端盖落料拉深冲孔复合模设计
34页 11000字数+说明书+实习报告+5张CAD图纸【详情如下】
凸凹模.dwg
凸模.dwg
切边凹模.dwg
模具专业实习报告.doc
端盖.dwg
端盖落料拉深冲孔复合模总装图.dwg
端盖落料拉深冲孔复合模设计论文.doc

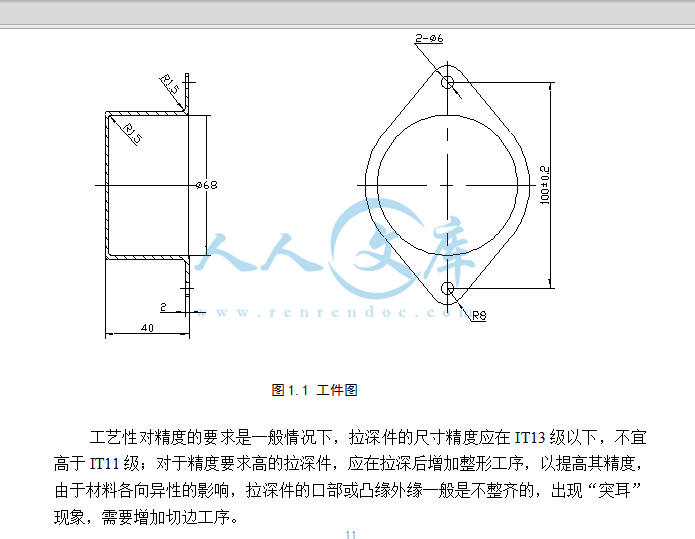
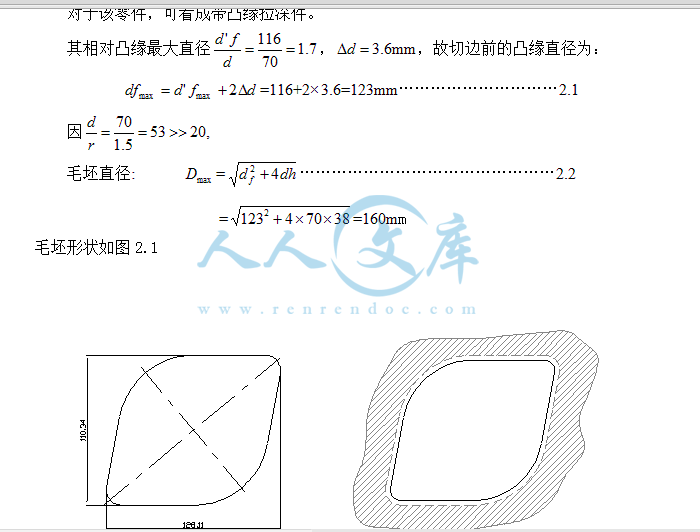
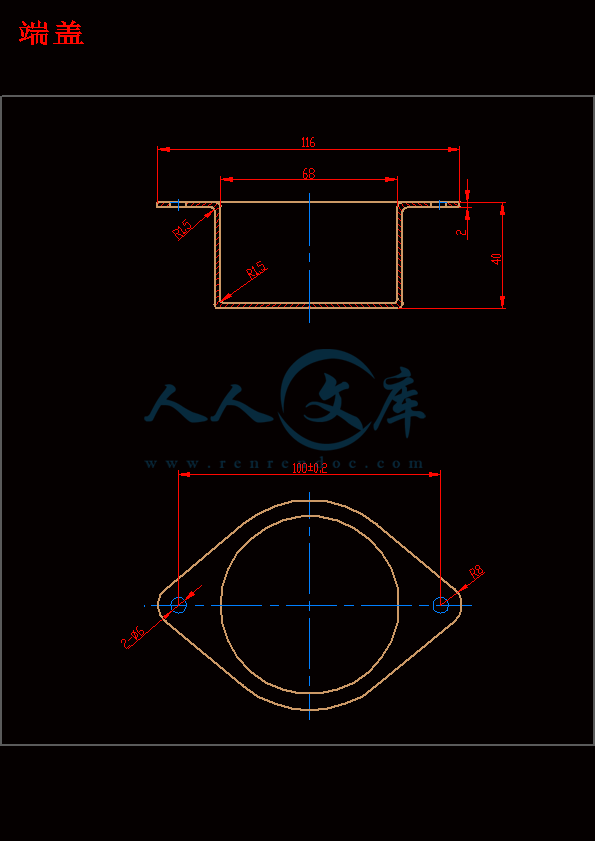
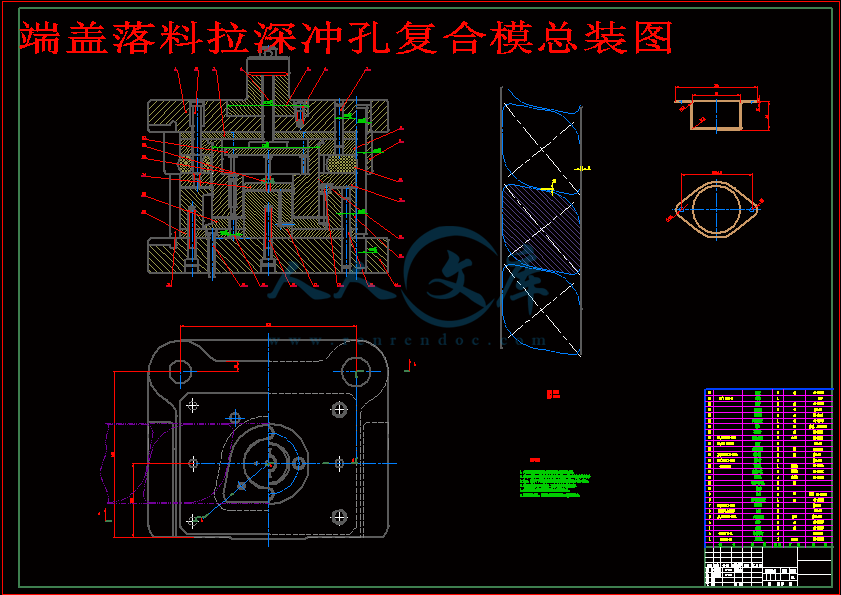
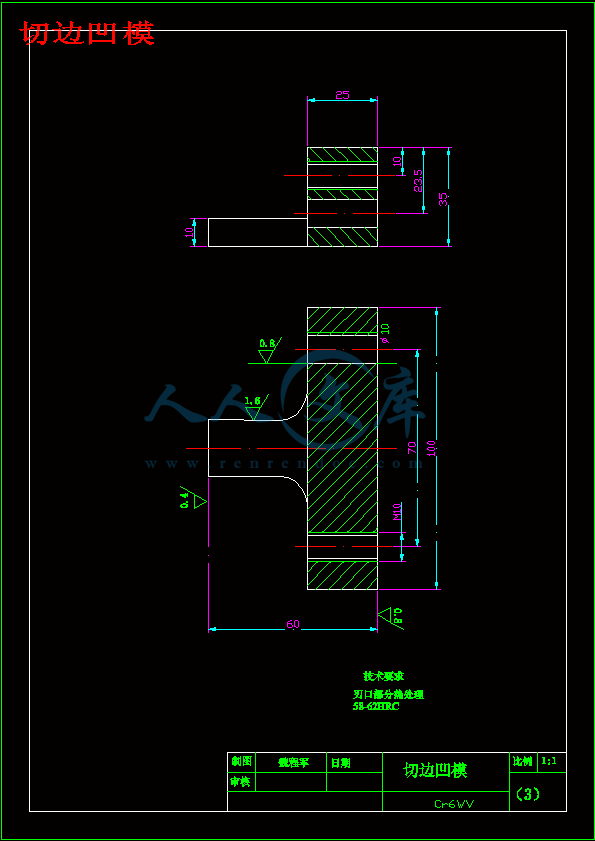


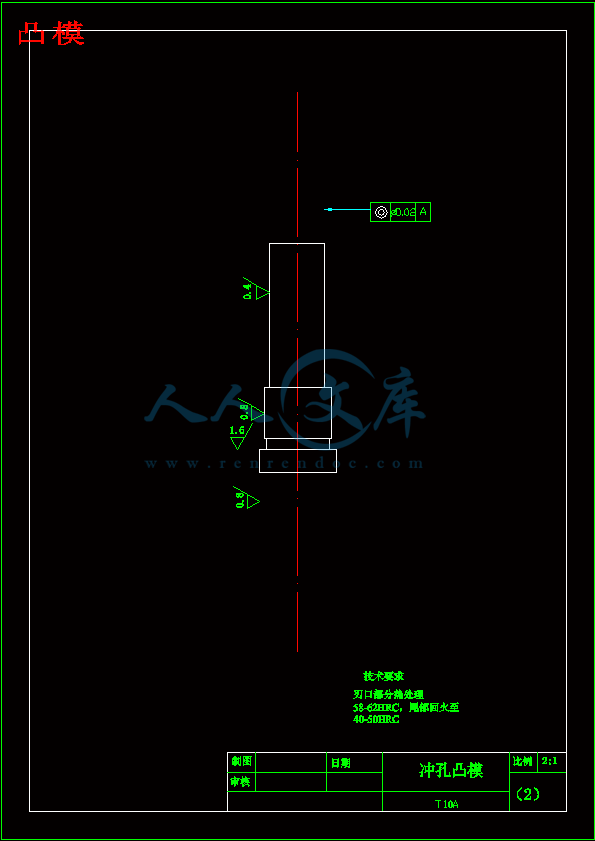
摘 要
随着中国工业不断地发展,模具行业也显得越来越重要。本文针对端盖的冲裁工艺性和拉深工艺性,分析比较了成形过程的三种不同冲压工艺(单工序、复合工序和连续工序),确定用一幅复合模完成落料、拉深和冲孔的工序过程。介绍了端盖冷冲压成形过程,经过对端盖的批量生产、零件质量、零件结构以及使用要求的分析、研究,按照不降低使用性能为前提,将其确定为冲压件,用冲压方法完成零件的加工,且简要分析了坯料形状、尺寸,排样、裁板方案,拉深次数,冲压工序性质、数目和顺序的确定。进行了工艺力、压力中心、模具工作部分尺寸及公差的计算,并设计出模具。还具体分析了模具的主要零部件(如凸凹模、卸料装置、拉深凸模、垫板、凸模固定板等)的设计与制造,冲压设备的选用,凸凹模间隙调整和编制一个重要零件的加工工艺过程。列出了模具所需零件的详细清单,并给出了合理的装配图。通过充分利用现代模具制造技术对传统机械零件进行结构改进、优化设计、优化工艺方法能大幅度提高生产效率,这种方法对类似产品具有一定的借鉴作用。
关键词:端盖;模具设计;复合模;拉深冲孔
ABSTRACT
With China's industries continue to develop and die industry is also becoming increasingly important. Based on the Cover of the stamping process and the deep drawing process, Comparative analysis of the process of forming three different stamping process (single processes, complex processes and continuous processes) confirm completion of a composite model blanking, drawing processes and punching process. On the cover of the cold stamping process, right after the Cover of the mass production, quality components, and the use of structural components of the analysis, research, in line with lower performance prerequisite to the identification of stampings, Stamping method used to complete the processing components, and a brief analysis of the blank shape, size, layout, the Conference Board, the number of Drawing, stamping processes in nature, number and sequence determination. For the process, the center of pressure, the die size and the tolerance of the calculation, design mold. Also analyzes the mold of the main components (such as punch and die and dump devices, drawing punch, slates, Punch plate, etc.) design and manufacturing, stamping equipment selection, punch-gap adjustment and establishment of a vital parts machining process. Die requirements set out a detailed list of parts, and gives a reasonable assembly. By fully utilizing modern manufacturing technology to mold traditional mechanical parts for structural improvements, design optimization, Process optimization methods can greatly enhance production efficiency, the method of similar products have some reference.
