数控铣床Z轴进给系统设计
说明书 42页20000字数+6张CAD图纸
轴承盖A1.dwg
1联轴器A2.dwg
A2齿轮.dwg
Z轴进给运动装配图A0.dwg
主轴图零件.dwg
外文翻译--数控机床性能测试设备的开发和利用 中文版.doc
外文翻译--数控机床性能测试设备的开发和利用 英文版.pdf
客户资料--数控铣床Z轴进给系统设计
数控铣床Z轴进给系统设计论文.doc
数控铣床Z轴进给系统设计.txt
滚珠丝杠A1.dwg
论文.doc

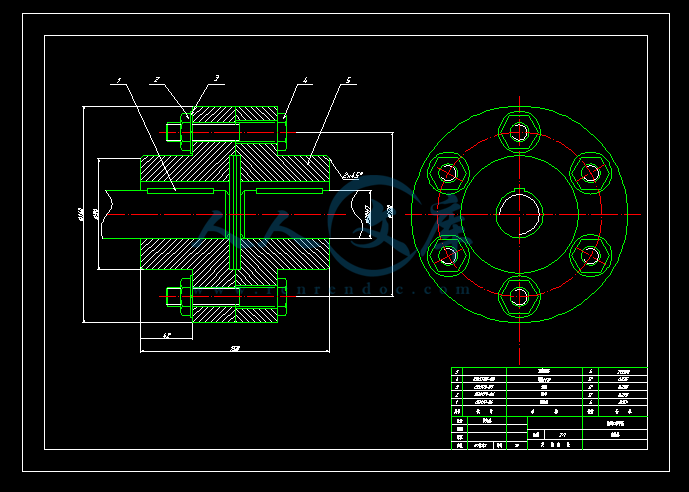
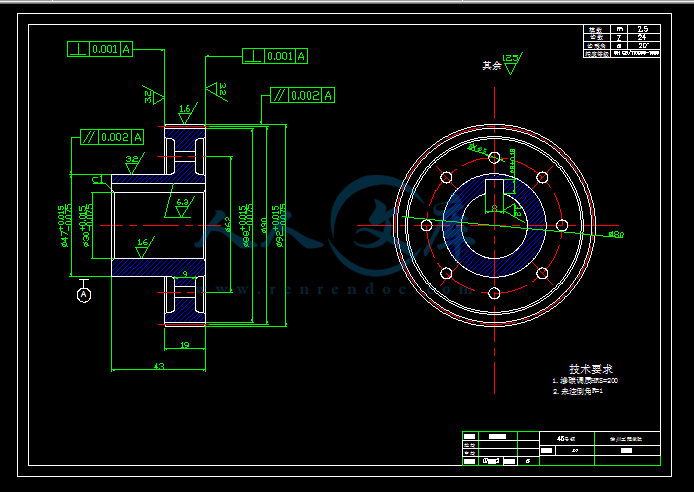
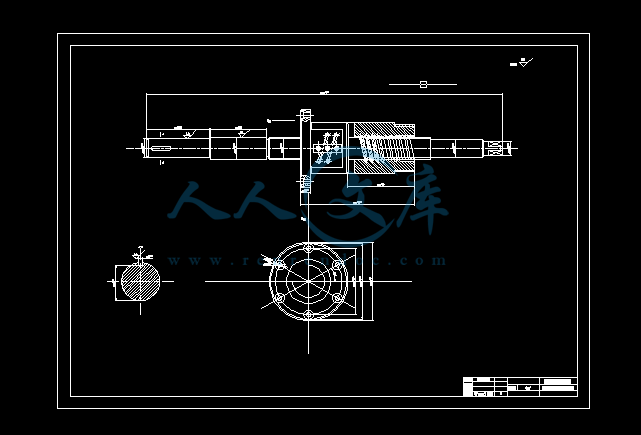
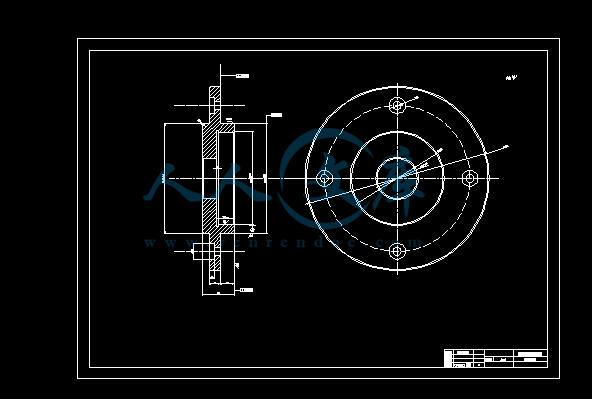

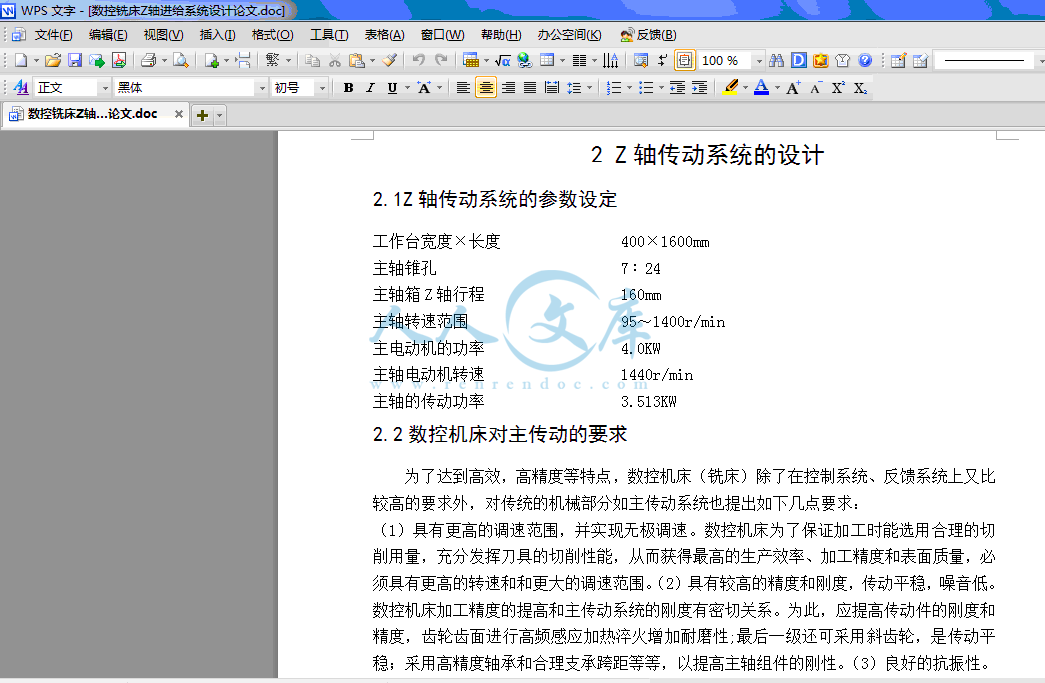
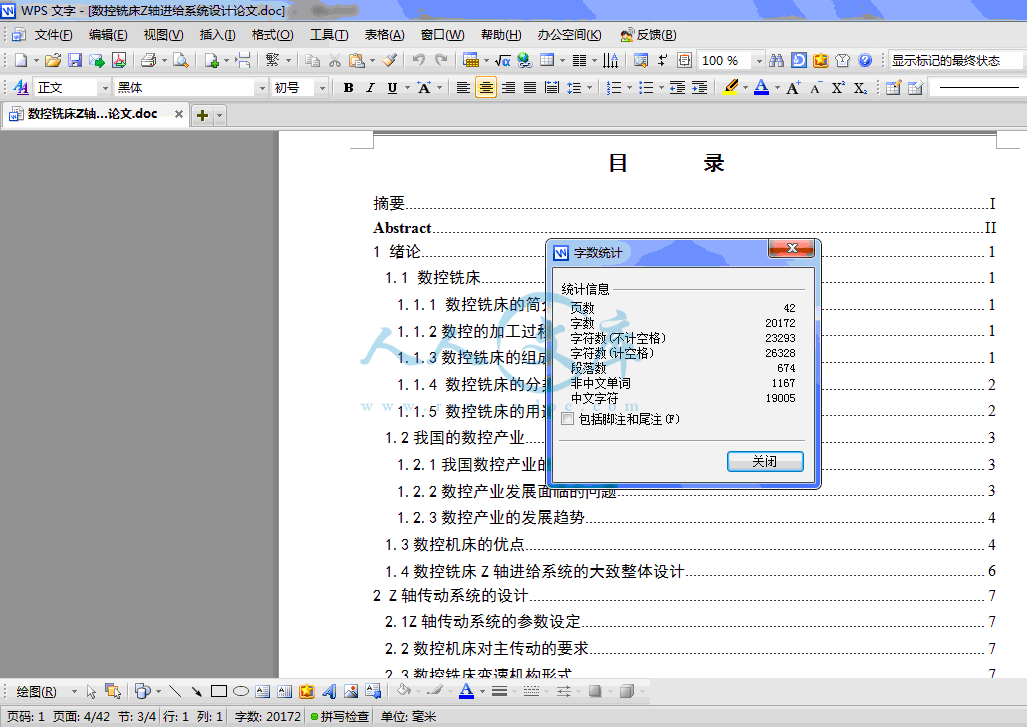

数控铣床Z轴进给系统设计
目 录
摘要I
AbstractII
1 绪论1
1.1 数控铣床1
1.1.1 数控铣床的简介1
1.1.2数控的加工过程1
1.1.3数控铣床的组成1
1.1.4 数控铣床的分类2
1.1.5 数控铣床的用途和工艺特点2
1.2我国的数控产业3
1.2.1我国数控产业的现状3
1.2.2数控产业发展面临的问题3
1.2.3数控产业的发展趋势4
1.3数控机床的优点4
1.4数控铣床Z轴进给系统的大致整体设计6
2 Z轴传动系统的设计7
2.1Z轴传动系统的参数设定7
2.2数控机床对主传动的要求7
