摘要
本文详细介绍了遥控器电池后盖注塑模具的设计,共分十四节,主要包括:塑件材料的分析与设计方案的论证;注塑机的选择;模具结构的设计;成型零件的设计;导向机构的设计;脱模机构的设计;侧向分型与抽芯机构的设计等。
本次设计为一模两腔,塑件材料选用了丙烯腈-丁二烯-苯乙烯共聚物(即工程材料ABS),浇口形式选用了侧浇口,模具结构为直接分型——推杆推出机构。通过以下计算和设计是可行的,并可以应用到实际生产中。
本次设计主要是对一种塑料遥控器电池后盖进行模具设计。本文先介绍了注射模具国内外的发现状况及发展趋势,其次介绍了注射成型原理和工艺过程;根据塑件要求选择合适的注塑机,进而选择合适的浇注系统与冷却系统;通过计算,对导向机构、脱模机构和侧向分形与抽芯机构进行设计。
该模具的凸凹模均采用嵌入式的型腔和型芯,精度高,节省材料,改善了模具加工的工艺性,降低了模具的生产成本。该模具采用单分型面设计,通过滑块和斜导柱实现开合模动作,模具运动平稳可靠。塑件能顺利脱模,该模具总体结构设计合理,模具的制造成本低。成型的壳体塑件质量合格稳定,使塑件质量符合设计和使用要求。
关键词:遥控器电池后盖;注塑模具;侧抽芯机构;导向机构;脱模机构
The Design of the Telecontroller Injection Mold
Abstract
This paper introduced the design of telecontroller,and consisted 14 parts.Mainly include analysis of plastic material and argumentation of design project; selecting injection machine; devising mold structure;devising molding parts; devising oriented framework; devising stripping framework; devising side parting and pulling framework.
The mold is consisted of two cavities. The plastic material select acrylonitrile butadiene-styrene copolymer (i.e.engineering material ABS). The sprue form choose a side gate, die structure for direct classification--push rod pushing mechanism.By the following calculation and design is feasible, and can be applied to practical production.
