摘 要
本文作者研究的主要是数控车床的主传动系统,这类主传动系统的设计可用于对普通车床的改造,以适应当前我国机床工业发展的现状,具有一定的经济效益和社会效益。
本文作者完成的设计主要包括根据一些原始数据(其中包括机床的类型、规格等)结合实际条件和情况对车床一些参数进行拟定,再根据拟定的参数,进行传动方案的比较,确定传动方案。然后计算各传动副的传动比及齿轮齿数,再估算齿轮的模数和各轴的轴径,并对齿轮和轴的强度、刚度进行校核。除此之外,还要对箱体内的主要结构进行设计,一些零件的选型,如电磁离合器的选择等,从而完成对整个主传动系统的设计。
关键词:数控车床 主传动系统 设计
Abstract
What author of this text study numerical control main transmission of lathe mainly, the main design of transmission can use for to ordinary transformation of lathe, In order to adapt to the current situation of the present industrial development of lathe of our country, have certain economic benefits and social benefit.
The design that the author of this text finished includes according to some initial data mainly( type, specification of including the lathe ,etc.) Combine actual condition and situation draft to some parameters of lathe, and then according to the parameter drafted, Carry on the comparison of the transmission scheme, confirm the transmission scheme. It then can't calculate every transmission transmission of the packs than and gear wheel tooth count, estimate modulus and the every axle foot-paths of axle of gear wheel more, And check the intensity, rigidity of gear wheel and axle . In addition, will design the main structure in the body of the case , the selecting types of some parts, Electromagnetic choice of clutch,etc., finish to whole main design of transmission for instance.
Keywords:NC machine tool; main driving system; design
目录
0.引言···········································1
1.总体设计方案拟定·······························2
1.1拟定主云动参数·······························2
1.2运动设计·····································3
1.3动力设计和结构草图设计·······················3
1.4轴和齿轮的验算·······························3
1.5主轴变速箱设计·······························3
1.6进给电机伺服系统设计·························3
2.参数拟定·······································5
2.1车床主参数和基本参数·························5
2.2各级转速的确定·······························5
3.运动设计·······································6
3.1主运动拟定方案······························6
3.2 传动方案的比较·······························6
3.3 各级传动比的计算·····························8
3.4 各轴转速的确定方法···························10
3.5 转速图拟定···································10
4. 主传动系统设计································11
4.1 带轮及带的计算·······························11
4.2 齿轮的计算···································13
4.3 电磁离合器的选择和使用·······················21
4.4 轴的设计和验算······························24
5. 主轴变速箱的装配设计·························30
5.1 箱体内结构设计的特点························30
5.2 设计的方法··································31
6. 典型零件的加工工艺(轴类、盘类、箱体类等)····33
6.1 轴类零件的加工······························33
6.2 箱体类零件的加工····························47
致谢············································56
参考文献········································57
0 引言
这次毕业设计中,我所从事设计的课题是CA6140数控车床主传动机构设计及典型零件的数控加工。此类数控车床属于经济型中档精度机床,这类机床的传动要求采用手动与电控双操纵方式,在一定范围内实现电控变速。总体的设计方案就是对传动方案进行比较,绘出转速图,对箱体及内部结构进行设计,包括轴和齿轮的设计、校核等。
为什么要设计此类数控车床呢?因为随着我国国民经济的不断发展,我国制造业领域涌现出了许多私营企业,这些企业的规模普遍不大,没有太多的资本。一些全功能数控系统,其功能虽然丰富,但成本高,对于这些中小型企业来说购置困难,但是中小型企业为了发展生产,希望对原有机床进行改造,进行数控化、自动化,以提高生产效率。我国机床工业的发展现状是机床拥有量大、工业生产规模小,突出的任务就是用较少的资金迅速改变机械工业落后的生产面貌,使之尽可能提高自动化程度,保证加工质量,减轻劳动强度,提高经济效益。我国是拥有300多万台机床的国家,而这些机床又大量是多年累积生产的通用机床,自动化程度低,要想在近几年内用自动和精密设备更新现有机床,不论是资金还是我国机床厂的能力都是办不到的。因此,普通机床的数控改造,大有可为。它适合我国的经济水平、教育水平和生产水平,已成为我国设备技术改造主要方法之一。目前,我国经济型数控系统发展迅速,研制了几十种简易数控系统,有力地促进了我国数控事业的发展。经济型数控机床系统就是结合现实的生产实际,我国的国情,在满足系统基本功能的前提下,尽可能地降低价格。

