摘 要
随着人们的生活水平不断提高,对生活质量的要求也越来越高,各种电器不断进入人们的生活当中,以满足人们对不断提高的生活需求。
风扇轴套是日常生活中常见到的一种机械零件,通过拉伸、冲裁等工序将零件加工出来。级进模是一种很常用而且工作效率也很高的冲压模,冲压模具是现在加工盘盖类、轴套类零件最常用的方法,此种加工方法广泛应用于机械零件、仪表仪器、日常生活、军工产品、车船、交通工具等,冲压模加工具有以下优点:成品零件力学性能好、材料利用率高、能够加工其它加工方法所难以加工复杂零件、容易实现自动化,而且加工效率高,适合于大批量生产且成本低;另外原材料一般不需要加热等处理,也节约了加工成本,但是要对其进行排样。它所具有的优点是其它加工方法所不具有的。级进模是冲压模的一种,其加工效率比复合膜低但是比一般的单工序冲压模高,结构相对复杂:比复合膜的结构简单,但是比单工序模的结构复杂。级进模的结构一般由导料定位装置、多付拉伸模、冲裁模等主要部件组成。在外加压力机的情况下就可以对板料进行冲裁、冲压,拉伸等加工工序的操作。
关键词:机械零件;复杂零件;级进模;板料;压力机
Abstract
As people life level increases the demand for the quality of life, more and more is also high, various electric constantly into people's life, to meet people to improve life demand.
Fan collar is see daily life in a mechanical parts, through blanking process such as tensile, will parts processing out. Progressive die is a very common and high efficiency also punch mould and stamping mould is now processing plate cover class and the sleeves kind parts is the most commonly used method, the processing method is widely used in mechanical parts, instrument, daily life, military products, vehicle traffic tools, stamping mould processing has the following advantages: finished parts mechanics performance is good, material utilization rate, processing method that can process other it is difficult for processing complex parts, easy to realize automation and the processing efficiency high, suitable for mass production and cost is low; Additional materials generally do not need to heating processing, also save the processing cost, but in its arrangement. The advantage is that it has other processing methods with. Progressive metal stamping progressive die is a kind of, its processing efficiency than composite film than the average low but progressive metal stamping single process structures are relatively high, than composite membrane complex: simple structure, but better than the single procedure mode complex structure. The structure of the progressive die by conducting knew a device general tensile modulus, and pay extra punch die and other major parts. The situation in plus press of sheet metal for cutting, stamping, processes such as drawing of the operation.
