摘要
注塑成型工艺已经在我国的农业、工业、制造业、国防及日常生活等方面广泛的运用。为了探究注塑成型工艺的生产过程及其模具的设计制造过程,本次毕业设计参考相关书籍,结合生活实际,对整套注塑模具的生产设计过程进行详细探究。
本文将对塑料板凳的注塑模具设计,详细描述了整套模具的设计过程。主要内容包括塑件的基本介绍、塑件的结构及成型工艺分析、材料的选择及成型工艺、注射机的选择及校核、模具的工作及结构原理、浇注系统的设计、成型零件的设计、侧向分型抽芯机构的设计、合模导向机构的设计、温度调节系统的设计、排气系统的设计、推出机构的设计等。在正确的分析材料的特点和塑件的工艺特点后,运用三维软件对塑件和模具的设计,制造及质量进行分析;运用CAXA软件绘制完整的模具装配图和其主要零件图。此次设计综合运用多中专业基础知识、如模具设计与制造基本理论、机械设计、材料成型基础、塑性成型工艺、计算机基础技术、模具CAD/CAM等。
通过对整个模具设计的过程,进一步加深对注塑成型工艺的了解,同时也巩固了对成型工艺的类型、结构、工作原理等的理论知识,以及在实践中总结并掌握模具设计的关键要点及其设计方法。
关键词: 成型工艺;设计;制造;塑料
Abstract
Injection molding process has been widely used in China's agricultural、 industrial、 manufacturing、defense and other aspects of daily life. In order to explore the injection molding process and mold production process design and manufacturing process, this graduation design reference books, combined with real life, the production of injection molds for the entire design process detailed inquiry.
This article will bench plastic injection mold design, detailed description of the entire mold design process. The main contents include a basic introduction to plastic parts, design selection and verification, working principle and structure of the mold, pouring system structure and plastic parts molding process analysis, choice of materials and molding process, injection machine, forming part of the design, side parting pulling mechanism design, design-oriented organization designed to mold temperature control system, the design of the exhaust system, the introduction of design institutions. After the characteristics and process characteristics of plastic parts correct analysis of the material, the use of three-dimensional software for plastic parts and mold design, manufacturing and quality analysis; using CAXA software to draw a complete mold assembly drawing and its major parts diagram. The design of the integrated use of multi-professional knowledge, such as mold design and manufacture of basic theory, mechanical design, material forming the basis of the plastic molding process, basic computer technology, tooling CAD / CAM and so on.
