【温馨提示】 购买原稿文件请充值后自助下载。
[全部文件] 那张截图中的文件为本资料所有内容,下载后即可获得。
预览截图请勿抄袭,原稿文件完整清晰,无水印,可编辑。
有疑问可以咨询QQ:414951605或1304139763
摘 要
本次设计的是食品搅拌机,这种搅拌机是我们生活中使用的搅拌机的其中一种,搅拌机在生活中的应用相当的广泛,搅拌水果,奶油,得出的味道爽口,还可以搅拌蛋糕液,馅料、打蛋及和制面团,特别在酒家、饭店、面包屋以及食品厂家等作搅拌食料,揉和面团之用,是生产优质糕点的理想设备,使我们的生活更加方便。搅拌非常均匀,生产率高,质量好,成本低。整机结构紧凑,其主要组成结构包括:搅拌装置,搅拌传动系统。它是通过电动机带动皮带轮,用联轴器连接,经过减速器后通过四杆机构搅拌。本设计主要设计内容是食品搅拌机的机架设计、传动设计、搅拌动作的设计、电机选用,四杆机构设计,机架外型尺寸的确定,各零部件结构的选材、校核,完成总装图和零件图。
关键词:食品搅拌机;联轴器;四杆机构设计;传动设计;
Abstract
The design of the food mixer, this mixer is a mixer used in our lives in one of mixer applications in life quite extensive, stirring fruit, cream, come to the taste of refreshing, you can stir the cake liquid filling, beat eggs and and made the dough, especially in restaurants, hotels, housing and food manufacturers such as bread for stirring foodstuffs, dough kneading and use, is ideal for production of high quality bakery equipment, make our lives more convenient. Mixing is very uniform, high productivity, good quality and low cost. Compact structure, the structure of its main components are: stirrer, stirring drive. It is driven by the motor pulley, with the coupling connection, after a gear after the mixing through the four-bar linkage. The design of the main design elements are food mixer rack design, transmission design, mixing action design, motor selection, the four-bar linkage design, frame shapes and sizes determine the structure of each component selection, verification, complete the assembly map and part drawing.
Keywords:food mixer;coupling; four-bar linkage design;transmission design;
目 录
引言1
1食品搅拌机的工作原理和原理图3
2食品搅拌机的用途3
3食品搅拌机的设计要求和原始数据4
4设计方案的分析4
5连杆机构的设计4
5.1曲柄存在的条件5
5.2运动轨迹的计算6
6电动机选择7
6.1电动机选用的基本原则7
7带传动的设计9
7.1带传动组成、类型9
7.1.1传动带的组成及工作原理9
7.1.2V带的类型9
7.2带传动的设计计算和参数选择10
7.2.1确定计算功率Pc10
