摘 要
围板箱作为产品外包的物流设施,围板箱越来越受客户的欢迎,使用量巨大。然而,现有的围板箱生产方式落后,在生产中人为因素较大,这使得围板箱的生产上存在着生产效率低,质量不稳定等缺陷。这严重影响着围板箱的应用。为了提高劳动生产率,降低工人劳动强度,节约生产成本,我们对围板箱的现有生产工艺进行了研究,通过对原有围板箱生产工艺的分析,设计了适应于围板箱的自动合围装置。
围板包装箱在生产过程中主要分为上料、拼接、钻铆、合围等几部分工序,本论文主要是设计合围装置的说明。将2个用铰链连起来的2片木板的两端分别铆接起来。连接起来的木板链一端是只有孔,另一端是仅铆接了半面铰链(另半面没有铆接)。首先第一步是铆接了半面铰链的一端在前另一端在后,通过挡板来约束定位;第二步运用气压缸来推动夹紧块来夹紧木板,使之不能像对滑动;之后在是夹紧装置绕主轴旋转180°,在重复第一、二步操作(第二次只旋转90°),使两块木板合围,之后通过平移夹紧旋转装置使需要铆接的部分移到铆接机上,在上铆钉铆接从而完成合围。
关键词:围板箱;合围;铆接;自动生产线
Abstract
Hoardings box as outsourcing logistics facilities around the crate more and more popular with customers , a huge amount of use . However, the backward the existing hoardings box mode of production in the production of man-made factors , which makes the production of hoardings box there is low productivity, unstable quality defects . This has seriously affected the application of hoardings box . In order to improve labor productivity, reduce labor intensity , reduce production costs , we conducted a research on the hoardings Box existing production process through the analysis of the production process of the original hoardings box , designed to adapt to the hoardings box automatically encirclement devices.
The hoardings box on materials , stitching, drilling and riveting , encircled in the production process is divided into several parts process of this thesis is the design of the encirclement device . Two hinges to link two of