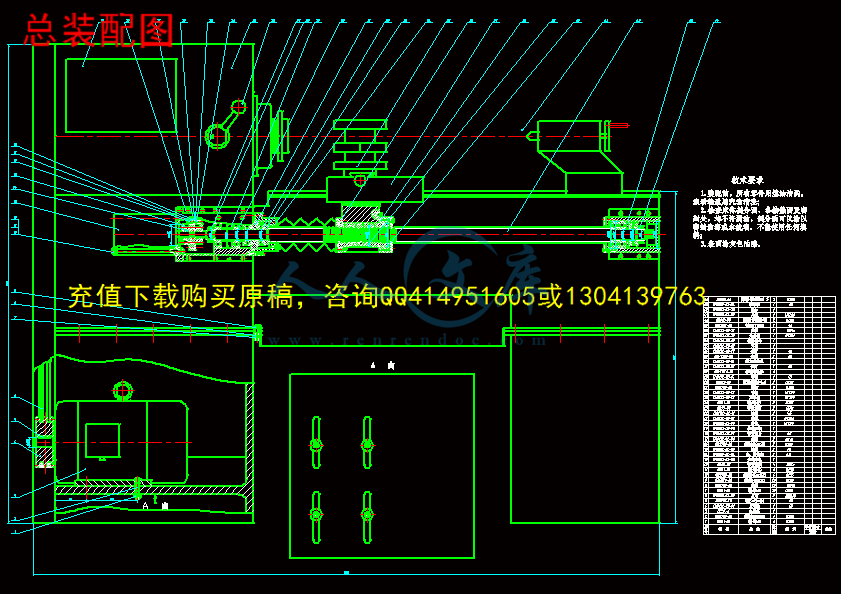

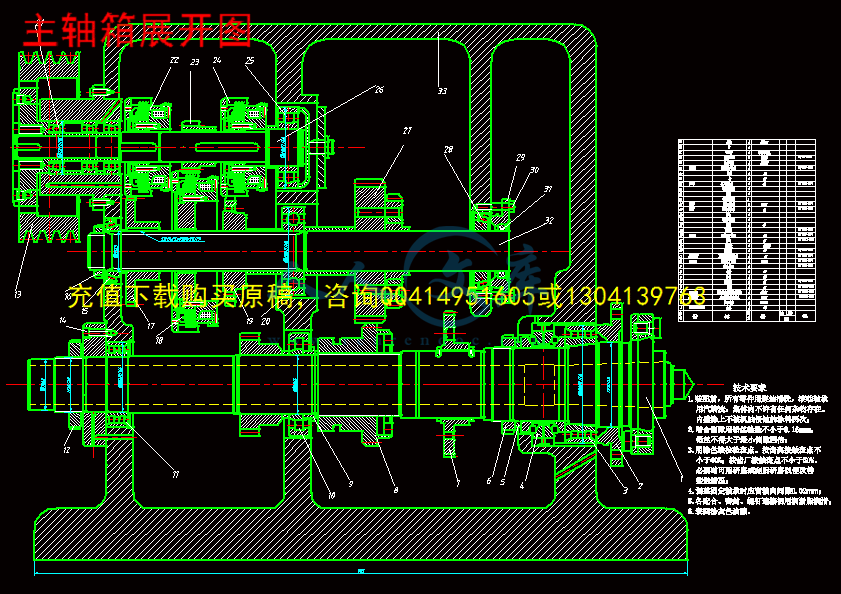

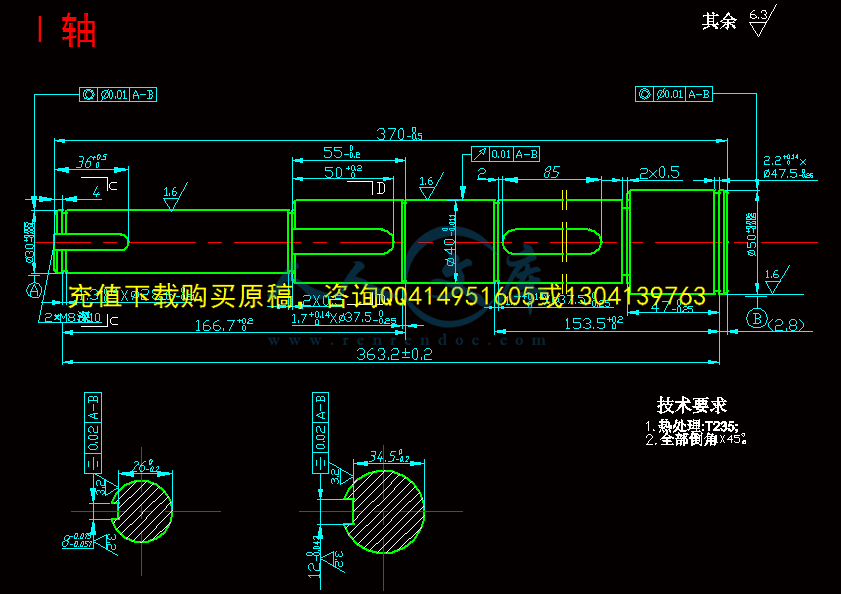