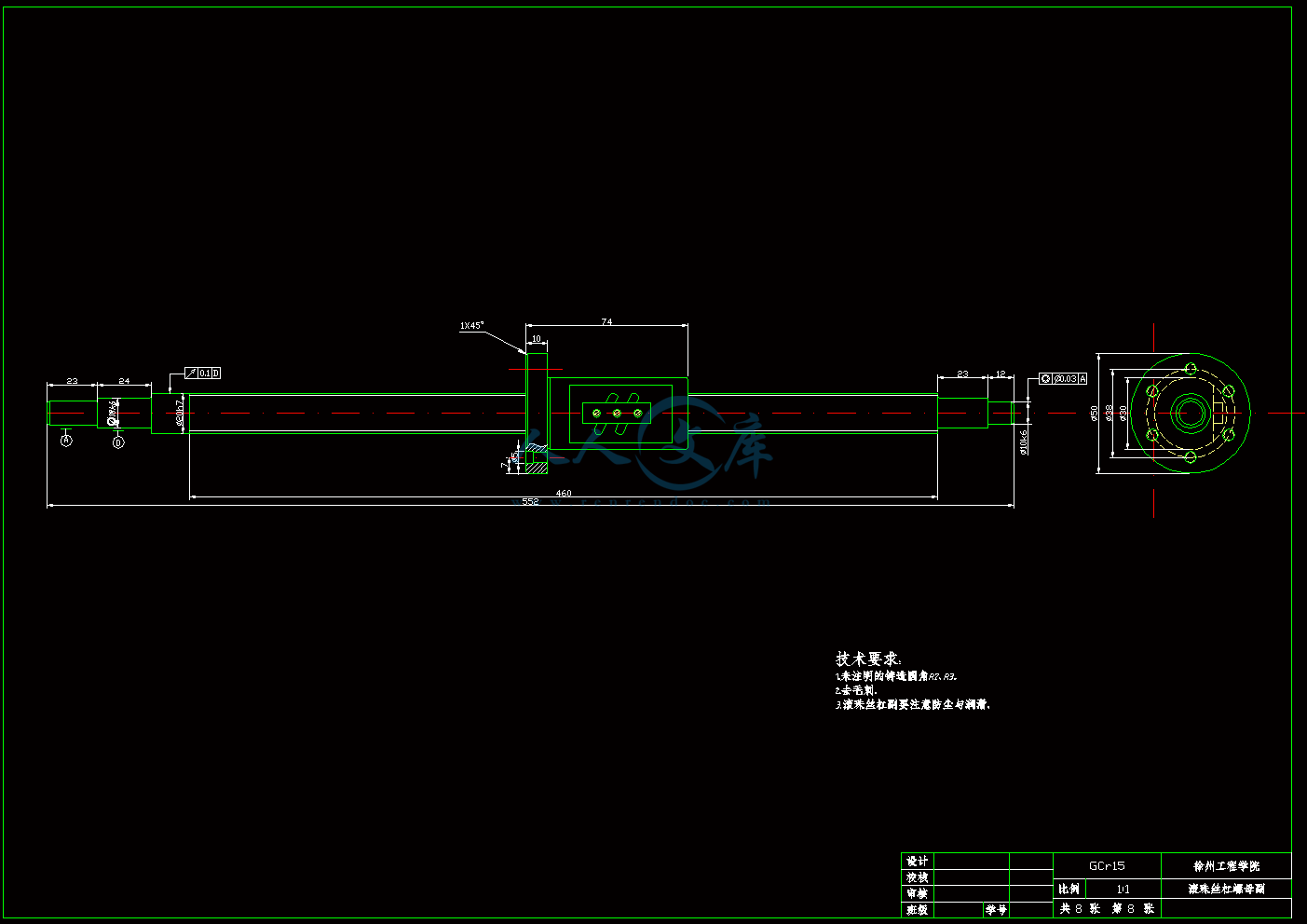

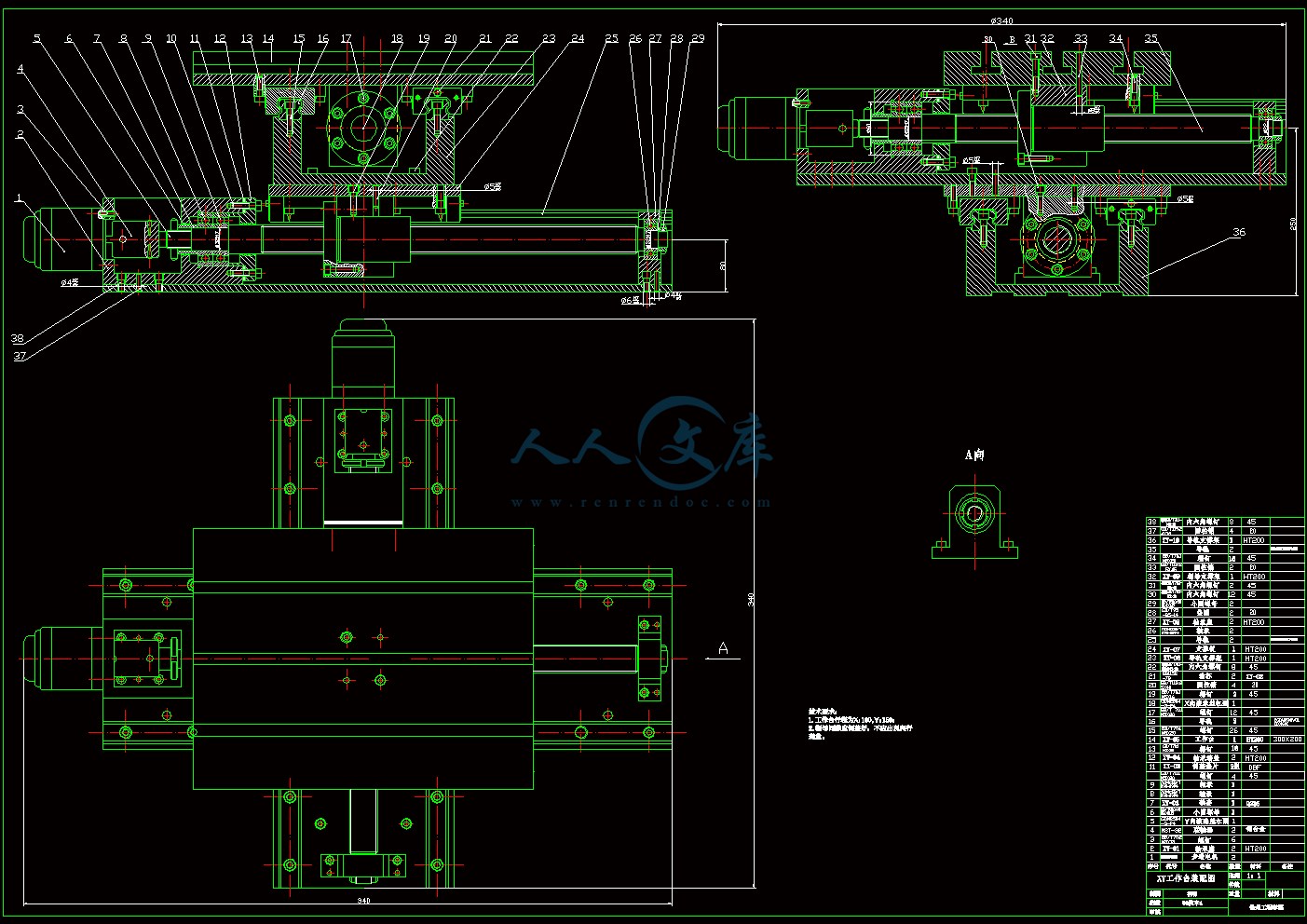
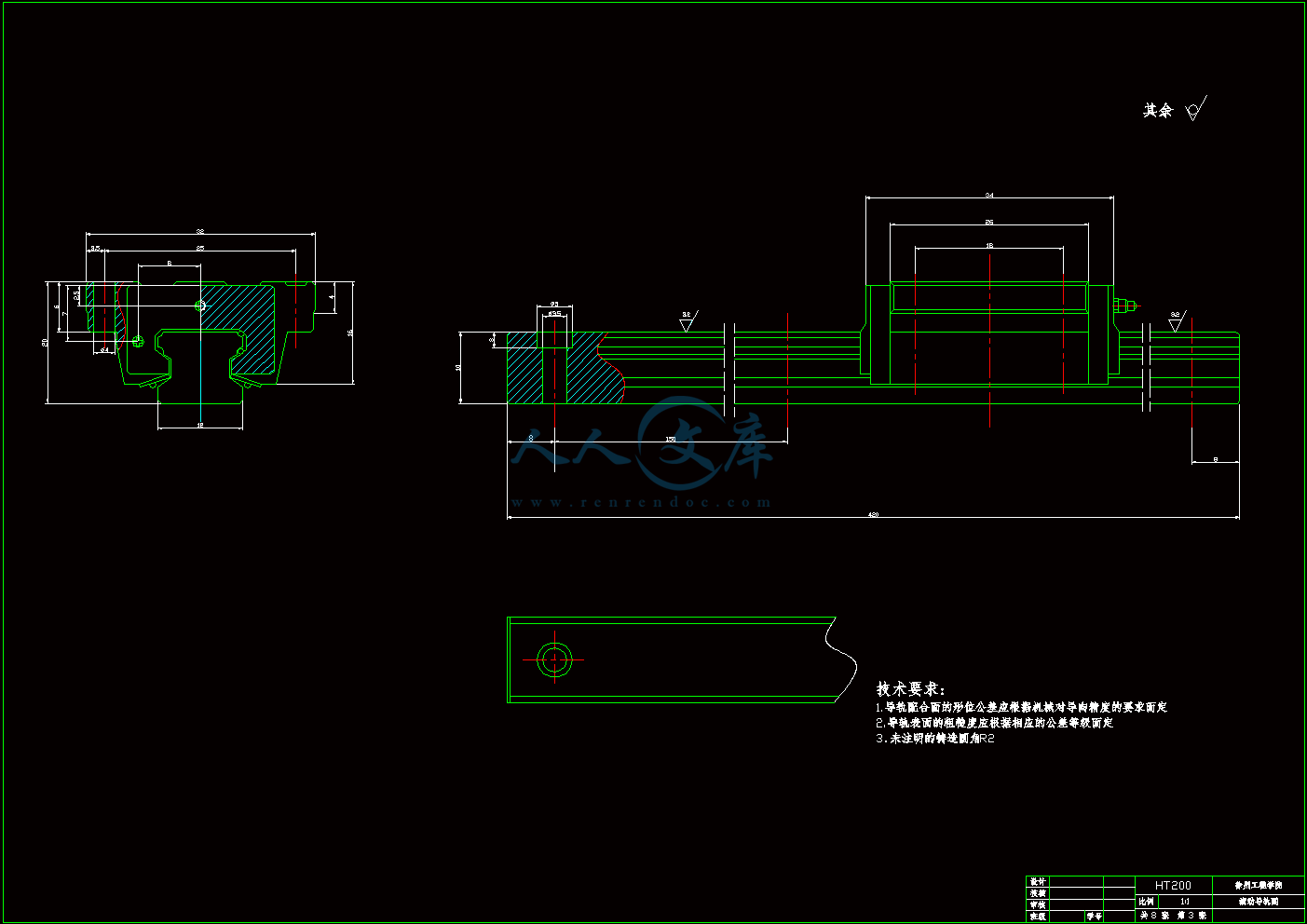
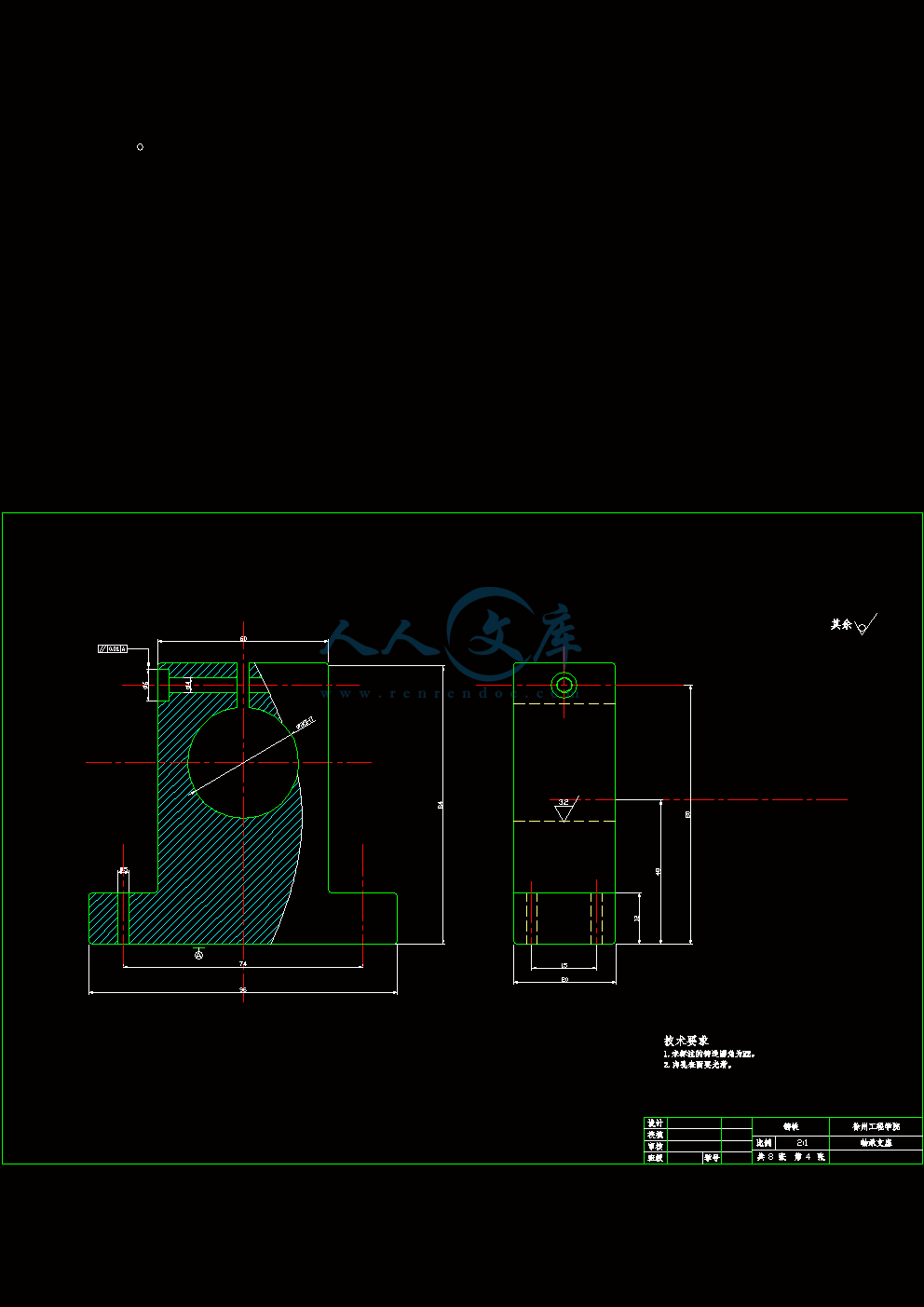
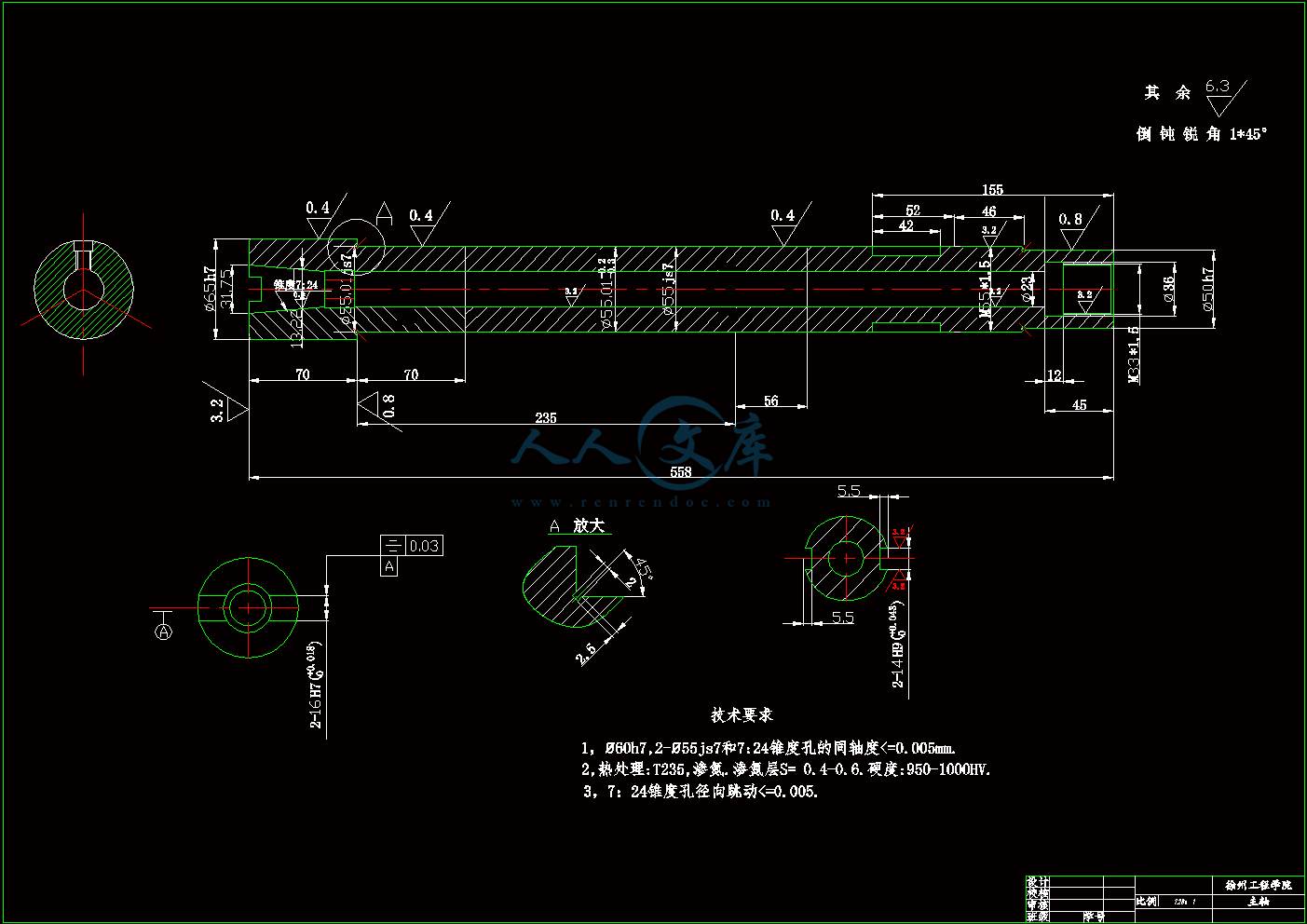
目 录
摘 要I
AbstractII
1 绪论1
1.1 序言1
1.2设计主要任务2
2 进给系统设计3
2.1总体方案设计3
2.1.1 概述3
2.1.2 机械系统设计3
2.2 伺服电机设计5
2.2.1 伺服电机概述5
2.2.2 伺服电机选择6
2.3 滚珠丝杠副介绍10
2.3.1 滚珠丝杠副概述10
2.3.2 滚珠丝杠副特点11
2.3.3 滚珠丝杠副结构11
2.4 滚珠丝杠副设计12
2.4.1 设计滚珠丝杠副原理12
2.4.2滚珠丝杠副选择13
2.4.3 滚珠丝杠副预紧14
2.4.4滚珠丝杠副校核15
2.5 滚珠丝杠副密封与润滑17