the ends of the planks were riveted . Connected one end of the wood chain is the only hole , the other end is only half a face riveted hinge ( the other half of a riveting ) . First step is riveting half-face one end of the hinge in front the other end of the baffle to constrain the positioning ; second step the use of pneumatic cylinder to push the clamping block for clamping wood , so they can not like sliding ; after clamping device around the spindle 180 ° , repeat the first and second steps ( second rotation only 90 ° ) , so that the two pieces of wood encircled by the pan after clamping rotary device to make part moved to the riveting machine riveting , thus completing the encirclement on the rivet .
Key words: Hoardings box ; encirclement ; riveting ; automated production lines
目 录
摘 要III
AbstractIV
目 录V
1 绪论1
1.1本课题的研究内容和意义1
1.2国内外的发展概况1
1.3 本文主要设计内容4
2 生产线总体结构设计5
2.1 围板箱生产工艺分析5
2.1.1 围板尺寸参数5
2.1.2 生产线工艺流程5
2.1.3 总体结构7
2.1.4 生产节拍的拟定7
2.1.5 控制系统8
3 各部分具体设计9
3.1木料传入部分设计9
3.2 木料的定位夹紧装置设计9
3.3 旋转移位装置10
3.3.1 电动机的选取11
3.3.2 传动比的分配13
3.4 伸缩移位19
3.5 铆接20
3.5.1 定位20
3.5.2 送钉装置20
3.5.3 铆接装置29
4 结论与展望35
致 谢36
参考文献37
1 绪论
1.1 本课题的研究内容和意义
围板箱是由托盘、箱体和箱盖三部分组成,组成每层围板的四片或六片木板用L型铰链连接。由于装箱的灵活性、对装载物的适应性和重复使用性,围板箱被广泛应用于机械、化工、电子、五金以及其他领域的物流配送,具有能回收、降低成本、环保等优点。
围板箱的优点:
1. 围板箱的长、宽根据托盘的尺寸确定,使用层数可根据承载物的高度来决定,最大限度地提高箱体空间的利用率。
2. 由于无钉化作业,显著地降低了工人在装卸过程中发生工伤的风险。
3. 不存在因箱体的部分损坏而令整箱报废的情况,对于同一尺寸,可实现完全互换使用。
