CA6140 车床自动刀架【Word+CAD图纸】【优秀】
收藏
资源目录
压缩包内文档预览:
编号:444553
类型:共享资源
大小:1.55MB
格式:ZIP
上传时间:2015-06-28
上传人:小***
认证信息
个人认证
林**(实名认证)
福建
IP属地:福建
45
积分
- 关 键 词:
-
x0048
ca6140
车床
自动
刀架
word
cad
图纸
优秀
优良
- 资源描述:
-
您若下载本次文件,将获得(CAD图纸+word文档)源文件哦!
以下为本次文件的目录及部分图纸截图
【需要其他机械类资料可以联系QQ97666224】
第一章 绪论
1.1课题背景
1946年诞生了世界上第一台电子计算机,这表明人类创造了可增强和部分代替脑力劳动的工具。它与人类在农业、工业社会中创造的那些只是增强体力劳动的工具相比,起了质的飞跃,为人类进入信息社会奠定了基础。6年后,即在1952年,计算机技术应用到了机床上,在美国诞生了第一台数控机床。
我国目前机床总量380余万台,而其中数控机床总数只有11.34万台,即我国机床数控化率不到3%。近10年来,我国数控机床年产量约为0.6~0.8万台,年产值约为18亿元。机床的年产量数控化率为6%。我国机床役龄10年以上的占60%以上;10年以下的机床中,自动/半自动机床不到20%,FMC/FMS等自动化生产线更屈指可数(美国和日本自动和半自动机床占60%以上)。可见我们的大多数制造行业和企业的生产、加工装备绝大数是传统的机床,而且半数以上是役龄在10年以上的旧机床。用这种装备加工出来的产品普遍存在质量差、品种少、档次低、成本高、供货期长,从而在国际、国内市场上缺乏竞争力,直接影响一个企业的产品、市场、效益,影响企业的生存和发展。所以必须大力提高机床的数控化率。
在美国、日本和德国等发达国家,它们的机床改造作为新的经济增长行业,生意盎然,正处在黄金时代。由于机床以及技术的不断进步,机床改造是个"永恒"的课题。我国的机床改造业,也从老的行业进入到以数控技术为主的新的行业。在美国、日本、德国,用数控技术改造机床和生产线具有广阔的市场,已形成了机床和生产线数控改造的新的行业。在美国,机床改造业称为机床再生(Remanufacturing)业。从事再生业的著名公司有:Bertsche工程公司、ayton机床公司、Devlieg-Bullavd(得宝)服务集团、US设备公司等。美国得宝公司已在中国开办公司。在日本,机床改造业称为机床改装(Retrofitting)业。从事改装业的著名公司有:大隈工程集团、岗三机械公司、千代田工机公司、野崎工程公司、滨田工程公司、山本工程公司等。
1.2机床改造的内容及意义
1.2.1研究意义
企业要在当前市场需求多变,竞争激烈的环境中生存和发展就需要迅速地更新和开发出新产品,以最低价格、最好的质量、最短的时间去满足市场需求的不断变化。而普通机床已不适应多品种、小批量生产要求,数控机床则综合了数控技术、微电子技术、自动检测技术等先进技术,最适宜加工小批量、高精度、形状复杂、生产周期要求短的零件。当变更加工对象时只需要换零件加工程序,无需对机床作任何调整,因此能很好地满足产品频繁变化的加工要求。
普通车床经过多次大修后,其零部件相互连接尺寸变化较大,主要传动零件几经更换和调整,故障率仍然较高,采用传统的修理方案很难达到大修验收标准,而且费用较高。因此合理选择数控系统是改造得以成功的主要环节。
数控机床在机械加工行业中的应用越来越广泛。数控机床的发展,一方面是全功能、高性能;另一方面是简单实用的经济型数控机床,具有自动加工的基本功能,操作维修方便。经济型数控系统通常用的是开环步进控制系统,功率步进电机为驱动元件,无检测反馈机构,系统的定位精度一般可达±0.01至0.02mm,已能满足CW6140车床改造后加工零件的精度要求。
1.2.2主要研究内容及技术路线
(1)纵向和横向滚珠丝杠的选型及校核。
(2)纵向和横向步进电机的选择。
(3)主轴交流伺服电机的选择与校核。
(4)其他元件的选择。



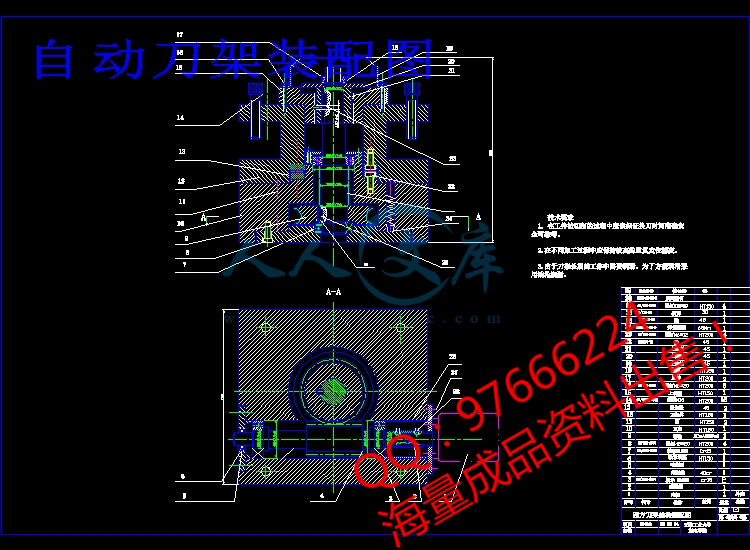

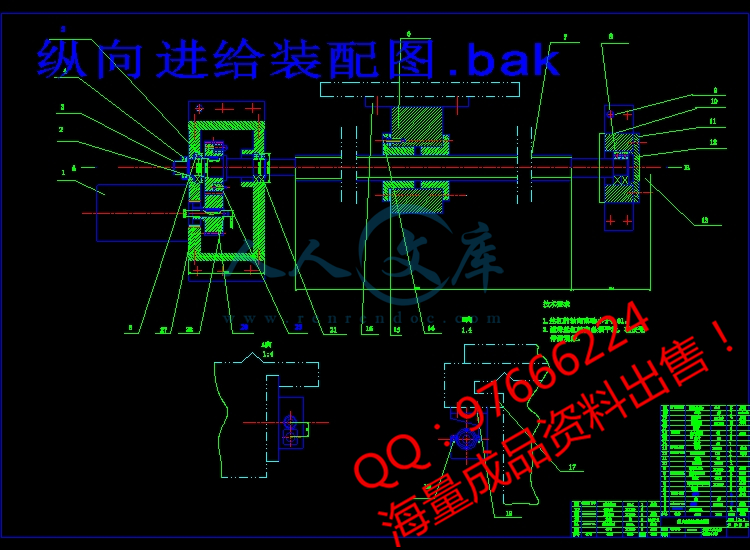
- 内容简介:
-
天津工业大学2008届本科生毕业设计(论文)第一章 绪论1.1课题背景 1946年诞生了世界上第一台电子计算机,这表明人类创造了可增强和部分代替脑力劳动的工具。它与人类在农业、工业社会中创造的那些只是增强体力劳动的工具相比,起了质的飞跃,为人类进入信息社会奠定了基础。6年后,即在1952年,计算机技术应用到了机床上,在美国诞生了第一台数控机床。 我国目前机床总量380余万台,而其中数控机床总数只有11.34万台,即我国机床数控化率不到3。近10年来,我国数控机床年产量约为0.60.8万台,年产值约为18亿元。机床的年产量数控化率为6。我国机床役龄10年以上的占60以上;10年以下的机床中,自动/半自动机床不到20,FMC/FMS等自动化生产线更屈指可数(美国和日本自动和半自动机床占60以上)。可见我们的大多数制造行业和企业的生产、加工装备绝大数是传统的机床,而且半数以上是役龄在10年以上的旧机床。用这种装备加工出来的产品普遍存在质量差、品种少、档次低、成本高、供货期长,从而在国际、国内市场上缺乏竞争力,直接影响一个企业的产品、市场、效益,影响企业的生存和发展。所以必须大力提高机床的数控化率。 在美国、日本和德国等发达国家,它们的机床改造作为新的经济增长行业,生意盎然,正处在黄金时代。由于机床以及技术的不断进步,机床改造是个永恒的课题。我国的机床改造业,也从老的行业进入到以数控技术为主的新的行业。在美国、日本、德国,用数控技术改造机床和生产线具有广阔的市场,已形成了机床和生产线数控改造的新的行业。在美国,机床改造业称为机床再生(Remanufacturing)业。从事再生业的著名公司有:Bertsche工程公司、ayton机床公司、Devlieg-Bullavd(得宝)服务集团、US设备公司等。美国得宝公司已在中国开办公司。在日本,机床改造业称为机床改装(Retrofitting)业。从事改装业的著名公司有:大隈工程集团、岗三机械公司、千代田工机公司、野崎工程公司、滨田工程公司、山本工程公司等。1.2机床改造的内容及意义1.2.1研究意义 企业要在当前市场需求多变,竞争激烈的环境中生存和发展就需要迅速地更新和开发出新产品,以最低价格、最好的质量、最短的时间去满足市场需求的不断变化。而普通机床已不适应多品种、小批量生产要求,数控机床则综合了数控技术、微电子技术、自动检测技术等先进技术,最适宜加工小批量、高精度、形状复杂、生产周期要求短的零件。当变更加工对象时只需要换零件加工程序,无需对机床作任何调整,因此能很好地满足产品频繁变化的加工要求。普通车床经过多次大修后,其零部件相互连接尺寸变化较大,主要传动零件几经更换和调整,故障率仍然较高,采用传统的修理方案很难达到大修验收标准,而且费用较高。因此合理选择数控系统是改造得以成功的主要环节。 数控机床在机械加工行业中的应用越来越广泛。数控机床的发展,一方面是全功能、高性能;另一方面是简单实用的经济型数控机床,具有自动加工的基本功能,操作维修方便。经济型数控系统通常用的是开环步进控制系统,功率步进电机为驱动元件,无检测反馈机构,系统的定位精度一般可达0.01至0.02mm,已能满足CW6140车床改造后加工零件的精度要求。1.2.2主要研究内容及技术路线(1)纵向和横向滚珠丝杠的选型及校核。(2)纵向和横向步进电机的选择。(3)主轴交流伺服电机的选择与校核。(4)其他元件的选择。1.3 机床的经济型数控化改造主要解决的问题(1) 恢复原功能,对机床、生产线存在的故障部分进行诊断并恢复。(2) NC化,在普通机床上加数显装置,或加数控系统,改造成NC机床、CNC机床。(3) 翻新,为提高精度、效率和自动化程度,对机械、电气部分进行翻新,对机械部分重 新装配加工,恢复原精度;对其不满足生产要求的CNC系统以最新CNC进行更新。(4) 技术更新或技术创新,为提高性能或档次,或为了使用新工艺、新技术,在原有基础上进行较大规模的技术更新或技术创新,较大幅度地提高水平和档次的更新改造。第二章 总体改造方案首先是数控系统的选择。本设计方案数控系统选用外购的成套产品。由于本人水平有限,做不出数控系统,只能选用成套的数控系统;再者,成套的数控系统功能要比自己搭建的功能丰富。这里选用广州数控的928TB数控系统。 进给传动的作用是接受数控系统的指令,驱动刀具作精确定位或按规定的轨迹作相对运动,加工出符合要求的零件,对进给传动的要求是高精度、高速度。改造中我们采用广州数控的928TB数控系统,其带有X、Z轴控制功能,其采用步进电机开环驱动系统实现X、Z轴运动控制,这样结构简单,安装调试和维修都非常方便。电机有数控系统直接控制,不需要另外的步进电机控制系统。加装主轴脉冲发生器,以实现切削螺纹功能。脉冲发生器与主轴用同步带连接。拆除原车床的纵向和横向丝杠、光杠、溜板箱及挂轮箱中的齿轮,用滚珠丝杠替换原有普通滑动丝杠,将选取的纵向滚珠丝杠副通过托架安装在原溜板箱与床鞍连接的部位上,纵横向滚珠丝杠两端尽可能利用原固定和支承方式。横向进给机构改造中,步进电机、齿轮箱体安装在中拖板的后侧。纵、横向进给机构都采用了一级齿轮减速,并用双片齿轮错齿法消除间隙,双片齿轮间没有加弹簧自动消除间隙,因为弹簧的弹力很难适应负载的变化情况。当负载较大时,弹簧弹力显得小,起不到自动消除间隙的作用;当负载较小时,弹簧弹力又显得大,则加速齿轮的磨损。为此采用人工定期调整螺钉紧固的办法来消除间隙。拆除原刀架和小拖板,换上数控可转位刀架。数控系统自带刀架控制器。数控机床的加工是由程序控制完成的,所以坐标系的确定与使用非常重要。根据 ISO841 标准,数控机床坐标系用右手笛卡儿坐标系作为标准确定。数控车床平行于主轴方向即纵向为Z轴,垂直于主轴方向即横向为X轴,刀具远离工件方向为正向。CA6140 车床的坐标原点定在卡盘基座与主轴中心的交点上,数控系统是通过检测参考点的具体位置来确定机床坐标系的,选用两个接近开关X轴方向和Z轴方向各安装在一个机床上,用于建立参考点,当移动刀架两个都有信号输出时,刀架的当前位置就为参考点R,测量XR和ZR,并将它写入机床数据库,即可在数控系统中建立坐标系。