【温馨提示】 购买原稿文件请充值后自助下载。
[全部文件] 那张截图中的文件为本资料所有内容,下载后即可获得。
预览截图请勿抄袭,原稿文件完整清晰,无水印,可编辑。
有疑问可以咨询QQ:414951605或1304139763
摘要
对于机电产品来说,其设计、制造水平、产品的质量、成本及生产周期是息息相关的。随着现代科学技术的发展, 特别是计算机技术的突飞猛进, 人工设计、单件生产这些传统的设计与制造方式已无法适应现代工业发展的要求, 采用计算机辅助设计及制造(Computer Aided Design and Computer Aided Manufacturing,简称 CAD/CAM)技术已成为整个制造行业当前和将来技术发展的重点和趋势。数控技术是制造业实现自动化、柔性化、集成化生产的基础, 是提高产品质量、劳动生产率必不可少的手段。在数控加工过程中, 加工程序的编制是基础性工作, 因此 CAD/CAM技术对数控加工领域来说就显得很重要。CAD/CAM软件系统是由多个功能模块组成的, 如三维绘图、图形编辑、曲面、数控加工、仿真模拟、动态显示等。这些模块以工程数据库为基础, 进行统一管理, 既保持了底层数据的完整性和一致性, 实现了数据共享, 又节约了系统资源和运行时间。
本文是关于UG平台下数控加工中刀具路径的应用研究,即在采用UG CAM技术进行仿真加工时,为了完成高质量的型面数控加工, 如何合理地生成控制刀具运动的加工程序。
关键词:刀具路径 数控加工UG NX4.0
Abstract
For the mechanical and electrical products, its design, manufacturing, product quality, cost and production cycles are closely related. With modern science and technology development, especially in the rapid development of computer technology, artificial design, a single production of these traditional design and manufacturing methods have been unable to adapt to the demands of modern industrial development, using computer-aided design and manufacturing (Computer Aided Design and Computer Aided Manufacturing, referred to CAD / CAM) technology has become the manufacturing industry at present and the future development of key technologies and trends. NC technology is the manufacturing automation, flexible and integrated production base, is a essential method to improve the quality of products, labor productivity.In the process of the NC manufacturing, programming the NC processor is