4. 运输时可将围板折叠为双层或四层相连接的木板结构摆放在托盘上,大大地减少贮运体积,有效的降低运输成本。
在循环包装系统里,方便灵活的围板箱有着无可比拟的优势。这是一种标准的物流器具,损坏的顶盖与侧板很容易进行替换,整体循环包装系统的投资比较低廉,而使用寿命则可达十年之久,这也是一种可靠的坚固的可以折叠的包装系统。由于装箱的灵活性、对装载物的适应性和重复使用性,围板箱被广泛运用于机械、化工、电子、五金以及其他领域,此外还具有传统木箱不具备的很多优点,因而这种产品在国外也特别受欢迎,运用也很普遍。
a b
图1.1 围板
如图1.1中围板样式,本论文主要生产设计的是图b所示的围板。
然而,现有的围板箱生产方式落后, 在生产中人为因素较大,这使得围板箱的生产上存在着生产效率低, 质量不稳定等缺陷,这严重影响着围板箱的应用。
为了提高劳动生产率,降低工人劳动强度,节约生产成本,使用自动生产线产品生产和质量稳定,我们对围板箱的现有生产工艺进行了研究,在此特设计围板包装箱的自动生产线合围装置。
1.2 国内外的发展概况
制造业是国名经济发展的支柱产业,也是科学技术发展的载体及使其转化为规模生产力的工具与桥梁。装备制造业是一个国家综合制造能力的集中体现,重大装备研制能力是衡量一个国家工业化水品和综合国力的重要标准。现在,我国正值“十一五”建设期间,国家将振兴装备制造业作为推进工业结构优化升级的主要内容。按照立足科学发展,着力自主创新、完善体制机制、促进社会和谐的总思路,组织实施国家自主创新能力建设规划和高技术产业发展规划,大力加强自主创新支撑体系建设,着力推进重大产业技术与装备的自主研发,实现高技术产业由大到强的转变,全面提升我国全面提升我国的自主创新能力和国际竞争力,为调整经济结构、转变经济增长方式,实现全面建设小康社会的奋斗目标奠定坚实基础。
板箱作为产品外包的物流设施,围板箱越来越受客户的欢迎,使用量巨大。然而,现有的围板箱生产方式落后, 在生产中人为因素较大,这使得围板箱的生产上存在着生产效率低, 质量不稳定等缺陷,这严重影响着围板箱的应用。
在国内,围板箱是一款可反复循环使用的新型包装,适用于紧固件、金属球、冲压
件等不规则产品的包装,是出口到欧洲的产品包装的不二选择。围板箱基本以木板为主要材料,侧板大多数都是采用模板或者大板制作,使得材料的选取过于苛刻,而且成本比较高。围板箱的生产也主要以人工为主,木板加工以半自动化为主。
而国外,德国KTP公司可以说是制造围板箱的代表,经过其几代人的努力,现今已经研制出了可折叠式塑料围板箱(见图1.2)。其生产方式也采用了全自动化的生产线模式,箱子规格也都已经基本标准化,方便统一规格生产。
图1.2 折叠式围板箱
从国内外发展情况来看,国内外的围板箱生产具有以下的优缺点:
1、在国内,围板箱的规格可以根据买家的要求来制定,比较方便灵活;在国外,围板箱的规格趋于标准化,方便一体化生产,销售,物流规格可渐渐统一,适应以后的发展前景。
2、在国内,围板箱各部分不存在因箱体的部分损坏而令整箱报废的情况,对于同一尺寸,可实现完全互换使用;在国外,部分围板箱已经趋于一体化,防水,防尘,全面保护物品,存储较方便。
3、在国内,使用木板为主材料,成本低廉;在国外,开始使用可完全回收利用的塑料,从而减少树木的砍伐,保护环境。