图2-1进给系统总体改造示意图58第三章 数控系统的选择 数控系统主要有三种类型,改造时,应根据具体情况进行选择。2.1步进电机拖动的开环系统 系统的伺服驱动装置主要是步进电机、功率步进电机、电液脉冲马达等。由数控系统送出的进给指令脉冲,经驱动电路控制和功率放大后,使步进电机转动,通过齿轮副与滚珠丝杠副驱动执行部件。只要控制指令脉冲的数量、频率以及通电顺序,便可控制执行部件运动的位移量、速度和运动方向。这种系统不需要将所测得的实际位置和速度反馈到输入端,故称该之为开环系统,该系统的位移精度主要决定于步进电机的角位移精度,齿轮丝杠等传动元件的节距精度,所以系统的位移精度较低。该系统结构简单,调试维修方便,工作可靠,成本低,易改装成功。2.2异步电动机或直流电机拖动,光栅测量反馈的闭环数控系统 该系统与开环系统的区别是:由光栅、感应同步器等位置检测装置测得的实际位置反馈信号,随时与给定值进行比较,将两者的差值放大和变换,驱动执行机构,以给定的速度向着消除偏差的方向运动,直到给定位置与反馈的实际位置的差值等于零为止。闭环进给系统在结构上比开环进给系统复杂,成本也高,对环境室温要求严。设计和调试都比开环系统难。但是可以获得比开环进给系统更高的精度,更快的速度,驱动功率更大的特性指标。可根据产品技术要求,决定是否采用这种系统。2.3交/直流伺服电机拖动,编码器反馈的半闭环数控系统 半闭环系统检测元件安装在中间传动件上,间接测量执行部件的位置。它只能补偿系统环路内部部分元件的误差,因此,它的精度比闭环系统的精度低,但是它的结构与调试都较闭环系统简单。在将角位移检测元件与速度检测元件和伺服电机做成一个整体时则无需考虑位置检测装置的安装问题。当前生产数控系统的公司厂家比较多,国外著名公司的如德国SIEMENS公司、日本FANUC公司;国内公司如广州数控、中国珠峰公司、北京航天机床数控系统集团公司、华中数控公司和沈阳高档数控国家工程研究中心等。选择数控系统时主要是根据数控改造后机床要达到的各种精度、驱动电机的功率和用户的要求,所以依据改造的具体要求选用合适的数控系统。本设计是改造成经济型机床,所以选用广州数控的GSK98TB数控系统,其为步进电机开环拖动,虽然精度不是很高,但优于普通车床精度,且改造简单。广州数控的928TB数控系统,其最小指令单位:0.01mm,丰富循环加工指令:单头、多头螺纹、单面进刀自动切深等自动循环,内外圆柱面、端面、锥面、球面、切槽等粗加工循环,具有螺纹加工能力,中/英制螺纹加工:公制0.0112.00mm螺矩、英制2.20200.00牙/英寸。性能适合经济型车床,操作界面简单易懂,且为国产,对支持我国数控系统国产化有一定意义。 针对机床切削螺纹功能,主轴控制系统含有主轴控制功能,可以不必加装光电编码器,但是电机与主轴传动比必须为1:1,因此选用主轴电机与主轴传动比为1:1,这样也可以简化改造。第四章 机械部分的改造 为了充分发挥数控系统的技术性能,保证改造后的车床在系统控制下重复定位精度,微机进给无爬行,使用寿命长、外型美观,机械部分作了如下改动。(1) 床身为了使改造后的机床有较高的开动率和精度保持性,除尽可能地减少电器和机械故障的同时,应充分考虑机床零件、部件的耐磨性,尤其是机床导轨的耐磨性。增加耐磨性的方法有1,增加导轨的表面强度如:淬火;2,降低摩擦系数等。当前国内外数控机床的床身等大件多采用普通铸铁。而导轨则采用淬硬的合金钢材料,其耐磨性比普通铸铁导轨高5至10倍。据此,在改造中利用旧床身,采用淬火制成导轨,贴塑用螺钉和粘剂固定在铸铁床身上。粘接前的导轨工作表面采用磨削加工,表面粗糙度Ra0.8mm,以提高粘接强度。(2) 主轴变速箱选用数控系统,主运动方式和传统机床一样都要求有十分宽广的变速范围(116)来保证加工时选择合理的切速,从而获得较高的生产率和表面质量,所以要根据具体情况对主轴边速箱进行改造。本设计方案拆除主轴机械变速系统,在主轴上增加了交流异步电动机变频调速系统,改用数控系统直接调速。原因会在下文介绍。(3) 拖板拖板是数控系统直接控制的对象,不论是点位控制还是连续控制,对被加工零件的最后坐标精度将受拖板运动精度、灵敏度和稳定性的影响。对于应用步进电机作拖动元件的开环系统尤其是这样。因为数控系统发出的指令仅使拖板运动而没有位置检测和信号反馈,故实际移动值和系统指令值如果有差别就会造成加工误差。因此,除了拖板及其配件精度要求较高外,还应采取以下措施来满足传动精度和灵敏度要求。在传动装置的布局上采用减速齿轮箱来提高传动扭矩和传动精度(分辨率为0.01mm)。传动比计算公式为: (3-1)式中:为步进电机的步距角(度);p为丝杠螺距,mm;为脉冲当量,即要求的分辨率,mm。在齿轮传动中,为提高正、反传动精度必须尽可能的消除配对齿轮之间的传动间隙,其方法有两种,柔性调整法和刚性调整法。柔性调整法是指调整之后的齿轮侧隙可以自动补偿的方法,在齿轮的齿厚和齿距有差异的情况下,仍可始终保持无侧隙啮合。但将影响其传动平稳性,而且这种调整法的结构比较复杂,传动刚度低。刚性调整法是指调整之后齿轮侧隙不能自动补偿的调整方法,它要求严格控制齿轮的齿厚及齿距误差,否则传动的灵活性将受到影响。但用这种方法调整的齿轮传动有较好的传动刚度,而且结构比较简单。在设备改造中应用的配对齿轮侧隙方法是刚性调整法。采用滚珠丝杠代替原滑动丝杠,提高传动灵敏性和降低功率、步进电机力矩损失。 (4) 自动换刀装置为了满足在一台机床上一次装夹完成多工序加工,可采用自动刀架。自动刀架不但可代替普通车床手动刀架,还可用作数控机床微机控制元件。刀架体积小,重复定位精度高,适用于强力车削并安全可靠。(5) 拖板箱采用数控系统控制。拆除原拖板箱,利用此位置安装新拖板箱,新拖板箱除固定在滚珠丝杠的螺母上。挂轮箱、走刀箱拆除,使改造后的机床外型美观、合理。改造后机床的启动、停机均由数控系统完成,故拆除原机床操纵杆,变向杠、立轴等杠杆零件。3.1 滚珠丝杠的选择3.1.1滚珠丝杠副的特点 滚珠丝杠副具有与滚动轴承相似的特征。与滑动丝杠副或液压缸传动相比,有以下主要特点:传动效率高:滚珠丝杠的传动效率可达85%98%,为滑动丝杠副的24倍,由于滚珠丝杠副的传动效率高,对机械小型化,减少启动后的颤动和滞后时间以及节约能源等方面,都具有重要意义。运动平稳:滚珠丝杠副在工作过程中摩擦阻力小,灵敏度高,而且摩擦系数几乎与运动速度无关,启动摩擦力矩与运动时的摩擦力矩的差别很小。所以滚珠丝杠副运动平稳,启动时无颤动,低速时无爬行。传动可逆性:与滑动丝杠副相比,滚动丝杠副突出的特点是具有运动的可逆性。正逆传动的效率几乎可高达98%。滚珠丝杠副具有运动的可逆性,但是没有象滑动丝杠副那样运动具有自锁性:因此,在某些机构中,特别是垂直升降机构中使用滚珠丝杠副时,必须设置防止逆转的装置。可以预紧:通过对螺母施加预紧力能消除滚珠丝杠副的间隙,提高轴向接触刚度,但摩擦力矩却增加不大。定位精度和重复定位精度高:由于滚珠丝杠副具有传动效率高,运动平稳,可以预紧等特点,所以滚珠丝杠副在工作过程中温升较小,无爬行。并可消除轴向间隙和对丝杠进行预紧拉伸以补偿热膨胀,能获得较高的定位精度和重复定位精度。同步性好:用几套相同的滚珠丝杠副同时驱动相同的部件和装置时,由于反应灵敏,无阻滞,无滑移,其启动的同时性,运行中的速度和位移等,都具有准确的一致性,这就是所谓同步性好。使用寿命长:滚珠丝杠和螺母的材料均为合金钢,螺纹滚道经过热处理,并淬硬至HRC58-62,经磨削达到所需的精度和表面粗糙度。实践证明,滚珠丝杠副的使用寿命比普通滑动丝杠副高56倍。使用可靠,润滑简单,维修方便:与液压传动相比,滚珠丝杠副在正常使用条件下故障率低,维修保养也极为方便;通常只需进行一般的润滑与防尘。在特殊使用场合,如核反应堆中的滚珠丝杠副,可在无润滑状态下正常工作。3.1.2. 纵向滚珠丝杠螺母副的型号选择与校核步骤(1)最大工作载荷计算 滚珠丝杠上的工作载荷Fm (N) 是指滚珠丝杠副的在驱动工作台时滚珠丝杠所承受的轴向力,也叫做进给牵引力。它包括滚珠丝杠的走刀抗力及与移动体重力和作用在导轨上的其他切削分力相关的摩擦力。由于原普通CA6140车床的纵向导轨是三角形导轨,则用公式3-2计算工作载荷的大小。 (3-2)1)车削抗力分析 车削外圆时的切削抗力有Fx、Fy、Fz,主切削力Fz与切削速度方向一致,垂直向下,是计算车床主轴电机切削功率的主要依据。且深抗力Fy与纵向进给方向垂直,影响加工精度或已加工表面质量。进给抗力Fx与进给方向平行且相反指向,设计或校核进给系统是要用它。 纵切外圆时,车床的主切削力Fz可以用下式计算: (3-3) =5360(N)由 Fz:Fx:Fy=1:0.25:0.4 (3-4)得 Fx=1340(N) Fy=2144(N)因为车刀装夹在拖板上的刀架内,车刀受到的车削抗力将传递到进给拖板和导轨上,车削作业时作用在进给拖板上的载荷Fl、Fv和Fc与车刀所受到的车削抗力有对应关系,因此,作用在进给拖板上的载荷可以按下式求出:拖板上的进给方向载荷 Fl=Fx=1340(N)拖板上的垂直方向载荷 Fv=Fz=5360(N)拖板上的横向载荷 Fc=Fy=2144(N)因此,最大工作载荷 =1.151340+0.04(5360+909.8) =1790.68(N)对于三角形导轨K=1.15,f=0.030.05,选f=0.04(因为是贴塑导轨),G是纵向、横向溜板箱和刀架的重量,选纵向、横向溜板箱的重量为75kg,刀架重量为15kg.(2)最大动载荷C的计算滚珠丝杠应根据额定动载荷Ca选用,可用式3-5计算:C=, (3-5) L为工作寿命,单位为10r,L=60nt/10;n为丝杠转速(r/min),n=;v为最大切削力条件下的进给速度(m/min),可取最高进给速度的1/21/3;L0为丝杠的基本导程,查资料得L。=12mm;fm为运转状态系数,因为此时是有冲击振动,所以取fm=1.5。V纵向=1.59mm/r 1400r/min=2226mm/minn纵向=v纵向1/2 /L。