【温馨提示】 购买原稿文件请充值后自助下载。
[全部文件] 那张截图中的文件为本资料所有内容,下载后即可获得。
预览截图请勿抄袭,原稿文件完整清晰,无水印,可编辑。
有疑问可以咨询QQ:414951605或1304139763
摘 要
缸套—活塞环摩擦副是一个集往复、冲击运动于一体的复杂的摩擦学系统,本文是在摩擦、磨损、润滑理论的基础上,研究发动机活塞和缸套运动区域内,摩擦表面减少磨损的表面形貌设计,研究缸套工作表面加工出蜂窝状微坑后对发动机性能的影响。
首先,回顾了缸套工作表面储油结构的发展历程,探讨了目前国内外缸套工作表面储油结构的发展状况。
研究了内燃机活塞运动区域缸套摩擦表面减少磨损的表面形貌设计,提出在缸套工作表面加工出蜂窝状微坑来改善缸套—活塞环摩擦副的润滑和磨损状况。分析了蜂窝状微坑的流体润滑机理。
对各种缸套工作表面微坑加工方法进行了研究,分析了它们的微坑加工原理和特点,重点分析了振动冲击加工微坑方法,并且利用这种方法控制微坑分布规律和结构参数。
完成了振动冲击加工缸套蜂窝微坑的试验条件准备,设计了数控微坑成型机,购买了珩磨机,进行了机床的布置、安装、改造,设计和制造了夹具和矩阵工具头。
利用数控微坑成型机和低频振动冲击装置,完成了对多种微坑结构参数的洛嘉牌摩托车发动机气缸套、东风4型机车缸套和斯太尔WD615柴油机气缸套的微坑加工。
设计并进行了洛嘉牌摩托车发动机微坑气缸套和斯太尔WD615柴油机微坑气缸套的台架试验,台架试验表明使用微坑气缸套可明显减少缸套和活塞的磨损、机油消耗量和排放。
关键词:缸套,微坑,台架试验,耐磨性
ABSTRACT
The cylinder and piston rings is the complicated tribology system that has the reciprocating motion and the impacting motion. The topography of the tribological surface that can reduce the abrasion within the district of the cylinder and piston rings moving has been studied and designed. The honeycomb micro-pits cylinder how to influence the characteristic of the engine also has been studied in the paper.
First, the development of the structure that can store the lubrication is reviewed. The present development of the storing lubrication structure on the working surface of the cylinder is researched.
Second, the honeycomb micro-pits are manufactured on the working surface of the cylinder to improve the lubrication and abrasion of the cylinder and piston rings. The theory of dynamic lubrication of the honeycomb micro-pits is researched.
All kinds of processing methods of micro-pits on the working surface of the cylinder are studied. Its processing principle and feature are analyzed. The method of the impacting to manufacture micro-pits is researched with emphasis. This method can be used to control the distributing regulation and the structural parameter.
The test condition of the impacting to manufacture micro-pits is ready. The numerical controlled micro-pits processing machine is designed. The honing machine is purchased. The machines are disposed, installed, reconstructed. The clamping fixtures and the matrix tools are designed and manufactured.