7.2.2确定V带的型号11
7.2.3确定带轮直径11
7.2.4确定带长及中心距a012
7.2.5验算包角13
7.2.6确定V带的根数z14
7.2.7确定初拉力F015
7.2.8计算带轮轴所受的压力Q15
7.3V带的截面尺寸15
7.4带轮的设计16
8减速器的选用18
9轴系零、部件的设计19
9.1轴的设计19
9.2轴的校核21
9.3轴承的选用23
9.3.1轴承的型号23
9.3.2滚动轴承的配合形式23
9.3.3滚动轴承的轴向定位23
9.4联轴器的选用23
9.4.1选用的联轴器型号23
9.4.2联轴器的配合形式24
10搅拌容器的设计24
11机架的设计24
11.1底架的设计24
11.1.1底架的材料选择24
11.1.2底架的大体尺寸25
11.2支架的设计25
11.3减速器底架的设计25
12零件的加工工艺规程26
12.1工艺路线26
结论28
谢 辞30
参考文献31
附录31
引言
饮食水平是一个国家文明程度和人民生活质量高低的重要标志。食品的质量和供应状况,直接关系着全民族的体质,影响到国家的政治安定和社会进步。世界上经济发达的国家都十分重视发展食品工业。中国食品工业负有满足人民日益增长的物质文化生活需要和为国家经济建设提供积累的双重任务,是国民经济的重要组成部分。发展食品工业可以加速农业结构及其产品品质的优化调整,提高农产品经济价值,促进农业生产的良性循环。同时,对于带动和促进饲料工业、包装机械工业、机械工业、电子工业和精细化学工业等相关行业协调发展,适应餐饮业,旅游业等第三产业崛起的需要,繁荣城乡市场,扩大外贸出口以及扩大劳动就业等都具有十分重要的作用。 80年代以来,中央和地方都十分重视食品工业的发展,制定了一系列支持食品工业发展的政策。同时,国务院制定了“90年代中国食物结构发展与改革纲要”中国食品工业协会制定了“九五中国食品工业科技发展纲要”。河南省食品工业经过20多年的快速发展,各项指标已走在中国的前列,尤其是作为一个农业大省,在调整经济结构、推进农业产业化进程中,大力发展食品工业更是具有重要的意义。因此,在刚刚结束的省人代会上把以畜产品加工、粮油加工、果蔬加工为主体的食品工业做为第一大支柱产业来培育。目前,中国食品工业已初步形成门类比较齐全、技术不断进步、产品日益丰富、运销网络通畅的生产经营体系,成为国民经济中处于重要战略地位的一大产业。年产值5400多亿元。在中国各工业门类中,产值第一。
由上可知,食品机械在国民经济中的地位是如此之高。搅拌机在生活中的应用相当的广泛,搅拌水果,奶油,得出的味道爽口,还可以搅拌蛋糕液,馅料、打蛋及和制面团,特别在酒家、饭店、面包屋以及食品厂家等作搅拌食料,揉和面团之用,是生产优质糕点的理想设备。因此设计一个合理的搅拌机是非常的必要。
在目前市场上,搅拌机的种类很多,食品搅拌机也有各种各样的。因此,对一个搅拌机进行设计和研究是很有必要的,同时也有一定实践价值。从学习层面及设计手法上看:使用了UG或PRO/E等软件来完成机构的三维造型,并用软件对其机构进行模拟运动仿真,分析其可行性。这是一种有别于以前靠用做出相应的实物来验证其可行性的新设计方法。使用运动仿真的优点:节省了实验成本、缩短了设计时间、能轻易通过软件改变一些参数实现更多的验证方案、有利于创新设计的实现等等。
这是一个比较综合性的设计课题,自己的经验也不足,要想做好该课题,必须要熟悉的掌握机械原理、机械优化设计、工程力学、机械设计、数控加工、机械制造基础、产品造型等方面的一些理论知识。因此,这也是对我大学四年所学专业知识的一个综合应用。通过做此课题,我将能了解这本科四年来我对专业知识掌握的程度,同时也是一个系统的复习。这将给我以后走向社会起到一个很好的开头作用。
搅拌机包含的机构及需要实现的动作:
搅拌机构:实现模仿手的动作对食品作用。可以将搅拌机构设计为4杆机构,实现搅拌头的曲线运动。
容器机构:使容器得以不断有序的循环转动。可以将容器机构看作是一个圆周运动,容器盆下加一块装有电机的支撑板,由带传动带动容器盆旋转运动。
中间机构:实现搅拌机构与容器盘机构连接,保证他们相互间的联合运动。

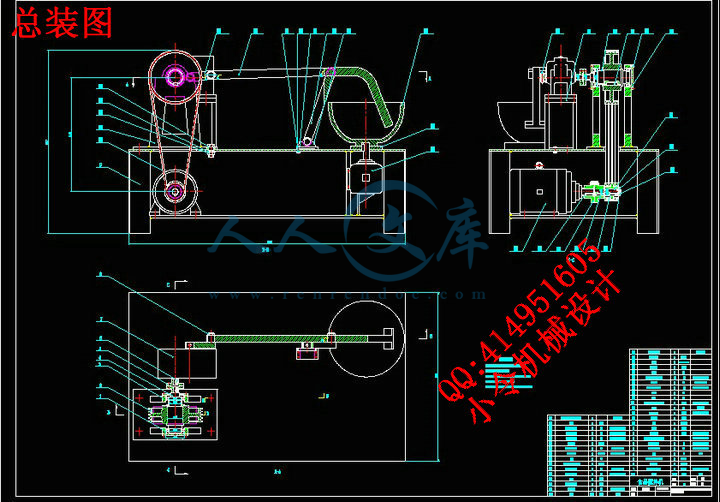

