【温馨提示】 购买原稿文件请充值后自助下载。
[全部文件] 那张截图中的文件为本资料所有内容,下载后即可获得。
预览截图请勿抄袭,原稿文件完整清晰,无水印,可编辑。
有疑问可以咨询QQ:414951605或1304139763
摘 要
数控技术是当今先进制造技术和装备最核心的技术,机械制造业的竞争,其实质是数控技术的竞争。从目前世界上数控技术及其装备发展的趋势来看,其主要研究热点有以下几个方面:1.功能发展方向;2.结构体系发展方向;3.高速、高效、高精度、高可靠性发展方向;
CK6163型数控机床是开环式的数字程序控制车床。能进行内外圆柱面、圆锥面、圆弧面、圆柱螺纹和圆锥螺纹等加工。机床主轴的启动、停止和变速,纵向和横向进给运动的行程和速度,刀具的变换和冷却,都可以自动控制。并具有直线、锥度、直螺纹和锥螺纹等自动循环机能。
CK6163型数控机床有床头箱、变速箱、进给机构、刀架、控制箱等组成。床头箱中由操纵油缸中的活塞杆带动拔叉来控制双向内齿离合器的接通或放松,使主轴实现四级变速。主运动采用分离传动从而使变速箱实现四级变速。进给机构由床鞍纵向进给电液脉冲马达、滚珠丝杠副和中间传动齿轮副组成。
关键词:数控技术;床头箱;变速箱;进给机构;滚珠丝杠;
Abstract
Numerical control technology is the core technology of the advanced manufacturing technology and equipment, machinery manufacturing competition, and its essence is the competition of numerical control technology.From the numerical control technology and equipment development trend, its main research focus has the following several aspects:1 .The direction of function development;2. The direction of structural system development;3. High speed, high efficiency, high precision and high reliability;
CK6163 numerical controlled machine tool is the open loop type digital program controlled lathe. To inside and outside the cylinder, cone surface, such as processing arc face, straight thread and taper thread. Start, stop, and variable speed machine tool