=22261/2 /12=92.75r/min L=60nt/10=6092.7515000 /10=83.5则 C= =1.51790.68=11740(N) 初选滚珠丝杆副的尺寸规格,相应的额定动载荷Ca不得小于最大动载荷C:因此有CaC=11740N.另外假如滚珠丝杠副有可能在静态或低速运转下工作并受载,那么还需考虑其另一种失效形式-滚珠接触面上的塑性变形。即要考虑滚珠丝杠的额定静载荷Coa是否充分地超过了滚珠丝杠的工作载荷Fm,一般使Coa/Fm=23.初选滚珠丝杠为:外循环,因为内循环较外循环丝杠贵,并且较难安装。考虑到简易经济改装,所以采用外循环。并考虑原车床丝杠尺寸为T40 X 12,选取滚珠丝杠直径为40mm,型号为CD40X6-2.5P2。主要参数为Dw=4.763mm,L。=8mm,dm=40mm,=219,圈数列数2.51 (3) 纵向滚珠丝杠的校核1)传动效率计算 滚珠丝杠螺母副的传动效率为 = tg/tg(+)= tg 219/tg(219+10)=92% (3-6)2)刚度验算 滚珠丝杠副的轴向变形将引起导程发生变化,从而影响其定位精度和运动平稳性,滚珠丝杠副的轴向变形包括丝杠的拉压变形,丝杠与螺母之间滚道的接触变形,丝杠的扭转变形引起的纵向变形以及螺母座的变形和滚珠丝杠轴承的轴向接触变形。1_丝杠的拉压变形量11=FmL / EA (3-7)=1790.682280 / 20.610(31.5) = 0.0064mm2 滚珠与螺纹滚道间的接触变形量2 采用有预紧的方式,因此用公式 2= 0.0013 (3-8) = =0.0028mm在这里 =1/3Fm=1/31790.68=597NZ= dm/Dw=3.1463/4.763=41.53 Z=41.533.51=145.36丝杠的总变形量=1+2=0.0064+0.0028=0.0092mm4所以丝杠很稳定。3.1.3横向滚珠丝杠螺母副的型号选择与校核步骤(1)型号选择1) 最大工作载荷计算 由于导向为贴塑导轨,则:k=1.4 f =0.05 ,Fl为工作台进给方向载荷,Fl=2144N , Fv=5360N , Fc=1340N ,G=60kg , t=15000h,最大工作载荷:F m=kFl+ f(Fv+2Fc+G) =1.42144+0.05(5360+21340+9.875) =3452.6N2)最大动负载的计算v横=1400r/min 0.79mm/r = 1106 mm/minn横丝= v横1/2 / L。纵=11061/2 / 5 =110.6r/minL=60nt/10=1106110.615000 /10=99.54C =fmFm=99.541.53352.6=23283.8N初选滚珠丝杠型号为:CD256-3.5-E其基本参数为 Dw =3.969mm ,=211,L。=6mm,dm=25mm,圈数列数3.51(2)横向滚珠丝杠的校核1)传动效率计算=tg /tg (+)=tg211/tg(211+10)=93%2)刚度验算1丝杠的拉压变形量1=FmL/EA = 3352.6320/20.61025 = 0.0026mm2滚珠与螺纹滚道间的接触变形量2=0.0013 =0.0013= 0.0099mm 在这里 Fyj=1118NZ=dm/Dw=3.1450/3.969=39.56Z=39.563.51=138.48丝杠的总变形量=1+2=0.0026+0.0099=0.0125mm100mm时n=6m由结构确定,在这里均取3,d3为螺钉直径.(1)D=26时的尺寸 =n-d3-1 则d3=2.5 取M4的螺钉=26+2.52.5=32.25=32.25+32.5=39.25=0.9D=0.926=23.4m=3(2)D=37d3=2.5mm取M4的螺钉=37+6.25=43.25mm=43.25+7.5=50.75mm=0.937=33.3mmm=3mm3.4.2 通盖图3-6 通盖=D+(22.5)d3+2S2(有套环)=D。+(2.53)d3 =(0.850.9)Dd。=d3+(12) D100mm时n=4D100mm时n=6m由结构确定,在这里均取3mm,d3为螺钉直径.(1)D=6通盖尺寸,内加密封圈d3取M4螺钉=32.5 =39.75=23.4 d=18m=3(2)D=37通盖尺寸 d3取M4螺钉=43.25 =50.75=33.3 d=25m=33.5丝杠轴承的选型与校核3.5.1滚珠丝杠用轴承的选型选用型号 7602025TVP的60推力角接触轴承 轴径 d=25mm 外径d=52mm 宽度B=15mm 球径Dw=6.35mm 球数Z=16 动载荷Ca=22000N 静载荷Coa=44000N 预加载荷500N 极限转速2600r/min3.5.2校核 大部分滚动轴承是由于疲劳点蚀而失效的。轴承中任一元件出现疲劳步剥落扩展迹象前院运转的总转数或一定转速下的工作小时数称为轴承寿命(指的是两个套圈间的相对转数或相对转速)。 同样的一批轴承载相同工作条件下运转,各轴承的实际寿命大不相同,最高和最低的可能相差数十倍。对一个具体轴承很难预知其确切寿命,但是一批轴承则服从一定的概率分布规律,用数理统计的方法处理数据可分析计算一定可靠度R或失效概率n下的轴承寿命。实际选择轴承时常以基本额定寿命为标准。轴承的基本额定寿命是指90%可靠度,常用材料和加工质量,常规运转条件下的寿命,以符号L10(r)或L10h(h)表示。不同可靠度,特殊轴承性能和运转条件时其寿命可对基本额定寿命进行修正,称为修正额定寿命。 标准中规定将基本额定寿命一百万转(10r)时轴承所能承受的恒定载荷取为基本额定动载荷C。也就是说,在基本额定动载荷作用下,轴承可以工作10r而不发生点蚀失效,其可靠度为90%。基本额定动载荷大,轴承抗疲劳的承载能力相应较强。径向基本额定动载荷Cr对向心轴承(角接触轴承除外)是指径向载荷,对角接触轴承则是指引起轴承套圈间产生相对径向位移时的载荷径向分量。对推力轴承,轴向基本额定动载荷Ca是指中心轴向载荷。(1) 当量载荷滚动轴承若同时承受径向和轴向联合载荷,为了计算轴承寿命时在相同条件下比较,需将实际工作载荷转化为当量动载荷。在当量动载荷作用下,轴承寿命与实际联合载荷下轴承的寿命相同。当量动载荷P的计算公式是:P= (3-14)表3.4 轴承滚动当量动载荷计算的X,Y值轴承类型 Fa/Cor e 单向轴承双列轴承Fa/FreFa/FreFa/FreFa/FreX Y XY XYXY 角接触球轴承=150.0150.381 00.441.4711.65 0.722.390.0290.41.401.572.280.0580.431.301.462.110.0870.461.231.3820.120.471.191.341.930.170.501.121.261.820.290.551.021.141.660.440.561.001.121.630.580.561.001.121.63当量动载荷式中Fr为径向载荷,N;Fa为轴向载荷,N;X,Y分别为径向动载荷系数和轴向动载荷系数,可由上表查出。 上表中,e是一个判断系数,它是适用于各种X,Y系数值的Fa/Fr极限值。试验证明,轴承Fa/Fre或 Fa/Fre时其X,Y值是不同的。单列向心轴承或角接触轴承当Fa/Fre时,Y=0,P=Fr,即轴向载荷对当量动载荷的影响可以不计。深沟球轴承和角接触球轴承的e值随Fa/Cor的增大而增大。Fa/Cor反映轴向载荷的相对大小,它通过接触角的变化而影响e值。=0的圆柱滚子轴承与滚针轴承只能承受径向力,当量动载荷Pr=Fr;而=90的推力轴承只能承受轴向力,其当量动载荷Pa=Fa。 由于机械工作时常具有振动和冲击,为此,轴承的当量动载荷应按下式计算: P=fd(XFr+Yfa)冲击载荷系数fd由表3.3选取表3.5 冲击载荷系数表载荷性质 机器举例fd平稳运转或轻微冲击电机,水泵,通风机,汽轮机1.01.2中等冲击车辆,机床,起重机,冶金设备,内燃机1.21.8强大冲击破碎机,轧钢机,振动筛,工程机械,石油钻机1.83.0由于轴承载荷与纵向载荷之比:=0.25C 此轴承合乎要求另外由于横向丝杠与纵向丝杠采用同一轴承,且载荷小于纵向,因此同理可验证其是合理的。3.6主轴脉冲发生器的安装将脉冲发生器与原车床挂轮组首根外伸轴采用同步齿形带联接,这能最大限度的利用原车床附件。这同样需要制造一对相同齿数的齿轮及脉冲发生器固定装置,且需要对挂轮组首根外伸轴改造。本设计采用此方案。(1)安装前准备工作图3.7 CA6140挂轮组示意图1-挂轮轴a 2-挂轮a 3挂轮架 4-挂轮轴b 5-挂轮b 6-主轴箱把挂轮a 、挂轮b、挂轮轴b 、挂轮架拆除;在挂轮轴a上铣一个键槽,用于联接齿轮,并车一段外螺纹;做一个支架,用于固定脉冲发生器准备一对相同齿数的齿轮以及同步齿形带(2)安装把支架固定在进给箱外表面,2个L型支架用螺栓连接;把脉冲发生器固定在支架上;安装齿轮及同步带。齿轮和轴,采用过盈配合。主轴传动可经过原有CA6140车床主轴箱中58/58和33/33两级齿轮(实现11)传递到原有CA6140车床的挂轮轴a。安装总图如 图3.8脉冲编码安装示意图1-挂轮轴 2-同步齿形带 3-脉冲发生编码器 4-支架(2)主轴脉冲发生器安装注意事项主轴脉冲发生器属于光学元件,安装时应小心轻放;不能有较大的冲击和振动,以防损坏玻璃光栅盘,造成报废;更应注意主轴脉冲发生器的最高运行转速,车床主轴的转速必须小于此转速,以免损坏脉冲发生器。第五章 电机的选择4.1主轴电机的选择 机床主传动的作用是把电机的转速和转矩通过一定途径传给主轴,使工件以不同的速度运动,主传动性能的好坏,直接影响零件的加工质量和生产效率。考虑到改造的经济性,可采用机床原有的普通三相异步交流电动机拖动。考虑到加工过程中当电网电压和切削力矩发生变化时,电机的转速也会随之波动,直接影响加工零件的表面粗糙度。因此为提高加工精度,实现主轴自动无级变速,改用主轴伺服电机,从而不需进行机械换档。采用机床原有的普通三相异步交流电动机拖动,在机床转速需要改变时,需要停机手动调转速,若采用主轴伺服系统,则不需要停车手动变速,实现调速自动化,节省操作时间,提高生产效率,同时减轻工人劳动强度。 