2.6 滚轴丝杠副支撑选择及轴承选用18
2.6.1 支撑方式选择18
2.6.2 轴承选择19
2.6.3 轴承配合与润滑20
2.7 联轴器简介20
2.8 联轴器基本要求21
2.9 联轴器选择22
2.10 联轴器校核23
2.10.1 转矩校核23
2.10.2 销抗剪强度校核24
3 导轨设计25
3.1 导轨概述25
3.2 导轨分类25
3.3 导轨选型与长度计算25
3.4 导轨副技术要求26
3.5导轨的间隙调整27
4 防护罩设计29
4.1 基本要求29
4.2 选择设计29
4.3 其他设计30
4.3.1 基本要求30
4.3.2 支撑架设计31
总 结32
致 谢33
参考文献34
摘 要
数控车床进给系统是指能分别沿着X 向和Y向做进给运动的系统,是许多机电一体化设备的基本部件,如数控车床的纵—横向进刀机构、数控铣床和数控钻床的X-Y工作台、激光加工设备的工作台、电子元件表面贴装设备等。模块化的X-Y数控工作台,通常由导轨座、移动滑块、工作、滚珠丝杠螺母副,以及伺服电动机等部件构成。其中伺服电动机做执行元件用来驱动滚珠丝杠,滚珠丝杠螺母带动滑块和工作平台在导轨上运动,完成工作台在X、Y方向的直线移动。