spindle, longitudinal and transverse feed motion of stroke and speed, transformation and the cooling of a tool, can be controlled automatically. And with a straight line, taper, straight thread and automatic cycle function of taper thread and so on.
CK6163 numerical controlled machine tool headstock, transmission, feeding mechanism, tool carriage, control box, etc. Bedside box by manipulating the oil cylinder piston rod to control the bidirectional drive fork of the internal tooth clutch connected or relax, for level 4 speed of spindle. Separation is used in the main movement transmission so that realize four speed gearbox. Feed mechanism by the bed saddle longitudinal feed electric hydraulic pulse motor, ball screw pair and the intermediate transmission gears.
Key words: Numerical control technology; Bedside cabinet; Gearbox; Feed mechanism;
Ball screw;
目 录
摘 要III
AbstractIV
目 录V
1 绪论1
1.1本课题的研究内容和意义1
1.2国内外的发展概况1
1.3本课题应达到的要求2
2 总体方案3
2.1 CK6163的现状和发展3
2.2 CK6163卧式车床的总体方案3
3 主轴箱的设计4
3.1 主轴箱的运动设计4
3.1.1 已知条件4
3.1.2 结构分析式4
3.1.3 拟定转速图4
3.1.4 确定转速图5
3.1.5 确定各变速组传动副齿数6
3.2 齿轮传动设计7
3.2.1 渐开线直齿轮设计7
3.2.2 斜齿轮设计8
3.3 主轴传动设计11
3.3.1 确定主轴最小直径11
3.3.2 主轴最佳跨距的确定11
3.3.3 主轴刚度的校核12
3.4 带传动设计12
3.5 滚珠螺母丝杠14
3.5.1 滚珠丝杠副的种类与结构14
3.5.2 内循环式14
3.5.3 外循环式14
3.5.4 滚珠丝杠副的结构参数15
3.5.5 滚珠丝杠副的结构特点15