这里选用ZJY208-7.5B型主轴伺服电机,采用全封闭式无外壳风冷结构,外形美观、结构紧凑。采用优化的电磁设计,电磁噪声低、运行平稳、效率高。采用进口高精度轴承和转子高精度动平衡工艺,确保电机运行在最高转速范围内稳定可靠,振动小、噪声低,采用变频电机专用耐电晕漆包线,F级绝缘等级,IP54防护等级,确保电动机在-1540环境温度及粉尘油雾环境下可靠使用。采用高速、高精度光电编码器,与高性能驱动器配合可作高精度速度和位置控制。过载能力强,可30分钟150%额定功率下可靠运行。耐冲击,寿命长,性能价格比高。这里选用DAP03-075型交流异步主轴伺服驱动单元来控制电机的运动。DAP03交流异主轴伺服驱动单元采用高性能 DSP和CPLD 等集成芯片实现数字式控制,可靠高,智能功率 IPM 模块驱动,动态响应特性好,采用异步电机矢量控制算法,有效调速范围宽,从1.5r/min-6000r/min,其中恒转矩调速范围为1.5r/min-1500r/min,转速波动小。只需外部触点信号就能实现主轴定位,380V电源直接输入,不需要电源变压器,安装方便、成本低。由数控系统来输出0-10V信号来控制伺服驱动单元,进而控制电机运动。4.2纵向步进电机的选择4.2.1 确定系统的脉冲当量脉冲当量是指一个进给脉冲使机床执行部件产生的进给量,它是衡量数控机床加工精度的一个基本技术参数。因此,脉冲当量应根据机床精度的要求来确定,CA6140的定位精度为0.015mm,因此选用的脉冲当量为0.01mm/脉冲 0.005mm/脉冲。本设计采用的数控系统脉冲当量为0.01mm/脉冲。4.2.2步距角的选择根据步距角初步选步进电机型号,并从步进电机技术参数表中查到步距角b ,三种不同脉冲分配方式对应有两种步距角。步距角b 及减速比 i与脉冲当量p 和丝杠导程 L0 有关。初选电机型号时应合理选择b及i, 并满足: b (pi360)/L0 (4-1)由上式可知:b pi360/L0=3600.011/10=0.36初选电机型号为:90BYG5502具体参数如表4.1所示 表4.1 90BYG5502具体参数 纵向电机步距角相数驱动电压电流90BYG55020.36 550V3A静转矩空载起动频率空载运行频率转动惯量重量 5N.m 2200 3000040 kg.cm4.5kg图4-1 电机简图4.2.3矩频特性: =J=J10(N.cm) (4-2)由于: nmax=(r/min) (4-3)则: Mka=J(N.cm)式中:J为传动系统各部件惯量折算到电机轴上的总等效转动惯量(kg.cm);为电机最大角加速度(rad/s);nmax为与运动部件最大快进速度对应的电机最大转速(r/min);t为运动部件从静止启动加速到最大快进速度所需的时间(s);vmax为运动部件最大快进速度(mm/min); p为脉冲当量(mm/脉冲);b为初选步进电机的步距角()步,对于轴、轴承、齿轮、联轴器,丝杠等圆柱体的转动惯量计算公式为J=(kg.cm),对于钢材,材料密度为7.810(kg.cm),则上式转化为J=0.78DL10(kg.cm),式中:Mc为圆柱体质量(kg);D为圆柱体直径(cm),JD为电动机转子转动惯量,可由资料查出。(1)丝杠的转动惯量Js Js=Js/i,i为丝杠与电机轴之间的总传动比由于i=1则: Js=0.78DL10 (4-4) =0.78(6.3)17010=208.9( kg.cm)(2)工作台质量折算工作台是移动部件,其移动质量惯量折算到滚珠丝杠轴上的转动量JG:JG=()M( kg.cm),式中:L。为丝杠导程(cm);M为工作台质量(kg).由于L。=1cm,M=90kg则 : JG=()M (4-5)=90=2.28( kg.cm)1)一对齿轮传动小齿轮装置在电机轴上转动惯量不用折算,为J1.大齿轮转动惯量J2折算到电机轴上为 =J2() (4-6)2)两对齿轮传动传动总速比i=i1i2,二级分速比为i1=z2/z1和i2=z4/z3.于是,齿轮1的转动惯量为J1,齿轮2和3装在中间轴上,其转动惯量要分别折算到电机轴上,分别为J2()和J3().齿轮4的转动惯量要进行二次折算或以总速比折算为:=J4()() (4-7)因此,可以得到这样的结论:在电机轴上的传动部件转动惯量不必折算,在其他轴上的传动部件转动惯量折算时除以该轴与电机轴之间的总传动比平方。由于减速机构为一对齿轮传动,且第一级i=1,则可分别求出各齿轮与轴的转动惯量如下:n=45,m=1.5的转动惯量J45,其分度圆直径d=451.5=67.5mmS=27mm 则:J45=0.786.7510=4.371 kg.cmn=40,m=1.5的转动惯量J40,其分度圆直径d=401.5=60mmS=27mm 则:J40=0.78610=2.73kg.cm两输入输出轴的转动惯量为:J输入=0.781.81310=0.106 kg.cm ; L=130mmJ输出=0.782.51310=0.396 kg.cm ; L=130mm查表得:JD=4 kg.cm综上可知:J=JD+Js+JG+J30+J40+J60+J50+2J45=252.302 kg.cm (4-8) 又由于 V =1.461600=2236mm/min则:Mka=252.30210=41.1N.cm(3)力矩的折算:1)Mkf空载摩擦力矩Mkf= (4-9)式中:G为运动部件的总重力(N); f为导轨摩擦系数;i为齿轮传动降速比;为传动系统总效率,一般取=0.70.85;L。为滚珠丝杠的基本导程(cm)。由于G=9010=900N, f=0.05, i=1, =0.85则Mkf =8.4N.cm2)M。附加摩擦力矩 M。=(1-。) (4-10)式中:Fyj为滚珠丝杠预加负载,即预紧力,一般取1/3Fm;Fm为进给牵引力(N), 。为滚珠丝杠未预紧时的传动效率,一般取。0.9得 Fyj=1/3Fm=1/31728.8=576.3N又 L。=10mm , =0.95则 M。=96.6 N.cm 则 =+M。=41.1+8.4+96.6=140 N.cm由于=则所选步进电机为五相十拍的经表查得 :=0.951则 =1.67N.m=0.955=4.75N.m所以所选步进电机合乎要求4.2.4据步进电机的矩频特性计算加减速时间校核的快速性T=(fn-f0) (4-11)式中:T为加减速时间,Jr和Jl分别为转子,负载的转动惯量(kg.m)为电机得步距角(),Tcp,Tl为电机最大平均转矩,负载转矩(N.m)f。,fn为起始加速时,加速终了时的频率(Hz)由于 Jr=0.410 kg.mJl=0.0252 kg.m=0.36Tcp=5 N.mTl=1.67 N.mf0=2200Hzfn=30000Hz 则T=(30000-2200) =1.2s1.5s所以选此步进电机能满足要求。4.3 横向步进电机的选择4.3.1步距角的确定 b pi360/L。 (4-12)L。=6mm , i=1 , p=0.005 b 0.3初选电机型号为:90BYG5502,为了便于设计和采购,仍选用90BYG5502型直流电动机。 4.3.2距频特性(1)力矩的折算1)空载摩擦力矩Mkf =GfL。/2i G=6010=600Nf=0.05L。=6mm=0.8 =3.5(N.cm)2)附加摩擦力矩 M。=(1-。)(N.cm)Fyj=1/3Fm=1/33433.6=1144.5NL。=6 M。=115 N.cm(2)转动惯量的折算1)滚珠丝杠的转动惯量Js=0.78DL10 D=4cm L=26cm Js=0.78DL10=0.78(4)2610=5.19 N.cm2)工作台转动惯量 JG=M (4-13) L。=0.6cmM=60kg JG=M=60=0.54( kg.cm) (3)减速装置的转动惯量折算Z=30 d=mz=1.530=45mm J=0.78D L10 =0.784.51.810 =0.58kg.cmZ=40 d=mz=1.540=60mm 又由于 J输入=0.106 kg.cm J输出=0.396 kg.cm JD=15.8 kg.cm则 J=Js+JG+JJ=58 kg.cmMka= J10vmax=0.781600=1248mm/mint=1.5sp=0.005b=0.3Mka=50=7.257N.cmMkq=Mka+Mkf+M0=7.527+3.5+115=125.7N.cm又 MkqMjmax步进电机为五相十拍=0.95 Mjmax=16N.mMkq=1.257N.m0.9516=15.2N.m所以此步进电机符合条件(4)上升时间校核t=(fn-f0)Jr=1.5810 kg.mJl=5.810 kg.m=0.3Tcp=16N.mTl=1.257N.mf0=2500Hzfn=35000Hz t= (35000-2500)=0.086s1.5s合乎要求第六章 数控刀架的选择拆除原车床上的刀架,换上数控刀架,能够在数控系统的控制下自动转位,完成换刀功能。使用数控刀架,可以节约换刀时间,多刀夹持,提前对好刀,设置好刀偏,短时间内只需要调整刀偏值,不用再次对刀,更是大大的节约了时间。这里选用AK21系列刀架,AK21系列数控转塔刀架特别适用于经济型数控车床,可多刀夹持,实现了加工程序的自动化,高效化。它采用鼠齿盘作为分度定位元件,分度工位由定位盘、霍尔传感器控制,可任意工位定位;具有定位精度高,稳定可靠,应用范围广,结构简单,维修方便。下表为AK21160*4*4C刀架主要参数。表6.1 AK21160*4*4C主要参数安装图及尺寸: 型 号ABCL1L2H1HXX1yh12MH3H4NAK211604C1171261463882732177016017011432132060/32主要参数:序号项目 1刀台方(mm)1602工位数(个)43装刀基面高(mm)704装刀基准孔高(mm)/5单工位转位时间(s)3.246刀架转速(r/min)177最大切向力矩(N .m)5008最大颠覆力矩(N .m)12509重复定位精度(mm)0.00510毛重(Kg)3811净重(Kg)3012箱体尺寸(mm)560400353总结 在生活逐渐自动化的今天,产品更新日益加快,对加工制造的精度和加工效益都提出了很高的要求,因此对机床等加工设备提出了很高的要求。