导轨副、滚珠丝杠螺母副和伺服电动机等均以标准化,由专门厂家生产,设计时只需根据工作载荷选取即可。控制系统根据需要,可以选取用标准的工作控制计算机,也可以设计专用的微机控制系统。
该设计从确定小型数控车床的方案入手,设计进给系统的装配图和主要零件图。确定数控车床数控系统后,详细论述进给传动系统各组成部分,以及各部分的计算和选用。
关键词:数控车床; 进给系统; 装配图; 零件图
数控车床进给系统的具体参数如下:
X方向行程:100mm
Y方向行程:1500mm
工作台面的参考尺寸:240260mm
工作台和工件最大物重质量60kg
工作台表面滑动摩擦系数为0.5
平均切削力:500N
快进进给速度:1000mm/min
最高运动速度:10000mm/min
脉冲当量0.001mm
定位精度: 0.02mm
工作寿命:每天8小时,工作8年,250天/年
1 绪论
1.1 序言
数控技术是用数字信息对机械运动和工作过程进行控制的技术,是现代化工 业生产中一门新型的,发展十分迅速的高新技术。数控装备是以数控技术为代表 的新技术对传统制造业和新型制造业的渗透,形成的一种机电一体化技术。这一 技术使生产过程中的生产效率、产品成本及工人劳动强度等方面问题得以明显改 善,特别是针对对市场化生产的小批量、多品种特点,有无可比拟的优势。数控机床是采用了数控技术的机床。即能按照程序逻辑,一步步处理生产过程的机床。数控技术也叫计算机数控技术,目前它是采用计算机实现数字程序控制的技术。这种技术用计算机按事先存贮的控制程序来执行对设备的运动轨迹和外设的操作时序逻辑控制功能。由于采用计算机替代原先用硬件逻辑电路组成的数控装置,使输入操作指令的存贮、处理、运算、逻辑判断等各种控制机能的实现,均可通过计算机软件来完成,处理生成的微观指令传送给伺服驱动装置驱动电机或液压执行元件带动设备运行。
制造业是作为衡量一个国家经济的重要指标,体现了一个国家或一个民族的科技实力,是一个时代科学技术发展最明显的突出体现。尤其是在最近几十年了,发达的资本主义国际凭借其先进的制造技术,利用其强大的科技和财政实力获得了巨大的经济利益。我国的制造业起步晚、基础差,但近二十年来,我国投入了巨大的人力物力,并取得了骄人的成绩。