摘要
模具发展水平是体现当代工业国家发展水平的一个非常重要衡量标准,作为机械专业的学生,了解和认识模具对于国家的模具发展水平的提高是一个非常重要的发展基础,也是全面提高所学专业知识的途径之一。本文介绍和分析了冷冲模具的特点、结构和作用及它的发展趋势,主要内容为冲裁、弯曲等基本冲压工艺及其模具设计,既根据所给内容及工件要求对模具结构进行设计、零件排样,最佳方案选择,模具各主要部分力的计算,冲压设备的选择,弹性元件的计算及模架的选择,对主要工作机构进行合理的理论数值计算,及确定主要零件凸凹模刃口尺寸及公差,最终完成模具设计。通过本次设计,对于专业知识的实际综合运用能力,分析能力,实际问题的解决能力是一个重要的提高过程。
关键词:模具结构,工艺力,弹性元件
ABSTRACT
Mold levels of development embodies contemporary industrial level of development of the country, a very important yardstick, as a mechanical professional students understanding and knowledge of our country's Die Mold raising its level of development is a very important foundation for the development, comprehensively improve the professional knowledge acquired one of the ways. This paper describes and analyzes the Die with the characteristics, structure and role and its development trend, mainly as blanking, Bending basic stamping and die design process, according to both the contents and requirements of the work piece to die structure for the design, Parts layout, the best options, die of the main part of the calculation, stamping equipment selection, elastic element of calculation and die-choice, the main organizations of reasonable theoretical numerical calculation, and identify key components of punch and die cutting edge dimensions and tolerances, and ultimately complete mold design. During this design expertise for the integrated use of the actual capabilities, analytical ability, the solution of practical problems is the ability to raise an important process.
