【温馨提示】 购买原稿文件请充值后自助下载。
[全部文件] 那张截图中的文件为本资料所有内容,下载后即可获得。
预览截图请勿抄袭,原稿文件完整清晰,无水印,可编辑。
有疑问可以咨询QQ:414951605或1304139763
摘 要
工业机器人专用减速器作为重要的机械传动部件具有体积小、重量轻、传动效率高等特点。本设计全面考虑到运转平稳、多齿啮合、轮齿均载等运动学和动力学的要求,从而实现承载能力高、传递效率高、可靠性高和动力学性能优良等指标,并且要便于制造、装配和检修,设计了具有合理结构的工业机器人专用减速器即摆线针轮行星减速器。
本论文所涉及的科研项目主要通过对摆线针轮行星减速器的主要零件的概念进行详细阐述,给出了摆线针轮减速器的用途,使用说明以及注意事项。列出了摆线针轮行星减速机的构造即输出部分,输入部分。通过对针摆行星传动减速器传动工作原理和特点进行分析,对针轮输出机构及针摆行星传动这种传动方式进行分析,以获得其理论设计和方法。从摆线针轮行星传动的共同点出发以及针摆轮行星减速器相对于少齿差行星减速器的优点提出针摆行星传动形式的设计计算方法。
本论文主要从以下方面出发对摆线针轮行星传动进行了研究:参照传统针摆行星传动基本设计计算方法以及对摆线针轮行星传动主要零部件的基本参数设计计算,并对摆线轮、柱销,针轮进行受力分析最终计算出转臂轴承和各支撑轴承所能承受的载荷大小,完成包括摆线轮、柱销等主要零件强度校核计算和轴承的寿命计算,给出主要零件机械加工的工艺过程,然后利用CAD画出了主要零件的草图和最后的装配图。
关键词:摆线传动 ; 摆线轮 ; 受力分析
Abstract
The cycloid—gear reducer is one of the most important transmission components of the pumping unit by its smaller volume,lighter weight and effective transmission. In order to realize four targets which include high transmission efficiency, high reliability and the excellent dynamics performance and guarantee credible lubricate ability, receive high efficiency of transmission, and make it easy for manufacture, assembly and inspection, we thought over all the requests in the round and design the rational structure cycloid—gear reducer.