但同时也要看到,我们国家的制造业和西方发达资本主义国家的制造业还有差距,而且在某种层度上说,差距还很大,这就要求我们国家还要付出更大的努力去提高我国的制造业在世界制造业中的地位,使我国的制造业对我国的经济发展能够发挥更大的作用,为人民和人类带来更大的帮助。
数控车床、车削中心,是一种高精度、高效率的自动化机床。配备多工位刀塔或动力刀塔,机床就具有广泛的加工艺性能,可加工直线圆柱、斜线圆柱、圆弧和各种螺纹、槽、蜗杆等复杂工件,可咨询:宁波众鑫数控机床厂。具有直线插补、圆弧插补各种补偿功能,并在复杂零件的批量生产中发挥 了良好的经济效果。传统的机械加工都是用手工操作普通机床作业的,加工时用手摇动机械刀具切削金属,靠眼睛用卡尺等工具测量产品的精度的。现代工业早已使用电脑数字化控制的机床进行作业了,数控机床可以按照技术人员事先编好的程序自动对任何产品和零部件直接进行加工了。数控加工广泛应用在所有机械加工的任何领域,更是模具加工的发展趋势和重要和必要的技术手段。
数控车床又称为 CNC车床,即计算机数字控制车床,是目前国内使用量最大,覆盖面最广的一种数控机床,约占数控机床总数的25%。数控机床是集机械、电气、液压、气动、微电子和信息等多项技术为一体的机电一体化产品。