Using the numerical controlled micro-pits processing machine, the motorcycle cylinder, the locomotive cylinder and the diesel engine cylinder are manufactured the honeycomb micro-pits that have many structural parameters.
The bench tests of the motorcycle cylinder and the diesel engine cylinder are planned and carried out. The bench tests show the abrasion of the cylinder and piston rings, the lubrication consumption and particulate emission can be reduced using the honeycomb micro-pits motorcycle cylinder.
Keywords: cylinder, micro-pits, bench test, wearability
目 录
摘 要I
ABSTRACTII
第1章 绪 论1
1.1 缸套的磨损形式1
1.1.1 缸套的正常磨损1
1.1.2 腐蚀磨损2
1.1.3 磨料磨损2
1.1.4 熔着磨损2
1.2 国内外研究现状3
1.3 表面微坑加工方法的发展史5
1.4 本文的研究方向及所完成的主要工作6
第2章 蜂窝状微坑的工作机理7
2.1 具有蜂窝状微坑储油结构的缸套的提出7
2.2 蜂窝状微坑的润滑原理8
2.2.1 理论分析9
2.2.1.1 假设9
2.2.1.2 最小油膜厚度最大瞬时值的计算9
2.2.1.3 上、下止点油膜厚度的计算13
2.2.2 结论与分析14
2.3 蜂窝状微坑对排放和机油耗的影响15
2.3.1 排放物的生成机理及危害15
2.3.2 机油消耗与排放物的关系16
2.3.3 降低机油耗和排放的措施17
第3章 表面微坑加工方法19
3.1 自激振动方法19
3.1.1 自激振动的产生19
3.1.2 缸套波纹形内孔表面的形成20
3.1.3 用自激振动形成缸套波纹形孔面的特点22
3.2 滚压方法22
3.3 激光珩磨22
3.3.1 激光打孔原理22
3.3.2 激光珩磨机床23
3.3.3 激光珩磨形成的储油结构24
3.3.4 试验结果24
3.3.5 激光珩磨的特点25
3.4 振动冲击加工方法26
3.4.1 表面微坑振动冲击加工原理26
3.4.2 加工工艺过程及要求29
3.4.3 微坑振动冲击加工对缸套耐磨性的影响29
3.4.3.1 储油微坑对缸套──活塞环耐磨性的影响29
3.4.3.2 冲击微坑残余应力对缸套耐磨性的影响30
3.4.4 实验结果30
第4章 试验条件32
4.1 试验设备32
4.1.1 数控微坑成型机32
4.1.2 珩磨机34
4.2 夹具34
4.3 矩阵工具头37
第5章 蜂窝状微坑缸套的台架试验38
5.1 台架试验方法38
5.1.1 试件准备38
5.1.1.1 摩托车发动机气缸套38
5.1.1.2 斯太尔WD615柴油机气缸套39
5.1.2 试验参数42
5.1.2.1 摩托车气缸套试验参数42
5.1.2.2 斯太尔WD615气缸套试验参数43
5.1.3 试验方法及过程43
5.1.3.1 摩托车气缸套43
5.1.3.2 斯太尔WD615气缸套43
5.2 台架试验结果43
5.3 台架试验结论44
第6章 总结与展望45
致 谢47
参考文献48
附录51
第1章 绪 论
内燃机是机械车辆的动力源。它是一个集往复、回转、冲击等运动为一体的复杂的摩擦学系统。据统计,一台六缸柴油机有600多对摩擦副[1],磨损是导致内燃机零部件失效和整机性能劣化的主要原因,尤其随着高科技的发展,对内燃机的可靠性、寿命、排放、经济性等要求越来越高,使得其摩擦、磨损问题更加突出。缸套—活塞环摩擦副被汽车行业称为三大磨损副之一。它们的磨损是一个很大的问题。每年都要消耗大量的活塞环备件,而缸套磨损后的修理也很麻烦,费用高。多年来一直列为行业攻关课题。本文在分析缸套—活塞环摩擦副的磨损机理和摩擦学特性的基础上,着重研究缸套表面储油结构对发动机缸套—活塞环摩擦副性能的影响,使设计的缸套达到最高的可靠度、最佳的经济性能和合理的使用寿命。
1.1 缸套的磨损形式[2][3]
缸套—活塞环摩擦副长期在高温高压、冲击应力、腐蚀等恶劣工况下工作,磨损很严重,是影响发动机正常工作的主要原因[4]。发动机缸套磨损后,活塞与缸套的配合间隙加大,气密性下降,发动机的动力性和经济性下降,造成起动困难,机油温度和油耗增加,

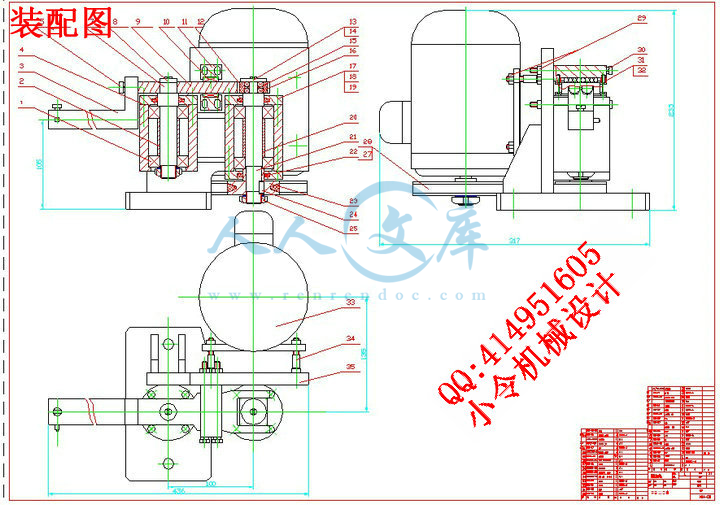
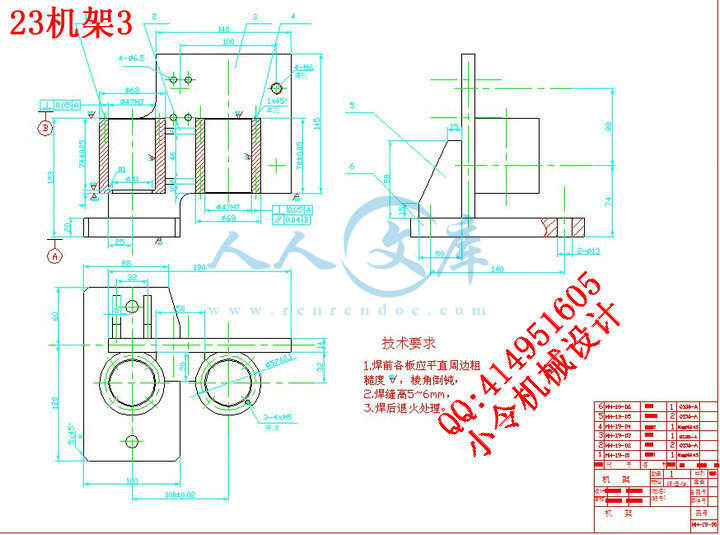
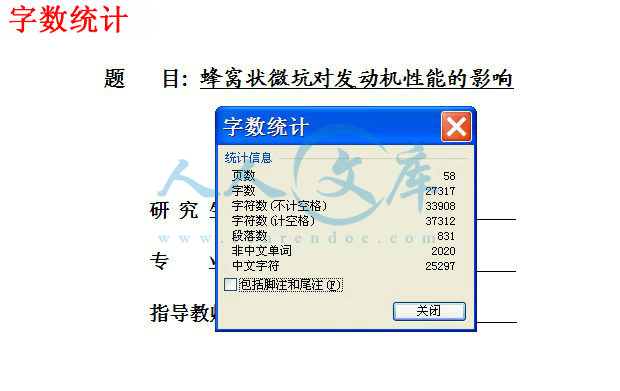