3.5.6 滚珠丝杠副的安装支撑方式15
4 变速箱的设计17
4.1 运动部分计算17
4.1.1 参数确定的步骤和方法17
4.2 传动设计18
4.2.1 传动结构式、结构网的选择18
4.2.2 主传动顺序的安排19
4.2.3 传动系统的扩大顺序的安排19
4.2.4传动组的变速范围的极限植19
4.2.5 最后扩大传动组的选择20
4.3 转速图的拟定20
4.3.1 主电机的选定20
4.3.2 双速和多速电机的应用20
4.3.3 电机的安装和外形20
4.3.4 常用电机的资料21
4.3.5 齿轮传动比的限制21
4.4 带轮传动部分的设计21
4.4.1 带轮直径确定的方法、步骤21
4.4.2 三角带传动的计算21
4.4.3 选择三角带的型号21
4.4.4 确定带轮的计算直径D1、D222
4.5 齿轮传动部分的设计24
4.6 电磁离合器的选择28
4.6.1 按扭距选择28
4.6.2 步骤28
4.7 轴的设计计算29
4.7.1 轴Ⅱ的设计计算29
4.7.2 轴Ⅶ的设计计算29
4.8 纵向进给系统的设计计算34
4.8.1 纵向进给系统的设计34
4.8.2 纵向进给系统的设计计算34
5 结论与展望40
5.1 结论40
5.2 不足之处及未来展望40
致谢41
参 考 文 献42
1 绪论
1.1本课题的研究内容和意义
数控机床通常由控制系统,伺服系统,检测系统,机械传动及其他辅助系统组成。数控机床相比较于普通机床有以下特点:(1)加工精度高,拥有稳定加工质量;(2)拥有多坐标的联动,能加工较为复杂的工件;(3)加工时间短;(4)生产效率高;(5)自动化程度高,减轻劳动强度;
数控机床的控制方式有很多种,主要分为开环控制,闭环控制和半闭环控制。开环控制系统没有反馈装置,系统不会计算误差,精度不高,但属于经济型;闭环控制系统和半闭环控制系统都装有反馈装置,他们区别在于反馈检测装置安装位置不同,闭环控制系统的反馈装置在工作台上,而半闭环控制系统的反馈装置在轴端或者丝杆上。本次研究的CK6263型数控机床的控制就属于开环控制系统。
CK6163型数控车床,是车床中应用最广泛、最典型的一种数控车床。该机床是开环式的数字控制车床。能进行内外圆柱面、圆锥面、圆弧面、圆柱螺纹和圆锥螺纹等加工。机床主轴的起动、停止和变速,纵向和横向进给运动的行程和速度,刀具的变换和冷却,都可以自动控制。并具有直线、锥度、直螺纹和锥螺纹等自动循环功能。在该机床中采用液压卡盘、液压尾座、快换刀架和机床外对刀装置。该机床使用于加工形状复杂的中小批量的零件。
数控机床的主传动方式分为集中传动方式和分离传动方式。集中传动是指主传动和变速传动在同一个主轴箱内的传动方式,其优点在于结构紧凑,便于实现集中操作,安装调整方便,主要用于普通精度的大中型机床;分离传动是指主传动的大部分传动和变速传动安装于远离主轴的单独变速箱内,通过带传动将运动传到主轴箱的传动方式,其优点在于变速箱内各传动件所产生的的振动和热能不直接传给或少传给主轴,有利于提高主轴工作精度,主要运用于对精度要求高的机床。