2.3数控铣床变速机构形式7
2.4主轴的设计8
2.4.1主轴材料的选择8
2.4.2主轴结构的确定8
2.4.3轴的校核计算9
2.5齿轮传动的设计计算12
2.5.1模数的估算:13
2.5.2齿轮分度圆直径的计算13
2.5.3齿轮宽度B的确定14
2.5.4齿轮其他参数的计算14
2.5.5齿轮的校核(接触疲劳强度):14
3 Z轴进给系统总体方案的设计15
3.1设计参数15
3.2工作原理15
3.3总体方案设计15
3.3.1 数控系统的选择15
3.3.2传动机构的选择16
3.3.3联轴器选择16
4 主要零部件的计算与选用18
4.1Z轴工作载荷分析18
4.2 Z轴工作载荷计算18
4.3滚珠丝杠螺母副的计算与选用18
4.3.1丝杠导程的确定18
4.3.2动载荷C计算19
4.3.3效率计算20
4.3.4滚珠丝杠的精度选择20
4.3.5滚珠丝杠的制动20
4.4滚珠丝杠螺母副支承的选择21
4.5滚珠丝杠螺母副的间隙消除与预紧22
4.6轴承的计算与选用22
4.6.1轴承初选22
4.6.2轴承的计算23
4.6.3确定轴承的规格型号24
4.7传动系统的刚度计算24
4.7.1丝杠拉压刚度KT24
4.7.2滚珠丝杠螺母副的轴向接触刚度KN25
4.7.3支承轴承的轴向刚度KH25
4.7.4丝杠传动的综合拉压刚度K25
4.8伺服电动机的选择计算25
4.8.1确定步进电动机的类型25
4.8.2确定脉冲当量26
4.8.3最大静态转矩的选择26
4.9负载转动惯量的计算26
4.9.1工作台折算到丝杠上的转动惯量27
4.9.2丝杠折算到电动机的转动惯量27
4.9.3传动系统折算到电机轴上的总转动惯量27