我国旧式机床占较大比重,这种单一的靠手工操作的机床,在很大程度上已经不能满足现代化的要求,数控机床的改造已经成为一种必要。但这次机床的改造是在原有的机床上换掉部分零部件,使它具有数控机床的基本功能,如不用手工操作能自动控制进给量及自动换刀等,但又考虑到,由于CA6140本身的局限性和经济性原因,改造成车床属于经济型数控车床,因此在这次设计中有些组件选型精度不是很高,选择了相对比较实惠的型号。 因为我们以前的基础知识掌握得不牢固,在这次设计中遇到了很多的问题,但在这过程中,我们又学会了很多东西,在以前的课程设计中,只是设计一个小的机构或者简单的机器,这次是一个对我来说很大的题目。刚开始有点不知从何下手的感觉,在老师的指导下,随着设计的进行,特别是把以前学过的知识又温习了一下,而且把很多门课程都串联在一起,形成一个大的框架,有一种豁然开朗、焕然一新的感觉。 通过这最后的毕业设计,重新把以前所学知识练习一遍,使所学知识融入到实践中,不仅加固了以往所学知识,更重要的是使我们掌握了独自做一个设计的能力,以前的设计都是时间比较短,任务比较简单,通过毕业设计使我们能更好的适应以后的上班工作。参考文献1 吴振彪主编机电综合设计中国人民大学出版社,20002 余英良主编机床数控改造设计与实例机械工业出版社,19973 机床设计手册编写组编机床设计手册第一,三,四册机械工业出版社,19984 明兴祖主编数控加工技术化学工业出版社,20015 胡占齐,杨莉主编机床数控技术机械工业出版社,19866 黄调,赵松年主编机电一体化技术基础及应用机械工业出社,19997 杨有君主编数字控制技术与数控机床机械工业出版社,19998 王先逵主编机械制造工艺学机械工业出版社,20029 廖念钊,古莹庵主编互换性与技术测量中国计量出版社200010 李壮云主编江西科学技术出版社. 中国机械设计大典第五卷,200211 陈碧秀等主编实用中小电机手册。辽宁科学技术出版社,200012 王槐德主编. .中国标准出版社,2003.13 普通CA6140车床的说明书.14 邱宣怀主编.高等教育出版社,2002.15 薛严成.上海科学技术出版社,1999.附录附表 1 说明书中各符号一览表名称符号单位步进电机的步距角b()/脉冲脉冲当量pmm滚珠丝杠导程L。mm转动惯量J千克/米平方车床的切削功率PmkW机床电机功率PeKW进给方向载荷Fl,FxN拖板上垂直方向载荷Fv,FzN拖板上横向方向载荷Fc,FyN扭矩MN.m传动效率变形量mm临界载荷FkN稳定系数nk最大静转矩MjmaxN.cm名义启动转矩MnqN.cm空载启动转矩MkqN.cm最大动负载CN额定静载荷CoaN额定动载荷CaN最大工作载荷FmN主轴恒功率调速范围Rnp电动机恒功率调速范围Rp英文资料Evaluation of Size Effect on Micro-machine-tools Design for MicrofactoryM. Yamanaka1, S. Hirotomi2 and K. Inoue31Tohoku University, 6-6-01, Aramaki-Aoba, Sendai 980-8579, Japan, yamanakaelm.mech.tohoku.ac.jp2Shimano Inc, Japan3Tohoku University, JapanAbstract. A micro lathe with a machine base size of 150100 mm (postcard size) was developed by the authors. It has a good cutting performance for brass test workpieces. To know the developed machine is most suitable size for machining the given workpiece size, the error functions, which affect the cutting performance, are examined how to change to the machine tool size. The calculation method and a simple size effect of error functions are proposed and their usefulness is examined by some calculation results.Keywords: Microfactory, Machine tools, Lathe, Machine design, Size effect1. Introduction Ordinary production systems use enlarged machine tools aiming at high rigidity regardless of the size of the parts produced. The concept of microfactory is to use small machine tools corresponding to the miniaturization of workpieces. This is useful for saving resources, space, and energy. Some prototypes were developed to realize this concept 1. Okazaki developed an NC micro lathe which is 322830 mm in size 1. Park developed a miniaturized 3-axis milling machine of 200300200 mm 2. The authors are developing micro lathes aiming at the practical use in mass production systems of small/micro parts for optics, IT and electronics, until now 3. The machine with a base size of 150100 mm (postcard size) has been developed and the relation between machine characteristics and cutting performance are evaluated to clarify advantage/disadvantage of the developed lathe 4. To design micro machine tools, it is important to properly understand the merits and demerits of downsizing. Mishima proposed a design tools 5 combined with the form-shaping theory of machine tools6 and Taguchi method 7. It offers a simplified method to consider the deformation of machine tool structures and the component errors. The developed micro lathe has a good cutting performance for the test workpiece. However, it is obscure that the developed machine is most suitable size for machining the given workpiece size. It is impossible to make many sizes of machine tools and evaluate their performances. In this paper, the outline of developed micro lathe is introduced, and the influence of accuracies according to the machine size to the cutting performance is examined in a simulation. The calculation method considering the size effect on micro machine tools design is discussed with the calculation results.2. Micro Lathe The maximum size of target workpiece was assumed to be5 10 mm and the lathe was designed. The size of the machine base was decided to be of A6 size (150100 mm) for its foot print area considering the degree of miniaturization, its practicality, assembly and, in particular, a sufficient rigidity. Each device of the machine was designed with this restriction. The developedmicro lathe MTS 2 (product of Nano Corporation, Japan) is