Keywords: Cover; Mold design; Composite molding; Drawing Punch
目 录
1 分析零件的工艺性 1
2 确定工艺方案 2
2.1 计算毛坯尺寸 2
2.2 确定是否要压边圈 3
2.3 计算拉深次数 3
2.4 确定工艺方案 4
3 主要工艺参数的计算 5
3.1 确定排样、裁板方案 5
3.2 计算工艺力、初选设备 6
3.2.1 计算工艺力 6
(1)落料力 6
(2)冲孔力 7
(3)推件力 7
(4)拉深力 7
(5)压边力 8
3.2.2 拉深功的计算 9
3.2.3 初选压力机 9
3.2.4 计算压力中心 10
3.2.5 计算凸、凹模刃口尺寸及公差 10
4 模具的结构设计 12
4.1 模具结构形式的选择 12
4.1.1 模架的选用 12
4.1.2 模具的闭合高度 13
4.2 模具工作部分尺寸计算 13
4.2.1 落料凹模 13
4.2.2 拉深凸模 14
4.2.3 凸凹模 15
4.2.4 弹压御料板 16
4.2.5 上垫板 18
4.2.6 压边圈 19
5 模具的整体安装 20
5.1 模具的总装配 20
5.2 模具零件 21
6 选定冲压设备 22
7 模具的装配 22
7.1 复合模的装配 22
7.2 凸、凹模间隙的调整 22
8 重要零件的加工工艺过程编制 23
结论 26
参考文献 27
致谢 28
附录 30
实习报告 37
冲压件工艺性是指冲压零件在冲压加工过程中加工的难易程度。虽然冲压加工工艺过程包括备料—冲压加工工序—必要的辅助工序—质量检验—组合、包装的全过程,但分析工艺性的重点要在冲压加工工序这一过程里。而冲压加工工序很多,各种工序中的工艺性又不尽相同。即使同一个零件,由于生产单位的生产条件、工艺装备情况及生产的传统习惯等不同,其工艺性的涵义也不完全一样。这里我们重点分析零件的结构工艺性。
该零件是端盖,如图1.1,该零件可看成带凸缘的筒形件,料厚t=2mm,拉深后厚度不变;零件底部圆角半径r=1.5mm凸缘处的圆角半径也为R=1.5mm;尺寸公差都为自由公差,满足拉深工艺对精度等级的要求。对结构与尺寸的要求是拉深件因尽量简单、对称,并能一次拉深成形;拉深件的壁厚公差或变薄量一般不应超出拉深工艺壁厚变化规律;当零件一次拉深的变形程度过大时,为避免拉裂,需采用多次拉深,这时在保证必要的表面质量前提下,应允许内、外表面存在拉深过程中可能产生的痕迹;在保证装配要求下,应允许拉深件侧壁有一定的斜度;拉深件的径向尺寸应只标注外形尺寸或内形尺寸,而不能同时标注内、外形尺寸。
工艺性要求材料具有良好的塑性,屈强比值越小,一次拉深允许的极限变形程度越大,拉深的性能越好;板厚方向性系数r和板平面方向性系数反映了材料的各向异性性能,当r较大或较小时,材料宽度的变形比厚度方向的变形容易,板平面方向性能差异较小,拉深过程中材料不易变薄或拉裂,因而有利于拉深成形。
该零件结构较简单、形状对称,完全由圆弧和直线组成,没有长的悬臂和狭槽。零件尺寸除中心孔和两中心孔的距离尺寸接近IT11级外,其余尺寸均为自由尺寸且无其他特殊要求,利用普通冲裁方法可以达到零件图样要求。零件材料为20号钢,退火抗拉强度为400Mpa,屈服强度为206Mpa.此材料具有良好的结构强度和塑性,其冲裁加工性较好。该零件的冲裁性较好,可以冲裁加工,适于大批大量。
2.1 计算毛坯尺寸
由于板料在扎压或退火时所产生的聚合组织而使材料引起残存的方向性,反映到拉深过程中,就使桶形拉深件的口部形成明显的突耳。此外,如果板料本身的金属结构组织不均匀、模具间隙不均匀、润滑的不均匀等等,也都会引起冲件口高低不齐的现象,因此就必需在拉深厚的零件口部和外缘进行修边处理。这样在计算毛坯尺寸的时候就必需加上修边余量然后再进行毛坯的展开尺寸计算。
根据零件的尺寸取修边余量的值为3.6mm。
在拉深时,虽然拉深件的各部分厚度要求发生一些变化,但如果采用适当的工艺措施,则其厚度的变化量还是并不太大。在设计工艺过程时,可以不考虑毛坯厚度的变化。同时由于金属在塑性变形过程中保持体积不变,因而,在计算拉深件的的毛坯展开尺寸时,可以认为在变形前后的毛坯和拉深间的表面积相等。 结 论
本次设计成功地设计出一副落料、拉深、冲孔复合模,在设计过程中对很多工艺力进行了详细的计算,在压力机的选择上参照了现行选择压力机的通用法则。这次设计解决了采用双动压力机进行冲孔、拉深、落料的传统模式,将落料、拉深及冲孔同时在一副装在闭式单动压力机上的模具中完成,很大程度的提高了生产效率和制造精度。很适合中国现在模具高速自动化发展的趋势。6 选定冲压设备
冲压设备选择是冲压工艺过程设计的一项重要内容,它直接关系到设备的安全和使用的合理,同时也关系到冲压工艺过程的顺利完成及产品质量、零件精度、生产效率、模具寿命、板料的性能与规格、成本的高低等一系列重要问题。