4.10负载力矩的计算27
4.10.1计算折算到电动机主轴上切削负载力矩27
4.10.2计算折算到电动机上的摩擦负载力矩27
4.10.3计算附加负载力矩28
4.10.4加速力矩28
4.10.5计算空载时的快进力矩28
4.10.6计算切削时的工进力矩28
4.10.7计算空载启动力矩28
4.10.8确定步进电动机的最大静转矩29
4.11导轨的选择29
4.11.1导轨的介绍29
4.11.2导轨的参数选取30
4.11.3导轨的间隙调整31
4.11.4导轨材料与热处理32
5主要零件的校核33
5.1 滚珠丝杠螺母副的校核33
5.1.1 滚珠丝杠螺母副临界转速的校核33
5.1.2滚珠丝杠螺母副寿命的校核33
结论34
致谢35
参考文献36
1 绪论
1.1 数控铣床
1.1.1 数控铣床的简介
科学技术的发展以及世界先进制造技术的兴起和不断成熟,对数控加工技术提出了更高的要求;超高速切削、超精密加工等技术的应用,对数控机床的数控系统、伺服性能、主轴驱动、机床结构等提山了更高的性能指标;FMS的迅速发展和CIMS的不断成熟,又将对数控机的可靠性、通信功能、人工智能和自适应控制等技术提出更高的要求。随着微电子和计算机技术的发展,数控系统的性能日益完盖,数控技术的应用领域日益扩大。
数控铣床是在数控加丁中心领域中最具代表性的一种典型机床,在数控机床中所占的比率最大,数控加工中心、柔性制造单元等都是数控铣床基础上派生或发展起来的。它具有功能性强、加工范围广、工艺较复杂等特点,主要用于各种复杂的平面、轮廓、曲面等零件的铣削加工,同时还可以进行钻、扩、镗、攻螺纹等加工,在航空航天、汽车制造、机械加工和模具制造业中应用非常广泛。