the basis for the preparation work, so the CAD / CAM technology is very important in the field of NC manufacturing. CAD / CAM software system is composed of several modules, such as 3-D graphics, graphics editing, surface, NC, simulation, dynamic display, and so on. These modules based on a database project, unified management, while maintaining the underlying data integrity and consistency, data sharing, and also saving system resources and run-time.
This paper is about the applied research of NC tool path, used UG CAM technology that in the simulation process, in order to complete the high-quality face NC, how to generate a reasonable control of the processing campaign tool.
Key words: Tool Path NC UG NX4.0
目录
摘要 I
Abstract II
第一章 绪 论 1
1.1数控加工技术的定义 1
1.2数控加工技术的现状 1
1.3数控加工技术的发展趋势 2
1.3.1 高速、高精加工技术 3
1.3.2 5轴联动加工和复合加工机床快速发展 3
1.3.3 智能化、开放式、网络化 3
1.3.4 重视新技术标准、规范的建立 4
1.4 CAD/CAM 软件在数控加工中的应用 5
1.4.1 CAD/CAM 在数控加工中的基本功用。 5
1.4.2 CAD/CAM 软件的优缺点。 6
1.5设计前言 6
第二章 刀具路径中的走刀方式和切削方向的选择 8
2.1 走刀方式和切削方向 8
2.2走刀方式 8
2.3 刀具运动轨迹生成中的走刀方式和切削方向的选择 8
2.3.1 二轴半加工方式 8
2.3. 2 三维曲面加工方式 9
2.4 本章小结 12
第三章 刀具路径在高速铣削中的应用研究 14
3.1高速切削技术及其刀具路径 14
3.1.1高速切削技术发展现状与优点 14
3.1.2高速削刀具路径的确定 14
3.2高速铣削时生成刀具路径的优化策略 16
3.2.1高速铣削编程时需要注意的几个原则 16
3.2.2高速铣削时刀具路径生成的策略 16
3.2.3高速铣削程序后置处理时优化 20
3.3 高速粗铣削加工淬硬钢时刀具路径方案的选择 20
3.3.1 实验过程 21
3.3.2 结果与讨论 22
3.3.3 研究结果 23
3.4本章小结 24
第四章 UG CAM刀具路径创建应用基础 25
4.1初始化加工环境 25
4.1.1 选择加工配置文件 25
4.1.2选择模板零件 25
4.1.3初始化加工环境 25
4.2 操作导航器 25
4.2.1操作导航器视图 25
4.2.2参数继承关系 27
4.3创建几何 27
4.3.1创建加工坐标系 28
4.3.2创建铣削几何 28
4.3.3创建铣削边界 29
4.3.4创建铣削区域 29