By analyzing characteristics and working principle of cycloid drive, and the output pin wheel cycloid drive’s working principle, we obtion the design theory and method of this new kind of reduce. This paper mainly complete works include that provide the design method and complete the prototype design and dynamics analysis of virtual prototype.
This paper researches the following aspects of the output pin wheel cycloid drive. First, the basic parameters and dimensions of main parts of the output pin wheel cycloid drive are designed referring to design and calculation methods of the traditional cycloid drive, and mechanical analysis of the transmission system and the load condition and life of rotary arm bearings and steady bearings of each shafts are calculated, and at the same time the calculations including the strength of cycloid wheel, pins and other major parts are completes. Then, using CAD to draw sketches of the main components and final assembly drawing.
Keywords:Planet—cycloid Reducer; Cycloid ;force analysis
目 录
摘 要III
AbstractIV
目 录V
1 绪论1
1.1 课题研究的背景和依据1
1.2 本课题的研究意义1
1.3 课题国内外研究现状及发展趋势1
2 摆线针轮行星传动的简介4
2.1摆线针轮的概念4
2.2 摆线针轮减速机的用途,使用说明和注意事项4
2.2.1 用途4
2.2.2 使用条件4
2.2.3 润滑4
2.2.4 安装5
2.3 摆线针轮行星减速器的构造5
2.4 齿廓曲线的形成及其啮合原理6
2.5 摆线针轮行星传动的特点及应用8
3工业机器人的总体设计9
3.1工业机器人的组成9
3.1.1 工业机器人的系统组成9
3.1.2 工业机器人的基本机能组成9
3.2 机器人的结构分析9
3.2.1 机器人的总体结构的概念9
3.2.2机器人的传动结构10
3.3机器人的设计分析及总体方案的确定11
3.3.1 设计的任务要求11
3.3.2总体方案的确定12