1.1.2数控的加工过程
数控车床加工零件的主要过程主要包括一下内容:
(1)根据被加工零件的图样与工作方案,用规定的代码与程序格式,将刀具的移动轨迹、加工工艺过程、工艺参数、切削用量等编写成数控系统能够识别的指令形式,即编写加工程序。
(2)将所编写的加工程序输入数控装置。
(3)数控装置对输入的程序(代码)进行译码、运算处理,并像各坐标轴的伺服驱动装置和辅助功能控制装置发出相应的控制信号,以控制车床各部件的运动。
(4)在运动过程中,数控系统需随时检测车床坐标轴的位置、行程开关的状态等,并与程序的要求相比较,以决定下一步动作,直到加工出合格的零件。
(5)操作者随时对车床的加工情况、工作状态进行观察和检查,必要时还需要对车床动作和加工程序进行调整,以保证车床安全、可靠的运行。
1.1.3数控铣床的组成
数控铣床一般由数控系统、机床基础部件、主轴箱、进给伺服系统及辅助装置等几大部分组成。
(1)数控系统
数控系统是机床运动控制的中心,通常数控铣床都配有高性能、高精度、集成软件的微机数控系统,具有直线插补、圆弧插补、刀具补偿、固定循环、用户宏程序等功能,能完成绝大多数的基本铣削以及镗削、钻削、攻螺纹等循环加工。
(2)机床基础部件
通常是指底坐、立柱、工作台、横梁等,是整个机床的基础和框架。
(3)主轴箱
包括主轴箱和主轴传动系统,用于装刀具并带动刀具旋转、主传动大多采用专用的无级调速电动机驱动。
(4)进给伺服系统
由进给电动机和进给执行机构组成,按照程序设定的进给速度实现刀具和工件之间的相对运动,其主轴垂直方向进给运动及工作台的横向和纵向进给运动均由各自的交流伺服电机来驱动。
(5)辅助装置
包括液压、气动、润滑、冷却系统和排屑、防护等装置。