4.4创建刀具 30
4.5创建加工方法 30
4.5.1设置加工余量和公差 30
4.5.2设置进给量 31
4.6创建程序 33
4.7创建操作 34
4.8本章小结 35
第五章 减速箱部分零件刀具路径的应用研究 36
5.1减速箱端盖加工刀具路径的应用研究 36
5.1.1确定端盖数控加工的平面和孔 36
5.1.2确定走刀路线和安排加工顺序 37
5.1.3确定定位和夹紧方案 38
5.1.4确定切削用量 38
5.1.5制订数控加工技术文件 40
5.1.6数控刀具的参数信息 41
5.1.7生成刀轨 41
5.1.8进行切削仿真 41
5.1.9输出CLSF文件 42
5.2减速箱低速轴加工刀具路径的应用研究 42
5.2.1确定走刀路线和安排加工顺序 43
5.2.2确定切削用量 46
5.2.3确定定位和夹紧方案 46
5.2.4制订数控加工技术文件 46
5.2.5数控刀具的参数信息 47
5.2.6生成刀轨 48
5.2.7进行加工仿真 48
5.2.8生成CLSF文件 48
5.3本章小结 48
本文总结 49
设计总结 50
致谢 51
参考文献 52
科技译文 53
The development of NC 53
现代制造技术及其发展 56
Advanced processing technology developments 58
模具加工技术的最新发展 61
第一章 绪 论
1.1数控加工技术的定义
一般来说,计算机辅助制造(Computer Aided Manufaturing,CAM)包括计算机辅助生产计划、计算机辅助工艺过程设计、计算机数控编程、计算机控制加工过程等内容.而其中的数控加工编程则是计算机辅助制造(CAM)的关键内容。所谓数控加工技术,主要是指用记录在媒体上的数字信息对专用机床实施控制,使其自动完成规定加工任务的一门编程技术。运用数控加工可以保证产品达到极高的加工精度和稳定的加工质量;操作过程可以实现自动化;生产准备周期短;可以大量节省专用工艺设备,适应产品快速更新换代的需要。它与CAD紧密衔接,可以直接从产品的数字定义产生加工指令,从而保证零件具有精确的协调和互换性;产品最后用坐标测量机检验.可以严格控制外形和尺寸精度。零件形状越复杂,加工精度越高,设计更改越频繁,生产批量越小,数控加工的优越性就越容易得到发挥。例如:在卷烟机械行业新产品研发过程中,需要经过无数次的设计、优化与试制,最后才能获得成功,这些都离不开数控加工编程技术。数控加工编程技术在现代机械产品生产中占有举足轻重的地位,得到了广泛的应用。
数控加工是依靠程序来控制数控专用机床的加工过程的,因此数控加工程序是十分重要的环节,必须认真对待。一个理想的数控加工程序不仅能保证加工出符合设计要求的合格零件,同时也可使数控机床的功能得到合理的应用和充分的发挥以及安全可靠地工作。
1.2数控加工技术的现状
随着制造业的发展,中小批量生产的趋势日益增强,对数控机床的柔性和通用性提出了更高的要求,希望市场能提供不同加工需求、迅速高效、低成本地构筑面向用户的控制系统,并大幅度地降低维护和培训成本,同时还要求新—代数控系统具有方便的网络功能,以适应未来车间面向任务和定单的生产组织和管理模式。为此,近10年来,随着计算机技术的飞速发展,各种不同层次的开放式数控系统应运而生,发展很快。目前正朝标淮化开放体系结构的方向前进。就结构形式而言,当今世界上的数控系统大致可分为如下4种类型。


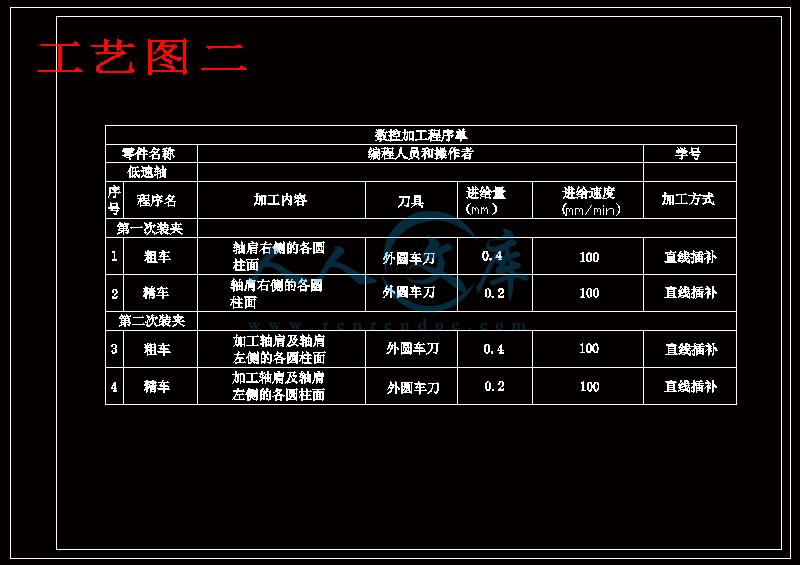

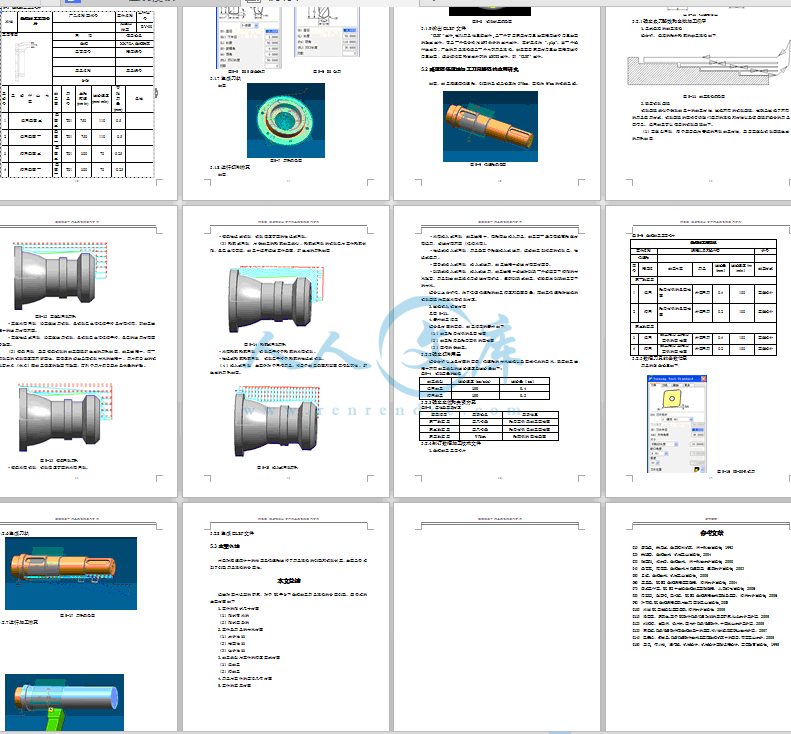