CK6163型数控机床就是采用了分离传动,来提高工作精度。
1.2国内外的发展概况
数控技术及装备是发展新兴高新技术产业和尖端工业的使能技术和最基本的装备。世界各国信息产业、生物产业、航空、航天等国防工业广泛采用数控技术,以提高制造能力和水平,提高对市场的适应能力和竞争能力。工业发达国家还将数控技术及数控装备列为国家的战略物资,不仅大力发展自己的数控技术及其产业,而且在"高精尖"数控关键技术和装备方面对我国实行封锁和限制政策。因此大力发展以数控技术为核心的先进制造技术已成为世界各发达国家加速经济发展、提高综合国力和国家地位的重要途径。
目前,欧、美、日等工业化国家已经先后完成数控机床产业化进程,而我国是从20世纪80年代才开始起步,处于发展阶段。国内本土数控机床企业大多处于“粗放型”阶段,在产品设计水平、质量、精度、性能等方面与国外先进水平相比落后了5-10年;在高、精、尖技术方面的差距则达到了10-15年。同时中国在应用技术及技术集成方面的能力也还比较低,相关的技术规范和标准的研究制定相对滞后,国产的数控机床还没有形成品牌效应。同时,中国的数控机床产业目前还缺少完善的技术培训、服务网络等支撑体系,市
场营销能力和经营管理水平也不高。更重要原因是缺乏自主创新能力,完全拥有自主知识产权的数控系统少之又少,制约了数控机床产业的发展。
十二五期间我国将持续投入,且力度加大,力争通过10-15年的时间,实现由机床工具生产大国向机床工具强国转变,实现国产中高档数控机床在国内市场占有主导地位等一系列中长期目标。
在数控机床制造方面,德国和日本一直处于领先地位,德国是老牌工业强国,其锻压机械种类齐全,基本上每一种锻压设备都有代表世界最先进水平的产品,比如通快的钣金成形机床、舒勒的大型覆盖件压力机、多工位压力机和冲压自动生产线、米勒万家顿的电动螺旋压力机、奥姆科的热模锻压力机、哈森克勒佛的离合器式螺旋压力机、拉斯科的锻锤、辛北尔康普的大型液压机、瓦格纳-班宁的碾环机、雷菲尔德的旋压机、FELSS的旋锻机等等的锻压机械。日本的锻压机械和德国一样,在世界上居于领先地位,尽管在大型和重型锻压设备方面不如德国,但在数控锻压机械,尤其在伺服驱动压力机方面具有很高的技术水平。而在我国沈阳、大连两市已基本成为全国数控车床、加工中心的中央综治委开发基地;在长江三角洲地区已成为数控磨床、电加工机床、板材加工设备、等的主要生产基地。
1.3本课题应达到的要求
本课题主要研究CK6163型数控机床的设计,主要设计主轴箱和变速箱,还有涉及到进给机构的设计,以及一些零部件的设计。而主要问题是:相关文献资料的缺乏,对一些结构设计部分的具体设计指导,以及制图软件的高级运用技巧。
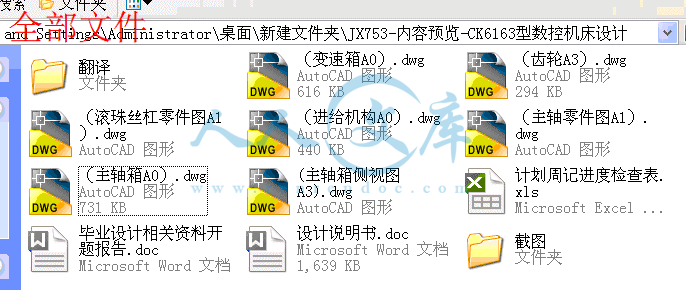


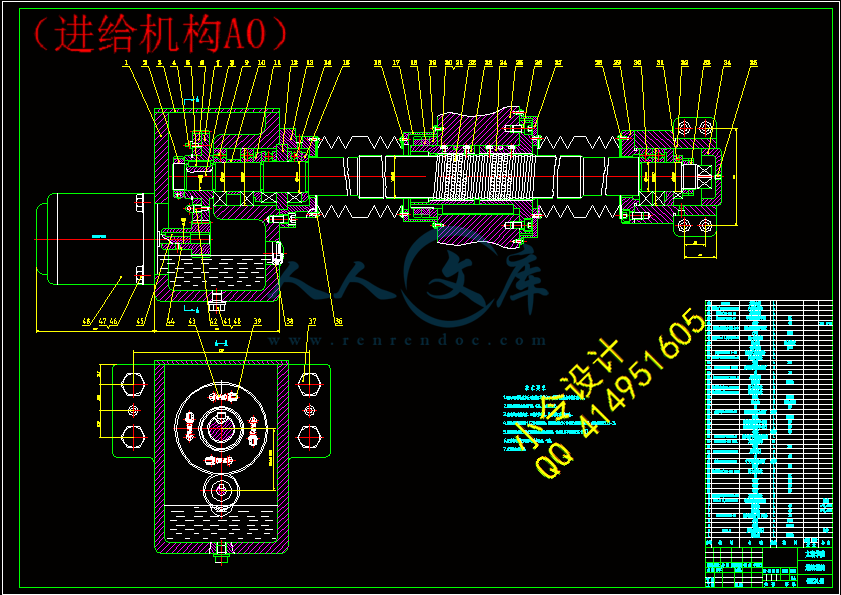
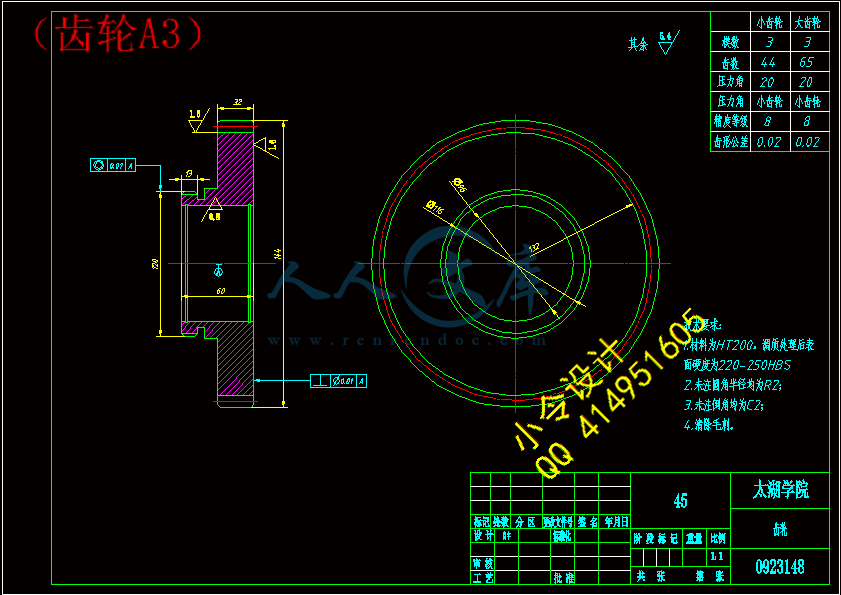
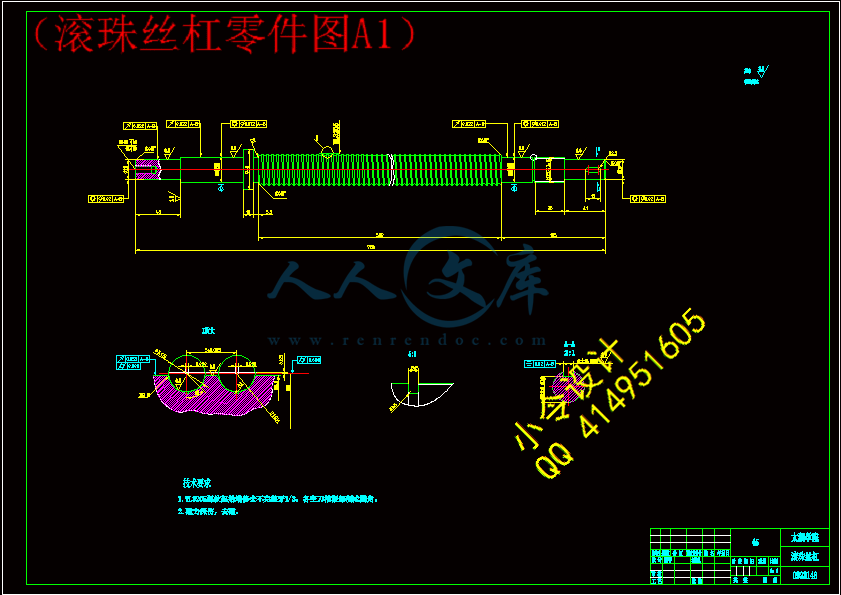