在前面的设计中,我们已经对冲压设备的吨位以及闭合高度等参数进行了确定。这里根据前面所算出来的各项数据。查表选择压力机,确定选用闭式单点压力机J31-630B,其主要具体参数如下:
公称压力 1000KN
滑块行程 120mm
封闭高度调节量 110mm
工作台尺寸 600460mm
柄孔尺寸 60×75mm
立柱间距离 420mm
工作台板厚 110mm
7 模具的装配
7.1 复合模的装配
复合模一般以凸凹模作为装配基件。其装配顺序为:①装配模架,导套与上模座采用配合,导柱与下模座采用基轴制配合;②装配凸凹模组件(凸凹模及其固定板)和凸模组件(凸模及其固定板);③将凸凹模组件用螺钉和销钉安装固定在指定模座(正装式复合模为上模座,倒装式复合模为下模座)的相应位置上;④以凸凹模为基准,将凸模组件及凹模初步固定在另一模座上,调整凸模组件及凹模的位置,使凸模刃口和凹模刃口分别与凸凹模的内、外刃口配合,并保证配合间隙均匀后固紧凸模组件与凹模;⑤试冲检查合格后,将凸模组件、凹模和相应模座一起钻铰销孔;⑥卸开上、下模,安装相应的定位、卸料、推件或顶出零件,再重新组装上、下模,并用螺钉和定位销紧固。
7.2 凸、凹模间隙的调整
冲模中凸、凹模之间的间隙大小及其均匀程度是直接影响冲件质量和模具使用寿命的主要因素之一,因此,在制造冲模时,必须要保证凸、凹模间隙的大小及均匀一致性。通常,凸、凹模间隙的大小是根据设计要求在凸、凹模加工时保证,而凸、凹模之间间隙的均匀性则是在模具装配时保证的。
冲模装配时调整凸、凹模间隙的方法很多,需根据冲模的结构特点、间隙值的大小和装配条件来确定。这里用垫片法来调整。
垫片法是利用厚度与凸、凹模单面间隙相等的垫片来调整间隙,是简便而常用的一种方法。其方法如下:
参考文献
[1]刘心冶. 冷冲压工艺及模具设计[M]. 重庆:重庆大学出版社,1998
Liu Xinye.Cold stamping technique and Die design[M].Chongqing:Chongqing University Press,1998(in Chinese)
[2]卢险峰. 冲压工艺模具学[M]. 北京:机械工业出版社,2000
Lu Xianfeng.Stamping technique and die learning[M].Beijing:Machine Industry Press,2000(in Chinese)
[3]梁柄文. 实用板金冲压工艺图集[M]. 北京:机械工业出版社,1999
Liang Bingwen.Utility plate stamping technique album[M]. Beijing:Machine Industry Press,1999(in Chinese)
[4]模具实用技术丛书编委会. 冲模设计应用实例[M]. 北京:机械工业出版社,2002
Die utility technology series newsroom.Stamping die design apply example[M]. Beijing:Machine Industry Press,2002(in Chinese)
[5]杜东福. 冷冲压工艺及模具设计[M]. 长沙:湖南科学技术出版社,1990
Du Dongfu.Cold stamping technique and Die design[M].Changsha:Hunan Science Technology Press.1990(in Chinese)
[6]成虹. 冲压工艺与模具设计[M]. 成都:电子科技大学出版社,2000
Cheng Hong.Stamping technique and Die disian [M].Chengdu:Electron Technology Uninersity Press, 2000(in Chinese)
[7]冯柄尧. 模具设计与制造简明手册[M]. 上海:上海科学技术出版社,1998
Feng Bingyao.Die design and produce simplicity handbook[M].Shanghai:Shanghai Science Technology Press,1998(in Chinese)
[8]王树勋,高广升. 冷冲压模具结构图册大全[M]. 广州:华南理工大学出版社,1988
Wang Shuxun,Gao Guangsheng.Cold stamping die fabric album overall[M].Guangzhou:
Huanan Science University Press, 1988(in Chinese)
[9]郑家贤. 冲压工艺模具设计实用技术[M]. 北京:机械工业出版社,1999
Zheng Jiaxian.Stamping technique die design utility technology[M]. Beijing:Machine Industry Press,1999(in Chinese)