【温馨提示】 购买原稿文件请充值后自助下载。
[全部文件] 那张截图中的文件为本资料所有内容,下载后即可获得。
预览截图请勿抄袭,原稿文件完整清晰,无水印,可编辑。
有疑问可以咨询QQ:414951605或1304139763
摘要:破碎机械设备,属于矿山机械范畴。这这类机械设备在冶金、建材、化工、能源、交通建设、城市建设和环保等诸多领域有广泛的用途。简摆一般制成大型和中型的,复摆一般制成中型和小型的。简摆破碎机可以产生很大的破碎力,这是复摆破碎机所不能能、低能耗的新型颚式破碎机,从而大大提高了破碎机的性能,缩短了产品开比的,故在大型破碎机中一般用这种结构,复摆腭式破碎机的生产能力高于简摆腭式破碎机约30%,同时也因为过大的垂直行程,使得定、动腭衬板(齿板)磨损很快,大大降低了使用寿命。我国自50年代生产腭式破碎机以来,在破碎机设计方面经历了类比、仿制、图解法设计阶段,目前正向计算机辅助设计阶段过渡。国外从上世纪中后期开始利用计算机仿真技术对颚式破碎机机构、腔型、产量和磨损等进行优化,高性发周期,提高了产品的市场竞争力。
本文中所设计PEJ900X1200简摆颚式破碎机的设计要求为:破碎机偏心轴偏心距为25mm,连杆长度为1325mm左右,破碎腔设计为900×1200mm,破碎腔啮角20度,传动角为45~55度,动颚上端厚度为316mm,肘板长度为300~400mm,破碎机悬挂高度为100~160mm。腭式破碎机动颚水平行破碎腔啮角的大小直接关系到物料的受力状态,机架结构设计和破碎机产量,小的啮角有利于提高破碎机产量,利用先进破碎原理进行物料破碎,但破碎机高度将增加。所以根据经验值,本设计采用的啮角为20度。
关键词:简摆 腭式 破碎腔
Abstract:Broken mechanical equipment, areas of mining machinery. That such machinery and equipment in metallurgy, building materials, chemicals, energy, transportation, urban construction and environmental protection, and many other fields have a wide range of uses. Pendulum the type breaker put into large and medium-general, made of medium-sized compound pendulum general and small. Pendulum the type breaker can produce great breaking force, which is facing complex than can not be broken by the machine, so the large breakers in general with such a structure, the compound pendulum palate crusher capacity than simple pendulum palate crusher - About 30 per cent, but also because of too great a vertical journey, making set, moving the palate liner (tooth plate) and wear very quickly and greatly reduce the service life.Our country since the 50's productions Oral cavitytype breaker, hasexperienced analogy, the imitation, the graphic method design stage inthe breaker design aspect,At present to computer-aided design stage transition. The productionmanufacture At present to computer-aided design stage transition. The productionmanufacture Oral cavit the type breaker more and more big, the performancemore and more good, the variety are more and more many, and in oninternational holds the certain market. the type breaker more and more big, the performancemore and more good, the variety are more and more many, and in oninternational holds the certain market.
In this article designs PEJ900X1200 Pendulum the type breaker thedesign request is:The breaker eccentric shaft distance is 25mm, the connecting rodlength is about 1325mm, the broken cavity design is 900×1200mm,The broken cavity gnaws angle 20, the transmission angle is 45~55,moves the jaw upper extreme thickness is 316mm, The wrist plate length is 300~400mm, the breaker is hanging highly is100~160mm.Designs small the jaw type broken mobile jaw horizontal travellingschedule to have the use to reduce static, moves Board the attrition,improves the breaker stress,Lengthens board the service life. The broken cavity gnaws the anglethe size directly to relate the material the stressful condition, therack structural design and the breaker output, small gnaws the angleto be advantageous to enhances the breaker output,Uses the advanced broken principle to carry on the material brokenly,but the breaker highly will increase.