3.3.3 工业机器人的主要技术参数12
4 摆线针轮行星齿轮传动的传动比计算和传动特点12
4.1摆线针轮行星齿轮传动的传动比计算13
4.2啮合的齿廓形成原理14
5 摆线针轮行星齿轮传动设计15
5.1针轮行星轮系的材料15
5.2 第一套摆线针轮加速器的设计15
5.2.1 选择结构形式,齿数及材料15
5.2.2 强度计算针齿中心圆半径15
5.2.3计算摆线轮和针轮的几何尺寸16
5.2.4 转臂轴承的选择计算17
5.2.5 针齿销弯曲强度计算18
5.2.6 W输出机构销轴弯曲强度计算19
5.3 第二套摆线针轮减速器的设计20
5.3.1 选择结构形式,齿数及材料20
5.3.2 接触强度计算针齿中心圆半径20
5.3.3 计算摆线轮和针轮的几何尺寸20
5.3.4 转臂轴承的选择计算21
5.3.5 针齿销弯曲强度计算22
5.3.6 W输出机构销轴弯曲强度计算22
6行星齿轮传动输出轴的轴承选择24
7 主要零件的机械加工工艺规程25
7.1 摆线轮的加工工艺路线25
7.2 针齿壳的加工工艺路线26
7.3 输出轴加工工艺26
7.4 偏心套加工工艺27
8结论与展望29
8.1 结论................................................................................................................................29
8.2 展望................................................................................................................................29
致谢.30
参考文献31
1 绪论
1.1 课题研究的背景和依据
减速器是连接动力机部分和工作机部分的应用最为广泛的通用传动机械,行星齿轮减速器对齿轮的齿廓曲线的主要要求是保证瞬时传动比是常数。目前,满足这一要求的常用于齿轮传动的齿廓曲线主要是渐开线和摆线。
1926年L.Braren发明了摆线针轮减速器,在少齿差行星传动结构上,将变幅外摆线的内侧等距曲线首先用于行星轮廓曲线并且把圆弧作为中心轮齿廓曲线以及渐开线少齿差行星传动模式,保留Z-X-F类N型行星齿轮传动。此发明专利被日本住友公司于1938年买断,当时日本人执行的是“引进—消化—创新”技术路线。
摆线针轮传动与普通渐开线齿轮或蜗轮传动相比的主要优点有:高传动比和高效率,一级减速时传动比范围是11~87,两级减速时的传动比范围是20~128;同轴输出机构重量轻和体积小;传动平稳且噪音低;因为针摆传动同时啮合的齿数要比渐开线齿轮传动同时啮合的齿数多,所以承载能力较大,啮合效率较高。
1.2 本课题的研究意义
减速器是各种机械设备中最常见的部件,它的作用是将电动机转速减少或增加到机械设备所需要的转速, 摆线针轮行星减速器由于具有减速比大、体积小、重量轻、效率高等优点,在许多情况下可代替二级、三级的普通齿轮减速器和涡轮减速器,所以使用越来越普及,为世界各国所重视。
