目录
前言1
摘要5
Abstract6
第一章 绪论7
一 数控系统发展及趋势7
(一)国内外数控系统发展概况7
(二)数控技术发展趋势7
(三)智能化新一代PCNC数控系统10
二 普通机床数控改造的必要性11
(一)微观看改造的必要性11
(二)宏观看改造的必要性12
三 数控改造的内容及优缺点12
(一)国外改造业的兴起12
(二)数控化改造的内容13
(三)机床数控化改造的优缺点13
四 数控机床机构组成、特点及分类14
(一)数控机床的组成14
(二)数控机床机构的特点16
(三)数控机床的分类19
五 普通机床数控化改造市场22
(一)改造的市场22
(二)进口设备和生产线的数控化改造市场22
第二章 C6140普通车床数改的总体方案24
一 总体方案24
(一)主传动系统和进给系统的改造24
(二)主轴脉冲发生器25
(三)主轴脉冲发生器的结构及原理26
第三章 数改C6140车床传动装置设计27
一 滚珠丝杠螺母副27
(一)滚珠丝杠副的工作原理、特点及类型28
(二)滚珠丝杠副的结构29
二 纵向进给系统的设计与计算32
(一)纵向进给系统的设计计算32
(二)滚珠丝杠设计计算34
(三)齿轮及转距的有关计算39
三 横向进给系统的设计与计算42
(一)横向进给系统的设计计算43
(二)滚珠丝杠设计计算44
(三)齿轮及转矩有关计算46
四 滚珠丝杠副轴向间隙的调整和预紧方法47
五 滚珠丝杠副的安装结构50
(一)支承结构50
六 进给系统传动齿轮间隙的消除51
(一)采用减速箱的目的及注意事项51
(二)减少或消除空程的必要性和方法51
第四章 数改C6140自动刀架设计53
一 自动刀架的分类53
二 自动刀架的设计53
第五章 数改6140步进电机的设计56
一 步进电机的工作方式56
二 步进电机的选择56
(一)步进电机选用的基本原则56
(二)数改C6140纵向进给系统步进电机的确定58
(三)数改C6140横向进给系统步进电机的确定58
第六章 数改6140车床导轨设计60
一 导轨的作用60
二 塑料导轨软带60
第七章 数控系统硬件电路设计63
一 数控系统基本硬件组成63
二 单板机控制系统的设计64
第八章 CA6140生产成本及经济技术分析66
第九章 结 论67
参考文献68
专题:70
高速切削的刀具材料及切削技术的应用70
附录Ⅰ:外文文献79
Numerical Control79
附录Ⅱ:中文翻译92
数字控制92
致 谢104
摘要
我国是世界上机床产量最多的国家,但数控机床的产品竞争力在国际市场中仍处于较低水平,即使在国内市场也面临着严峻的形势:一方面国内市场对各类机床产品特别是数控机床有大量的需求,而另一方面却有不少国产机床滞销积压,国外机床产品充斥市场,严重影响我国数控机床自主发展的势头。这种现象的出现,除了有经营上、产品质量上和促销手段上等的原因外,一个最主要的原因就是新产品(包括基型、变型和专用机床)的开发周期长,不能及时针对用户的需求提供满意的产品。
普通机床的数控化改造事业方兴未艾,在我国目前形式下将大批故障机床尤其是一大批闲置的普通机床进行改造、升级,以较小的投入尽快使这批设备在经济发展中发挥效能、创造效益,的确是许多企业的一项不可忽视的课题。
关键词: 脉冲发生器 滚珠丝杠 滚珠丝杠螺母副 自动刀架
塑料导轨软带
Abstract
My national yes machine output mos statet state in the world,the product competitive power at international market suffer still get off to inferiority level , of the therefor numerically-controlled machine , granted that at home market too be faced with austere posture:on the one hand domestic market versus all manner of tool product especially numerically-controlled machine be covered with demand,whereas on the other hand refuse have got not a little made in one's country tool dull sale overstock,abroad tool product overflow market,had a strong impact on me national numerically-controlled machine independence extend momenta into.show such phenomenal face,except to have got manage upper, product quality upper sum sales promotion instrument good cause besides,the development cycle length of the both one upmost cause namely novelty(include fundamental mode, derivative and special machine),be be incapable of in season aim at user's demand supply satisfied product.
General machine tool 'numerical control melt reclaim undertaking be in the ascendant from, upratein our country for the moment form down move in bulk malfunction tool above all crowd idle general machine tool proceed rebuild, up upgrade,withal lesser project into as soon as possible gotten these batch EQUIPment at economic development exert EFFiciency, create benefit,the one term nonnegligible problem of the forsooth yes heap enterprise.