是机械制造设备中具有高精度、高效率、高自动化和高柔性化等优点的工作母机。控机床的技术水平高低及其在金属切削加工机床产量和总拥有量的百分比是衡量一个国家国民经济发展和工业制造整体水平的重要标志之一。数控车床是数控机床的主要品种之一,它在数控机床中占有非常重要的位置,几十年来一直受到世界各国的普遍重视并得到了迅速的发展。
1.2设计主要任务
进给系统机械传动结构是伺服进给系统的主要组成部分,主要由传动机构、运动变换机构、导向机构、执行件组成,它是实现成形加工运动所需的运动及动力的执行机构。由于数控机床的进给运动是数字控制的直接对象,被加工工件的最终位置精度和轮廓精度都与进给运动的传动精度、灵敏度和稳定性有关。进给系统是数控加工的关键环节,是数字控制的直接对象,被加工工件的最终坐标位置精度和轮廓精度都与传动结构有关。脉冲当量是0.001mm,快进速度是1000mm/min,X轴行程:100mm ,Y轴行程: 150mm。合理设计进给系统的结构;完成进给部件(包含滚珠丝杠螺母副、燕尾槽导轨、导轨防护罩等)的结构设计及总图和零件图;完成主传动系统的设计计算;完成二万字的毕业论文及5000字的译文。