摘 要
机械加工行业作为一个传统而富有活力的行业,近十几年取得了突飞猛进的发展,在新经济时代,行业呈现了新的发展趋势,由此对其它的质量,性能要求有了新的变化。现在机械加工行业发生着结构性变化,工艺工装的设计与改良已成为企业生存和发展的必要条件,工艺工装的设计与改良直接影响加工产品的质量与性能。
本文首先介绍了气门摇臂轴支座的作用和工艺分析,其次确定毛坯尺寸,然后进行了工艺规程设计,最后进行夹具设计。此次设计是对气门摇臂轴支座的加工工艺和夹具设计,其零件为铸件,具有体积小,零件结构简单的特点,由于面比孔易加工,在制定工艺规程时,就先加工面,再以面为基准来加工其它,其中各工序夹具都采用专用夹具,其机构设计简单,方便且能满足要求。
关键词:气门摇臂轴支座;工艺分析 ;工艺规程设计 ;夹具设计
Abstract
Machining industry ,as a traditional and vibrant industry, has been rapidly developed for a few past decades. In the new economic area,the industry presented a new development trend,and the trends also changes the quality and the performance of the production in some new abstracts. Machining industry is now taking place in structural changes, process design and improvement of equipment has become the necessary conditions of the enterprise survival and development, process equipment design and improved products directly affect the quality and performance.
This article introduces the role and process analysis of the valve rocker arm bearing support,followed by determining blank size, and then proceed to order the design process, the final fixture design. What will be disgned is The machining process and fixture design of the Valve Rocker Arm Bearing support,which has the chatacteristics of three abstrcat.its components for castings, with a small size, simple structure and the characteristics of parts,because the surface is easier than the easy processing, point of order in the development process, the surface on the first processing , and then to surface as a benchmark to other processing, including the processes used special fixture, and its design is simple, convenient and can meet the requirements.