4、国内,围板箱的生产方式采取以半自动化为主,有订单再生产的方式;在国外,围板箱的生产方式采取全自动化生产线的模式。
围板箱生产过程中对于木板的连接采用的是铆接方式连接的,自动钻铆技术的国内外状况如下:
自动钻铆技术从上个世纪50年代开始起步,经历了手动、半自动化、全自动化等
阶段,在其发展过程中,不断吸收了其他技术,成为了-I-J综合多学科、多技术的专用
技术,逐步走向完善。
(1) 国外发展现状
自上世纪50年代以来,自动钻铆技术在美国、法国、前苏联、德国等国都得到了相应的发展。
美国是最早发展自动钻铆技术的国家,早在50年代初就已在飞机铆接装配生产线上应用了自动钻铆机,经过50多年的发展,现在世界各航空航天工业发达国家都已广泛采用这项技术。自动钻铆技术主要包含以下内容:
①设备的研制、开发;
②对各种干涉配合新型紧固件进行自动安装;
③自动钻铆工艺;
④数字化铆接的实现。
目前,波音、 空客的有关飞机结构设计手册中明确规定:为确保连接质量, 设计时应使自动化铆接获得最大限度的使用。由此可以看出,自动钻铆技术不只是工艺机械化、自动化的要求,更主要的还是飞机本身性能的要求。由于设计上的这一要求,就使得自动钻铆技术的发展具有生命力。所以近20年来,自动钻铆技术得到迅速发展。
美国自动钻铆机的最早制造厂商是GEMCOR(通用电气机械公司)[14],它是向世界各国飞机制造行业提供自动钻铆机的主要厂商之一。该公司生产的系列化产品质量可靠,并配套有各种型号的数控托架。到现在为止,销售的自动钻铆机数量已达2000台以上,其中190台具有定位系统。公司生产的自动钻铆机主要型号有G200、G300、G400、G900、G666、G39A、G4013、G4026、G5013。其中G200、G400型是较早的型号,G300为比较通用的型号,而G900型的功能比较齐全。具有无头铆钉钻铆功能的型号有G900、G666、G39A、G400自动钻铆机G4013、G4026、G5013。近几年无头铆钉的工作原理有所发展,机床采用GEMCOR专利的SQUEEZE/SQUEEZE双挤铆方式,先预挤铆,再进行挤铆,不仅能保证上下铆头同步成形上下镦头,而且铆接质量大大提高。各种型号机床可通过改变下铆砧形状和尺寸来适应各种结构的要求。GEMCOR公司生产的数控托架(也称自动定位系统)主要型号有G63、G79、G86、747WRS、G2000等。
世界各航空工业发达国家的自动钻铆技术基本上都是从美国引进的,然后再进行国产化, 以适应本国航空工业发展的需要。法国自动钻铆机在80年代初为适应欧洲发展A300系列飞机而开发的一项专用设备。十年来,他们依靠优良的技术和售后服务,不仅占领了欧洲的大部分市场,而且挤进了亚洲和北美市场,成为与美国GEMCOR公司自动钻铆机相抗衡的竞争对手,日益得到广大用户的信任。
RBCOULES AUTOMATION工厂生产自动钻铆机的基本品种有P.100型(台式)、P.300、P.600型(基本型)和PRECA CNC370型数控钻铆系统等[15]。它的产品可根据用户的特殊需求,在基本型基础上作各种改进。前苏联与西方相比,自动钻铆技术发展较晚。五六十年代苏联致力于发展压铆技术,
生产了型号众多的压铆机。压铆机只能完成铆接工序,与一次定位即能完成夹紧、钻孔、插钉、形成墩头等自动钻铆机相比,无论从生产效率及接头质量等方面都显逊色。前苏联自70年代初引进了美国GEMCOR公司的自动钻铆机后,已发展了自己的自动钻铆机系列。