The design is mainly remote control battery cover of a plastic mold design. This paper first describes the situation and development trend of the injection mold found at home and abroad, followed by injection molding principle and process; plastic parts require the injection molding machine, and then select the appropriate gating system and cooling system;, oriented agencies, stripping agencies and lateral fractal design core-pulling mechanism.
The mold punch and die are embedded in the cavity and core, high precision, material savings, improved mold process, reducing the cost of production of the mold. The mold with a single parting surface design, mold opening and closing action slider and Bevel Pillar, the mold movement is smooth and reliable. Plastic parts smooth stripping overall structure of the mold design, mold manufacturing costs low. The molding of the plastic parts of the housing of acceptable quality and stability, so that the quality of plastic parts comply with the design and use requirements.
Key Words: telecontroller; Injection Mold; Devising Side Parting; Devising Oriented Framework; Pulling Framework
目 录
1绪论1
1.1题目背景1
1.2题目国内外相关研究情况1
1.3中国与国外先进技术的差距2
1.4塑料模具发展走势2
2塑件材料分析与方案论证4
2.1塑件材料的选择及其结构分析4
2.2ABS的注射成型工艺4
2.3塑件收缩率与模具尺寸的关系6
2.4方案论证7
3注射机的选择11
3.1确定零件的体积11
3.2选择注射机及注射机的主要参数11
3.2.1注射机的类型11
3.2.2注射机的主要技术参数12
3.2.3注塑机的校核13
4模具结构设计15
4.1浇注系统15
4.1.1浇注系统的作用15
4.1.2浇注系统布置15
4.2浇注系统设计15
4.2.1浇口套的设计:15
4.2.2冷料井设计17
4.2.3分流道的设计18
4.3浇口设计18
4.3.1浇口的类型19
4.3.2浇口的位置19
5成型零件设计20
5.1分型面的设计20
5.2成型零件应具备的性能21
5.3成型零件的结构设计21
5.3.1凹模(型腔)结构设计21
5.3.2型芯的结构设计21
5.4成型零件工作尺寸计算22
5.4.1影响塑件尺寸和精度的因素22
5.4.2成型零件工作尺寸的计算23
5.4.3成形型腔壁厚的计算25
6导向机构的设计27
6.1导向机构的作用27
6.2导柱导向机构27
6.2.1导向机构的总体设计27
6.2.2导柱的设计28
6.2.3导套的设计28
7脱模机构的设计30
7.1脱模机构的结构组成30
7.1.1脱模机构的设计原则30
7.1.2脱模机构的结构30
7.1.3脱模机构的分类30
7.2脱模力的计算31
7.3简单脱模机构31
7.3.1顶杆脱模机构的设计要点31
7.3.2顶杆的形状32
7.3.3顶杆强度的计算32
7.4复位装置33
8侧向分型与抽芯机构的设计34
8.1侧向分型与抽芯机构的分类34
8.2斜滑块侧向分型与抽芯机构34
8.2.1斜滑块侧向分型与抽芯机构设计要点34
8.3斜导柱的计算35
8.3.1抽拔力的计算35
8.3.2抽芯距的计算35
8.4斜滑块的设计36
8.5开模结构设计37
9排气系统的设计38
10温度调节系统的设计39
10.1温度调节系统的作用39
10.1.1温度调节系统的要求39
10.1.2温度调节系统对塑件质量的影响39