Keywords: Impulse generator Ball screw Ball screw nut deputy
Automatism knife rest Plastic rack soft strap
第一章 绪论
一 数控系统发展及趋势
(一)国内外数控系统发展概况
随着计算机技术的高速发展,传统的制造业开始了根本性变革,各工业发达国家投入巨资,对现代制造技术进行研究开发,提出了全新的制造模式。在现代制造系统中,数控技术是关键技术,它集微电子、计算机、信息处理、自动检测、自动控制等高新技术于一体,具有高精度、高效率、柔性自动化等特点,对制造业实现柔性自动化、集成化、智能化起着举足轻重的作用。目前,数控技术正在发生根本性变革,由专用型封闭式开环控制模式向通用型开放式实时动态全闭环控制模式发展。在集成化基础上,数控系统实现了超薄型、超小型化;在智能化基础上,综合了计算机、多媒体、模糊控制、神经网络等多学科技术,数控系统实现了高速、高精、高效控制,加工过程中可以自动修正、调节与补偿各项参数,实现了在线诊断和智能化故障处理;在网络化基础上,CAD/CAM与数控系统集成为一体,机床联网,实现了中央集中控制的群控加工。
长期以来,我国的数控系统为传统的封闭式体系结构,CNC只能作为非智能的机床运动控制器。加工过程变量根据经验以固定参数形式事先设定,加工程序在实际加工前用手工方式或通过CAD/CAM及自动编程系统进行编制。CAD/CAM和CNC之间没有反馈控制环节,整个制造过程中CNC只是一个封闭式的开环执行机构。在复杂环境以及多变条件下,加工过程中的刀具组合、工件材料、主轴转速、进给速率、刀具轨迹、切削深度、步长、加工余量等加工参数,无法在现场环境下根据外部干扰和随机因素实时动态调整,更无法通过反馈控制环节随机修正CAD/CAM中的设定量,因而影响CNC的工作效率和产品加工质量。由此可见,传统CNC系统的这种固定程序控制模式和封闭式体系结构,限制了CNC向多变量智能化控制发展,已不适应日益复杂的制造过程,因此,对数控技术实行变革势在必行。

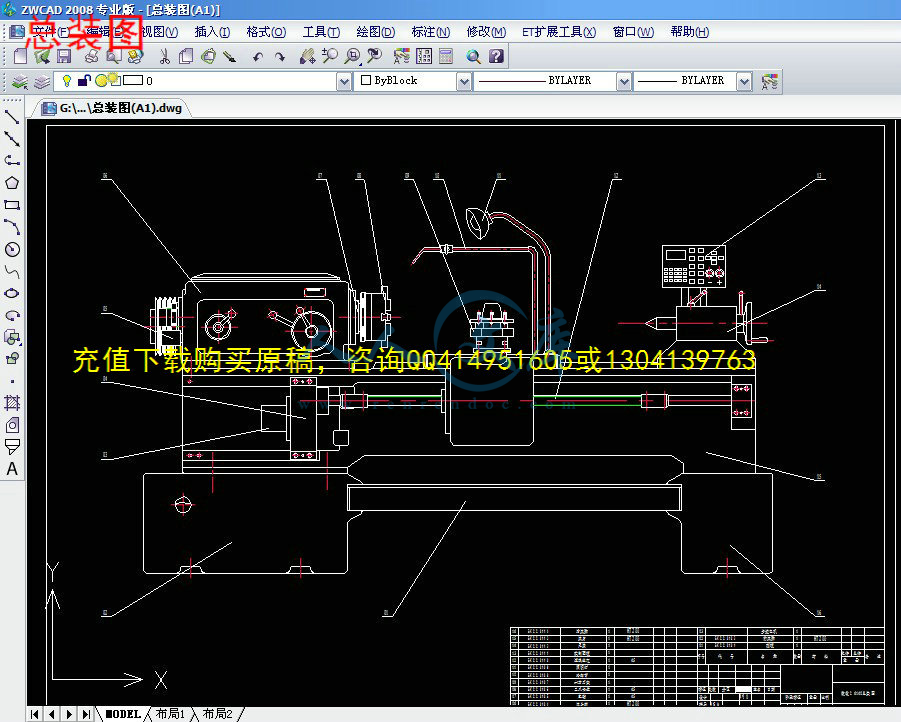