摆线针轮行星减速器作为重要的机械传动部件具有体积小、重量轻、传动效率高的特点。本设计在全面考虑多齿啮合、运转平稳、轮齿均载等运动学和动力学的要求,现高承载能力、高传递效率、高可靠性和优良动力学性能等指标,而且要便于制造、装配和检修,设计了该具有合理结构的摆线针轮行星减速器。
1.3 课题国内外研究现状及发展趋势
针摆齿轮传动与普通渐开线齿轮或蜗轮传动相比的优点有:传动比高和高效率高;同轴输出结构体积小和重量轻;传动平稳和噪声低。因为摆线针轮传动同时啮合的齿对数要比渐开线齿轮传动同时啮合的齿对数多,所以承载能力更大,啮合效率更高;由于摆线轮以及针轮轮齿均可精磨、淬硬,比渐开线少齿差传动内齿轮的被加工性好,齿面硬度要更高,因而使用寿命更长;摆线轮的加工技术已经成熟,专业加工设备齐全,因此摆线轮已纳入通用件,在国内已做到通用化大批量生产,生产成本下降,因此摆线针轮专用减速器当前得到广泛应用。摆线针轮减速技术到现在,虽在品种、规格等许多方面做了改进,但在本质、原理上没有创新。现如今摆线针轮减速机,其原理和结构依然是1926年德国的原型。
图1.1 摆线针轮减速器的应用
目前,摆线针轮减速器的研究在国内外都得到了积极发展,从1990年开始,住友机械株式会社在“80系列”的基础上推出最新“90样本”的摆线针轮减速器,它的机型由15种扩大到21种,传动比由8种扩大到16种。我国对日本提高摆线针轮减速器性能的主要措施已进行较深入的分析,并且在赶超世界水平的同时也有了自己的创新成果,如与工程实际相符的摆线轮与输出机构受力分析以及对摆线轮齿形的优化设计等。
摆线针轮减速器所能传递的最大功率为132KW,输入轴的最高转速为1800r/min。美国研发直升飞机传动装置所做的摆线针轮传动装置试验样机,采用的是四片摆线轮,可以达到输入轴动平衡的新结构,输入转速达到2000r/min,传动功率达到205KW。
这些年来国内对摆线针轮传动的研究一直在不断发展,并且也取得了一些成果。主要如下:
(1) 中国农业大学何胜勇对行星摆线针轮减速机虚拟样机的建造与有限元分析进行了研究;
(2) 哈尔滨工业大学于影,于波,陈建新对摆线针轮行星减速器进行优化设计;
(3) 天津工程师范学院的戚厚军建立的2K.v型摆线针轮行星减速器的动力学模型.是以2K-V6型摆线针轮行星减速器为研究对象,在不改变减速器的外形尺寸及结构的情况下,分析了摆线轮修形和短幅系数对摆线轮齿啮合刚度的影响规律,和传动系统中的各种零件的刚度及针径系数对机器整机振动性能的影响;
(4) 大连交通大学何卫东教授主持的国家自然科学基金资助的项目《高承载能力高传动效率高可靠性新型针摆行星传动的研究》的科研成果《双曲柄四环板针摆行星传动》于2005年4月通过鉴定;
(5) 浙江大学吕方教授开发了一种新型的传动机械——长幅外摆线针轮行星传动减速机;
(6) 大连铁道学院张动生采用非线性有限元分析软件MSCMARC建立了摆线轮与各受力齿接触模型;首次对针齿和摆线轮齿面接触进行静态有限元分析,得出了摆线轮和针齿间的接触状态;
(7) 四川大学张流俊在首次应用有限元法取代传统的经验法进行摆线针轮减速器的结构设计,并提供了一个通用的摆线针轮减速机结构设计计算软件包。