10.2冷却系统的机构40
10.2.1模具冷却系统的设计原则40
10.2.2模具冷却系统的结构41
11塑料模具用钢42
11.1注塑模材料应具备的要求42
11.2模具材料选用的一般原则42
11.3本模具所选钢材及热处理42
12模具工作过程44
13模具的可行性分析44
13.1本模具的特点45
13.2市场效益及经济效益分析45
14总结46
参考文献47
致谢48
毕业设计(论文)知识产权声明49
毕业设计(论文)独创性声明50
附录51
1 绪论
1.1题目背景
塑料注射模具是成型塑料制件的一种重要工艺装备,在塑料制品的生产中起着关键的作用。塑料模具工业从起步到现在,历经半个世纪,有了很大发展,模具水平有了较大提高。在成型工艺方面,多材质塑料成型模、高效多色注射模、镶件互换结构和抽芯脱模机构的创新设计方面也取得较大进展。气体辅助注射成型技术的使用更趋成熟,如青岛海信模具有限公司、天津通信广播公司模具厂家在29—34英寸电视机外壳以及一些厚壁零件的模具上运用气辅技术,一些厂家还使用了C-MOLD气辅软件,取得较好的效果。如上海新普雷斯等公司就能为用户提供气辅成型设备及技术。在制造技术方面,CAD/CAM/CAE技术的应用水平上了一个新台阶,以生产家用电器的企业为代表,陆续引进了相当数量的CAD/CAM系统。如美国EDS的UGⅡ、美国Parametric Technology公司的Pro/Engineer、美国CV公司的CADS5、美国Delta cam公司的CADS5、美国Delta cam公司的Doct5、日本HZS公司的 CRADE、以色列公司的Cimatron、美国AC-Tech等[1]。
整体来看,中国塑料模具无论是在数量上,还是质量、技术和能力等方面都有了很大的进步,但与国民经济发展的需求、世界先进水平相比,差距任然很大。一些大型、精密、复杂、长寿命的中高档塑料模具每年仍需大量进口。在总量供不应求的同时,一些低挡塑料模具却供过于求,市场竞争激烈,还有一些技术含量不太高的中高档塑料模具也有供过于求的趋势。
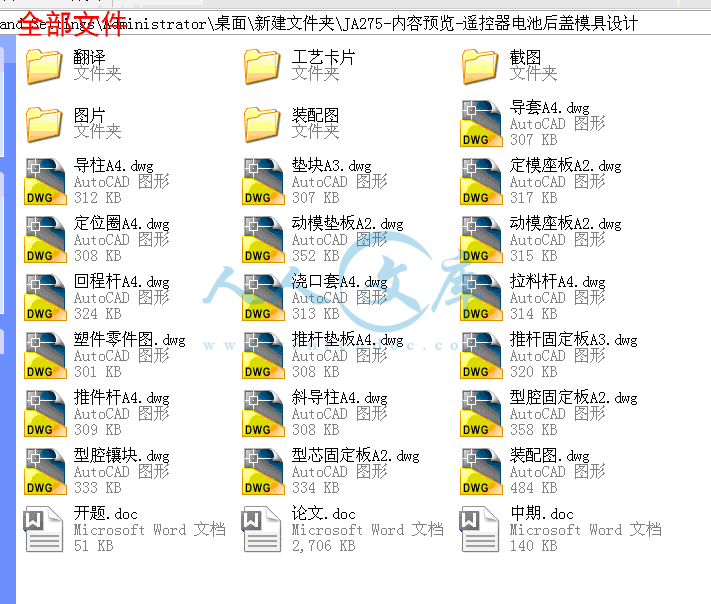
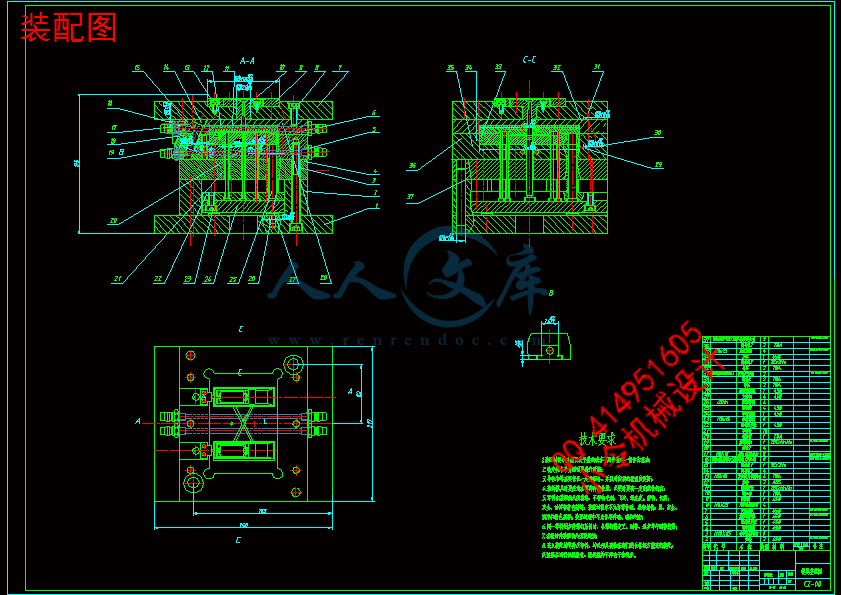
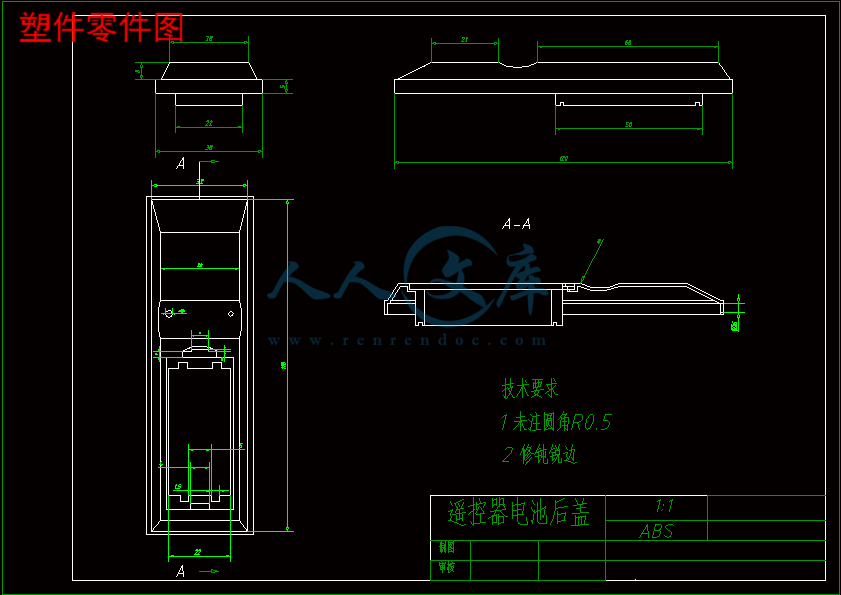
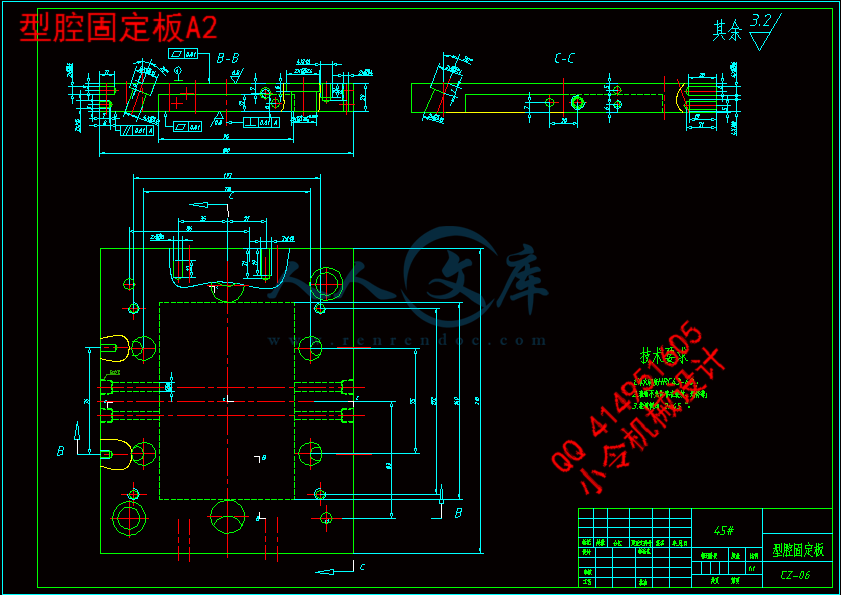
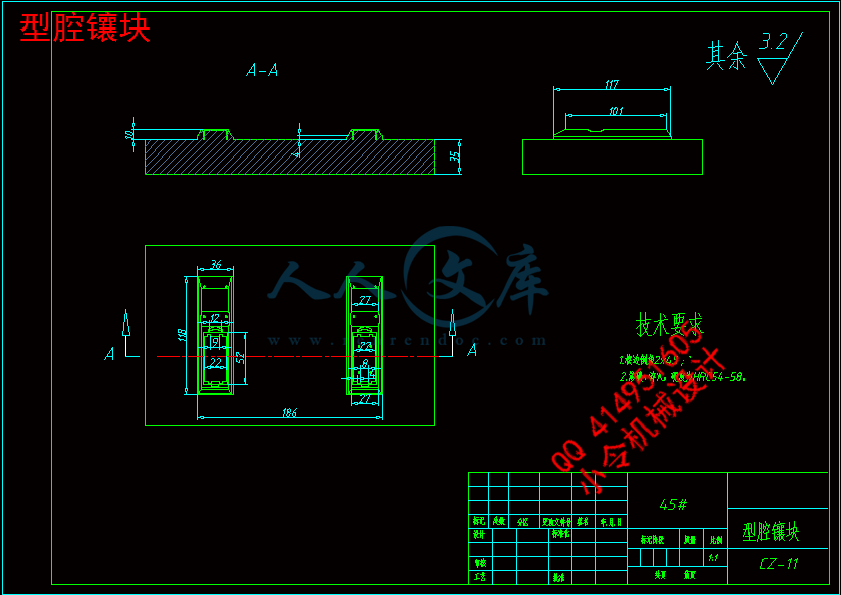
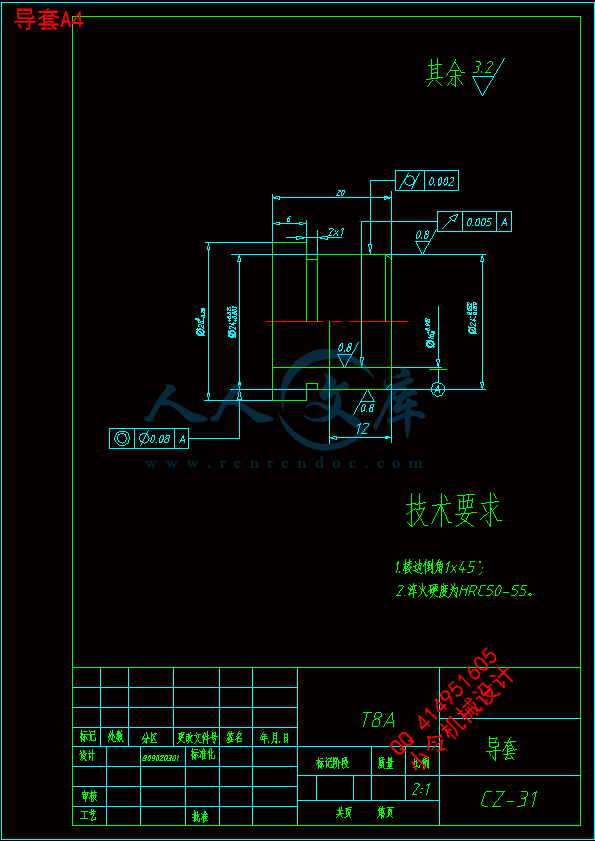