keyword: Pendulum type of Oral cavity broken cavity
目 录
1 概述
2 物料破碎及其意义
2.1 物料破碎及其意义3
2.2 破碎物料的性能及破碎比5
3 工作原理和构造
3.1 工作原理10
3.2简摆腭式破碎机的结构11
4 主要零部件的结构分析
4.1连杆14
4.2动腭15
4.3齿板的结构16
4.4肘板17
4.5调整装置17
4.6保险装置18
4.7机架结构19
4.8传动件20
4.9飞轮20
4.10润滑装置20
5 简摆腭式破碎机的主参数设计计算
5.1 机构参数21
5.2 破碎力25
5.3 功率的计算27
5.4 主要零件受力计算28
6 重要零件的设计和校核
6.1带轮的设计30
6.2曲轴的设计计算32
6.3 滑动轴承的设计计算36
7 腭式破碎机的饿安装与运转
7.1破碎机的安装38
7.2机架的安装38
7.3连杆的安装39
7.4肘板的安装39
7.5动腭的安装39
7.6齿板的安装39
7.7破碎机的运转40
8用对一个主要零件进行有限元分析
8.1solidworks软件介绍41
8.2CosmosWorks功能和特点41
8.3对曲轴的有限元分析42
8.3变形结果48
参考文献49
致谢50
1 概述
破碎机械是对固体物料施加机械力,克服物料的内聚力,使之碎裂成小块物料的设备。
破碎机械所施加的机械力,可以是挤压力、劈裂力、弯曲力、剪切力、冲击力等,在一般机械中大多是两种或两种以上机械力的综合。对于坚硬的物料,适宜采用产生弯曲和劈裂作用的破碎机械;对于脆性和塑性的物料,适宜采用产生冲击和劈裂作用的机械;对于粘性和韧性的物料,适宜采用产生挤压和碾磨作用的机械。
在矿山工程和建设上,破碎机械多用来破碎爆破开采所得的天然石料,使这成为规定尺寸的矿石或碎石。在硅酸盐工业中,固体原料、燃料和半成品需要经过各种破碎加工,使其粒度达到各道工序所要求的以便进一步加工操作。
通常的破碎过程,有粗碎、中碎、细碎三种,其入料粒度和出料粒度,如表1——1所示。所采用的破碎机械相应地有粗碎机、中碎机、细碎机三种。
表1—1 物料粗碎、中碎、细碎的划分(mm)
类别入料粒度出料粒度
粗碎
中碎
细碎300~900
100~350
50 ~100100~350
20~100
5~15
制备水泥、石灰时、细碎后的物料,还需进一步粉磨成粉末。按照粉磨程度,可分为粗磨、细磨、超细磨三种。
所采用的粉磨机相应地有粗磨机、细磨机、超细磨机三种。