Keywords: mechanical parts; Complex parts; Progressive die; Sheet; press
目 录
引 言5
1 风扇轴套零件的设计7
1.1 分析零件的使用要求7
1.2 零件的设计图7
1.2.1 分析其结构及工艺的特点8
2 选用合理的排样方式9
2.1 计算坯料的直径9
2.2 确定加工方案9
2.3 选择板料10
3 确定拉伸系数及凹凸模的相关尺寸11
3.1 计算拉伸系数11
3.1.1 判断能否一次将制件拉伸成形:11
3.1.2 确定各次拉伸的拉伸系数,及其圆筒直径12
3.2 确定凹凸模的圆角半径14
3.3 核算坯料直径及计算各次拉伸高度14
3.3.1 重新计算坯料直径并计算拉伸高度14
3.3.2 计算首次拉伸高度14
3.3.3 计算后续拉伸的高度14
3.4 确定凸凹模尺寸15
3.4.1 确定各伸模的具体尺寸15
3.4.2 算冲底孔、落料模具工作部分的具体尺寸17
4 计算冲压力及选用冲压设备18
4.1计算压边力18
4.2 计算拉伸力19
4.2.1 计算各次拉伸的拉伸力19
4.2.2 计算拉伸的拉伸功19
4.3 计算所需的冲裁力20
4.3.1 计算侧刃冲裁的冲裁力20
4.3.2 冲工艺槽孔20
4.3.3 冲底孔、落料20
4.4 计算卸料力、推件力20
4.5 初步选用压力机22
5 计算压力中心23
5.1 冲压件的压力中心23
5.2 模具的压力中心23
6 模具的总体结构设计24
6.1 确定模具的定位方式和送料方式24
6.2 卸料与出件方式25
6.2.1 确定卸料方式25
6.2.2 确定顶件方式25
7 确定模具的主要部件26
7.1 垫板的设计26
7.2 设计凹凸模26
7.2.1 校核凹凸模强度及凹模厚度27
7.2.2 确定凹模尺寸28
7.2.3 橡胶的厚度28
7.2.4 墩平装置29
7.3 选定并校核螺钉的强度30
7.3.1 紧固螺钉30
7.3.2 选择卸料螺钉30
7.4 根据模具尺寸选用模架31
7.4.1 选用模架形式31
7.4.2 选用并确定模架31
7.5 选用模柄32
8 确定压力机32
9. 模具零件的材料及其加工工艺34
9.1 选用模具材料34
9.2 模具主要部件的加工工艺35
9.2.1 模具凹、凸模的加工工艺35
9.2.2 凸模固定板的加工工艺36
9.2.3 模架的加工36
9.3 模具的装配37
9.4 模具的总装配37
9.5 模具的经济性分析39
10 结论40
谢 辞41
参考文献:42
引 言
冲压模具的种类很多,按照工序分有:单工序模、级进模、复合膜;按照冲裁件的精度分有:普通冲裁模、精密冲裁模;按照其尺寸分类有:小型模具、中型模具、大型模具;按照导向形式分有:无导向模具、有导向模具。还有根据模架的不同形式的分类等,或者是以上模具的派生性,根据不同需要而设计的各种形式。
冲压工艺是使用压力机通过冲压模具使材料分离或者是产生塑性变形的、以获得一定形状和尺寸的制品的一种少、无切削加工工艺。因为一般是在常温或者较低的温度下对材料进行加工的,因而也称为冷冲压工艺。也是加工厚度较薄的板状金属材料最常用的加工方法,因此也称为板料成型。主要是应用在金属方面,在非金属领域的使用相对较少。在生产刚开始的时候,虽然设备、模具、厂房等投入成本的很大,但是与其它加工方法(比如锻造、铸造、焊接、铆接、机械切削加工等)相比,有很多优点:制件性能稳定,强度好,材料利用率高,加工效率高等,特别是在大批量生产中更能体现出冲压加工的优越性。冲压工艺主要包括冲裁、拉伸、弯曲、涨形、翻边、扩口、缩口等,本次我研究的课题中的级进模就属于冲压模的一种。
自从计算机在模具行业中的应用以来,人们终止了以前单靠经验和机械绘图来完成模具的设计的历史。计算机辅助设计(CAD)的出现,很大程度地降低了模具设计的成本,也大大地缩短了设计周期、提高了模具设计的质量 。促进了模具行业的发展。以及随后发展起来的计算机辅助制造(CAM)、计算机辅助分析工程(CAE),Pro/E、UG等3D软件的应用,特别是现在CAD/CAM/CAE集成软件的应用,在模具设计中发挥着越来越重要的作用。
我国的模具行业在最近的几年才迅速发展起来的,相对其它国家而言,起步很晚,虽然发展很快,目前我国在模具制造中已经取得了很大的成就,甚至在一些方面也达到了世界顶级水平,比如我国精冲模方面的多工位与多功能冲压模具已经达到世界先进水平,不但已经取代进口,还有部分出口到发达国家。



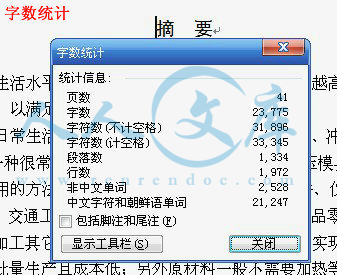