Keywords: Die structure, process, the elastic element
目 录
第1章 绪论1
第2章 冲压加工概述2
2.1 冷冲压加工及冲压分类2
2.2 冲压技术的现状及发展方向3
第3章 冷冲压模具设计过程4
3.1冲压零件的技术要求4
3.2 冲压工艺设计4
3.3 主要工艺参数计算7
3.4 主要工作部分尺寸计算9
3.5 冲裁模主要零件设计12
3.6 卸料、出件、弹性元件装置的设计13
3.7 模具总体结构设计15
3.8 模具装配要点18
3.9 模具动作过程20
结 论22
参考文献23
致 谢24
附录1英文资料及中文翻译25
1英文资料25
2译文如下31
附录236
第1章 绪论
冲压工艺与冲压设备正在不断地发展,特别是精密冲压,高速冲压,多工位自动冲压以及液压成型,超塑性冲压等各种冲压工艺的迅速发展,把冲压的技术水平提高到了一个新高度。新型模具材料的采用,模具的推广,模具结构的改善及其精度的提高,显著地延长了模具的寿命和扩大冲压加工工艺范围。
由于冲压工艺具有生产效率高、质量稳定、成本低以及可以加工复杂形状工件等一系列优点。在机械、汽车、国防、家用电器、以及日常生活用品等行业应用非常广泛,占有十分重要的地位。随着工业产品的不断发展和生产技术水平的不断提高,冲压模具作为各部分的重要的基础工艺装备将起到越来越大的作用。
冷冲压具有生产效率高,加工成本低,材料利用率高,产品的尺寸精度稳定,操作简单,易于实现机械化和自动化等。因而在批量生产中得到了广泛的应用,在现代化工业生产中占有十分重要的地位,是国防工业和民用工业生产中必不可少的加工方法,在电子产品中,冲压件约占80%-85%,在汽车、农业机械产品中,冲压件约占75%-80%,在轻工业产品中,冲压件占约95%以上,此外,在航空及航天工业生产中,冲压件也占有很大比例。
随着工业产品质量的不断提高,冲压零件日趋复杂化及规模化,冲压模具正向着高效、精密、长寿命、大型化方向发展,冲模制造难度日益增大,制造的种类也日益增多。模具的制造正由过去的劳动密集、依靠人工的手工技巧及采用传统机械加工设备的行业转变为技术密集型行业,从过去单一的机械加工时代转变成机械加工、电加工以及其他特种加工相结合的时代。特别是近几年来在国外已经发展起来、国内亦开始使用的冲压柔性制造单元(FMC)和冲压柔性制造系统(FMS)代表了冲压生产新的发展趋势。模具制造技术现代化是模具工业发展的基础。计算机技术、信息技术、自动化技术等先进技术正在不断向传统制造技术渗透、交叉、融合,形成先进制造技术。模具制造技术,已经发展成为技术密集型的综合加工技术。
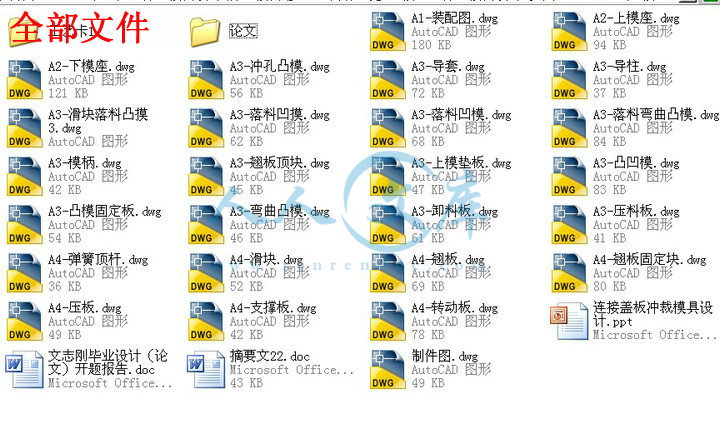


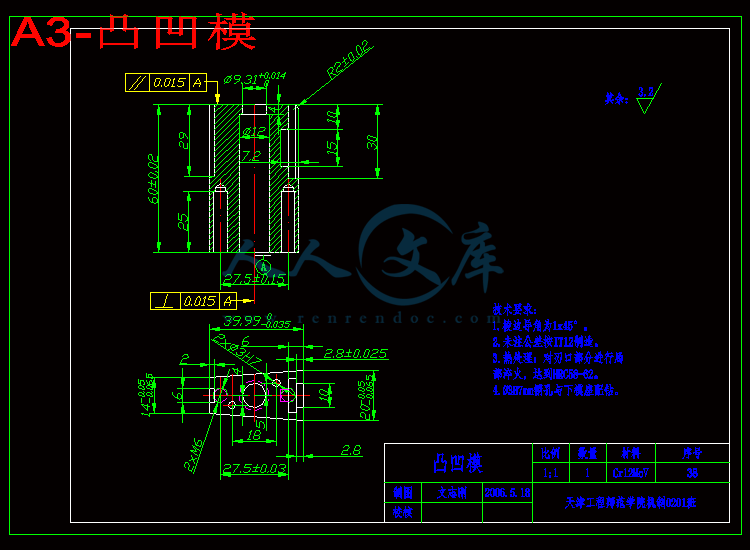
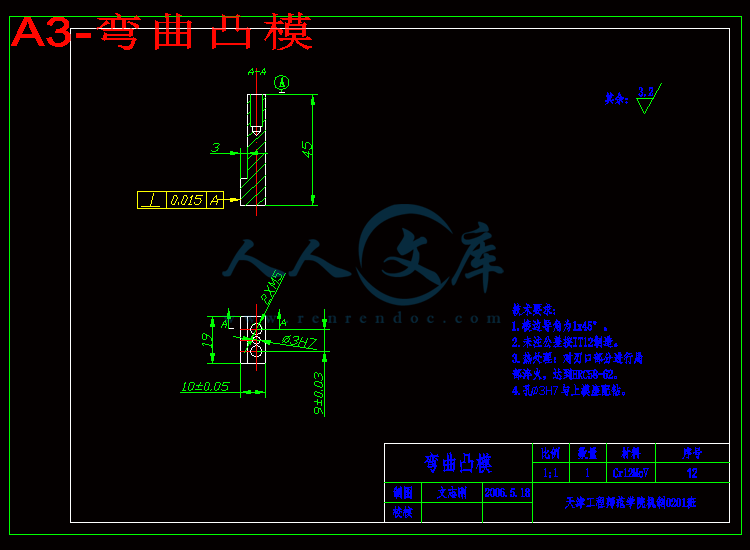
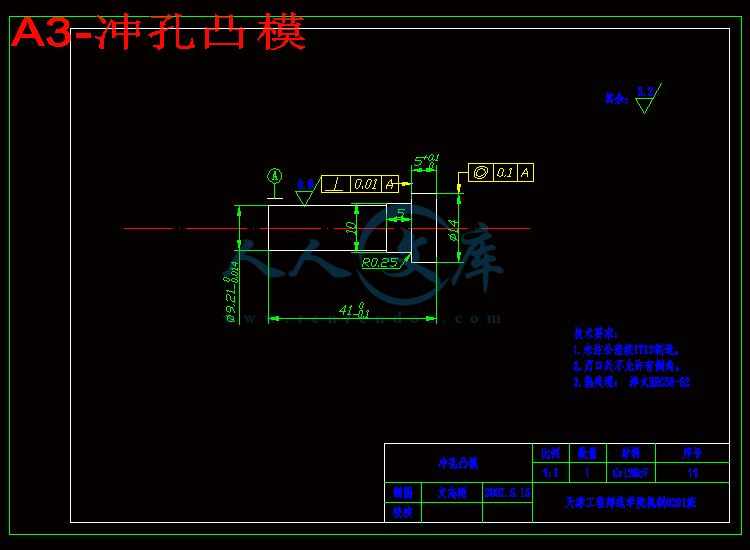
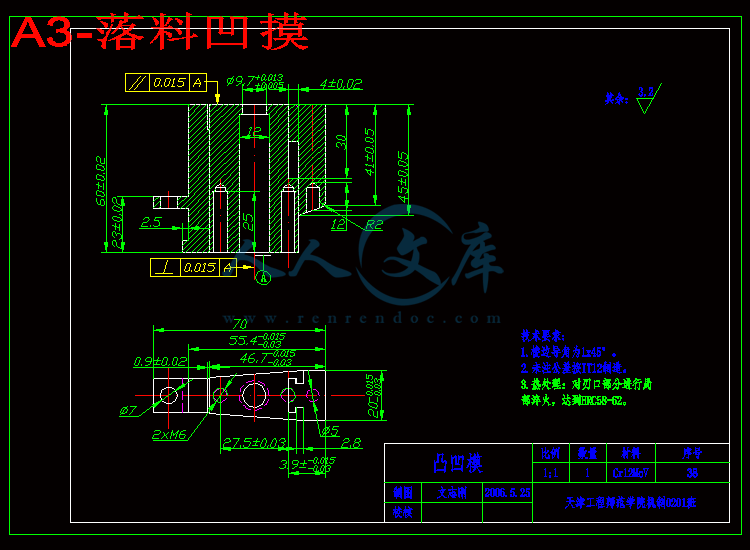