shown in Fig. 1.1. X and Z-axis tables, which use the same modules, are guided by cross-roller ways, and driven by a 2-triangle screw thread and an AC 15-mm in square servomotor. The size of the table is about 5080 mm (excluding motor). The weight including the motor is 585 g. The headstock is fixed on the X-axis table and the tool post is mounted on the Z-axis table.Figure 1.1. Appearance of developed micro lathe MTS2 (Nano Corporation, Japan, base size: 150x100 mm) A micro motor of 16 mm diameter is used to drive the work spindle in the headstock from the balance with the table. A rotary speed of more than 10000 min-1 is necessary to obtain a cutting speed of about 150 m/min for small-diameter workpieces. Because of this, a direct drive is preferred, but a reducer is required to drive the workpiece because the motor torque of a 16 mm class motor is extremely small (only a few mNm), which is generally not enough to obtain a sufficient cutting power. The rotary speed is secured as much as possible by selecting a high-speed motor. The planetary roller reducer using traction drives is adopted for this work spindle. The reduction ratio is 4. The size and weight of the headstock is 754030 mm, its weight is 230 g (include motor).3. Calculation of Error in Consideration of Size Effect There are many error functions, which affect the cutting performance. Here, only four error functions, namely the assembly error, the motion error, the deformation by cutting force and the thermal deformation, are considered, and how they change to the machine tool size is examined. Then we propose the calculation method of error in consideration of size effect. The model with dimensions of above-mentioned micro lathe and those of enlarged/reduced are used to calculate by using the formshaping theory. The deviation from the target position of the tool point is obtained and the proposed method is evaluated.3.1 Calculation method The above-mentioned micro lathe is modeled as shown in Fig. 1.2. The model consists of eight elements. The numbers from 0 to 7 are given to the reference point in coordinate transformation on each element. Though the bed is actually one solid component, it is divided into two parts virtually to consider the influence of the beds rigidity. The target position in the tool point is apart from the point 0 to h in Z-direction and R in X-direction, respectively. An orthogonal coordinate system Si corresponding to an element i is defined. The transformation from Si to Si+1 is represented by the coordinate transformation, which is represented by the homogeneous transformation matrices Ai. Vector rw represents the relative displacement between the workpiece and the tool, and vector rT represents the position of the tool point. The relation between rw and rT is given by Eq. (1), and rw is defined as the form-shaping function.The error between element i and i+1 is represented by another homogeneous transformation matrix i as follows.The form-shaping function considering the error is defined as rw expressed byThe form-shaping error function re, which expresses the error as a quantitative deviation from the target position, is defined as Eq. (4).The error between elements of the micro lathe is represented by 6 components, which are translational and rotational motions along the X, Y and Z axes, as x, y, z, , , and , respectively. The limited four error functions may affect between elements shown in Fig. 1.3. The assembly error appears between all elements except between the bed 1 and the bed 2, which are divided into two parts. The motion error appears between the elements that move relatively during cutting. Because force and heat propagate through an element, the deformations by cutting force and heat appear between all elements. Moreover, as shown in Table 1, it was analyzed and classified which error components are affected by above-mentioned four error functions. For example, the motion error between the workpiece and the work spindle depends on the runout of the work spindle. Because the workpiece rotates around the Z-axis, the translational error in X and Y except Z-axes are considered. The assembly error can not define the direction to appear, and is assumed to appear in all 6 components. The deformations by cutting force and heat are assumed