Key points through the entire mold design process, and further deepen their understanding of the injection molding process, but also to consolidate the process of forming the type, structure and operating principles of the theory of knowledge, as well as summary and master mold design and in practice.
Keywords: Molding process; design; making; plastic.
目 录
引言1
1 塑件的基本介绍2
1.1 塑件3D建模2
1.2 塑件名称2
1.3 塑件材料2
1.4 塑件前景3
1.5 塑件总体要求3
2 塑件的结构及工艺性分析4
2.1 塑件结构分析4
2.2 塑件的工艺性分析4
2.3 开模方向4
2.4 脱模斜度5
2.5 收缩率5
2.6 表面粗糙度5
2.7 塑件壁厚6
2.8 圆角6
3 材料的选择与工艺参数7
3.1 材料的选择及其性能7
3.2 塑件的成型工艺8
4 注射机的选择及校核10
4.1 注射机的相关参数10
4.2 注射机的选择11
4.3 锁模力的校核11
4.4 开模行程的校核12
5 模具的工作及结构原理说明13
5.1 模具的工作原理13
5.2 模具的结构说明13
6 浇注系统的设计15
6.1 浇注系统的设计要求15
6.2 型腔的数目及分布15
6.3 双分型面的选择与设计16
6.4 主流道的设计17
6.5 分流道的设计18
6.6 冷料穴的设计19
6.7 浇口的设计19
7 成型零部件的设计21
7.1 凹模的设计21
7.2 凸模的结构设计22
7.3 成型零部件尺寸的设计22
8 侧向分型抽芯机构的设计25
8.1 斜导柱的倾角25
8.2 斜导柱直径设计25
8.3 斜导柱长度的设计26
8.4 滑块的设计26
8.5 导滑槽的设计27
8.6 楔紧块的设计27
8.7 滑块定位的设计27
9 合模导向机构的设计28
9.1 导柱、导套的设计28
10 温度调节系统的设计30
10.1 温度调节系统的设计要求30
10.2 冷却回路的设计30
11 排气系统的设计31
12 推出机构的设计32
12.1 顶出力的计算32
12.2 凝料推出机构的设计33
13 支撑零部件设计34
14 常见问题及其解决办法35
14.1 熔接痕产生的原因及解决办法35
14.2 充模不力产生的原因及解决办法35
14.3 弯曲变形产生的原因及解决办法35
结论37
谢辞38
参考文献39
引言
随着我国工业技术的飞跃性发展,模具在我国国民经济的各个领域中发挥越来越大的作用,享有着“工业之母”的美称。模具制造是指通过注塑、压铸和锻压等方式得到所需的各种产品或工件,一个设计合理的塑件往往能够代替几个传统金属构件。利用塑性材料独有的特性,一次注塑成型往往就可以得到非常复杂的形状,所带来的实际应用效果非传统工艺所能相比。模具的生产与制造融合了多项高精密技术为一体,既是高新技术产品,又是高新技术载体。采用模具成型工艺,运用高新技术控制对所需的塑件进行加工生产,不仅可以提高生产时效,保质保量。而且还能减少生产线对材料的过度依赖,压缩了生产成本,更好的获取经济效益。
注塑成型是塑性成各个领域型加工中最常见的加工方法,其中注塑模具已经被广泛的采用。它的成型效果、制造精度、生产周期以及生产效率的高低,直接影响到产品的质量、产量和成本。注塑成型现已被广泛的应用于机械、电子、航空、航天、军工、交通、汽车、建材、医疗器械、生物、能源和日用品等领域。在一些发达国家,模具的生产制造早已形成产业链,成为这些国家的基础经济工业之一。模具产业,在美国被成为“美国工业的基石”,在日本被称为“促进社会富裕的源泉、动力”。工业要发展,模具要先行。没有高水平的模具产业链就没有高水平的工业产品。现在,模具工业水平是衡量一个国家制造工业制造水平高低的重要标志。
综上所述,进行模具设计是一项综合性的研究,其目的和意义在于以下几点:
(1)查阅中内外文献检索和阅读的能力;
(2)运用专业理论,解决实际问题的能力;
(3)设计,绘图的能力,包含计算机的使用能力;
(4)对模具设计制造的初步了解及掌握;
(5)形象思维和逻辑思维相结合的表达能力;
(6)撰写毕业论文的能力;
(7)养成认真、严肃、严谨的作风。


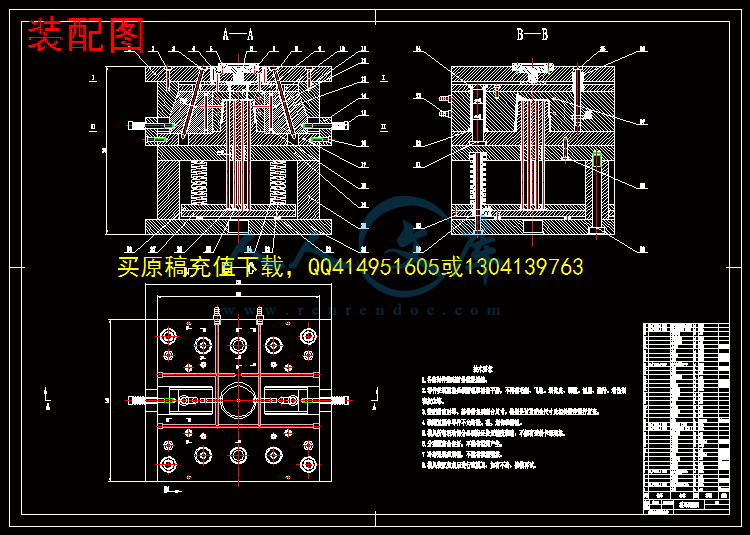
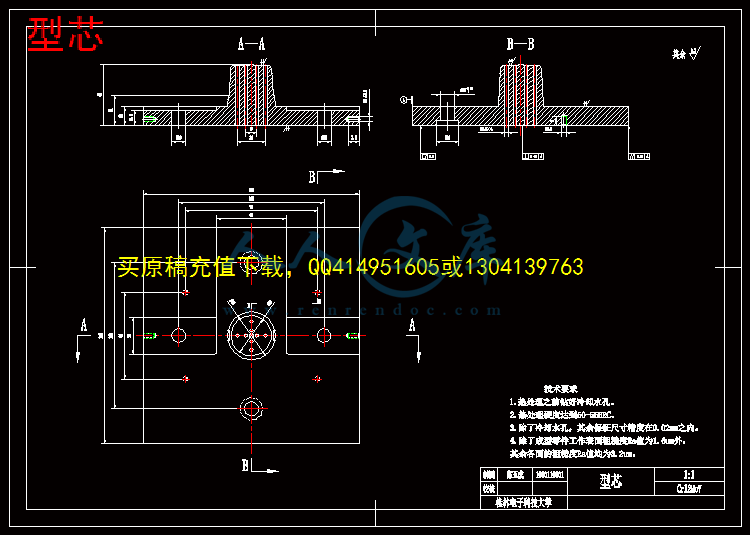
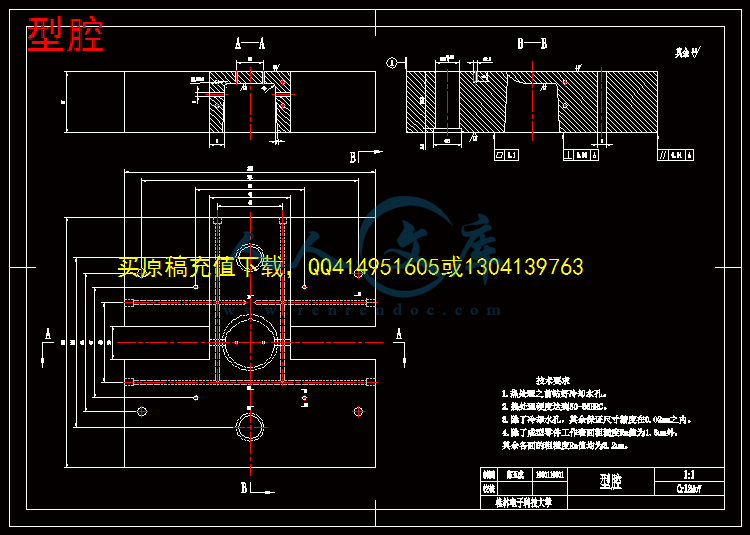