Key words: JPEG; discrete cosine transform; MATLAB; graphical user interface
目 录
摘 要III
AbstractIV
目 录V
1 绪论1
1.1本课题的研究内容和意义1
1.2国内外的发展概况1
1.3本课题应达到的要求2
2 气门摇臂轴支座主要结构的机械设计3
2.1.零件的工艺分析及生产类型的确定3
2.1.1零件的作用3
2.1.2 零件的工艺分析3
2.1.3 确定零件的生产类型4
2.2 选择毛坯种类,绘制毛坯图5
2.2.1 选择毛坯种类5
2.2.2 确定毛坯尺寸及机械加工总余量5
2.2.3 设计毛坯图6
2.2.4 绘制毛坯图6
2.3 选择加工方法,制定工艺路线7
2.3.1 定位基准的选择7
2.3.2 零件的表面加工方法的选择7
2.3.3加工阶段的划分8
2.3.4工序的集中与分散8
2.3.5工序顺序的安排8
2.3.6 确定工艺路线9
2.3.7 加工设备及工艺装备选择10
2.3.8工序间加工余量的确定11
2.3.9切削用量以及基本时间定额的确定12
3 气门摇臂轴支座零件专用夹具的设计23
3.1 确定夹具的结构方案23
3.1.1 确定定位方案,选择定位元件23
3.1.2 确定导向装置24
3.1.3 确定夹紧机构25
3.1.4 确定辅助定位装置25
3.2 设计夹具体26
3.3 在夹具装配图上标注尺寸、配合及技术要求26
4总结与展望28
致 谢29
参考文献30
1 绪论
1.1本课题的研究内容和意义
本次设计是在我们学完了大学的全部基础课,技术基础课以及专业课之后而进行。此次的设计是对大学期间所学各课程及相关的应用绘图软件的一次深入的综合性的总复习,也是一次理论联系实际的训练。其目的在于:
1.巩固我们在大学里所学的知识,也是对以前所学知识的综合性的检验;
2.加强我们查阅资料的能力,熟悉有关资料;
3.树立正确的设计思想,掌握设计方法,培养我们的实际工作能力;
4.通过对气门摇臂轴支座的机械制造工艺设计,使我们在机械制造工艺规程设计,工艺方案论证,机械加工余量计算,工艺尺寸的确定,编写技术文件及查阅技术文献等各个方面受到一次综合性的训练。初步具备设计一个中等复杂程度零件的工艺规程的能力。
5.能根据被加工零件的技术要求,运用夹具设计的基本原理和方法,学会拟定夹具设计方案,完成夹具结构设计,初步具备设计出高效,省力,经济合理并能保证加工质量的专用夹具的能力。
6.通过零件图,装配图绘制,使我们对于AutoCAD绘图软件的使用能得到进一步的提高。
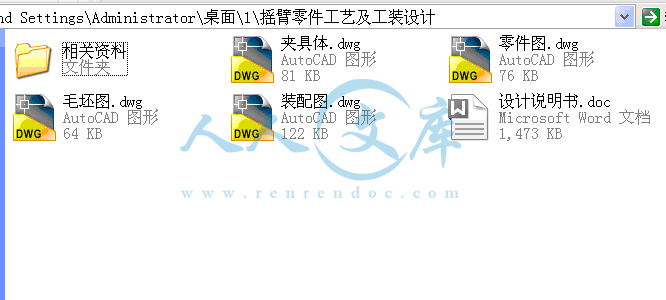

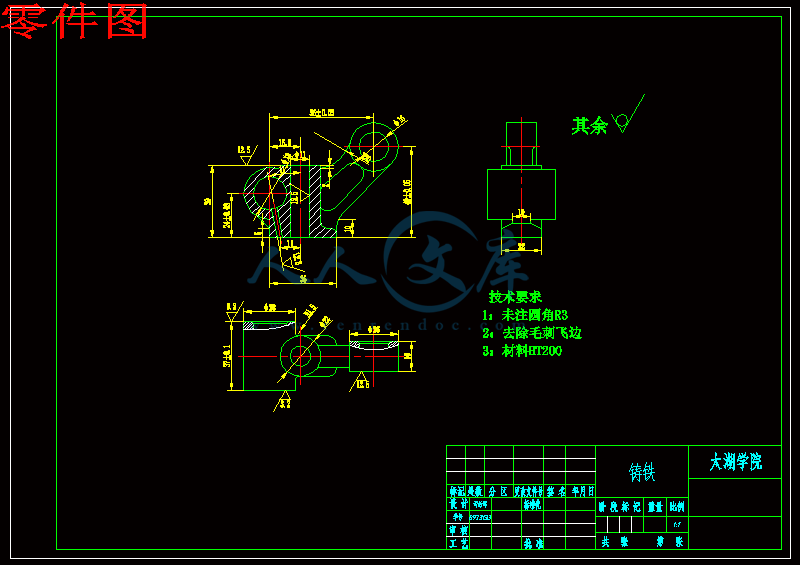
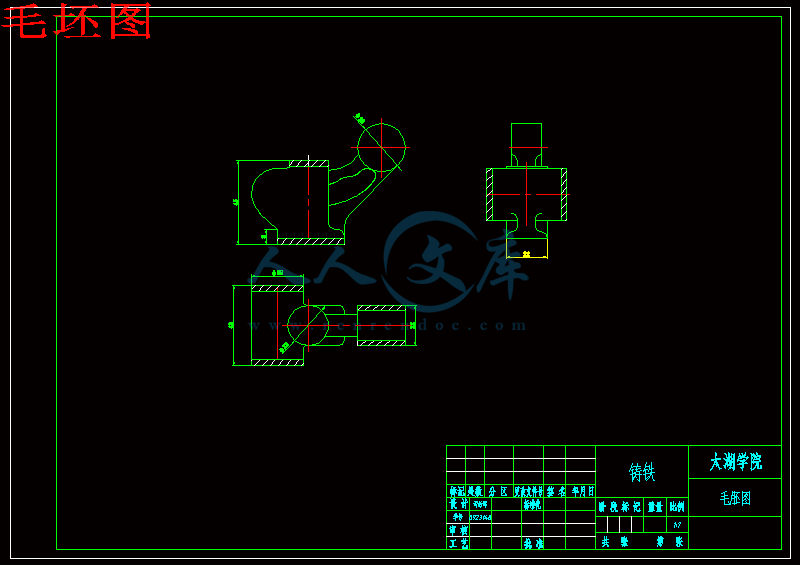
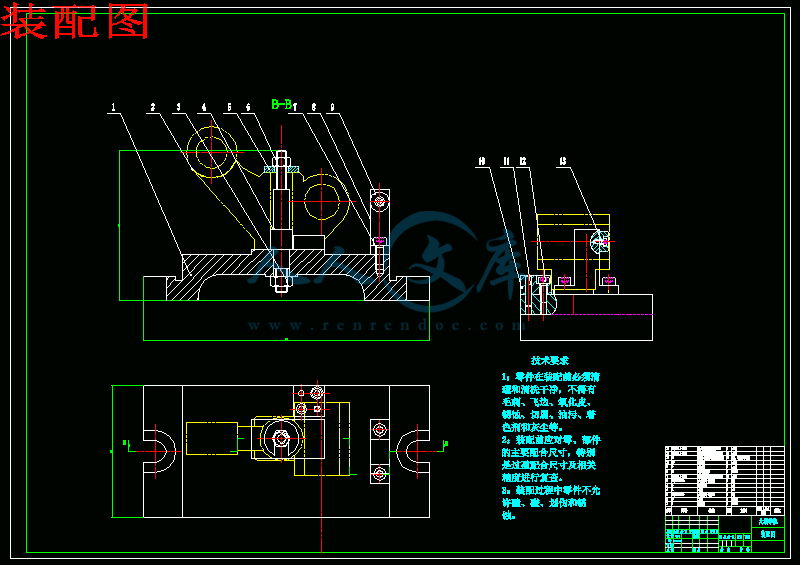
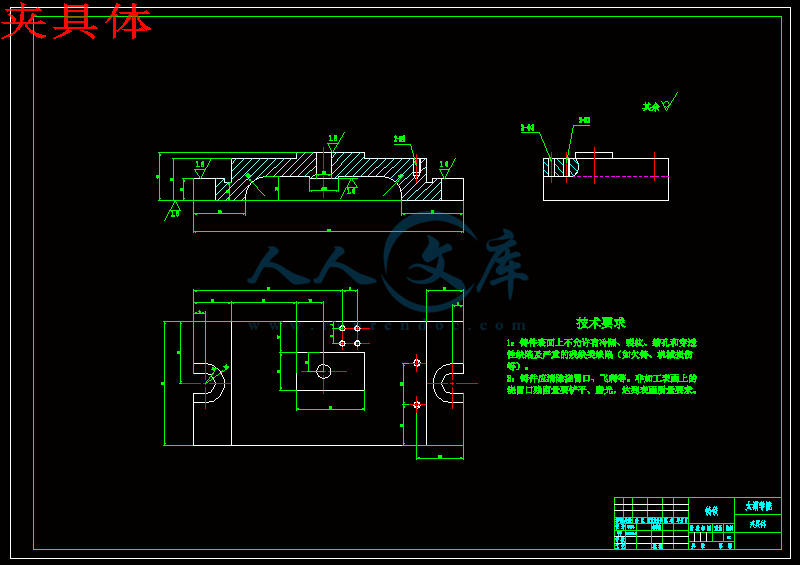