在加工过程中,破碎机的效率要比粉磨机高得多,先破碎再粉磨,能显著地提高加工效率,也降低电能消耗。
工业上常用物料破碎前的平均粒度 D刁民破碎后的平均粒度d之比来衡量破碎过程中物料尺寸变化情况,比值i称为破碎比(即平均破碎比)
为了简易地表示物料破碎程度和各种破碎机的方根性能,也可用破碎机的最大进料口尺寸与最大出料口尺寸之比来作为破碎比,称为公称破碎比。
在实际破碎加工时,装入破碎机的最大物料尺寸,一般总是小于容许的最大限度进料口尺寸,所以,平均破碎比只相当于公称破碎比的0.7~0.9。
每各破碎机的破碎比有一定限度,破碎机械的破碎比一般是i=3~30。如果物料破碎的加工要求超过一种破碎机的破碎比,则必须采用两台或多台破碎机械串连加工,称为多级破碎。多级破碎时,原料尺寸与最终成品尺寸之比,称总破碎比,如果各级破碎的破碎比各是 , … 。则总破碎比是
= …
由于破碎机构造和作用的不同,实际选用时,还应根据具体情况考虑下列因素;
1)物料的物理性质,如易碎性、粘性、水分泥沙含量和最大给料尺寸等;
2)成品的总生产量和级配要求、据以选择破碎机类型和生产能力;
3)技术经济指标,做到既合乎质量、数量的要求、操作方便、工作可靠,又最大限度节省费用。
2 物料破碎及其意义
2.1 物料破碎及其意义
从矿山开采出来的矿石称为百年原矿。原矿是由矿物与脉石组成的,露天矿井开采出来的原矿其最大粒度一般在200~1300mm之间,地下矿开采出来的原矿最大粒度一般在200~600mm之间,这些原矿不能直接在工业中应用,必须经过破碎和磨矿作业,使其粒度达到规定的要求、破碎是指将块状矿石变成粒度大于1~5mm产品的作业,小于1mm粒度的产品是通过磨碎作业完成的。
2.1.1 破碎的目的
(1)制备工业用碎石
大块石料经破碎筛分后,可得到各种不同要求粒度的碎石。这些碎石可制备成混凝土。它们在建筑、水电等行业中广泛应用。铁路路基建造中也需要大量的碎石。
(2)使矿石中的有用矿物分离
矿石有单金属和多金属,而且原矿多为品位较低的矿石。将原矿破碎后,可以使有用金属与矿石中的脉石和有害杂质分离,作为选矿的原料,除去杂质而得到高品位的精矿
(3)磨矿提供原料
磨矿工艺所需粒度大于1~5mm的原料,是由破碎产品提供的。例如在炼焦厂、烧结厂、制团厂、粉末冶金、水泥等部门中,都是由破碎工艺提供原料,再通过磨碎使产品达到要求的粒度和粉末状态。

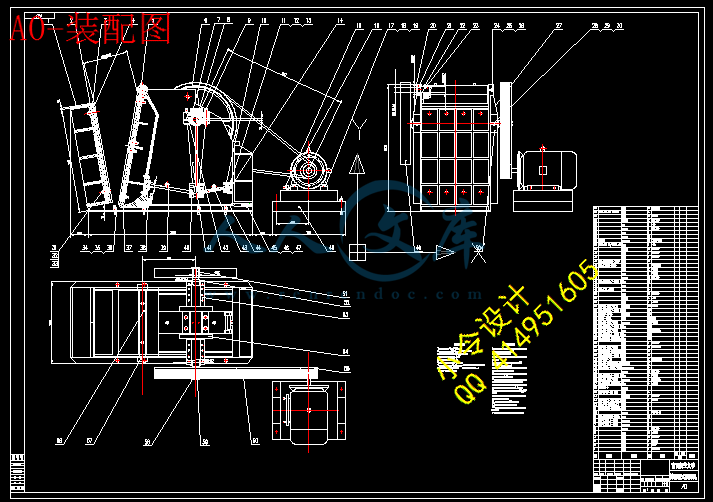

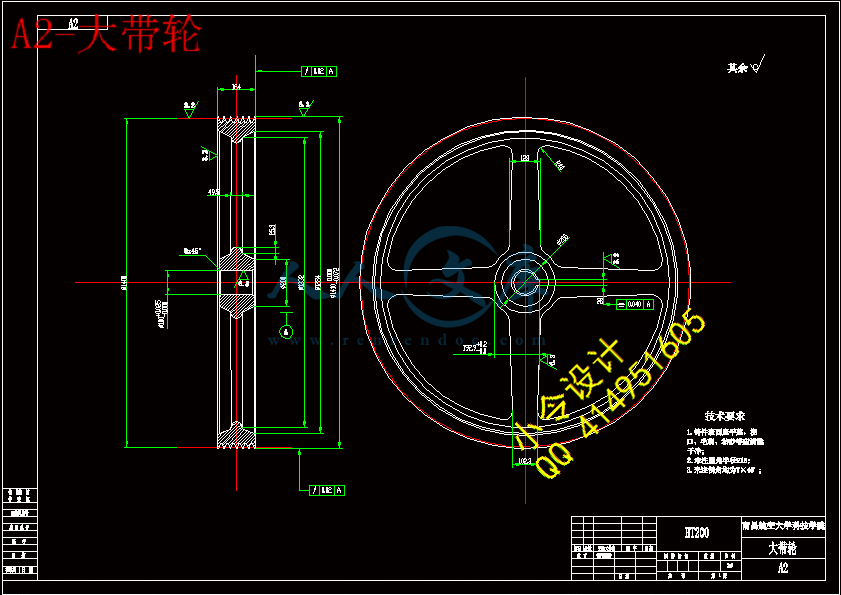