to appear in 3 components of translationalerror.3.2 Size effect of errorTable 2 shows to what extent the amount of error of each item in Table 1 changes when the size of the machine tool is changed n times, which is examined by other reports 8,9 and the calculation. It is thought that the difficulty of assembly is constant regardless of the machine size. Therefore, the size effect of the assembly error is 1. The motion error depends on the accuracies of guides in a slide table or bearings in a work spindle. Here, it is considered that the machine element of same absolute accuracy can be selected regardless of the size, and the size effect of the motion error is assumed to be 1 as well as the assembly error. The cutting force is divided in 3 directions, namely principle, the thrust and the feed force. A simple bend and compression of beam according to the direction of applied force on each element is considered, the size effect of deformation by cutting force is assumed to be 1/n and 1/n2, respectively. If the temperature increases, generally a material expands. The deformation t of a member having a length can be calculated using the formulawhere, t is the linear coefficient of thermal expansion and T is the temperature rise of the member. Therefore, the size effect of thermal deformation is considered as n.The dimensions of each element of the model in Fig. 1.2 are required to calculate the error. The real dimensions of the developed micro lathe shown in Fig. 1.1, and these are used as that of a model for n= 1. Then the model is enlarged n times and the error in Eq. (4) is calculated by the method mentioned above using the size effect of errors shown in Table 1.2. And how the error changes according to n is examined changing n from 0.5 to 10. However, the dimensions of workpiece and tool are assumed to be constant regardless of n, where R is 2.5 mm, h is 10 mm and t is 8 mm. In this method, actual values of error are required for the calculation. Hence, the magnitude of each error for n= 1 is decided as shown in Table 1.1. The assembly and the motion errors were decided in consideration of actual micro lathe. Both errors can take a positive or negative value, and are expressed with the sign of + or -. The deformations by cutting force and heat are obtained by FEM. The deformation of workpiece and tool were not considered. The element 7 is fixed and the magnitude of deformation of each element is obtained. The tangent force applied to a workpiece is calculated by the rated torque of the motor of the work spindle, and it is assumed to be the principal cutting force. The ratio among 3-divided cutting forces is decided by the reference 8. The deformation of each element when the atmosphere rises by 20 K is calculated as the thermal deformation. Because the target is a cylindrical component, the errors R in cutting radius and z in longitudinal direction are defined as the evaluation function of error. R and R are the actual and instructed cutting radii, respectively. R is given as follows. The assembly and motion errors take positive or negative values in Table 1.1, and the number of those items is 44. If the case of plus/minus in each item is combined, there are 244 patterns to calculate. This combination is so large that the orthogonal table in Taguchi method 7 is applied and the calculation is held in small combinations. Here, the orthogonal table of L64 is used to obtain re by Eq. (4) and the evaluation functions are calculated in 64 cases.The relation between the machine size n and the average of evaluation function is shown in Fig. 1.4. The max/min values are also plotted in the figure. The magnitude of R increases as n increases. The difference between the maximum and the minimum values increases too. The assembly error and the thermal deformation may be the reason for this. Though the magnitude of assembly error does not depend on n, as shown in Table 1.2, the movement in coordinate transformation becomes large as n increases, so that re becomes large. The thermal deformation increases because of its size effect. As for z, there is the minimum value near n = 1.5. z increases as well as R when n increases more than it. When n becomes small, z increases slightly by the size effect of the deformation by cutting force. This suggests