(8) 大连铁道学院关天民和万朝燕对新型摆线针轮传动进行理论及受力分析;
(9) 大连铁道学院关天民教授提出了一种较为准确的针摆轮行星传动销孔式输出机构的受力分析理论,利用此理论可以得到整个工作过程中输出机构和柱销的受力情况;
(10) 鞍山钢铁学院高兴蚊、黄秋波对具有双面支撑输出机构以及多齿差齿形摆线针轮行星传动的齿廓曲线形状和啮合特性进行了理论分析。摆线针轮减速器的发展趋势是达到更高的运动精度,更高的传递功率和更广的传动范围。
自20世纪90年代以来来,在工业专用机器人回转装置选择中。摆线轮传动作为一种比较理想的传动形式应用其中。如日本住友重机械工业株式会社研发成功的机器人用R.v列,FA系列及FT系列产品均采用了摆线针轮传动结构形式,由于采用了最新的设计理论。从而产品外型美观大方、结构合理、传递功率得到提高。
近年来出现了数种在摆线针轮行星传动基础上的新型传动型式,使其能够更好适应高
精度的运动传递和控制,用于机器人关节驱动、精密机床等高精度摆线轮传动技术的研究,其中常用的有以下几种:
(1). TWINSPFN减速器近来由斯洛伐克的一家公司推出,这种轴承式减速器不仅能承受非常大的径向力而且还能承受轴向力,并且使用寿命和传动效率也有所提高。
(2) .RV减速器。RV减速器是近年来由日本帝人公司推出的一种摆线传动,是由第一级普通渐开线直齿轮减速器部分和第二级针摆轮减速器部分组合成的两级行星传动机构。
(3) .三片摆线轮减速器,是由日本著名的住友重机械工业株式会社推出的产品,在此传动中采用了三片相互呈角布置的摆线轮结构,增加了摆线轮的数量提高了传动效率。
(4). Dojen减速器由美国Mectrol公司生产,传动机构采用了机芯式设计,每个针齿都采用悬臂方式,在针齿另一端加工有锥度,和机壳上的锥孔相配合,能自动定心,不仅能保证顺利装配又能消除全部间隙。
(5). 摆线球齿减速器,是一种将外摆线、内摆线轮结合起来的双摆线减速器,既将针轮改为钢球齿轮,又将两摆线轮改为摆线沟槽,因而是摆线针轮减速器的一种变形。
FA高精度减速器是当今世界上最新的传动装置,它具有体积小.传动比范围大.寿命长、稽度保持稳定、效率高等一系列的优点.由于它与机器人中常用的谐波传动相比有较高的疲劳强度、大的刚度和长的寿命。两且回差耪度高,因此FA减速机在工业专用机器人传动中正在得到越来越广泛的的应用:它还广泛用于测量装置,微型大传动比减速装置、办公设备、摆线传动装置,智能住宅传动装置等机械系统中.由于在这些精密传动中,通常传递的载荷不大,但要求传动精度高,传递运动准确,因而对其传动链的设计要求较高。

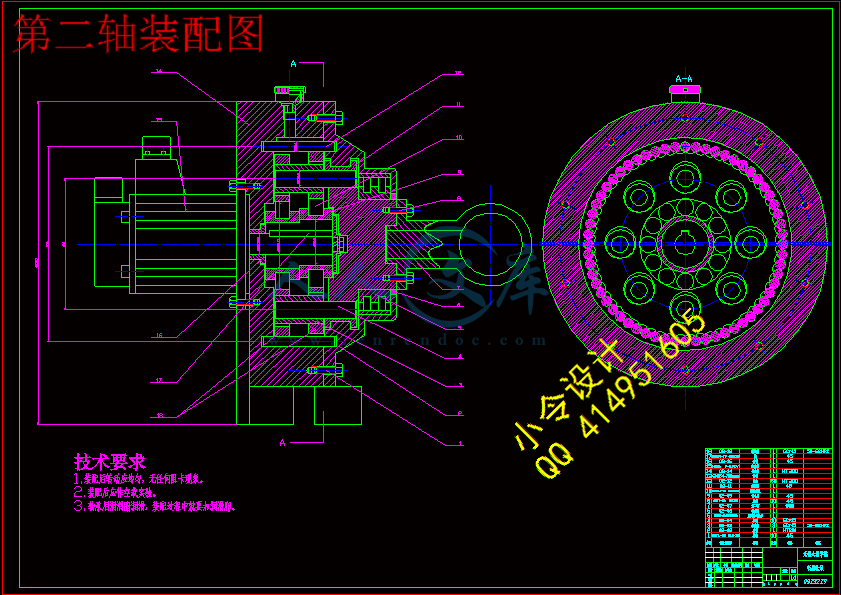
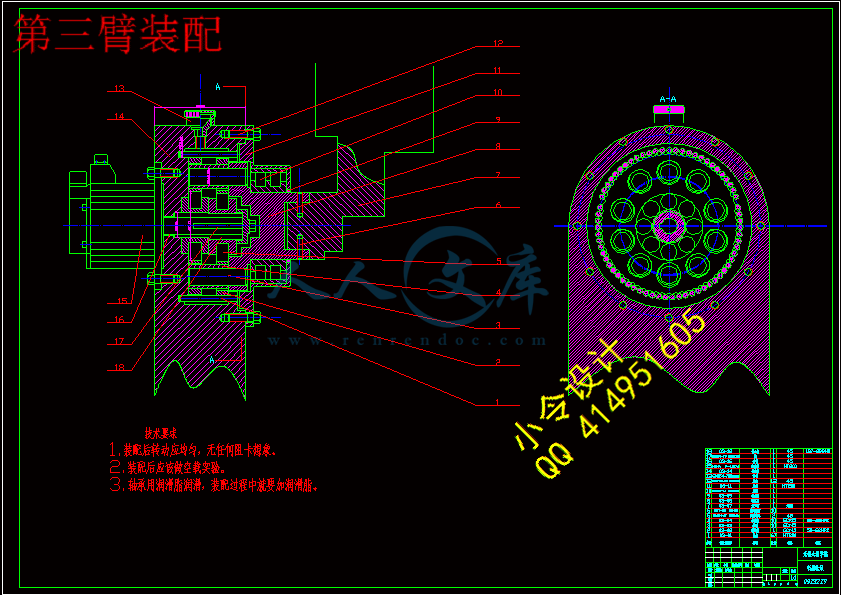
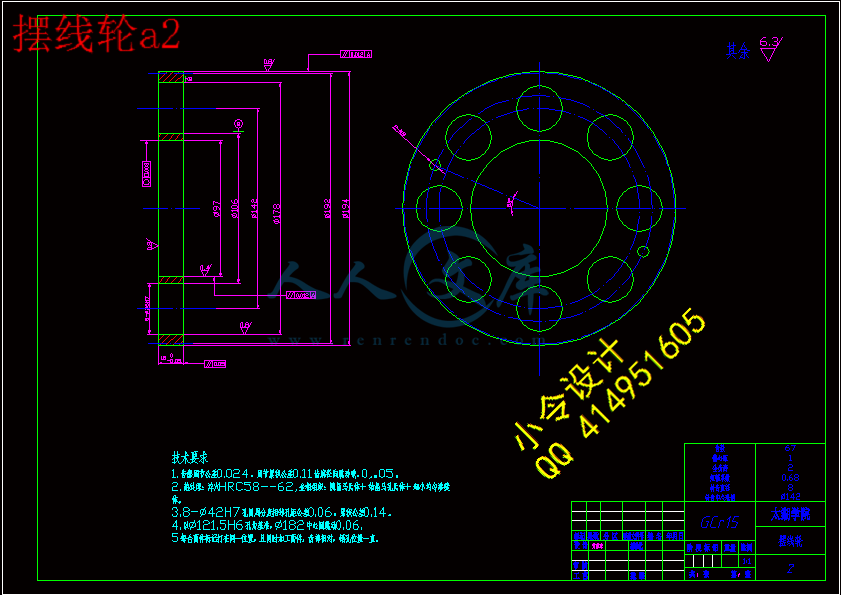
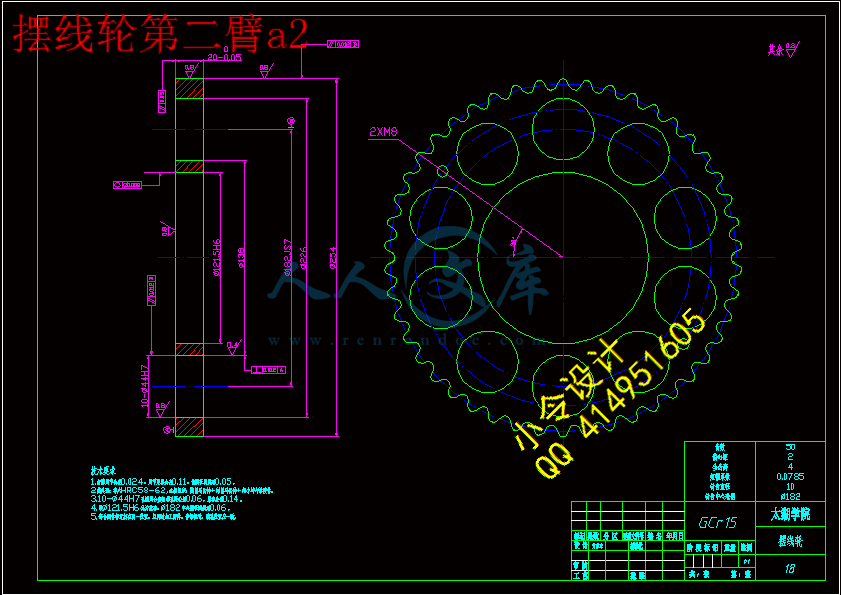
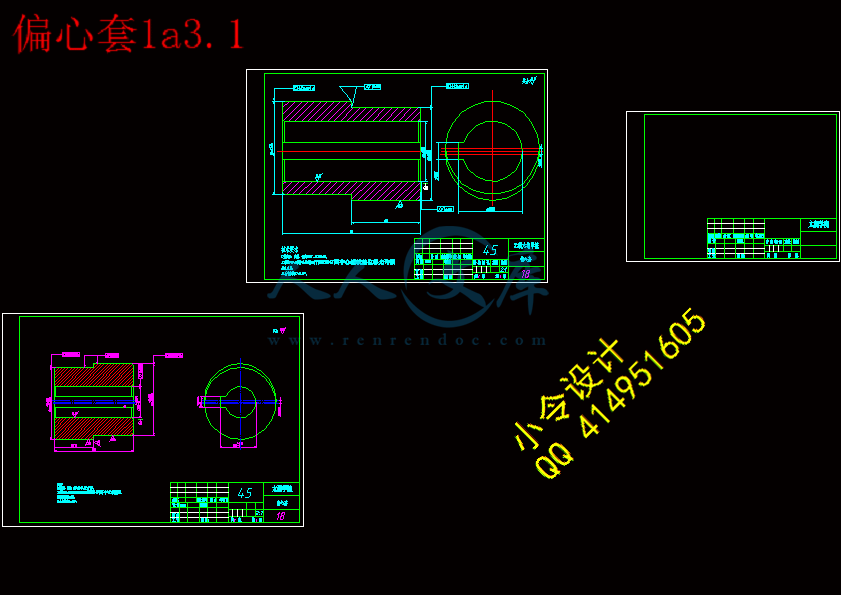