香烟横包机右支架工艺规程及夹具设计
摘要:本课题是香烟横包机右支架的机械加工工艺设计和镗床镗模设计,因为零件本身不是很复杂,而且加工精度不是很高,所以其工艺简单。通过对零件的工艺分析,设计了工艺规程,确定了其毛坯的制造形式、加工基准和设计基准、工艺路线、机械加工余量和各工序的切削用量及基本工时,也确定了选用的刀具与机床。为提高劳动生产效率,降低劳动强度,设计了三个平行孔的专用夹具,基于零件的几何形状,设计其夹具为T68镗床上的专用镗模,通过对其定位基准、引刀方式、夹紧方案的选择,最终确定了主要用于加工零件的孔系的镗模,它依靠专用的导向元件——镗套引导镗孔刀具,保证了加工达到了较高的位置精度,并使镗孔的位置精度不受机床精度的影响,利用其夹具精加工孔系时保证了平行孔轴线距误差小于±0.02mm;平行孔的不平行或不垂直度小于0.01/200;平行孔不同轴度误差小于0.01mm。
关键词:加工工艺,夹具,加工精度,镗模
The right support cigarettes horizontal packaging machine’s Technology of order and Fixture design
Abstract:The issue is the right of cigarettes Wang charter stent machining process design and boring - boring machine design, because parts itself is not very complicated and machining accuracy is not very high, so its simple process. Part of the process analysis, design of process in order and set its rough form the manufacture, processing benchmarks and design criteria, process line, machinery allowance and the amount of the cutting process and the basic hours of work, defines the use of knives and machine tools. To improve labor productivity and reduce labor intensity, the three parallel design Kong special fixture, Based on the geometry of components, fixture design for its T68 Boring Boring on the dedicated mode, through its positioning benchmarks primers knife, the choice of clamping program, and the final of the main components for the processing of boring holes mold, It relies on a dedicated oriented components -- guide sets Boring Boring Tool ensure that the processing to achieve a higher position accuracy, Boring enable the location accuracy from the impact of precision machine tools, use their fixture finishing holes at ensuring the parallel hole axis from the error is less than ± 0.02 mm; The parallel hole parallel or vertical is less than 0.01/200; Hole different parallel axis error of less than 0.01 mm.
Keywords:Processing ,Fixture,Precision Machining,Boring die,
目录
1 绪论2
1.1 现代制造技术和工艺2
1.2现代机械工业的生产特点2
1.3夹具及其作用3
1.4现代机床夹具的发展方向3
1.5 本课题的任务和主要内容5
2 零件的分析6
2.1零件的结构与作用6
3 工艺规程的设计9
3.1确定毛坯的制造形式9
3.2 基准的选择9
3.3 制订工艺路线9
3.4 机械加工余量10
3.5 确定切削用量及基本工时14
4 专用夹具设计31
4.1 问题提出31
4.2 夹具的设计31
结论36
致谢37
参考文献38
绪论
1.1 现代制造技术和工艺
现代制造技术包括材料、工艺、设计、制造、管理等方面的新兴技术,现代制造技术的应用是中国制造业发展的脊梁,机械制造业是国民经济最重要的基础产业,而机械制造技术的不断创新则是机械工业发展的技术基础和动力。现代制造技术是以传统制造技术与计算机技术、信息技术、自动控制技术等现代高新技术交叉融合的结果,是一个集机械、电子、信息、材料与管理技术于一体的新型交叉学科,它使制造技术的技术内涵和水平发生了质的变化。因此,凡是那些能够融合当代科学进步的最新成果,最能发挥人和设备的潜力,最能体现现代制造水平的制造技术均称为现代制造技术,它给传统的机械制造业带来了勃勃生机。现代机械制造技术的发展主要表现在两个方向上:一是精密工程技术,以超精密加工的前沿部分、微细加工、纳米技术为代表,将进入微型机械电子技术和微型机器人的时代;二是机械制造的高度自动化,以CIMS和敏捷制造等的进一步发展为代表。
机械制造工艺是各种机械的制造方法和过程的总称。其研究对象是机械产品的制造工艺,包括零件加工和装配两方面。工艺是使各种原材料、半成品成为产品的方法和过程,是生产中最活跃的因素,落实在由工件、刀具、机床、夹具所构成的工艺系统中,和生产实际联系十分紧密。

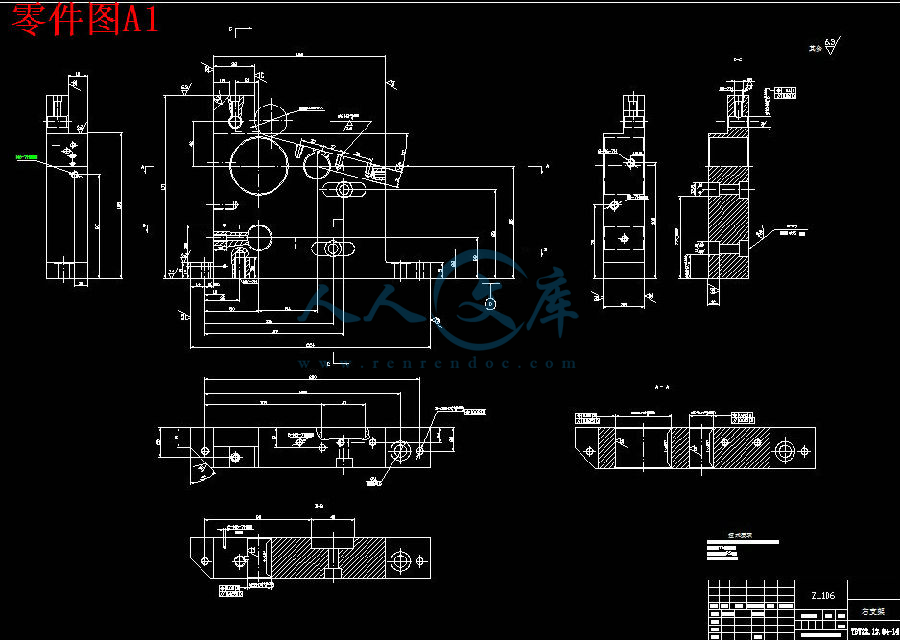