德国在发展自动钻铆技术方面走的是另一条道路,在此项技术的应用与发展中,凭借其雄厚的资金、技术力量,一方面大量引进先进的自动钻铆系统和柔性装配系统,另一方面自己也积极研制开发高自动化的铆接装配系统。故德国的自动钻铆技术虽然起步较晚,但己比较先进,脱机编程系统已应用成熟,可与CATIAV5进行数据交换,实现数字化铆接。目前BRGTJE公司的机身铆接柔性工装和柔性装配生产线在世界处于领先地位[16]。
(2) 国内发展现状
我国自动钻铆机的研制起步较早,上世纪70年代初开始研制自动钻铆机,并研制出各种型号的自动钻铆机若干台。但是由于设备本身运行的稳定性以及配套产品应用需求等方面存在问题,中断了研制和使用。到了80年代中期,随着对外转包生产项目的增加,各飞机制造厂开始从国外引进自动钻铆机并将其应用于实际生产中。
西飞公司分别于1985和1992年引进G400及G900自动钻铆机。这两台机床均配以手动托架,分别用于加工美国波音公司和麦道公司(已于1997年并入波音公司)的垂尾平尾及法航、意航、加航的零件。随着国际问技术交流的不断深入,我国又同美国麦道公司合作生产干线客机MD.90.30。西飞公司的两台自动钻铆机已满足不了生产的需求。1993年从GEMCOR公司引进了G4026SXX.120型自动钻铆机,用于MD.90.30等飞机的机翼壁板的铆接装配生产。由于没有引进与之配套的托架系统,1995年西飞公司与西北工业大学联合研制数控托架。该托架采用Z坐标两立柱支撑的结构形式。由于受当时工艺制造水平的限制,围框刚性不足,存在一定问题。随着麦道干线机合作生产项目的终结.数控托架的研制工作也宣告终止。1998年西飞公司引进APS公司的RM$335钻铆机,取代G400机床。
自动钻铆技术在国外发展极为迅速,而我国与国际先进水平差距越来越大。从整个航空航天产业全局的生存和发展出发,从技术经济综合效益考虑,需要逐步缩小与国外先进水平的差距。通过引进国外先进的数控钻铆系统及铆接生产线,学习积累国外先进技术和工艺方法。再结合型号研制,对引进的自动钻铆机开发配套数控托架,从而降低制造成本.探索出一条适应于我国国情的工艺技术改造的心路。
1.3 本文主要设计内容
本论文主要完成围板合围工艺,主要是研究如何将两组两块用铰链连接的木板,一端是长板没有铆接,另一端是短板仅铆接了半面铰链(另半面没有铆接)的木板链通过装置合围成如图1.1(b)所示的围板箱,对于两组木板链的接口采用铆接的方式进行连接,铆接过程中需要考虑如何定位以及如何自动上铆钉,因此也需要设计定位夹紧装置和自动供钉装置,确定合围铆接方案。第二章主要说明围板参数,以及总体结构方案和合围工序的流程图;第三章是具体说明我所设计的合围装置各部分装置的设计。第四章是对整个设计说明的总结及不足和改进之处。
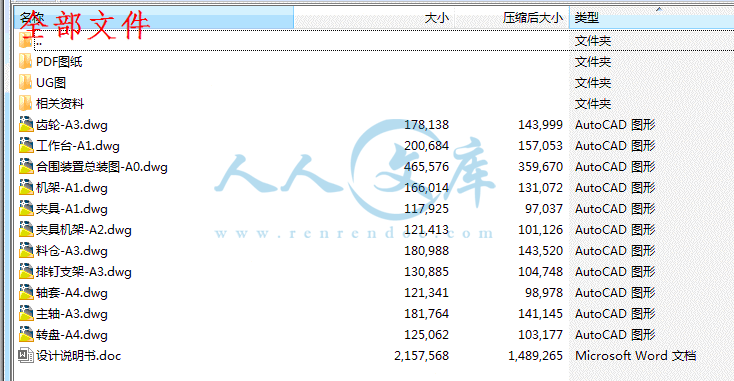
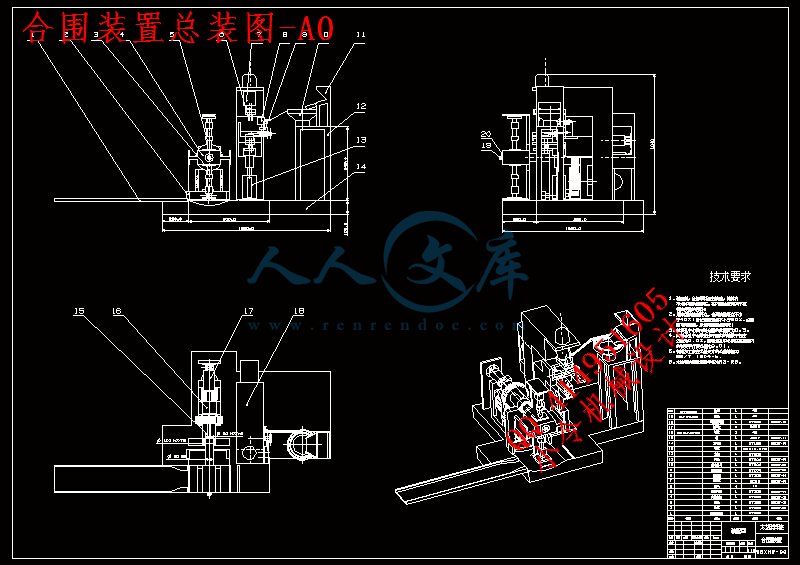

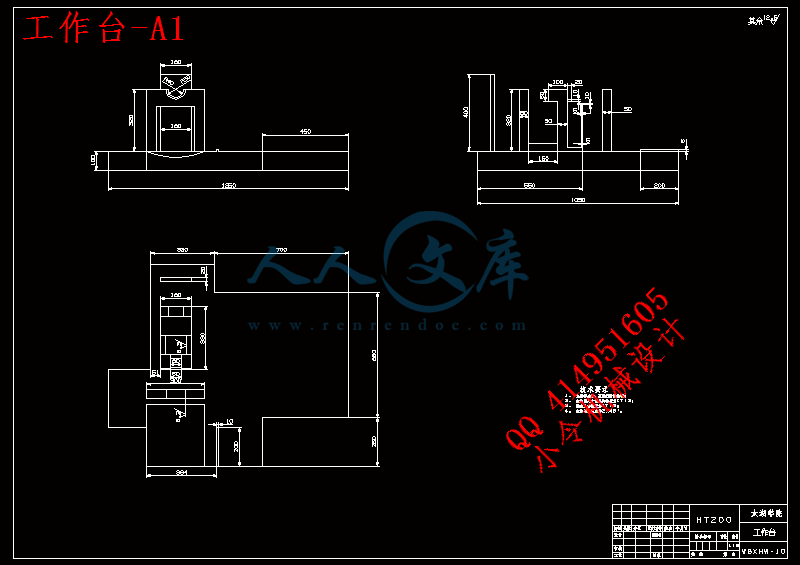
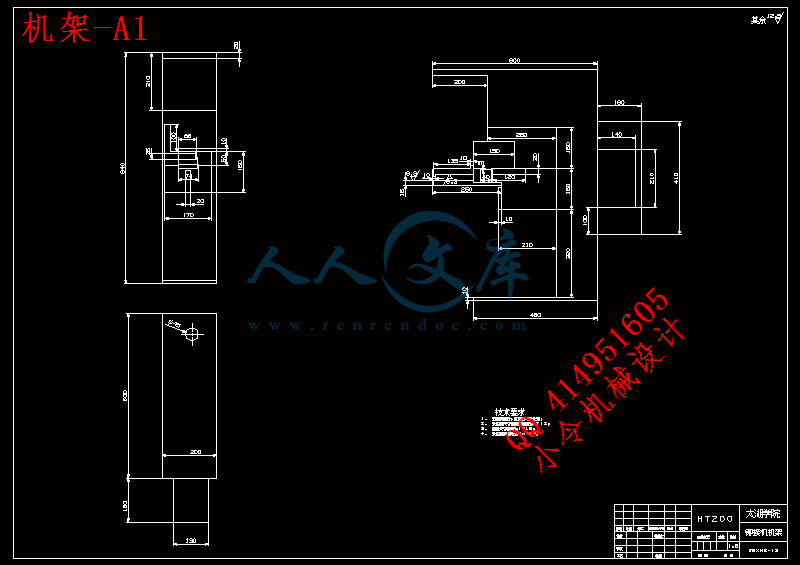
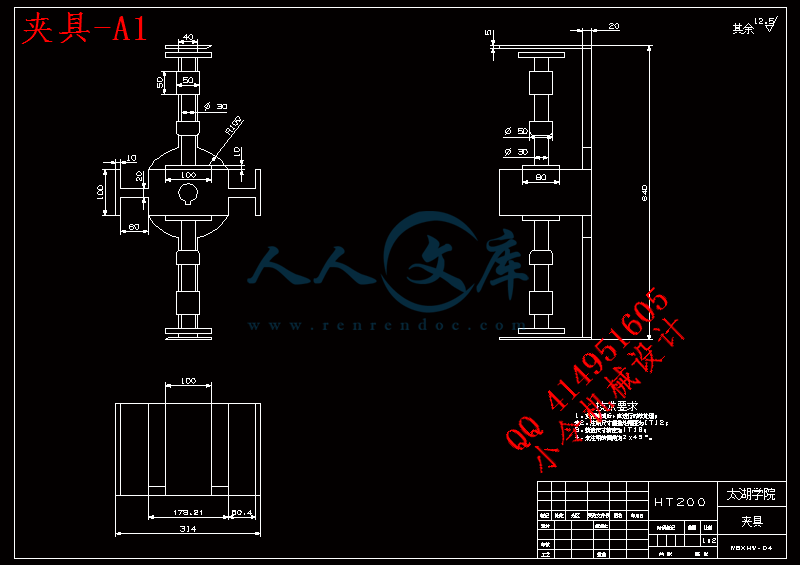