that an optimum size of this kind of machine exists for a given size of workpiece. Here, R is set as 2.5 so that R x, y and R is almost constant from Eq. (6) though n becomes small.Each mean value for n is normalized by dividing by that for n= 1 to know the tendency of change of evaluation function to n. The result is shown in Fig. 1.5. R and z become 8 and 3.4 times as large as at n= 10. It can be said that the sensitivity of R to the machine size is higher. The calculation result by the proposed method changes greatly by the values of error and the size effect shown in Tables 1.1 and 1.2. In this study, though, the size effect of error functions was simplified, more examination is necessary to improve the accuracy of calculation.4. Conclusions The influence of accuracies according to machine size on cutting performance is examined. The conclusions may be summarized as follows:1. The error function, which affects the cutting performance, is examined. Then the calculation method of error in considerlation of size effect is proposed applying the form-shaping theory.2. The calculation model is built by using the dimensions of the actual micro lathe. The relation between machine size and error is obtained. The assembly error and the thermal deformation have the strongest influence.References1 Okazaki, Y., et al., (2004) Microfactory: Concept, historyand developments. Trans. ASME, J. ManufacturingScience and Engineering 126: 837-8442 Park, J. K., et al., (2006) A precision meso scale machine tools with air bearings for microfactory. Proc 5th Int.Workshop on Microfactories, Besancon, France (CDROM)3 Iijima, D, et al., (2004) Micro Turning System 3 (MTS3): A practical CNC lathe for microfactories. Proc. 4th Int. Workshop on Microfactories, Shanghai, China 1: 50-554 Yamanaka, M, et al., (2006), Relation between mechanical characteristic and cutting performance of micro lathe. Proc 5th Int. Workshop on Microfactories, Besancon, France(CD-ROM)5 Mishima, N., (2003) Design of a Miniature Manufactuirng System for Micro-fabrication. Proc 10th Annual Conf. for Concurrent Engineering, Modeira, Pirtugal 1129-11356 Reshtov, D. N., Portman, V. T., (1988) Accuracy of machine tools. ASME Press, New York7 Taguchi, G., Konishi, S., (1994) Quality engineering series. ASI Press8 Sugita, T., et al., (1984) Fundamentals of cutting (in Japanese). Kyoritsu Publish.中文翻译评价为微型工厂设计的微型机床的尺度效应M. Yamanaka1, S. Hirotomi2 and K. Inoue31Tohoku University, 6-6-01, Aramaki-Aoba, Sendai 980-8579, Japan, yamanakaelm.mech.tohoku.ac.jp2Shimano Inc, Japan3Tohoku University, Japan摘要: 一种微型机床总体尺寸为150100 mm(明信片大小)现在发展起来。它在切割黄铜制品的实验中表现出良好的性能。根据所给工件的大小,误差函数,这些影响切削性能的方面来确定机床的大小。受计算方法和简单的尺寸的影响的误差函数的提出是为审查通过一些计算结果。关键词:微型工厂 ,机床,车床,机械设计,尺寸效应1.导言 普通生产系统的使用大机床是针对高刚性,不论零件大小。微型工厂的概念是用小机床相应的小型化工件。这是对于节省资源,空间和能源是有益的。一些原型的开发就是为了实现这种观念1。冈崎研制出一种微型数控车床大小为322830mm1。开发的一种微型三轴铣床为200300200mm2。作者正在开发的微型车床着眼于实际使用在大规模生产系统中的小型/微型光学部件,信息技术和电子产品,截至目前为止3。已经研制成功的一种机床包括基座面积为150100mm(明信片大小),正在做机床的机械特性与切削加工性能两者之间关系的评价,以彻底弄清这种车床的优劣4 。设计微型机床时正确认识到小型化所带来优点和缺点是非常重要的。三岛提出了一个设计工具5 结合机床的仿型刨原理6和田口原理7。它提供了一种简化方法去考虑机床的结构变形和组件的误差。发展起来的微型车床对于测试工件表现出良好的切削加工性能。但是,所研制的机床大小对于工件尺寸是否是最合适模糊不清。也不可能设计许多大小不同的型号的机床来评估它们的表现。 在这篇论文中介绍的微型车床,对于机器的大小相对应的切削加工性能对于精度的影响已经在一个仿真中测试。设计微型机床时考虑到尺寸效应的计算方法与计算结果已经被讨论。2 .微型车床 车床设计时目标工件的最大尺寸假设为510mm。机床底座被设计为A6尺寸(150100mm)考虑到它的小型化程度和实用性。机器的每个部件都用此限制。这种微型车床MTS2(由日本Nano公司生产),引进Fig.1.1 X和Z 轴工作台,这种工作台使用相同的模块,用交叉辊子导向,用2三角螺纹与15mm方形交流伺服电机驱动。工作台大小是约5080mm(不包括电机 。包括电机的重量为585g。主轴箱固定在X轴上,刀架装在Z轴上。图1.1微型车床MTS2外观(Nano公司,日本,基座面积:150x100mm) 装在主轴箱里的工作主轴是由16毫米直径微电机驱动,主轴箱与工作台相连。转速超过10000转/分钟对于切削小直径工件时要取得切削速度约150米/分钟是很必要的。正因为如此,直接驱动是首选,但是需用减速机驱动工件,因为16毫米级电动机的转矩是非常小的(只有几mNm ),一般不足够提供足够的切削功率。旋转的速度可以保障的,可以选择转速尽可能高的电机。行星辊减速器用来驱动主轴。该减速器减速比是4 。尺寸为754030mm,它的重量是230 g(包括电动机)。3 .考虑到尺寸效应的计算误差 有许多误差函数会影响到切削性能。在这里,只考虑四个误差函数,即装配误差,运动误差,切削力导致的变形和热变形,以及它们如何影响机床尺寸已经被计算。那么,我们提出的计算误差的方法应考虑尺寸效应。
- 温馨提示:
1: 本站所有资源如无特殊说明,都需要本地电脑安装OFFICE2007和PDF阅读器。图纸软件为CAD,CAXA,PROE,UG,SolidWorks等.压缩文件请下载最新的WinRAR软件解压。
2: 本站的文档不包含任何第三方提供的附件图纸等,如果需要附件,请联系上传者。文件的所有权益归上传用户所有。
3.本站RAR压缩包中若带图纸,网页内容里面会有图纸预览,若没有图纸预览就没有图纸。
4. 未经权益所有人同意不得将文件中的内容挪作商业或盈利用途。
5. 人人文库网仅提供信息存储空间,仅对用户上传内容的表现方式做保护处理,对用户上传分享的文档内容本身不做任何修改或编辑,并不能对任何下载内容负责。
6. 下载文件中如有侵权或不适当内容,请与我们联系,我们立即纠正。
7. 本站不保证下载资源的准确性、安全性和完整性, 同时也不承担用户因使用这些下载资源对自己和他人造成任何形式的伤害或损失。

人人文库网所有资源均是用户自行上传分享,仅供网友学习交流,未经上传用户书面授权,请勿作他用。